Academia.edu no longer supports Internet Explorer.
To browse Academia.edu and the wider internet faster and more securely, please take a few seconds to upgrade your browser .
Enter the email address you signed up with and we'll email you a reset link.
- We're Hiring!
- Help Center
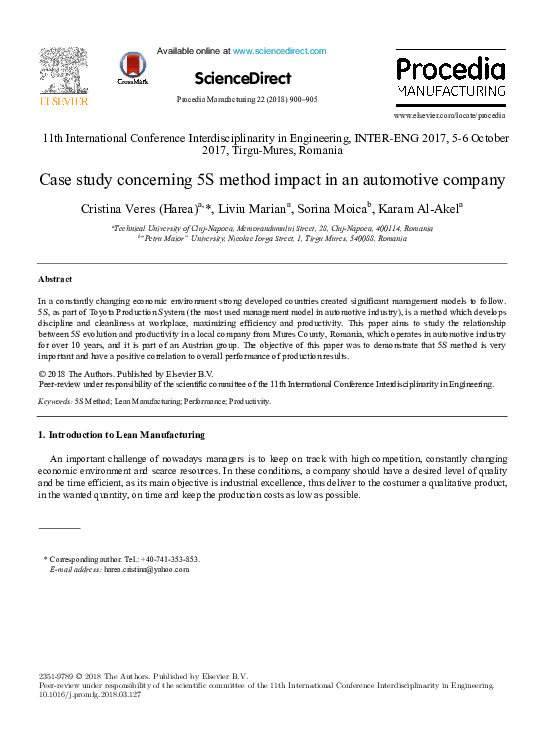
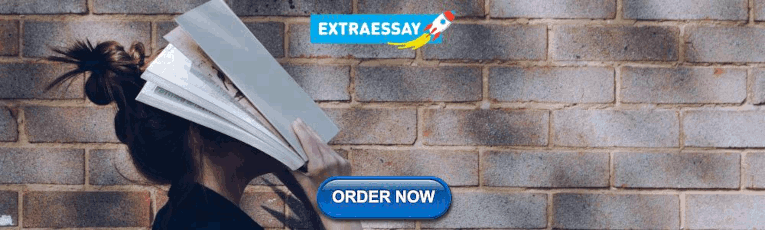
Case study concerning 5S method impact in an automotive company

2018, Procedia Manufacturing
Related Papers
Sumeet Alhat
Under the concept of "Industry 4.0", production processes will be pushed to be increasingly interconnected, information based on a real time basis and, necessarily, much more efficient. In this context, capacity optimization goes beyond the traditional aim of capacity maximization, contributing also for organization's profitability and value. Indeed, lean management and continuous improvement approaches suggest capacity optimization instead of maximization. The study of capacity optimization and costing models is an important research topic that deserves contributions from both the practical and theoretical perspectives. This paper presents and discusses a mathematical model for capacity management based on different costing models (ABC and TDABC). A generic model has been developed and it was used to analyze idle capacity and to design strategies towards the maximization of organization's value. The trade-off capacity maximization vs operational efficiency is highlighted and it is shown that capacity optimization might hide operational inefficiency.
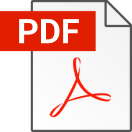
Procedia Manufacturing
Martina Varisco
International Journal of Business and Systems Research
Tamás Koltai
Benny Tjahjono
Johan Stahre
Veikko Turunen
Nemanja Sremcev
Malin Tarrar (Karlsson)
RELATED PAPERS
Rahmawati Munir
Epidemiology (Cambridge, Mass.)
Jussi Kauhanen
idawati supu
Stanislav Korenko
Clara Gajardo Guzman
Organic Letters
ANGEL FABIAN ZAPATA VIDAL
F. Antoniou
Neuza Corte de Oliveira
Lebanese Medical Journal
Ahmad Mourad
Jaideep Srivastava
Historia de las …
Jose Fonfria Diaz
E-Mabis: Jurnal Ekonomi Manajemen dan Bisnis
Hristo Abrashev
Pamukkale University Journal of Engineering Sciences
Dilek şahin
Open-file report /
Kathryn Schoenecker
Medical principles and practice : international journal of the Kuwait University, Health Science Centre
Mustafa Aydin
Conservation Biology in Sub-Saharan Africa
Johnny Wilson
General and Comparative Endocrinology
Deborah Power
Lancet (London, England)
Fabio Tarantino
anthony downey
Authorea (Authorea)
Daniel Bracewell
European urology open science
Marco Puglisi
HAL (Le Centre pour la Communication Scientifique Directe)
Léonie Hénaut
RELATED TOPICS
- We're Hiring!
- Help Center
- Find new research papers in:
- Health Sciences
- Earth Sciences
- Cognitive Science
- Mathematics
- Computer Science
- Academia ©2024
Lean Safety - assessment of the impact of 5S and Visual Management on safety
J C Sá 1,2 , V Manuel 1 , F J G Silva 1 , G Santos 3 , L P Ferreira 1 , T Pereira 1 and M Carvalho 1
Published under licence by IOP Publishing Ltd IOP Conference Series: Materials Science and Engineering , Volume 1193 , 9th Manufacturing Engineering Society International Conference (MESIC 2021) 23rd-25th June 2021, Gijόn, Spain Citation J C Sá et al 2021 IOP Conf. Ser.: Mater. Sci. Eng. 1193 012049 DOI 10.1088/1757-899X/1193/1/012049
Article metrics
946 Total downloads
Share this article
Author e-mails.
Author affiliations
1 School of Engineering, Polytechnic of Porto, Rua Dr. António Bernardino de Almeida, 431, 4200-072 Porto, Portugal
2 Instituto Politécnico de Viana do Castelo, Rua Escola Industrial e Comercial Nun Alvares - 4900-347 Viana do Castelo - Portugal
3 School of Design, Polytechnique Institute of Cávado and Ave, Campus do IPCA - Lugar do Aldão, 4750-810 Barcelos, Portugal
Buy this article in print
This study was developed in a furniture company and aimed to implement some Lean tools, such as 5S and Visual Management to reduce waste, by improving the production process. To carry out this analysis an observation plan was used, having the Spaghetti diagram as a reference as well as the value-added analysis of the operations. The implementation of 5S's allowed the improvement of the visual management and the organization through a reorganization of the layout, as well as normalization of the production process. With this, a reduction of 40% was achieved in terms of waste related to activities that did not add value to the product, such as unnecessary movements, waiting times and even movement of materials, having achieved a level of productivity of 74% and 87% in the finishing and joinery sections, respectively. In addition to improvements in the production process, the impact of the measures at the safety level (lean safety) was assessed. For this purpose, a questionnaire was prepared to assess the opinion of the employees, in which 40% considered that the implementation of the tools provided a greater motivation to develop their work activities safely.
Export citation and abstract BibTeX RIS
Content from this work may be used under the terms of the Creative Commons Attribution 3.0 licence . Any further distribution of this work must maintain attribution to the author(s) and the title of the work, journal citation and DOI.
Case study concerning 5S method impact in an automotive company
- Scinapse’s Top 10 Citation Journals & Affiliations graph reveals the quality and authenticity of citations received by a paper.
- Discover whether citations have been inflated due to self-citations, or if citations include institutional bias.
Evaluating the Impact of 5S Implementation on Occupational Safety in an Automotive Industrial Unit
- Conference paper
- First Online: 17 April 2019
- Cite this conference paper
- Joana P. R. Fernandes 4 ,
- Radu Godina 5 &
- João C. O. Matias 4 , 6
Part of the book series: Springer Proceedings in Mathematics & Statistics ((PROMS,volume 281))
Included in the following conference series:
- International Joint conference on Industrial Engineering and Operations Management
880 Accesses
2 Citations
Lean is becoming a world-class word that represents continuous improvement and most of all the importance of focusing on creating value. The implementation of Lean Manufacturing will lead us to improve quality, reducing costs and at the same time the elimination of non-value-added activities. For these reasons, several organizations try to adopt the philosophy. Although the application of Lean principles brings numerous benefits to organizations, at this time the optimization of the productive process is not enough. Ensuring optimal safety conditions of all the employees has been one of the top priority, exceeding “quality” or “performance” as indicators of success. In this paper, a case of study in one industrial unit of one of Europe’s largest car producers is tested and then it is evaluated how the implementation of lean tools, more specifically 5S , can contribute to the occupational safety conditions. The present work demonstrates another of the several advantages that is obtained from the use of 5S . Apart from being a powerful tool for organizing and optimizing the workplace environment, this study demonstrates that it is also essential to ensure occupational safety.
This is a preview of subscription content, log in via an institution to check access.
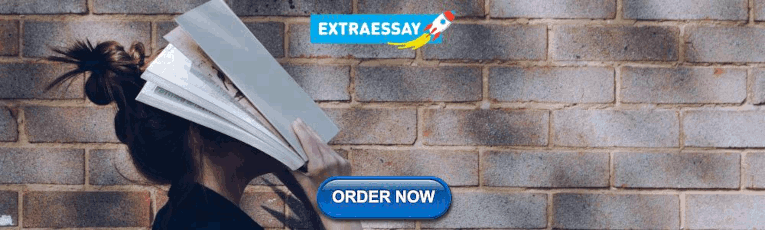
Access this chapter
- Available as PDF
- Read on any device
- Instant download
- Own it forever
- Available as EPUB and PDF
- Durable hardcover edition
- Dispatched in 3 to 5 business days
- Free shipping worldwide - see info
Tax calculation will be finalised at checkout
Purchases are for personal use only
Institutional subscriptions
Ciccullo, F., Pero, M., Caridi, M., Gosling, J., Purvis, L.: Integrating the environmental and social sustainability pillars into the lean and agile supply chain management paradigms: a literature review and future research directions. J. Clean. Prod. 172 , 2336–2350 (2018)
Article Google Scholar
Marodin, G., Frank, A.G., Tortorella, G.L., Netland, T.: Lean product development and lean manufacturing: testing moderation effects. Int. J. Prod. Econ. 203 , 301–310 (2018)
Alefari, M., Salonitis, K., Xu, Y.: The role of leadership in implementing lean manufacturing. Procedia CIRP 63 , 756–761 (2017)
Soliman, M., Saurin, T.A.: Lean production in complex socio-technical systems: a systematic literature review. J. Manuf. Syst. 45 , 135–148 (2017)
Shah, R., Ward, P.T.: Lean manufacturing: context, practice bundles, and performance. J. Oper. Manag. 21 , 129–149 (2003)
Sundar, R., Balaji, A.N., Satheesh Kumar, R.M.: A review on lean manufacturing implementation techniques. In: Procedia Engineering, pp. 1875–1885. Elsevier (2014)
Google Scholar
Arunagiri, P., Gnanavelbabu, A.: Identification of high impact lean production tools in automobile industries using weighted average method. In: Procedia Engineering, pp. 2072–2080. Elsevier (2014)
Korkut, D.S., Cakıcıer, N., Erdinler, E.S., Ulay, G., Muhlis, A.: 5S activities and its application at a sample company. J. Biotechnol. 8 , 1720–1728 (2009)
AL-Tahat, M.D., Jalham, I.S.: A structural equation model and a statistical investigation of lean-based quality and productivity improvement. J. Intell. Manuf. 26 , 571–583 (2015)
Pinto, J.L.Q., Matias, J.C.O., Pimentel, C., Azevedo, S.G., Govindan, K.: Just in Time Factory: Implementation Through Lean Manufacturing Tools. Springer (2018)
Veres (Harea), C., Marian, L., Moica, S., Al-Akel, K.: Case study concerning 5S method impact in an automotive company. Procedia Manuf. 22 , 900–905 (2018)
Jilcha, K., Kitaw, D.: Lean influence on occupational safety and health in manufacturing industries. Glob. J. Res. Eng. (2016)
Sari, A., Suryoputro, M., Rahmillah, F.: A study of 6S workplace improvement in ergonomic laboratory. In: IOP Conference Series: Materials Science and Engineering (2017)
Pacana, A., Woźny, A.: Draft questions of 5S pre-audit with regard to health and safety standards for tires retreating plant. Prod. Eng. Arch. 13 (4) (2016)
Gul, M., Ak, M.F.: A comparative outline for quantifying risk ratings in occupational health and safety risk assessment. J. Clean. Prod. 196 , 653–664 (2018)
ISO 45001, Occupational health and safety. https://www.iso.org/iso-45001-occupational-health-and-safety.html
ISO 45001: 2018(en), Occupational health and safety management systems—Requirements with guidance for use. https://www.iso.org/obp/ui/#iso:std:iso:45001:ed-1:v1:en
Anaya-Aguilar, R., Suárez-Cebador, M., Rubio-Romero, J.C., Galindo-Reyes, F.: Delphi assessment of occupational hazards in the wineries of Andalusia, in southern Spain. J. Clean. Prod. 196 , 297–303 (2018)
Lay, A.M., Saunders, R., Lifshen, M., Breslin, F.C., LaMontagne, A.D., Tompa, E., Smith, P.M.: The relationship between occupational health and safety vulnerability and workplace injury. Saf. Sci. 94 , 85–93 (2017)
Camuffo, A., Stefano, F.D., Paolino, C.: Safety reloaded: lean operations and high involvement work practices for sustainable workplaces. J. Bus. Ethics 143 , 245–259 (2017)
Kelby, J.: How to use lean to improve and drive safety performance. Presented at the ASSE Professional Development Conference and Exposition, 9 Sept 2014
Li, S., Wu, X., Zhou, Y., Liu, X.: A study on the evaluation of implementation level of lean construction in two Chinese firms. Renew. Sustain. Energy Rev. 71 , 846–851 (2017)
Horberry, T., Larsson, T.J., Johnston, I., Lambert, J.: Forklift safety, traffic engineering and intelligent transport systems: a case study. Appl. Ergon. 35 , 575–581 (2004)
Download references
Acknowledgements
This work was financially supported by the research unit on Governance, Competitiveness and Public Policy (project POCI-01-0145-FEDER-006939), funded by FEDER funds through COMPETE2020—POCI and by national funds through FCT—Fundação para a Ciência e a Tecnologia. Radu Godina would like to acknowledge financial support from Fundação para a Ciência e Tecnologia (UID/EMS/00667/2019).
Author information
Authors and affiliations.
DEGEIT, University of Aveiro, 3810-193, Aveiro, Portugal
Joana P. R. Fernandes & João C. O. Matias
Research and Development Unit in Mechanical and Industrial Engineering (UNIDEMI), Department of Mechanical and Industrial Engineering, Faculty of Science and Technology (FCT), Universidade NOVA de Lisboa, 2829-516, Caparica, Portugal
Radu Godina
GOVCOPP, University of Aveiro, 3810-193, Aveiro, Portugal
João C. O. Matias
You can also search for this author in PubMed Google Scholar
Corresponding author
Correspondence to João C. O. Matias .
Editor information
Editors and affiliations.
Department of Military Science and Technology, Portuguese Military Academy, Amadora, Portugal
Department of Exact Sciences and Engineering, Portuguese Military Academy, Amadora, Portugal
Sandra Pinelas
School of Technology and Management, Polytechnic Institute of Viseu, Viseu, Portugal
Rights and permissions
Reprints and permissions
Copyright information
© 2019 Springer Nature Switzerland AG
About this paper
Cite this paper.
Fernandes, J.P.R., Godina, R., Matias, J.C.O. (2019). Evaluating the Impact of 5S Implementation on Occupational Safety in an Automotive Industrial Unit. In: Reis, J., Pinelas, S., Melão, N. (eds) Industrial Engineering and Operations Management II. IJCIEOM 2018. Springer Proceedings in Mathematics & Statistics, vol 281. Springer, Cham. https://doi.org/10.1007/978-3-030-14973-4_13
Download citation
DOI : https://doi.org/10.1007/978-3-030-14973-4_13
Published : 17 April 2019
Publisher Name : Springer, Cham
Print ISBN : 978-3-030-14972-7
Online ISBN : 978-3-030-14973-4
eBook Packages : Mathematics and Statistics Mathematics and Statistics (R0)
Share this paper
Anyone you share the following link with will be able to read this content:
Sorry, a shareable link is not currently available for this article.
Provided by the Springer Nature SharedIt content-sharing initiative
- Publish with us
Policies and ethics
- Find a journal
- Track your research
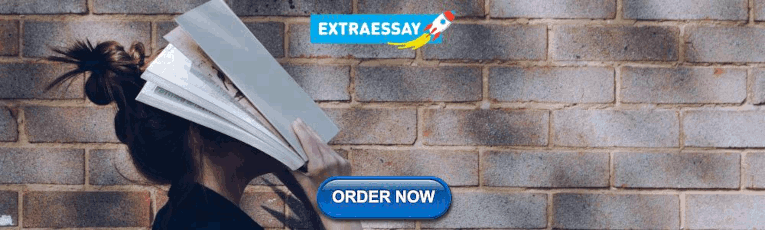
IMAGES
VIDEO
COMMENTS
Abstract. In a constantly changing economic environment strong developed countries created significant management models to follow. 5S, as part of Toyota Production System (the most used management model in automotive industry), is a method which develops discipline and cleanliness at workplace, maximizing efficiency and productivity.
This paper aims to study the relationship. between 5S ev olution and produc tivity in a local company f rom Mures County, Romania, w hich operates in automotive i ndustry. for over 10 yea rs, and ...
This case study covers the data collected for January - December 2016: • 5S evolution - a checklist audit, made of 17 questions, is done in all 8 segments of the company and a percentage is assigned by a special committee; • Productivity - due to confidential data, we used percentage values.
TLDR. The results showed that 5S along with the shadow boarding technique creates improvement in efficiency, workspace, equipment search time, working environment, and safety, which would strongly support the objectives of multinational companies to achieve continuous improvement and higher performance. Expand.
The purpose of this study was to assess the impact of 5S lean tool on the service operation of Toyota Dasmarinas-Cavite with the use of Correlation Analysis. Through this approach, it was found out that 5S has significant impact on the company's performance quality of employees, department operations' productivity, and workplace safety.
"Case study concerning 5S method. impact in an automotive company". [7] Singh, K., Deokar, A. 2018. "E ects of 5S Implementation on Performance of. Organization". [8]
This paper aims to study the relationship between 5S evolution and productivity in a local company from Mures County, Romania, which operates in automotive industry for over 10 years, and it is part of an Austrian group. The objective of this paper was to demonstrate that 5S method is very important and have a positive correlation to overall ...
Fernandes et al. [] in his research to study the 5S contribution to occupational safety performance by implementing 5S in an automotive production line, the author used risk assessment tools to find that the 2S (set in order) gives the significant impact to safety.The advantage of this paper is that the researcher analyzed all the "S" one by one to find the most significant stage in 5S ...
Evaluating the Impact of 5S Implementation on Occupational Safety in an Automotive Industrial Unit ... but a significant instrument for managing the company . 5S is an acronym from the ... Moica, S., Al-Akel, K.: Case study concerning 5S method impact in an automotive company. Proc. Manuf. 22, 900-905 (2018) Google Scholar ...
5S as a methodology has come out of the techniques within Total Productive Maintenance (TPM) and from the Toyota ... Implementation Of 5s Technique In An Automotive Industry 021 ... (2013), "Performance Improvement Through 5S in Small Scale Industry- A case study", International journal of Modern Engineering Research, Vol. 3, pp-1654-1660. ...
4. Case study concerning 5S implementation project in an automotive company. The company involved in the present case study is Hirschmann Automotive an Austrian company which - produces auto ...
Case study concerning 5S method impact in an automotive company. C VERES, L MARIAN, S MOICA, K AL-AKEL. Procedia Manufacturing 22, 900-905, 2018. 273: ... Case Study Regarding the Implementation of One-Piece Flow Line in Automotive Company. ID APAFAIAN, MD EGRI, C VERES. Procedia Manufacturing 46, 244-248, 2020. 22:
Veres et al. did a case study in an Austrian automotive company, Hirchmann Automotive, based in Mures, Romania. The 5S method was applied in the company, as a function of the Toyota Production System (TPS). ... Veres C, Marian L, Moica S, Al-Akel K (2018) Case study concerning 5S method impact in an automotive company. Procedia Manuf 22(January ...
In Abstract a constantly changing economic environment strong developed countries created significant management models to follow. 5S, as part of Toyota Production System (the most used management model in automotive industry), is a method which develops discipline In a constantly and cleanliness changing economic at workplace, environment ...
at Auto car Exhaust. The implementation of 5S has immediate and significant effect on the sequence of activities in the work post, thus influencing the performance of process in the analyzed company. (16) Khedkar et al. (2012) worked on implementation of 5S on plastic moulding industry. 5S is used in small industry
Japanese automotive company, Toyota, founded lean manufacturing (LM) or Toyota Production System (TPS), ... Case study concerning 5S method impact in an automotive company. Procedia Manuf., 22 (2018), pp. 900-905, 10.1016/j.promfg.2018.03.127. View PDF View article Google Scholar [8]
Abstract. This study was developed in a furniture company and aimed to implement some Lean tools, such as 5S and Visual Management to reduce waste, by improving the production process. To carry out this analysis an observation plan was used, having the Spaghetti diagram as a reference as well as the value-added analysis of the operations.
Case study concerning 5S method impact in an automotive company Cristina Veres (Harea)P. a, P0F*, Liviu MarianP. a. P, Sorina MoicaP. b. P, Karam Al-AkelP. a. P a P Technical University of Cluj-Napoca, Memorandumului Street, 28, Cluj-Napoca, 400114, Romania P b P "Petru Maior" University, Nicolae Iorga Street, 1, Tirgu Mures, 540088 ...
In a constantly changing economic environment strong developed countries created significant management models to follow. 5S, as part of Toyota Production System (the most used management model in automotive industry), is a method which develops discipline and cleanliness at workplace, maximizing efficiency and productivity.
In this paper, a case of study in one industrial unit of one of Europe's largest car producers is ... The site was divided in half so that each sorting company had its ... L., Moica, S., Al-Akel, K.: Case study concerning 5S method impact in an automotive company. Procedia Manuf. 22, 900-905 (2018) Google Scholar Jilcha, K., Kitaw, D.: Lean ...
Case study concerning 5S method impact in an automotive company. Procedia Manuf. (2018) ... A case study involving Design for Lean Six Sigma phases of Define, Measure, Analyse, Design, and Verify was utilised to build an API site TPM pilot program. ... Application of Lean Manufacturing to Improve the Duct Production Process of an Air ...
Download scientific diagram | The implementation steps of 5S method [10]. from publication: Case study concerning 5S method impact in an automotive company | In a constantly changing economic ...
In this company it is observed that the tools used in several sections such as assembly, production, packagings are not place in correct place after their usage. ... a case study. Int. J. Lean Enterprise Res., 1 (1) (2014), pp. 22-40. ... Case study concerning 5S method impact in an automotive company. Procedia Manuf., 22 (2018), pp. 900-905.