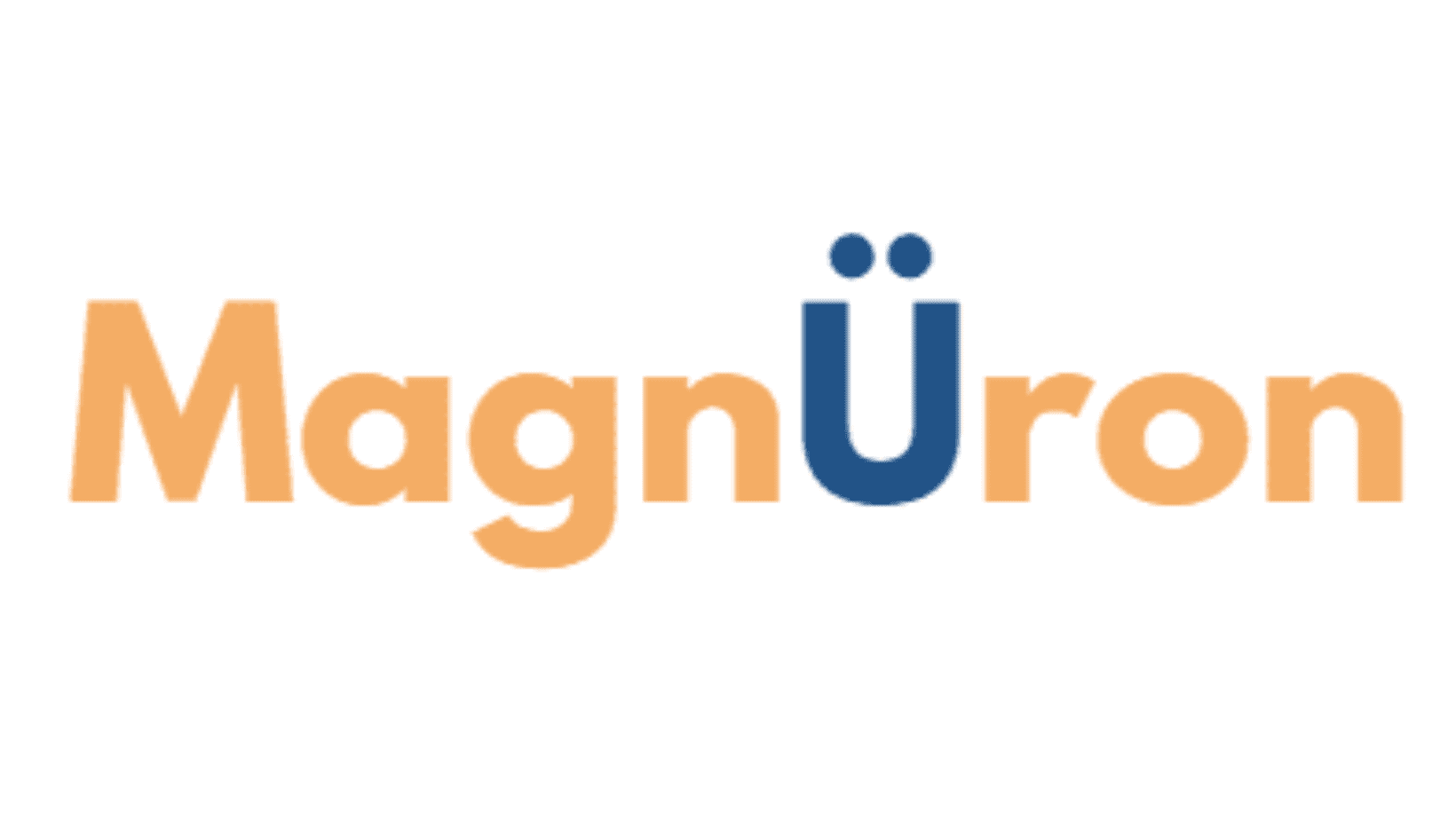
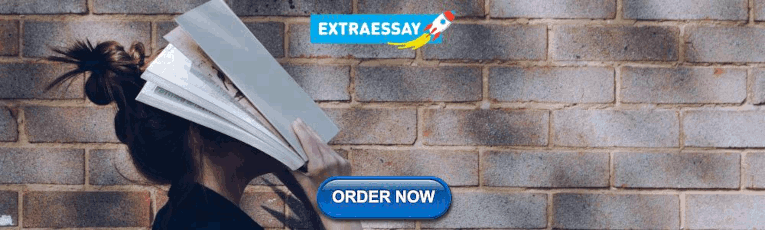
Mastering the 8D Problem Solving Method: A Comprehensive Guide

It is often said that “a stitch in time saves nine.” Efficient problem-solving is an essential skill , especially in a professional environment.
When it comes to addressing complex issues, the 8D Problem Solving method has gained significant traction across various industries. In this comprehensive guide, we will explore the 8D Problem Solving method, its history, and its application across multiple sectors.
History of the 8D Problem Solving Method
The 8D Problem Solving approach has its origins in World War II when the American military was under intense pressure to produce reliable weapons as quickly as feasible.
The military established a methodical approach to problem-solving, focusing on quality control and continual improvement, to ensure that resources were used effectively.
This was the first instance of what would later develop into the 8D technique.
The writings of Walter Shewhart , W. Edwards Deming , and Joseph M. Juran , who set the groundwork for contemporary quality control and continuous improvement ideas, had a substantial impact on the development of the 8D Problem Solving approach.
These guidelines stress the value of data-driven decision-making and the necessity for businesses to take a pro-active approach to problem-solving.
The Ford Motor Company faced intense competition from Japanese automakers in the 1980s, which caused it to struggle.
Ford used quality control and continuous improvement as its guiding principles and included the 8D Problem Solving process into its business practices to regain its footing.
The automobile sector adopted the 8D methodology widely as a result of the initiative’s success.
The 8D Problem Solving approach gained popularity outside of the automobile industry as it showed continuous promise.
The 8D methodology is now being used by businesses in a variety of industries, such as manufacturing, healthcare, and technology, to solve complicated issues, enhance their operations, and guarantee customer happiness.
The 8D Problem Solving approach has attained widespread acceptance throughout a number of industries.
It is a potent tool for businesses looking to improve their problem-solving skills and promote long-term success due to its systematic approach, emphasis on teamwork, and emphasis on continual improvement.
The Eight Disciplines of 8D Problem Solving
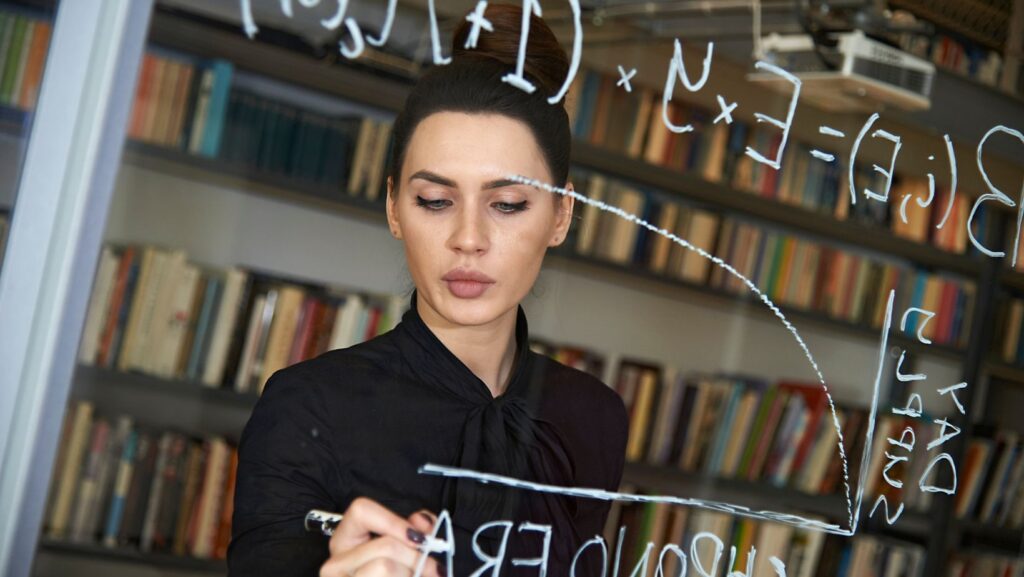
D1: Form a Team
Assembling a diverse team with relevant expertise
The first phase in the 8D process is to put together a varied team of people with the necessary knowledge, making sure that all viewpoints and skill sets are represented. This multidisciplinary approach makes it easier to recognize problems and produce creative solutions.
Defining roles and responsibilities
The tasks and responsibilities of each team member must be established once the team has been constituted. Team members can work cooperatively and effectively by setting clear expectations, ensuring that everyone’s abilities are utilized to the utmost extent. It keeps the problem-solving process on track and upholds accountability.
D2: Define the Problem
Accurate problem description
Accurately characterizing the current problem is the second discipline of the 8D technique. In order to do this, the team must acquire pertinent data, analyze it, and create a clear, succinct statement describing the problem. A focused and efficient problem-solving approach is built on a well identified problem.
Gathering data and identifying root causes
To create long-lasting solutions, the problem’s underlying causes must be determined. The team must gather information from a variety of sources, such as consumer feedback, product testing, or process performance measurements, in order to accomplish this. The team is able to uncover patterns, trends, and potential fundamental causes thanks to this data-driven approach, which also ensures that the problem-solving procedure is unbiased and grounded in facts.
D3: Develop an Interim Containment Plan
Quick, temporary solutions
Minimizing the effects of a problem is crucial in the field of problem solving. Creating an interim containment strategy, which offers quick, temporary solutions to the issue, is the third discipline in the 8D technique. These quick fixes aid in limiting the harm, stopping more problems, and buying the team some time while they produce a more long-term fix.
Mitigating damage and preventing further issues
It is essential to keep an eye on the interim containment plan’s efficacy and adjust as necessary as you go. This guarantees that the short-term fix works to contain the harm and stop the issue from getting worse. Any lessons learnt during this phase should also be recorded by the team because they will be helpful in creating the ultimate corrective action.
D4: Identify Root Causes
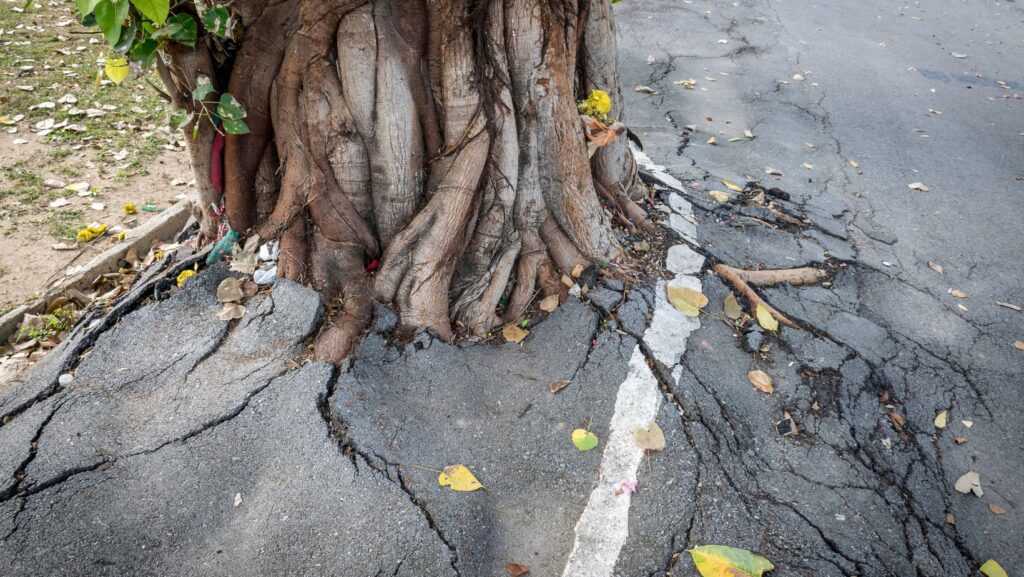
Root cause analysis techniques
The fourth discipline of the 8D technique entails examining the issue more closely in order to determine its underlying causes. Various root cause analysis methods, including the Five Whys, Fishbone Diagram, and Fault Tree Analysis, must be used in this situation. The team may create focused solutions that address the issue at its source rather than just treating its symptoms by determining the fundamental causes of the problem.
Verifying root causes through data
Verifying potential root causes with data is crucial after the team has discovered them. Taking this step, the team can avoid being misled by assumptions or unrelated elements and instead concentrate on the real core cause. The team may be confident that their suggested remedies will be successful in tackling the problem by validating the main causes using data.
D5: Choose and Verify Permanent Corrective Actions
Developing and evaluating potential solutions
The team can now consider various solutions after determining the root reasons. “Two heads are better than one,” as the saying goes, and this collaborative process frequently produces innovative and useful ideas. The team should assess each alternative after producing a list of potential corrective actions based on elements including feasibility, cost, and potential impact. This makes it more likely that the selected solution will be both workable and efficient.
Implementing and verifying chosen solution
It’s crucial to assess the effectiveness of the chosen solution before fully applying it. A small-scale trial or a pilot program can be used to accomplish this. The team may be certain that their selected corrective action will be successful when used on a bigger scale by confirming the solution’s success in resolving the issue.
D6: Implement Permanent Corrective Actions
Developing a detailed action plan
The team must create a thorough action plan for putting the selected solution into practice when it has been verified. This strategy should specify the actions, materials, and timetable required for a full integration of the solution into the organization’s operations. A comprehensive action plan makes for an effective implementation that minimizes any hiccups or setbacks.
Monitoring implementation and adjusting as needed
It’s essential to keep an eye on the permanent remedial action’s development and adjust, as necessary. The team may make sure that the solution is properly integrated and produces the required results by remaining alert and reacting to any unforeseen obstacles.
D7: Prevent Recurrence
Identifying potential future issues
The 8D method’s seventh discipline focuses on predicting prospective problems that might develop in the future from comparable underlying causes. The team can help to prevent repeat incidences and continuously enhance the organization’s procedures by foreseeing and addressing these possible issues.
Adjusting processes and procedures to prevent recurrence
The team should analyze and make any necessary modifications to the organization’s systems and procedures to stop the issue from happening again. This can entail creating new quality control procedures, updating the documentation, or changing the training materials. Implementing these changes, the company can promote a climate of continuous development and make sure that the lessons discovered throughout the problem-solving procedure are incorporated into every aspect of its day-to-day work.
D8: Congratulate the Team
Recognizing team achievements
It’s important to acknowledge the team’s effort and commitment when the 8D technique has been implemented successfully. Celebrating their accomplishments promotes a sense of ownership, boosts morale, and encourages continuing commitment to ongoing growth.
Sharing lessons learned with the organization
The team should share their lessons learned with the broader organization. Doing so, they can help to disseminate the knowledge gained during the problem-solving process, fostering a culture of learning and improvement throughout the company.
Practical Application of the 8D Problem Solving Method

Numerous industries, including aerospace, automotive, healthcare, manufacturing, and technology, have successfully used the 8D Problem Solving method. These actual instances show how adaptable and successful the system is at solving a variety of challenging issues .
Although the 8D method offers a structured approach to problem-solving, it is crucial to customize the procedure to the particular requirements and context of the current problem.
This could entail modifying the chronology, modifying the root cause analysis methods, or adding new data sources.
The team can ensure the most efficient problem-solving procedure by continuing to be adaptable and flexible.
Tips for Successful 8D Problem Solving Implementation
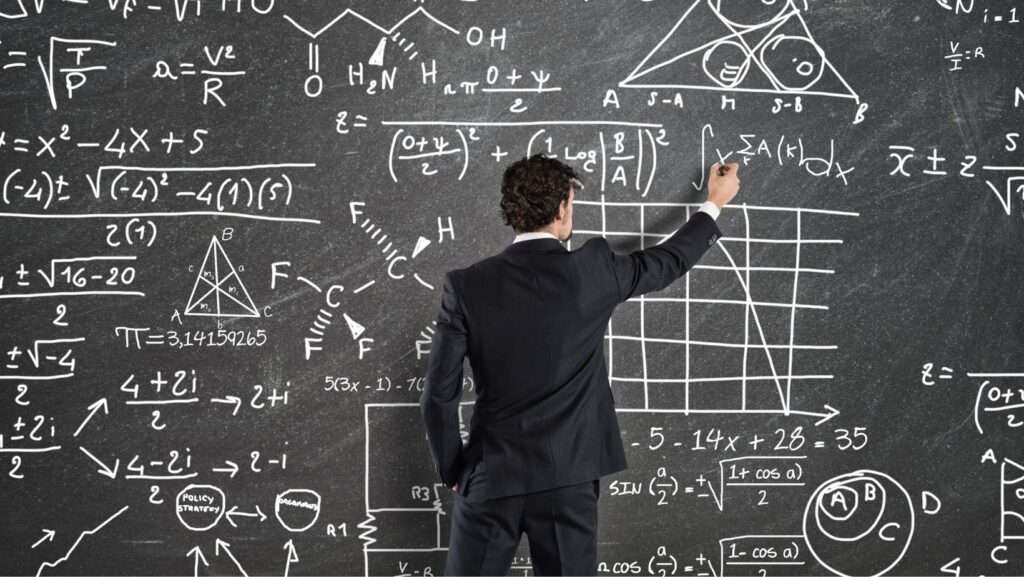
Emphasizing clear communication
Clear communication is the lifeblood of effective problem-solving.
Throughout the 8D process, the team should prioritize open and honest communication, ensuring that all members have a thorough understanding of the problem, the chosen solution, and their individual responsibilities.
Fostering a culture of collaboration and continuous improvement
A collaborative and improvement-focused culture is key to the success of the 8D method.
Encouraging open dialogue, mutual support, and ongoing learning, the organization can create an environment in which the 8D method can thrive.
Employing project management tools and techniques
Project management tools and techniques can be invaluable in facilitating the 8D process.
Using tools such as Gantt charts, project management software, or Kanban boards, the team can better track progress, allocate resources, and manage timelines.
These tools can help to keep the problem-solving process organized and efficient, ensuring that the team stays on track and achieves their goals.
Final Thoughts
The 8D Problem Solving method is an effective and adaptable way for tackling complicated challenges in a variety of industries.
Organizations may methodically identify and address problems, stop them from happening again, and promote a culture of continuous improvement and adhering to the eight disciplines.
As we’ve seen, the 8D method’s effectiveness depends on putting together a varied team, upholding clear communication, customizing the procedure for particular circumstances, and using efficient project management tools and approaches.
We urge you to use the 8D Problem Solving method inside your organization now that you have a thorough understanding of it.
Doing this, you may not only address issues more quickly, but also unleash the long-term growth potential of your company.
If you can master the 8D approach, your business will have a better future and you’ll be well-equipped to traverse the waters of problem-solving.
Q: What is the 8D Problem Solving method?
A : A systematic strategy for addressing complicated challenges across multiple industries is the 8D Problem Solving method. It consists of eight disciplines that help firms recognize problems, find solutions, stop them from happening again, and promote a continuous improvement culture.
Q: What are the origins of the 8D Problem Solving method?
A : The United States military created a systematic approach to problem-solving during World War II that was centered on quality control and continual improvement, and this is where the 8D technique got its start. The Ford Motor Company later adopted and promoted the technique in the 1980s.
Q: What are the eight disciplines of the 8D Problem Solving method?
A : The eight disciplines of the 8D method are
- Form a Team
- Define the Problem
- Develop an Interim Containment Plan
- Identify Root Causes
- Choose and Verify Permanent Corrective Actions
- Implement Permanent Corrective Actions
- Prevent Recurrence
- Congratulate the Team
Q: How can the 8D method be applied across different industries?
A : The 8D method is adaptable and may be used to solve a wide variety of complicated problems in a number of different industries, including manufacturing, aerospace, automotive, healthcare, and technology. Organizations should modify the process to match the particular requirements and context of the current challenge in order to utilize the 8D technique effectively.
Q : What are some tips for successfully implementing the 8D Problem Solving method?
A : To ensure the success of the 8D method, organizations should
- Emphasize clear communication.
- Foster a culture of collaboration and continuous improvement.
- Employ effective project management tools and techniques .
Q: What is the role of root cause analysis in the 8D method?
A : The 8D method’s key element is root cause analysis, which identifies the root reasons of an issue. Organizations can create focused solutions that solve the issue at its foundation rather than just masking the symptoms by addressing the root causes.
Q: How can the 8D method help prevent the recurrence of problems?
A : By recognizing potential future issues that may result from comparable root causes and modifying processes and procedures accordingly, the 8D technique aids in preventing the recurrence of problems. This proactive strategy assists companies in making continuous improvements and reducing the possibility that similar issues will arise again.
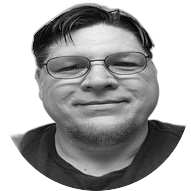
Ronnie Patterson
Ronnie Patterson, founder of MagnÜron, is a multifaceted entrepreneur with a diverse background in music, electronics engineering, and engineering management. Drawing on experience across various industries, He offers expertise in SEO, operations, and strategy to help businesses thrive. Possessing a unique perspective and unwavering commitment to collaboration, and ideal partner for growth and success.
Similar Posts
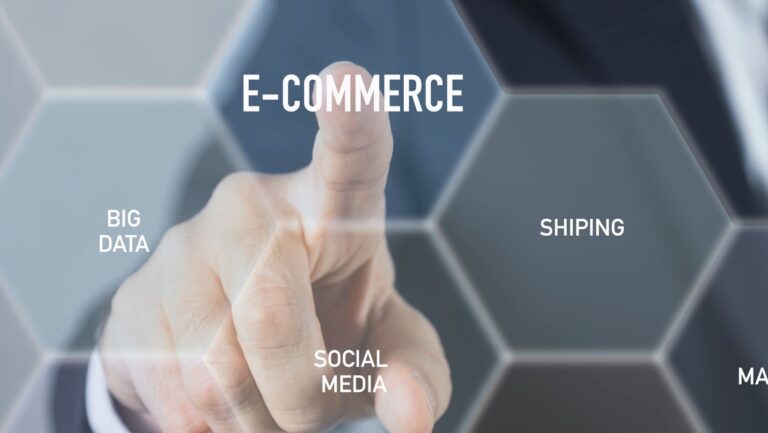
E-commerce Analytics for Data-Driven Decision Making: 7+ Key Steps
Businesses must harness the power of data and analytics to…
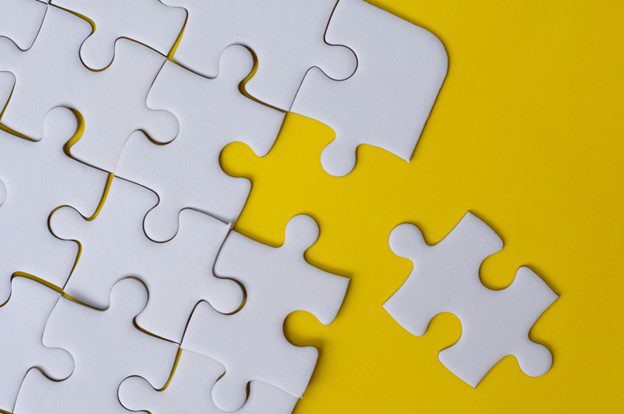
15 Challenges Faced by New Businesses, and How to Solve Them!
Establishing a new business is an exciting adventure full of…
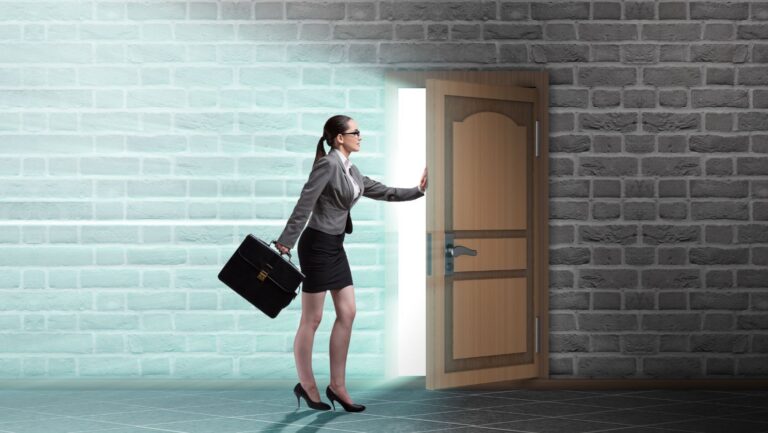
Opportunity Cost The Significance In Decision-Making
What Is Opportunity Cost? A key idea in economics and…
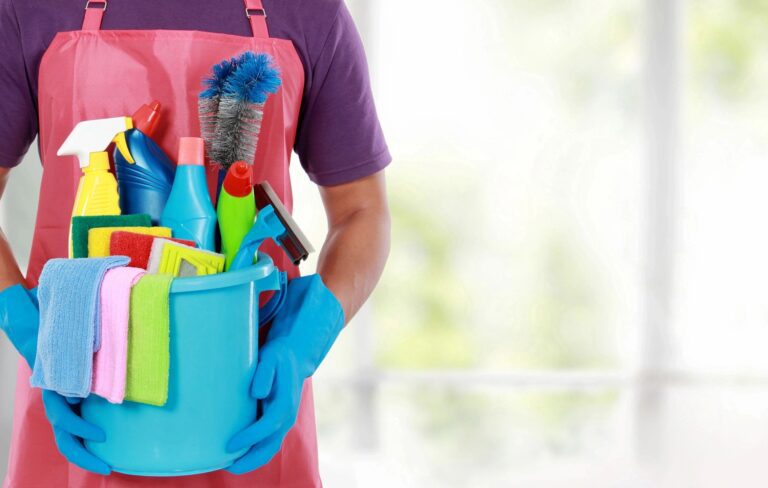
How to Start a Cleaning Business: Tips for Establishing and Growing Your Cleaning Company
Starting a cleaning business can be a great way to…
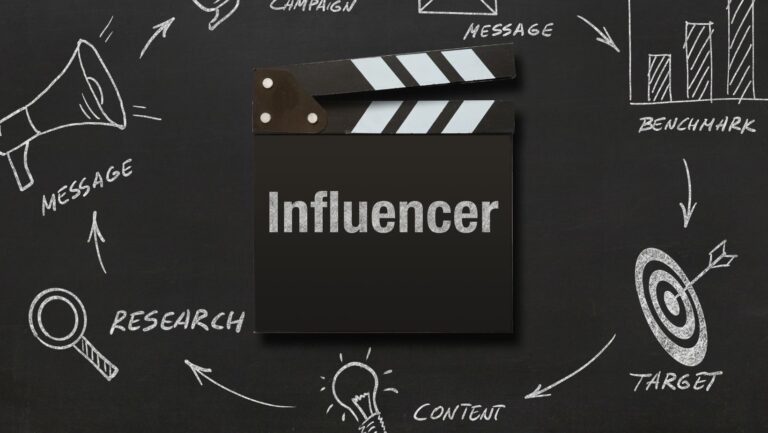
Influencer Marketing 101: Boosting Your Business with Social Influence
Influencer marketing has emerged as a major change in digital…
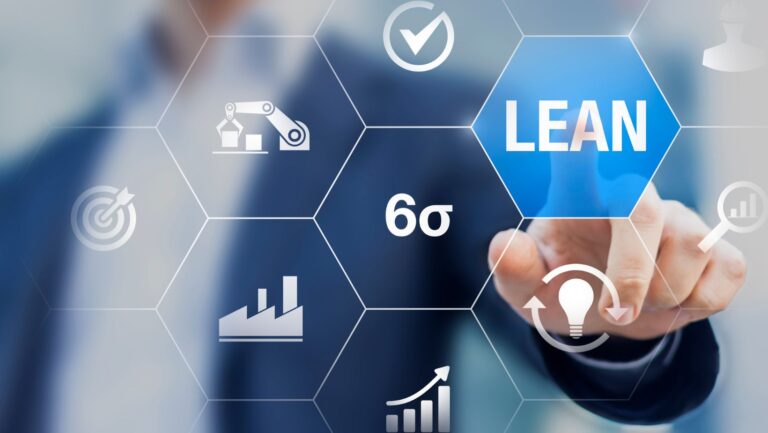
Lean Principles: Streamlining Your Small Business Operations
Efficiency is critical to success in today’s competitive business environment,…
Project Review Insights
Empowering Management Excellence
The harder you work for something, the greater you'll feel when you achieve it.

Guide to Problem-Solving Methodologies: 8D, PDCA, DMAIC, and Kaizen
Welcome 2024! Embracing and mastering problem-solving methodologies is essential for organizations on their continuous improvement journey throughout the year. By learning these techniques, teams can streamline and enhance their problem-solving processes, fostering a culture of innovation and resilience in the face of challenges.
This proactive approach will empower organizations to navigate uncertainties, drive efficiency, and achieve sustainable growth in the dynamic landscape of 2024 and beyond.
This article explores four widely adopted methodologies: 8D (Eight Disciplines), PDCA (Plan-Do-Check-Act), DMAIC (Define-Measure-Analyze-Improve-Control) , and Kaizen .
Each methodology brings a unique approach to problem-solving, tailored to different contexts and challenges.
Problem-Solving Methodologies
1. 8d (eight disciplines).

The 8D problem-solving methodology is structured into eight steps, providing a systematic approach to identifying, solving, and preventing problems.
The steps include:
- D1: Form a Team
- D2: Define the Problem
- D3: Develop Interim Containment Actions
- D4: Identify the Root Cause
- D5: Choose Permanent Corrective Actions
- D6: Implement Corrective Actions
- D7: Prevent Recurrence
- D8: Congratulate the Team
8D emphasizes teamwork, data-driven analysis, and a focus on both short-term containment and long-term solutions. It encourages a thorough investigation into the root cause to prevent recurrence.
2. PDCA (Plan-Do-Check-Act)
PDCA, also known as the Deming Cycle, is a continuous improvement method popularized by W. Edwards Deming.

The PDCA cycle comprises four stages:
- Plan : Identify the problem and plan for change
- Do : Execute the plan on a small scale
- Check : Analyze the results and compare against the expected outcomes
- Act : Implement necessary changes on a larger scale and standardize improvements
PDCA is iterative, promoting a constant feedback loop for ongoing improvement. It is versatile and applicable across various industries and processes.
3. DMAIC (Define-Measure-Analyze-Improve-Control)
DMAIC is a core component of the Six Sigma methodology, designed to improve processes by eliminating defects. The five stages of DMAIC are:
- Define : Clearly articulate the problem, project goals, and customer requirements
- Measure : Collect relevant data to understand the current state of the process
- Analyze : Identify root causes of problems through data analysis
- Improve : Develop and implement solutions to address the root causes
- Control : Sustain the improvements and monitor the process to prevent regression
DMAIC emphasizes data-driven decision-making and statistical analysis to achieve measurable and sustainable improvements.
Kaizen , a Japanese term meaning “continuous improvement,” is a philosophy that promotes incremental, continuous changes.
Key principles of Kaizen include:
- Standardize processes
- Practice 5S (Sort, Set in order, Shine, Standardize, Sustain)
- Empower employees to suggest and implement improvements
- Focus on small, manageable changes
Kaizen fosters a culture of continuous improvement at all organizational levels, encouraging employees to contribute to the evolution of processes and systems.
Related Article: Understanding the 5S Methodology: Streamlining Success in Workspaces
Choosing the Right Tool or the Right Problem-Solving Methodologies
While each methodology offers a unique approach, the most effective one depends on the specific context:
- 8D: Ideal for complex problems, customer complaints, and team-based problem-solving.
- PDCA: Suitable for quick improvements, testing new ideas, and cyclical progress.
- DMAIC: Effective for data-driven, statistically controlled process optimization and defect reduction.
- Kaizen: Perfect for fostering a culture of continuous improvement, small incremental changes, and employee engagement.
Final Thoughts
Effective problem-solving is essential for organizational success and continuous improvement. The 8D , PDCA, DMAIC , and Kaizen methodologies offer distinct approaches, allowing organizations to choose the one that aligns best with their goals and context.
By incorporating these methodologies, businesses can enhance their problem-solving capabilities, driving efficiency, quality, and overall success.
As the New Year begins, I wish you all lots of happiness and good luck in your projects!
Join our vibrant community of enlightened readers! Elevate your knowledge with exclusive updates and insights by subscribing today!
A heartfelt thank you for investing your time in reading this article. For a deeper dive into Project and Operations Management, along with best practices, delve into more of my articles at www.projinsights.com .
Your thoughts and feedback are invaluable to us. Reach out to us at [email protected] ; we cherish every comment.
If you’ve found value in my content and feel like supporting, why not treat me to a coffee ?
And here’s an invitation: Subscribe to experience daily blog posts. Don’t keep this treasure to yourself—share it with your family and friends. Thank you!
Subscribe Our Free Newsletter
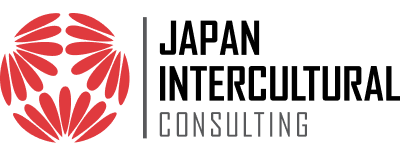
Saihatsu Boshi – Key to Japanese problem-solving
The Japanese are well-known to be perfectionists in various aspects of their work. Non-Japanese who work with them, either as employees or suppliers, need to be familiar with one of the key techniques they use for pursuing perfection, “ saihatsu boshi .”
Translated literally, this means “prevention of reoccurrence.” But the simplicity of this phrase belies the deep significance it has for many Japanese. Of course, people everywhere can agree that making sure problems don’t happen again is a good thing. However, the Japanese have developed a structured process for doing this. And they often express frustration when working with people from other cultures who do not take this approach and thus run the risk of the same problems cropping up again. In Japan, saihatsu boshi is simply accepted standard behavior, and anything else would suggest unprofessionalism or lack of commitment. Thus, in order to optimize their relationships with Japanese, it’s useful for non-Japanese to adopt this technique.
The first step in saihatsu boshi is “ genin wo mitsukeru “, which translates as getting to the root of the problem, or discovering the root cause. This process is what Americans might refer to as a detailed post-mortem analysis. It involves looking at all the possible reasons why something went wrong, and identifying specifically what factors led to the failure, mistake, problem, or defect. A vague answer like “it was human error” or “it was a random glitch” are deemed unacceptable.
In many non-Japanese cultures, this root cause analysis is difficult because individuals are not comfortable being forthright about their errors that led to a problem. This is because in many cultures, admitting a mistake can be viewed as a weakness, be acutely embarrassing, or cause one to be the target of punishment or even dismissal. In the Japanese environment, however, people are expected to put aside their pride in the pursuit of perfection and the common good. The lifetime employment custom also makes it safer for people to be forthright about instances where their performance was not perfect, because they won’t fear being let go as a result.
Once the root cause has been identified, “ taisaku ” – countermeasures – need to be put in place. This is true no matter how difficult to control or rarely-occurring a root cause might be. For example, if you have identified your root cause as a simple mistake made by someone on the production line, your countermeasure might involve instituting double-check procedures, adding additional inspection staff at the end of the line, or altering the operator’s job so that fatigue or distractions are reduced.
As an example of the Japanese demand for countermeasures even in situations where they might seem impossible, one of my clients lost a boatload of product headed toward the U.S. when the ship carrying it hit a typhoon and sank to the bottom of the Pacific. The company was infuriated when the shipping firm seemed unable to come up with a countermeasure. From the shipping company’s perspective, typhoons are not something that humans can do anything about. But from the Japanese perspective, anything can be countermeasured. Perhaps the shipping company could build ships with thicker hulls, or buy more accurate weather forecasting equipment. When the shipping company did not produce a countermeasure, it irreparably damaged its relationship with its Japanese client.
And here lies one of the morals of this story: in Japanese eyes, any mistake or failure is of course a huge negative. But if you can produce a good root cause analysis and corresponding countermeasures, you can often get a second chance. The damage from not doing this kind of saihatsu boshi can be worse than from the initial mistake or problem. Japanese feel that although having a problem is a bad thing, letting the same problem happen again is even worse.
In this sense , saihatsu boshi is all about organizational learning – the ability for a company to absorb the lessons of its own experience. Saihatsu boshi is a way of ensuring that individuals and the entire organization will learn from things that go wrong, and change its ways of doing things so that they will never be repeated. The countermeasures created in the saihatsu boshi process usually consist of improvements in processes and procedures. Thus, saihatsu boshi is really the backbone of the vaunted Japanese ability to do kaizen (continuous improvement.)
Here’s one more example of saihatsu boshi . I was using a Japanese-owned translation company as a subcontractor. I had asked them to prepare a translation for a client, and send it to them by Federal Express immediately before leaving on a trip to Japan. When I returned from Japan, I called the client to discuss the document, which they were supposed to have been reviewing while I was gone, only to discover that they had never received it. Upon investigation, it turned out that the Federal Express had been duly delivered to the company, but was misrouted by the mailroom staff and had never made it to my counterpart’s desk. In this situation, many American suppliers would have said “it wasn’t our fault” and the case would be closed. However, I received a phone call from the Japanese who runs the translation company, saying how he didn’t want me to have to worry about a repeat of this kind of problem. So he would institute a new procedure: anytime they sent a Federal Express to one of my clients in the future, they would always make a follow-up call the next day to make sure that they had received it. From my perspective, this was customer service above-and-beyond the call of duty, but when I told him so, he was surprised that I thought so. From his point of view, implementing a countermeasure when something had gone wrong was standard operating procedure. Imagine the consternation of a Japanese who is used to being dealt with in this way when faced with a “it’s out of our hands” kind of approach.
So, let’s say that something has gone wrong or there is some problem in the work you have been doing with Japanese. What’s the best way to address it using the saihatsu boshi technique? First, show your intention to do saihatsu boshi by saying something like “we want to make sure this doesn’t happen again”, “we want to prevent a reoccurrence of this problem”, or “we want to be sure to avoid this kind of problem in the future.” Then, describe in detail the root cause or causes. Even when dealing with someone of higher rank than you or a client, being honest about the root causes is extremely important. This willingness to be forthright, even about your own mistakes or failures, will be valued. Then, for each root cause, describe in detail what countermeasure or countermeasures you plan to adopt. Finally, finish with a reaffirmation of your commitment to avoiding having this same problem happen again, and your desire for a continued good working relationship.
Other articles you may be interested in:
HORENSO – (REPORT, CONTACT AND CONSULT)
GENIN TSUIKYU – JAPANESE BUSINESS GETS TO THE ROOT OF THE MATTER
SAIHATSU BOSHI – “THOSE WHO FORGET THE MISTAKES OF THE PAST ARE DOOMED TO REPEAT THEM”
Related articles
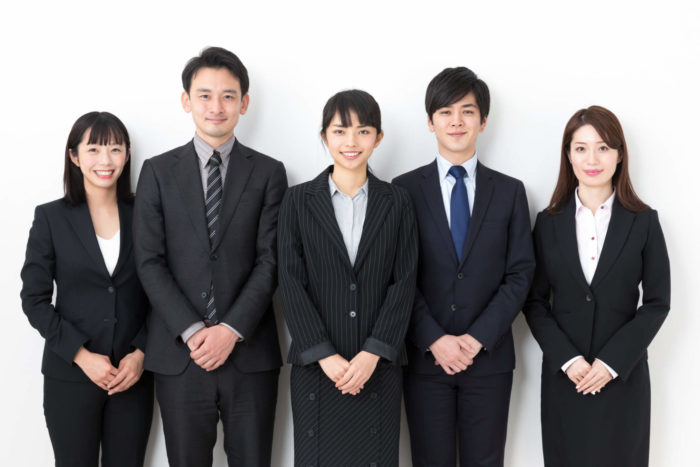
New approaches needed by Japanese companies to Generation Z
Judging by this article in the Nikkei Business magazine (¥), many of the concerns and valu
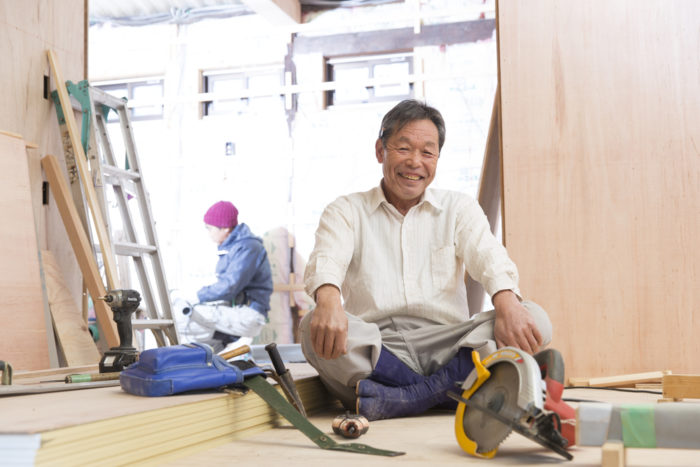
(Video) So, What is Monozukuri Actually?
Monozukuri is one of those well-known and often used Japanese words among people from outside of Jap
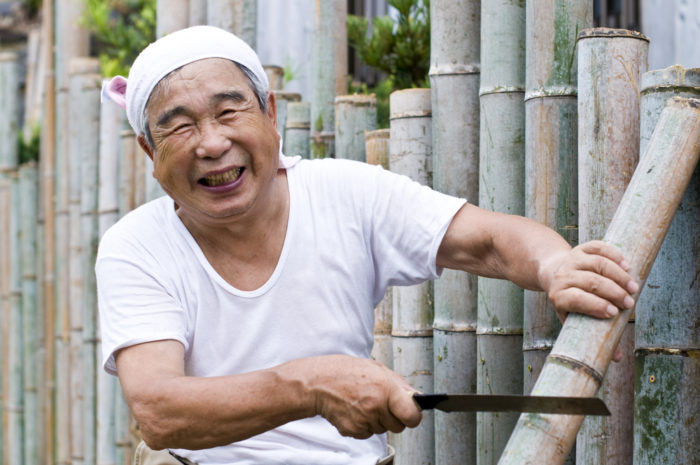
(Video) So, What is Ikigai Actually?
Ikigai - The Japanese word for the goal that gets you going - is often misunderstood by non-Japanese
What can we help you achieve?
- Privacy Overview
- Strictly Necessary Cookies
- Cookie Policy
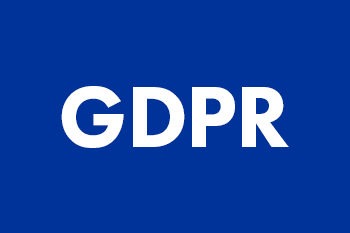
This website uses cookies so that we can provide you with the best user experience possible. Cookie information is stored in your browser and performs functions such as recognising you when you return to our website and helping our team to understand which sections of the website you find most interesting and useful.
Strictly Necessary Cookie should be enabled at all times so that we can save your preferences for cookie settings.
If you disable this cookie, we will not be able to save your preferences. This means that every time you visit this website you will need to enable or disable cookies again.
More information about our Privacy Policy
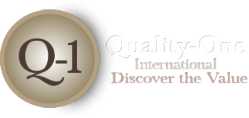
Eight Disciplines of Problem Solving (8D)
– Eight Disciplines of Problem Solving –
⇓ Introduction to 8D
⇓ What is 8D
⇓ Why Apply 8D
⇓ When to Apply 8D
⇓ How to Apply 8D
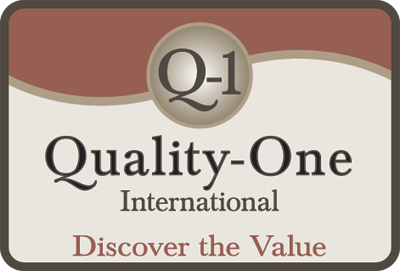
Introduction to Eight Disciplines of Problem Solving (8D)
The Eight Disciplines of Problem Solving (8D) is a problem solving methodology designed to find the root cause of a problem, devise a short-term fix and implement a long-term solution to prevent recurring problems. When it’s clear that your product is defective or isn’t satisfying your customers, an 8D is an excellent first step to improving Quality and Reliability.
Ford Motor Company developed this problem solving methodology, then known as Team Oriented Problem Solving (TOPS), in the 1980s. The early usage of 8D proved so effective that it was adopted by Ford as the primary method of documenting problem solving efforts, and the company continues to use 8D today.
8D has become very popular among manufacturers because it is effective and reasonably easy to teach. Below you’ll find the benefits of an 8D, when it is appropriate to perform and how it is performed.
What is Eight Disciplines of Problem Solving (8D)
The 8D problem solving process is a detailed, team oriented approach to solving critical problems in the production process. The goals of this method are to find the root cause of a problem, develop containment actions to protect customers and take corrective action to prevent similar problems in the future.
The strength of the 8D process lies in its structure, discipline and methodology. 8D uses a composite methodology, utilizing best practices from various existing approaches. It is a problem solving method that drives systemic change, improving an entire process in order to avoid not only the problem at hand but also other issues that may stem from a systemic failure.
8D has grown to be one of the most popular problem solving methodologies used for Manufacturing, Assembly and Services around the globe. Read on to learn about the reasons why the Eight Disciplines of Problem Solving may be a good fit for your company.
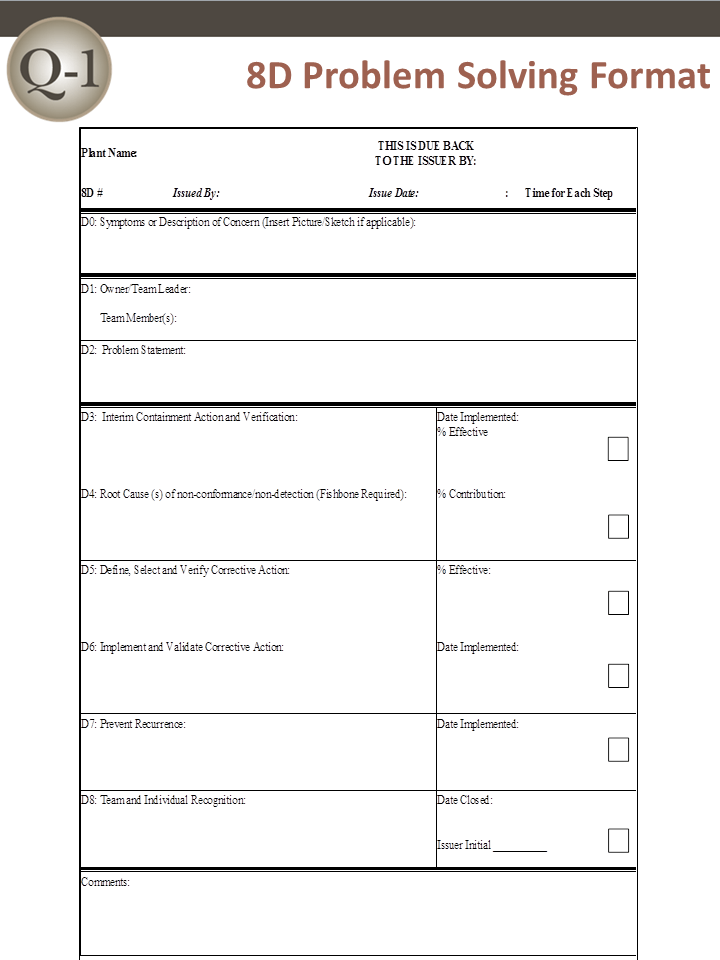
Why Apply Eight Disciplines of Problem Solving (8D)
The 8D methodology is so popular in part because it offers your engineering team a consistent, easy-to-learn and thorough approach to solving whatever problems might arise at various stages in your production process. When properly applied, you can expect the following benefits:
- Improved team oriented problem solving skills rather than reliance on the individual
- Increased familiarity with a structure for problem solving
- Creation and expansion of a database of past failures and lessons learned to prevent problems in the future
- Better understanding of how to use basic statistical tools required for problem solving
- Improved effectiveness and efficiency at problem solving
- A practical understanding of Root Cause Analysis (RCA)
- Problem solving effort may be adopted into the processes and methods of the organization
- Improved skills for implementing corrective action
- Better ability to identify necessary systemic changes and subsequent inputs for change
- More candid and open communication in problem solving discussion, increasing effectiveness
- An improvement in management’s understanding of problems and problem resolution
8D was created to represent the best practices in problem solving. When performed correctly, this methodology not only improves the Quality and Reliability of your products but also prepares your engineering team for future problems.
When to Apply Eight Disciplines of Problem Solving (8D)
The 8D problem solving process is typically required when:
- Safety or Regulatory issues has been discovered
- Customer complaints are received
- Warranty Concerns have indicated greater-than-expected failure rates
- Internal rejects, waste, scrap, poor performance or test failures are present at unacceptable levels
How to Apply Eight Disciplines of Problem Solving (8D)
The 8D process alternates inductive and deductive problem solving tools to relentlessly move forward toward a solution. The Quality-One approach uses a core team of three individuals for inductive activities with data driven tools and then a larger Subject Matter Expert (SME) group for the deductive activities through brainstorming, data-gathering and experimentation.
D0: Prepare and Plan for the 8D
Proper planning will always translate to a better start. Thus, before 8D analysis begins, it is always a good idea to ask an expert first for their impressions. After receiving feedback, the following criterion should be applied prior to forming a team:
Collect information on the symptoms
Use a Symptoms Checklist to ask the correct questions
Identify the need for an Emergency Response Action (ERA), which protects the customer from further exposure to the undesired symptoms
D1: Form a Team
A Cross Functional Team (CFT) is made up of members from many disciplines. Quality-One takes this principle one step further by having two levels of CFT:
- The Core Team Structure should involve three people on the respective subjects: product, process and data
- Additional Subject Matter Experts are brought in at various times to assist with brainstorming, data collection and analysis
Teams require proper preparation. Setting the ground rules is paramount. Implementation of disciplines like checklists, forms and techniques will ensure steady progress. 8D must always have two key members: a Leader and a Champion / Sponsor:
- The Leader is the person who knows the 8D process and can lead the team through it (although not always the most knowledgeable about the problem being studied)
- The Champion or Sponsor is the one person who can affect change by agreeing with the findings and can provide final approval on such changes
D2: Describe the Problem
The 8D method’s initial focus is to properly describe the problem utilizing the known data and placing it into specific categories for future comparisons. The “Is” data supports the facts whereas the “Is Not” data does not. As the “Is Not” data is collected, many possible reasons for failure are able to be eliminated. This approach utilizes the following tools:
- Problem Statement
- Affinity Diagram (Deductive tool)
- Fishbone/Ishikawa Diagram (Deductive tool)
- Problem Description
D3: Interim Containment Action
In the interim, before the permanent corrective action has been determined, an action to protect the customer can be taken. The Interim Containment Action (ICA) is temporary and is typically removed after the Permanent Correct Action (PCA) is taken.
- Verification of effectiveness of the ICA is always recommended to prevent any additional customer dissatisfaction calls
D4: Root Cause Analysis (RCA) and Escape Point
The root cause must be identified to take permanent action to eliminate it. The root cause definition requires that it can be turned on or off, at will. Activities in D4 include:
- Comparative Analysis listing differences and changes between “Is” and “Is Not”
- Development of Root Cause Theories based on remaining items
- Verification of the Root Cause through data collection
- Review Process Flow Diagram for location of the root cause
- Determine Escape Point, which is the closest point in the process where the root cause could have been found but was not
D5: Permanent Corrective Action (PCA)
The PCA is directed toward the root cause and removes / changes the conditions of the product or process that was responsible for the problem. Activities in D5 include:
- Establish the Acceptance Criteria which include Mandatory Requirements and Wants
- Perform a Risk Assessment / Failure Mode and Effects Analysis (FMEA) on the PCA choices
- Based on risk assessment, make a balanced choice for PCA
- Select control-point improvement for the Escape Point
- Verification of Effectiveness for both the PCA and the Escape Point are required
D6: Implement and Validate the Permanent Corrective Action
To successfully implement a permanent change, proper planning is essential. A project plan should encompass: communication, steps to complete, measurement of success and lessons learned. Activities in D6 include:
- Develop Project Plan for Implementation
- Communicate the plan to all stakeholders
- Validation of improvements using measurement
D7: Prevent Recurrence
D7 affords the opportunity to preserve and share the knowledge, preventing problems on similar products, processes, locations or families. Updating documents and procedures / work instructions are expected at this step to improve future use. Activities in D7 include:
- Review Similar Products and Processes for problem prevention
- Develop / Update Procedures and Work Instructions for Systems Prevention
- Capture Standard Work / Practice and reuse
- Assure FMEA updates have been completed
- Assure Control Plans have been updated
D8: Closure and Team Celebration
Teams require feedback to allow for satisfactory closure. Recognizing both team and individual efforts and allowing the team to see the previous and new state solidifies the value of the 8D process. Activities in D8 include:
- Archive the 8D Documents for future reference
- Document Lessons Learned on how to make problem solving better
- Before and After Comparison of issue
- Celebrate Successful Completion
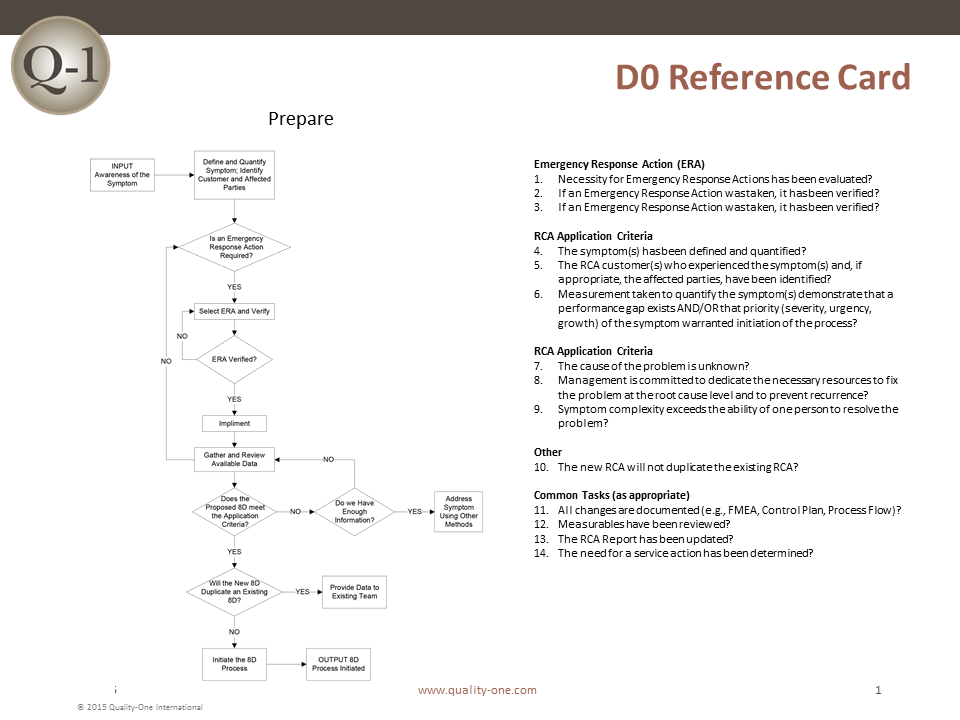
8D and Root Cause Analysis (RCA)
The 8D process has Root Cause Analysis (RCA) imbedded within it. All problem solving techniques include RCA within their structure. The steps and techniques within 8D which correspond to Root Cause Analysis are as follows:
- Problem Symptom is quantified and converted to “Object and Defect”
- Problem Symptom is converted to Problem Statement using Repeated Whys
- Possible and Potential Causes are collected using deductive tools (i.e. Fishbone or Affinity Diagram)
- Problem Statement is converted into Problem Description using Is / Is Not
- Problem Description reduces the number of items on the deductive tool (from step 3)
- Comparative Analysis between the Is and Is Not items (note changes and time)
- Root Cause theories are developed from remaining possible causes on deductive tool and coupled with changes from Is / Is Not
- Compare theories with current data and develop experiments for Root Cause Verification
- Test and confirm the Root Causes
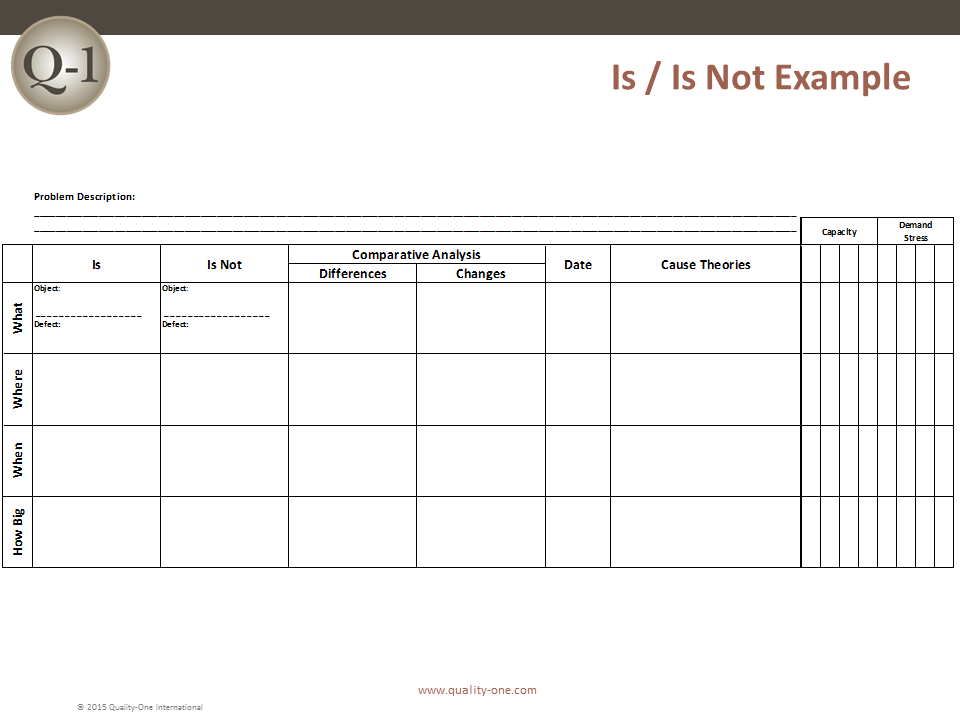
Example: Multiple Why Technique
The Multiple / Repeated Why (Similar to 5 Why) is an inductive tool, which means facts are required to proceed to a more detailed level. The steps required to determine problem statement are:
- Problem Symptom is defined as an Object and Defect i.e. “Passenger Injury”
- Why? In every case “SUV’s Roll Over”
- Why? In every case, it was preceded by a “Blown Tire”
- Why? Many explanations may be applied, therefore the team cannot continue with another repeated why past “Blown Tire”
- Therefore, the Problem Statement is “Blown Tire”
- Why? Low (Air) Pressure, Tire Defect (Degradation of an Interface) and High (Ambient) Temperature
- Counter measures assigned to low pressure and tire defect
This example uses only 4 of the 5 Whys to determine the root causes without going further into the systemic reasons that supported the failure. The Repeated Why is one way to depict this failure chain. Fault Tree Analysis (FTA) could also be used.
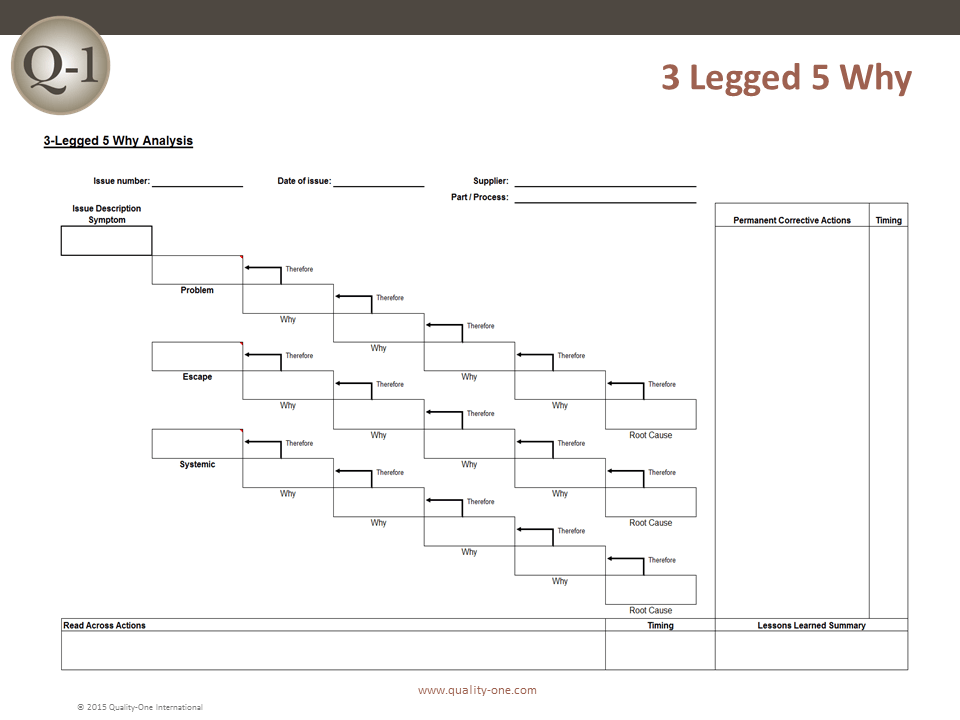
Learn More About Eight Disciplines of Problem Solving (8D)
Quality-One offers Quality and Reliability Support for Product and Process Development through Consulting, Training and Project Support. Quality-One provides Knowledge, Guidance and Direction in Quality and Reliability activities, tailored to your unique wants, needs and desires. Let us help you Discover the Value of 8D Consulting , 8D Training or 8D Project Support .
Contact Us | Discover the Value!
(248) 280-4800 | [email protected]
Remember Me
- Don't have an account? Register
- Lost your password? Click here
- Already have an account? Log in

- Guide: 8D Problem Solving
Daniel Croft
Daniel Croft is an experienced continuous improvement manager with a Lean Six Sigma Black Belt and a Bachelor's degree in Business Management. With more than ten years of experience applying his skills across various industries, Daniel specializes in optimizing processes and improving efficiency. His approach combines practical experience with a deep understanding of business fundamentals to drive meaningful change.
- Last Updated: June 13, 2023
- Learn Lean Sigma
8D Problem Solving is a systematic and structured approach used to solve business related problems. It names has been given by the fact there are 8 steps or 8 disciplines that are followed to identify, correct and eliminate recurring problems.
8D Problem Solving is regarded as robust methodology that has proven its worth across multiple industries and manufacturing in particular. The methodology was Initially developed within the automotive industry, it has since been widely adopted in manufacturing, logistics and health care to name a few. The 8D approach goes beyond helping team just identify the root cause of problem but also provides a structured approach for implementing and verifying corrective actions.
Table of Contents
What is 8d problem solving.
The 8D Problem-Solving methodology was developed in the late 1980s by Ford Motor Company. The term “8D” stands for “Eight Disciplines,” which represent the eight critical steps in problem-solving.
Initially it was only intended to resolve issues within the automotive manufacturing process. However, over the year since then the methodology has gained universal acceptance and is now applied across various sectors. The 8D approach was heavily influenced by quality management systems like Total Quality Management (TQM) and methodologies like Six Sigma and forms a key part of quality roles and Six sigma qualifications.
8D is also encourages collaborative team based approach to addressing issues in the workplace This methodology was purposefully designed to be a cross-functional effort, ensuring to bring together expertise from different departments or disciplines to comprehensively address an issue by looking at it from all point of view. Here are the key components:
Preparation : Before diving into problem-solving, the team gathers all necessary resources and tools.
Team Establishment : A cross-functional team is assembled, each member having a specific role and responsibility.
Problem Description : The issue at hand is clearly defined to ensure everyone has a shared understanding.
Interim Actions : Short-term solutions are implemented to contain the problem and prevent further damage.
Root Cause Analysis : Various tools and methods are used to identify the real cause of the problem.
Permanent Corrective Actions : Long-term solutions are selected and verified to eliminate the root cause.
Implementation : The long-term solutions are implemented across the board, including necessary changes to policies and procedures.
Prevent Recurrence : Measures are taken to ensure that the problem does not occur again.
Team Recognition : The team is congratulated and acknowledged for their efforts.

How does 8D Compare to over Problem-Solving Methods?
Between quality management systems and lean six sigma there are several problem-solving methodologies such as PDCA (Plan-Do-Check-Act), DMAIC (Define-Measure-Analyze-Improve-Control), and A3 . However the combination of the 8D steps results in a comprehensive frame work that is:
Team-Oriented : Unlike some methodologies that can be carried out by individuals, 8D strongly emphasizes team collaboration as a core principle as seen in steps D1 and D8.
Structured Framework : 8D provides a very detailed, step-by-step guide for solving complex problems, by breaking it down in to logical steps making it easier to manage and track progress.
Broad Applicability : While some methodologies like DMAIC are closely tied to Six Sigma, 8D can be applied in various contexts without being tied to a particular quality management system.
Focus on Prevention : 8D not only aims to solve the problem but also focuses on implementing changes to prevent its recurrence, making it a complete approach to problem solving.
The 8 Disciplines Explained
D0: prepare for the process.
Before you start 8D you should prepare for the 8D process. This phase sets the foundation for the entire methodology, ensuring that the team is able to tackle the problem effectively. Therefore, effective preparation helps in avoiding unnecessary delays and ensures that you’re not solving the wrong problem.
Within the initial preparation step you should also the time to think about what knowledge, expertise and experience you need within the team. Cross-functional teams are important, as they bring alternative perspectives and skills to the table rather than everyone looking at the problem from one point of view. Make sure you consider expertise, availability, and interest when selecting team members.

D1: Establish the Team
In D1 you should establish the team by clearly defining the roles and responsibilities for each team member. This includes assigning a team leader, subject matter experts, and roles for data collection , analysis, and communication this helps to provide the team members clarity on how they will be involved and contribute to the success of the problems solving activity.
Team Composition
Once roles are defined, where possible ensure that the team is balanced in terms of skills and expertise. A well-rounded team will be more effective in tackling various aspects of the problem.
Communication
Establish clear methods communication, both within the team and with external stakeholders. Such as deciding on regular meeting schedules that everyone can attend, reporting formats, and tools for collaboration.
D2: Describe the Problem
In D2 it is time to create a well formed problem statement. This step is key as it provides a foundation for understanding the problem which will lead to generally more successful problem-solving. It ensures that everyone clearly understands what needs to be addressed, setting the scope for the entire process. Ensure that the problem is clearly understood by everyone in the team at this stage to prevent confusion later on in the process.
5W1H Method of creating a Problem Definition
Use data gathering techniques such as observations, interviews, and document reviews can help to precisely identify the problem. A useful tool to use at this stage could be the 5W1H Problem definition method.
You can find out more about this method with our 5W1H guide .

Problem Definition – is / is not template
When creating your problem definition ensure to be specific, measurable, and unambiguous when stating the problem. You should avoid generalities and ensure that the problem statement is understandable to someone unfamiliar with the issue. If you are new to this process it may be helpful to give the statement to someone unfamiliar to the process and see if they understand it or if they have questions. You can then clarify any questions by adjusting the problem description to improve the claity.
D3: Implement and Verify Interim Actions
In D3 while the team is investigating the root cause, interim actions are must be implement to contain the problem and minimize its impact. This is particularly important in critical situations affecting safety, compliance, or customer satisfaction.
In this step you should identify, plan, and execute short-term fixes that can quickly contain the problem. This could include quarantining the product to ensure it is not sent out to the customer or even pausing production lines that continue to product defects. Ensure these actions are documented for future reference.
Use metrics and KPIs to gauge the effectiveness of the interim actions. Make adjustments as necessary.
D4: Root Cause Analysis
D4 is where you start to understand what is causing the issue by identifying the underlying reason for the problem. The objective is to find the root cause, not just the symptoms.

At this stage there are a range of quality and lean six sigma tools that can be used to conduct root cause analysis , which can include the Fishbone Diagram for structured brainstorming and the 5 Whys technique for causal chain analysis.
We have a range of guides on all of these techniques for you to use.

Once identified, it is important validate the root cause through experimentation or additional data analysis to ensure it’s the actual cause and not a symptom, this can often be an overlook critical step in the root cause process.
D5: Choose and Verify Permanent Corrective Actions
In D5 you need to choose what actions to be taken to prevent the problem reoccurring and any solutions implemented should be verified that the actions correct the problem this can involve trial runs, further data collection and inspections of product or services being produced.
You should also consider factors like cost, impact, and feasibility when choosing a permanent corrective action and should also conduct a risk assessment to evaluate potential negative outcomes of the actions taken
An implementation or action plan is often useful to document at this stage to detail the steps for implementation, assign responsibilities, and set timelines.
D6: Implement Permanent Corrective Actions
Once verified, implement the corrective actions across all relevant departments or processes. This can involved documenting the new process and training out to all stakeholders involved to ensure the new process is followed and that the stakeholders understand the reason for the change.
At this point you should continue to regularly monitor the situation to ensure the corrective actions are sustained and effective, this could be for a period of 30, 60 or 90 days after the problem was resolved to ensure the new process has become a sustained and issues do not reoccur.
D7: Prevent Recurrence
In D7 to prevent recurrent you should review and update organizational policies or standard operating procedures (SOPs) to prevent a recurrence of the problem and document the new standard process
It is important to conduct regular reviews to continuously monitor the process and ensure procedures are being followed but also to identify further opportunities for process improvement.
D8: Congratulate the Team
The final step D8, after the hard work and successful problem resolution, it is important to acknowledging and congratulating the team is vital for morale and future engagement. With the recognition of a successful 8D Problem-solving activity complete you are more likely to encourage future participation as the method gets a reputation as being useful and successful at solving problems.
Whether it’s a team lunch, certificates of achievement, or simply a public acknowledgment, celebrate the success in a way that resonates with your team.
Finally it is always important to conduct a lessons-learned session and document the insights gained during the process for future reference. This can be used as a future point of reference for problem solving activities.
Mastering the art of problem-solving is crucial in today’s complex and fast-paced environment. The 8D Problem-Solving methodology offers a structured, team-based approach to tackling challenges that can arise in any sector, be it manufacturing, public services, or logistics. This guide has walked you through each of the eight disciplines, offering best practices and highlighting common pitfalls to avoid. We’ve also enriched your understanding through real-world case studies that demonstrate the methodology’s versatility and effectiveness. Remember, the strength of 8D lies not just in identifying and resolving problems, but also in preventing their recurrence through systemic improvements. By adhering to the principles and steps outlined in this guide, you’re well on your way to becoming an adept problem solver, capable of driving continuous improvement in your organization.
- Zarghami, A. and Benbow, D.W., 2017. Introduction to 8D problem solving . Quality Press.
- Camarillo, A., Ríos, J. and Althoff, K.D., 2017. CBR and PLM applied to diagnosis and technical support during problem solving in the Continuous Improvement Process of manufacturing plants . Procedia Manufacturing , 13 , pp.987-994.
Q: What is 8D problem solving?
A: 8D problem solving is a systematic approach used to address and resolve complex problems. It is widely utilized in various industries to identify the root causes of issues, develop effective solutions, and prevent their recurrence.
Q: Why is it called "8D" problem solving?
A: The name “8D” refers to the eight disciplines or steps involved in the problem-solving process. Each discipline represents a specific stage in the methodology, allowing for a structured and comprehensive approach to problem resolution.
Q: What are the eight disciplines (8D) in problem solving?
A: The eight disciplines in problem solving, often abbreviated as 8D, are as follows:
- D1: Form a team
- D2: Define the problem
- D3: Implement containment actions
- D4: Determine the root cause
- D5: Develop and implement corrective actions
- D6: Validate the effectiveness of corrective actions
- D7: Prevent recurrence
- D8: Congratulate the team
Q: What is the purpose of forming a team in the 8D problem-solving process?
A: Forming a team at the beginning of the 8D problem-solving process helps ensure that the right individuals with the necessary expertise are involved in addressing the problem. The team collaboratively works towards understanding the issue, analyzing data, and developing effective solutions.
Q: How is the root cause determined in the 8D problem-solving process?
A: Determining the root cause (D4) involves conducting a thorough analysis of the problem. Various tools and techniques, such as cause-and-effect diagrams, 5 Whys, and data analysis, are employed to identify the underlying factors contributing to the problem.
Q: Can the 8D problem-solving methodology be applied to any type of problem?
A: Yes, the 8D problem-solving methodology is a versatile approach that can be applied to various types of problems across different industries. It provides a structured framework for problem resolution and can be tailored to suit the specific needs and requirements of different situations.

Daniel Croft is a seasoned continuous improvement manager with a Black Belt in Lean Six Sigma. With over 10 years of real-world application experience across diverse sectors, Daniel has a passion for optimizing processes and fostering a culture of efficiency. He's not just a practitioner but also an avid learner, constantly seeking to expand his knowledge. Outside of his professional life, Daniel has a keen Investing, statistics and knowledge-sharing, which led him to create the website learnleansigma.com, a platform dedicated to Lean Six Sigma and process improvement insights.
Download Template

Free Lean Six Sigma Templates
Improve your Lean Six Sigma projects with our free templates. They're designed to make implementation and management easier, helping you achieve better results.

Other Guides
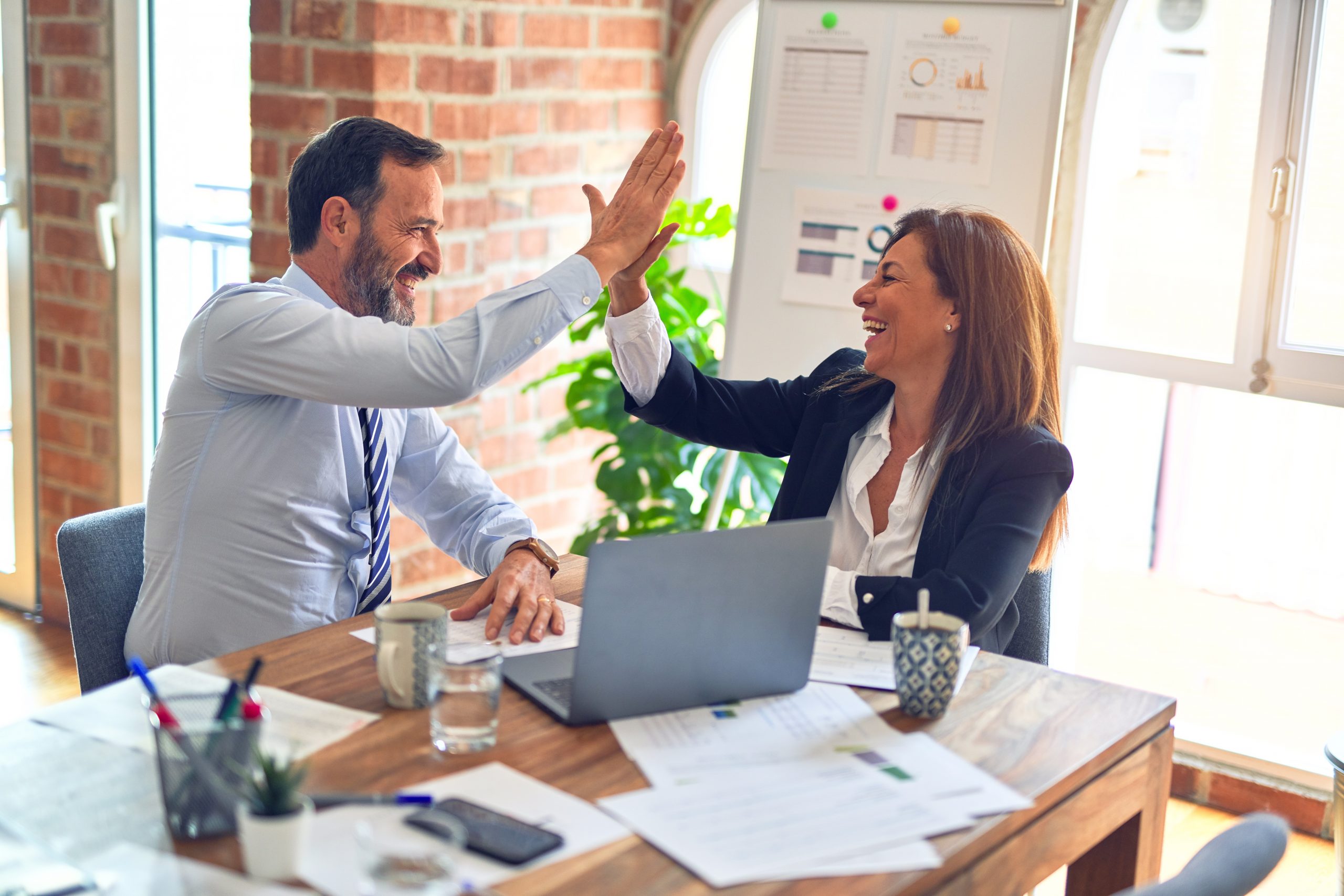
Published: November 7, 2018 by Ken Feldman
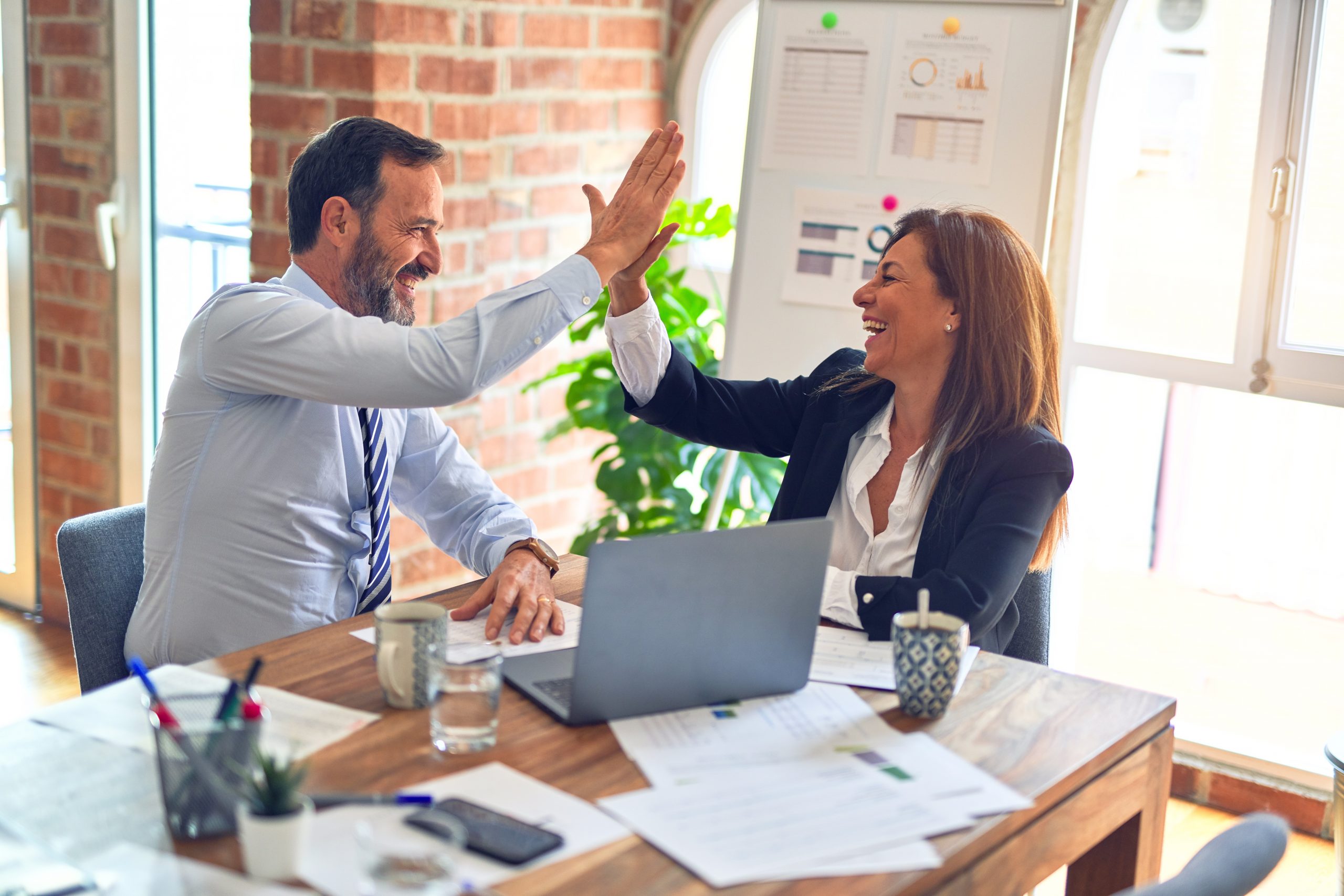
It’s easy to feel overwhelmed by the number of different approaches to problem solving. Some of the most common ones are PDCA , DMAIC , A3, 6S , Agile , 5 Whys , fishbone diagrams , and others. In this article, we’ll look at the 8D process for problem-solving and process improvement. We will present the benefits of 8D along with some best practices and an example of how to use it. This will provide you with some practical applications for use in your own organization.
Overview: What is the 8D process?
The history of 8D is somewhat controversial. While everyone seems to agree that the popularity of the approach can be credited to Ford Motor company, the basis of the process is a little less clear. Senior leadership at Ford saw the need for the Powertrain division to have a methodology where teams could work on recurring problems.
In 1986, work began to develop a manual and training course that would create a new approach to solving engineering design and manufacturing problems. The title of this manual was Team Oriented Problem Solving (TOPS), and it was first published in 1987. But where did the original idea come from?
Many give credit to the U.S. War Production Board, which developed a simple, four-step approach in 1945 for improving job methods. Here’s what they looked like.
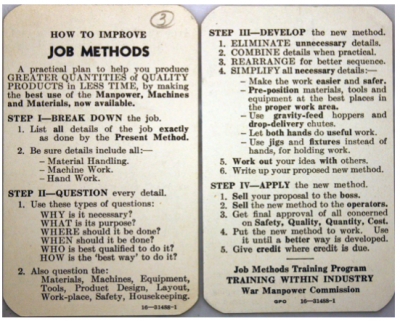
Image source: allaboutlean.com .
In reality, the 8D process is officially known as the Eight Disciplines of Problem-Solving. To make things a little more confusing, it’s really nine steps. While originally developed as 8 steps or disciplines, it was subsequently revised to include a step zero, which was to plan and prepare for solving the problem.
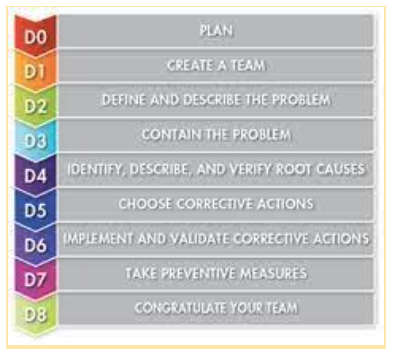
Image source: ASQ.org .
Let’s provide a little more detail for each step.
- D0 — Plan: Collect information and data on the problem symptoms. Decide what preparations will be needed to complete the 8D process. Decide whether you will need an Emergency Response Plan to minimize or mitigate the immediate impact of your problem on the customer.
- D1 — Create a team: Put together a cross-functional team consisting of a core group plus a selection of subject matter experts ( SMEs ). Be sure to provide everything the team will need to be successful, including any training needed to properly execute the process.
- D2 — Define and describe the problem: Using relevant data, describe the problem in as detail as possible. Be sure to focus on your problem at this point, not your solution.
- D3 — Contain the problem: Protect your customer by creating containment actions to prevent any further negative impact to them.
- D4 — Identify, describe, and verify root causes: You can use a multitude of tools such as the 5 Whys, fishbone diagrams, brainstorming , and others to identify potential root causes. Use data to validate your root causes.
- D5 — Choose corrective actions: Select the most appropriate actions to resolve and eliminate the root causes of your problem.
- D6 — Implement and validate your corrective actions: Implement your recommended solutions and corrective actions, and continue to monitor to assure yourself that they actually solved your problem.
- D7 — Take preventative measures: Revise your systems to proactively try to prevent these and similar problems from arising in the future.
- D8 — Congratulate your team: Communicate the work of the team and celebrate their efforts.
3 benefits of the 8D process
It goes without saying that removing problems, improving your process, and preventing future problems will provide many benefits to your organization. Here are a few.
1. Simple and effective
The 8D process has been compared to the PDCA model. Like PDCA, 8D is structured, organized, and simple in concept.
2. Drives you to the root cause
By following the sequential steps, this process should lead you to the elimination of your problem and prevent it from arising again.
3. Team approach
The use of a cross-functional team composed of a core group of people working in the problem area as well as subject matter experts contributing on an as needed basis will give you the synergy of combined knowledge and experience that should lead you to a solution.
Why is the 8D process important to understand?
While simple in concept, there are a number of things you should understand that will make this process both effective and efficient.
Elimination of the root cause
If you understand and follow the 8D steps, you will be able to eliminate — or at least mitigate — the negative impact of your problem.
Discipline
The 8D steps are sequential and build on each other. If you have the discipline to stay on track, you will optimize the use of the 8D process.
Problem-solving tools
8D is a process and methodology. You will need to understand the purpose of each step so you can apply the proper problem-solving tools in each step.
An industry example of 8D
A consumer product company located in Mexico City was experiencing an increase in its delivery trucks returning without having made product deliveries to its customers. There did not seem to be an obvious reason or solution, so the president of the company chartered a team to look into the problem. He assigned the company’s Lean Six Sigma Master Black Belt to put together and facilitate a team and chose to use the 8D problem-solving methodology.
He followed the process by first having a planning and preparation meeting to lay out the plan for analyzing the problem. He suggested that some of the delivery supervisors go out into the field to see if they can observe any unusual conditions. They also collected some data and recorded their observations.
A vigorous brainstorming session ensued in which the team listed all the possible reasons the problem was occuring. These potential root causes were validated by the data that was collected and the observations of the supervisors. They discovered the trucks were coming back without delivering all of the product because the customers didn’t have enough money to pay for the product. These were very small customers who had to pay cash on delivery.
The question then became: Why didn’t they have enough money? The next root cause was that the trucks were arriving later in the day, after the customer had already paid for most of their other deliveries and thus had no money left. Why were the trucks arriving so late? Because they got stuck in traffic because they left the yard too late. Why were they leaving so late? Because they were loading the trucks and doing the paperwork in the morning.
Eventually, the team arrived at a solution that had the trucks loaded, prepped, and ready to go when the drivers arrived early in the morning. The result was a dramatic reduction in returned goods and a significant increase in cash flow. The president was confident that the use of the 8D process got them to the right solution quickly and efficiently.
3 best practices when thinking about the 8D process
Like most of the other problem-solving approaches, there are some recommended practices that will help you and your team be successful. Here are a few that will help you stay on track.
1. Pick the best team that you can
Don’t seek volunteers, but hand-select the best team members that are available. It will be their knowledge and expertise that will make the team successful. Likewise for the team facilitator or leader.
2. Take your time
Don’t rush to solutions or what you think is the root cause of your problem. Thoroughly explore your problem so that the solutions that you eventually come up with will resolve the problem and prevent future occurrences. Think creatively.
3. Be specific about what your problem is
Use data to help you understand your problem. Don’t just rely on anecdotal stories or assumptions to decide the root cause of your problem.
Frequently Asked Questions (FAQ) about 8D
1. when should i use the 8d process.
Use this process when you’re trying to solve for safety or regulatory issues, increasing customer complaints, warranty costs (which indicate greater-than-expected failure rates), internal rejects, waste, scrap, and poor performance or test results.
2. Can the 8D process be used in non-manufacturing processes?
Yes. While the 8D process was developed in the manufacturing function of Ford Motor Company, it can just as easily be applied in any type of process or function where you are experiencing problems.
3. What is the difference between the 8D and 5D process?
For a less complex problem, you may decide to use a 5D process. This simplified process will have you form a team, identify your problem, implement containment actions, identify the root cause, and implement corrective actions to eliminate the problem.
So, what is the 8D process?
The 8D process, also known as the Eight Disciplines of Problem Solving, is a method developed at Ford Motor Company used to resolve problems. It is focused on product and process improvement.
The purpose of 8D is to identify, correct, and eliminate recurring problems. It establishes a permanent corrective action based on a problem analysis and determination of the root causes. Although it was originally comprised of eight stages, or “disciplines,” it was later revised to nine to include a planning and preparation stage.
About the Author
Ken Feldman
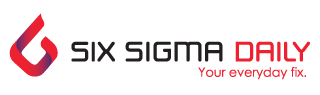
No Problem at All: Diagnosing the 8 Disciplines of Problem Solving
When problems appear, discipline is vital. Disciplines also help, and the eight disciplines of problem-solving (also referred to as the 8Ds) offer a proven process improvement structure that provides a framework for identifying root causes, eliminating them, and preventing reoccurrence.
The enduring popularity of the 8Ds attests to their power. It’s a tried and tested format on which you can rely — no matter what has gone wrong elsewhere.
How the 8 Disciplines of Problem Solving Evolved
In the 1980s, the Ford Motor Company published its manual, Team Oriented Problem Solving (TOPS), the first articulation of the 8Ds. Eventually, it refined the original procedures into the current 8Ds.
Ford also added an initial planning stage (D0). There are now nine steps of 8D. Fortunately, the actual process is more intuitive than its numbering.
Initially developed for the auto industry, the 8D problem-solving process has been successfully adopted across multiple industries, including healthcare, government, finance, retail, and manufacturing.
How 8D Can Help You
The benefits of 8D include:
- More effective and efficient problem solving
- A team-oriented approach
- Open communication within the team and with management
- A framework for corrective action that allows for systemic changes and continual improvement
- Intense examination of the control systems that permitted the problem
- Easy integration with process-improvement tools
You can apply the 8Ds whenever processes break down. Engineers and manufacturers often turn to them when they receive customer complaints or discover safety or regulatory issues. They also come in handy when a system’s amount of waste or a product’s failure rates hit problematic levels.
What Are the 8 Disciplines of Problem Solving?
The 8Ds provide a methodical approach to problem-solving. The sequence of nine steps will take you from the initial discovery of an issue to your celebratory toast when you fix it.
The designers added a planning stage to the original 8D methodology. This stage focuses on the one following, bringing clarity and intention to the project.
Summarize the Issue
You’ll describe it in greater detail later, but you’ve started this process because you identified a problem. What is it?
Collect the information on the problem’s symptoms and identify apparent gaps or additional needs. You might also want to consult a subject matter expert and get their input on your issue. They may be able to save you time further down the road.
Identify and Take Emergency Responses
If your house is on fire, put it out. Then you can take a hard look at the wiring.
As soon as you’ve identified a problem, take any necessary action to limit or contain a dangerous situation. Don’t overreact or prematurely make uncertain changes. Just exercise common sense.
Plan for the 8Ds
Your actual project plan will change as you make discoveries. This document is simply an outline of the project’s space within your company. It’s a theory about the necessary investment of time and other scarce resources.
Identify the resources you have and need. Sketch out schedules and note the variables that will affect them.
D1: Form Your Team
Create a team to tackle the problem.
Add the Right People
The group should be small enough to be efficient but large enough to cover all necessary process/product knowledge and technical skills. Some recommend a team of about five members. Make sure this team has the necessary authority and allotted time they need.
Identify both a team leader and a project champion in management (if necessary). Establish guidelines for harmonious group work.
This is also the time to perform team-building exercises if you want.
Review the Problem
Get team members up to date and fully on board. Review the initial brief for the project and discuss scope and priorities. Team members should all have the opportunity to voice initial concerns and complications.
D2: Define and Describe the Problem
Outline the problem in as much detail as possible, using quantifiable terms. Clarify both what the problem is and is not . The latter will help you begin eliminating potential reasons for failure.
As you define the problem, you should also understand whether your situation is “something changed” or “never been there.” Has something gone off course, or has a new variable or context appeared?
Identify Critical Process Steps
Create a flowchart for the flawed process, and indicate which steps are critical to the problem at hand. In this step, you will start to approach root cause analysis, though you won’t isolate and verify a root cause until D4.
Outline Project Plan
At this point, you will develop a more detailed, high-level project plan that includes milestones, objectives, and a fuller schedule.
D3: Contain the Problem
D3 focuses on interim containment action rather than permanent and preventive action.
This step isn’t about emergency action, which should have been taken already. You’ve put out the house fire, but you still need to lodge your tenants elsewhere while your electricians go through the place.
Find a Temporary Solution
Take whatever action is necessary for the satisfaction of your customers or the effectiveness of your organization. You may need to develop workarounds, issue (non-emergent) recalls, or establish a resource for affected customers.
The ideal interim solution is:
- Inexpensive
- Simple and quick to implement
- Easy to reverse
- Validated by customer or employee feedback
When you’ve realized your long-term solution, you can do away with interim measures.
D4: Find the Root Cause
Root cause analysis is at the heart of most problem-solving tools and processes. It’s time to dig deep into the problem and find out what’s gumming up the works.
Develop Root Cause Theories
You’ll complete the process of elimination that you began when defining the problem. Refer to your flowchart. What could be causing the problem?
Use root cause analysis tools like the Fishbone Diagram and the five whys . Find all possible factors that could contribute to the breakdown.
Test and Review Causes
Test each of your potential causes, collecting data until you can rule out all but one.
Identify Escape Point
In addition to finding the root cause, you need to figure out what part of the control system allowed it to escape detection and be contained. Find the point where someone or something should have caught the issue. That’s the escape point.
Correctly identifying and solving escape-point issues is essential to preventing future problems.
D5: Identify and Test Solutions
You’ve found the problem and its escape point. Of course, that’s only half the battle. Now you need to solve them — permanently and completely.
Define what “solved” looks like. Is there a threshold of minimum acceptability?
Develop Solutions
Give your team the time to consider potential approaches to both the root cause and escape point issues. The first idea may not be the best, and brainstorming tools such as affinity diagrams can help.
Test Solutions
Make sure they work. You should also perform risk and cost analysis for any final contenders.
D6: Choose Solutions and Put Them Into Practice
Choose your best solutions, outline your implementation plan, and move forward with it. Both management and team members should sign off on the solution.
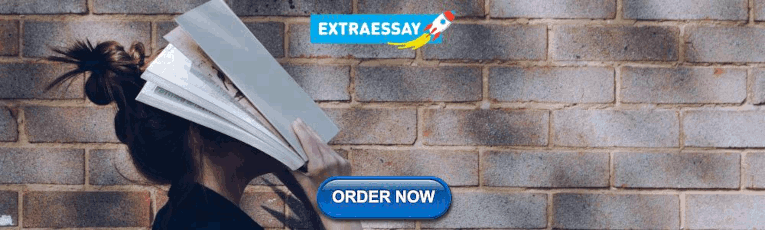
Implement, Validate, Monitor
After putting your plan into practice, check with customers and stakeholders to ensure that their concerns are fully addressed. Continue to monitor the situation to make sure the solution is sustainable and effective. You’ll also keep an eye out for any unintended consequences.
Move From the Interim to the Permanent Solution
Once you have the permanent solution up and running, you can end interim measures.
D7: Prevent Recurrence
By addressing the escape point and continuing to monitor the situation, you’re doing a fair amount to prevent an exact recurrence. But make sure that all contributing systems have been updated to reflect new input.
You should also preserve all documentation so that future teams have it as a resource for similar problems. Even better, prevent those similar problems.
Improve and Standardize Systems Across the Organization
Are there analogous areas of the organization that could use review? Are their policies and procedures in line with those you’ve developed?
Conduct an audit of operational procedures, management processes, and training manuals.
D8: Celebrate and Recognize Contributions
You’re not done quite yet. Recognition and validation are vital for a healthy organization, so take time to acknowledge individual contributions and the team’s accomplishments.
Perform a Final Review
Look at team output with a focus on before-and-after results. Finalize documentation and add it to the company library.
You should also take the time to reflect on your 8D experience. Explore trouble spots or areas that could use clarification for the next problem-solving team.
Reward your team appropriately. This can include anything from company-wide emails to dinner to bonuses. Even a personal email goes a long way toward making people feel like valued members of a community.
Then Do It All Again
When you make the eight disciplines of problem-solving part of your organizational DNA, you prepare to solve all kinds of problems in a streamlined, effective way.
The 8Ds integrate seamlessly with the Six Sigma methodology and make a great addition to your toolkit.
- Product overview
- All features
- App integrations
CAPABILITIES
- project icon Project management
- Project views
- Custom fields
- Status updates
- goal icon Goals and reporting
- Reporting dashboards
- workflow icon Workflows and automation
- portfolio icon Resource management
- Time tracking
- my-task icon Admin and security
- Admin console
- asana-intelligence icon Asana Intelligence
- list icon Personal
- premium icon Starter
- briefcase icon Advanced
- Goal management
- Organizational planning
- Campaign management
- Creative production
- Content calendars
- Marketing strategic planning
- Resource planning
- Project intake
- Product launches
- Employee onboarding
- View all uses arrow-right icon
- Project plans
- Team goals & objectives
- Team continuity
- Meeting agenda
- View all templates arrow-right icon
- Work management resources Discover best practices, watch webinars, get insights
- What's new Learn about the latest and greatest from Asana
- Customer stories See how the world's best organizations drive work innovation with Asana
- Help Center Get lots of tips, tricks, and advice to get the most from Asana
- Asana Academy Sign up for interactive courses and webinars to learn Asana
- Developers Learn more about building apps on the Asana platform
- Community programs Connect with and learn from Asana customers around the world
- Events Find out about upcoming events near you
- Partners Learn more about our partner programs
- Support Need help? Contact the Asana support team
- Asana for nonprofits Get more information on our nonprofit discount program, and apply.
Featured Reads
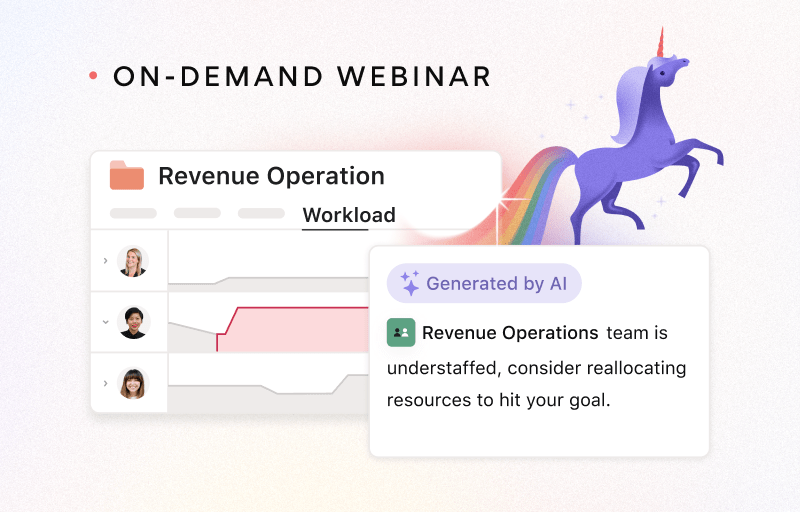
- Project management |
- What is 8D? A template for efficient pr ...
What is 8D? A template for efficient problem-solving
How you respond when problems arise is one of the most defining qualities of a manager. Luckily, there are tools you can use to master problem-solving. The 8D method of problem-solving combines teamwork and basic statistics to help you reach a logical solution and prevent new issues from arising.
You’ve spent months overseeing the development of your company's newest project. From initiation, planning, and execution, you’re confident this may be your best work yet.
Until the feedback starts rolling in.
There’s no sugar-coating it—things don’t always go as planned. But production or process issues are hardly a signal to throw in the towel. Instead, focus on honing your problem-solving skills to find a solution that keeps it from happening again.
The 8D method of problem solving emphasizes the importance of teamwork to not only solve your process woes but prevent new ones from occurring. In this guide, we’ll break down what 8D is, how to use this methodology, and the benefits it can give to you and your team. Plus, get an 8D template to make solving your issue easier.
What is 8D?
The eight disciplines (8D) method is a problem-solving approach that identifies, corrects, and eliminates recurring problems. By determining the root causes of a problem, managers can use this method to establish a permanent corrective action and prevent recurring issues.
How do you use the 8D method?
The 8D method is a proven strategy for avoiding long-term damage from recurring problems. If you’re noticing issues in your workflow or processes, then it’s a good time to give this problem-solving method a try.
To complete an 8D analysis, follow “the eight disciplines” to construct a statistical analysis of the problem and determine the best solution.
The eight disciplines of problem-solving
8D stands for the eight disciplines you will use to establish an 8D report. As you may notice, this outline starts with zero, which makes nine total disciplines. The “zero stage” was developed later as an initial planning stage.
To illustrate these steps, imagine your organization experienced a decline in team innovation and productivity this past year. Your stakeholders have noticed and want to see changes implemented within the next six months. Below, we’ll use the 8D process to uncover a morale-boosting solution.
D0: Prepare and plan
Before starting the problem-solving process, evaluate the problem you want to solve. Understanding the background of the problem will help you identify the root cause in later steps.
Collect information about how the problem has affected a process or product and what the most severe consequences may be. Planning can include:
Gathering data
Determining the prerequisites for solving the problem
Collecting feedback from others involved
If we look back at our example, you may want to figure out whether this decline in morale is organization-wide or only applies to a few departments. Consider interviewing a few employees from different departments and levels of management to gain some perspective. Next, determine what knowledge and skills you will need to solve this lapse in productivity.
D1: Form your team
Create a cross-functional team made up of people who have knowledge of the various products and workflows involved. These team members should have the skills needed to solve the problem and put corrective actions in place.
Steps in this discipline may include:
Appointing a team leader
Developing and implementing team guidelines
Determining team goals and priorities
Assigning individual roles
Arranging team-building activities
From our example, a solid team would consist of people with first-hand experience with the issues—like representatives from all departments and key people close to workshop-level work. You may also want to pull someone in from your HR department to help design and implement a solution. Most importantly, make sure the people you choose want to be involved and contribute to the solution.
D2: Identify the problem
You may have a good understanding of your problem by now, but this phase aims to break it down into clear and quantifiable terms by identifying the five W’s a and two H’s (5W2H):
Who first reported the problem?
What is the problem about?
When did it occur and how often?
Where did it occur (relating to the sector, supplier, machine, or production line involved)?
Why is solving the problem important?
How was the problem first detected?
How many parts/units/customers are affected?
Use your team’s insights to answer these questions. From our example, your team may conclude that:
Employees feel overwhelmed with their current workload.
There is no real structure or opportunity to share new ideas.
Managers have had no training for meetings or innovation settings.
Disgruntled employees know they can achieve more—and want to achieve more—even if they seem disengaged.
Once you answer these questions, record an official problem statement to describe the issue. If possible, include photos, videos, and diagrams to ensure all parties have a clear understanding of the problem. It may also help to create a flowchart of the process that includes various steps related to the problem description.
D3: Develop an interim containment plan
Much like we can expect speedy first aid after an accident, your team should take immediate actions to ensure you contain the problem—especially if the problem is related to customer safety.
An interim containment plan will provide a temporary solution to isolate the problem from customers and clients while your team works to develop a permanent corrective action. This band-aid will help keep your customers informed and safe—and your reputation intact.
Because your findings revealed workers were overworked and managers lacked training, your team suggests scheduling a few mandatory training sessions for leaders of each department covering time and stress management and combating burnout . You may also want to have a presentation outlining the topics of this training to get key managers and stakeholders interested and primed for positive upcoming changes.
D4: Verify root causes and escape points
Refer back to your findings and consult with your team about how the problem may have occurred. The root cause analysis involves mapping each potential root cause against the problem statement and its related test data. Make sure to test all potential causes—fuzzy brainstorming and sloppy analyses may cause you to overlook vital information.
In our example, focus on the “why” portion of the 5W2H. You and your team identify six root causes:
Managers have never had any training
There is a lack of trust and psychological safety
Employees don’t understand the objectives and goals
Communication is poor
Time management is poor
Employees lack confidence
In addition to identifying the root causes, try to pinpoint where you first detected the problem in the process, and why it went unnoticed. This is called the escape point, and there may be more than one.
D5: Choose permanent corrective actions
Work with your team to determine the most likely solution to remove the root cause of the problem and address the issues with the escape points. Quantitatively confirm that the selected permanent corrective action(s) (PCA) will resolve the problem for the customer.
Steps to choosing a PCA may include:
Determining if you require further expertise
Ensuring the 5W2Hs are defined correctly
Carrying out a decision analysis and risk assessment
Considering alternative measures
Collecting evidence to prove the PCA will be effective
Your team decides to roll out the training used in the interim plan to all employees, with monthly company-wide workshops on improving well-being. You also plan to implement meetings, innovation sessions, and team-coaching training for managers. Lastly, you suggest adopting software to improve communication and collaboration.
D6: Implement your corrective actions
Once all parties have agreed on a solution, the next step is to create an action plan to remove the root causes and escape points. Once the solution is in effect, you can remove your interim containment actions.
After seeing success with the training in the interim phase, your stakeholders approve all of your team’s proposed PCAs. Your representative from HR also plans to implement periodic employee wellness checks to track employee morale .
To ensure your corrective action was a success, monitor the results, customer, or employee feedback over a long period of time and take note of any negative effects. Setting up “controls” like employee wellness checks will help you validate whether your solution is working or more needs to be done.
D7: Take preventive measures
One of the main benefits of using the 8D method is the improved ability to identify necessary systematic changes to prevent future issues from occurring. Look for ways to improve your management systems, operating methods, and procedures to not only eliminate your current problem, but stop similar problems from developing later on.
Based on our example, the training your team suggested is now adopted in the new manager onboarding curriculum. Every manager now has a “meeting system” that all meetings must be guided by, and workloads and projects are managed as a team within your new collaboration software . Innovation is improving, and morale is at an all-time high!
D8: Celebrate with your team
The 8D method of problem-solving is impossible to accomplish without dedicated team members and first-class collaboration. Once notes, lessons, research, and test data are documented and saved, congratulate your teammates on a job well done! Make an effort to recognize each individual for their contribution to uncovering a successful solution.
8D report template and example
Check out our 8D report template below to help you record your findings as you navigate through the eight disciplines of problem solving. This is a formal report that can be used as a means of communication within companies, which makes for transparent problem-solving that you can apply to the entire production or process chain.
Benefits of using the 8D method
The 8D method is one of the most popular problem-solving strategies for good reason. Its strength lies in teamwork and fact-based analyses to create a culture of continuous improvement —making it one of the most effective tools for quality managers. The benefits of using the 8D method include:
Improved team-oriented problem-solving skills rather than relying on an individual to provide a solution
Increased familiarity with a problem-solving structure
A better understanding of how to use basic statistical tools for problem-solving
Open and honest communication in problem-solving discussions
Prevent future problems from occurring by identifying system weaknesses and solutions
Improved effectiveness and efficiency at problem-solving
Better collaboration = better problem solving
No matter how good a manager you are, production and process issues are inevitable. It’s how you solve them that separates the good from the great. The 8D method of problem solving allows you to not only solve the problem at hand but improve team collaboration, improve processes, and prevent future issues from arising.
Try Asana’s project management tool to break communication barriers and keep your team on track.
Related resources
What is a flowchart? Symbols and types explained
What are story points? Six easy steps to estimate work in Agile
How to choose project management software for your team
7 steps to complete a social media audit (with template)
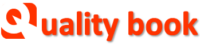
8D (Eight Disciplines) – The problem Solving tool
In this modern era, to sustain products in the market needs to use advanced manufacturing processes. Modern machinery and cost effective processes for produce quality products with low cost. but as you all know that. It’s difficult to constant manufacturing processes and sustain product quality. Because it is natural that, during the working time unexpected problems can be occurred and that kind of problems must be resolved in respective manner. Some organizations are used outmoded technique that solve the issues on temporary basis. As well those problems can be possible reoccur in processes in future.
So, needs to efficient system that eliminate the possibility of reoccur issues as well as smooth the manufacturing processes. Fortunately, we have some problem solving tools can solve the issue permanently. 8D (Eight disciplines) is one of the popular problem solving tool that in now days, organizations are adopting pleasurably. OK, so let’s see how to implement 8D in organization.
What is 8D (Eight Disciplines)?
“8D (Eight Disciplines) is problem solving tool / methodology used for correctly identified the cause of the problem, fixed and dissipate possibility of recurrence of quality problems.”
8D model is systematic approach popularly used in responding to manufacturing issues. Generally, quality team conduct eight disciplines processes for identify root causes of problem and eliminate it by appropriate actions. The 8D (Eight Discipline) model is correctly identify the cause of the problem. And apply such actions to prevent recurrence of the problem. 8D is perform as preventive and corrective action system by implement step by step process to identify potential and actual problems in processes.
Benefits of 8D (Eight Disciplines)
- The 8D method is very easy for implement in workplace as well as logical method that clearly indicate required steps of problem solution.
- The method is very popular in automotive industry, mean your customer may ask for 8D report for its own application implementation. Because it is reliable and well know problem solving tool for automotive industry.
- An excellent way of reporting non conformance to suppliers and their corrective actions.
- 8D helps to eliminate complicated issues at appropriate locations where defined the causes of the problem incorrect, lack of consequences in implementation and same problem appear again.
- The team approach works best when the problem, and its associated information is labyrinthine. Because 8D is designed and capable for special cause of problems identification and elimination.
8D (Eight Disciplines) Process Chart: Table
8d (eight disciplines) methodology.
- D1: Team Establishment
- D2: Problem Description
- D3: Containment Action
- D4: Root cause
- D5: Corrective Action
- D6: Implement and validation corrective actions
- D7: Prevent recurrence
- D8: Verify and congratulate team
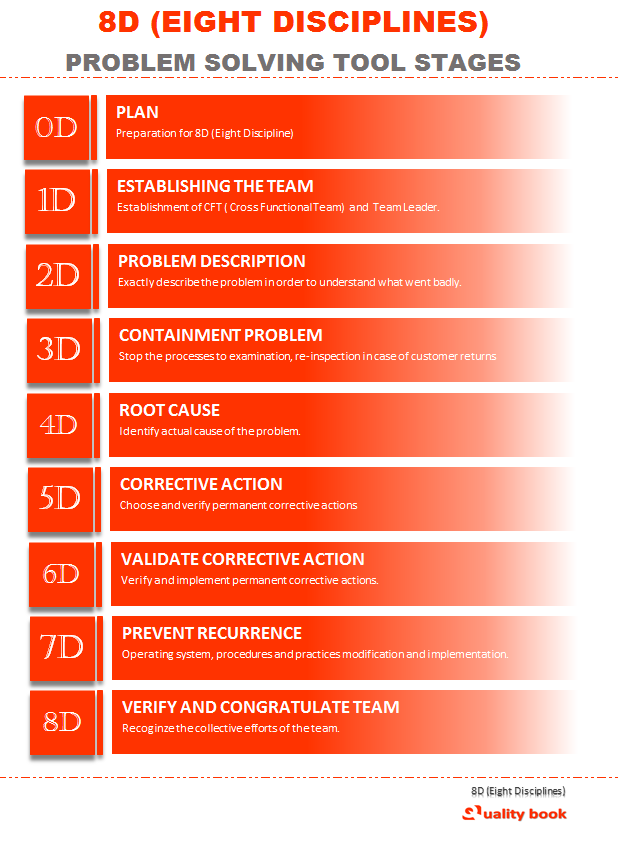
The 8D (eight Disciplines) is a process for systematic introduction of quality perfection, improvement and elimination of problems. Here in this article I will show you step by step approach and using several examples of the problem solving tools . When we involve in 8D methodology and its processes using a structured method, we become very effective at identifying cause of problems, defining problems and mistakes. As well as easily establish root causes and taking actions that solve and prevent problem identifying in processes.
So, let’s see 8D (Eight Disciplines) in deep:
As you well know, whenever any problem occurring in the manufacturing processes before you must see some warning sign that indicate the problem. Which is being experience in terms of an undesirable results and can be describe using data to identify the variation as expected and actual results.
Actually, this is the preparation stage that require to be complete before starting the eight disciplines processes in organization. Generally, peoples asking what type of preparation required before 8D process? –
A deep analysis and empathetic of the issues and problems, previous experience with same issues or related issues are necessary to determine. If the eight disciplines (8D) is the correct method to be used for solving the issues.
You have to ask the questions as below as recognizing the problem:
- Describe it is new problem in organization / division? If same problem, occur previously at where? If it is new how long from it were being in process. Or it is unknown cause?
- Has it occurred before? where? and what solutions / actions are applied at on it? What is the history of this problem?
- Why it’s happened again? is there proper solutions are not applied? what causes behind it is occur again?
- What problem solving method was used? It was joint method for one or more problem? if it is separately performed what was defects remained in method?
- To consider warning sign of problems is it really looks very complex to one person cannot resolve the problem?
- To consider above points, does the problem warrant required an eight Disciplines (8D) method? if yes, why and proceed it.
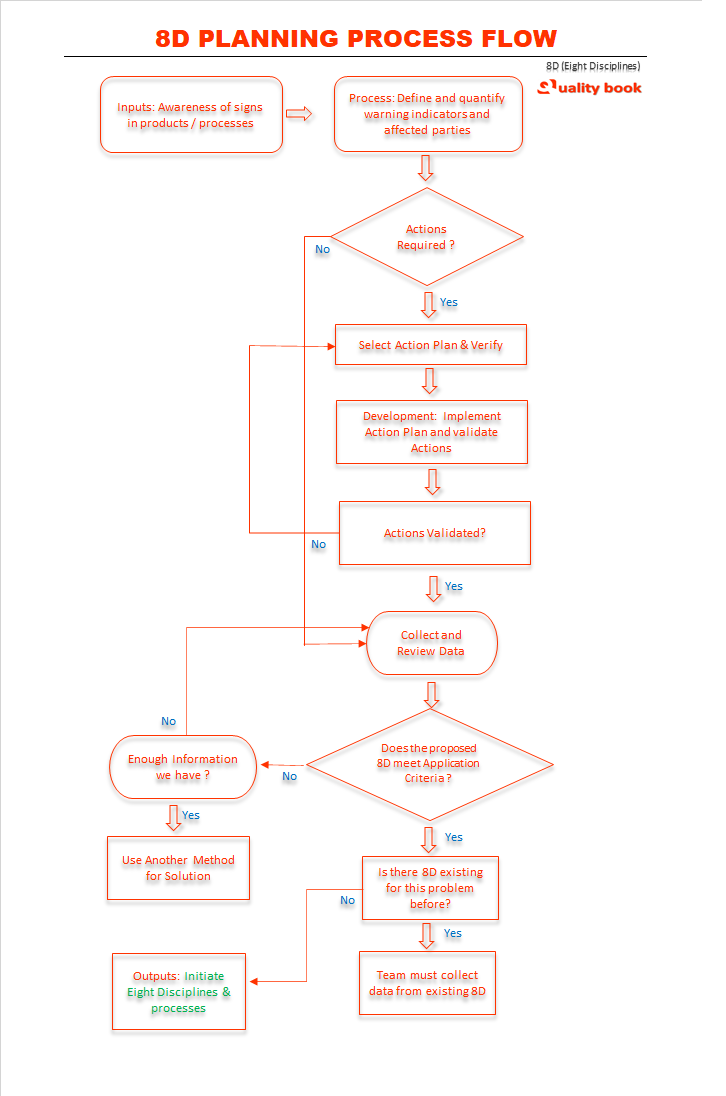
The 8D (eight disciplines) process is a team based problem solving methodology. Hence the team members must be involve for identify, action plan and eliminate issues of appropriate problem. A deeper understanding of the problem & its previous records are required to ensure if the 8D solved issues for raise issue.
D1 » Team Establishment
The team establishment is first step of the 8D (Eight Disciplines) approach. This discipline is significant stage as the eight disciplines is based on the substance of team cooperation. Establishment group of peoples called CFT (Cross Functional Team) where must each one from different department is selected by management, with the production process knowledge, product knowledge, and skill in the required technical disciplines to solve the problem and implement corrective actions.
Why team approach is important?
- CFT (Cross Functional team) build by group of peoples from different department and expertise. So any technical issues can be possible to identify, fix and eliminate problem through it.
- A Cross functional team can perform more effectively than individuals trying to solve problems.
- Cross functional team may have adequate capability to introduce proper solution of the problem.
- A group of people can discuss, focus on negative effects of actions, and can think creatively.
- Brainstorming as a group can stimulate ideas giving the team a better perspective of the problem.
A Cross functional team for eight disciplines consists of more than two people who are closely concern to the problem. Generally, involves peoples form different departments in the organization coming together to solve a problem. The skills that the team members require for this discipline to ensure the proper solution are:
- (A). Team member must knowledge of product / part / item (manufacturing processes, assembly etc.)
- (B). Team member must know the process where the problem has showed itself.
- (C). Team member must have knowledge of the customer application, technical use and end application requirements.
- (D). Team member must have skill about decision making, communication skill , and analysis of the processes and data related to manufacturing processes.
How to define team role & responsibility?
Usually, every team must have leader, here the same team leader has an important role to establish procedures and implement actions accordingly. The team leader must prepare a list defining the team structure as eight disciplines concern. the list is also important to establish role & responsibility in 8D processes. Every team member has its own importance in 8D methodology. Because every single member comes with different expertise. Hence to solve problem multifunction conception and views helpful for appropriate issues.
The role and responsibilities of the individual team member must have allocate by the team and will involve some of the points are:
Data collection and analysis, experimentation, decision making processes, modelling managing resources, planning and implementation of action plans, action plan verification and validation, communications etc.
The common processes and requirements for the 8D processes needed to contribute to the problem solving effort.
D2 » Problem Description
Problem description is a second stage designate for deep into the problem & getting a more complete information and sophisticated understanding of the problem. The problem description indicates, problem clearly identify and the eight discipline problem solving planner activities to take as much actual information as possible. Which organizes the first analysis perform in the problem solving process. You have to describe problem accurately in this stage, clear designed information is foundation to further steps of analysis.
The process of this discipline as below:
Describe The Problem Process Flow: Table
A problem description is the results of a practice that uses the is / is not method to magnify the problem statement. The location and nature of the problem have to be describe along with its impacts. Another very important analyzing results of information. To ensure that the problem involves is recurrent or whether it could occur on particular process or product.
See table below help for better understanding:
Describe the problem with Is / Is Not Method: Table
When the describing the problem with 5W + 2H (Who, What, Why, Where, When, how, how many / much) method should be use. Where you get the answered thoroughly and systematically by the questions.
See picture below for problem analysis worksheet:

Remember that, you have to specified problem statement been defined, and you have get to know for certain why that is occurring. So Is / Is not analysis must been perform for it. You have to also verify that the similar parts / components displayed the same problem? current process flow identified? does this process flow represent a change.
Once you get the answer you can collect the data and analyze it. The information you collected are evaluated for potential root causes, and identify physical evidence of the problem. The problem description been reviewed for completeness with 8D (Eight disciplines) customer and affected parties, and document the activities.
D3 » Containment Action
This is the stage where are taken correct containment action to prevent escalation of the problem. Or at the worst delivering non-conforming product to the customer. You have to describe the containment action plan to put in place in order to eliminate the effects of the problem. In this stage, immediate correction action should be carrying out in the shortest time possible. The main objective of the implement interim actions / containment actions to isolate issues from parties while a permanent solution is being develop and implement.
Why containment action required?
- When the cross functional team working on identification of the root causes of problem , collecting information and other related processes might possible some defective product produced by manufacturing in tenure. So, it is extremely important containment actions on this condition at appropriate locations.
- To ensure the customer has minimal or no impact felt as a results of the problem identified, as well prevent these defective products from getting the customer.
- In case of any defective lot / product reached to customer, it may not comply requirements to end application, hence customer will claim and complaints as results customer dissatisfaction.
- Due to immediate actions, the similar products and processes must be verified and ensure the risk levels are minimum or not evident.
Through PDCA Cycle
Plan » Prepare the most effective containment action plan and implementation including verifying the containment action effectiveness and concerned activities such as work instructions , resources and equipment available.
Do » The plan must execute as containment action plan prepared, and ensure that the actions should be clearly communicated at processes and management levels.
Check » It is cross function team responsibility that every containment actions prepared during the planning section must be implemented exactly accordingly and ensure that it may continue to be effective. One of the important activity of this section is to verify and ensure that. The activities must not any other side effects raise as a result of the containment actions.
Act » Take the actions to ensure containment action are effective and sustained with all manufacturing and supporting processes. Take the questioners and get the feedback from internal and external customers to implement and make sure is there further containment actions or correction required to rectify other issues.
8D – Containment actions checklist
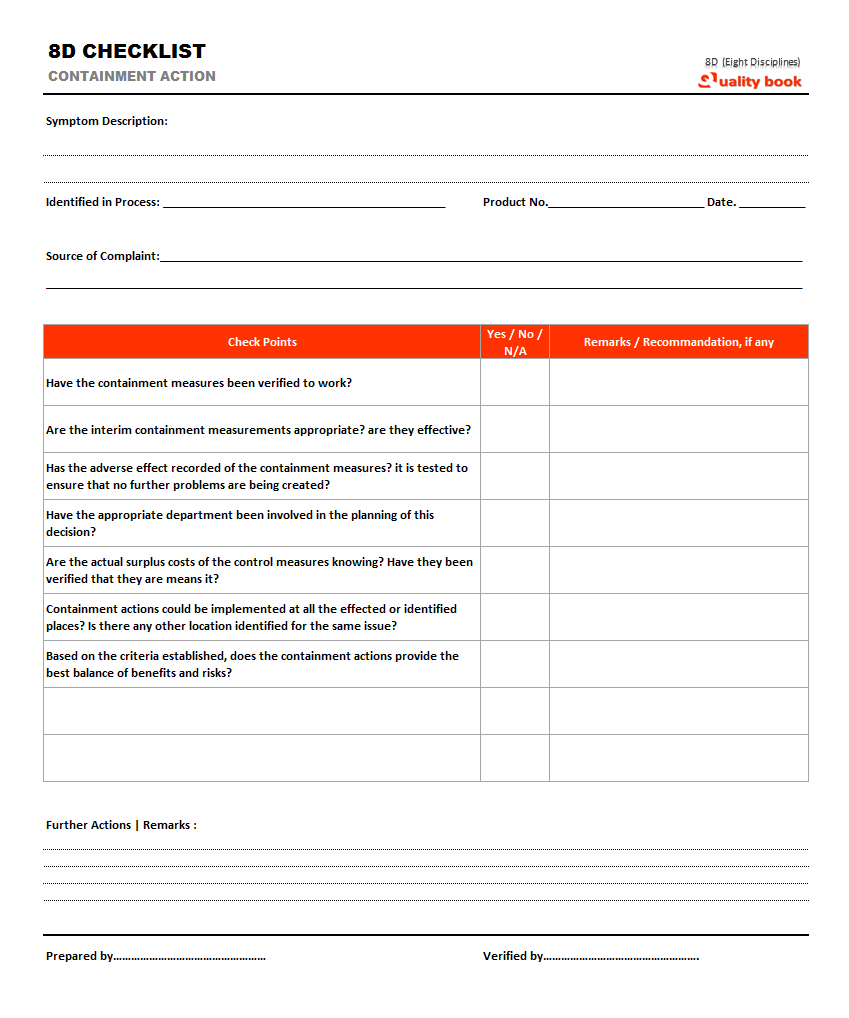
8D containment action points:
D4 » root cause.
On this stage in Eight disciplines (8D) problem solving process, needs to establish and describing the root causes of a problem is the core of this disciplines. And you will have appraise the team structure and configuration to ensure that all the right skills and experience is available for the upcoming phases or processes in the problem solving effort.
Elimination of the problem should be detecting the real cause of the problem. The objective of the explain and verify root causes is to identify all significant causes which could clarify why this problem happens. An eliminate and confirm the root cause by examine each significant cause against the describe problem and results of tested data.
For define and verify root causes you have to step out as below:
- Establish a process flow and Cause and Effect Diagram to include all the sources of variations.
- Develop a stratification cause and effect diagram, but remember that, the cause and effect diagrams used input from all team members, lack of the information of remains any points or data left, you will not get real cause.
- Establish comparative analysis, by determine critical differences between problem location and non-problem locations.
- You can also use time line analysis. Graphical / visual charts give you better understanding in most cases.
- Index the potential causes of problems by use both the process flow and cause and effect diagram.
- By using the both the tool, you can analyze the potential cause for the most likely cause.
- Determine slot of data, identify the potential cause as a root cause.
- Collect and analyze the appropriate information to identify the potential cause as a root cause.
- Specify causes that permitted the apparent warning sign to occur, are the root causes and often repressed deep in the processes. You can use the tools to help in the whole processes that is problem solving techniques are : (1) Pareto charts (2) 5 Whys analysis (3) Statistical analysis (4) Flow charts (5) Fishbone diagram (6) GR & R study (7) FMEA (8) Frequent audits (9) Fault tree Analysis (10) Brainstorming etc..
The time line is one of the important and useful tool that manage the records at time line of all events in and around the problem.
A company making steel tubes is experiencing a pits on tubes problem identified.
The significant processes / event are recorded on a time line are:
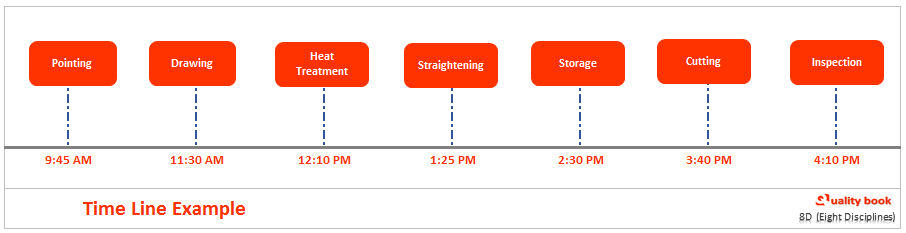
The time line helps to draw processes and events on time. Though it you can get the answer when actually the problem was first seen at which location. Now you can filter out possible causal theories later in the process by identifying what could possibly have caused the problem and what could not have caused the problem.
There are more three important stages you have to concentrate are:
(1) Develop possible causal theories (2) Establish possible root causes (3) Verify possible root causes and define and verify escape point.
You must do deeply thought about the possible causes and documents on separate media. For each of the cause you have to prepare a proper theory that describe how that the possible cause would result in the problem being experienced. You have to do write note of each ideas for develop causal theory for possible root causes.
Ask the simple question to each causal points that answered in “IS” / “IS NOT”. Does this explain the reason why the problem exists on the “IS” and not on the “IS NOT”. For separately of the possible root causes, there now requirements to be useful action to validate the possible root cause. This should be carried out in practical terms wherever possible.
D5 » Corrective Action
On the fifth stage of eight disciplines, the cross functional team must determine which corrective actions should be establishing and implement in the short period of time to ensure that the processes and product quality maintained and controlled. The corrective actions must be requirements that satisfy both the parties internal and external customers. Once the root causes are known, team concentrate on the permanent solutions, by systematic approach is needed to use the root cause analysis to establish actions for proper solution. The points that you need to focused on:
- Empathetic and defining the problem, the eight disciplines (8D) team must be able to defining the problems and implement the solution practically.
- Enclosing the effects of the problem, please note that implementation and using the program for solution must be cost effective.
- Identifying and verifying the root cause of the problem.
- Need to permanently solve the problem, and the solution must be feasible.
- Confirm the potential solutions through testing programs, and remember that the implementation program should not fail during the implement in production so, it is important the solution is a test and essential characteristic such as mistake proof and affordable.
- Verify that the solution eliminates the problem and its effects;
In fifth stage of eight disciplines, the team can introduce the additional control in the processes, and ensure that the solution is properly validated that during the implementation in running production it will not raise any unwanted issues, so trail on the small quantities first to verify the solution is effective is necessary. To ensure that the permanent corrective actions need to establish proper process flow for it, see the example process flow:
Verify Corrective Actions Process Flow: Table
Verify the corrective actions.
It is extremely important that all the established actions and implementation plans for fix the issues must be performed to not leading any further problems. So, cross functional team must well aware of this kind of technicality and must should try out the implementation program with small part of production or small quantities first to verify its effectiveness.
Corrective actions test with pre-production with small quantity can confirm that the identified corrective actions will resolve the problem of the customer, and ensure that will do not any undesirable side effects.
Check points
Somethings that still need to confirm and ensure that corrective action is will properly works at real production. Some points that help you to re-verify the condition such as:
- (1) List and measure all of the indicators related to the program.
- (2) identify which of the indicators are most direct relation to the program.
- (3) Determine intervals to measure the problem.
- (4) identify what cross fictional team prioritized the customer / end user evaluation after the implementation.
- (5) confirm the scientific methods used to verify effectiveness etc.
D6 » Implement and validation corrective actions
On the stage of validation corrective actions, the cross functional team consists of measuring the long term effectiveness of the corrective actions. The purpose of verification of the corrective action is ensure that the actions are implemented are efficient and these are eliminated permanently through effective controls and activities that are embedded in the tasks of the process. Some indicators that you can ensure that the corrective actions are properly works:
- Test and control results display improvement
- Less Rejection or reject ppm (%) in process.
- Measurements such as dimension, units’ appearance are correct according to tolerance and specifications.
- Controls on incoming raw materials for quality improvement.
- Increased satisfaction ratio and feedbacks from customers.
The statistical tools such as process capability, histograms, control charts etc. can used to measured and verify the effectiveness of the implemented corrective actions. The cross functional team must have informed to customer about the results achieved, if the process capability submitted with the requirements the customer validates the corrective measures functional. The 8D team confirms whether the capability complies with internal manufacturing requirements, if the process capability complied the team validates the corrective action.
Checkpoints:
You can use PDCA cycle for implement this stage in manufacturing processes. The implementation of the permanent corrective action conduct to implement to verify the plan for validation of the corrective action. You can plan to withdraw containment (immediate) action as part of implementation of the corrective actions.
There is also important that each resources used in processes must be properly planned as well as all documentation, process instructions and communication implementation for corrective actions. Check that the corrective actions have been implemented and integrated into the appropriate tasks and manufacturing processes. Take the actions on any variation from the plan or expected results.
D7 » Prevent recurrence
On this stage, the cross functional team have to determine what action should be taken to prevent recurrence of the problem. You have to amend those operating systems, regular practices, management system as well as procedures to prevent recurrence of this problem and all similar issues. Because preventing recurrence is a one of the important task of problem’s solution. The general process flow of the prevent recurrent is:
- Input implemented corrective actions and validation
- Review the history / previous record of the problem.
- Analyze how this problem occurred and escaped.
- Identify affected parties and opportunities for similar problems to occur and escape
- Identify the system’s policies, practices and procedures that allowed this problem to occur and escape to the customer.
- Revise the process flow of the management or operating system.
- Analyze how similar problems could be addressed.
- Develop plans to coordinate necessary actions. And verify prevent actions.
- Develop systematic prevent recommendations to process owner.
- Identify and choose prevent actions. And implement preventive actions.
- Make the system changes to prevent recurrence.
- Verify the preventive actions are effectives? If yes, Standardize the new practices.
- Notify all personnel of the resolution actions by using failure mode effects analysis.
In this stage of the 8D (eight disciplines) cross functional team analyses whether the corrective action implemented would prevent or improve the quality of similar products and processes. To ensure the prevent recurrent of the problem, you should verify results of their actions and must validate that the results is on target. To verify the actions, you must check out below points:
D8 » Verify and congratulate team
The last stage of the 8D (Eight Disciplines) Is verification of the introduced actions in previous stages are effective. It is highly recommended that verification be made by comparing the measures of the problem with outcomes from upcoming actions of material or outcomes from rejecting of next lot. Once cross functional team has complete implementation all previous stages and ensure that the actions taken in previous stages are works. All team member deserve to be congratulate as well to know that their efforts are appreciate and that the organization knows about their accomplishments.
The cross functional team must have skills and experience to be able to make progress toward as satisfactory problem resolution, and skills and experiences are base reasons for individual selection. Different skills and experiences will support to be drafted in at various stages throughout the process to get the deep understanding about the symptom of problem, root causes and resolution.
The 8D report
From beginning to end of all 8D (Eight Disciplines) processes, the single document calls 8D report is essential part once complete. Team assume that all things are complete and fix as appropriate actions for appropriate issues. This report serves as a communication tool displaying overall process of the 8D (Eight Disciplines) processes along with actions taken. So, let’s see example format of 8D report:
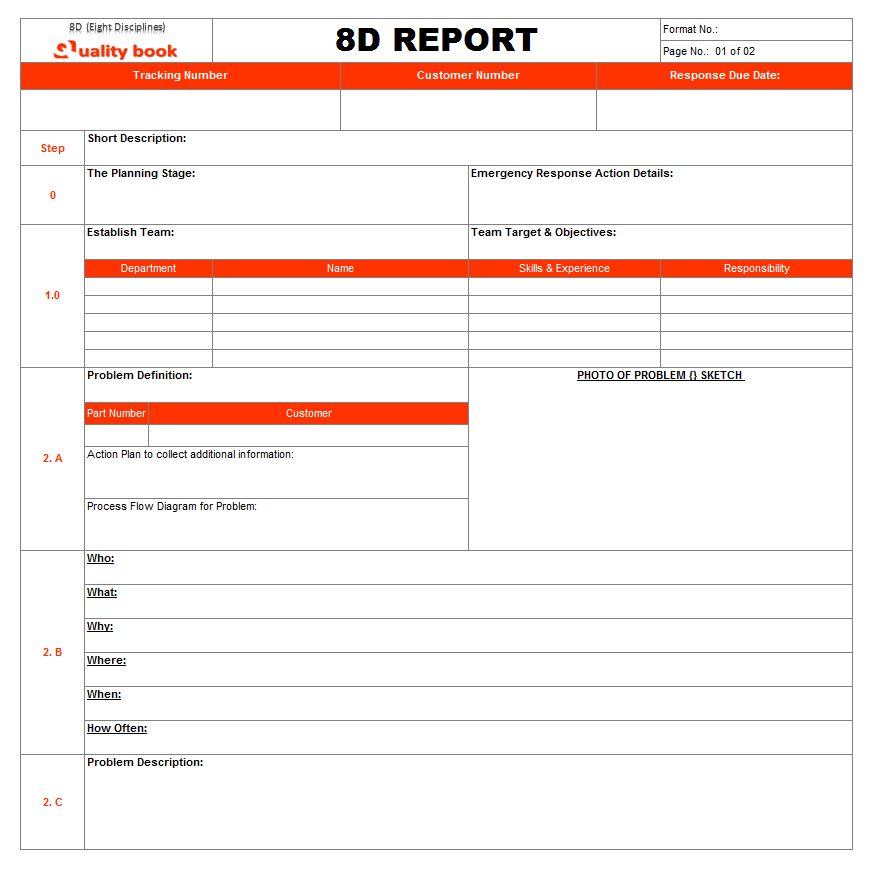
Conclusion:
When the problem has been resolve. The cross functional team should release a final document with stage wise brief description about its experiences. The 8D report give quick and better explanation of how the whole process had handling by team and also 8D serves report as a communication tool displaying overall progress of process.
We can assume that, the successful corrective actions have eliminated repetition of problems and prevention of similar issues. Further, team must ensure that corrective actions will be assess on their ability to help avoiding future problems. If we do not distinguish between major and minor problems, any issue will hold the delivery of customer and that is the reason we must have to categorize by identify systematic issues to eliminate appropriate problems.
Related Posts
Six sigma does not equal total customer satisfaction, quality control circle [qcc] : basic guide, entrepreneurship: navigating challenges and cultivating success, 7s management, enterprises quality management innovation, pre-control charts | pre-control limits | narrow-limit gauging, cost control in production | efficiency and optimization, lean: kanban tools, lean manufacturing optimises enterprise production.

How it works
For Business
Join Mind Tools
Article • 8 min read
8D Problem Solving Process
Solving major problems in a disciplined way.
By the Mind Tools Content Team
(Also known as Global 8D Problem Solving)
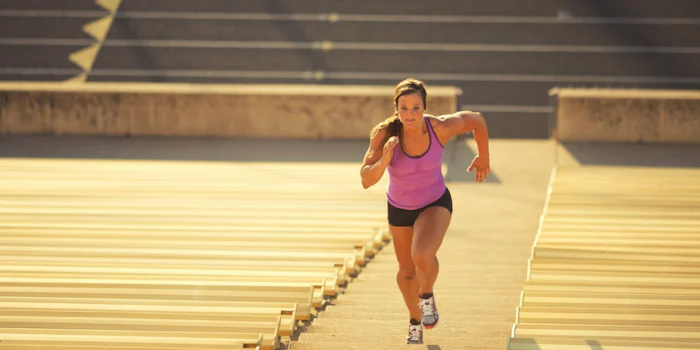
When your company runs into a major problem, you need to address it quickly. However, you also need to deal with it thoroughly and ensure that it doesn't recur – and this can take a lot of effort and elapsed time.
The 8D Problem Solving Process helps you do both of these seemingly-contradictory things, in a professional and controlled way. In this article, we'll look at the 8D Problem Solving Process, and we'll discuss how you can use it to help your team solve major problems.
Origins of the Tool
The Ford Motor Company® developed the 8D (8 Disciplines) Problem Solving Process, and published it in their 1987 manual, "Team Oriented Problem Solving (TOPS)." In the mid-90s, Ford added an additional discipline, D0: Plan. The process is now Ford's global standard, and is called Global 8D.
Ford created the 8D Process to help teams deal with quality control and safety issues; develop customized, permanent solutions to problems; and prevent problems from recurring. Although the 8D Process was initially applied in the manufacturing, engineering, and aerospace industries, it's useful and relevant in any industry.
The eight disciplines are shown in figure 1, below:
Figure 1: The 8D Problem Solving Process
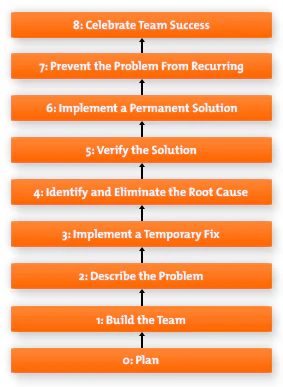
The 8D Process works best in teams tasked with solving a complex problem with identifiable symptoms. However, you can also use this process on an individual level, as well.
Applying the Tool
To use the 8D Process, address each of the disciplines listed below, in order. Take care not to skip steps, even when time is limited; the process is only effective when you follow every step.
Discipline 0: Plan
Before you begin to assemble a team to address the problem, you need to plan your approach. This means thinking about who will be on the team, what your time frame is, and what resources you'll need to address the problem at hand.
Discipline 1: Build the Team
You should aim to put together a team that has the skills needed to solve the problem, and that has the time and energy to commit to the problem solving process.
Keep in mind that a diverse team is more likely to find a creative solution than a team of people with the same outlook (although if outlooks are too diverse, people can spend so much time disagreeing that nothing gets done).
Create a team charter that outlines the team's goal and identifies each person's role. Then, do what you can to build trust and get everyone involved in the process that's about to happen.
If your team is made up of professionals who haven't worked together before, consider beginning with team-building activities to ensure that everyone is comfortable working with one another.
Discipline 2: Describe the Problem
Once your team has settled in, describe the problem in detail. Specify the who, what, when, where, why, how, and how many; and use techniques like CATWOE and the Problem-Definition Process to ensure that you're focusing on the right problem.
Start by doing a Risk Analysis – if the problem is causing serious risks, for example, to people's health or life, then you need to take appropriate action. (This may include stopping people using a product or process until the problem is resolved.)
If the problem is with a process, use a Flow Chart , Swim Lane Diagram , or Storyboard to map each step out; these tools will help your team members understand how the process works, and, later on, think about how they can best fix it.
Discovering the root cause of the problem comes later in the process, so don't spend time on this here. Right now, your goal is to look at what's going wrong and to make sure that your team understands the full extent of the problem.
Discipline 3: Implement a Temporary Fix
Once your team understands the problem, come up with a temporary fix. This is particularly important if the problem is affecting customers, reducing product quality, or slowing down work processes.
Harness the knowledge of everyone on the team. To ensure that each person's ideas are heard, consider using brainstorming techniques such as Round Robin Brainstorming or Crawford's Slip Writing Method , alongside more traditional team problem solving discussions.
Once the group has identified possible temporary fixes, address issues such as cost, implementation time, and relevancy. The short-term solution should be quick, easy to implement, and worth the effort.
Discipline 4: Identify and Eliminate the Root Cause
Once your temporary fix is in place, it's time to discover the root cause of the problem.
Conduct a Cause and Effect Analysis to identify the likely causes of the problem. This tool is useful because it helps you uncover many possible causes, and it can highlight other problems that you might not have been aware of. Next, apply Root Cause Analysis to find the root causes of the problems you've identified.
Once you identify the source of the problem, develop several permanent solutions to it.
If your team members are having trouble coming up with viable permanent solutions, use the Straw Man Concept to generate prototype solutions that you can then discuss, tear apart, and rebuild into stronger solutions.
Discipline 5: Verify the Solution
Once your team agrees on a permanent solution, make sure that you test it thoroughly before you fully implement it, in the next step.
- Conducting a Failure Mode and Effects Analysis (FMEA) to spot any potential problems.
- Using Impact Analysis to make sure that there will be no unexpected future consequences.
- Using Six Thinking Hats to examine the fix from several different emotional perspectives.
Last, conduct a Blind Spot Analysis to confirm that you and your team haven't overlooked a key factor, or made an incorrect assumption about this solution.
Discipline 6: Implement a Permanent Solution
Once your team reaches a consensus on the solution, roll your fix out. Monitor this new solution closely for an appropriate period of time to make sure that it's working correctly, and ensure that there are no unexpected side effects.
Discipline 7: Prevent the Problem From Recurring
When you're sure that the permanent solution has solved the problem, gather your team together again to identify how you'll prevent the problem from recurring in the future.
You might need to update your organization's standards, policies, procedures, or training manual to reflect the new fix. You'll likely also need to train others on the new process or standard. Finally, you'll need to consider whether to change your management practices or procedures to prevent a recurrence.
Discipline 8: Celebrate Team Success
The last step in the process is to celebrate and reward your team's success . Say "thank you" to everyone involved, and be specific about how each person's hard work has made a difference. If appropriate, plan a party or celebration to communicate your appreciation.
Before the team disbands, conduct a Post-Implementation Review to analyze whether your solution is working as you thought, and to improve the way that you solve problems in the future.
In the late 1980s, Ford Motor Company developed the 8D (8 Disciplines) Problem Solving Process to help manufacturing and engineering teams diagnose, treat, and eliminate quality problems. However, teams in any industry can use this problem solving process.
The eight disciplines are:
- Build the Team.
- Describe the Problem.
- Implement a Temporary Fix.
- Identify and Eliminate the Root Cause.
- Verify the Solution.
- Implement a Permanent Solution.
- Prevent the Problem From Recurring.
- Celebrate Team Success.
The 8D Problem Solving Process is best used with a team solving complex problems; however, individuals can also use it to solve problems on their own.
Ford is a registered trademark of the Ford Motor Company: https://www.ford.com/
You've accessed 1 of your 2 free resources.
Get unlimited access
Discover more content
Win-win negotiation.
Finding Solutions That Work for Everyone
Thomas Davenport and Larry Prusak: Working Knowledge
The Five Modes of Knowledge Generation According to Davenport and Prusak
Add comment
Comments (0)
Be the first to comment!
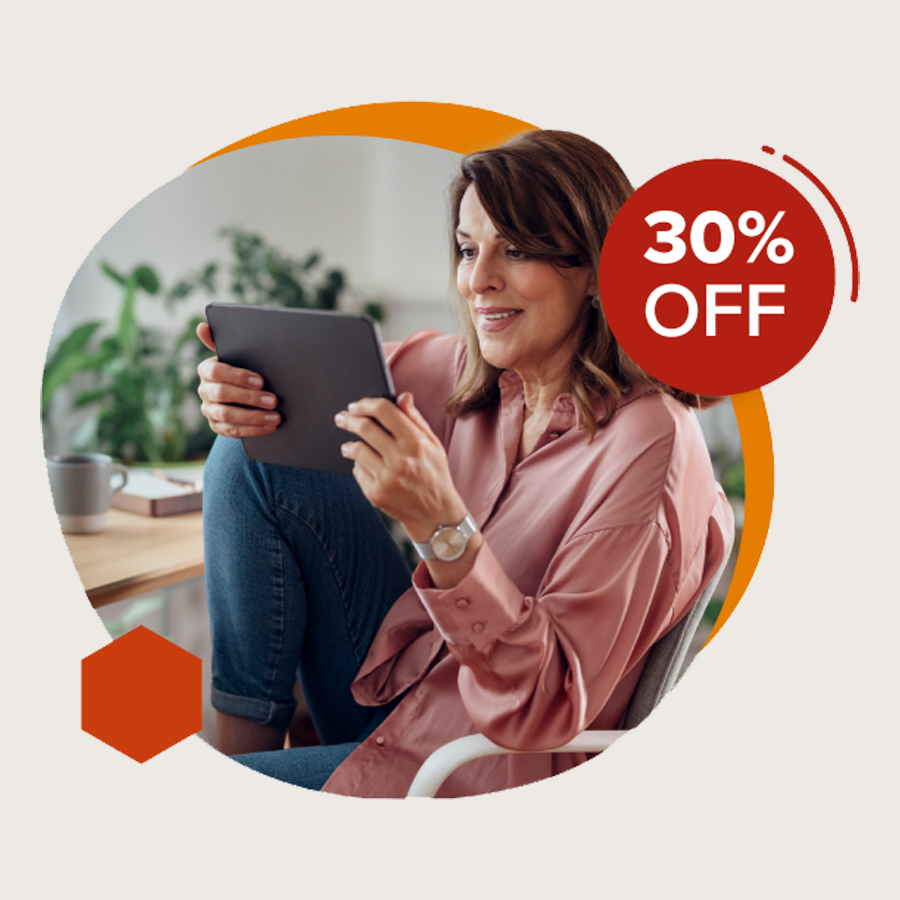
Gain essential management and leadership skills
Busy schedule? No problem. Learn anytime, anywhere.
Subscribe to unlimited access to meticulously researched, evidence-based resources.
Join today and take advantage of our 30% offer, available until May 31st .
Sign-up to our newsletter
Subscribing to the Mind Tools newsletter will keep you up-to-date with our latest updates and newest resources.
Subscribe now
Business Skills
Personal Development
Leadership and Management
Member Extras
Most Popular
Latest Updates
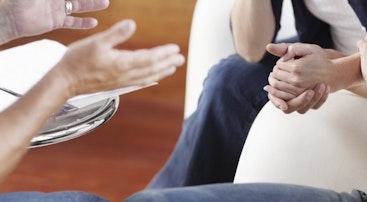
Winning Body Language
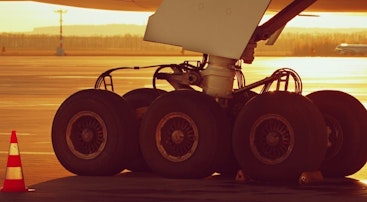
Business Stripped Bare
Mind Tools Store
About Mind Tools Content
Discover something new today
Nine ways to get the best from x (twitter).
Growing Your Business Quickly and Safely on Social Media
Managing Your Emotions at Work
Controlling Your Feelings... Before They Control You
How Emotionally Intelligent Are You?
Boosting Your People Skills
Self-Assessment
What's Your Leadership Style?
Learn About the Strengths and Weaknesses of the Way You Like to Lead
Recommended for you
Breaking the glass ceiling video.
How to Smash Through Invisible Barriers
Business Operations and Process Management
Strategy Tools
Customer Service
Business Ethics and Values
Handling Information and Data
Project Management
Knowledge Management
Self-Development and Goal Setting
Time Management
Presentation Skills
Learning Skills
Career Skills
Communication Skills
Negotiation, Persuasion and Influence
Working With Others
Difficult Conversations
Creativity Tools
Self-Management
Work-Life Balance
Stress Management and Wellbeing
Coaching and Mentoring
Change Management
Team Management
Managing Conflict
Delegation and Empowerment
Performance Management
Leadership Skills
Developing Your Team
Talent Management
Problem Solving
Decision Making
Member Podcast
.png)
1-888-326-9244
Create an Account
- Sign in or Register
- PRINTERS & SUPPLIES
- FLOOR MARKING
- SAFETY SIGNS
- PIPE MARKERS
- Free Samples
8D Methodology
Resource Navigation
- Resources Home
- Infographics
--> 03 February, 2023 4 MINUTE READ
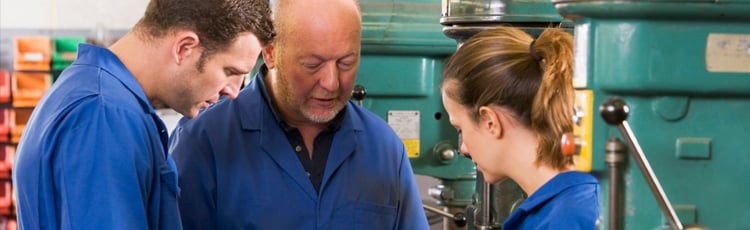
The 8D methodology (8D=eight disciplines) was developed in Ford Motor Company in the mid-1980s to be used by their suppliers to improve the resolution of problems. It appears in a variety of forms used to define eight disciplines. Sometimes it is defined as a nine-step problem-solving process. Because the 8D model is designed to solve specific problems that arise, more emphasis is placed on containing the problem (discipline 3) than in most other frameworks. The idea is to implement intermediate actions that will protect the customer from the problem until a permanent solution can be developed and implemented.
The Eight Steps of the 8D Methodology
The 8D Methodology was originally composed of eight "disciplines" or steps. In the 1980's Ford added a ninth discipline, planning, but the name "8D" was retained. The disciplines are:
- D1 Put Together A Team
D2 Define the Problem
D3 implement a temporary fix.
- D4 Identify Root Causes and Chose a Solution
- D5 Confirm The Solution Resolves The Problem
- D6 Fully Implement the Solution
D7 Prevent Recurrence
- D8 Recognize the Team
The 8D Methodology is based on the PDCA Cycle (Plan, Do, Check, Act). Each step in PDCA roughly corresponds to two steps in 8D Methodology:
- Plan Define a problem and hypothesize possible causes and solutions (8D steps D0-D2).
- Do Implement a solution (8D steps D3-D4).
- Check Evaluate the results (8D steps D5-D6).
- Act Either return to the planning step, or standardize the solution, depending on the results (8D steps D7-D8).
How Does the 8D Methodology Work?
The strength of the 8D Methodology is its ability to identify, correct, and permanently eliminate recurring problems in an ongoing system, by applying a quick fix and then addressing the root cause of the problem.
D0 Plan
The 8D Methodology often starts with a customer complaint about a problem with a product. In some cases a problem may be identified by management, or production workers. However the problem is first identified, the first step is to establish an initial plan. The plan includes a report on the problem, with an initial evaluation of its scope. This plan forms the basis for defining a team, identifying needed resources, and establishing a schedule for resolution.
D1 Put Together a Team
The team should be multidisciplinary, and include expertise in the product, process, or equipment being investigated. In the case of a problem with a product, understanding the customer's needs is critical, and having a representative from marketing or even a customer on the team is helpful. When processes and staff need to shift, it may be helpful to have an HR representative on the team.
The team's first task will be to write a purpose statement. This written document defines why the team exists, and what it is supposed to do. Having the team discuss this and create the document in their first meeting helps to get everyone on the same page.
What, specifically, is going wrong? The problem needs to be defined using quantifiable terms. The customer's complaint may be, "This product doesn't work!" How is it not working? Defining the problem may require establishing test methods and collecting data, interviewing customers, or talking with the workers who are involved with making the product.
"Gemba" is an important principle to apply when defining the problem. Gemba means to go to the physical location where the problem is - the real place - and look for yourself. The objective is to get first-hand information.
At this point, the team is not looking for the cause of the problem, or "where it comes from;" instead, they are collecting as much information as possible to determine the characteristics of the problem, or "what it is."
If the problem is affecting customers, impacting productivity or costs, or is creating an injury, health, or environmental hazard, it needs to be addressed immediately. A temporary fix should be identified, evaluated, and implemented. These fixes may involve reworking the product, adding additional quality checks, or inspecting and sorting incoming parts from your suppliers.
If no temporary fix is feasible, it will be necessary to stop shipping the project or to shut down the process that has the problem.
Do not implement a temporary fix without an evaluation. The team needs to be sure the temporary fix is safe, will truly address the current problem, and is easy and cost effective to implement - without causing new problems of its own.
D4 Identify Root Causes
With the temporary fix in place, the next step is to identify the root cause of the problem. The overall goal of the 8D Methodology is to permanently eliminate the problem. That can only be done if the root cause is identified and eliminated.
Techniques such as the "Five Whys" can be used to identify the root cause. This approach involves asking the question "Why?" over and over (often five times) until the root cause is revealed. Other methods, such as fish-bone diagrams, Parento Analysis, or Fault Tree Analysis are also available to help identify the root cause. However the root cause is identified, the team should then decide how to eliminate it.
D5 Confirm the Solution Resolves The Problem
One of the best ways to test a solution is to implement it in a small way, and monitor what happens. For example, if a manufacturing process involves a number of cells, the solution can be implemented in one cell and the results monitored. If it is successful in the one cell, it can then be implemented in all cells. If the solution cannot be tested in a small way, then techniques such as Failure Mode and Effect Analysis can be used to analyze proposed changes to a system or product.
The team needs to be careful to ensure they have not missed something. Conducting a Blind Spot Analysis can be useful for identifying things that have been overlooked. Look for unintended consequences and negative side-effects that may result from implementing the solution.
D6 Fully Implement the Solution
Once the solution has been verified - it will eliminate the root cause without starting new problems - it can be fully implemented by making permanent changes.
Once changes have been made, steps need to be taken to ensure those changes remain in effect, and that any new procedures continue to be followed. This usually involves incorporating the changes in written standards. Training may be required to bring people up to speed on new methods, procedures, and standards.
D8 Recognize the Team
Recognizing the accomplishments of the team is the final step. It can be a simple "thank you," but it should be done in a way such that others in your organization hear about what has been done. A common way to say thank you is with an article in the company newsletter, or with a poster placed on bulletin boards throughout the facility. Be sure that everyone on the team is named so that everyone is recognized for being a part of the team.
RELATED RESOURCES

ANSI Z87.1 Eye Safety & Eye Protection Glasses
Workers in nearly every industry can benefit from eye protection. Eye safety should be a top priority to ...
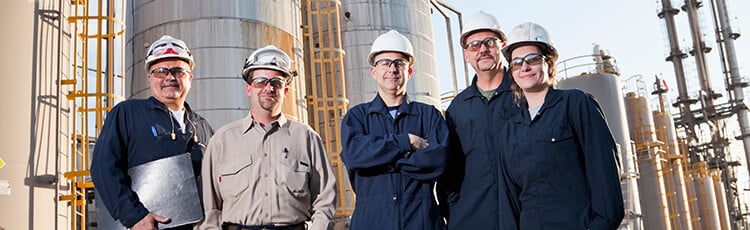
Jishuken is a form of problem solving using gemba kaizen combined with a kaizen blitz, but it involves more ...
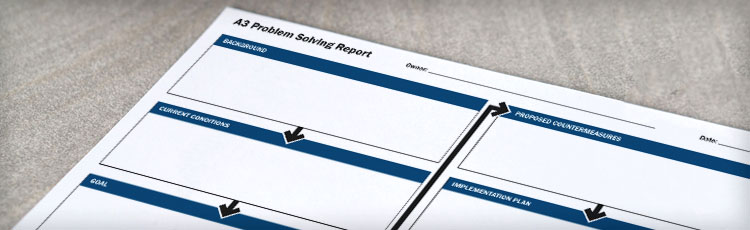
A3 Problem Solving
What is A3, and what does it have to do with problem solving? A3 is a standard paper size, roughly 11"x17" - ...
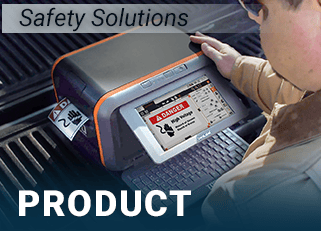
Modal title
Are you a ComplianceQuest Customer?
8D Management (8 Disciplines Management)

8D Management & The 8D of Problem Solving
Problems are a part of life and a business is no exception. Even with the best of intentions and systems, some errors can creep in and be hard to detect. It may be nothing serious or can have serious repercussions such as reputation damage, heavy fines, product recall, property loss, and so on. It becomes essential to identify the problem, its consequences on the one hand, and causes on the other to be able to not only resolve it for now but also ensure prevention of its recurrence. One of the methodologies, popular amongst engineers and professionals mainly in the automotive industry but now applied across several industries is the eight disciplines (8D) model. It helps to identify, correct, and eliminate recurring problems, affecting improvement in product and process.
Related Assets
Key Highlights: 8D is an extremely effective, proven problem-solving framework, especially in the manufacturing and automotive sector. However, to truly…
What is Quality 4.0? Is it a buzzword for defining the next generation of quality management systems? Does it refer…
Unless you live in an alternate universe, as a business leader you are bound to encounter problems, issues, or challenges.…
What is 8D?
The 8D is a systematic, holistic and proven methodology designed to identify the root cause of a problem, plan a quick fix, and implement corrective actions and preventive actions to avoid their recurrence. If your product is defective or not meeting your customer requirements, then 8D is an excellent first step to improve Quality and Reliability.
One of the core parts of introducing 8D problem solving, greatly accepted by most disciplines of industries, and having huge effectiveness levels in improving product and process quality, would be 8D (Eight Disciplines). Key steps in the 8D methodology are forming a team, defining the problem, identifying and implementing interim containment, identifying the root causes, implementing and verifying permanent corrective actions, and avoiding future recurrence of problems. The 8D process for root cause analysis concludes by highlighting that the team members not only play a vital role but also recognizes them, hence reinforcing that this approach is a collaborative one. 8D has become very popular among manufacturers, assembly, and services around the globe because it is effective and comparatively easy to teach.

Why Apply Eight Disciplines of Problem Solving (8D)
The 8D methodology, developed to represent the best practices in problem solving, provides the engineering teams with an effective and efficient team-oriented problem solving skill, a better understanding of Root Cause Analysis (RCA) and how to use basic statistical tools required for problem solving. 8D helps the management understand and resolve problems better, identify necessary systemic changes and inputs for change , and facilitate a more candid and open communication in problem solving discussions.
8D improves the Quality and Reliability of your products, and if performed correctly, prepares the engineering team for future problems.
When to Apply Eight Disciplines of Problem Solving (8D)
The 8D problem solving process is used to solve major, critical, chronic, and recurring problems. The 8D is typically required during safety or regulatory issues, customer complaints , warranty concerns, poor performance or test failures, internal rejects, and to minimize waste and scrap.

How to Use Root Cause Analysis to Transform Your Safety Program
8d (eight disciplines) problem solving approach.
The 8D is a systematic process for the introduction and improvement of quality, and elimination of problems. Here we will show you the step by step approach of the problem solving tools that can make you proficient at identifying causes of problems, defining problems, and errors. Additionally, it helps identify root causes and take actions to solve and prevent identified problems in processes. So, let’s take a peep inside:

D0: Planning and preparing for the 8D
Proper planning and preparation are always a good start before taking any action. So, you need to consider the following before forming a team:
- Problem description
- Timeframe for the resolution
- The number of resources to accomplish this

D1: Team establishment
Create a team with people who varied backgrounds and experiences which will lead to the best quality inputs and a complete solution. For the team to function smoothly, define clear roles, and responsibilities for your people, and have a team leader.

D2: Problem description
The 8D method’s primary focus is to describe the problem appropriately and objectively such that it captures all the vital information. During this analysis, repeated 5W1H (why, what, who, where, when, and how) are required to be asked to develop a clear description.

D3: Problem containment plan
A temporary problem containment plan is sometimes needed to minimize the impact of the problem until you develop permanent solutions. On developing the plan based on the hypothetical cases, the resources for addressing the main problem can be released. At times, new processes may be required to work around the problem until you have a permanent fix.

D4: Root Cause Analysis (RCA)
With the problem temporarily contained, you can now turn to identify all of the root causes of the nonconformance . There are several tools to identify the actual root cause of an issue including the 5W1H to understand the problem in-depth, Fishbone diagrams to visually categorize causes, and Pareto charts to identify the vital causes.

D5: Permanent Corrective Action
Once the root cause of the problem is determined, the team can start brainstorming permanent corrections to identify what the best long-term solution will be. Brainstorming sessions combined with tools such as affinity diagrams help organize ideas based on their relationships and determine the best course of action.

D6: Implement and Validate the Permanent Corrective Action
Once the solution is identified, the management needs to implement and verify the corrective action using the PDCA (plan-do-check-act) approach for small-scale testing before large-scale rollout. Thus, the outcomes and corrective actions are tracked to ensure expected results. To successfully implement a permanent change, a project plan should incorporate:
- Development of the project plan for implementation
- Communicating the plan to all stakeholders
- Validating improvements using measurement

D7: Prevent Recurrence
A complete solution of problems means preventing them from occurring. Besides, preventative measures should also be implemented for corrective actions in the 8D methodology. This requires reviewing management processes, operating procedures, and training manuals to ensure that best practices are followed.
At this stage, organizations should consider actions including updating process audit questions and regularly verifying them based on corrective actions to reduce risk in other processes, presenting poka-yoke or error-proofing devices to big-risk processes, and conducting red rabbit tests to see how long it takes poka-yoke devices to detect defective product.

D8: Verification and Team Celebration
Once the problem is solved, the ultimate step is to congratulate the team. It’s important to recognize their efforts and share their success across the organization because teams require feedback to allow for satisfactory closure. This facilitates motivation and employee engagement while helping you improve quality control, execute process improvements, and aid change management as you grow.

Create a team with people who are having varied backgrounds and experiences which will lead to the best quality inputs and a complete solution. For the team to function smoothly, define clear roles, and responsibilities for your people, and have a team leader.

A complete solution of problems means preventing them from occurring initially. Besides, preventative measures should also be implemented for corrective actions in the 8D methodology. This requires reviewing management processes, operating procedures, and training manuals to ensure that best practices are followed.
8D Root Cause Analysis (RCA) and Corrective Action Process
The 8D Root Cause Analysis, as well as the 8D Corrective Action process, is a widely systematic approach in quality management, especially concerning 8D in quality control. This method includes eight comprehensive steps that are devised to problem solving by dealing with root causes of the problems comprehensively. The steps of the 8D process start with the formation of a team, a clear definition of the problem, and move on to interim containment actions. This is then followed by detailed root-cause analysis using the 8D RCA process, development and verification of permanent corrective actions, implementation, and recurrence preventing efforts. Encouraging details in the analysis: the 8D methodology steps encompass collaborative efforts and documentation that ensure durable solutions and continuous improvement in organizational processes. Root Cause Analysis (RCA) is embedded within the 8D process and includes the following steps and techniques:

Problem Symptom is measured and transformed to “Object and Defect”

Problem Symptom is reformed to Problem Statement using the 5W1H process

Potential Causes are gathered using the tools like Fishbone or Affinity Diagram

Problem Statement should fit using both the “is” and the “isn’t” sections of the question

Root Cause concepts are developed from remaining possible causes on the tool and related changes from is/is not

Compare theories with recent data and develop experiments for Root Cause Verification

Test and confirm the Root Causes

Customer Success
3 Women Leaders Making a Powerful Impact in Global Quality and Safety Management
How to use the 8d approach.
8D portrays 8 steps of a structured approach to solve difficult, recurring, or critical problems by providing transparency, driving a team approach, and increasing the chances of solving the problem.
Proper plan for solving the problem and identify the prerequisites.
Team creation
Gather a cross-functional team with product/process knowledge.
Problem description and definition
Use the data and information to specify the problem by identifying in quantifiable terms the who, what, where, when, why, how, and how many (the 5W1H) for the problem.
Problem Containment Plan development
Develop and implement interim actions to eliminate the problem from any customer in the future.
Specify and assess Root Causes
Identify and review all relevant causes and sources of variation that analyze why the problem has occurred and figure out why the problem was not noticed at first using 5W1H or diagrams.
Verify Permanent Solutions
After collecting data confirm that the possible solutions will actually resolve the problem.
Implement and Validate Corrective Actions
Discuss and review results and develop plans to implement the best solutions or countermeasures.
Preventive measures
Transform the operation systems, management systems, procedures, and practices to avoid the recurrence of similar problems.
Compliment your team
Recognize the collective efforts of your team and formally thank them for their involvement.
8D Problem Solving Tools and Techniques
The 8D problem solving methodology is the set of tools and methods aiming for complex quality issues. 8D problem solving techniques are basically comprised of a fishbone diagram, 5 Whys analysis, Pareto charts, process flowcharts, and Failure Mode and Effects Analysis (FMEA) to come to terms with the 8D framework. Integration with statistical tools and data analysis in every step of 8D analysis is sure to make the most accurate identification of the root cause.
This approach would ensure that cross-functional teams' participation would not only be present in the brainstorming sessions but also in the 8D problem solving process at the problem solving stage.

Training in 8D Methodology
8D training is an inevitable imperative that makes its deployment in organizations effective. The 8D methodology provides all the necessary details that the teams could apply to the skills and knowledge required at every step in 8D of quality control. Training the workforce on 8D methodology will make them able to apply these aspects when dealing with real-world problems, which will better off the quality and efficiency of the entire organization. It ensures that all these measures and strategies have been inducted to make sure that 8D problem solving approaches are not just tools for problem solution but have been inducted to lay down the base for sustainable quality improvement and prevention practices in the organizational processes.
Great product, support, and people to work with!
We have rolled-out CQ across our company to automate various elements of QMS requirements such as Document Management, Complaints, Non-conformances, Corrective Action (8D and A3), Supplier Management and Audit Management. We have been using the software for more than 2 years. We are glad to see how well the system is being used across the company. We have several thousand users on the system currently and working to scale the usage further. CQ solution has been configured to meet our needs, works elegantly across languages, across time zones, and business verticals. With integration between CQ and SAP to exchange critical data, the process automation provides a lot of productivity.
CQ configuration team and support have worked hard to ensure that our needs continue to be met. They consistently go above and beyond. We cannot be more pleased with our use of CQ QMS capabilities and would definitely recommend to anyone who is looking for a modern cloud based EQMS solution especially if you want a scalable EQMS solution.
Lia Budiman, Continental Contitech

8D Problem Solving Report
8D problem solving reports and templates are useful tools to initiate a problem solving process. These reports are used to explain what 8D is and including information about each step so that one will know what needs to be done by attempting this to solve problems. Keeping these reports easily available can avoid repeating work on the same problems over and over again.
8D reports must be detailed and incorporate information at every step within the 8D process. Those who are working on the problem should provide sufficient information when completing a report so that someone who was not on the current 8D team can pull it out and understand what the problem was and what solutions were implemented.

Who Can 8D Help?
The 8D methodology is universally applicable for every organization that needs solving. Although, there are a few industries and sectors where this 8D approach is successfully used such as manufacturing, the automotive industry, engineering companies that manufacture products or parts, and medium and large-scale enterprises.
Improve quality, eliminate problems and identify the root cause of a problem with 8d Methodology
Related checklists.

Quality Assurance Checklist – Part A (Project Management)
Checklist | September 7th, 2022

Quality Assurance Checklist – Part B (Project Deliverables)

Quality Control Area Safety Audit Checklist for Pharmaceutical Companies
Checklist | April 22nd, 2022
Quality-centric Companies Rely on CQ QMS

Frequently Asked Questions
The 8D methodology is often used since it provides a consistent, simple, and thorough approach to solving raised problems at various stages. If properly applied, it gives several advantages such as:
A systematic approach for improving team-oriented problem solving skills
A clear understanding of basic statistical tools needed for problem solving
A practical understanding of the ‘ root cause analysis’ tool
Creating and expanding relative information about past failures and lessons learned to avoid future problems in the organization
Improving skills for corrective action deployment
When the team is trying to find the root cause of the problem and deploy corrective actions, some defective products will continue to be manufactured. To prevent these defective parts from reaching the customer, interim containment ensures that the defects are contained in the facility till the problem is completely solved. If defective parts reach the customer, it may result in warranty claims, field failures, and customer complaints.
To implement the 8D process successfully, the following factors are crucial:
The right team
An accurate description of the problem
Avoiding skipping through steps
Ensuring cooperation within the team and management support
Understanding the difference between real causes and possible causes
Related Insights

5 Dos and Don’ts When Choosing a QMS Solution for Your Enterprise
Every investment a business makes should have a measurable impact. In the case of an EQMS, the ROI is based…
Cost of Quality: Finding the Sweet Spot Between Expense and Excellence
Every company has a key responsibility to take into account the…
Countdown Begins: Preparing for FDA’s Amended Quality Management System Regulations (QMSR) Final Rule
On January 31, 2024, the US Food and Drug Administration…
PPAP Management: Streamline Your Product Approval Process Digitally
Optimize and manage your PPAP process with the innovative features…
Connect with a CQ Expert
Learn about all features of our Product, Quality, Safety, and Supplier suites. Please fill the form below to access our comprehensive demo video.

Please confirm your details
By submitting this form you agree that we can store and process your personal data as per our Privacy Statement. We will never sell your personal information to any third party.
In Need of Smarter Ways Forward? Get in Touch.
Got questions we can help.
Chat with a CQ expert, we will answer all your questions.

- 5S (7S) – Japanese concept of workplace improvement
- Process Management and Process improvement
Course objectives
Participants will learn how to minimize and eliminate waste in the workplace by using the 5S method coming from the Japanese industry. They will become familiar with the implementation of 5S methodology step-by-step, how to create a “lean” work environment that allows performing work tasks simply and correctly (so-called Visual Workplace) all the time. Based on examples comming from real implementations they will understand the benefits and pitfalls of applying the 5S method. Participants will learn how to set up 5S standards for their working area properly.
Course content
- History of the 5S method, main terms and abbreviations, 7S extended concept of USA
- Purpose and objectives of 5S implementation - explanation of the basic pillars of Toyota Production System (TPS) - elimination of losses (clarification of individual types of waste MUDA = Waste Management), visualization and 5S as the first step in the implementation of the so-called lean workplace.
- 1S - SEIRI (Sort) - sorting items into necessary and unnecessary categories. Purpose of the 5S Red tag system
- 2S - SEITON (Straighten) - how to create a workplace layout by using visual management tools. How to determine the proper place, the quantity for the necessary items in the workplace, workplace ergonomics analysis
- 3S - SEISO (Shine) - how to set up the standards for cleaning and workplace cleaning schedule (linked to TPM/autonomous maintenance). How to define the procedure and basics of regular workplace cleaning
- 4S - SEIKETSU (Standardize) - how to set up standards for each work activities and working performance. How to create standards for a workplace in the production area, to put in 5S standard at all workplaces/office. How to avoid anomalies in the workplace. Opportunity to prepare a 5S Company Manual, etc.
- 5S - SHITSUKE (Sustain) - Self-discipline - a system of motivation and assessment of 5S compliance at each area. Preparing a 5S Checklist for a selected area. 5S audits performance, etc.
- 6S - SAFETY - Occupational health and safety (according to the ISO 45001 standard) and minimizing any workplace risks
- 7S - SPIRIT - Transformation of the company culture - 7S is the basis of longterm improvement of company productivity at minimal cost, helps to eliminate waste and increase self-discipline. The top management engagement is a must.
- Examples of 5S implementation comming mainly from automotive in Japan and Europe.
Designed for
- Quality Manager
- IMS Manager
- Production Manager
- Logistics Manager
- LEAN Manager
- Occupational Health and Safety Manager
Additional information
* UTC +1 time zone (DE, BE, DK, NL, NO, SE, AT, ES, FR, IT, SI, SK, CZ, PL, HU, ...)
Creating a tailor-made corporate course
Training dates in english language, similar training, recommend to a friend.
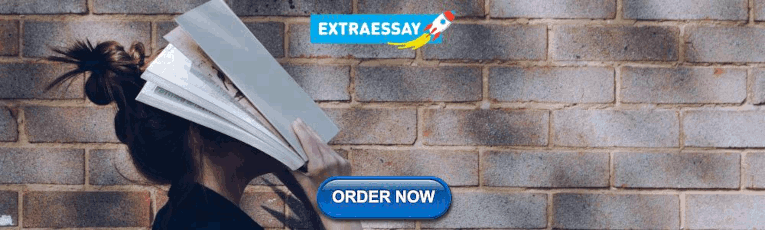
IMAGES
VIDEO
COMMENTS
The eight disciplines (8D) model is a problem solving approach typically employed by quality engineers or other professionals, and is most commonly used by the automotive industry but has also been successfully applied in healthcare, retail, finance, government, and manufacturing. The purpose of the 8D methodology is to identify, correct, and ...
The disciplines are: D0: Preparation and Emergency Response Actions: Plan for solving the problem and determine the prerequisites. Provide emergency response actions. D1: Use a Team: Establish a team of people with product/process knowledge. Teammates provide new perspectives and different ideas when it comes to problem solving.
The 8D Problem Solving approach has attained widespread acceptance throughout a number of industries. It is a potent tool for businesses looking to improve their problem-solving skills and promote long-term success due to its systematic approach, emphasis on teamwork, and emphasis on continual improvement. The Eight Disciplines of 8D Problem ...
1. 8D (Eight Disciplines) The 8D problem-solving methodology is structured into eight steps, providing a systematic approach to identifying, solving, and preventing problems. The steps include: D1: Form a Team. D2: Define the Problem. D3: Develop Interim Containment Actions.
Thus, in order to optimize their relationships with Japanese, it's useful for non-Japanese to adopt this technique. The first step in saihatsu boshi is "genin wo mitsukeru", which translates as getting to the root of the problem, or discovering the root cause. This process is what Americans might refer to as a detailed post-mortem analysis.
The 8D problem solving process is a detailed, team oriented approach to solving critical problems in the production process. The goals of this method are to find the root cause of a problem, develop containment actions to protect customers and take corrective action to prevent similar problems in the future. The strength of the 8D process lies ...
The very first seeds of the 8D Problem-Solving methodology were sown during World War II. It was incorporated into Military Standard 1520, a framework aimed at addressing product and service failures. At the time, the military faced complex challenges that often involved multiple variables and high stakes.
8D short for the 8 Disciplines, is a globally recognized problem-solving methodology. It is primarily used as a quality tool where customer complaints of faulty or defective products are needing to be addressed. However, it is not exclusively used for customer complaints; it is well suited to these situations, and many large organizations would ...
8D Problem Solving is a systematic and structured approach used to solve business related problems. It names has been given by the fact there are 8 steps or 8 disciplines that are followed to identify, correct and eliminate recurring problems. 8D Problem Solving is regarded as robust methodology that has proven its worth across multiple ...
In reality, the 8D process is officially known as the Eight Disciplines of Problem-Solving. To make things a little more confusing, it's really nine steps. While originally developed as 8 steps or disciplines, it was subsequently revised to include a step zero, which was to plan and prepare for solving the problem. Image source: ASQ.org.
Open communication within the team and with management. A framework for corrective action that allows for systemic changes and continual improvement. Intense examination of the control systems that permitted the problem. Easy integration with process-improvement tools. You can apply the 8Ds whenever processes break down.
The eight disciplines (8D) method is a problem-solving approach that identifies, corrects, and eliminates recurring problems. By determining the root causes of a problem, managers can use this method to establish a permanent corrective action and prevent recurring issues. First introduced by Ford, the 8D method offers a consistent way of ...
Eight Disciplines (8D) is a problem-solving methodology designed to address, correct, and eliminate recurring problems impacting business operations, manufacturing, and product development ...
The 8D (eight Disciplines) is a process for systematic introduction of quality perfection, improvement and elimination of problems. Here in this article I will show you step by step approach and using several examples of the problem solving tools.When we involve in 8D methodology and its processes using a structured method, we become very effective at identifying cause of problems, defining ...
The Ford Motor Company® developed the 8D (8 Disciplines) Problem Solving Process, and published it in their 1987 manual, "Team Oriented Problem Solving (TOPS)." In the mid-90s, Ford added an additional discipline, D0: Plan. The process is now Ford's global standard, and is called Global 8D. Ford created the 8D Process to help teams deal with ...
The 8D methodology (8D=eight disciplines) was developed in Ford Motor Company in the mid-1980s to be used by their suppliers to improve the resolution of problems. It appears in a variety of forms used to define eight disciplines. Sometimes it is defined as a nine-step problem-solving process. Because the 8D model is designed to solve specific ...
8D stands for the 8 disciplines of problem solving. They represent 8 steps to take to solve difficult, recurring or critical problems (often customer failures or major cost drivers). The structured approach provides transparency, drives a team approach, and increases the chance of solving the problem. D1: Create a Team: Gather a cross ...
When to Apply Eight Disciplines of Problem Solving (8D) The 8D problem-solving process is used to solve major, critical, chronic, and recurring problems. The 8D is typically required during safety or regulatory issues, customer complaints, warranty concerns, poor performance or test failures, internal rejects, and to minimize waste and scrap.
The eight disciplines are: Recognise the efforts of the team. TOPS 8D is a reductionist problem solving approach in that it looks for a solution to remedy the immediate problem, but does not require an optimal solution nor does it investigate outside the direct system of interest. (Therefore in a worst case scenario, implementation of a ...
The 8D methodology, also known as Eight Disciplines Problem Solving, is a structured approach used to identify, analyze, and resolve complex problems or quality issues. Each "D" represents a step ...
Establish the team from different departments and choose a team leader. Clearly describe the problem in order to understand what went wrong. Stop the process, put a temporary fix in place (e.g., introducing 100% inspection) Brainstorm on finding the root cause(s) of the problem, why was is not detected. Choose and verify the permanent action plan.
8D Approach | 8D Problem-Solving Steps. The eight disciplines for process improvement or problem-solving are as follows: 8D Step - D1: Establish the Team. Identify team leader and team members. Establish a team of competent people with product/process knowledge. Cross-functional team-CFT members must be related to the concerned problem.
7S - SPIRIT - Transformation of the company culture - 7S is the basis of longterm improvement of company productivity at minimal cost, helps to eliminate waste and increase self-discipline. The top management engagement is a must. Examples of 5S implementation comming mainly from automotive in Japan and Europe.