
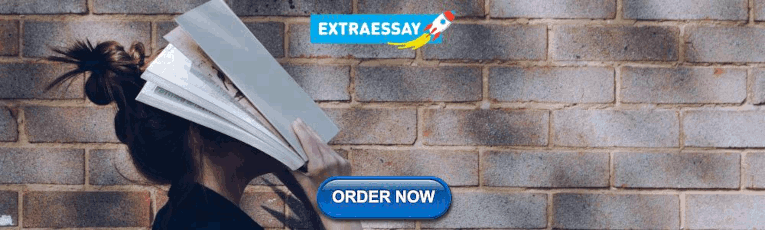
5S Methodology in Textile and Garment Industry
Mofizur Rahaman Akash Fabric Marketing, Unifill Composit Dyeing Mills Ltd. Email: [email protected]
What is 5S Methodology? 5S is a workplace organization method that uses a list of 5S sort, set in order, shine, standardize & sustain. The 5S methodology is a systematic approach that originated in Japan and has been widely adopted in manufacturing industries , including the textile and garment industry. The list describes how to organize a work space for efficiency and effectiveness by identifying and storing the items used, maintaining the area and items, and sustaining the new organizational system. The decision-making process usually comes from a dialogue about standardization, which builds understanding among employees of how they should do the work.

In some quarters, 5S has become 6S, the sixth element being safety (safe).
Sort: Sort is sorting through all items in a location and removing all unnecessary items from the location.
- Reduce time loss looking for an item by reducing the number of unnecessary items.
- Reduce the chance of distraction by unnecessary items.
Simplify inspection:
- Increase the amount of available, useful space.
- Increase safety by eliminating obstacles.
Implementation:
- Check all items in a location and evaluate whether or not their presence at the location is useful or necessary.
- Remove unnecessary items as soon as possible. Place those that cannot be removed immediately in a ‘red tag area’ so that they are easy to remove later on.
- Keep the working floor clear of materials except for those that are in use for production.
Set in order: Set in order is putting all necessary items in the optimal place for fulfilling their function in the workplace.
- Make the workflow smooth and easy.
- Arrange work stations in such a way that all tooling/equipment is in close proximity, in an easy to reach spot and in a logical order adapted to the work performed. Place components according to their uses, with the frequently used components being nearest to the workplace.
- Arrange all necessary items so that they can be easily selected for use. Make it easy to find and pick up necessary items.
- Assign fixed locations for items. Use clear labels, marks or hints so that items are easy to return to the correct location and so that it is easy to spot missing items.
Shine: Shine is sweeping or cleaning and inspecting the workplace, tools and machinery on a regular basis.
- Improves the garment production process efficiency and safety, reduces waste, prevents errors and defects.
- Keep the workplace safe and easy to work in.
- Keep the workplace clean and pleasing to work in.
- When in place, anyone not familiar to the environment must be able to detect any problems within 15 metres (50 ft) in 5 seconds.
- Clean the workplace and equipment on a daily basis, or at another appropriate (high frequency) cleaning interval.
- Inspect the workplace and equipment while cleaning.
Standardize: Standardize is to standardize the processes used to sort, order and clean the workplace.
- Establish procedures and schedules to ensure the repetition of the first three ‘S’ practices.
- Develop a work structure that will support the new practices and make it part of the daily routine.
- Ensure everyone knows their responsibilities of performing the sorting, organizing and cleaning.
- Use photos and visual controls to help keep everything as it should be.
- Review the status of 5S implementation regularly using audit checklists.
Sustain / self-discipline Sustain is the developed processes by self-discipline of the workers. Also translates as “do without being told”.
- Ensure that the 5S approach is followed.
- Organize training sessions.
- Perform regular audits to ensure that all defined standards are being implemented and followed.
- Implement improvements whenever possible. Worker inputs can be very valuable for identifying improvements.
Conclusion: In textile & garment industry, 5S methodology can help improve efficiency, reduce waste, and improve quality by creating a more organized and standardized workplace. By eliminating unnecessary items, organizing workstations and tools, and establishing standard procedures, the 5S methodology can help companies reduce costs, increase productivity, and improve customer satisfaction.
You may also like:
- Implementation of SMED in Garment Industry
- KPI (Key Performance Indicator) in Garment Industry
- Concept of Six Sigma and Its Application in Textile Industry
- Concept of ISO 9000, Six Sigma and Lean Production for Apparel Industry

Founder & Editor of Textile Learner. He is a Textile Consultant, Blogger & Entrepreneur. He is working as a textile consultant in several local and international companies. He is also a contributor of Wikipedia.
Share this Article!
Related Posts:

Leave a Comment Cancel reply
Save my name, email, and website in this browser for the next time I comment.
Notify me of follow-up comments by email.
Notify me of new posts by email.

Textile and Finance
Implementation of 5S in Apparel Industry
5S comes from 5 Japanese words and each of them starts with S. These are seiri , seiton , seiso , seiketsu , and shitsuke , if we translate these 5 Japanese words into English then we get Sort , Set in Order , Shine , Standardize , and Sustain . In the garment industry 5S works as a basic tool of Lean Manufacturing, a technique to set a well organized, clean, and visually attractive workplace. That’s why the implementation of 5S in the Apparel Industry is required.

Implementing the 5’S method is a base to implement quality improvement/lean procedures. Expecting the team to be and they do activities in each department: like monitoring, evaluate and drive the aspects very clean and organized so that, your Factory will look very planned and well Set-up.
Let’s have a look at the difference in English and Japanese words for 5S

Basic Concepts for 5S Implementation in Apparel
S1. sort (seiri).
5S start with sort. Sort means to sort out unnecessary items, use all machines, tools, equipment for regular use. Define daily needed items, weekly needed items, and monthly needed items and keeping separate. The store is broken, unusable or occasionally used items also should be defined. Keep records for eliminating unnecessary items that exist and new items. Each and every section of garments you may find many things are kept in a haphazard way. So for these, you need to follow the first S from the 5S, i.e Sort. Sorting according to items characteristics and importance.
S2 – Set in Order – SEITON
Setting order is important for 5S. All items, sections, and areas (In, exist) are clearly identified by a label and everything should be well organized. Never mix/store two category items in one place. Dividing lines, aisle mark, Stairway is clearly identified and clean as per standard. Confirm that the exits are accessible and unlocked during working hours. Confirm that, where necessary, the emergency exit doors have no panic hardware or lever style (one hand, one motion door openers). If you keep all of your store materials in your garments warehouse in a planned order basis, then whenever required that materials you can easily find out and get those materials. That’s why all materials should be kept in accordance with the set in order.

S3 – Shining – SEISO
The third S from 5S is Shine, actually mean cleanliness. All items/place of workplace Floors, walls, stairs, ceilings, pipework Racks, cabinets, shelves, Machines, equipment, tools, Stored items, materials, products, and lighting everything required to be kept clean. All cleaning tools and materials are easily accessible. Cleaning assignments are defined and are being followed by the checklist and hang checklist on visible board. Do periodical pest control to make sure there is no insect. Cleanliness is not only a compliance issue but also this increase a healthy working environment in garments factories or offices.

Download: S3: Shine, Cleaning Schedule (Excel 20kb)
S4 – Standardize – SEIKETSU
The first three steps of 5S are the key to implement 5S in the workplace. This section is about visualization by Information displays, related SOPs, signs, color coding and other markings are established everywhere of the factory also included procedures for maintaining the first three S’s are being displayed. Do regular 5’s audit using a checklist, give & post rating to each area. Need formal training, keep training records to approach towards improvement. These standardizations increase the operating efficiency of the apparel industry.

S5 – Sustain – SHITSUKE
This section is to sustain 5S in the textile and garments factory to be the way of life rather than just a routine. Success stories are being displayed (i.e. before and after pictures) in every section of the 5S board. Give rewards and recognition is part of the 5S system to sustain 5S.
S6 and S7(Extension of 5S)
Now, 5S have two additional points 6th “S” for “Safety” and the 7 th “S’’ is “Security”. These two new points’ objective is to make a safe workplace for all employees. It is the employer’s responsibility to provide safety and security for both factory and office place in the apparel industry.
Advantages of 5S for Garments
If you properly follow 5S for your textile and garments industry, then you will get the following benefits:
- Health and Safety is ensured
- The base of implementation of quality improvement
- Productivity Increase
- Save time, cost and storage space
- Minimization of accidents & mistakes
- Increases efficiency
- Creates workplace ownership
- The first step for Lean procedures
- Increase customer satisfaction
- Reduce inventory time
- Reduce downtime, wastage
- Good working environment
- Visualization and labeling
- Boost morale
- Improve company image
- Optimize organization and workplace as per requirement
- Routine wise work schedule and visual Standard Operating Procedure (SOP) everywhere
- Everybody knows their working responsibility where and when
- Disciplined housekeeping
For implementing 5S in Apparel Industry you need to follow the followings:
- Need central 5S committee and section-wise subcommittee
- 5S organogram and committee list as enclosed
- Section-wise 5S checklist
- 5S display board in every section
- Make a separate T-shirt for a committee
- Conduct 5s training and drive for good housekeeping
- Conduct a section-wise 5S audit and submit a report.
- Evaluate score and take corrective action for improvement in every department.
Actions Need to Implement 5S in Garments Industry
- Take “before” photographs.
- Check that the first three S’s are implemented properly.
- All team activity documents/checklists should be publicly displayed on a 5S board.
- Establish the routines and standard practices for regularly and systematically repeating the first three S’s.
- Standardize red tag procedures and holding area rules (see Seiri).
- Create a maintenance system for housekeeping. Make a schedule for cleaning the workplace. A common approach is to ask a cross-functional team to do it.
- Inter-departmental competition is an effective means of sustaining and enhancing interest in 5S.
- Assign responsibility to individuals for a work area and machinery.
- Regular inspection/audit and evaluation by a special team (including senior management persons) to be continued.
- Instead of criticizing poor cases, praise and commend good practices or good performers.
- Take “after” photographs and post them on the 5S board(s).
- Give a reward for the top-scoring section.
You can download Presentation File on 5S if you need it.
5S Presentation: PowerPoint (6.3MB)
5S Training: PowerPoint (5.1MB)
5S Presentation (English & Bangla): PowerPoint (6.9MB)
6 thoughts on “ Implementation of 5S in Apparel Industry ”
MaasyaAllah, thank you very much Pak Washim for sharing this knowledge. It helps me a lot.
Jazakallahu khoiron. Barakallahu fik.
5S is an integral facet of manufacturing excellence. Though early resistance may be felt, the benefits will soon become apparent. Visual Management is absolutely key. Great article.
Thanks a lot for your idea sharing with us. It is great post!
It’s a great idea for me thanks for published it .
Thanks for sharing your info. I was able to find good information from your blog post
Leave a Reply
You must be logged in to post a comment.
Discover more from ORDNUR
Subscribe now to keep reading and get access to the full archive.
Type your email…
Continue reading
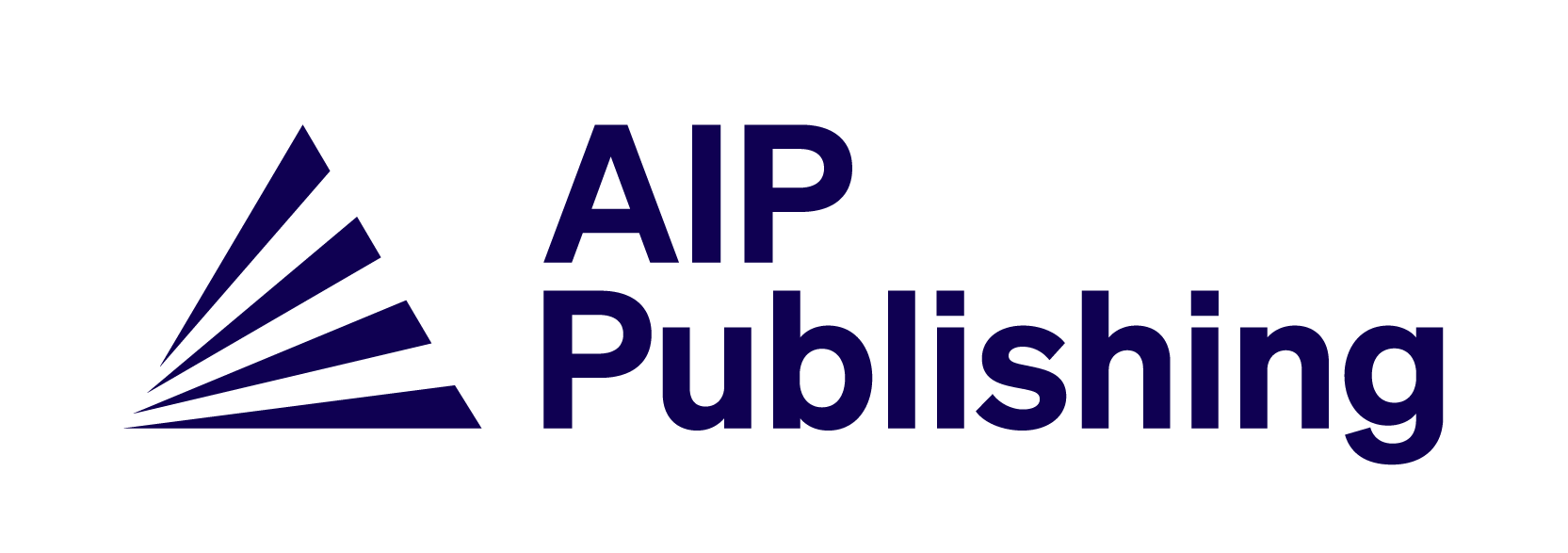
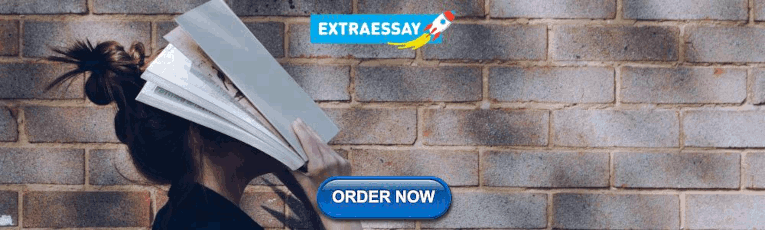
A critical review on implementation of 5S and six sigma in textile industry
- Article contents
- Figures & tables
- Supplementary Data
- Peer Review
- Reprints and Permissions
- Cite Icon Cite
- Search Site
Jesica Roshima Alexander , A. Vasudeva Reddy , N. Konda Reddy; A critical review on implementation of 5S and six sigma in textile industry. AIP Conf. Proc. 8 September 2023; 2800 (1): 020280. https://doi.org/10.1063/5.0163127
Download citation file:
- Ris (Zotero)
- Reference Manager
The purpose of this paper is to review quality management literature comprising of Lean management, Six Sigma in textile industry. This paper highlights the implementation of quality management practices and improvement in the productivity through extensive literature review. The literature survey has confirmed that a clear dependency upon the commitment of top management and leaders of the business unit through support and optimized resource allocation for reducing waste, thereby improving quality, reducing cost of production and ultimately increasing customer satisfaction. Implementing TQM across is a process with a number of iterations before tasting the fruit of success. It is an approach, focusing on detailed formulation of strategies undertaken towards successful organizational improvement through enhanced innovation. This paper provides a mode of viewing quality through excellence model along with lean and six sigma principles with customer as the primary focus for the business.
Sign in via your Institution
Citing articles via, publish with us - request a quote.
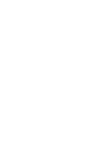
Sign up for alerts
- Online ISSN 1551-7616
- Print ISSN 0094-243X
- For Researchers
- For Librarians
- For Advertisers
- Our Publishing Partners
- Physics Today
- Conference Proceedings
- Special Topics
pubs.aip.org
- Privacy Policy
- Terms of Use
Connect with AIP Publishing
This feature is available to subscribers only.
Sign In or Create an Account
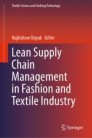
Lean Supply Chain Management in Fashion and Textile Industry pp 269–290 Cite as
Lean Manufacturing: Case Studies from Fashion and Textile Industries
- Majo George 3 ,
- Nguyen Minh Ngoc 3 ,
- Le Khac Yen Nhi 3 ,
- Vuong Nguyen Dang Tung 3 ,
- Le Phan Thanh Truc 3 &
- Rajkishore Nayak 4
- First Online: 30 August 2022
791 Accesses
1 Citations
Part of the book series: Textile Science and Clothing Technology ((TSCT))
This chapter will focus on various case studies relating to the failure and success of various industries in the fashion and textile manufacturing sector. From the earlier chapters (Chaps. “Lean Manufacturing: Case Studies from Fashion and Textile Industries” – “Digital Technologies for Lean Manufacturing” , it has been clearly mentioned that the implementation of various lean tools such as Kaizen, Muda, 5S and Kanban can help the traditional industries to improve their productivity and efficiency by reducing waste. This chapter will discuss the implementation of lean manufacturing by some of the fashion and textile industries and its impact on productivity and efficiency. The chapter has been divided into three sections for better flow and understanding. The first section will discuss some case studies focusing on the failure of some of the industries from Africa and India due to not implementing of lean manufacturing tools. The second section will focus on the case studies focusing on the success of some of the fashion and textile industries by adopting lean manufacturing tools. Finally, the third and last section will focus on the future directions and conclusions of this chapter.
- Case studies
- Fashion and textiles
- Failure and success
This is a preview of subscription content, log in via an institution .
Buying options
- Available as PDF
- Read on any device
- Instant download
- Own it forever
- Available as EPUB and PDF
- Compact, lightweight edition
- Dispatched in 3 to 5 business days
- Free shipping worldwide - see info
- Durable hardcover edition
Tax calculation will be finalised at checkout
Purchases are for personal use only
Aboagyewaa-Ntiri J, Mintah K (2016) Challenges and opportunities for the textile industry in Ghana: a study of the adinkra textile sub-sector. Int Bus Res 9(2):127–136
Article Google Scholar
Ahmmed AS, Ayele M (2020) In-depth analysis and defect reduction for ethiopian cotton spinning industry based on TQM approach. J Eng 2020:1–8. https://doi.org/10.1155/2020/5792434
Calisir F (2007) Factors affecting service companies’ satisfaction with ISO 9000. Manag Serv Qual 17:579–593
Carmignani G, Zammori F (2015) Lean thinking in the luxury-fashion market: evidences from an extensive industrial project. Int J Retail Distrib Manag 43(10/11):988–1012. https://doi.org/10.1108/IJRDM-07-2014-0093
Ganguly-Scrase R (2003) Paradoxes of globalization, liberalization, and gender equality: the worldviews of the lower middle class in West Bengal, India gender and society. Sage Publ 17(4):544–566
Google Scholar
Goswami O (1990) Sickness and growth of India’s textile industry: analysis and policy option. Econ Pol Wkly 25(44):2429–2439
Karthi S, Devadasan SR, Murugesh R (2011) Lean Six Sigma through ISO 9001 standard-based quality management system: an investigation for research. Int J Prod Qual Manag 8:180–204
Khan AM, Islam M (2013) Application of 5S system in the sample section of an apparel industry for smooth sample dispatch. Res J Manag Sci 2(7):28–32. ISSN 2319–1171
Kquofi S, Amate P, Tabi-Agyei E (2013) Symbolic representation and socio-cultural significance of selected Akan proverbs in Ghana. Int Inst Sci Technol Educ 3(1):86–98
Kumar S, Thavaraj S (2015) Impact of lean manufacturing practices on clothing industry performance. Int J Text Fash Technol (IJTFT) 5(2):1–14
Kuwornu-Adjaottor JET, Appiah G, Nartey M (2016) The philosophy behind some Adinkra symbols and their communicative values in Akan. Philos Pap Rev 7(3):22–33. https://doi.org/10.5897/PPR2015.0117
Mizuno K (1996) Rural industrialization in indonesia: a case study of community-based weaving industry in West Java, 1st edn. Institute of Developing Economies
Niranjana S (2004) Thinking with handlooms: perspectives from Andhra Pradesh. Econ Pol Wkly 39(6):553–563
Quarcoo AK (1972) The language of the adinkra patterns, 1st edn. Institute of African Studies, University of Ghana, Legon
Quartey P, Abor J (2011) Do Ghanaians prefer imported textiles to locally manufactured ones? Mod Econ 2(1):54–61. https://doi.org/10.4236/me.2011.21009
Rahani AR, Al-Ashraf M (2012) Production flow analysis through value stream mapping: a lean manufacturing process case study. Int Symp Robot Intell Sens 2012:1727–1734
Rother M, Shook J (1998) Learning to see: value stream mapping to create value and eliminate Muda. The Lean Enterprise Institute, Brookline, MA
Roy T (2002) Acceptance of innovations in early twentieth century Indian weaving. Econ Hist Rev New Ser 55(3):507–532
Shiferaw A (2017) Productive capacity and economic growth in Ethiopia. CDP Background 34:1–24
Srinivasulu K (1994) Handloom weavers’ struggle for survival. Econ Pol Wkly 29(36):2331–2333
Syduzzaman Md, Biswas MAS, Yeasmin D (2016) Developing a framework for implementing total quality management in the apparel industry: case study on a Bangladeshi apparel manufacturing factory. Int J Textile Sci 5(5):87–95
Tanusree S (2015) A Study of the present situation of the traditional handloom weavers of Varanasi, Uttar Pradesh, India. Int Res J Soc Sci 4(3):48–53
Teichgräber UK, de Bucourt M (2012) Applying value stream mapping techniques to eliminate non-value-added waste for the procurement of endovascular stents. Eur J Radiol 81:e47–e52. https://doi.org/10.1016/j.ejrad.2010.12.045
Download references
Author information
Authors and affiliations.
School of Business and Management, RMIT Vietnam, Ho Chi Minh City, Vietnam
Majo George, Nguyen Minh Ngoc, Le Khac Yen Nhi, Vuong Nguyen Dang Tung & Le Phan Thanh Truc
School of Communication & Design, RMIT Vietnam, Ho Chi Minh City, Vietnam
Rajkishore Nayak
You can also search for this author in PubMed Google Scholar
Corresponding author
Correspondence to Majo George .
Editor information
Editors and affiliations.
School of Communication and Design, RMIT University Vietnam, Ho Chi Minh, Vietnam
Rights and permissions
Reprints and permissions
Copyright information
© 2022 The Author(s), under exclusive license to Springer Nature Singapore Pte Ltd.
About this chapter
Cite this chapter.
George, M., Ngoc, N.M., Nhi, L.K.Y., Tung, V.N.D., Truc, L.P.T., Nayak, R. (2022). Lean Manufacturing: Case Studies from Fashion and Textile Industries. In: Nayak, R. (eds) Lean Supply Chain Management in Fashion and Textile Industry. Textile Science and Clothing Technology. Springer, Singapore. https://doi.org/10.1007/978-981-19-2108-7_11
Download citation
DOI : https://doi.org/10.1007/978-981-19-2108-7_11
Published : 30 August 2022
Publisher Name : Springer, Singapore
Print ISBN : 978-981-19-2107-0
Online ISBN : 978-981-19-2108-7
eBook Packages : Engineering Engineering (R0)
Share this chapter
Anyone you share the following link with will be able to read this content:
Sorry, a shareable link is not currently available for this article.
Provided by the Springer Nature SharedIt content-sharing initiative
- Publish with us
Policies and ethics
- Find a journal
- Track your research
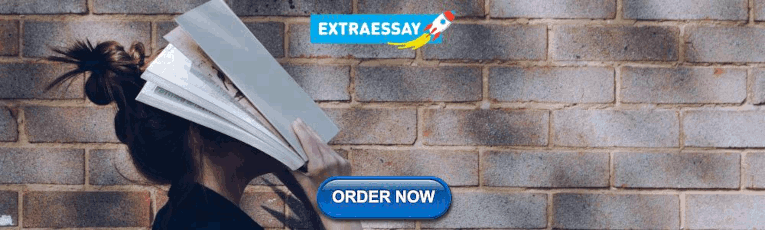
IMAGES
VIDEO
COMMENTS
Energy Efficiency & Productivity Case Study: 5S in Garment Industry ...
The 5S method is a Japanese system that involves workplace management improvements. It further analyses the effect of the 5S method in the apparel & textile industry as a case study and how its implementation directly impacts saving time and costs. 5S process helps to eliminate waste, reduce defects, and help in improving the productivity of ...
In summary, this book chapter focuses on understanding the role of lean management especially 5S in the fashion and textile industry. Regarding 5S implementation, the case study of company A has shown the process of four phases with the purpose of optimizing the procedures in the warehouse to eliminate the current operation wastes.
The assembly line cycle time was reduced from 50 min to 41.50 min as a result of this implementation. In another case study, Choomlucksana et al. (2015) used lean manufacturing techniques such as 5S, visual control, and Poka-Yoke to discover waste reduction opportunities and increase the efficiency of production processes. The non-value-added ...
3. CASE STUDY We have performed a case study in one of the departments of a garment factory. The steps of the 5S method for the organization of the work place have been followed and examples of good practices will be presented. The following remarks could be considered as work instructions in order to implement the 5S rules.
5S is a workplace organization method that uses a list of 5S sort, set in order, shine, standardize & sustain. The 5S methodology is a systematic approach that originated in Japan and has been widely adopted in manufacturing industries, including the textile and garment industry. The list describes how to organize a work space for efficiency ...
This paper introduces the effect of implementation 5s method in the Egyptian apparel & textile factories as a real case study and how this implementation of 5s makes a direct effect in increase ...
implementation of 5S. The problem has been identified during site assessment . Those problems has been solved by using 5S concept. Case study has helped to understand the before and after implementation of the scenery which has been discussed briefly. After 2(1st November to 30th January,2014) month working there, got the expected success. The ...
This case study deals with the 5S implementation in an industry, Implementation of 5S can result in considerable improvements in environmental performance beside with improved housekeeping and health and safety.[5]5S can improve the quality, productivity and working conditions in organizations.[5]
Abstract. 5S is a systematic and visual approach to improve the working culture at the workplace. The implementation of the 5S has been seen central to increase the cleanliness in operational as ...
The 5S method is a Japanese system that involves workplace management improvements. It further analyses the effect of the 5S method in the apparel & textile industry as a case study and how its ...
For implementing 5S in Apparel Industry you need to follow the followings: Need central 5S committee and section-wise subcommittee. 5S organogram and committee list as enclosed. Section-wise 5S checklist. 5S display board in every section. Make a separate T-shirt for a committee.
Jesica Roshima Alexander, A. Vasudeva Reddy, N. Konda Reddy; A critical review on implementation of 5S and six sigma in textile industry. AIP Conf. Proc. 8 September 2023; 2800 (1): 020280. ... Lean Six Sigma Applications in the Textile Industry: a case study ", ... in the Apparel industry in Sri Lanka ",
Time taken for 1 piece before implementation of 5s = 665/500 =1.33minutes Price of one piece = 45 Rs. No of pieces can be produced in 50 minutes = 50/1.33 = 38 pieces Amount saved in 50 minutes = 38*40 = 1520 Rs In 665 minutes we can save 50 minutes. For 1 month = 26 working days * 8 working hour. = 208 working hours.
It includes five Japanese words Seiri, Seiton, Seiso, Seiketsu and Shitsuke, which means Sort, Set in order, Shine, Standardize and Sustain respectively. The benefit of 5S technique lies in improvement of productivity, quality, health and safety. According to (Deshpande et al., 2015) every organization aims for profit.
As part of the project of implementing 5s principles, the work-study officer decided to provide costs in the various stages of the production process. The loss due to waste production was provided in a detailed report to the executive management and highlighted to each departmental manager. The next step was an investigation into the causes of ...
This research deals with implementation of 5S methodology in a manufacturing industry, which is a small scale industry located in industrially developed ... case study. Keywords:5S, implementation, ... As all the five steps start with the letter "S" it has been termed as 5S techniques in short form. The case study is carried out in a small ...
5.1 Case Study 1. Applying Muda Concept to Natural Fiber Clothing Manufacturing. As more customers go against the cost of waste, businesses are searching for grand tools and techniques for the identification of the Muda in their operations (Rahani and Ashraf 2012).The Muda refers to the wastes (or non-value-added activities) that need to be eliminated in the business process for an ...
V. IMAGES OF 5S IMPLEMENTATION IN INDUSTRY SEIRI Images of 5S Implementation in Industry Seiri Fig. 5:- Red tag area Fig. 6:- unnecessary material storage Seiri is the first step of 5S methodology. It is the waste reduction step. The function of this step is separating necessary and unnecessary things and eliminating waste material.
The study has been taken after studying for 3 months at ten (10) different apparel industries in Pakistan. For development of textile and apparel sector of Pakistan a study has been conducted in apparel sector which is contributing on a very large scale in Pakistan export. The methodology that was adopted was started with making of a 5S committee and trained them over the 5S concept in detail ...
Agrahari et al (2015) implemented 5S methodology in a small scale industry to achieve housekeeping and productivity. A case study was presented using 5S methodology and questions were asked to ...
All required manufacturing data to determine the number of Kanban cards and its flow was collected from the manufacturing line itself. All input operation/s and output operation/s of each operation and the machine used in each operation were studied. It was decided to maintain 4 pieces bundles. A 4 pieces bundle was considered as 1 Kanban.