
- Lean Philosophy
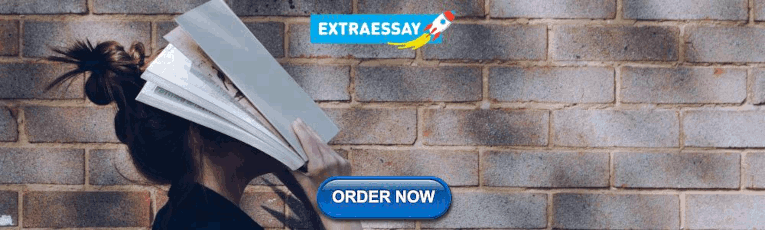
Eight Steps To Practical Problem Solving

The Toyota Way To Problem Solving
The art of problem solving is constantly trying to evolve and be re-branded by folks in various industries. While the new way might very well be an effective method in certain applications. A tried and true way of identifying and solving problems is the eight steps to practical problem solving developed by Toyota, years ago. The system is structured, but simple and practical enough to handle problems of the smallest nature, to the most complex issues.
Using a fundamental and strategic way to solve problems creates consistency within an organization. When you base your results off facts, experience and common sense, the results form in a rational and sustainable way.

The Eight Step Problem Solving Process
- Clarify the Problem
- Breakdown the Problem
- Set the Target
- Analyze the Root Cause
- Develop Countermeasures
- Implement Countermeasures
- Monitor Results and Process
- Standardize and Share Success
The eight steps to practical problem solving also include the Plan, Do, Check and Act (PDCA) cycle. Steps one through five are the planning process. The doing is found in step six. Step seven is the checking . Step eight involves acting out the results of the new standard.
This practical problem solving can be powerful tool to issues facing your organization. It allows organizations to have a common understanding of what defines a problem and what steps are going to be taken in order to overcome the problem efficiently.
The Eight Steps Broken Down:
Step 1: clarify the problem.
A problem can be defined in one of three ways. The first being, anything that is a deviation from the standard. The second could be the gap between the actual condition and the desired condition. With the third being an unfilled customer need.
In order to best clarify the problem, you have to see the problem with your own eyes. This gives you the details and hands-on experience that will allow you to move forward in the process.
Step 2: Breakdown the Problem
Once you’ve seen the problem first hand, you can begin to breakdown the problem into more detailed and specific problems. Remember, as you breakdown your problem you still need to see the smaller, individual problems with your own eyes. This is also a good time to study and analyze the different inputs and outputs of the process so that you can effectively prioritize your efforts. It is much more effective to manage and solve a bunch of micro-problems one at a time, rather than try and tackle a big problem with no direction.
Step 3: Set the Target

Step three is all about commitment and focus. Your attention should now turn towards focusing on what is needed to complete the project and how long it will take to finish. You should set targets that are challenging, but within limits and don’t put a strain on the organization that would hinder the improvement process.
Step 4: Analyze the Root Cause
This is a vital step when problem solving, because it will help you identify the actual factors that caused the issue in the first place. More often than not, there are multiple root causes to analyze. Make sure you are considering all potential root causes and addressing them properly. A proper root cause analysis, again involves you actually going to the cause itself instead of simply relying on reports.
Step 5: Develop Countermeasures
Once you’ve established your root causes, you can use that information to develop the countermeasures needed to remove the root causes. Your team should develop as many countermeasures needed to directly address any and all root causes. Once you’ve developed your countermeasures, you can begin to narrow them down to the most practical and effective based off your target.
Step 6: Implement Countermeasures
Now that you have developed your countermeasures and narrowed them down, it is time to see them through in a timely manner. Communication is extremely important in step six. You’ll want to seek ideas from the team and continue to work back through the PDCA cycle to ensure nothing is being missed along the way. Consider implementing one countermeasure at a time to monitor the effectiveness of each.
You will certainly make mistakes in throughout your problem solving processes, but your persistence is key, especially in step six.
Step 7: Monitor Results and Process
As mistakes happen and countermeasures fail, you need a system in place to review and modify them to get the intended result. You can also determine if the intended outcome was the result of the action of the countermeasure, or was it just a fluke? There is always room for improvement in the problem solving process, but you need to be able to recognize it when it comes to your attention.
Step 8: Standardize and Share Success
Now that you’ve encountered success along your problem solving path, it is time to set the new processes as the new standard within the organization and share them throughout the organization. It is also a good time to reflect on what you’ve learned and address any possible unresolved issues or troubles you have along the way. Ignoring unresolved issues will only lead to more problems down the road.
Finally, because you are a true Lean organization who believes continuous improvement never stops, it is time to tackle the next problem. Start the problem solving process over again and continue to work towards perfection.
Additional Resources
- 8D for Problem Solving – creativesafetysupply.com
- Training to Use 8D Problem-Solving Tactics – blog.creativesafetysupply.com
- The Great Root Cause Problem Solving Debate – realsafety.org
- Design Thinking: Empathy and Iteration for Innovation and Problem-Solving – creativesafetypublishing.com
- 10 Commandments to Continuous Improvement – lean-news.com
- Lean Manufacturing Implementation – The First 5 Steps – iecieeechallenge.org
- No Problem is a Problem – jakegoeslean.com
- The Transitional Steps Involved In The 5s Principles During Implementation – 5snews.com
- The Tools of Kaizen – blog.5stoday.com
Related posts:
- 3P and Lean
- The Vacation Paradox
- Why Single Minute Exchange of Die (SMED)?
- Total Quality Management And Kaizen Principles In Lean Management
- An Engaged Employee is a Productive Employee
- Jim Womack’s Top Misconceptions of the Lean Movement
- Muda, Mura, and Muri: The Three Wastes
GTU Practical
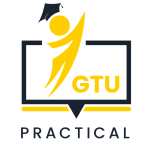
GTU PPS Practical List
Programming for problem solving practical list.
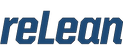
Practical Problem Solving
There is no other business tool more important than problem solving. Despite this, there are very few organisations that really takes it seriously and build a culture of solving problems. Problem solving is the key to both improved results and higher engagement of employees.
Practical problem solving (PPS) is perhaps the single most important tool we have at our disposal. This is the one skill, along with standardized work that Toyota invests the most time and effort in when it comes to developing it’s people. Without these two skills there can be no Continous Improvement, no elimination of waste and no reduction in quality problems. There are a variety of methods and concepts in problem solving, but we like the most practical problem solving. Not only because it gives quick results and that Toyota uses it but also because it is simple, logical and really requires no additional structure of the company (unlike more advanced methods such as six sigma). PPS is something everyone should do as part of their daily work. From the CEO down to the shop floor.
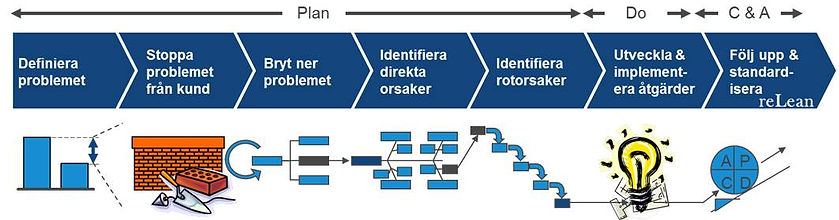
PDCA (Plan Do Check Act), is central to Lean and the problem-solving mindset. It is the basis of all work carried out. PDCA’s strength comes from its simplicity, whether in problem solving, project management or just general planning.
PDCA is the basis for the practical problem solving we teach. It is also the foundation of project planning and general planning in order to achieve a time-efficient process. PDCA teaches us to make well informed, fact based, decisions and implement quickly - a very central concept for Lean. below we will focus on the PDCA from a problem-solving perspective but as you can read in the Lean leadership and decisions sections you will see that PDCA is applied everywhere.
We usually divide the problem solving process in 7 steps (you can see them in the picture above). Sometimes you can even add a step 0 where we prepare the problem solution. Let's take a closer look at how we get through the different steps when we solve a problem
The problem solving process

Define the problem
The first step is to define what the problem really is. We can not do anything until we know that. Sometimes it is called Gap Analysis, which is not entirely wrong, it's about finding a quantifiable gap. A quantifiable gap in turn requires a standard or target. Otherwise, we have nothing to compare against. If there is no standard then introducing this is the first step of a solution. At times just this is sufficient to resolve the issue. We need to gather as much information as we can about the problem at this stage. The better the data is the easier it will be to quantify the problem. Try to specify the problem in a SMART way (Specific, Measurable, Action-oriented, Realistic and Time bound).
Stakeholder analysis
Break down the problem
For us statistics geeks, this is the most enjoyable step in solving the problem. We start by finding the point of cause - where the problem originates from. Here we typically apply the questions of “5W2H” – Where? When? What? Who? Which? How? How many? You will note that when we break down the problem, we do not ask “Why?”. Typical issues here are What shift? Which product? Which machine? What day? What temperature? How much for what? Which types a problem? Was in the process? Was in the machine? Was in business? Repeat on all factories? etc. Sometimes more advanced tools (you can read about it in the DMAIC process) for statistical analysis are required, but you’ll be able to tackle 80% of your problems with those questions and a spread sheet. Once we arrived at a very specific and SMART problem we need to set an equally specific and SMART goal for our problem. You see that we are only now setting a target for ourselves. We can only do this when we have broken the problem down.
Measure and standardise
Before we are done, there are a few things left to do. First, measure and monitor the KPIs to ensure we’ve stopped the problem. We usually test by removing the action and see if the problem occurs again. Important that we control by following both process and KPI. It works like the last step to reflect and standardise. First and foremost, are all standards updated to reflect our improvements? Once that's done, we ask ourselves if there are any similar product or process that can take advantage of what we have learned. Can we replicate the solution? The last thing we do is to celebrate our success and think about the next problem to tackle.
To make life easier, we have of course added a few templates for this. You can find them here below. There are two templates, one simple and one advanced. The simple are usually found in all breast or back pockets of Toyota to fast pick up and structure a problem. The more sophisticated picked up when the problem requires.
Idntifying direct causes
The most common tool used to define direct causes is an “Ishikawa” or “Fish bone” diagram. We use it to think through the possible causes. Sometimes we do it as a brainstorming exercise on the place where the problem happens sometimes we ask someone in the group sit down and make a proposal which we then discuss in a group. The key in this step is not to rule out possible causes. When we are satisfied with our first draft we start verifying any possible direct cause using facts. A bit of a warning. It is often here that we jump to what we believe is the right solution immediately. Again and again. And the problem will not disappear. Weird?! When we have found our direct causes based on the facts we move on to the next step.
5 Why analysis
Here’s how we at reLean think about 5 why analysis. It is also how we were educated on the topic at Toyota;
1. Define the problem (if possible, ask yourself where the problem occurs)
2. Identify direct causes (Make a proper Ishikawa if needed)
3. Ask the question why for every direct cause. Evaluate each why a new Ishikawa, or think at least that any why can branch out in response in Man, Machine, Material, Method (and environment & management whether to be picky)
4. Evaluate each option that appeared in your logic trees with facts (or common sense, depending on how advanced the problem is)
5. Iterate the process for each step the deeper you go (5 whys can be anywhere between 2 to 15 why)
6. When you find the root cause of your problem, ask yourself if you've found the short term (removing the problem for good) or long term (see to that similar problems do not happen again) solution to the root cause of the problem. Both need to be identified and remedied.
Be smart when you make your 5 whys analysis and do not create the entire tree without first verifying the facts of each step and close non-relevant paths directly. "Employee mistake" or similar statements are not acceptable root causes. Never. The principle of the 5 whys is really very simple but it’s still a challenging thing to do. 5 Why is about the art of breaking down a symptom of the real problem - the root cause - by asking questions. Sounds simple in theory, but verifying a root cause or discarding others is a hard thing to do. As humans we are pre-programmed to jumps to conclusions instead of verifying the facts.
Test your why trees to wait for the tree and ask the question "therefore" in the other direction.
Continue asking “why” until you can not ask "why" anymore. When the answer that comes back illogical we stop.
Find both solutions. There are always both short-term and long-term responses to each root cause. Sometimes they are the same, but they are there.
Structure - Problem solving is about structure, ensure that you have a structured template to work on your 5 why analysis.
Develop and implement countermeasures
When we have identified our Root Cause it's time to develop some kind of solution to eliminate or mitigate them. There are always two solutions to every problem. A short-term and a long term solution. Examples of short-term solutions are a jig or poka yoke that makes us unable to assemble two things the wrong way around. The short-term measures ensure that a problem does not continue and we can take away our containment without any risk to the customer. The long-term measures, however often point back to our sourcing, product design, development processes or our management methodology. Here we need to strengthen our processes and methods so that we do not repeat the same error as the just solved. This solves the real root cause that builds up the company in the long term. Now we create clear plans and responsibility for all the actions and rapidly implement all the measures.
Protect the costumer and contain the problem
Once we figured out what the problem is, we sometimes need to put containment in place to stop the problem from affecting our customers. If we put it in place then one of our goals with the problem solution will be to remove the containment again. Far too many times the problem solution stops at this stage which results in layer upon layer of manual inspections so as not to "leak" through problems instead of actually solving them.
Identifying root- causes
There are several ways to carry this out, the most common tend to be 5 why, as described below. You can also use the factor analysis for more math problem formulations. Whatever the method, it is important to be methodical and stick to the facts. Causes can easily turn into excuses and then you will have to start over. If it happens it is usually because it is not factual.
Logic trees and hypothesis trees
Structure is among the most important thing in leadership as it is in problem solving. It helps us to structure thoughts, ideas, communication and strategies. It allows us to ensure that we think of everything and not miss anything. It allows us to easily involve others in our thoughts and use the forces of teamwork.
A great way to structure things are using logic and hypothesis trees. Building these are one of the first things you learn at top consulting firms such as McKinsey & Company. The structure of the different tree types themselves are the same, but the use is slightly different between logic and hypothesis tree. The easiest way to explain it is using an example. We can solve the problem in two ways depending on the conditions we have:
Logic-driven. Logic-driven problem solving is like a math problem. Each part of the problem is divided into sub-sections which in turn are divided into further parts. We think of all possible options. In this way we create a holistic tree that cover all the possible problem causes.
Hypothesis-driven. Hypothesis-driven problem solving is different in that we have an idea of what the solution might be. We add branches on the tree in the same way as in logic-driven problem solving, but instead of taking all the solutions we say what we most probably think the problem is (as we verify the hypothesis and move on, or starts).
Problem: I’m 5 kilograms overweight (un-Lean) and my wife (and thus me) want them to disappear for the summer.
A logic-driven tree had explored all the possible reasons that I weigh 5 kg too much and started asking the question "how do I lose 5 kg for the summer?". We had explored all the possibilities and then tried to verify which ones will actually have an effect.
A Hypothesis Tree would rather attack the challenge of a hypothesis; "The only long-term healthy way to lose 5 kg for the summer is to eat healthily and exercise more". Since this had been broken up into a couple of categories that I suspect applying myself had meant "stop eating unnecessary snacks on the sofa", "max one after work per week" and "running at least 3 times a week."
There we have the difference between logic and hypothesis tree. Use our template and create your own logic and hypothesis trees.

Statistical tools
There are several advanced statistical tools that are frequently used in 6 sigma processes, but we also use as needed. It is unnecessary to boil the ocean for a cup of tea and use them all the time as they are time consuming and advanced tools, but when they are really needed to break down a problem, they are really good!
Regression Analysis
Regression analysis is an important tool in Six Sigma's DMAIC process, but also widely used in quality engineering. The aim of regression analysis is to interpret a number of data points to identify trends or patterns. For the more advanced applications an app called minitab is widely used but in most cases it is sufficient to open excel and plot two values against each other in a common chart. It usually goes a long way in helping us to draw conclusions.
Process capability index
According to all the mechanical and quality technical standards a process should be Capable, repeatable and reliable. It simply means that the machine should be capable to do the right thing, having the ability to always produce the same outcome and be so reliable that it can do it all the time. The Process capability index is a tool used to assess how capable a process is. Process capability index is a widely used tool in fields such as Six Sigma and quality control.
SIPOC is a structured way of describing an end-to-end process in a simple and comprehensive way. SIPOC stands for Supplier, Input, high-level Process, Outputs and Customers. SIPOC is an important part of the DMAIC process in the world of six sigma.

Within the area of you often hear people refer to the 7 Quality Tools, which are used to identify and classify quality problems. These tools are very useful and strongly connected with practical problem solving, especially when we break down the problem according 5W2H.

Pareto - An excellent tool to prioritise issues and actions
Histogram - Applicable when working on tolerance problems, process capability etc.
Control charts (SPS) - Applicable to more advanced problems where we want to identify a process outside its operating limits or tolerances
Regressionsanalys - Often more useful that we thing. Great tool to identify trends or behaviours of two or more parameters
Grafer - Data can be visualised in many ways. It's important to be able to work with many types of graphs that can help us identify patterns, deviations, trends and gaps
Fish bone analysis - Also known as "Ishikawa" is a cause and effect analys that allows us to structure potential problem causes
Check sheets - A simple way of recording information, it gives us a vast amount of information on a problem and it can easily be presented in various ways
- What is Lean?
- Our Approach To Lean
- History & What We’ve Done
- Lean Research
- Lean Capability Development
- Login / Sign up
Sign up and join the community
Email address *
Subscribe to our newsletter
Please select all the ways you would like to hear from us Email
Your personal data will be used to support your experience throughout this website, to manage access to your account, and for other purposes described in our privacy policy .
Home > A3 8 Step Practical Problem Solving – Skill Level 2: Understanding
A3 8 Step Practical Problem Solving – Skill Level 2: Understanding
15th May 2020 -
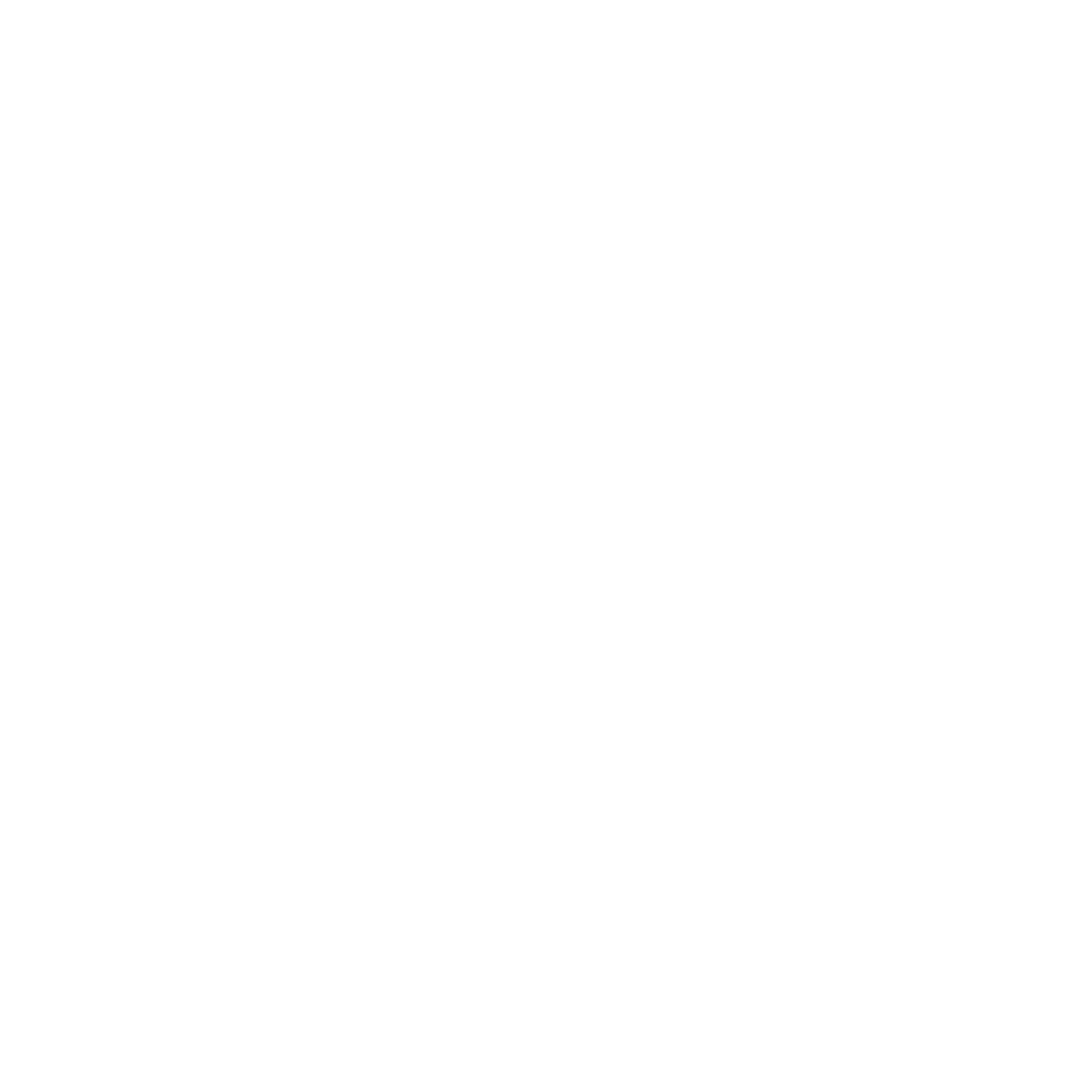
Course Summary
Objectives : Through completeing this Skill Level 2 course you will gain a deep Understanding of how to actually apply the 8 Steps of the A3 Practical Problem Solving (PPS) method, by using a case study and completing a PPS A3.
Duration: 12 hours of self-paced learning where you will complete “teach & try out” sessions on our online platform .
This course is online only with no “live coaching” sessions for extra support .
There is also another version of this skill level 2 course that is available with additional live coaching support, contact us here to find out more information.
Content: This online course is interactive and contains 31 Teach Point Videos, PPS A3 Case Study, 8 Learning Confirmations and a Certificate of Completion.
Support Material :- There are 12 downloads available including a PPS Teach Poster & Facilitation Guide, A3 Visual Guide, 7 Problem Solving Tools Leaflet, Blank A3 Template .
Play Introduction Video
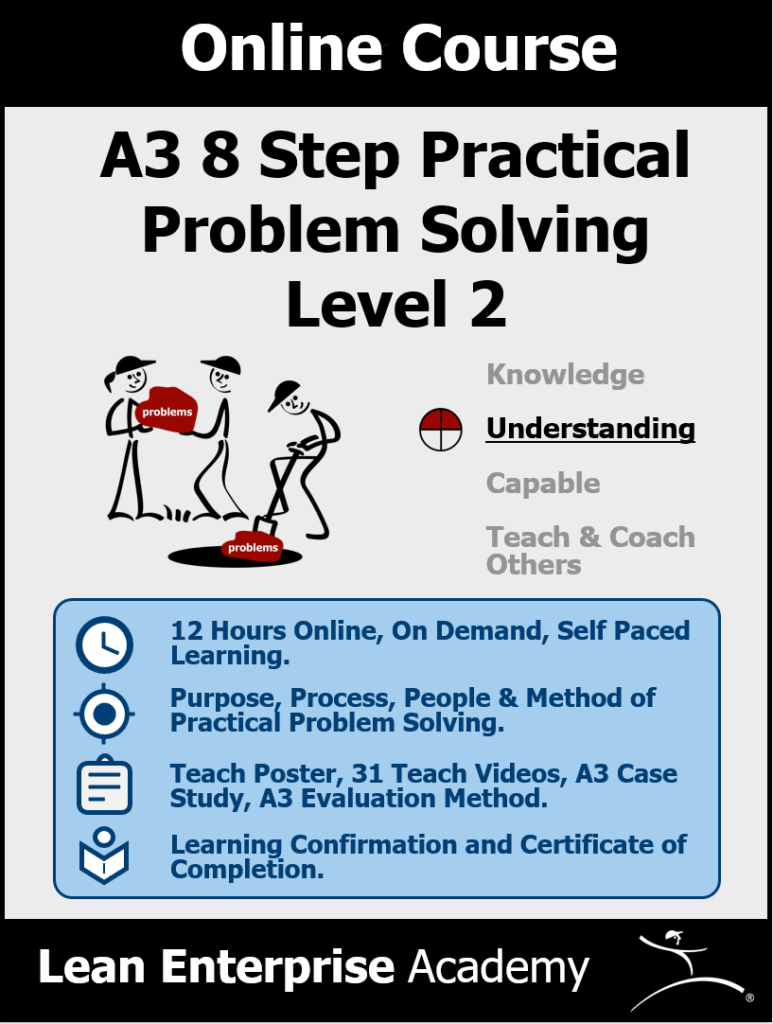
Watch Example T each Point Video From the Course

Course Introduction
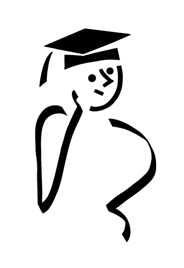
Please complete our FREE Skill Level 1: Knowledge course before starting this Skill Level 2: Understanding course. This course will give you deeper understanding of how to apply the 8 steps of the A3 Practical Problem Solving Method.
Problem Solving is the number one skill to develop in people who want to apply lean thinking & practise within their organisation.
Why? Because the starting point for lean is understanding what situational problems you need to solve and following a robust method to solve them – rather than jumping to solutions. Therefore, if you can engage everyone in identifying and solving problems you will deliver more value to your customers and organisation.
Skill Level 2 – PPS A3 8 Step Method
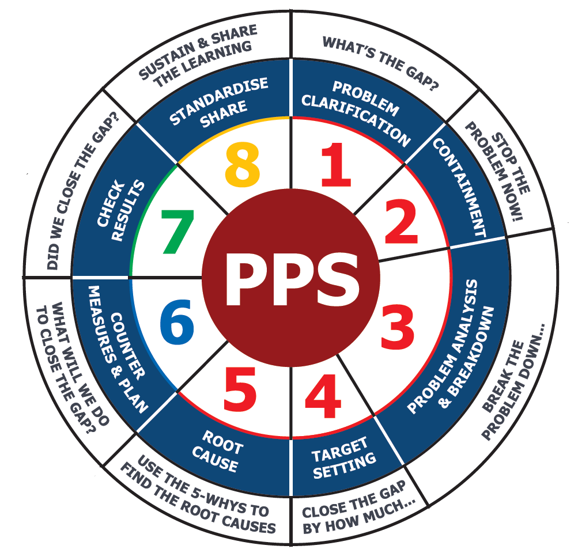
During the course you will gain a deeper understanding of the method and “thinking way” behind solving a problem.
You will learn about about :-
You will also gain some practical experience by completing a PPS A3 from a case study exercise and then compare it with our A3 answer!
The video teach points and learning exercise are broken down into steps to enable you to do short burst learning at your convenience.
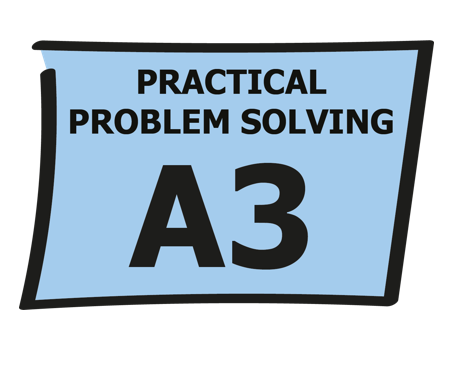
Course Structure & Materials
Language:- English Speaking
Course Structure
12 Hours of self-paced guided learning on our web based learning platform. We recommend you take no longer than 2 weeks to complete.
Once enrolled you will have unlimited access to the course for life!
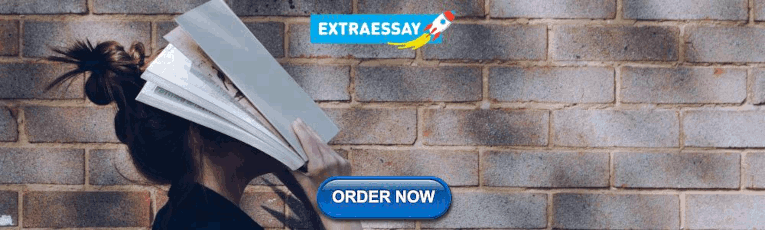
About Our Teach Poster Concept
Where ever possible we try and use a visual “Teach Poster” to explain the subject matter. These are simple, imaged based triggers to remind you of the key concepts and learning points.
From our experience, we have found this to be the most effective way to teach others and enable them to share their knowledge quickly and easily with others.
Support Material Included in this course
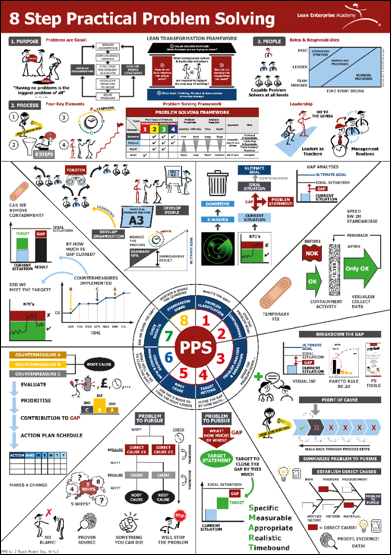
Visual Teach Poster for Skill Levels 1 & 2
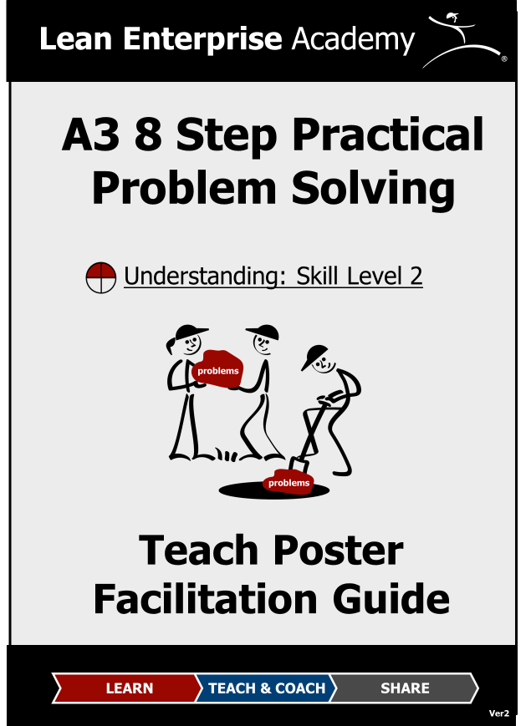
Skill Level 1 & 2 Teach Poster Facilitation Guide
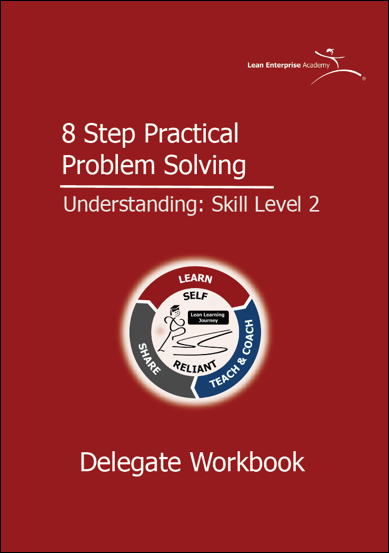
Delegate Workbook
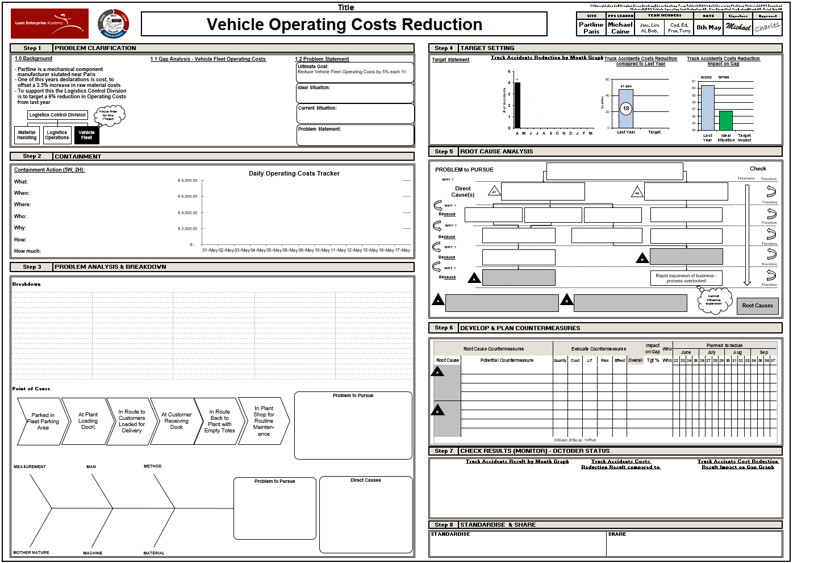
A3 Learning Exercise Worksheet
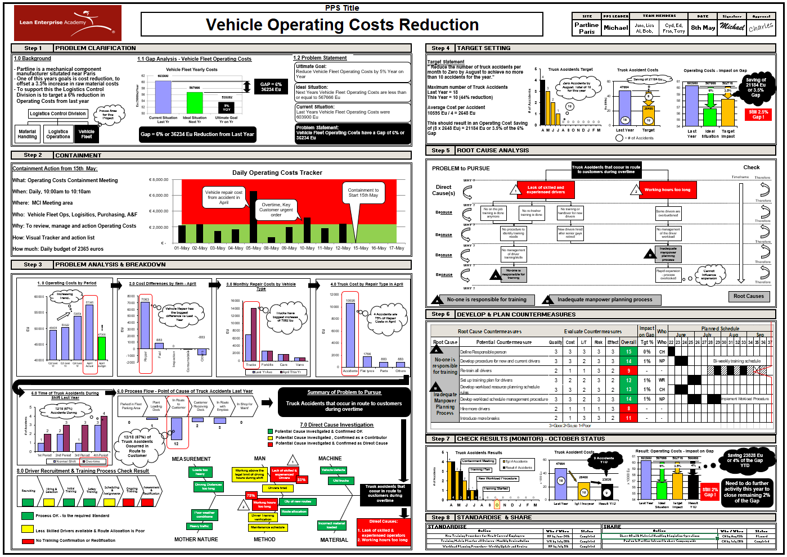
A3 Learning Exercise Answer Sheet
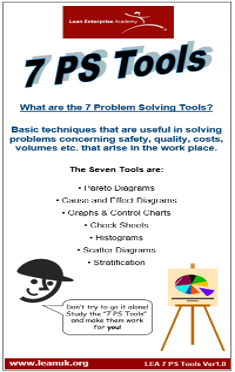
7 Problem Solving Tools Leaflet
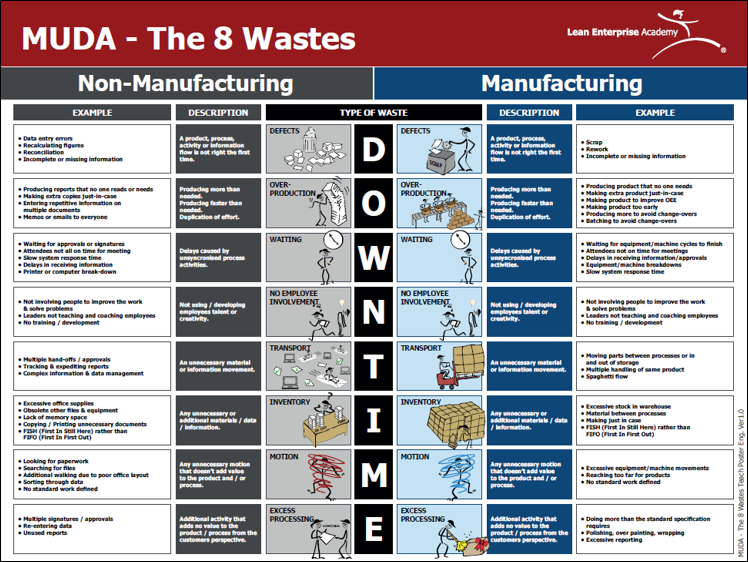
Muda – The 8 Wastes Teach Poster
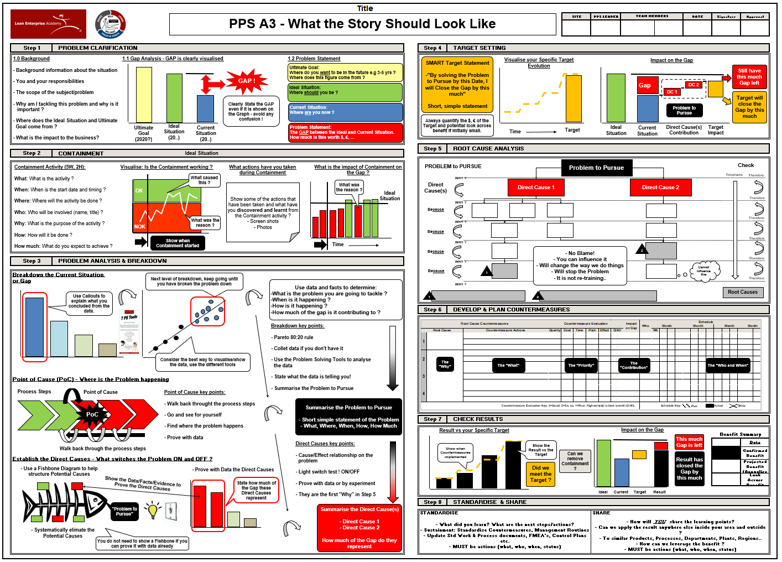
A3 Visual Guide – What Good Looks Like

Blank A3 WorkSheet
Learning Outcomes
By completeing this Skill Level 2 course you will have gained a deeper Understanding about A3 Practical Problem Solving :-
- The thinking way behind 8 step method to solve a problem.
- Experience of constructing a PPS A3 using a case study.
- How to visualise your problem on to an A3.
- The 7 Problem solving tools.
- What is Muda – the 8 Wastes.
Once you have completed this Skill Level 1 & 2 you will know more about the “why and what” of A3 Practical Problem Solving and be able to explain the subject and it’s correct application.
Completion of the Course
At the end of the course recieve a “Certificate of Completion ” for Skill Level 2 (not for capability to do) upon successfully completing the Learning Confirmations.
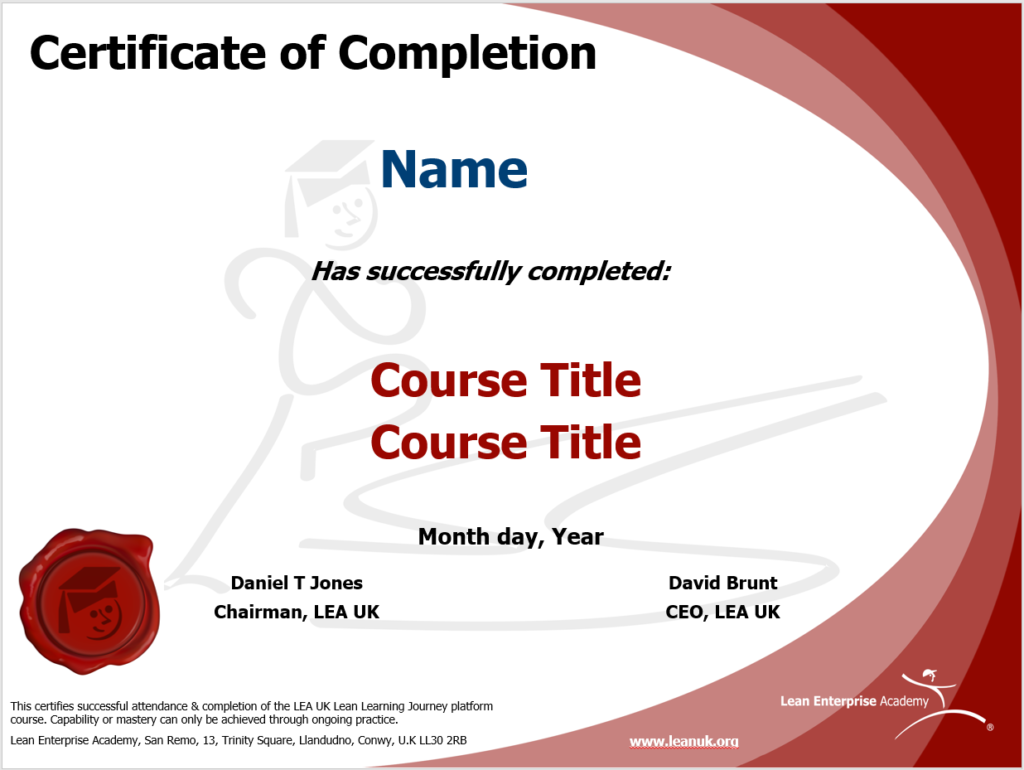
Progressing onto skill Level 3: Capable

Skill Level 3 is aimed at making you capable through “step by step” implementation on a real business problem. An experience PPS A3 Coach is necessary to guide you through this process, so you can receive the feedback and correct A3 evaluation necessary to develop your skill – as described in John Shook’s Managing to Learn book .
If you don’t have access internally to a Skill Level 4 Coach we can offer you online or face to face coaching – just contact us directly if you are interested .
Who is this course for?
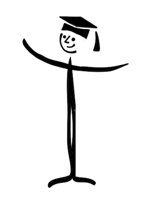
The first step in learning “Problem Solving” is to understand the different types of problems and methods available to solve them. As a guide to ensuring the right people get the right skills , we have developed a Problem Solving Framework as shown below ( This is explained more in our Level 1 Course ) which indicates “ Who ” should get developed in A3 Practical Problem Solving.
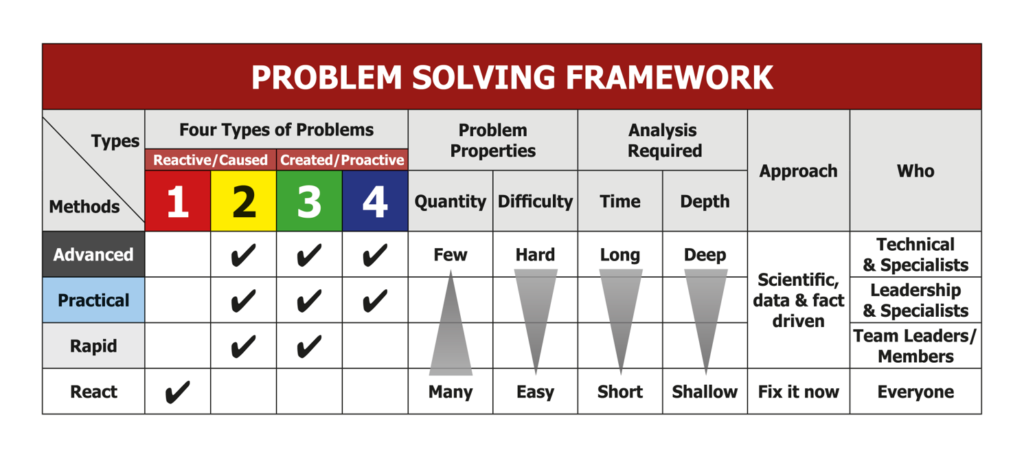
Want to deploy A3 Practical Problem Solving into your organisation ?
We offer online or “face to face” teaching and coaching on any of our courses. We can situationally apply our learning process to meet your capabilty needs, but also ensure it supports your current business conditions.
- Mutliple groups & flexible group sizes.
- Location and time zone considerations.
- Flexibility for timing & schedule of learning activities.
- Connecting the learning activities with achieveing business results.
- Cascade approach using your own leaders to develop others.
Use our Course & Materials internally in your own organisation!
- The online Course & Material can be used internally by your Skill Level 4 Leaders to use as an internal learning process for them to teach and coach others.
- All of the Courses and Materials can be easily made available to use internally in your organisation for an affordable subscription fee of just £119.99 per person/year.
Purchase this Course
LEA is a Non-for-Profit organisation and we only aim to cover our time & material costs when charging for training
Individual Enrolment
Part of the LEA’s purpose is to enable individuals and organisations to learn and improve better, faster and cheaper. In support of this we are trying to make our online materials affordable to all customers. Purchase this Course now for only £50 by clicking the button below!
Organisational Enrolment
We offer online or “face to face” teaching and coaching on any of our courses. We can situationally apply our learning process to meet your capabilty needs. We will taylor an approach to suit your requirments and business conditions, including :-
- Flexible group sizes of 1 to 5 people and multiple groups.
- Flexibility for timing & schedule of Learning Activities.
- Connecting the learning activities with achieving business results.
- A cascade learning approach using your own leaders to develop others.
Example Proposal of Organisational Capability Development
To enable us to adress your situational needs , arrange now for a brief discussion with a Senior LEA Coach.
Purchase Course Support Materials
Want a printed copy of course materials to use .
In addition to the digital downloads that are available as part of the course, you can also purchase a printed copy of the material directly from our shop.
What Questions Do you Have ?
I f you have any further questions, comments or concerns about enrolment in this course, please don’t hesiate to contact us
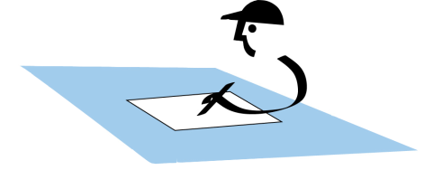
Course Coaches
Check out the details and experience of the course creators and coaches.
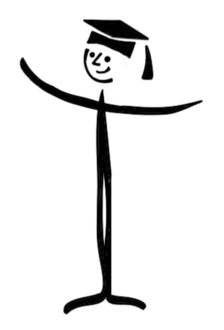
Online Learning Platform: You will be guided through your course that is hosted on our browser-based platform. By first signing up to our website you will then be able to view all purchased and non purchased courses available to you.
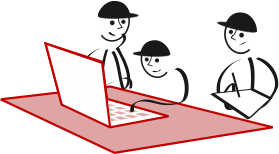
Cancelation Policy
You can cancel your enrolment at any time prior to the first session session for a full refund. Once you have attended the first session, you cannot cancel your enrolment. To cancel please contact us at:
Customer Feeback
Comming Soon
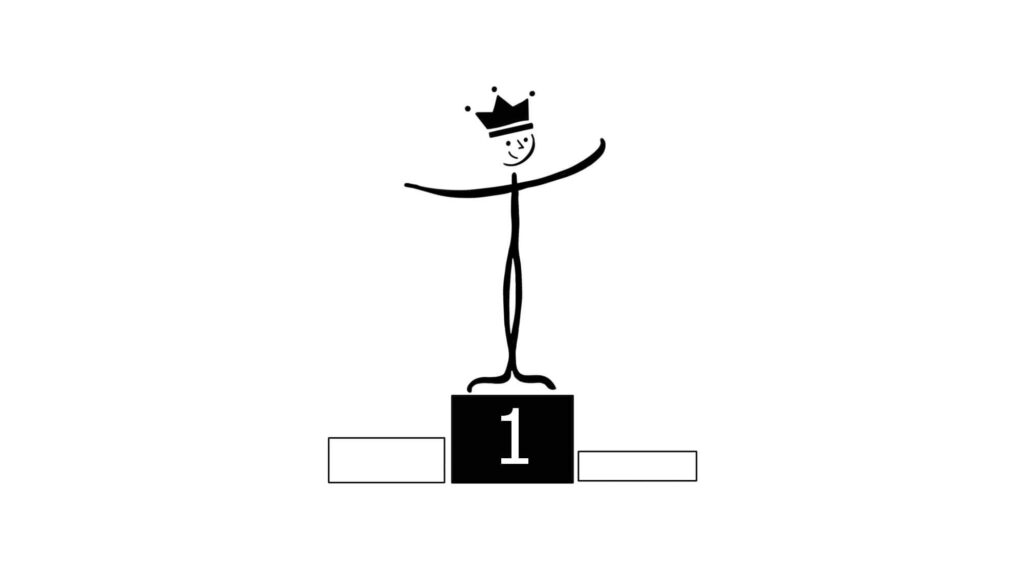
Course Content & Structure
Course Content
Ratings and reviews.
Very logical and practical. It makes things different about the problem solving activities. I learned to explain everything with graphs / charts. Thank you !
I found the course interesting and advanced in terms of problem solving tools. The A3 example is very good and complete. The step 2, containment was a new approach for me, it seems it needs to be exercised carefully, so some interim solutions could turn to permanent solutions. I will start using it, but I am going to develop an A3 example simpler.
Needs improving for online experience.

Toyota Practical Problem Solving (PPS)—Introduction
This entry was posted by pabloadmin on November 28, 2023 at 10:27 am

Lean is a lot of problem solving. Toyota excels at such problem solving, and they have developed their practical problem solving (PPS) approach. For many it is surprising how much time Toyota spends on defining and understanding the problem, whereas (many in) the rest of the world immediately jump to a (possibly inferior) solution. Let me … Read more
The post Toyota Practical Problem Solving (PPS)—Introduction first appeared on AllAboutLean.com .
- February 2024
- January 2024
- December 2023
- November 2023
- October 2023
- September 2023
- August 2023
- February 2023
- January 2023
- December 2022
- Uncategorized

Toyota Practical Problem Solving (PPS)—Monitor and Share

A Quick Recap

- Clarify the Problem
- Break Down the Problem
- Set a Target
- Root-Cause Analysis
- Develop Countermeasures and Implement
Monitor Process and Results
Standardize and share.

There are a few points to keep in mind when doing that. First, if you had multiple countermeasures, can you check the outcome individually for each countermeasure? This is a lot easier if you implement countermeasures one by one as suggested in my last post. Otherwise the cause (i.e., the change in the system) and the effect (the improvement) will get muddled and it is hard to understand what caused what.
Second, also check for other effects of your change. Did it also improve some other factors as a side benefit? Did an improvement in the machine availability also somehow improve quality? Such additional effects are actually quite common. Any free additional improvement is nice and welcome. However, it is also possible that something else got worse. For example, did a faster machine speed make quality worse? In this case you have to consider whether the benefit of your improvement is worth the negative side effects.
Also check the views of the different stakeholders. Try to answer the question “What is in it for me?” from the point of view of the customer, company, employee, and also yourself. Is the customer happy about the change? Are the operators happy?
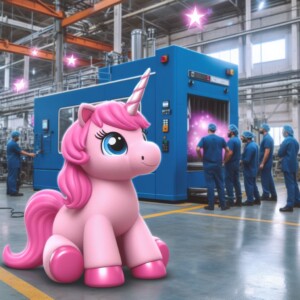
At this point, you have to make a decision. Is the project a success? Did you reach your performance targets and improve the KPIs. Are the negative side effects negligible? If yes, you can continue to standardize and share the results. After that, you can focus on the next biggest issue you have in your area of responsibility. It is rare that managers run out of things to fix. In the pink unicorn situation that you indeed run out of problems to fix, look harder for problems…
If you have not (yet) reached your goals, then the problem is not (yet) solved. You need to go back to understand and break down the problem some more, do more root-cause analysis, and see what you can do differently to achieve your goals.
In my experience, this is often unpleasant and difficult. The final presentation for the project was may be already done, the deadline for the implementation has passed, and focus, resources, and (your) time have already been allocated for the next project. This all needs to be turned back since the problem has not yet been solved. It is, however, a great learning experience. On the other hand, at least some bosses see it as a failure, and hence many employees are worried about how this will impact their career plans. Every company gets the employees it deserves…

For the company it is also beneficial if you can share the results. In some cases, the project you just did was merely a test on a small scale to see if it works. Maybe you have ten (nearly) identical production lines, and you fixed the problem for one line. Great. Now fix the other nine. Use the lessons learned from your project to apply it to other, similar problems. This may be another improvement project, where the learning from this current project help to speed up PDCA for the subsequent projects.

You have done it. You have solved a problem using the Toyota Practical Problem Solving approach. This is the right way to do it, and much better than continuous firefighting (albeit some companies and some people just LOOOOOVE firefighting, since it looks so good; see my post on Heroes, Firefighting, and Corporate Culture ). Now, go out, make sure your problems are solved properly rather than addressing the symptoms, and organize your industry!
PS: Many thanks to the team from the Toyota Lean Management Centre at the Toyota UK Deeside engine plant in Wales, where I participated in their 5-day course. This course gave us a lot of access to the Toyota shop floor, and we spent hours on the shop floor looking at processes. In my view, this the only generally accessible course by Toyota that gives such a level of shop floor involvement.
5 thoughts on “Toyota Practical Problem Solving (PPS)—Monitor and Share”
In my opinion, when you improve but have not met the objective, the best is to stay where you have arrived and, from there, make new efforts to meet the initial objective.
I have made Comments earlier. Why are these not published?
Hi Michael, you commented on another article of this series, I think: Toyota Practical Problem Solving (PPS)—Countermeasures and Implement . I thought it was a useful comment.
I sometimes delete comments if they are spam, others are removed automatically by my spam filter, but I haven’t deleted one of yours nor is one of yours in my (recent) spam filter.
Hope this clears up the confusion 🙂
Hi Christopher, in six sigma we are taught that one-factor-at-a-time experiments are inefficient. I appreciate this clashes with Toyota’s approach. But, what are your thoughts on say putting a Taguchi design in the monitor process & results?
Hi Jonathan, good point. I have used Design of Experiments myself, too, and find them quite useful. The problem is that for a good DOE, you need to switch factors on and off or generally change the variable to find out its impact. E.g. for a simple 2 variable analysis you could have 4 points (Low/Low; Low/High; High/Low; and High/High). This would require you to “undo” previous improvements, which could be a bother and could be detrimental for the sake of understanding the system. Doing the improvements one by one may actually be best in most cases. But, an interesting point. Thanks for sharing!
Leave a Comment
Notify me of new posts by email.
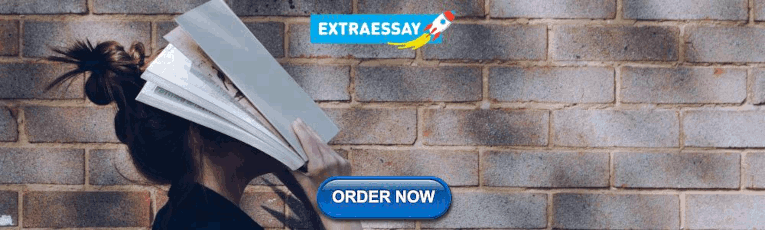
IMAGES
VIDEO
COMMENTS
Practical Problem Solving (PPS) is an eight-step process for implementing the incremental improvements characteristic of any Lean management program. Here's a brief look at Practical Problem Solving and what this fundamental Lean concept entails.
Implement Countermeasures. Monitor Results and Process. Standardize and Share Success. The eight steps to practical problem solving also include the Plan, Do, Check and Act (PDCA) cycle. Steps one through five are the planning process. The doing is found in step six. Step seven is the checking . Step eight involves acting out the results of the ...
Lean is a lot of problem solving. Toyota excels at such problem solving, and they have developed their practical problem solving (PPS) approach.For many it is surprising how much time Toyota spends on defining and understanding the problem, whereas (many in) the rest of the world immediately jump to a (possibly inferior) solution.
A3 8 Step Practical Problem Solving (PPS) is a structured and effective problem-solving process used by individuals and teams to solve challenging, medium term, business and operational problems, originally pioneered by Toyota. Learn about the 8-step process, including clarifying the problem, containment, analysing & breaking it down, target ...
Practical Problem Solving. Practical Problem Solving (PPS) is a Lean methodology initially developed in the Toyota factory that expands on the PDCA cycle (Plan, Do, Check, Act) and turns problem-solving into a systematic eight-step process. Practical Problem Solving allows organizations to estab ...
Skill Level 2 will progress you to having a deeper Understanding about A3 Practical Problem Solving (PPS) 8 Steps by covering :-The thinking way behind each of the 8 steps to solve a problem. Real Experience of constructing a PPS A3 using a case study. How to visualise your problem on to an A3. The 7 Problem solving tools.
PPS Overview • DMAIC: A Six Sigma methodology, DMAIC stands for Define, Measure, Analyze, Improve, and Control. The 8 Steps to Practical Problem Solving 1. _____ the Problem: clearly describe the current situation while going to investigate the problem with our own eyes. Also try to contain the problem so it doesn't affect the customer.
PPS Lvl 1 Teach Poster Eng. Ver1.0 8 Step Practical Problem Solving Problems are Good! Roles & Responsibilities D P L E A R N I N G A C 8 STEPS 1 3 2 4 IMPROVING STRATEGY IMPROVING PROCESSES RUNNING PROCESSES TIME SPENT DOING EXEC TEAM MEMBER LEADER VALUE-DRIVEN PURPOSE: What Problem are we trying to solve?
Practical Problem Solving (PPS) is a teachable, scalable approach based on the scientific method, which can solve the vast majority of your problems. PPS teaches clear thinking, reinforces lean concepts and engages team members at all levels. To create and . sustain. problem solvers at all levels we need to link problem solving to core management
Facilitator's Guide. PPS Overview. An overview of the 8 steps to Practical Problem Solving. A step by step guide to presenting Gemba Academy's 5S course to lean learners in all positions. This guide includes key points, discussion items, quiz questions and answers, and helpful tips. Using Gemba Academy's online learning content, any ...
As listed in my previous post, the Toyota Practical Problem Solving approach consists of the steps listed below. Clarify the Problem. Break Down the Problem. Set a Target. Root-Cause Analysis. Develop Countermeasures and Implement. Monitor Process and Results. Standardize and Share. Before you start to clarify the problem, you may also need to ...
In this post of my series on the Toyota Practical Problem Solving (PPS), we finally get to the part many were excitedly waiting for—the development of countermeasures and their implementation. Some people like this part of actually doing the improvement (and hence finally the "Do" part of PDCA) so much that they skip the "Plan" part ...
1. The first step in the process has us clarifying the problem. In other words, we must clearly describe the current situation, while going to see with our own eyes in order to get the facts. 2. The second step of the process has us breaking the big vague problem downto its smaller, more specific problems. 3.
The Practical Problem Solving (PPS) model we learned and successfully applied from working with Toyota group, has 7 steps. We'll show you each of those steps and the most common pitfall at each ...
This is the last of an 8 part mini series on the A3 8 Step Practical Problem Solving method. We have already covered:-. Step 1 - Problem Clarification. Step 2 - Containment. Step 3 - Problem Analysis & Breakdown. Step 4 - Target Setting. Step 5 - Root Cause. Step 6 - Countermeasures & Plan. Step 7 - Check Results.
LIST OF PRACTICALS. Write a program to that performs as calculator ( addition, multiplication, division, subtraction). Write a C program to interchange two numbers. Write a C program to find that the accepted number is Negative, or Positive or Zero. Write a C program to check whether the entered character is capital, small letter, digit or any ...
A Quick Recap. As listed in my previous post, the Toyota Practical Problem Solving approach consists of the steps listed below. Clarify the Problem. Break Down the Problem. Set a Target. Root-Cause Analysis. Develop Countermeasures and Implement. Monitor Process and Results. Standardize and Share.
Practical problem solving (PPS) is perhaps the single most important tool we have at our disposal. This is the one skill, along with standardized work that Toyota invests the most time and effort in when it comes to developing it's people. Without these two skills there can be no Continous Improvement, no elimination of waste and no reduction ...
Objectives: Through completeing this Skill Level 2 course you will gain a deep Understanding of how to actually apply the 8 Steps of the A3 Practical Problem Solving (PPS) method, by using a case study and completing a PPS A3. Duration: 12 hours of self-paced learning where you will complete "teach & try out" sessions on our online platform.
Lean is a lot of problem solving. Toyota excels at such problem solving, and they have developed their practical problem solving (PPS) approach. For many it is surprising how much time Toyota spends on defining and understanding the problem, whereas (many in) the rest of the world immediately jump to a (possibly inferior) solution. Let me …
PPS is based upon the fundamental framework and 4 Steps of Select, Contain, Correct, Prevent. Disciplined Problem Solving. Basic thinking way and approach to solving a problem. Size of the Correct portion. Its is the largest portion indicating where we will spend most of our time whilst solving the problem.
A Quick Recap. As listed in my previous post, the Toyota Practical Problem Solving approach consists of the steps below. Clarify the Problem. Break Down the Problem. Set a Target. Root-Cause Analysis. Develop Countermeasures and Implement. Monitor Process and Results. Standardize and Share.