- +91 98 7373 3515
- Whatsapp: +91 8800 72 32 11
- [email protected] [email protected]
- Quick Quote

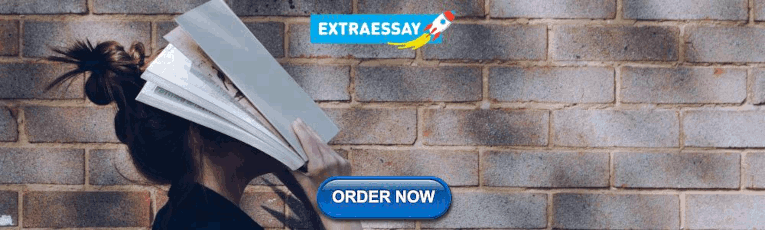
Quote Summary
You have no products in your cart.
- Shop by category
- E-Square Advantages
- LOTO Innovations
- Lockout Tagout Survey
- LOTO Policy & Program
- LOTO Procedure (MSP)
- LOTO Procedure Software
- LOTO Installation
- LOTO Training
- Online LOTO Courses
- LOTO Train-The-Trainer
- Gap Analysis/Audit
- Energy and Power
- Fertilisers
- Steel and Iron
- Off-Shore Projects
- Petrochemical
- Pharmaceutical
- Oil and Gas
- Ports and Dockyards
- Food Processing
- Construction
- Hospital Chains
- Retail and E-Commerce
- Hospitality
- Lockout Tagout Book
- Lockout Tagout Quiz
- LOTO Legislation
- OSHA Documentation
- NIOSH Documentation
- LOTO Case Study
- LOTO White Paper
- Group LOTO Procedure
- Lockout Tagout FAQ
- Lockout Tagout Videos
- Lockout Tagout
- Lockout Padlocks
- Lockout Tags
- Electrical Lockout
- Mechanical Lockout
- Lockout Tagout Kits
- Stations and Cabinets
- Related Products
- Customised LOTO

- Premier Lockout Safety Padlocks (PLSP)

- De-electric Padlocks

- Jacket Padlocks

- Cable Lockout Safety Padlocks

- Laminated Steel Padlock

- SS Lockout Padlocks

- Aluminium Padlocks

- Padlock Accessories

- Standard LOTO Tags

- Customised LOTO Tags

- Plain Color Tags

- Padlock Tags

- Tags on Roll / Box

- Safety Tags in a Box

- Laminated Tags

- Other Special Tags

- Lockout Hasp

- De-Electric Lockout Padlock

- Plug Lockout

- Blocking Bar Lockout

- Circuit Breaker Lockout

- Electrical Panel Lockout

- Electrical Lockout Kits

- Pin and Sleeve Lockout

- Fuse Lockout

- Valve Lockout

- Cable Lockout

- Mechanical LOTO Kits

- Blind Flange Lockout

- Lockout Padlock

- Cylinder Lockout

- Basic LOTO Kits

- Personal Lockout Kits

- Circuit Breaker LOTO Kits

- Mechanical / Valve LOTO Kits

- Electrical & Valve Combo Kits

- Other Lockout Kits

- Customised Lockout Kits

- Padlock Cabinets

- Key Cabinets

- Lockout Stations

- Open Lockout Stations

- Shadow Lockout Boards

- Group Lock Boxes

- Bags and Pouches

- MSDS Cabinets

- Confined Space Covers

- Hazard Communication

- Industrial Signages

- Safety Hooks and Cable Hangers

- Scaffolding Tags

- Shadow Boards

- Floor Stands

- Lockout Padlock Customisation

- Lockout Tags Customisation

- LOTO Kits Customisation

- Padlock/Key Cabinet Customisation

- Group Lock Box Customisation

- LOTO Stations Customisation

- Shadow Boards Customisation

- Open LOTO Stations Customisation

- Safety Poster Customisation

- Lockout PADLOCKS
- PLUG Lockout
- Key CABINETS
- BLIND FLANGE Lockout
- Lockout Tagout KITS
- PIN and SLEEVE Lockout
- MSDS CABINETS
- CONFINED SPACE Cover
- LOTO STATIONS
- CABLE Lockout
- Lockout BAG and POUCH
- ENERGY SOURCE ID Tags
- VALVE Lockout
- Lockout HASP
- LADDER Lockout
- Lockout SIGNS & LABELS
- CIRCUIT BREAKER Lockout
- CYLINDER Lockout
- SCAFFOLDING Tags & Holder
- Lockout TAGS ROLL/BOX
- Lockout SAFETY TAGS
- SHADOW LOTO Station
- FUSE Lockout
- LOTO POSTERS/BANNERS
- ELECTRICAL PANEL Lockout
- OPEN Lockout Station
- PNEUMATIC Lockout
- STEERING WHEEL Covers
- GROUP Lockout Box
- Padlock CABINETS
- LOTO ACCESSORIES
- CABLE Hangers
A Roadmap to LOTO Excellence, as Charted by OSHA!
Home > Learn Lockout Tagout > OSHA Case Study 1 – Printing Press Roll Cleaning
OSHA Case Study 1 - Printing Press Roll Cleaning
A printing press produces printed materials as its normal production function. The printing press's rollers have to be cleaned periodically during the work shift to ensure quality control. In this scenario, the press is not shut down for the cleaning operation. The printing press is Energized and its rollers continue to spin at a very high speed. In order for employees to clean the rollers they must bypass the printing press's machine guards, and use rags to clean the rollers. This exposes them to serious, ingoing nip point hazards created by the rollers. Severe laceration or amputated fingers could result if the rag or an employee's hand were to get caught in the rollers or in an area between the rollers and a fixed part of the machine. Although the employer has a Lockout/Tagout program for Servicing and/or Maintenance of the printing presses, for this particular cleaning operation the employer believes that Lockout/Tagout Procedures do not need to be implemented. According to the employer, this cleaning operation is exempt from Lockout/Tagout requirements because it falls under the minor servicing exemption and therefore the employer allows the equipment to remain operating during the cleaning operation. Remember, as stated above, the employees are still exposed to the Hazardous Energy of the printing press' during the cleaning operation.
Is this printing press roll cleaning activity covered by the Lockout/Tagout standard?
The employer argues that the roll cleaning activity is routine, repetitive, and integral to the production operation and that Lockout is not required because the minor Servicing exception described in 1910.147(a)(2)(ii) is applicable. Is the employer correct?
Book a Consultation!
Contact our safety experts today for your free, no-obligation consultation.
First Name*
State/Province
Zip/Postal Code*
Email Address*
Join our Newsletter
Empower me with the latest LOTO tips, news and updates.
Explore E-Square

Explore our extensive 1400+ LOTO devices

LOTO SERVICES
Ensure compliance & systematic implementation

LOTO TRAINING
Customized on-site, online & virtual-live sessions

LOTO SOFTWARE
Cloud-based solution for LOTO procedure writing
- E-Square Alliance Pvt. Ltd. 512, New Delhi House, Barakhamba Road New Delhi - 110001, India
- +91 8800 72 32 11 (Call)
- +91 8800 72 32 11 (Whatsapp)
- +91 98 7373 3515 (Technical Query)
- [email protected] [email protected]
Send Message
Worldwide Delivery
Wide Choice
Customisation Available
Direct Technical Support
COPYRIGHT © 2024 E-SQUARE ALLIANCE PVT. LTD. ALL RIGHTS RESERVED.
- Privacy Policy
- Slavery Policy
Download Data Sheet
Download Now
Any Questions?
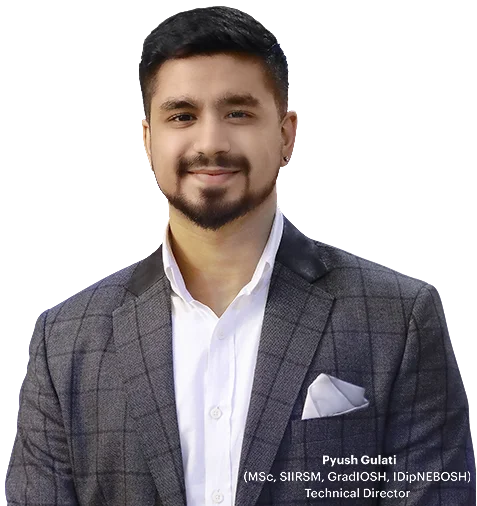
In Lockout Tagout, every detail counts. Let’s discuss yours.
Hi! I'm Pyush, the Technical Director at E-Square Please write to me here if you have any questions or require any kind of assistance. We will get back with an answer ASAP !
Case Study 1: Printing Press Roll Cleaning
Incorrect. In this case, the employer is not correct.
The minor servicing exception does not apply. Even though the roll cleaning activity takes place during normal production operations and is routine, repetitive, and integral to the production operation, the employer has not implemented alternative measures which provide effective protection from the ingoing nip points of the press rolls. Employees instead are required to bypass a machine guard, which is required by Subpart O of 29 CFR 1910 , and place their hands and cleaning rags into the press's danger zone. In the absence of alternative protective measures, this cleaning task is a servicing or maintenance activity that is covered by 1910.147 .
In summary, for the minor servicing exception to apply, each and every element of the exception must be met. In this case, the work is not being performed using alternative measures that provide effective employee protection.
For more information: Read the September 16, 1992, letter of interpretation to Mr. John Runyan of the Printing Industries of America, Inc., for details on how to use safe alternative measures for printing presses.
<< Return to Case Study Discussion | Next Case Study >>
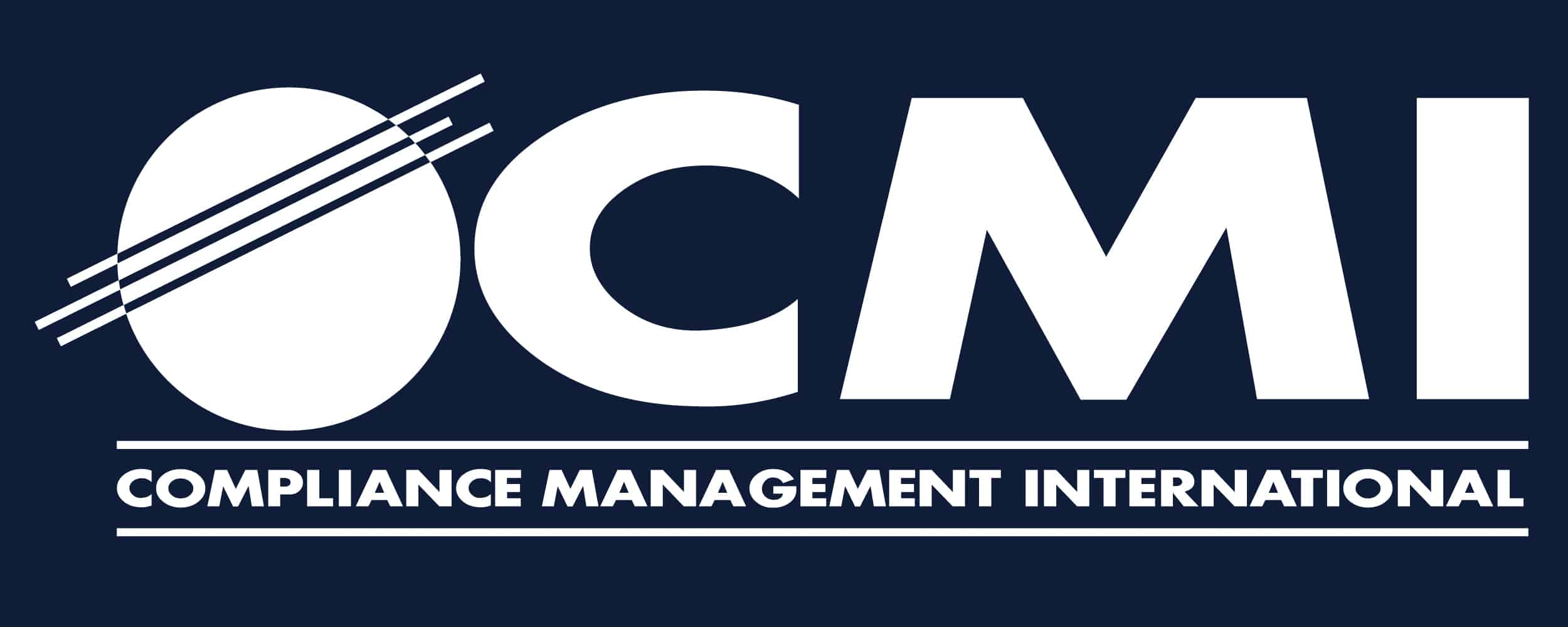
OSHA Case Study – Lockout Tagout and the Minor Servicing Exemption
Sep 20, 2023 | Health and Safety , Newsletter
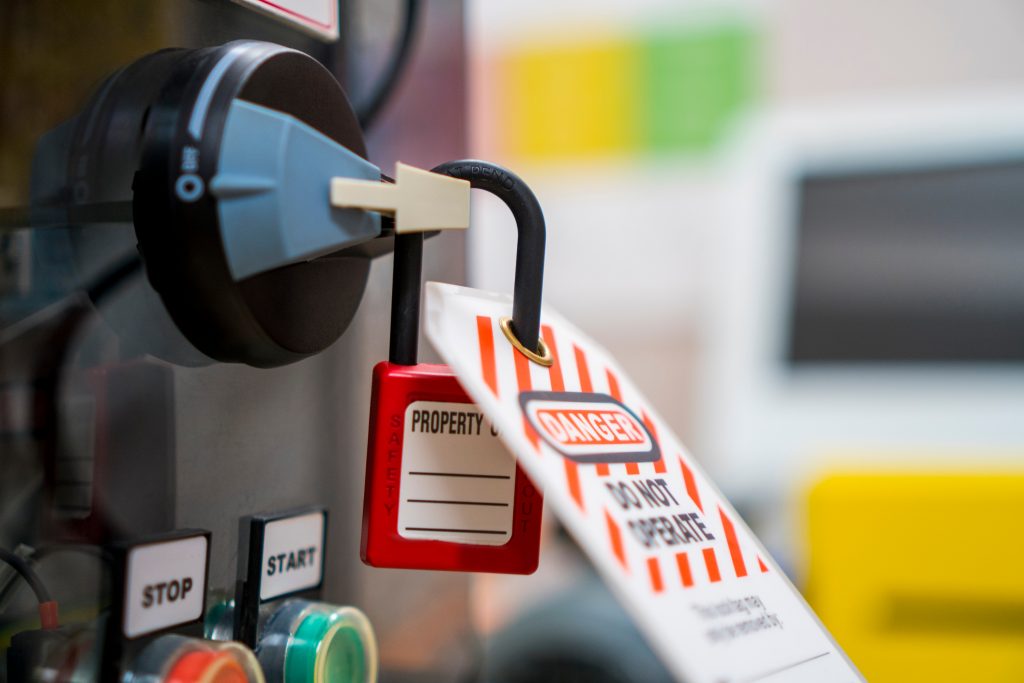
In this article, we are sharing an OSHA Case Study that explores the topics of lockout tagout, the minor servicing exemption, and machine guarding. Read on to test your understanding of when and how OSHA’s minor servicing exemption can be applied.
The Case Study:
A printing press produces printed materials as its normal production function. The printing press’s rollers have to be cleaned periodically during the work shift to ensure quality control.
In this scenario, the press is not shut down for the cleaning operation. The printing press is energized and its rollers continue to spin at a very high speed. In order for employees to clean the rollers, they must bypass the printing press’s machine guards, and use rags to clean the rollers. This exposes them to serious, ingoing nip point hazards created by the rollers. Severe laceration or amputated fingers could result if the rag or an employee’s hand were to get caught in the rollers or in an area between the rollers and a fixed part of the machine.
Although the employer has a lockout/tagout program for servicing and/or maintenance of the printing presses, for this particular cleaning operation the employer believes that lockout/tagout procedures do not need to be implemented. According to the employer, this cleaning operation is exempt from lockout/tagout requirements because it falls under the minor servicing exemption and therefore the employer allows the equipment to remain operating during the cleaning operation.
Remember, as stated above, the employees are still exposed to the hazardous energy of the printing press’ during the cleaning operation.
Is this printing press roll cleaning activity covered by the Lockout/Tagout standard? Yes or No?
If you said Yes:
You are correct. Even though this roll cleaning activity takes place during normal production operations, the employee is required to bypass a machine guard and/or place part of their body into a point of operation or associated danger zone. The cleaning operation is therefore covered as service and maintenance which took place during normal production operations. Therefore, the requirements of 29 CFR 1910.147 apply.
The employer argues that the roll cleaning activity is routine, repetitive, and integral to the production operation and that lockout is not required because the minor servicing exception described in 29 CFR 1910.147(a)(2)(ii) is applicable. Is the employer correct? Yes or No?
If you said No:
You are correct. The minor servicing exception does not apply. Even though the roll cleaning activity takes place during normal production operations and is routine, repetitive, and integral to the production operation, the employer has not implemented alternative measures which provide effective protection from the ingoing nip points of the press rolls. Employees instead are required to bypass a machine guard, which is required by Subpart O of 29 CFR 1910, and place their hands and cleaning rags into the press’s danger zone. In the absence of alternative protective measures, this cleaning task is a servicing or maintenance activity that is covered by 29 CFR 1910.147.
In summary, for the minor servicing exception to apply, each and every element of the exception must be met. In this case, the work is not being performed using alternative measures that provide effective employee protection.
In this case study, was your understanding of the standard challenged? Understanding and correctly applying OSHA standards to real, work place scenarios can be complicated. Many of OSHA’s regulations are interconnected, especially when it comes to Lockout Tagout, exemptions to Lockout Tagout, and thus, their reliance on adequate machine safeguarding methods.
Lockout Tagout exceptions (i.e., the minor servicing exception) can only be applied when the activity meets certain criteria first. An OSHA standard interpretation letter provides further explanation on when the exception can be applied:
The activity must take place during, and must be inherent to, normal production operations (which include the utilization of a machine or piece of equipment to perform its intended production function). These functions would be carried out by employees with the machine or equipment energized. They may include minor servicing activities (i.e., clearing of jams; minor cleaning or adjustments; lubrication) that safely take place while the process is performed in situations where extensive disassembly of the machinery/equipment is not required.
The activity must be:
1. Routine: The activity must be a regular course of procedure and be in accordance with established practices.
2. Repetitive: The activity must be repeated as part of the production process or cycle.
3. Integral: The activity must be inherent to the production process.
If all of these apply, then the employer can determine how to use alternative measures to provide effective protection from the hazardous energy. Alternative measures can include various applications of equipment safeguarding, as described in OSHA Subpart O: Machinery and Machine Guarding. Machine guarding can include fixed guarding, interlocks, and ensuring exclusive control by the person executing the exemption procedure.
Additionally, procedures for alternate measures should be developed and documented. The procedures must define how and when the exception will be applied and executed. Following development, employees who will use the procedure must be trained in them to ensure proper understanding and use.
CMI has a team of Health and Safety experts that can work with your team to develop equipment-specific Lockout Tagout Procedures, assess where minor servicing exceptions can be applied to your operations, and develop standard operating procedures for minor servicing activities. Our team can also evaluate equipment to determine where adequate machine safe guarding is in place and identify areas that may need improvement. We routinely conduct various trainings to ensure employers are in compliance with the control of hazardous energy standard, including Lockout Tagout for Affected employees, Lockout Tagout for Authorized employees, and hands-on periodic inspections for the execution of Lockout Tagout Procedures.
Written by Rebecca Caffrey, CSP
- Company News
- Construction Safety
- Environmental
- Health and Safety
- Industry News
- Regulatory Updates
No products in the cart.
Printing Press Cleaning
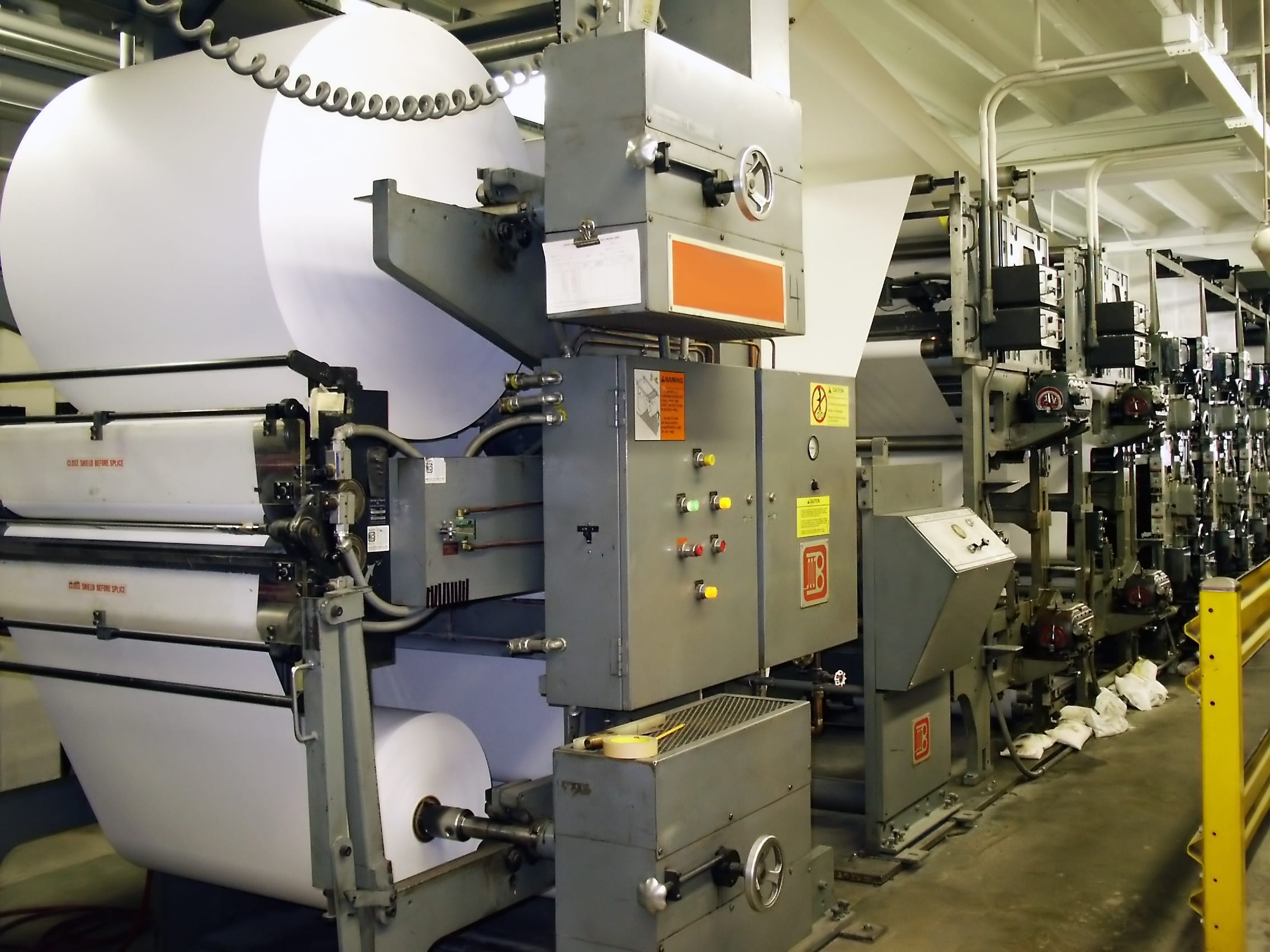
About Printing Press Cleaning
Are hughes environmental technicians certified.
Yes! Working with Hughes, you can expect technicians that are trained, certified and up-to-date on common best practices. We have an OSHA trainer on staff, and our technicians have been through OSHA 10- or 30-hour training. We also have Council-certified Indoor Environmentalists (CIE) and Council-certified Microbial Remediators (CMR) on staff. For a full list of certifications please visit our About page.
Do you perform work nationwide?
Yes! We are a National Service provider that is familiar with proper facility cleaning solutions. No matter where you are located, we have your facility cleaning needs covered. Contact us today to learn more.
Do you provide project reports after each cleaning?
Yes! After each project, Hughes can create a project report for you summarizing the work that was done. Each report will include before and after pictures. Please tell your account rep that you want a project report!
Explosion Hazard
Increase efficiency, bacterial growth, download statement of qualifications, printing press cleaning benefits, related services.
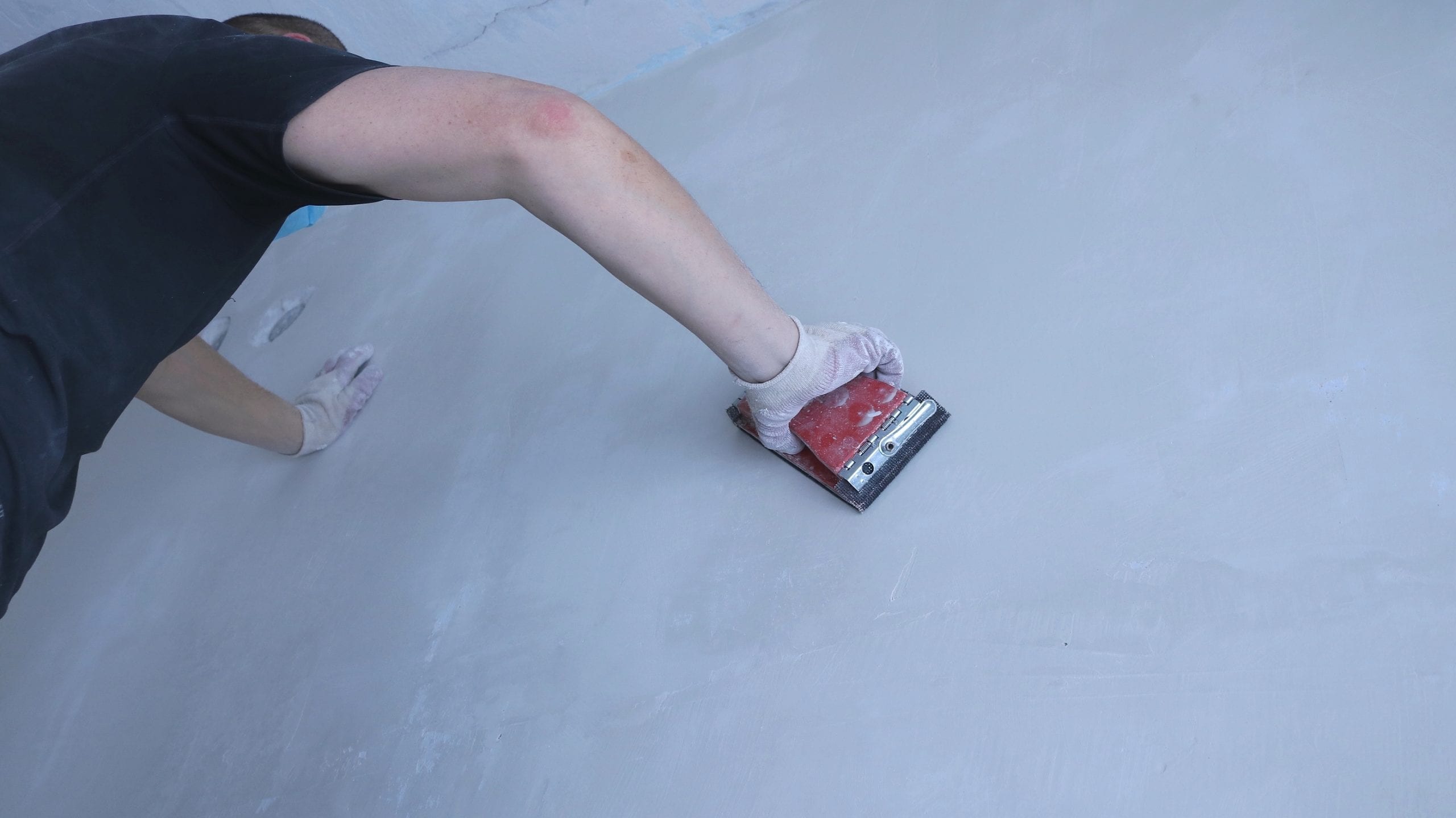
Hand Wiping

Heat Exchanger or Furnace Cleaning
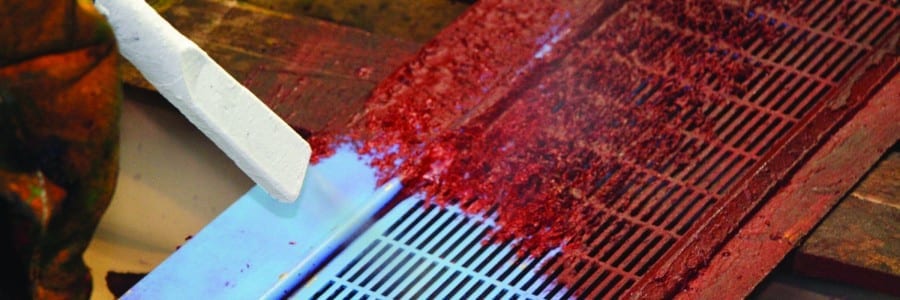
Media Blasting Services
Featured products.
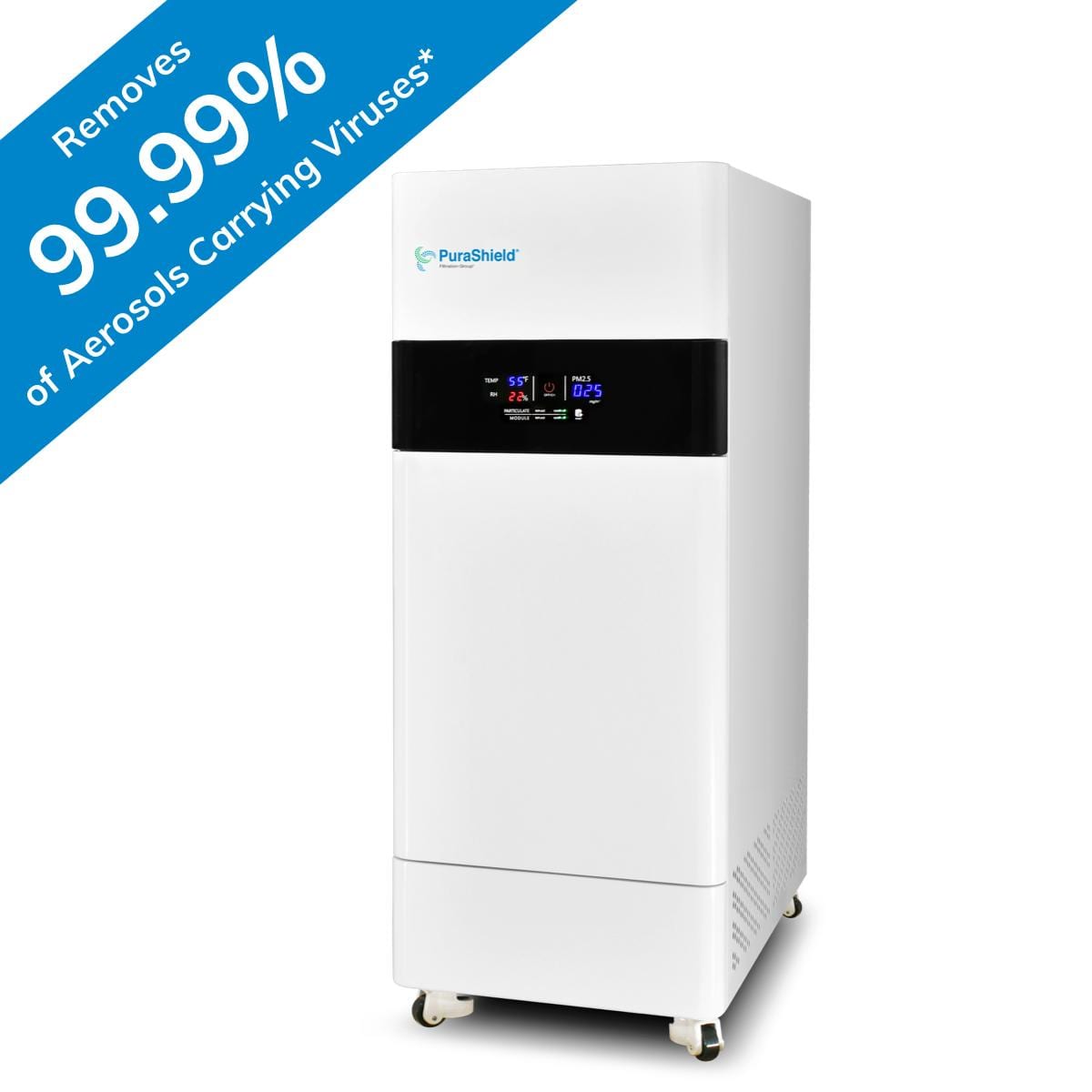
PuraShield Smart 500
PuraShield Smart 500 Molecular Air Scrubber PuraShield 500 fits powerful...
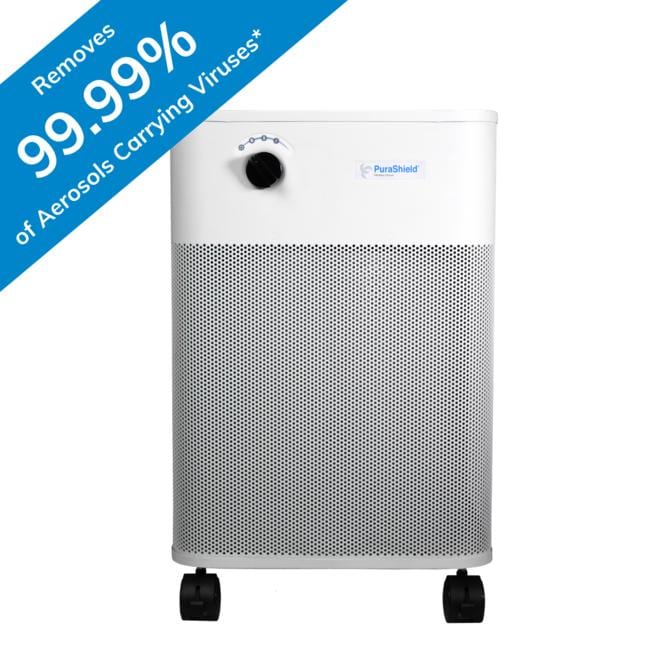
PuraShield 500
PuraShield 500 Molecular Air Scrubber PuraShield 500 fits powerful air...
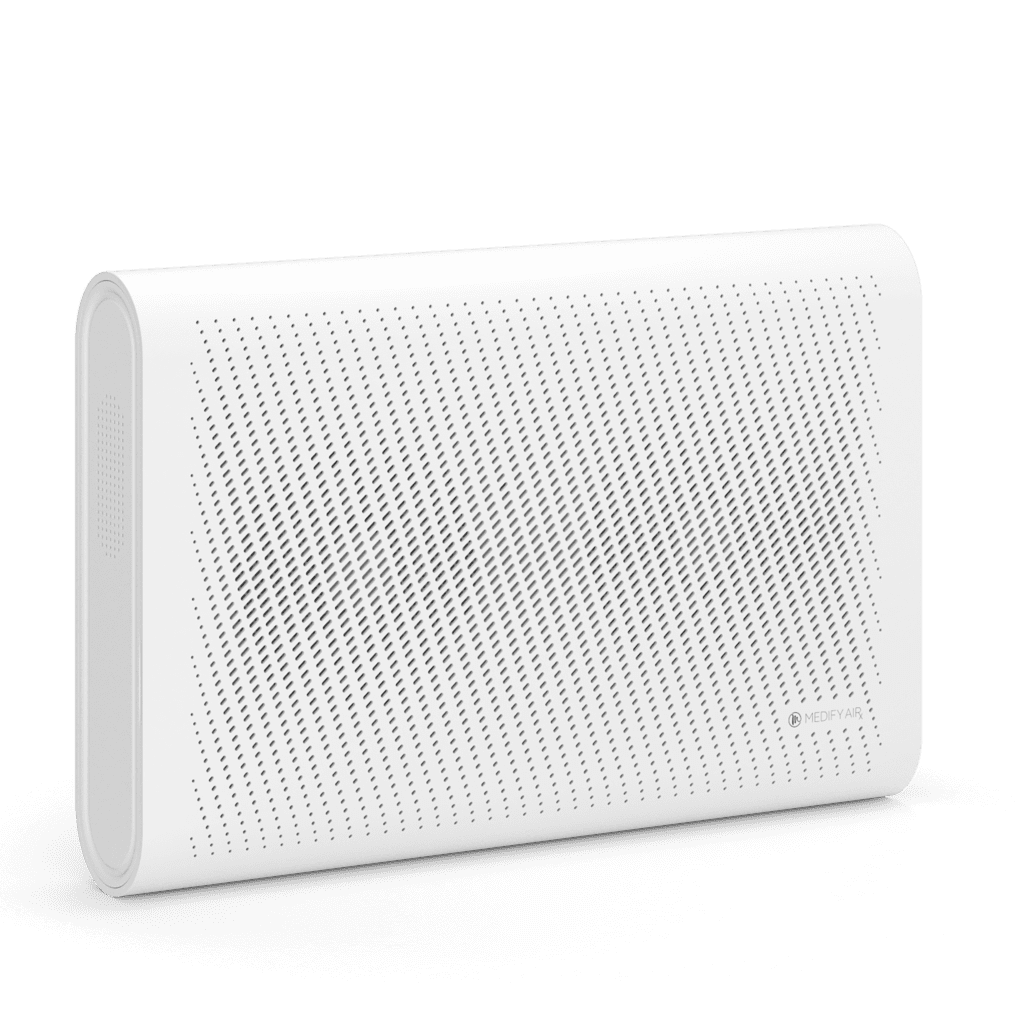
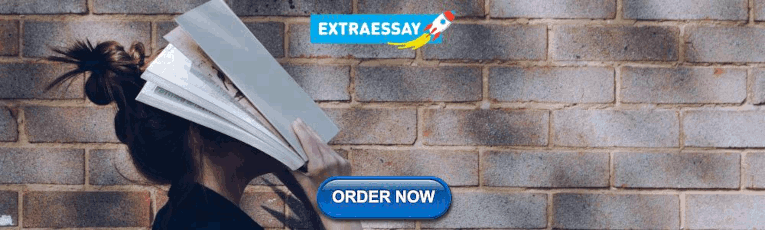
MA-35 Air Purifier
MA-35 Air Purifier The Medify Air MA-35 uses True HEPA...
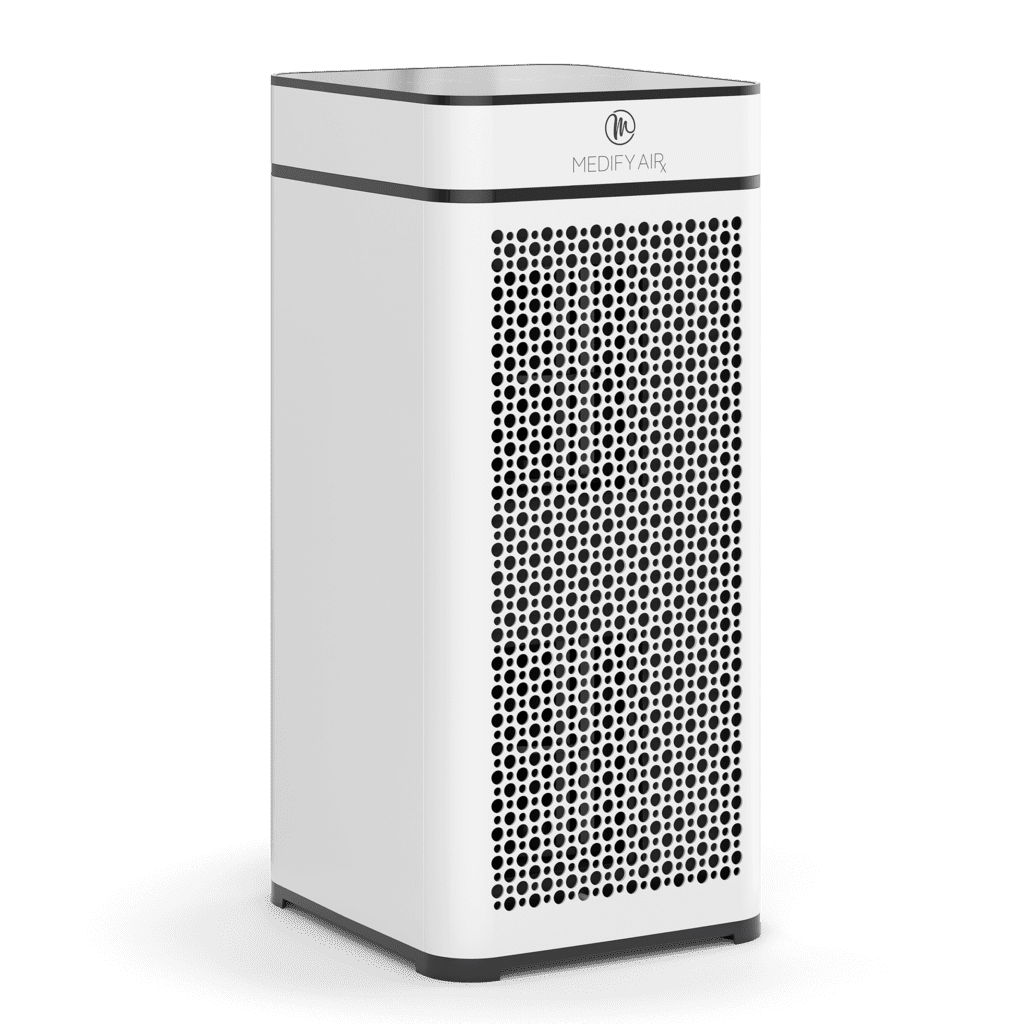
MA-40 Air Purifier
MA-40 Air Purifier The Medify Air MA-40 uses H13 True...
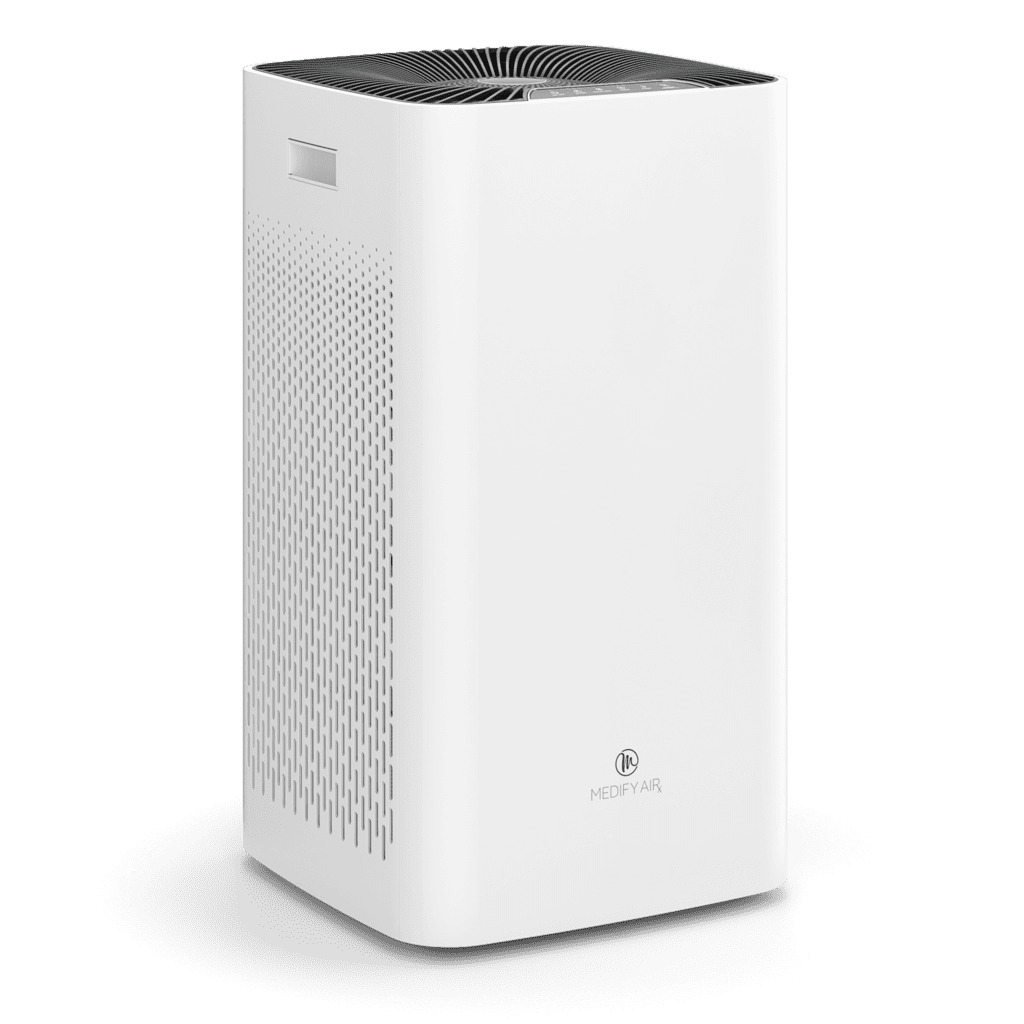
MA-112 Air Purifier
MA-112 Air Purifier The Medify Air MA-112 uses True HEPA...
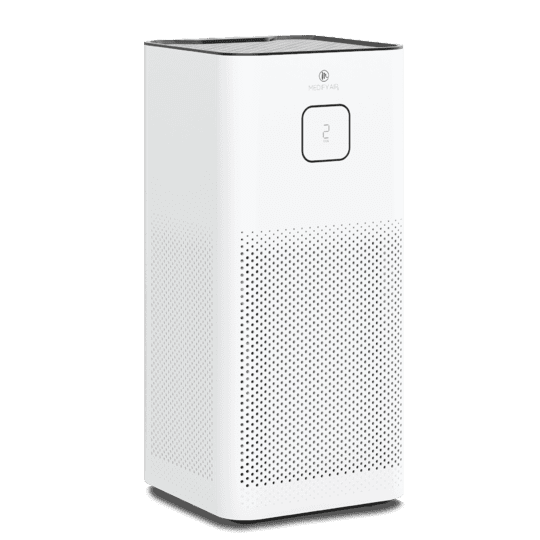
MA-50 Air Purifier
MA-50 Air Purifier Medify MA-50 has a perfect blend of...
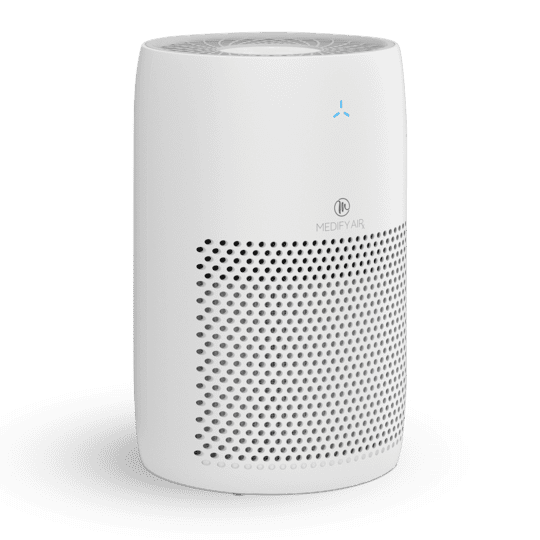
MA-22 Air Purifier
MA-22 Air Purifier Equipped with 3-stage HEPA H13 filtration that...
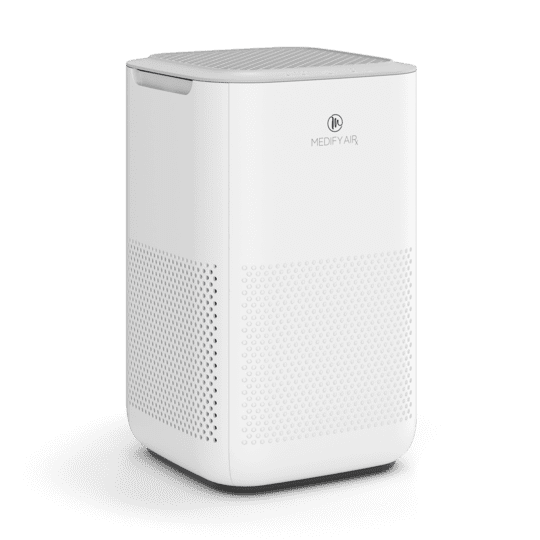
MA-15 Air Purifier
MA-15 Air Purifier Medify MA-15 is applauded for its compact...
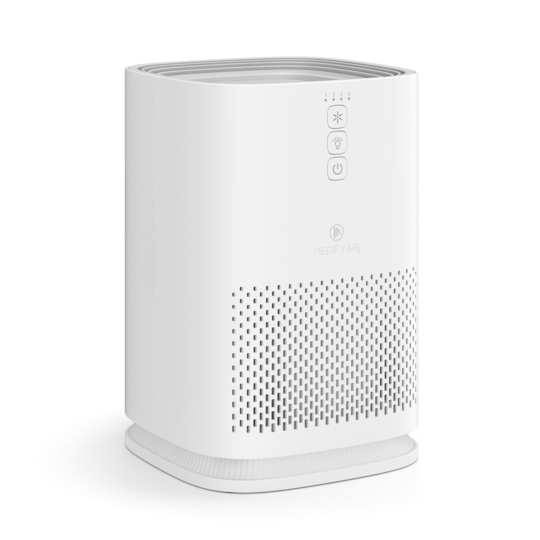
MA-14 Air Purifier
MA-14 Air Purifier The most powerful tabletop air purifier on...
Request a Quote
Have a question about hughes environmental we are here for anything you may need. need a quote we’ll have it within 24 hours of your request., corporate office, newsletter subscribe.
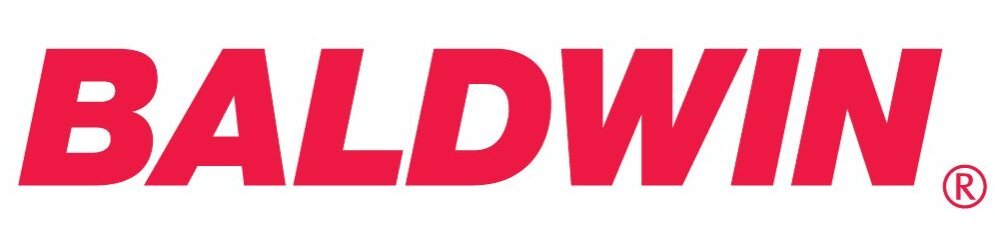
PREPAC® Advanced Cleaning Rolls For Sheetfed Offset Printing At Duma Druck
Outstanding cleaning features are keys to optimized productivity: Learn how German printer Duma Druck discovered this, saving time and production costs by using Baldwin’s PREPAC Advanced roll cleaning-cloth solution.
Customer: Duma Druck, established 1983 is situated in Wolfsschlugen, close to Stuttgart, Germany, is a commerial offset and digital printer well known for a consistent quality management. Challenge: Reduce the waste of paper, time and production costs. Solution: Baldwin PREPAC® Advanced cleaning rolls. Benefits: No more fluff on the impression cylinder, no dripping or toning, easy handling and increased production uptime thanks to enhanced cleaning efficiency leading to shorter wash times.
Read the full case study now - click the image below to access the full PDF:
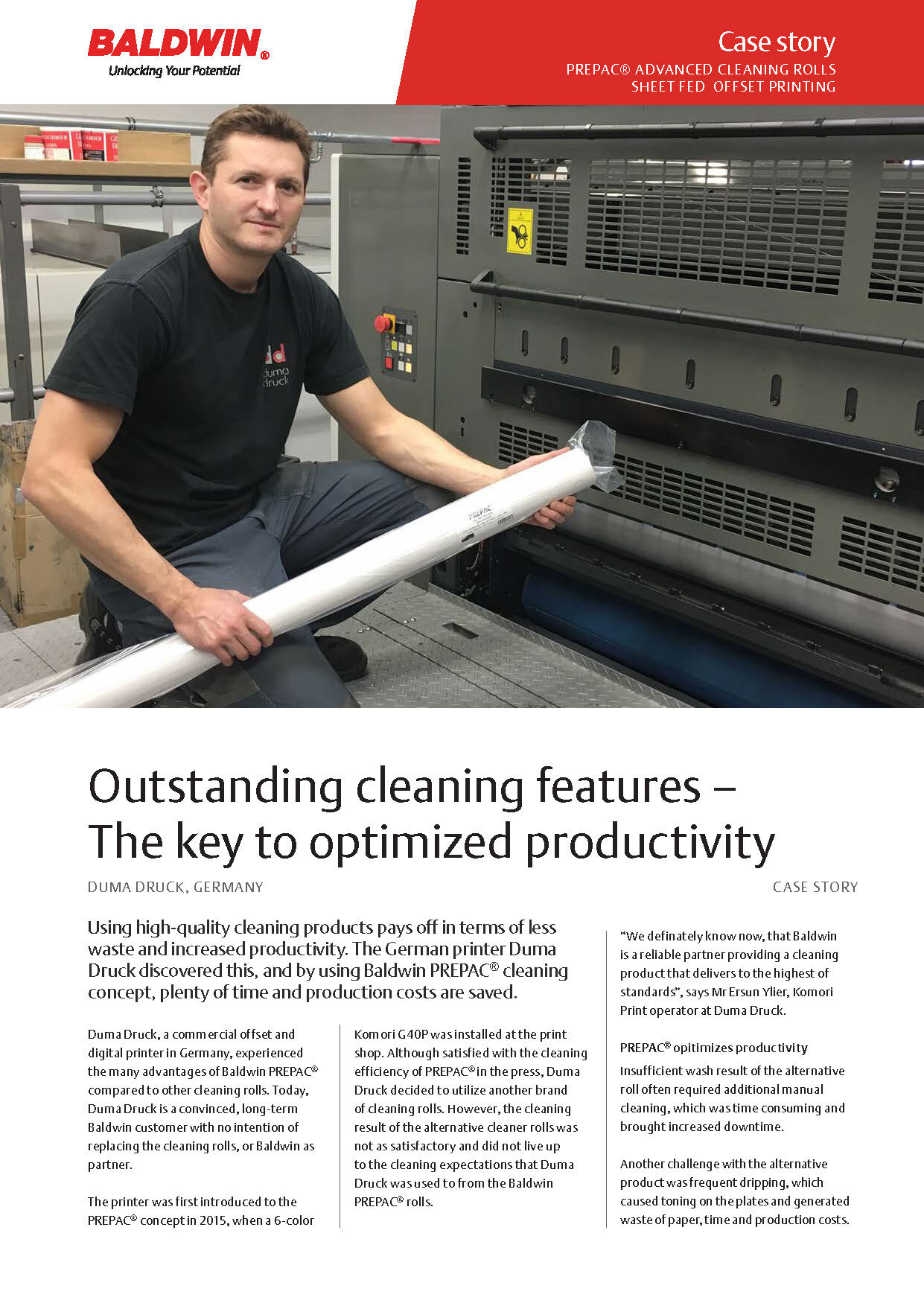
ABOUT US | CAREERS | PRIVACY NOTICE | BALDWIN GMBH TERMS & CONDITIONS | UK TAX STRATEGY | COOKIE SETTINGS youtube | twitter | LinkedIn
Baldwin Technology Co. is a proud member of the Barry-Wehmiller family of companies
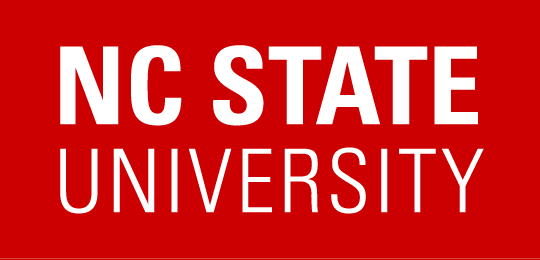
BioResources
- About the Journal
- Authors & Reviewers
- How to Self-Register
- Full Site Navigation
- Editorial Board
- Meet the Staff
- Editorial Policies
- General Instructions
- Ethics & Responsibilities
- Article Preparation
- Submission Instructions
- Acknowledgment of your Peer-Reviewing
- Writing Style Suggestions
- Reviewer Guidelines
- Back and Current Issues
- Scholarly Reviews
- Special Conference Collection Issues
- Competition Print Edition
- FRC: Pulp and Paper Fundamental Research Symposia Proceedings
- Paper Manufacturing Chemistry
- BioResources Early Career Investigator Award
- Distance Education: Online Masters Degree & Individual Courses
- Upcoming Conferences
- Hands-On Courses
- Affiliate Journal
A method of minimising paper requirements for offset printing
The conducted study desired to increase the accuracy of estimating paper quantity requirements for printing. Changes in press construction and auxiliary equipment help reduce the total waste during production; however, typical estimation methods do not take these changes into account. By specifying the number of important job parameters and using a dimensional analysis approach, it was possible to devise a model of waste sheet quantity estimation better suited for current production practices. Using this model, it is possible to reduce the quantity of paper required for a particular print run as well as better predict the total waste sheet quantity. As a result, less paper may be ordered, stocked, and utilised in production. Using this model, a printing house may develop unique technological allowance standards for their particular substrates and products. The method of waste quantity prediction presented in this paper is also suitable for establishing a quality control system.
Full Article
A Method of Minimising Paper Requirements for Offset Printing
Jacek Hamerlinski a, * and Yuriy Pyr’yev b
Keywords: Offset printing; Paper requirements; Paper waste; Dimensional analysis
Contact information: a: Research & Development Centre for the Graphic Arts, Miedziana 11, 00-958 Warsaw, Poland; b: Institute of Mechanics and Graphic Arts, Faculty of Production Engineering, Warsaw University of Technology, Konwiktorska 2, 00-217 Warsaw, Poland;
* Corresponding author: [email protected]
INTRODUCTION
In sheetfed offset printing, paper is always wasted in press setup and production errors (rejection via quality control procedures). In addition, the finishing processes require an additional allowance (this quantity is not affected by the printing process and is not covered in this paper). This means that during the printing process for a particular job, additional paper should be provided to account for “unsalable” production (Kipphan 2001). The additional paper provided is subsequently the technological allowance required to produce the final product. The additional quantity is calculated with respect to run length ( i.e. , the required number of final products) and printing process characteristics ( e.g. , type of press, number of colours). Formulae for such calculations are relatively simple and use statistical data from various sources, typically within one country (BPIF 2012; COBRPP 1986; Samarin 2002). Currently, there is widespread use of multi-colour presses, which use various automation systems (DeJidas and Destree 2005; Kipphan 2001) designed to shorten the makeready (press setup) time and reduce overall waste (Kipphan 2001). The industry-standard formulae have been found to be too pessimistic. For example, BPIF 2012 assumes that 500 waste sheets are required for each setup in four-colour printing. For that reason, paper quantity requirements have been calculated at a more drastic level than necessary. As the paper returns from production, sometimes it cannot be reused, and the surplus quantity drains both natural resources and company cash.
It must also be noted that waste paper (and any paper no longer suitable for printing after storage) must be processed, which consumes a varying amount of additional resources depending on the method selected (Hubbe 2007; 2014). Devising a method to limit the unnecessary allowance would make printing plants more sustainable. This particular study analyses the potential dependencies of paper waste on different factors, including printing process variables and the job data. The novel approach presented here may be useful as a starting point for creating company-specific models of estimating paper quantity for sheetfed offset printing process.
Estimating Paper Waste in Offset Printing
Basic estimation of paper waste in the sheetfed printing process is calculated using the following equation (Samarin 2002),
where n w is the estimated number of waste (unsalable) sheets, k is the number of job colours (4 in the case of CMYK offset printing), n is the required quantity of printed sheets, N m is the waste sheet quantity required for makeready, and p p is the percentage of waste expected during the press run.
The values of N m and p p can differ depending upon the press type and configuration, paper type, quality requirements, and quantity range (Samarin 2002). In some cases, the outcome is multiplied by specific correction factors that depend on paper weight (grammage), sheet size, press equipment, etc. (COBRPP 1986). If a press run requires front and back printing, the method of predicting the waste quantity depends on the selected method of second side printing, number of plate sets required, or using a press equipped for single-pass double-sided printing (COBRPP 1986). Similarly, when the quantity required exceeds the durability of the offset plates used for printing, more makeready waste sheets must be provided (COBRPP 1986). The values for N m and p p are tabularised for convenience. To find an appropriate value, one must know which press will be used for printing the specified job, as well as what other conditions (such as the quality requirements) will apply.
The offset printing process is generally stable if set up properly (Kipphan 2001) and in a typical printing environment, one may assume that the press setup is the largest source of waste sheets during any print run. Notably, the predicted waste sheet quantity is directly proportional to the number of printed colours, meaning that setting up a four-colour (CMYK) job will generate significantly less waste than setting up a job including additional spot colours.
This correlation leads to overestimation of the waste quantity for many presses with five or more printing units, especially when such presses include automated functions such as plate changing, blanket washing, or pre-inking. These features not only shorten the makeready time (Kipphan 2001), but also reduce the number of waste sheets produced thanks to faster, more precise, and more repeatable performance of standard tasks. Because the cost of printing is the largest contributor to total production costs (DeJidas and Destree 2005), changes in this area can significantly affect the financial standing of the company.
EXPERIMENTAL
Theoretical Problem Analysis
A study undertaken in the Research and Development Centre for the Graphic Arts (COBRPP) was aimed at reviewing the current standards of computing the technological allowances for sheetfed offset printing in correlation to the actual numbers of waste sheets registered in commercial print runs. During this study, it was found that the estimation of waste sheets was generally too high and that the same quantity of waste was predicted for a wide variation of press runs. Therefore, a different approach for predicting the waste sheet quantity has been developed. The new method of predicting the waste sheet quantity can make waste estimates more realistic, inherently lowering the demand for natural resources. Such an approach was based on the notion that there are several common factors affecting the printing process, and it should be possible to find a relationship between appropriate similarity numbers using dimensional analysis.
A number of parameters describing a given print run were analysed. The parameters selected should be known at the moment of estimation and/or registered during the print run. The parameters taken into account are set forth in Table 1, where M is mass, L is length, and T is time.
Table 1. A List of Parameters for Estimating Waste Sheet Quantity
With the exception of ink tack, all of the aforementioned parameters are regularly used in ordering and job description or costing. The ink tack, or a force required to split ink layers ( e.g. between the inking rollers), is an important parameter of the offset printing process, influencing many of the effects observed in printing (Gujjari et al . 2006; Mangin and Silvy 1997; Mattila and Passoja 2006; Vähä-Nissi et al . 2010). Ink tack is measured using different methods (Hamerlinski and Pyr’yev 2013; ISO 12634 1996), and these methods establish many different units of ink tack. As a result, the ink tack values quoted in different papers are not directly comparable (Massolt 2003), but instead are consistent for any measurement method and may also be verified in-house. The physical dimension of ink tack results from its understanding as the ink-splitting work required per area unit (Shakhgeldyan and Zagarinskaya 1975).
Furthermore, it is important to note that all the parameters may have only positive values. Because ISO 12647-2 describes several types of paper used for printing, such as 5 or even 8 (ISO 12647-2 2004; 12647-2 2013), it was decided that the function should also be different for each paper type. This study concentrated on the three types of paper most widely used in sheetfed offset printing, i.e. , uncoated paper (equivalent to ISO type 4 in ISO 12647-2), coated paper (equivalent to ISO types 1 and 2), and cardboard. It also assumed that the required print quality is an average standard, with no exceptionally high or low deviations. Therefore the quality level was not considered a factor in the model. However, adding a scaling coefficient based on expected quality should be sufficient in practical cases.
Theoretical Formula Approach
Having established the set of characteristic parameters, dimensional analysis was used to formulate a relationship between the parameters and the number of waste sheets for a given print run, in the form of,
where δ is the waste sheet coefficient (dimensionless) expressed as a ratio of waste sheet quantity to the number of copies printed, and p i is a characteristic parameter of job or printing process.
Assuming that the function is a product of power monomials, it may be expressed as,
where C 1 , A, B, …, J are constants. Using dimensional analysis leads to the theoretical formula:
Data obtained from actual press runs (using presses with 4, 5, and 6 units) in Polish printing houses were then used to calculate the values of the constants. The formula may be rewritten as
RESULTS AND DISCUSSION
Based on 120 collected commercial job data printed with sheetfed offset presses, the multidimensional linear regression was applied for a subset of jobs printed on a particular type of paper, allowing to calculate the values of constant C 1 and exponents A, B, C, E, H, and I for each paper type separately. It was discovered with the help of t -statistics that some parameters specified in Table 1 are statistically irrelevant for certain paper types; in such case a new model, omitting the irrelevant parameter, was analyzed. The model was considered correct only when all t -statistics exceeded critical values and the coefficient of determination was higher than 0.8 for the analytical formula. As a result, the models for the different paper types are inherently different, as shown in Table 2. The regression analysis resulted in a quite simple model for cardboard printing.
Table 2. Formulae for Estimating Waste Sheet Quantity for Different Paper Types
The estimated number of waste sheets may easily be derived from these equations by recognising that n w = δn . Essentially, the relationship between n w and δ entails that by adding 1 to the exponent of n in the equation from Table 2, one can obtain the formula for the waste sheet quantity.
The verification consisted of comparing the actual waste sheet quantity with the theoretical quantity computed using the appropriate formula for each case used in the linear regression model. The Root Mean Square (RMS) deviation of theoretical values from the actual figure is shown in Table 2 as a percentage of actual values.
Interestingly enough, regarding cardboard, the number of colours printed has no influence on the estimated quantity of waste sheets. For all types of paper, the exponents for quantity and number of colours vary drastically, suggesting that the number of waste sheets is in fact not directly proportional to the number of colours printed. The R 2 values indicate that these models are efficient enough to be used in industrial practice, a claim further supported by the values of the deviation of the root mean square from the actual print run data. The highest accuracy for the model was observed when studying coated paper.
Finally, to verify the model, the formulae have been used to calculate the expected waste quantity for some print runs not used in the linear regression. In comparison to standard waste sheet estimating methods (COBRPP 1986; Samarin 2002), it was found that the new model minimises the quantity of paper required for printing. In most of the comparative cases (taken from the number of experiments not used for linear regression analysis) depicted in Fig. 1, the quantity of waste sheets estimated using the new model was the most accurate in predicting the actual waste sheet quantity registered during the print run. Additionally, the waste sheet figures produced by the new model were consistently lower than any of the other models tested. The new model also properly predicted an unusually high quantity of waste associated with printing on cardboard (case 6), whereas the other methods produced results much lower than the actual value (Fig. 1). In case 5, the estimated waste sheet quantity was higher than not only the actual value, but also the quantity estimated by other methods (Fig. 1). However, that particular case used UV varnishing, which could have affected the credibility of the averaging of the ink consumption and ink tack required for calculation, according to the developed model. Nevertheless the model is suitably close to the experimental data even it such a case.
Table 3. A List of Parameters for Test Print Runs
The result of the comparison is shown in Fig. 1. This radar plot shows an actual quantity of waste sheets compared with three methods of estimating the waste quantity, “Theoretical” corresponding to the model discussed in this paper. It may be observed that it matches the actual figures better than the other two models.
Fig. 1. A comparison of different standards of waste sheet calculations vs . actual values from a sample of eight print runs in Poland
CONCLUSIONS
- Using the discussed method of estimating waste sheet quantity for a given sheetfed offset print run, it is possible to limit the quantity of paper for production, saving capital outlay and reducing environmental impact. The method is particularly suited for multi-colour sheetfed offset printing and is feasible for both short and long print runs. Its practical application will depend on the number of available data for analysis, and on the verification of basic assumptions regarding quality, work practices etc.
- The presented model is adaptable to the particular conditions of any printing house, by allowing an analysis of data gathered from the production runs for more precise estimation of the waste quantity in subsequent jobs. The results may be periodically reviewed to reflect changes in equipment, quality requirements, operators’ experience, etc. Most spreadsheets used for reporting and analysing various aspects of production management are capable of performing the calculations required for this model.
- The method is also suitable as an input for statistical quality control (SQC) and the various indicators used in “lean” production management systems.
REFERENCES CITED
BPIF Standard Document (2012). Allowances for Overs/Unders and Wastage , British Printing Industries Federation, Coventry, UK.
COBRPP (1986). “Materialy Pomocnicze do Opracowania/Weryfikacji Zakładowych Normatywow Zuzycia i Norm Ubytkow Oraz Systemu Rozliczen Materialow Poligraficznych (Supporting Information for Setting Up and Verifying Technical Allowances, Waste Sheets and Substrate Accounting System),” Branzowy Osrodek Normalizacji, Branzowy Osrodek Informacji Naukowej, Technicznej i Ekonomicznej, Warsaw, Poland.
DeJidas, L.P., and Destree, T. (2005). Sheetfed Offset Press Operating , GATF Press, Sewickley, PA.
Gujjari, C., Batchelor, W., Sudarno, A., and Banham, P. (2006). “Estimation of ink tack in offset printing and its relationship to linting in offset printing,” Proceedings of TAPPI International Printing and Graphic Arts Conference .
Hamerlinski, J., and Pyr’yev, Y. (2013). “Modelling of ink tack property in offset printing,” Acta Poligraphica 1(1), 31-40.
Hubbe, M.A. (2007). “Incinerate, recycle, or reuse?,” BioResources 2(1), 1-2.
Hubbe, M.A. (2014). “Recycling paper recycling,” BioResources 9(2), 1828-1829.
ISO 12634 (1996). “Graphic technology – Determination of tack of paste inks and vehicles by a rotary tackmeter,” International Standards Organization , Geneva, Switzerland.
ISO 12647-2 (2004). “Graphic technology – Process control for the production of halftone colour separations, proof and production prints – Part 2: Offset lithographic process,” International Standards Organization , Geneva, Switzerland.
ISO 12647-2 (2013). “Graphic technology – Process control for the production of halftone colour separations, proof and production prints – Part 2: Offset lithographic process,” International Standards Organization , Geneva, Switzerland.
Kipphan, H. (2001). Handbook of Print Media , Springer Verlag, Heidelberg/Berlin.
Mangin, P.J., and Silvy, J. (1997). “Fundamental studies of linting: Understanding ink-press-paper interactions non-linearity,” TAGA Proceedings, Technical Association of the Graphic Arts , p. 884.
Massolt, P. (2003). Keep Your Tack on Track , VIP Publications, Testprint, Cherry Hill, NJ.
Mattila, U., and Passoja, S. (2006). “Factors controlling adhesion and ink tack in HSWO (Heatset web offset),” Proceedings of International TAPPI Printing and Graphic Arts Conference .
Samarin, Y. (2002). Normativy Razkhodovanya Osnovnykh Poligraficheskikh Materialov (Standards for Production Usage of Graphic Arts Materials), Moscow State Print University, Moscow.
Shakhgeldyan, B. N., and Zagarinskaya, L. A. (1975). Poligraficheskiye Materyaly (Graphic Arts Materials) , Izdatelstvo Kniga, Moscow.
Vähä-Nissi, M., Kela, L., Kulachenko, A., Puukko, P., and Kariniemi, M. (2010). “Effect of printing parameters on delamination of board in sheet fed offset printing,” Appita Journal 63(4), 315-322.
Article submitted: April 8, 2014; Peer review completed: May 7, 2014; Revised version received: July 1, 2014; Accepted: July 2, 2014; Published: July 14, 2014.
Lockout Resources
Home » Lockout Resources » OSHA Documentation » Interactive Case Studies » Printing Press Roll Cleaning
Printing Press Roll Cleaning
A printing press produces printed materials as its normal production function. The printing press's rollers have to be cleaned periodically during the work shift to ensure quality control.
In this scenario, the press is not shut down for the cleaning operation. The printing press is Energized and its rollers continue to spin at a very high speed. In order for employees to clean the rollers they must bypass the printing press's machine guards, and use rags to clean the rollers. This exposes them to serious, ingoing nip point hazards created by the rollers. Severe laceration or amputated fingers could result if the rag or an employee's hand were to get caught in the rollers or in an area between the rollers and a fixed part of the machine.
Although the employer has a Lockout/Tagout program for Servicing and/or Maintenance of the printing presses, for this particular cleaning operation the employer believes that Lockout / Tagout Procedures do not need to be implemented. According to the employer, this cleaning operation is exempt from Lockout/Tagout requirements because it falls under the minor servicing exemption and therefore the employer allows the equipment to remain operating during the cleaning operation.
Remember, as stated above, the employees are still exposed to the Hazardous Energy of the printing press' during the cleaning operation.
Is this printing press roll cleaning activity covered by the Lockout/Tagout standard?
Even though this roll cleaning activity takes place during normal production operations, the employee is required to bypass a machine guard and /or place part of his/her body into a point of operation or associated danger zone. The cleaning operation is therefore covered as service and Maintenance which took place during normal production operations. Therefore, the requirements of 1910.147 apply.
For more information: Refer to Lockout/Tagout standard parts 1910.147(a)(2)(ii), (a)(2)(ii)(A), and (a)(2)(ii)(B).
Incorrect. Actually, the activity is covered by the Lockout/Tagout standard.
Even though this roll cleaning activity takes place during normal production operations, the employee is required to bypass a machine guard and/or place part of his/her body into a point of operation or associated danger zone. The cleaning operation is therefore covered as service and Maintenance which took place during normal production operations. Therefore, the requirements of 1910.147 apply.
The employer argues that the roll cleaning activity is routine, repetitive, and integral to the production operation and that Lockout is not required because the minor Servicing exception described in 1910.147(a)(2)(ii) is applicable. Is the employer correct?
Incorrect. In this case, the employer is not correct.
The minor Servicing exception does not apply. Even though the roll cleaning activity takes place during normal production operations and is routine, repetitive, and integral to the production operation, the employer has not implemented alternative measures which provide effective protection from the ingoing nip points of the press rolls. Employees instead are required to bypass a machine guard, which is required by Subpart O of 29 CFR 1910, and place their hands and cleaning rags into the press's danger zone. In the absence of alternative protective measures, this cleaning task is a servicing or Maintenance activity that is covered by 1910.147.
In summary, for the minor Servicing exception to apply, each and every element of the exception must be met. In this case, the work is not being performed using alternative measures that provide effective employee protection.
For more information: Read the September 16, 1992, letter of interpretation to Mr. John Runyan of the Printing Industries of America, Inc., for details on how to use safe alternative measures for printing presses.
Source: www.osha.gov
Lockout Services | Turnkey Programs | Lockout Procedures | Single-Source Procedures | Basic Procedures | Standard Procedures | Advanced Procedures | Custom Procedures | Energy Control Tags | Alternative Protective Measures | Minor Servicing Exception | Online Services | Lockout Audits | Corporate Standards | Lockout Training | Reference Guides | Services RFQ | DEenergizer | Lockout Devices | Electrical | Valve and Pneumatic | Accessories | Group Lockout/Tagout | Devices Index | Devices RFQ | Lockout Resources | OSHA Documentation | NIOSH Documentation | White Papers and Articles | Lockout/Tagout FAQ | Lockout/Tagout News | Lockout/Tagout Signs | Energy Source Reference | Training Material | Library | Glossary | Sitemap | About | Contact Information | Careers | Privacy Policy | Terms of Use | Legal Notice
Copyright © 2024 St. Claire, Inc. ♦ DEenergize is a trademark of St. Claire, Inc.
Español ♦ Français ♦ Deutsch ♦ Português
Physical Principles of Ultrasonic Technology
- © 1973
- L. D. Rozenberg 0
Acoustics Institute, Academy of Sciences of the USSR, Moscow, USSR
You can also search for this editor in PubMed Google Scholar
Part of the book series: Ultrasonic Technology (ULTE, volume 1)
5978 Accesses
18 Citations
This is a preview of subscription content, log in via an institution to check access.
Access this book
- Available as PDF
- Read on any device
- Instant download
- Own it forever
- Compact, lightweight edition
- Dispatched in 3 to 5 business days
- Free shipping worldwide - see info
Tax calculation will be finalised at checkout
Other ways to access
Licence this eBook for your library
Institutional subscriptions
About this book
Similar content being viewed by others.
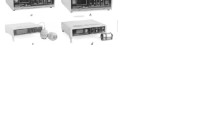
Ultrasonic Devices for Intensifying Technological Processes
The Basics of Ultrasound Physics
Physical Principles of Ultrasound
Table of contents (24 chapters), front matter, ultrasonic cutting, introduction.
L. D. Rozenberg
Investigation of the Ultrasonic Cutting Mechanism
Disintegration of the material in ultrasonic machining, forces acting in ultrasonic cutting, effect of abrasive breakdown and renewal on the variation of machining speed, methods for enhancing machining performance; recent machine tool developments, ultrasonic welding of metals, basic information on the ultrasonic welding of metals, physics of the ultrasonic welding process, technological aspects and equipment requirements of ultrasonic welding, industrial applications, ultrasonic cleaning, the ultrasonic cleaning mechanism, efficiency of ultrasonic cleaning, cavitation—abrasion erosion, vibratory systems and equipment for ultrasonic cleaning, editors and affiliations, bibliographic information.
Book Title : Physical Principles of Ultrasonic Technology
Editors : L. D. Rozenberg
Series Title : Ultrasonic Technology
DOI : https://doi.org/10.1007/978-1-4684-8217-1
Publisher : Springer New York, NY
eBook Packages : Springer Book Archive
Copyright Information : Springer Science+Business Media New York 1973
Softcover ISBN : 978-1-4684-8219-5 Published: 20 September 2012
eBook ISBN : 978-1-4684-8217-1 Published: 11 December 2013
Edition Number : 1
Number of Pages : XXIII, 515
Number of Illustrations : 198 b/w illustrations
Topics : Electrical Engineering
- Publish with us
Policies and ethics
- Find a journal
- Track your research

An official website of the United States government.
Here’s how you know
The .gov means it’s official. Federal government websites often end in .gov or .mil. Before sharing sensitive information, make sure you’re on a federal government site.
The site is secure. The https:// ensures that you are connecting to the official website and that any information you provide is encrypted and transmitted securely.
Occupational Safety and Health Administration
- 中文(简体) (Chinese-Simplified)
- 繁體中文 (Chinese-Traditional)
- Kreyòl ayisyen (Haitian Creole)
- 한국어 (Korean)
- Español (Spanish)
- Filipino/Tagalog
- Tiếng Việt (Vietnamese)
- Lockout-Tagout : Case Studies - Case Study 6: Steel Mill Teeming Car Repairs
Lockout/Tagout eTool
Case studies » case study 6: steel mill teeming car repairs.
An employee is assigned to adjust part of the drive mechanism on a teeming car in a steel mill. The teeming car is isolated from its energy sources and locked out, and the employee crawls underneath the car to start the maintenance job.
The employee, however, fails to shut down or deenergize a separate motor-driven unit used to position the teeming cars. While the employee is performing the maintenance, the motor-driven unit is activated for production purposes and rolls by on adjacent tracks, causing injury to the employee.
Is the employer required to shut down and lock out related machinery operating in the area of the covered service and maintenance, if that machinery could cause injury?
Correct. The employer is obligated to provide the servicing and maintenance employee with protection against hazardous energy from interconnected and nearby machines or equipment which could cause injury. In this case, the energy control procedures were implemented for the teeming car. The employer failed, however, to lock out interconnected and nearby machines or equipment which exposed the maintenance worker to hazardous energy. The employer could either provide effective machine guarding or ensure that the energy control procedure for the teeming car requires the authorized employee to implement the energy control procedures for the motor-driven unit and for other interconnected or nearby equipment or machines. If the employer were to install guarding, it must protect the authorized employee from the hazardous energy of the interconnected or nearby machinery. If the guarding does not adequately protect the authorized employee during this servicing and maintenance activity, the interconnected and nearby machines or equipment must be deenergized and locked out/tagged out. In this case study, because guarding had not been installed, the employer was obligated to implement energy control procedures for the interconnected or nearby machines. The employer therefore failed to implement procedures to shut down, isolate, block, and secure machines or equipment to control hazardous energy (described in 29 CFR 1910.147(c)(4)(ii)(B) ). NOTE: This analysis could be readily applied to a scenario where maintenance must be performed on a punch press in an area crowded with other presses or energized equipment.
Incorrect. In this scenario, this step must be taken. The employer is obligated to provide the servicing and maintenance employee with protection against hazardous energy from interconnected and nearby machines or equipment which could cause injury. In this case, the energy control procedures were implemented for the teeming car. The employer failed, however, to lock out interconnected and nearby machines or equipment which exposed the maintenance worker to hazardous energy. The employer could either provide effective machine guarding or ensure that the energy control procedure for the teeming car requires the authorized employee to implement the energy control procedures for the motor-driven unit and for other interconnected or nearby equipment or machines. If the employer were to install guarding, it must protect the authorized employee from the hazardous energy of the interconnected or nearby machinery. If the guarding does not adequately protect the authorized employee during this servicing and maintenance activity, the interconnected and nearby machines or equipment must be deenergized and locked out/tagged out. In this case study, because guarding had not been installed, the employer was obligated to implement energy control procedures for the interconnected or nearby machines. The employer therefore failed to implement procedures to shut down, isolate, block, and secure machines or equipment to control hazardous energy (described in 29 CFR 1910.147(c)(4)(ii)(B) ). NOTE: This analysis could be readily applied to a scenario where maintenance must be performed on a punch press in an area crowded with other presses or energized equipment.
Next Case Study >>
Case Study 1 2 3 4 5 6 7 | Case Studies Overview
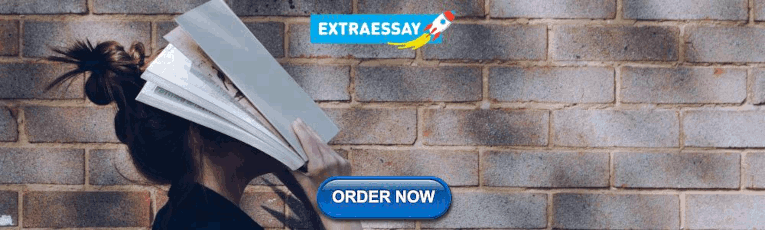
IMAGES
VIDEO
COMMENTS
A printing press produces printed materials as its normal production function. The printing press's rollers have to be cleaned periodically during the work shift to ensure quality control. In this scenario, the press is not shut down for the cleaning operation. The printing press is energized and its rollers continue to spin at a very high speed.
Case Study 1: Printing Press Roll Cleaning. A printing press produces printed materials as its normal production function. The printing press's rollers have to be cleaned periodically during the work shift to ensure quality control. In this scenario, the press is not shut down for the cleaning operation.
OSHA Case Study 1 - Printing Press Roll Cleaning. A printing press produces printed materials as its normal production function. The printing press's rollers have to be cleaned periodically during the work shift to ensure quality control. In this scenario, the press is not shut down for the cleaning operation. The printing press is Energized ...
Case Study 1: Printing Press Roll Cleaning. Incorrect. In this case, the employer is not correct. The minor servicing exception does not apply. Even though the roll cleaning activity takes place during normal production operations and is routine, repetitive, and integral to the production operation, the employer has not implemented alternative ...
Printing Press Roll Cleaning Case Study. A printing press produces printed materials as its normal production function. The printing press's rollers have to be cleaned periodically during the work shift to ensure quality control. In this scenario, the press is not shut down for the cleaning operation. The printing press is energized and its ...
The Case Study: A printing press produces printed materials as its normal production function. The printing press's rollers have to be cleaned periodically during the work shift to ensure quality control. ... Even though the roll cleaning activity takes place during normal production operations and is routine, repetitive, and integral to the ...
Following each case study scenario, you can walk through a series of questions and make decisions concerning the proper application of the Lockout/Tagout standard. After providing your answer, you will see an explanation that identifies and discusses the correct response. ... Printing Press Roll Cleaning; Automotive Component Lubrication ...
The best way to keep the grippers (and other parts clean) is to use Dry Ice Blasting. At Hughes Environmental we clean printing presses with no secondary waste. The presses do not have to be disassembled and no harsh chemicals or solvents are utilized only CO2. We can clean in 1/3 of the time of traditional chemical methods and it's 100% ...
Customer: Duma Druck, established 1983 is situated in Wolfsschlugen, close to Stuttgart, Germany, is a commerial offset and digital printer well known for a consistent quality management. Challenge: Reduce the waste of paper, time and production costs. Solution: Baldwin PREPAC® Advanced cleaning rolls. Benefits: No more fluff on the impression ...
cleaning process, the same piece of equipment is cleaned in less than two hours. A 56 inch six to seven color printing press takes nearly 90 minutes to clean with the traditional method. When cleaning with dry ice, it takes only 30 minutes. "We like our Cold Jet very well," said a department supervisor at a commercial printing facility.
Printing Trade Associations • P R I N T I N G P R O J E C T . EPA 744-K-93-001 . LITHOGRAPHY CASE STUDY 1 . This is the first in a series of case stud-MANAGING SOLVENTS AND WIPES. CASE STUDY 1. LITHOGRAPHY. B. eing responsive to the environment means learning new procedures and using new tools to do the same job with less hazard.
Original Press Release: R.G. Egan Equipment Launches New Product for the Wide Web Flexographic Printing Industry. WEBSTER, NEW YORK - Today R.G. Egan Equipment, the leading manufacturer of automatic roll cleaning systems that are designed for the printing and packaging industry, launched there latest cleaner technology for Central Impression Printing Press Drums.
printing industry that usually put a person in difficult situations and cause unsafe behaviors to include cleaning and preparing the printing machine, embedding paper, fixing the printing machine, maintaining the equipment, monitoring the printing process, moving printed paper, cutting and paper binding18. Therefore, this study was
In particular, this case study shows: •How a self-audit of ink remover products used in screen cleaning led to the substitu-tion of more environmentally appropriate solvents at press side. •How using a still to recover and reuse ink cleaning solvent saved the com-pany money. •How using a high-pressure water blaster and changing
Not in this case. The Lockout/Tagout standard does not specifically require the use of a work authorization permit. An employer may choose to use a generic energy control procedure and a work authorization permit to meet the requirements of 1910.147(c)(4) .
The ink tack, or a force required to split ink layers ( e.g. between the inking rollers), is an important parameter of the offset printing process, influencing many of the effects observed in printing (Gujjari et al. 2006; Mangin and Silvy 1997; Mattila and Passoja 2006; Vähä-Nissi et al. 2010). Ink tack is measured using different methods ...
Printing Press Roll Cleaning Case Study. A printing press produces printed materials as its normal production function. The printing press's rollers have to be cleaned periodically during the work shift to ensure quality control. In this scenario, the press is not shut down for the cleaning operation. The printing press is Energized and its ...
Ultrasonic Cleaning. Front Matter. Pages 245-245. Download chapter PDF Introduction. L. D. Rozenberg; Pages 247-251. Download chapter PDF ... 978-1-4684-8217-1 Published: 11 December 2013. Edition Number: 1. Number of Pages: XXIII, 515. Number of Illustrations: 198 b/w illustrations.
1. Febvre, Lucien and Martin, Henri-Jean, L'apparition du livre (Paris, 1971)Google Scholar; Rudolph, Hirsch, Printing, Selling, and Reading, 1450-1550 (Wiesbaden, 1974Google Scholar); Elizabeth, Eisenstein, The Printing Press as an Agent of Change, 2 vols. (Cambridge, 1979Google Scholar); Elizabeth Eisenstein, "Clio and Chronos, An Essay on the Making and Breaking of History-Book Time ...
Case Studies » Case Study 7: Overhead Crane Servicing and Maintenance A millwright is assigned to a servicing and maintenance task on an overhead crane. The employee initiates the prescribed energy control procedure by turning "off" the crane's electrical disconnect switch and placing his lock onto this energy isolating device.
Getting your laundry done is a long process which involves steps like: sorting your clothes, soaking them, washing (by hand or washing machines), hanging them to dry, ironing them and at last folding them. This process is tiresome and difficult for mostly everyone, especially for bachelors. It results in poor sanitary conditions as laziness ...
In this case study, because guarding had not been installed, the employer was obligated to implement energy control procedures for the interconnected or nearby machines. The employer therefore failed to implement procedures to shut down, isolate, block, and secure machines or equipment to control hazardous energy (described in 29 CFR 1910.147(c ...