Root Cause Analysis: A Complete Guide With Examples (2023)
Root Cause Analysis (RCA) is not just a structured method of problem-solving; it's a vital component of organisational leadership. The goal of RCA is to fully understand what caused an issue, allowing for effective corrective actions.
One of the first steps in a successful RCA is identifying performance or opportunity gaps within an organisation. These gaps reflect ways in which an organisation falls short or fails to deliver on its capabilities. RCA helps in pinpointing these gaps, thereby allowing for more targeted solutions.
This article will take you through the benefits of RCA and the three basic types of root causes behind workplace incidents. We’ll then explore the two popular methodologies for RCA and how you can use the RCA methodology to identify them.
Finally, we’ll share tools and best practices to help you implement a robust RCA framework so you can develop a comprehensive problem-solving process for safety and risk management in your organisation.
Read on to discover how RCA can revolutionise your approach to problem-solving and risk management.
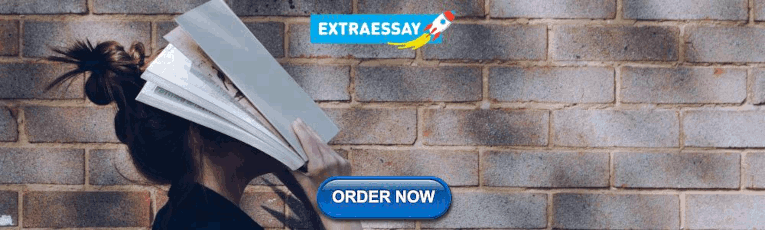
The benefits of Root Cause Analysis (RCA)
Without a structured RCA framework for resolving incidents, organisations risk implementing superficial quick fixes that may address some of the symptoms but not the core problems.
An effective RCA methodology helps an organisation's Health & Safety (H&S) team to identify the root causes of a reported incident in the workplace, which is essential to assign effective preventive or corrective actions . Implementing this framework have many benefits:
- Save time, money, and resources because they can identify and invest in the right preventive and corrective actions.
- Prevent the incident from recurring because they can correct the factors causing the issues.
- Prevent more damage or injury caused by a recurring incident.
- Prevent more downtime caused by a recurring incident.
- Boost productivity because they don’t have to revisit the same incident and spend extra time trying to solve the underlying issues.
The three basic types of root cause
There are three fundamental types of root causes:
- Environmental root cause These are causes related to external factors such as moisture levels, weather, or geography.
- Individual root cause These are causes related to an individual’s behaviour, personal choices, ability, or circumstance.
- Organisational root cause These are causes involving internal organisational structure or processes.
The two popular RCA frameworks
A study by Baylor University Medical Center Proceedings identified two popular RCA frameworks. We will cover each one with an example.
#1: The "5 Whys" Method
This is perhaps the most popular RCA technique because of its simplicity. The method is to ask why something happened at least five times. Here’s an example of how it works.
Incident: A construction worker fell and broke his arm.
- “Ask Why” #1: Why did he fall? Answer: He tripped on a wire
- “Ask Why” #2: Why was the wire on the ground? Answer: It was an extension wire needed to supply power to a tool on the other side.
- “Ask Why” #3: Why was the wire pulled across a thoroughfare? Answer: There was no power socket on the other side.
- “Ask Why” #4: Why is there only one power socket in that area? Answer: There aren’t enough portable generators on the site.
- “Ask Why” #5: Why aren’t enough portable generators on the site? Answer: The application requesting the budget to rent a few more portable generators is pending approval.
Using this RCA technique, we’ve identified the actual root cause to be an organisational root cause. The solution for the organisation is to improve the process of approving budgets.
Speeding up the process of approving budgets doesn’t just help prevent future similar incidents. It may also bring the added benefit of improving productivity when construction workers can quickly get what they need to perform their tasks.
Without using this RCA technique, one could have soon concluded that it was solely an environmental or individual root cause. Any corrective actions in these areas are likely to be ineffective or short-term.
#2: Causal Tree
A causal tree is used to evaluate other possible causes that contributed to the incident. This can help organisations identify other possible preventive or corrective actions. Here’s an example of how a causal tree could look like for the same incident example above:
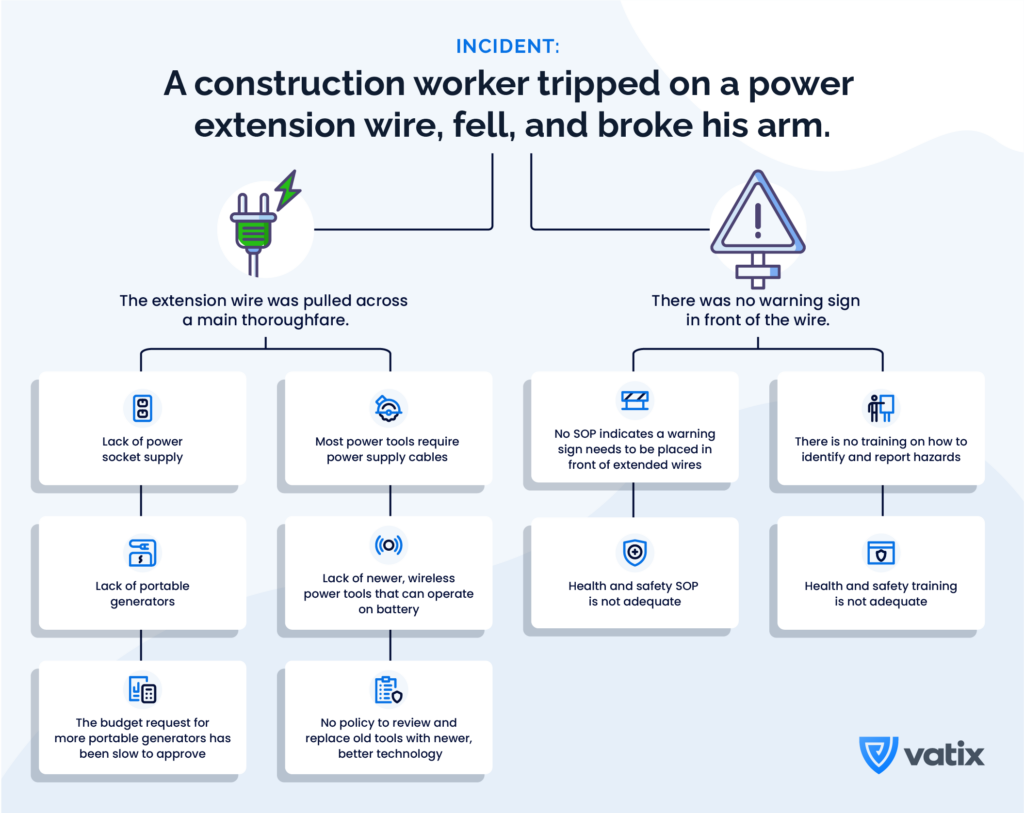
Organisations can explore other possible root causes that need addressing using a causal tree. This RCA methodology is beneficial for identifying root causes across environmental, individual, and organisational categories. Another advantage of using the causal tree framework is that it allows organisations to implement short-term solutions to prevent incidents while they take more time to find answers to more prominent issues. For example, the construction company can implement the short-term solution of placing warning signs in front of extended wires on the ground. Meanwhile, the organisation will look into solving the other root causes identified, such as improving the budget approval process and hazard reporting training.
Common Mistakes to Avoid in Root Cause Analysis
Root Cause Analysis (RCA) can be highly effective in addressing workplace safety issues when done correctly.
However, there are some common mistakes that organisations make when conducting RCA.
Mistake #1: Jumping to conclusions
One of the most common mistakes is jumping to conclusions without thoroughly examining the available information. This often leads to implementing quick fixes that do not address the root cause of the problem.
Tip: Ensure that you take the time to gather all relevant information and systematically work through the RCA process to identify the underlying cause.
Mistake #2: Focusing only on individual errors
Another mistake is solely blaming individuals for incidents without considering the broader organisational context. This can lead to a culture of blame and an unwillingness to report incidents in the future.
Tip: While it is essential to consider individual factors, also examine organisational root causes and environmental factors that may have contributed to the incident. This will help to create a more comprehensive understanding of the issue and lead to more effective solutions.
Mistake #3: Neglecting to involve the right people
One common mistake organisations make is neglecting to involve the right people in the RCA process. A successful RCA requires input from various stakeholders, including employees directly involved in the incident, supervisors, and management. Collaborative analysis helps in collecting a variety of viewpoints and promotes a sense of collective accountability for workplace safety.
Tip: Involving all pertinent stakeholders in the RCA process is crucial, as it aids in collecting a variety of viewpoints and promotes a sense of collective accountability for workplace safety.
Mistake #4: Inadequate documentation
Poor documentation of the RCA process and its outcomes can lead to a lack of accountability and hinder the implementation of corrective actions.
Tip: Document every step of the RCA process, including the incident description, investigation, root cause identification, and proposed corrective actions. This will help ensure that all stakeholders are aware of their responsibilities and can track the progress of the implemented solutions.
Mistake #5: Failing to follow up on corrective actions
Implementing corrective actions is only one part of the RCA process. Organisations sometimes fail to follow up on these actions, which can lead to a recurrence of the incident or issue.
Tip: Establish a system to monitor the progress of corrective actions and evaluate their effectiveness. Regularly review the implemented solutions and make any necessary adjustments to ensure that the root cause is fully addressed and the risk of recurrence is minimised.
How to implement a robust RCA framework
To enhance workplace safety, it is crucial to establish a strong RCA framework within your organisation.
These are the following steps to implement such a framework:
- Train the H&S team on how to use the different types of RCA frameworks.
- Make it easy for employees to report incidents and other events like near misses.
- Update the new employee training, health and safety training, and SOP guides on submitting incident reports and conducting RCA.
- Conduct regular health and safety training sessions.
- Creating an action plan: outline the steps to be taken, the stakeholders involved, and the timeline for implementation
The importance of high-quality incident and hazard reports
The effectiveness of any Root Cause Analysis (RCA) relies heavily on the input data's accuracy and quality. Therefore, it is imperative to have a reliable incident reporting system in place to ensure the provision of high-quality input data.
Here are the characteristics of a high-quality incident report:
- Records the incident's time, date, and location.
- Is honest, clear, and concise.
- Provides accurate information that doesn’t leave out important facts.
- Provide as much context as possible.
- It is written in a first-person, objective observation of what happened, not what they think might have happened.
To write an accurate incident report, employees should be encouraged to start writing the report as soon as possible.
Delaying writing the report can lead to inaccurate reports or reports without enough detail because the memory gets fuzzy. Whenever possible or relevant, employees should also attach photos for additional context.
To help you navigate the complexities of incident reporting, we strongly recommend downloading our free checklist and comprehensive guide .
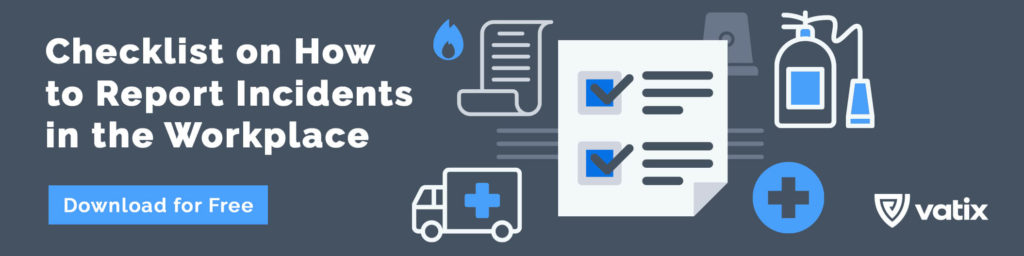
Best practices to improve incident reporting and RCA
One of the best practices to improve the quality of incident reports is digitalising the incident reporting process.
Here’s an example of how Vatix’s incident reporting systems can improve the quality of workplace incident reports and RCA.
- Higher quality incident reports Our mobile platform makes it easy for employees to report an incident from anywhere without the friction of filling out and submitting a paper form. Facilitating on-the-spot reporting for employees minimises the likelihood of postponing or neglecting to report incidents or other events. Faster reporting of incidents also improves the quality of the report. Employees are more likely to record details with better descriptions and upload photos directly from their mobile devices, improving the data needed for an effective RCA.
- Customise incident types to an organisation’s specific needs Our incident reporting software allows organisations to customise the types of incidents employees can report. These templates eliminate the need to print out, distribute, and file multiple forms.
- Easily customise the incident reporting template to capture relevant information. With our incident reporting software, organisations can customise the incident reporting forms to ensure employees submit all required and relevant information.
- Real-time reporting and location tracking for faster response Paper-based incident reporting causes a lot of delays and it can take hours before supervisors or managers can view the incident reports. With real-time mobile incident reporting, employees can submit incidents on-the-spot and the H&S team will be alerted with a location so they can respond to the incident within minutes. In some cases, faster response time with location tagging can be the difference between life and death.
- Easy to get more context at a glance Unlike manual paper-and-pen incident reporting forms, employees can easily add photographs to the incident report directly from their mobile. The incident reporting app also logs the location and provides visual maps for additional context at a glance.
Improve workplace health & safety processes
By combining mobile incident reporting with an effective RCA strategy, organisations can respond to incidents faster and more effectively to create a positive safety culture, leading to increased productivity and decreased risk of accidents and injuries. Talk to our sales here to learn more about how you can customise our mobile incident reporting software to fit your business and improve workplace safety.
Related Articles
Subscribe to our newsletter, subscribe to our newsletter.
- Business Essentials
- Leadership & Management
- Credential of Leadership, Impact, and Management in Business (CLIMB)
- Entrepreneurship & Innovation
- Digital Transformation
- Finance & Accounting
- Business in Society
- For Organizations
- Support Portal
- Media Coverage
- Founding Donors
- Leadership Team
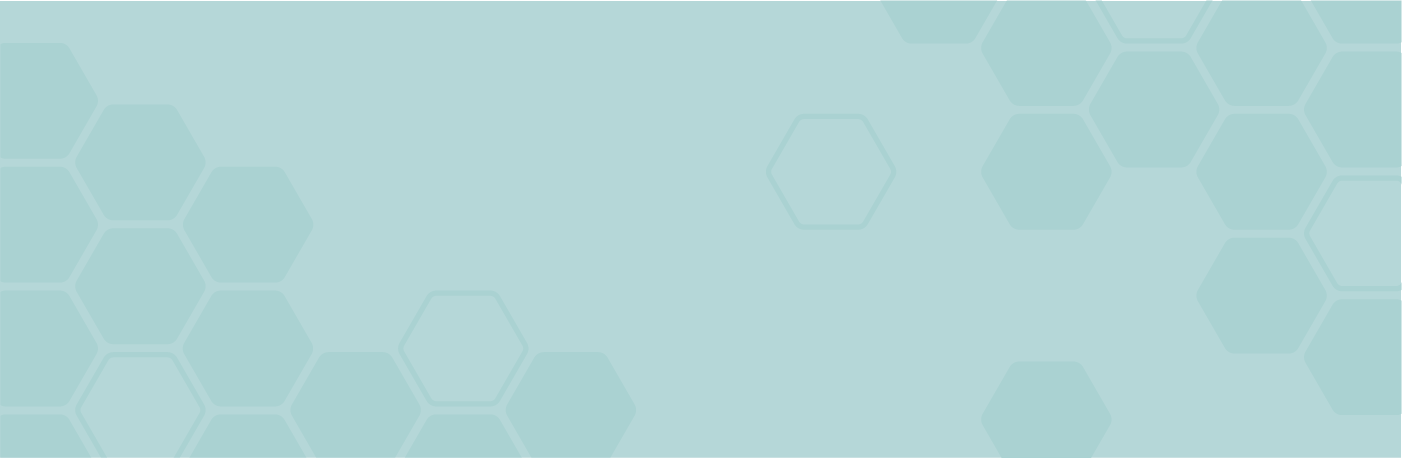
- Harvard Business School →
- HBS Online →
- Business Insights →
Business Insights
Harvard Business School Online's Business Insights Blog provides the career insights you need to achieve your goals and gain confidence in your business skills.
- Career Development
- Communication
- Decision-Making
- Earning Your MBA
- Negotiation
- News & Events
- Productivity
- Staff Spotlight
- Student Profiles
- Work-Life Balance
- AI Essentials for Business
- Alternative Investments
- Business Analytics
- Business Strategy
- Business and Climate Change
- Design Thinking and Innovation
- Digital Marketing Strategy
- Disruptive Strategy
- Economics for Managers
- Entrepreneurship Essentials
- Financial Accounting
- Global Business
- Launching Tech Ventures
- Leadership Principles
- Leadership, Ethics, and Corporate Accountability
- Leading with Finance
- Management Essentials
- Negotiation Mastery
- Organizational Leadership
- Power and Influence for Positive Impact
- Strategy Execution
- Sustainable Business Strategy
- Sustainable Investing
- Winning with Digital Platforms
Root Cause Analysis: What It Is & How to Perform One
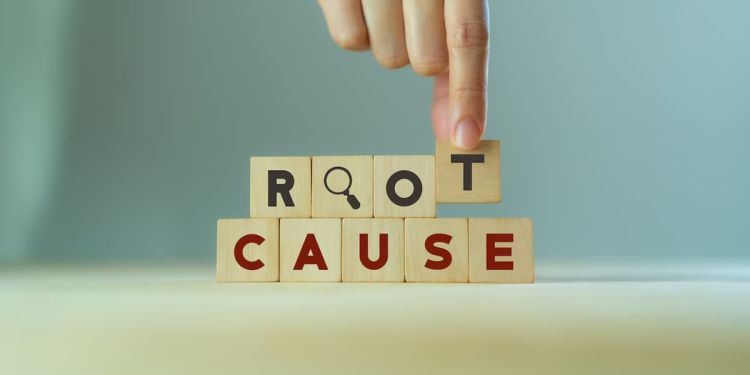
- 07 Mar 2023
The problems that affect a company’s success don’t always result from not understanding how to solve them. In many cases, their root causes aren’t easily identified. That’s why root cause analysis is vital to organizational leadership .
According to research described in the Harvard Business Review , 85 percent of executives believe their organizations are bad at diagnosing problems, and 87 percent think that flaw carries significant costs. As a result, more businesses seek organizational leaders who avoid costly mistakes.
If you’re a leader who wants to problem-solve effectively, here’s an overview of root cause analysis and why it’s important in organizational leadership.
Access your free e-book today.
What Is Root Cause Analysis?
According to the online course Organizational Leadership —taught by Harvard Business School professors Joshua Margolis and Anthony Mayo— root cause analysis is the process of articulating problems’ causes to suggest specific solutions.
“Leaders must perform as beacons,” Margolis says in the course. “Namely, scanning and analyzing the landscape around the organization and identifying current and emerging trends, pressures, threats, and opportunities.”
By working with others to understand a problem’s root cause, you can generate a solution. If you’re interested in performing a root cause analysis for your organization, here are eight steps you must take.
8 Essential Steps of an Organizational Root Cause Analysis
1. identify performance or opportunity gaps.
The first step in a root cause analysis is identifying the most important performance or opportunity gaps facing your team, department, or organization. Performance gaps are the ways in which your organization falls short or fails to deliver on its capabilities; opportunity gaps reflect something new or innovative it can do to create value.
Finding those gaps requires leveraging the “leader as beacon” form of leadership.
“Leaders are called upon to illuminate what's going on outside and around the organization,” Margolis says in Organizational Leadership , “identifying both challenges and opportunities and how they inform the organization's future direction.”
Without those insights, you can’t reap the benefits an effective root cause analysis can produce because external forces—including industry trends, competitors, and the economy—can affect your company’s long-term success.
2. Create an Organizational Challenge Statement
The next step is writing an organizational challenge statement explaining what the gap is and why it’s important. The statement should be three to four sentences and encapsulate the challenge’s essence.
It’s crucial to explain where your organization falls short, what problems that poses, and why it matters. Describe the gap and why you must urgently address it.
A critical responsibility is deciding which gap requires the most attention, then focusing your analysis on it. Concentrating on too many problems at once can dilute positive results.
To prioritize issues, consider which are the most time-sensitive and mission-critical, followed by which can make stakeholders happy.
3. Analyze Findings with Colleagues
It's essential to work with colleagues to gain different perspectives on a problem and its root causes. This involves understanding the problem, gathering information, and developing a comprehensive analysis.
While this can be challenging when you’re a new organizational leader, using the double helix of leadership —the coevolutionary process of executing organizational leadership's responsibilities while developing the capabilities to perform them—can help foster collaboration.
Research shows diverse ideas improve high-level decision-making, which is why you should connect with colleagues with different opinions and expertise to enhance your root cause analysis’s outcome.
4. Formulate Value-Creating Activities
Next, determine what your company must do to address your organizational challenge statement. Establish three to five value-creating activities for your team, department, or organization to close the performance or opportunity gap you’ve identified.
This requires communicating organizational direction —a clear and compelling path forward that ensures stakeholders know and work toward the same goal.
“Setting direction is typically a reciprocal process,” Margolis says in Organizational Leadership . “You don't sit down and decide your direction, nor do you input your analysis of the external context into a formula and solve for a direction. Rather, setting direction is a back-and-forth process; you move between the value you'd like to create for customers, employees, investors, and your grasp of the context.”

5. Identify Necessary Behavior Changes
Once you’ve outlined activities that can provide value to your company, identify the behavior changes needed to address your organizational challenge statement.
“Your detective work throughout your root cause analysis exposes uncomfortable realities about employee competencies, organizational inefficiencies, departmental infighting, and unclear direction from leadership at multiple levels of the company,” Mayo says in Organizational Leadership .
Factors that can affect your company’s long-term success include:
- Ineffective communication skills
- Resistance to change
- Problematic workplace stereotypes
Not all root cause analyses reveal behaviors that must be eliminated. Sometimes you can identify behaviors to enhance or foster internally, such as:
- Collaboration
- Innovative thinking
- Creative problem-solving
6. Implement Behavior Changes
Although behaviors might be easy to pinpoint, putting them into practice can be challenging.
To ensure you implement the right changes, gauge whether they’ll have a positive or negative impact. According to Organizational Leadership , you should consider the following factors:
- Motivation: Do the people at your organization have a personal desire for and commitment to change?
- Competence: Do they have the skills and know-how to implement change effectively?
- Coordination: Are they willing to work collaboratively to enact change?
Based on your answers, decide what behavior changes are plausible for your root cause analysis.
7. Map Root Causes
The next step in your analysis is mapping the root causes you’ve identified to the components of organizational alignment. Doing so helps you determine which components to adjust or change to implement employee behavior changes successfully.
Three root cause categories unrelated to behavior changes are:
- Systems and structures: The formal organization component, including talent management, product development, and budget and accountability systems
- People: Individuals’ profiles and the workforce’s overall composition, including employees’ skills, experience, values, and attitudes
- Culture: The informal, intangible part of your organization, including the norms, values, attitudes, beliefs, preferences, common practices, and habits of its employees
8. Create an Action Plan
Using your findings from the previous steps, create an action plan for addressing your organizational problem’s root cause and consider your role in it.
To make the action plan achievable, ensure you:
- Identify the problem’s root cause
- Create measurable results
- Ensure clear communication among your team
“One useful way to assess your potential impact on the challenge is to understand your locus of control,” Mayo says in Organizational Leadership , “or the extent to which you can personally drive the needed change or improvement.”
The best way to illustrate your control is by using three concentric circles: the innermost circle being full control of resources, the middle circle representing your ability to influence but not control, and the outermost circle alluding to shifts outside both your influence and control.
Consider these circles when implementing your action plan to ensure your goals don’t overreach.

The Importance of Root Cause Analysis in Organizational Leadership
Root cause analysis is a critical organizational leadership skill for effectively addressing problems and driving change. It helps you understand shifting conditions around your company and confirm that your efforts are relevant and sustainable.
As a leader, you must not only effect change but understand why it’s needed. Taking an online course, such as Organizational Leadership , can enable you to gain that knowledge.
Using root cause analysis, you can identify the issues behind your organization’s problems, develop a plan to address them, and make impactful changes.
Are you preparing to transition to a new leadership role? Enroll in our online certificate course Organizational Leadership —one of our leadership and management courses —and learn how to perform an effective root cause analysis to ensure your company’s long-term success. To learn more about what it takes to be an effective leader, download our free leadership e-book .

About the Author
tableau.com is not available in your region.
1 st Reporting

Conducting A Root Cause Analysis: Incident To Final Report
Posted 3.02.21 by: Bond Seidel
Incidents can happen in the blink of an eye. And reporting these incidents helps to drive progressive change to a safer workplace. But what happens when the cause of an incident is unclear? A root cause analysis suddenly isn’t just appropriate. It’s crucial. And knowing how to conduct a root cause analysis is as important as knowing how to report the incident in the first place.
A Root Cause Analysis is conducted by following 6 steps, beginning with the incident report and ending with a comprehensive root cause analysis. Understanding each stage of the root cause analysis is vital for successful preventive action plans creation and implementation.
Root cause analysis, also known as RCA, is the investigation process following an incident. The incident may or may not have caused harm to a person or property. Incidents may not have occurred at all, but instead, someone reported a dangerous situation. Either way, a root cause analysis ought to find completion following any form of incident.
This article will discuss the steps necessary to conduct a root cause analysis to a successful end. Tracing the incident’s steps and following the reporting and root cause analysis process to the end, we will find many useful tips and tricks to help facilitate your company’s reporting processes. Let’s jump right into why we want to do a root cause analysis in the first place to get us going.
Table of Contents
Why Conduct A Root Cause Analysis If There Is An Incident Report?
It may seem duplicative, even counter-productive, to produce a root cause analysis report following a previously reported incident. And in a sense, it may be slightly repetitive, but this is no reason not to complete a root cause analysis.
The sole purpose of a root cause analysis is to determine all the factors that contributed to an incident’s occurrence. It is a proactive management tool used to serve the process of corrective action.
An incident report documents an incident. However, those who complete incident reports are often more involved in reactive management of an incident than proactive management of the event. It is merely the nature of the beast.
To perform a root cause analysis, step out of reactive and progress towards proactive incident solution management.
So, why conduct a root cause analysis? Couldn’t we take a different approach to the incident report? Sure, you could do it, but why complicate a situation where reactive management is vital in controlling further incident damage or injury? Often incidents require a certain amount of reactive action merely to contain a hazard, which is often best left to its own devices.
Maintaining a separate procedure for root cause analysis allows for a more focused approach to proactive incident management. It also evades the corruption of a reactive issue’s causal factors that may, in the heat of the moment, obscure the real root cause as to why an incident occurred in the first place.
6 Steps To Completing A Root Cause Analysis
Analyzing industry-specific responses to incidents, we find that a complete root cause analysis procedure is completed best with a predefined set of steps. Wikipedia decomposes the RCA into four steps:
- Identify and describe the event.
- Establish a timeline from ordinary events to the incident event.
- Distinguish between the root and causal factors.
- Establish a causal graph connecting the root cause and the event/problem.
We believe that taking things to a more generalized, less industry-specific approach, and yet in more depth and detail, is appropriate. Here’s our take on completing a root cause analysis in most industries; see below.
- The Incident Report Analysis
Determining Leading Events
Analyzing leading conditions, documenting further witness information, analyzing completed data collection.
- Determining Corrective Action
The Incident And Report Analysis
Beginning with identifying an incident, we analyze the incident to determine its characteristics. The incident often finds presentation via an incident report, but there are many possible sources of information for the incident. For example, the RCA may generate following a customer complaint, risk management referral, or even a complaint presented by HR. No matter the source generated by the RCA, you have to start identifying the problem or incident.
As many RCAs are generated following incident reports, let’s go a layer deeper into these reports. An incident report should include the following:
- Administrative details
- Incident information
- Witness accounts and observations
- Actions and recommendations
The information provided ought to include as much information as possible; however, if you perform a root cause analysis, the incident will have already been recorded in the report. Analyze the information provided and look for holes in the information. Try to find any omissions, which can sometimes be the case.
For more information on what to include in incident reports, please read our article: 12 Things To Include In An Incident Report (With 5 Tips) .
As you analyze the incident report, a story should start to form in your mind about how it occurred. Aside from acts of nature, most incidents have precursor events. It is the classic cause and effect scenario. And it would help if you determined said causes.
When an incident occurs, we can determine any events that could have avoided the incident itself if removed.
Although events that lead up to incidents are apparent contributing factors, sometimes conditions are the prerequisites for incidents. At this stage in the root cause analysis, you should examine the conditions that surrounded the incident. Careful analysis of available data might reveal clues to establish the root cause or causes further. The information may also help us sort out the root causes from the other causal factors.
In certain incident types, witness information may require you to conduct a follow-up investigation. When analyzing the incident report data, depending on the nature of the incident, information might even be omitted simply by the assumptions of those involved at the time. Hindsight is 20/20, as they say.
Further witness information may include more than mere statements of those who were present to perceive the incident. The information may come from other forms of witnesses, such as the electronic sort. Incidents are often recorded using video surveillance equipment. You can use this to review incidents, and if there are any available other sources of information, you should collect and review them.
The fifth stage of the root cause analysis is analyzing the completed sets of data. It would be best if you had determined your leading events, the conditions surrounding and leading up to the incident, as well as any witness information.
This stage of the root cause analysis requires looking at all of the data you have collected and reviewed. Determine the actual essential factors and events that led up to causing the incident. Separate the essential factors from those that are coincidental or only partially responsible.
The simple way to accomplish this stage is to ask yourself if you removed that factor, would the incident still have occurred? Would it have been better or worse with that element removed from the equation? If the factor removed means the incident would not have happened, it is an essential contributing factor.
Once all contributing factors are organized, determining the root cause or causes of the incident should come naturally. And this drives us to the inevitable conclusion: how could the incident have been avoided?
Determining Corrective Action – The Final Report
Take a look at the root cause or causes you’ve determined during the course of your analysis. How could these factors have been manipulated to avoid an incident?
Most incidents are preventable. Whether you’re in security, manufacturing, medical care, or any other field, most of the time, we can avoid or prevent hazards from becoming damaging or threatening situations.
Analyze how preventing the incident could have occurred and document any possible and plausible solutions. For best results, document all ideas and eliminate them based on safety and feasibility. Using a methodology to brainstorm possible corrective actions, sometimes we can create a solution that exceeds what standard actions will achieve.
Your final root cause analysis report needs to be concise, comprehensive, and provide solutions. Preventable actions and strategies are always more effective than reactive actions. And you might be able to save someone from injury or worse.
Measures To Follow Through After The Root Cause Analysis
At this point, you’ve completed your RCA if you have followed the steps. But have you followed through on the recommendations? Has anyone completed corrective and preventive actions? The RCA becomes entirely pointless if nothing is done about the incident after all.
During the course of the RCA process, you may be asking yourself what the best method to try to determine the root causes is. Sure, it’s easy to say you need to figure something out, but how should you go about it? Is brainstorming the best option? If not, what is it? Let’s find out.
Root Cause Analysis Methodologies
If root cause analysis were a topic of study, it would be the study of cause and effect, with a major in investigative reporting. But many companies and organizations use a visual charting process as an effective means of communicating the root cause analysis. It is one of several methodologies used in the root cause analysis process. Let’s take a quick look at a few of the most efficient root cause analysis methods.
- Why 5 Analysis
The concept behind the ‘Why 5 Analysis’ is to ask the question Why, five times. For example, one might ask why did this car crash. The answer might be because a left tire blew up. Then ask why that happened, answer and repeat. The concept is to ask the question multiple times to keep diving deeper towards the problem’s root.
Although this method is brilliant in its simplicity, it also happens to be its curse. Many have argued that this method simplifies situations that you should not simplify. The method may inadvertently miss individual branches of thought by misdirection.
During the “Why 5 Method”, if the second “why” results in an answer that starts to lead away from the actual root cause, the domino effect of such a consequence could potentially skew results.
Due to the potential for misleading discrepancies, the “Why 5” method is best used in parallel, multiple times for a single incident. One may also determine that branching in our question chain is not only possible but often quite or even more probable than the assertion that a singular cause is at fault.
- Pareto Analysis
The idea behind the Pareto analysis is the Pareto rule. That is to say that eighty percent of the effects come from twenty percent of the causes. Another way of looking at the Pareto analysis method is to equate the methodology to a looking glass.
A looking glass, or magnifying glass to use a more common name, will take a small area of view and enhance it by presenting the small view on a larger scale. The concept of the 80/20 rule is similar.
The Pareto analysis breaks data into percentages of observations and then is represented graphically. Concurrently, Pareto analysis represented graphically is likely best left to massive data collection types of root cause analysis. This form of analysis uses a statistical-based methodology to conclude. Therefore, it may only be relevant for specific RCA applications.
- Change Analysis
Change analysis methodology for root cause determination finds credibility in situations involving evolving events or conditions. For example, analyzing the change in roadway conditions over time may allow for determining a root cause when it pertains to a single-vehicle car accident. Or perhaps a facility records notes of equipment conditions over time, and the change of these conditions is analyzed. The idea is that the conditions or events that evolved are analyzed using this method of determining the root cause of an incident.
- Brainstorming
Our most basic and one of our most potent methods for root cause analysis is brainstorming. Because of its power, this method is the one method described in the six steps of conducting an RCA, as mentioned earlier.
The brainstorming method allows freedom of thought to attempt to determine the possible root causes of an incident. Using rough brainstorming followed by a sort of elimination period is one of humanity’s best abilities. It uses the best of our creativity and real-world experience. The downside is that brainstorming can sometimes end up being mono-directional, depending on the person’s mindset or persons involved in the brainstorming process.
Brainstorming Tip: When using the brainstorming method to determine the root cause of an incident, use a minimum of three people to help with brainstorming. This method works best when there are multiple perspectives to help come up with ideas. It also helps prevent mono-directionality.
Conclusions On Conducting Incident Report Based Root Cause Analysis
From the information you’ve read thus far, you must realize that the root cause analysis, as simple or complex a process as you make it out to be, has three primary goals.
- To discover the primary root cause or causes of a problem or incident.
- Next, t o fully comprehend the nature of the incident and how it can be fixed or prevented.
- To apply resolutions as a proactive management tool to prevent the repeat of the incident.
If these three goals find themselves met, then the root cause analysis may be considered a completed process.
Using an incident report as the basis for a root cause analysis is inherently wise from a safety process standpoint. Although, depending on the industry, it may find itself discarded. Take the medical industry, for example. Many hospitals are inundated daily with hundreds, even thousands of incident reports.
The truth is that as industry leaders, we each need to have a process that involves sorting incidents by the level of priority and thus obtaining a resolution to the flood of incidents. If the most severe face triage to a root cause analysis, there may be the hope of achieving a successful reporting system after all.
In most industries, the hope is that there are nowhere near the number of incident reports filed as there are in the healthcare industry. Most businesses shy away from adding further paperwork to their plates, and for a good reason. But, there is a solution to the paperwork dilemma regarding incident reporting and root cause analysis.
Using a digital solution like that offered by 1ST Incident Reporting is the solution to the seemingly never-ending paperwork. With digitally based incident reports, not only can you set up instant notifications, you can access reports previously completed with lightning speed. What better way to do a root cause analysis than have digital access to the incident report?
- Featured Photo by cottonbro from Pexels .
- https://en.wikipedia.org/wiki/Root_cause_analysis
- https://en.wikipedia.org/wiki/Five_whys
- https://www.mindtools.com/pages/article/newTED_01.htm
- https://www.tableau.com/learn/articles/root-cause-analysis
- https://www.cms.gov/medicare/provider-enrollment-and-certification/qapi/downloads/guidanceforrca.pdf

Start reporting today
Join the globally-recognized brands that trust 1st Reporting to safeguard their organizations.
Join the globally-recognized brands that trust 1st Reporting to safeguard their organizations!
Privacy Overview
Customize your template.
Work with our team of experts to customize our templates to your exact business needs.
- First Name *
- Last Name *
- Phone Number * ✓ Valid number ✕ Invalid number
- Changes Requested
- By submitting your information you agree to receive email marketing and promotional communications from 1st Incident Reporting
- Name This field is for validation purposes and should be left unchanged.
Free Template Download
- I would like to learn more about a digital solution to manage my reports
- Email This field is for validation purposes and should be left unchanged.
- 281.412.7766
- [email protected]
- Learner Dashboard
- GET YOUR CAUSE MAPPING TEMPLATE

- About Cause Mapping®
- What is Root Cause Analysis?
- Cause Mapping® Method
- Cause Mapping® FAQs
- Why ThinkReliability?
- Online Workshops
- On-Demand Training Catalog
- On-Demand Training Subscription
- Company Case Study
- Upcoming Webinars
- Webinar Archives
- Public Workshops
- Private Workshops
- Cause Mapping Certified Facilitator Program
- Our Services
- Facilitation, Consulting, and Coaching
- Root Cause Analysis Program Development
- Work Process Reliability™
- Cause Mapping® Template
- Root Cause Analysis Examples
- Video Library
- Articles and Downloads
- About ThinkReliability
- Client List
- Testimonials
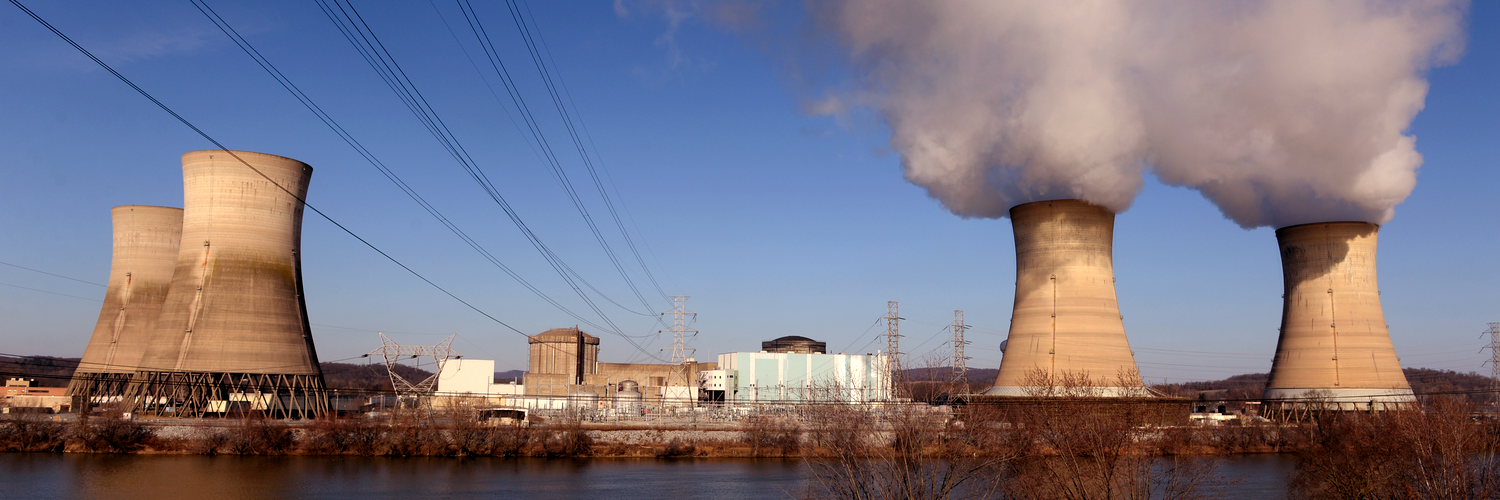
Case Study: Three Mile Island
Everyone seems to agree that root cause analysis is about solving problems, but there’s no agreement as to how a root cause analysis is done.
On March 28, 1979, there was a partial meltdown of the core in the number 2 reactor at Three Mile Island Nuclear Generating Station (TMI-2) near Harrisburg, Pennsylvania. This incident remains the worst accident in the history of U.S. commercial nuclear power. No one was injured and there was no significant release of nuclear radiation, but there was the real potential for a major disaster. The accident also stoked concerns about the safety of nuclear power and led to a drop in public support for nuclear power.
Getting to the root of the problem
Like nearly all accidents, a number of factors contributed to the accident at TMI-2. In order to understand what occurred at TM1-2, it is useful to know the basic plant design. TMI-2 had a closed primary loop where primary coolant was heated as it flowed through the reactor core and cooled as it transferred heat through the steam generator to the secondary loop. The heat that was transferred to the secondary loop was then used to turn a turbine connected to a generator to produce electricity.
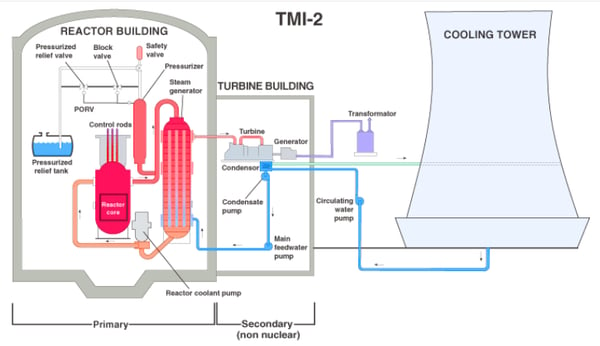
With something as complicated as the accident at TMI-2, it can help to have a simple method to organize the information. A Cause Map , an intuitive method for performing a root cause analysis , can be built to visually layout the cause-and-effect relationships of the causes that contributed to the accident. The first step in Cause Mapping it to define the problem by filling in an Outline which includes listing the impacts to the organizational goals. The Cause Map is built by starting at one of the impacted goals and asking “why” questions. Each answer to a “why” question is added as a box to the Cause Map. An example of a filled in Outline for TMI-2 is below.
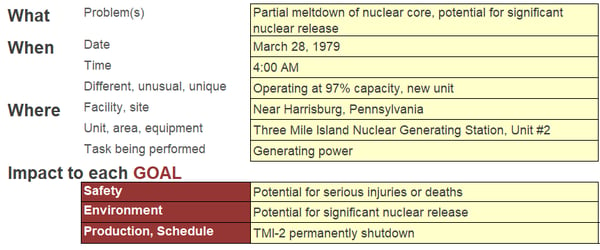
So WHY was there a potential for a significant nuclear release? There was a partial meltdown of the reactor core because the core was uncovered, meaning it didn’t have coolant on it to help transfer energy away from the core and it melted when the temperature increased significantly. The reactor was uncovered because a large volume of primary coolant was lost through a pressure relief valve. The Cause Map can continue to be expanded by asking “why” questions. To view a high-level Cause Map of this incident, click on the image below and download the PDF.
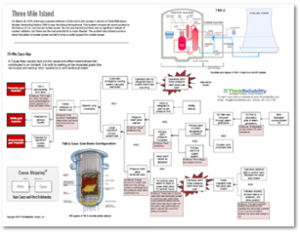
Stuck open relief valve
The accident began with failures in the secondary loop that resulted in a loss of feedwater to the secondary side of the steam generators, meaning that heat and pressure increased in the closed primary loop. The plant was designed to withstand a loss of feedwater, but an additional failure of a primary pressure relief valve magnified the problem.
The pressure relief valve (the safety valve labeled in the simplified system diagram above) was designed to open when the primary plant pressure increased above a set limit. The relief valve lifted as a result of the increased pressure after the loss of feedwater as intended, but it failed to reseat as designed after pressure decreased. The valve remained open as coolant continued to flow out of it until a manual block valve was closed to isolate it.
Operators unaware valve was open
As mentioned above, there was a block valve that could have been shut to stop the loss of coolant, but operators were unaware of the fact that the valve was stuck open. They did not take action to mitigate the situation until it was too late to prevent the partial meltdown of the core.
It is easy to see what was occurring in TMI-2 with the benefit of hindsight, but it wasn’t clear as the incident played out. The control room at the plant was huge and had hundreds of indications. When this incident occurred, operators received dozens of alarms, both audible and flashing lights, in a short period of time without any obvious priority.
In addition, operators had false indication that the pressure relief valve was closed. There was a light that operators assumed indicated valve position and it showed that the pressure relief valve was closed. The indication actually showed the status of the solenoid that operated the pressure relief valve and only indicated whether the solenoid was powered or not, not whether the valve was actually closed. The solenoid had operated as it was expected to close the valve, but the valve had failed to reseat so the light indicated that the pressure relief was closed when it was not. Operators had not been trained on the fact that the valve indicator only showed solenoid status nor where they could look for alternative confirmation that the valve was closed.
Alarms continued throughout the incident and the sheer volume of information made it difficult to interpret the situation accurately. Add in the indication that falsely led operators to believe the valve was closed and an extremely high stressful environment and it is much easier to understand why it took them so long to isolate the leaking pressure relief valve than it may have at first glance.
So what is “the” root cause?
Many people are tempted to say the stuck open relief valve was “THE” root cause of the Three Mile Island accident and it was certainly a major factor, but it doesn’t tell the whole story. Identifying a single “root cause” is generally not helpful and tends to limit the solutions that are considered. Building a Cause Map and identifying the system of causes (plural) that contributed to an incident helps investigators dig deeper and naturally widens the solutions that are considered. For example, it is not only important to understand that the relief valve was stuck open, but to also understand why it took so long for operators to identify that it was open. We likely wouldn’t be talking about this incident today if operators had a better understanding of the plant conditions as the accident occurred and were able to quickly take actions to mitigate the incident. In my opinion, the biggest lesson to be learned from Three Mile Island is that operators can only make decisions that are as good as the information and training they are given.
Additional root cause analysis resources:

Share This Post With A Friend

Similar Posts
Other resources.
- Root Cause Analysis blog
- Case studies
- Patient Safety blog
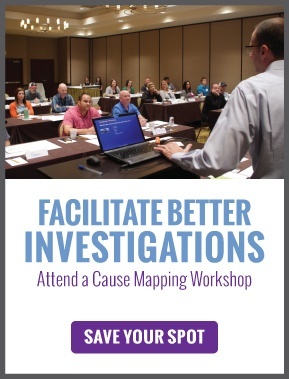
READ BY - - - - - - - - - -

Other Resources - - - - - - - - - -

Sign Up For Our eNewsletter
Case Studies
Sologic’s methodology, services and software are built on more than 20 years of field experience. explore the effectiveness of root cause analysis training and software across a variety of sectors via these real-life success stories. .

Download Root Cause Analysis Template Below
Excel | Word | PDF
This root cause analysis report template allows for a detailed examination of the event. Use it to record information on the incident’s background and contributing factors, actions taken to reduce future risk, findings related to the identified root cause, as well as other notable findings that aren’t directly related to the problem. It also allows you to record a description of the event itself, the timeline, the investigative team, and the methods used.
Simple Root Cause Analysis Template
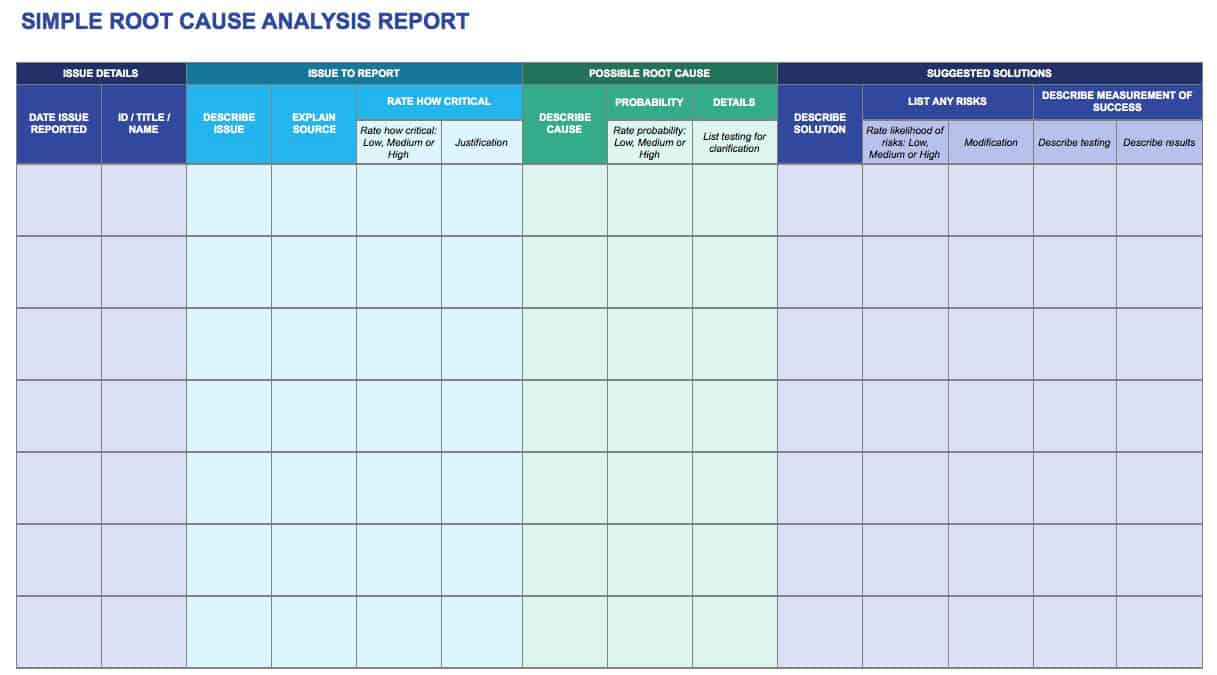
Download Simple Root Cause Analysis Template Below
Excel | PDF
This is a more stripped-down version of the root cause analysis template above. Use this template to examine simpler issues that don’t require detailed analysis. It allows you to record a short explanation of the issue or problem, list potential root causes and possible solutions, and report whether or not those solutions were successful.
Six Sigma DMAIC Methodology Root Cause Analysis Template
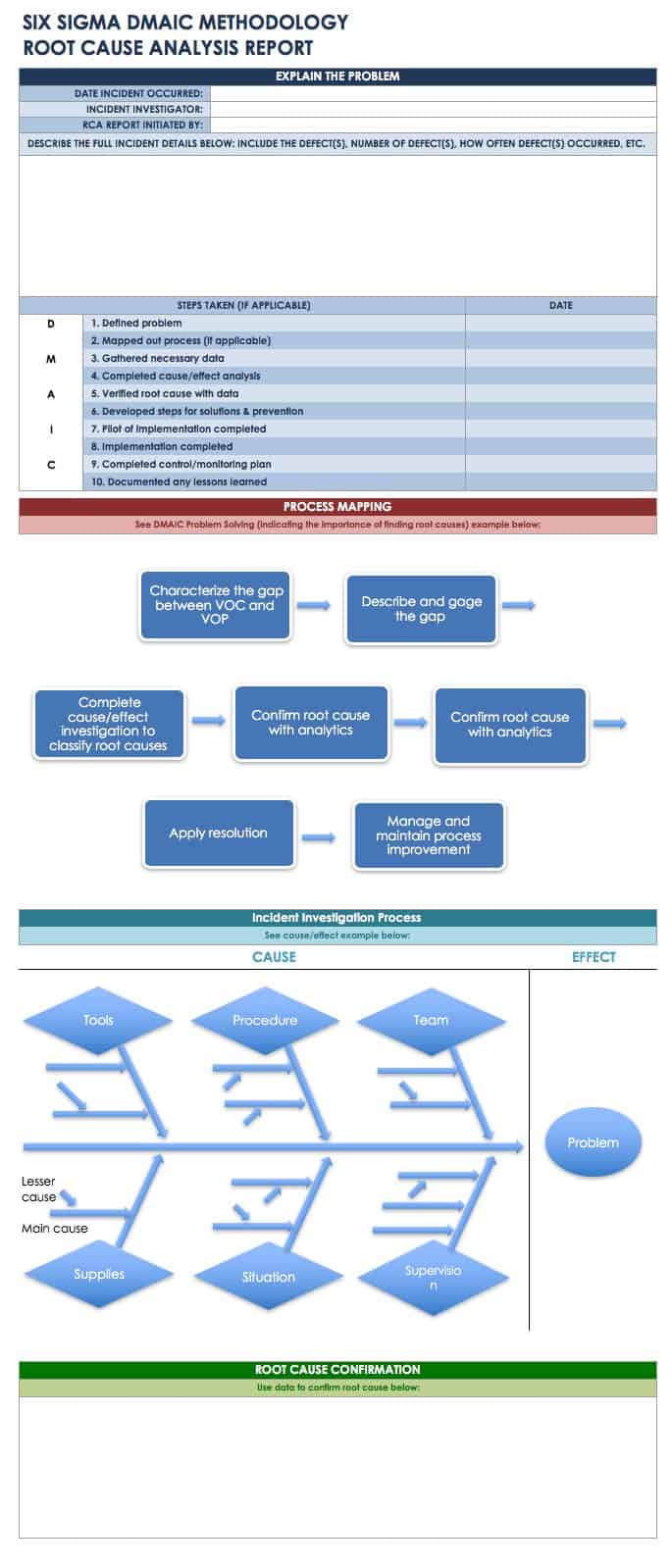
Download Six Sigma DMAIC Methodology Root Cause Analysis Template Below
Excel | Word | PDF
Six Sigma DMAIC is a methodology used to reduce errors and improve business processes. It prescribes its own approach to analyzing and investigating root causes. The “DMAIC” acronym refers to the steps involved in this process, which are similar to the steps described in the introduction:
- Define and Measure: What was expected to happen, and what was the problem that occurred instead? What happened, and when and where did it take place? What is the problem’s significance, and who was impacted?
- Analyze: What are the cause-and-effect relationships between the factors contributing to the problem? Why did the problem occur, and what must be done to keep it from recurring?
- Implement and Control: What are potential solutions to the problem, and what are the causes and benefits of implementing them? How can solutions be monitored and controlled so the problem doesn’t occur again?
This root cause analysis template walks you through each of the steps above, and allows you to enter information about the root cause action plan, resolution, and investigative team. What’s more, this root cause template includes diagrams that can be used to visualize how different contributing factors (e.g., people, processes, and equipment) relate to one another, as well as to the problem itself.
‘5 Whys’ Root Cause Analysis Template
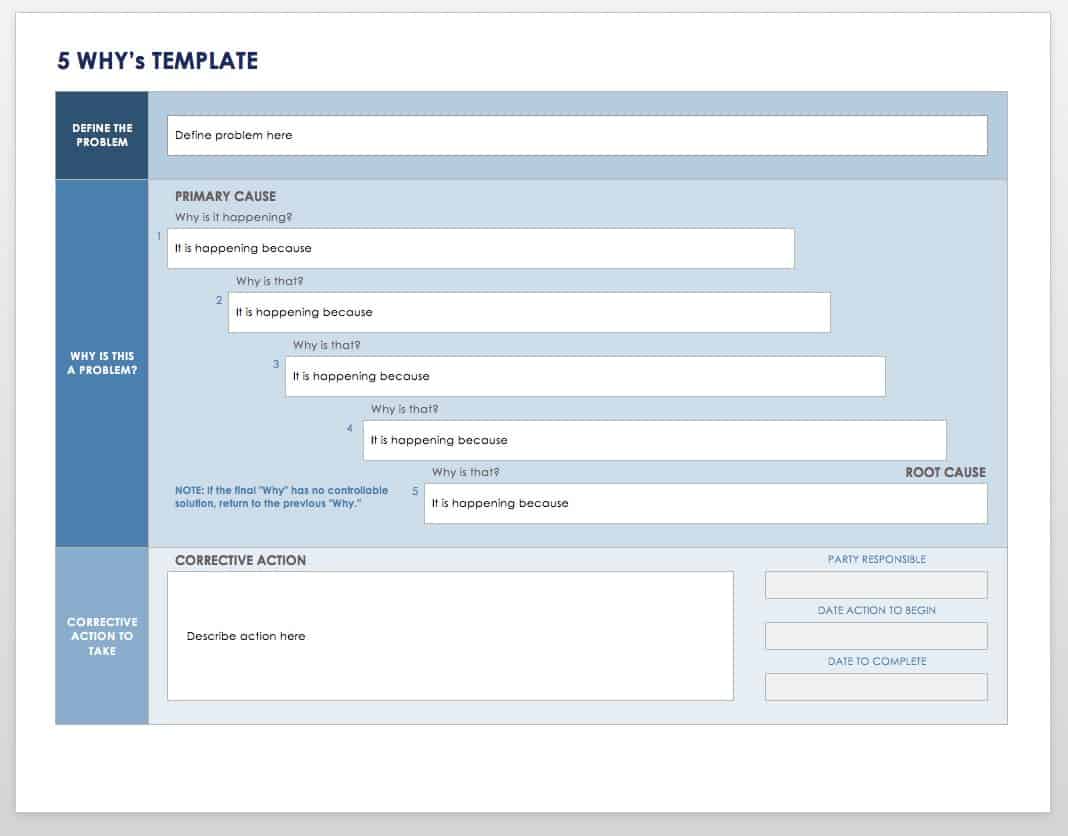
Download ‘5 Whys’ Root Cause Analysis Template Below
Excel | Word | PDF | Smartsheet
A 5 Why root cause analysis template is used to conduct a particular type of root cause investigation. When examining a problem or accident, “why” questions frequently arise (e.g., Why didn’t we address this issue sooner?). The “5 Why” process involves asking a series of these questions—first asking why the incident occurred, then asking why those sub-causes occurred, until the root cause of the issue is eventually uncovered. This template provides a framework for asking “why” questions and determining the root cause. You can also note corrective actions that will be taken to prevent the problem from recurring.
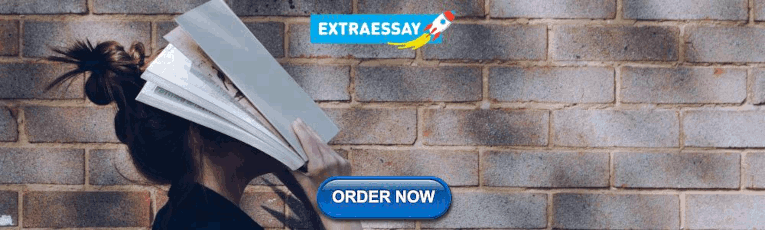
Cause Mapping Template
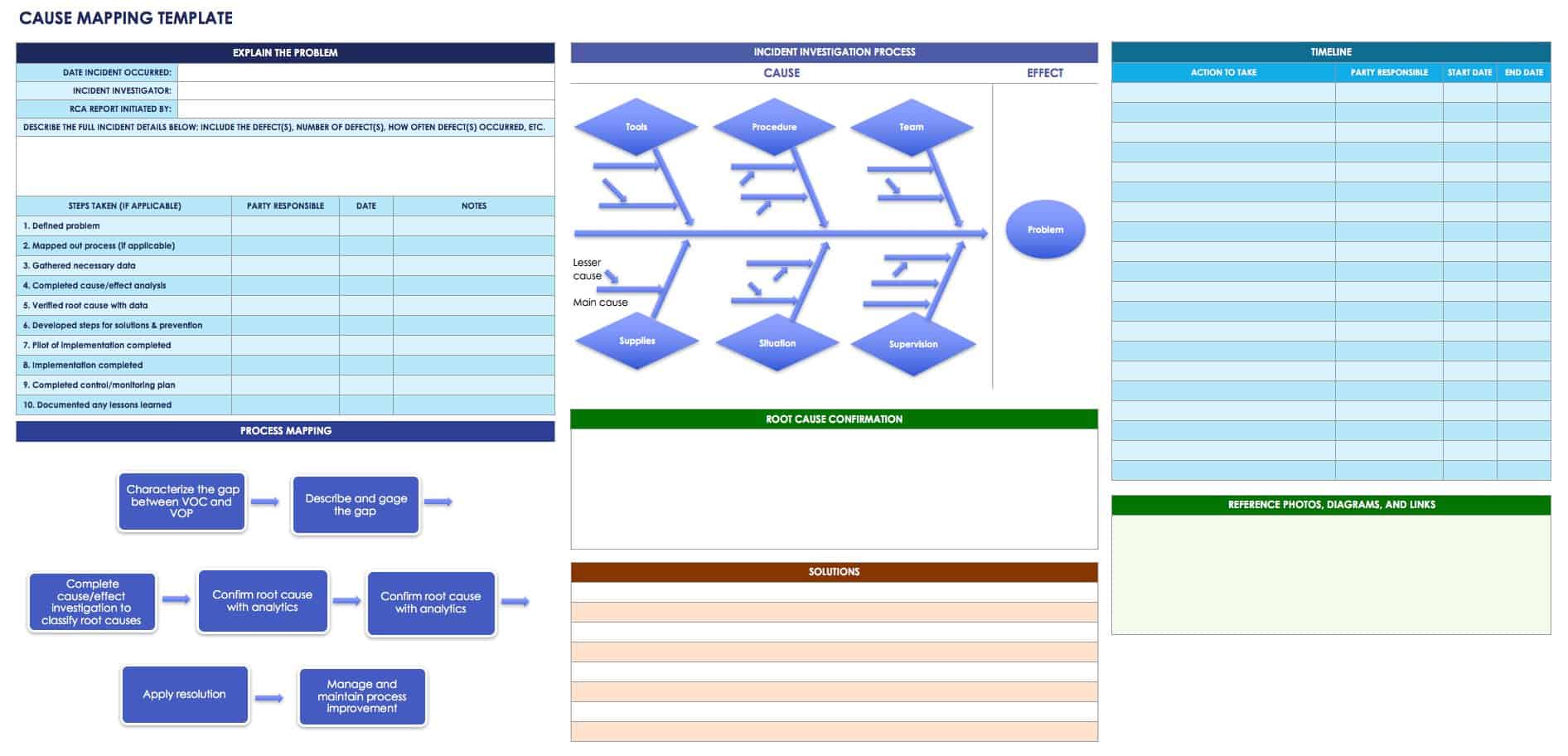
Download Cause Mapping Template Below
Excel | PDF
This cause mapping template combines elements of the root cause analysis template, the Six Sigma DMAIC template, and the 5 Whys root cause analysis template. It includes a detailed problem outline, a timeline, a “why” question analysis, diagrams to help illustrate the process, sections for proposing and evaluating possible solutions, and a section for creating an action plan.
Healthcare Cause Mapping Template
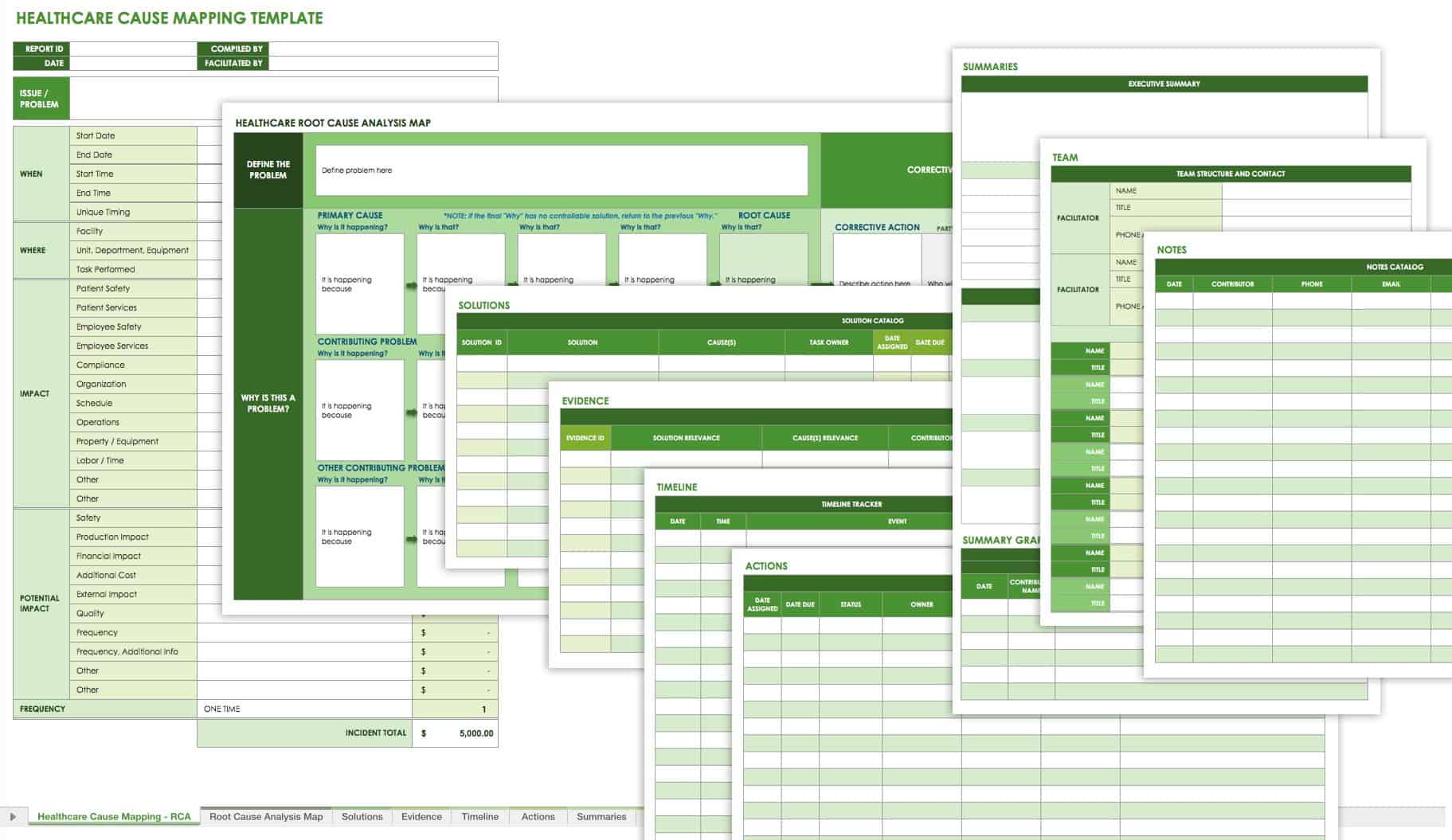
Download Healthcare Cause Mapping Template Below
This type of root cause template is formatted the same way as the generic cause mapping template, but is specifically tailored for healthcare organizations. Like the above template, it offers a “why” analysis and supplementary diagrams in addition to the standard elements. However, it also helps you examine how patient safety and services goals have been impacted by your analysis of the problem.
Root Cause Analysis Report Example: Explosion at Acme Chemical Company
Download Root Cause Analysis Report Example: Explosion at Acme Chemical Company
When filling out your own template, use this completed report as an example. This sample root cause analysis examines an explosion at Acme Chemical Company. It describes the incident background, contributing factors, who was involved, what root cause was identified, the risk reduction actions taken, prevention strategies, and incidental findings. Refer to this sample if you need guidance when completing your own root cause analysis.
What’s Included in a Root Cause Analysis
A root cause analysis template, also known as a root cause corrective action template, typically contains the following information:
Event description: The problem or accident being investigated is described in as much detail as possible. This includes the date and time of the event, what happened, who uncovered the problem, and who was impacted by the problem (as well as how they were affected).
- Timeline: This section includes a thorough description of all events before, during, and after the problem or accident occurred. This can help uncover potential underlying causes of the incident. Dates, times, and names of all parties involved are included here.
- Investigative Team/Method: This section identifies the team that will be responsible for investigating the problem, what methods they will use for collecting and analyzing data, and how their findings will be reported.
- Findings/Root Cause: The investigative team reports their findings and describes the root cause they have identified.
- Corrective Action: The action(s) that must be taken to correct the problem—and ensure it doesn’t happen again—are written here. These actions can result in project scope, schedule, and budget changes.
Discover a Better Way to Manage Finance Operations
Empower your people to go above and beyond with a flexible platform designed to match the needs of your team — and adapt as those needs change.
The Smartsheet platform makes it easy to plan, capture, manage, and report on work from anywhere, helping your team be more effective and get more done. Report on key metrics and get real-time visibility into work as it happens with roll-up reports, dashboards, and automated workflows built to keep your team connected and informed.
When teams have clarity into the work getting done, there’s no telling how much more they can accomplish in the same amount of time. Try Smartsheet for free, today.
Discover why over 90% of Fortune 100 companies trust Smartsheet to get work done.

An official website of the United States government
The .gov means it’s official. Federal government websites often end in .gov or .mil. Before sharing sensitive information, make sure you’re on a federal government site.
The site is secure. The https:// ensures that you are connecting to the official website and that any information you provide is encrypted and transmitted securely.
- Publications
- Account settings
Preview improvements coming to the PMC website in October 2024. Learn More or Try it out now .
- Advanced Search
- Journal List
- Med Princ Pract
- v.29(6); 2020 Dec

How Much of Root Cause Analysis Translates into Improved Patient Safety: A Systematic Review
Jimmy martin-delgado.
a Atenea Investigation Group, Fundación para el Fomento de la Investigación Sanitario y Biomédica de la Comunidad Valenciana (FISABIO), Valencia, Spain
Alba Martínez-García
b Department of Health Psychology, Universidad Miguel Hernández, Alicante, Spain
Jesús María Aranaz
c Preventive Medicine Service, Hospital Ramon y Cajal, Madrid, Spain
José L. Valencia-Martín
José joaquín mira.
d Alicante-Sant Joan d'Alacant Health District, Alicante, Spain
The aim of this systematic review was to consolidate studies to determine whether root cause analysis (RCA) is an adequate method to decrease recurrence of avoidable adverse events (AAEs).
A systematic search of databases from creation until December 2018 was performed using PubMed, Scopus and EMBASE. We included articles published in scientific journals describing the practical usefulness in and impact of RCA on the reduction of AAEs and whether professionals consider it feasible. The Mixed Methods Appraisal Tool was used to assess the quality of studies.
Twenty-one articles met the inclusion criteria. Samples included in these studies ranged from 20 to 1,707 analyses of RCAs, AAEs, recommendations, audits or interviews with professionals. The most common setting was hospitals (86%; n = 18), and the type of incident most analysed was AAEs, in 71% ( n = 15) of the cases; 47% ( n = 10) of the studies stated that the main weakness of RCA is its recommendations. The most common causes involved in the occurrence of AEs were communication problems among professionals, human error and faults in the organisation of the health care process. Despite the widespread implementation of RCA in the past decades, only 2 studies could to some extent establish an improvement in patient safety due to RCAs.
Conclusions
RCA is a useful tool for the identification of the remote and immediate causes of safety incidents, but not for implementing effective measures to prevent their recurrence.
Significance of the Study
- Root cause analysis is a widespread technique used in the last two decades to investigate latent causes of adverse events.
- Lack of expertise and time and a weak legal framework are some of the difficulties in fulfilling action plans from root cause analysis.
- It is not clear if root cause analysis is effective in preventing the recurrence of adverse events.
Introduction
Root cause analysis (RCA) emerged in the health care field almost 20 years ago. This technique is used worldwide to understand the remote and direct factors favouring the occurrence of an avoidable adverse event (AAE) [ 1 ], and improvement of patient safety [ 2 ].
Three studies have analysed the utility and limitations of this technique [ 3 , 4 , 5 ], all agreeing that barriers to implementing RCA correctly remain, and most of these were focused on active errors and not latent causes. The published results invite us to reflect on whether the impact of this technique in practice is proving to be all that is theoretically expected, first, because substantial resources and human talent are required [ 5 ], and, second, because many of the recommendations made in the framework of this technique are not applied failing to prevent the same incidents from recurring [ 6 ].
It is one thing to perform a multidisciplinary and multicausal analysis of why an incident occurred, and another, totally different thing to ensure that the proposals derived from this analysis to avoid the recurrence of safety incidents are implemented successfully. The usefulness of RCA may depend on the safety culture of health institutions, decision-making procedures and middle management leadership styles. The objective of this study was to assess the usefulness (i.e., its capacity to improve patient safety) of RCA in health care practice in order to avoid recurrence of AAEs.
We conducted a systematic review of studies published in scientific journals from database creation until December 2018 on the practical usefulness of RCA in the reduction of recurrent AAEs.
Eligibility Criteria
Only studies that analysed the efficacy of RCAs in the improvement of patient safety and studies that analysed the views of professionals on its feasibility were included. This study was designed to address whether the results of RCA improve patient safety, whether the RCA methodology has been fully carried out, and whether health professionals consider it feasible.
The MOOSE protocol was followed. Studies published in scientific journals were included to describe the AEs commonly analysed and the practical usefulness of RCA in the reduction of AAEs or its limitations in improving patient safety. No exclusions were made based on the year of publication, the design of the study, or language. Both quantitative and qualitative studies were included. Research taking a descriptive approach was also included.
Search Strategy
The review of published studies was carried out on MEDLINE, Scopus and EMBASE. The search strategies were defined based on the combination of keywords related to RCA ((“root cause analysis”[MeSH Terms] OR (“root”[All Fields] AND “cause”[All Fields] AND “analysis”[All Fields]) OR “root cause analysis”[All Fields]) AND (“delivery of health care”[MeSH Terms] OR (“delivery”[All Fields] AND “health”[All Fields] AND “care”[All Fields]) OR “delivery of health care”[All Fields])) AND (“patient safety”[MeSH Terms] OR (“patient”[All Fields] AND “safety”[All Fields]) OR “patient safety”[All Fields]), and using the Boolean operators “AND” and “OR.”
In a complementary manner, we conducted manual searches in Google Scholar for the identification of grey literature using the same search equation. We also carried out a manual search based on the bibliographic references of the selected publications.
Data Extraction
J.M.-D. and A.M.-G. independently reviewed all potentially relevant studies. When no consensus was achieved between them, a third researcher (J.J.M.) reviewed the study to reach a consensus. All reviewers were capable of understanding Spanish, English and French, and studies were included in local languages if they included an English abstract, which allowed the authors to decide whether they had to be included for full text reading. No unpublished studies were found, nor was there a need to contact any of the authors of the studies included. Data extracted from each study included country, review committee, inclusion of managers, inclusion of personnel involved, design, database used, employee review method, sample (RCA number, recommendations, audits or interviews conducted), the type of event analysed and the main findings. In addition, where possible, information was extracted on the applicability of the RCAs and the interest of health professionals in the RCA.
Data Synthesis
For each of the above variables, categories of possible options were generated and the presence or absence of information in each variable was coded. Heterogeneity in the methods and measures applied was described when possible. Numbers of participants and AEs were also included. AAEs were classified as sentinel where applicable.
Quality Evaluation
For the assessment of quality of the included studies, J.M.-D. and A.M.-G. used the Mixed Methods Appraisal Tool (MMAT) [ 7 ]. The results led to an overall score for methodological quality, varying from 40–60% (moderate quality) and 80% (considerable quality) to 100% (high quality). None of the studies were excluded based on the quality assessment.
A total of 169 studies were identified, of which 127 remained after exclusion of duplicates. Seventy-seven were excluded as these studies did not include results concerning the effectiveness of RCA in decreasing the number of AAEs. Finally, 21 papers meeting all inclusion criteria were included (Fig. (Fig.1 1 ).

Study selection flow diagram. RCA, root cause analysis.
The samples of the studies show a high variability, from 20 to 1,707 subjects with analysed data (RCA number, recommendations, audits or interviews conducted). The studies were mainly conducted in North America (52%; n = 11), Australia (19%; n = 4) and Europe (14%; n = 3); 57% were quantitative studies (6 longitudinal and 6 cross-sectional), 1 study was a randomised controlled trial, and the rest were qualitative analyses. The most common setting was hospitals (86%; n = 18). The type of incident most analysed was AAEs, in 71% ( n = 15) of the studies, where sentinel events represented 13% ( n = 2) of the AEs, and serious AEs classified as Severity Assessment Code 1 (for Queensland Health) or 3 (for the Department of Veterans Affairs) accounted for 20% ( n = 3), while for the remaining 10 studies, information about severity was not disclosed. Incidents related to safety made up 5% ( n = 1), and in the rest of the included studies, interviews or mock-ups were implemented.
In only 5 studies (24%) were managers or coordinators included, and in only 1 study were personnel from the service taken into consideration. Independent hospital databases and national or regional databases were mostly used, each accounting for 29% of the studies. Although the Veterans Affairs National Center for Patient Safety database was used in 5 of the studies (24%), they also examined individuals. For the rest of the cases, databases were not used.
Of the 21 articles, 9 were rated as having a moderate quality (MMAT 40–60%), 5 were rated as having a considerable quality (MMAT 80%), and 7 were rated as high quality (MMAT 100%). The key features of each study are presented in Table Table1 1 [ 3 , 4 , 5 , 6 , 8 , 9 , 10 , 11 , 12 , 13 , 14 , 15 , 16 , 17 , 18 , 19 , 20 , 21 , 22 , 23 , 24 ].
Main findings and features of the studies reviewed
RCA, root cause analysis, MMAT, Mixed Methods Appraisal Tool; NCPS, National Center for Patient Safety.
Utility of RCA
Only in 2 studies (9%) could it be established that RCAs contributed to the improvement of patient care to some extent. In these studies, only 54 RCAs were reviewed. In 3 other studies (15%), the authors did not conclude that their implementation contributed to the improvement of patient safety, and in 10 (50%) of them, the recommendations made were weak, which did not lead to a reduction of AEs.
Some studies warned that sometimes poorly designed action plans and measures may generate new risks and may be insufficient to prevent the occurrence of new events [ 5 , 6 , 10 , 16 ]. In the study carried out by Hibbert et al. [ 4 ], in which the effectiveness and sustainability of the proposals arising from 227 RCAs were analysed, it was found that 72% of the recommendations categorised as relevant were not formulated and that the most common recommendations did not refer to latent causes in clinical practices but to active errors. Likewise, other studies [ 3 , 6 ] stated that most of the proposed recommendations focused on active errors and neglected latent causes, which provides short-term solutions but only partially helps to avoid future incidents. However, 1 study (5%) did demonstrate the usefulness of RCA and its recommendations [ 20 ].
Three studies (15%) showed that the RCA method was not applied properly [ 3 , 5 , 25 ]. François et al. [ 5 ] stated that only 23% of the 98 events selected for in-depth analysis covered all the domains defined by the method. Singh [ 3 ] pointed out that 65% of the RCAs carried out were not properly completed. In 5 studies (25%), the involvement of the professionals in the realisation of the RCA was analysed. While these appear to suggest a consensus that the relevance of RCA to establishing improved procedures caused it to be perceived as a beneficial analytical instrument, the researchers concluded that professionals encounter difficulties in conducting RCAs [ 8 , 14 ].
The literature collected analysed the usefulness of RCA as a process that allows the determination of factors that contribute to the occurrence of AAEs. Most of these were caused by communication problems among professionals [ 3 , 13 , 14 , 19 ], human error [ 9 ] and, finally, faults in the organisation of the health care process [ 3 , 22 ].
Weaknesses in Using RCA
Despite the fact that for professionals, RCA is a tool that allows improvements to the safety culture through the prevention of future AAEs [ 3 , 5 ], studies have identified the main weaknesses diminishing the usefulness of RCA in the framework of patient safety [ 5 ]. RCA is an extensive process that requires proper qualifications and attitudes. Studies have shown that the RCA method is often not properly applied, which directly affects the rigor and depth of the analysis of this tool [ 3 , 5 , 25 ]. The most common difficulties are a lack of time and resources of the work teams. Although none of the studies reviewed refers to how much time is needed to perform an RCA, in the study conducted by McGraw and Drennan [ 26 ], the results of an RCA investigation of pressure ulcers showed that a nurse can take up to 20 h to complete it. These factors directly affect the RCA process, hindering its complete execution [ 5 ].
Lack of time does not seem to be the only element that hinders the performance of RCAs; describing the events from a perspective different from individual error is challenging to professionals, who are sometimes reluctant to participate because of the distrust generated by possible future consequences. The belief that there is a culture focused on searching “those responsible” − in addition to creating tension in the work environment that may cause interprofessional problems [ 5 , 18 ] − is one of the main reasons for professionals refusing to participate in incident reporting systems [ 27 ].
Impact on Reducing AAEs
None of the studies reviewed assessed the ability of this process to reduce future AAEs. Moreover, in the study by Lee et al. [ 23 ], difficulties were found in determining whether the improvement actions implemented after the RCA were able to reduce the occurrence of AAEs, as the action plans did not follow a pattern of controlled implantation. On the other hand, Morse and Pollack [ 24 ] and Sauer and Hepler [ 22 ] were the only ones that found sufficient follow-up time, which allowed the determination of whether the recommendations agreed on in the RCA reduced the occurrence of AAEs to some degree. In order to increase the commitment and interest of health professionals in carrying out RCA, some studies have evaluated the usefulness of a mock RCA as prior training to provide medical staff with basic knowledge about patient safety and the methodology of this tool. The results showed that its use raised their confidence in being able to perform RCA and decreased their anxiety in the face of a possible AE [ 10 , 18 ]. This is supported by Boussat et al. [ 28 ], who found that professionals who were involved in Experience Feedback Committees had better scores on the Hospital Survey on Patient Safety Culture, especially in non-punitive response to error, communication and organisational learning dimensions.
Improvements in Introducing Changes
The studies reviewed show that managers and the personnel involved in AAEs had a low participation in the committees in charge of carrying out RCA. Peerally et al. [ 25 ] pointed out the need to professionalise the investigation of incidents by involving experts, as well as patients and family members, who can provide a unique perspective on the care received. Including those professionals who have been directly involved in the event also seems to have positive consequences, as it can contribute to the recovery of second victims by making them part of the solution [ 29 ]. Despite the progress and improvement in quality of care, the involvement of report systems such as RCA, especially the implementation of measures adopted, does not seem to be successful. Most of the included countries have so-called apology laws (39 states of the USA have Medical Professional Apologies Statutes; e.g., the Maryland Courts and Judicial Proceedings Code Ann. §10-92041), which aim to improve the relationship with the patient and their families, allowing them to provide information that improves the quality of care [ 27 ]. However, the presence of the professionals involved in an AE in RCA committees was mentioned in only 1 study [ 6 ], and in none of the cases were relatives present.
Although AEs are sometimes inevitable and part of the uncertainty of medical practice, the ultimate goal of the RCA is to help to produce solutions and apply necessary measures to ensure they do not happen again, that there is a lower probability of their occurrence, or that if they occur the possible consequences are mitigated. Although some studies have demonstrated the usefulness of RCA and its recommendations [ 24 ], most published studies found that just over half of the recommendations that resulted from RCA were not useful enough to prevent the same incidents from recurring in the future [ 6 , 14 , 25 ]. For this reason, researchers have proposed RCA-based tools that seek greater involvement of frontline professionals in the implementation of proposals to prevent the recurrence of serious AEs [ 30 ]. The non-existence of a formalised system that allows these recommendations to be addressed in a specific period of time, as well as the limited power of RCA committees to ensure compliance with these improvement actions [ 17 ], hinders implementing the proposed actions. It must be borne in mind that, normally, the people who will have to assume the responsibility of approving the measures suggested by the RCAs and the professionals who must implement these measures are usually not those who participated directly in the RCA. This makes it difficult for the proposals to be carried out.
It seems, therefore, that RCA is a process with considerable validity through which much may be learned about incidents [ 12 , 15 ]. However, it does not seem to produce enough benefits to address and resolve the problem [ 23 , 25 ] and, thus, to avoid possible AAEs. As explained by Najafpour et al. [ 13 ], RCA is a reactive method for investigating an event and finding its underlying factors. This method could provide answers to questions related to what happened, and how and why it happened, and should be used to design preventive interventions. It should be performed using an outlined framework process of investigation and analysis of clinical incidents performed by professionals with experience in patient safety and should include at least one manager and one of the personnel involved in it.
Limitations
Some of the limitations encountered are that most of the published data related to RCAs pertain to analysing the method of determining whether RCA is being implemented. Only reported results and quotations were assessed. Finally, little of the scarce evidence available regarding the impact − which was our objective − of carrying out RCAs can actually contribute to reducing the recurrence of the same incident, which may be due to the limited decision-making power of committees or to the proposed plan of action not being followed up in time.
Although early studies suggested that RCAs are effective in promoting ideas for preventing recurrence, more recent studies do not confirm these findings. A common gap that limits the effectiveness of this tool lies in the fact that RCAs are not usually accompanied by subsequent control of whether the devised improvement plan is carried out. Further research should focus on how to translate the results of ACR recommendations into practice to prevent recurrence of AAEs.
Statement of Ethics
For this systematic review, the MOOSE protocol was followed.
Conflict of Interest Statement
The authors have no conflicts of interest to declare.
Funding Sources
This research was funded by the PROMETEO Research Program, Consellería de Educación, Investigación, Cultura y Deporte, Generalitat Valenciana (Prometeu173).
Author Contributions
The conception and design were made by J.J.M.; the data were collected by A.M.-G. and J.M.-D.; the article was supervised by J.J.M.; all the authors contributed to writing, revising and approving the final draft.
Advertisement
Integration of Lean Six Sigma with Internet of Things (IoT) for productivity improvement: a case study of contactor manufacturing industry
- CASE STUDIES
- Published: 04 July 2023
- Volume 14 , pages 1990–2018, ( 2023 )
Cite this article
- Santosh B. Rane 1 ,
- Sandesh Wavhal 1 &
- Prathamesh R. Potdar ORCID: orcid.org/0000-0001-8896-5322 2
527 Accesses
2 Citations
Explore all metrics
In today's era of digitalization and competitive market environment, organizations are more focused on manufacturing quality products at optimum cost to capture maximum business as a variety of options are available to customers for purchasing goods and services. In this scenario, the latest technologies-based productivity improvement can help organizations to achieve set targets of production and ensure the quality of products. In this study, the contactor manufacturing industry has been considered to demonstrate integrated Lean Six Sigma with the Internet of Things (IoT) approach for productivity improvement. A systematic literature survey was performed to understand the concept of Lean Six Sigma (LSS), Define Measure Analysis Improve Control approach and IoT technology. The implementation of the LSS approach reduced the rejection rate of contactors and saved the total production cost (Rs. 51,88,260/-) annually. The annual consumption of grinding wheels has been reduced by 8 quantities to produce the same quantity of contactors. The surface quality of magnets has been identified as a root cause for contactor rejections as it contributes 53.4% of total rejections. The improvement measures are recommended based on the expert's suggestions as grinding wheel dressing must be performed after the completion of a batch of 20,000 parts. The condition monitoring and IoT approach implementation are done by monitoring grinding speed (650–950 RPM), grinding wheel thickness reduction by 0.4–0.6 mm after dressing and dressing of grinding wheel after completion of 20,000 for reducing rejections. This study concluded that industries should implement the Lean Six Sigma approach with the latest technologies and appropriate tools at each stage to set processes to world-class standards and industries should identify opportunities for process and product improvement.
This is a preview of subscription content, log in via an institution to check access.
Access this article
Price includes VAT (Russian Federation)
Instant access to the full article PDF.
Rent this article via DeepDyve
Institutional subscriptions
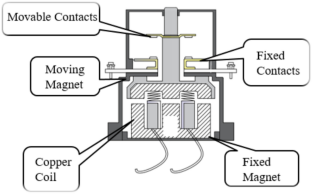
Similar content being viewed by others
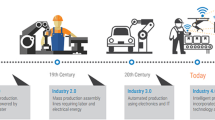
Literature review of Industry 4.0 and related technologies
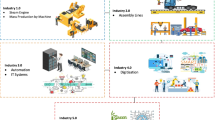
Future of industry 5.0 in society: human-centric solutions, challenges and prospective research areas
Six-sigma application in tire-manufacturing company: a case study.
Abrol SA, Bhargava C, Sharma PK (2021) Reliability analysis and condition monitoring of polymer based dye sensitized solar cell: a DOE approach. Mater Res Express 8:045309. https://doi.org/10.1088/2053-1591/abf629
Article Google Scholar
Alaba FA, Othman M, Hashem IAT, Alotaibi F (2017) Internet of Things security: a survey. J Netw Comput Appl 88:10–28. https://doi.org/10.1016/j.jnca.2017.04.002
Ali SM, Hossen MdA, Mahtab Z, Kabir G, Paul SK, ulAdnan ZH (2020) Barriers to Lean Six Sigma implementation in the supply chain: An ISM model. Comput Ind Eng 149:106843. https://doi.org/10.1016/j.cie.2020.106843
Alimohammadlou M, Mohammadi S (2016) Evaluating the productivity using malmquist index based on double frontiers data. Proced Soc Behav Sci 230:58–66. https://doi.org/10.1016/j.sbspro.2016.09.008
Antony J (2012) A SWOT analysis on six sigma: some perspectives from leading academics and practitioners. Int J Product Perform Manag 61:691–698. https://doi.org/10.1108/17410401211249229
Arias Velásquez RM (2020) Root cause analysis for inverters in solar photo-voltaic plants. Eng Fail Anal 118:104856. https://doi.org/10.1016/j.engfailanal.2020.104856
Arias Velásquez RM, Mejía Lara JV (2020) Root cause analysis improved with machine learning for failure analysis in power transformers. Eng Fail Anal 115:104684. https://doi.org/10.1016/j.engfailanal.2020.104684
Arias Velásquez RM, Mejía Lara JV (2020) Root cause analysis methodology for circuit breaker associated to GIS. Eng Fail Anal 115:104680. https://doi.org/10.1016/j.engfailanal.2020.104680
Bahari Z, Elgadi M, Rivet J, Dugué J (2009) Experimental study of the ternary Ag–Cu–In phase diagram. J Alloy Compd 477:152–165. https://doi.org/10.1016/j.jallcom.2008.10.030
Barot RS, Patel J, Sharma B, Rathod B, Solanki H, Patel Y (2020) Lean Six Sigma feasibility and implementation aspect in cast iron foundry. Mater Today Proc 28:1084–1091. https://doi.org/10.1016/j.matpr.2020.01.087
Belhadi A, Kamble SS, Zkik K, Cherrafi A, Touriki FE (2020) The integrated effect of big data analytics, Lean Six Sigma and green manufacturing on the environmental performance of manufacturing companies: the case of North Africa. J Clean Prod 252:119903. https://doi.org/10.1016/j.jclepro.2019.119903
Bidikar SG, Rane SB, Potdar PR (2022) Product development using design for six sigma approach: case study in switchgear industry. Int J Syst Assur Eng Manag 13:203–230. https://doi.org/10.1007/s13198-021-01199-4
Boutora S, Bentarzi H (2019) Ferroresonance study using false trip root cause analysis. Energy Proced Emerg Renew Energy Gener Autom 162:306–314. https://doi.org/10.1016/j.egypro.2019.04.032
Broder JS, Al-Jarani B, Lanan B, Brooks K (2020) Pigtail catheter insertion error: root cause analysis and recommendations for patient safety. J Emerg Med 58:464–472. https://doi.org/10.1016/j.jemermed.2019.10.003
Caro Teller JM, Pablos Bravo S, Serrano Garrote O, Ojeda García C, Carro Ruiz AM, Guede González AM, Ferrari Piquero JM (2020) Implementación Lean Six Sigma en la mejora del circuito de dispensación de medicación. J Healthc Qual Res 35:364–371. https://doi.org/10.1016/j.jhqr.2020.04.005
Chang DS, Kuo YC, Chen TY (2008) Productivity measurement of the manufacturing process for outsourcing decisions: the case of a Taiwanese printed circuit board manufacturer. Int J Prod Res 46:6981–6995. https://doi.org/10.1080/00207540701429934
Chaudhari SS, Bhole KS, Rane S (2023a) Comparison on conventional and digital technology assisted design methodologies of process heater radiant section. Int J Interact Des Manuf. https://doi.org/10.1007/s12008-023-01201-2
Chaudhari SS, Bhole KS, Rane S (2023b) An application of IIoT framework in system design, performance monitoring and control for industrial process heater. Int J Interact Des Manuf. https://doi.org/10.1007/s12008-023-01235-6
Cheah CK, Prakash J, Ong KS (2020) Overall equipment effectiveness: a review and development of an integrated improvement framework. IJPQM 30:46–71. https://doi.org/10.1504/IJPQM.2020.107240
Chi C-F, Sigmund D, Astardi MO (2020) Classification scheme for root cause and failure modes and effects analysis (FMEA) of passenger vehicle recalls. Reliab Eng Syst Saf 200:106929. https://doi.org/10.1016/j.ress.2020.106929
Costa LBM, Godinho Filho M, Fredendall LD, Gómez Paredes FJ (2018) Lean, six sigma and Lean Six Sigma in the food industry: a systematic literature review. Trends Food Sci Technol 82:122–133. https://doi.org/10.1016/j.tifs.2018.10.002
Costa LBM, Godinho Filho M, Fredendall LD, Ganga GMD (2020) The effect of Lean Six Sigma practices on food industry performance: Implications of the Sector’s experience and typical characteristics. Food Control 112:107110. https://doi.org/10.1016/j.foodcont.2020.107110
Costa LBM, Godinho Filho M, Fredendall LD, Devós Ganga GM (2021) Lean Six Sigma in the food industry: construct development and measurement validation. Int J Prod Econ 231:107843. https://doi.org/10.1016/j.ijpe.2020.107843
Dandage R, Mantha SS, Rane SB (2018a) Ranking the risk categories in international projects using the TOPSIS method. Int J Manag Proj Bus 11:317–331. https://doi.org/10.1108/IJMPB-06-2017-0070
Dandage RV, Mantha SS, Rane SB, Bhoola V (2018b) Analysis of interactions among barriers in project risk management. J Ind Eng Int 14:153–169. https://doi.org/10.1007/s40092-017-0215-9
Dandage RV, Mantha SS, Rane SB (2019) Strategy development using TOWS matrix for international project risk management based on prioritization of risk categories. Int J Manag Proj Bus 12:1003–1029. https://doi.org/10.1108/IJMPB-07-2018-0128
Darmawan MA, Putra MP, Wiguna B (2014) Value chain analysis for green productivity improvement in the natural rubber supply chain: a case study. J Clean Prod 85:201–211. https://doi.org/10.1016/j.jclepro.2014.01.098
Darmawan MA, Widhiarti RP, Teniwut YK (2018) Green productivity improvement and sustainability assessment of the motorcycle tire production process: a case study. J Clean Prod 191:273–282. https://doi.org/10.1016/j.jclepro.2018.04.228
de Marques PA, Matthé R (2017) Six Sigma DMAIC project to improve the performance of an aluminum die casting operation in Portugal. Int J Qual Reliab Manag 34:307–330. https://doi.org/10.1108/IJQRM-05-2015-0086
Dias J, Nunes E, Sousa S (2020) Productivity improvement of transmission electron microscopes-a case study. Proced Manuf 51:1559–1566. https://doi.org/10.1016/j.promfg.2020.10.217
Djatna T, Munichputranto F (2015) An analysis and design of mobile business intelligence system for productivity measurement and evaluation in tire curing production line. Proced Manuf 4:438–444. https://doi.org/10.1016/j.promfg.2015.11.060
Duan P, He Z, He Y, Liu F, Zhang A, Zhou D (2020) Root cause analysis approach based on reverse cascading decomposition in QFD and fuzzy weight ARM for quality accidents. Comput Ind Eng 147:106643. https://doi.org/10.1016/j.cie.2020.106643
Dweiri F, Ishaq S (2020) Cable insulation productivity improvement using Lean Six Sigma. IJPQM 30:488–508. https://doi.org/10.1504/IJPQM.2020.108573
Ferreras-Higuero E, Leal-Muñoz E, García de Jalón J, Chacón E, Vizán A (2020) Robot-process precision modelling for the improvement of productivity in flexible manufacturing cells. Robot Comput-Integr Manuf 65:101966. https://doi.org/10.1016/j.rcim.2020.101966
Fritz M, Berger PD (2015) Comparing two designs (or anything else!) using paired sample T-tests. In: Fritz M, Berger PD (eds) Improving the user experience through practical data analytics. Morgan Kaufmann, Boston, pp 71–89. https://doi.org/10.1016/B978-0-12-800635-1.00003-3
Chapter Google Scholar
Gavareshki MHK, Abbasi M, Karbasian M, Rostamkhani R (2020) Presenting a productive and sustainable model of integrated management system for achieving an added value in organisational processes. IJPQM 30:429–461. https://doi.org/10.1504/IJPQM.2020.108569
Ge J, Fu Y, Xie R, Liu Y, Mo W (2018) The effect of GVC embeddedness on productivity improvement: from the perspective of R&D and government subsidy. Technol Forecast Soc Chang 135:22–31. https://doi.org/10.1016/j.techfore.2018.07.057
Ghatorha KS, Sharma R, Singh G (2020) Application of root cause analysis to increase material removal rate for productivity improvement: a case study of the press manufacturing industry. Mater Today 26:1780–1783. https://doi.org/10.1016/j.matpr.2020.02.374
Gleeson F, Coughlan P, Goodman L, Newell A, Hargaden V (2019) Improving manufacturing productivity by combining cognitive engineering and lean-six sigma methods. Proced CIRP 81:641–646. https://doi.org/10.1016/j.procir.2019.03.169
Globerson S, Vitner G (2019) Measuring productivity in multi-stage, multi-product environment. IJPQM 26:290–304. https://doi.org/10.1504/IJPQM.2019.098365
Gupta P, Vardhan S (2016) Optimizing OEE, productivity and production cost for improving sales volume in an automobile industry through TPM: a case study. Int J Prod Res 54:2976–2988. https://doi.org/10.1080/00207543.2016.1145817
Gurley K, Edlow J, Burstein JL, Grossman SA (2020) Errors in decisionmaking in emergency medicine: the case of the landscaper’s back and root cause analysis. Ann Emerg Med. https://doi.org/10.1016/j.annemergmed.2020.05.031
Harikrishnan R, Rajeswaran M, Sathish Kumar S, Dinesh K (2020) Productivity improvement in poly-cover packing line through line balancing and automation. Mater Today 33:102–111. https://doi.org/10.1016/j.matpr.2020.03.253
Harris AM, Ziemba J, Bylund J (2020) Implementing a root cause analysis program to enhance patient safety education in urology residency. Urology 138:24–29. https://doi.org/10.1016/j.urology.2019.11.059
Hynes JP, Murray AS, Murray OM, Eustace SK, Gilchrist S, Dolan A, Lawler LP (2019) Use of Lean Six Sigma methodology shows reduction of inpatient waiting time for peripherally inserted central catheter placement. Clin Radiol 74:733.e5-733.e9. https://doi.org/10.1016/j.crad.2019.04.022
Inui T, Kawakami A, Miyagawa T (2012) Market competition, differences in technology, and productivity improvement: an empirical analysis based on Japanese manufacturing firm data. Jpn World Econ 24:197–206. https://doi.org/10.1016/j.japwor.2012.04.002
Islamoglu NE, Ryu K, Moon I (2014) Labour productivity in modular assembly: a study of automotive module suppliers. Int J Prod Res 52:6954–6970. https://doi.org/10.1080/00207543.2014.917773
Ismail R (2018) The impact of human capital and innovation on labour productivity of Malaysian small and medium enterprises. IJPQM 25:245–261. https://doi.org/10.1504/IJPQM.2018.094769
Jadhav JR, Mantha SS, Rane SB (2014a) Exploring barriers in lean implementation. Int J Lean Six Sigma 5(2):122–148. https://doi.org/10.1108/IJLSS-12-2012-0014
Jadhav JR, Mantha SS, Rane SB (2014b) Development of framework for sustainable Lean implementation: an ISM approach. J Ind Eng Int 10:72. https://doi.org/10.1007/s40092-014-0072-8
Jiang G, Zhang R, Ma W, Zhou D, Wang X, He X (2017) Cultivated land productivity potential improvement in land consolidation schemes in Shenyang, China: assessment and policy implications. Land Use Policy 68:80–88. https://doi.org/10.1016/j.landusepol.2017.07.001
Jones EC, Parast MM, Adams SG (2010) A framework for effective six sigma implementation. Total Qual Manag Bus Excell 21:415–424. https://doi.org/10.1080/14783361003606720
Kamble R, Wankhade L (2017) Perspectives on productivity: identifying attributes influencing productivity in various industrial sectors. IJPQM 22:536–566. https://doi.org/10.1504/IJPQM.2017.087868
Kaswan MS, Rathi R (2020) Green Lean Six Sigma for sustainable development: integration and framework. Environ Impact Assess Rev 83:106396. https://doi.org/10.1016/j.eiar.2020.106396
Khan SA, Badar MA, Alzaabi M (2020) Productivity improvement using DMAIC in a Caravan Manufacturing company. IJPQM 30:234–251. https://doi.org/10.1504/IJPQM.2020.107825
Kirkire MS, Rane SB (2017) Evaluation of success factors for medical device development using grey DEMATEL approach. J Model Manag 12:204–223. https://doi.org/10.1108/JM2-09-2015-0062
Kirkire MS, Rane SB, Jadhav JR (2015) Risk management in medical product development process using traditional FMEA and fuzzy linguistic approach: a case study. J Ind Eng Int 11:595–611. https://doi.org/10.1007/s40092-015-0113-y
Kirkire MS, Rane SB, Abhyankar GJ (2020) Structural equation modelling—FTOPSIS approach for modelling barriers to product development in medical device manufacturing industries. J Model Manag 15:967–993. https://doi.org/10.1108/JM2-09-2018-0139
Klefsjö B, Wiklund H, Edgeman RL (2001) Six sigma seen as a methodology for total quality management. Meas Bus Excell 5:31–35. https://doi.org/10.1108/13683040110385809
Kulkarni RG, Kulkarni VN, Gaitonde VN (2018) Productivity improvement in assembly workstation of motor winding unit. Mater Today Proc 5:23518–23525. https://doi.org/10.1016/j.matpr.2018.10.139
Kumar R, Kalra P, Kant S (2020) Productivity enhancement of assembly line by using Maynard operation sequence technique after identification of lean wastages. IJPQM 29:463–482. https://doi.org/10.1504/IJPQM.2020.106400
Kumar Banga H, Kumar R, Kumar P, Purohit A, Kumar H, Singh K (2020) Productivity improvement in manufacturing industry by lean tool. Mater Today Proc 28:1788–1794. https://doi.org/10.1016/j.matpr.2020.05.195
Kusneniwar A, Potdar P, Rane S (2019) Evaluation of performance characteristics and bite condition of single ferrule bite fitting by finite element analysis (FEA). In: Vasudevan H, Kottur VKN, Raina AA (Eds.) Proceedings of international conference on intelligent manufacturing and automation. Springer, Singapore, pp. 239–252. https://doi.org/10.1007/978-981-13-2490-1_22
Liang C, Zhou S, Yao B, Hood D, Gong Y (2020) Toward systems-centered analysis of patient safety events: improving root cause analysis by optimized incident classification and information presentation. Int J Med Inform 135:104054. https://doi.org/10.1016/j.ijmedinf.2019.104054
Liu W-Y, Chen C-H, Chen W-T, Shu C-M (2017) A study of caprolactam storage tank accident through root cause analysis with a computational approach. J Loss Prev Process Ind 50:80–90. https://doi.org/10.1016/j.jlp.2017.09.004
Liu C, Lore KG, Jiang Z, Sarkar S (2021) Root-cause analysis for time-series anomalies via spatiotemporal graphical modeling in distributed complex systems. Knowl-Based Syst 211:106527. https://doi.org/10.1016/j.knosys.2020.106527
Machado CG, Winroth MP, Ribeiro da Silva EHD (2020) Sustainable manufacturing in industry 4.0: an emerging research agenda. Int J Prod Res 58:1462–1484. https://doi.org/10.1080/00207543.2019.1652777
Mahalakshmi S, Arokiasamy A (2020) Productivity and quality enrichment through multi criteria trajectory optimisation of an industrial robot. IJPQM 30:279–303. https://doi.org/10.1504/IJPQM.2020.108380
Mahalakshmi S, Arokiasamy A, Ahamed JFA (2019) Productivity improvement of an eco friendly warehouse using multi objective optimal robot trajectory planning. IJPQM 27:305–328. https://doi.org/10.1504/IJPQM.2019.101517
Meena ML, Jain R, Kumar P, Gupta S, Dangayach GS (2018) Process improvement in an Indian automotive part manufacturing company: a case study. IJPQM 23:524–551. https://doi.org/10.1504/IJPQM.2018.090263
Mexia JT (1990) Best linear unbiased estimates, duality of F tests and the Scheffé multiple comparison method in the presence of controlled heteroscedasticity. Comput Stat Data Anal 10:271–281. https://doi.org/10.1016/0167-9473(90)90007-5
Article MathSciNet MATH Google Scholar
Mishra N, Rane SB (2019a) Business excellence initiative success prediction model based on logistic regression and artificial neural network. Int J Qual Innov 4:132–166. https://doi.org/10.1504/IJQI.2019.105749
Mishra N, Rane SB (2019b) Prediction and improvement of iron casting quality through analytics and Six Sigma approach. Int J Lean Six Sigma 10(1):189–210. https://doi.org/10.1108/IJLSS-11-2017-0122
Mishra DP, Sugla M, Singha P (2013) Productivity improvement in underground coal mines—a case study. J Sustain Min 12:48–53. https://doi.org/10.7424/jsm130306
Molan G, Molan M (2020) Theoretical model for accident prevention based on root cause analysis with graph theory. Saf Health Work. https://doi.org/10.1016/j.shaw.2020.09.004
Article MATH Google Scholar
Motlagh MA, Valmohammadi C, Modiri M (2020) Developing a qualitative model of productivity for service companies using fuzzy analytic hierarchy process: a case study. IJPQM 29:126–147. https://doi.org/10.1504/IJPQM.2020.104519
Mulugeta L (2020) Productivity improvement through lean manufacturing tools in Ethiopian garment manufacturing company. Mater Today Proc. https://doi.org/10.1016/j.matpr.2020.06.599
Murali CS, Prabukarthi A (2020) Productivity improvement in furniture industry using lean tools and process simulation. IJPQM 30:214–233. https://doi.org/10.1504/IJPQM.2020.107812
Murray A, Papa A, Cuozzo B, Russo G (2016) Evaluating the innovation of the Internet of Things: empirical evidence from the intellectual capital assessment. Bus Process Manag J 22:341–356. https://doi.org/10.1108/BPMJ-05-2015-0077
Nakamura K, Kaihatsu S, Yagi T (2019) Productivity improvement and economic growth: lessons from Japan. Econ Anal Policy 62:57–79. https://doi.org/10.1016/j.eap.2018.11.002
Nandakumar N, Saleeshya PG, Harikumar P (2020) Bottleneck identification and process improvement by Lean Six Sigma DMAIC methodology. Mater Today Proc 24:1217–1224. https://doi.org/10.1016/j.matpr.2020.04.436
Padhy R (2017) Six sigma project selections: a critical review. Lean Six Sigma J 8:244–258. https://doi.org/10.1108/IJLSS-06-2016-0025
Pandey H, Garg D, Luthra S (2018) Identification and ranking of enablers of green Lean Six Sigma implementation using AHP. IJPQM 23:187–217. https://doi.org/10.1504/IJPQM.2018.089156
Parmar PS, Desai TN (2020) Evaluating Sustainable Lean Six Sigma enablers using fuzzy DEMATEL: a case of an Indian manufacturing organization. J Clean Prod 265:121802. https://doi.org/10.1016/j.jclepro.2020.121802
Patil RB, Kothavale BS (2020) Failure modes and effects analysis of CNC turning center. In: Gupta VK, Varde PV, Kankar PK, Joshi N (eds.) Reliability and risk assessment in engineering, Lecture notes in mechanical engineering. Springer, Singapore, pp. 49–59. https://doi.org/10.1007/978-981-15-3746-2_5
Patil RB, Kothavale BS (2018) Failure modes and effects analysis (FMEA) of computerized numerical control (CNC) turning center. Int Rev Mech Eng (IREME) 12:78–87. https://doi.org/10.15866/ireme.v12i1.14156
Potdar P, Rane S (2018) Selection of the best manufacturer using TOPSIS and PROMETHEE for asset propelled industry (API). Ind Eng J 11:1–21. https://doi.org/10.26488/IEJ.11.10.1147
Potdar P, Rane S, Mishra N (2020) Design of experiments and Monte Carlo simulation based prediction model for productivity improvement in printing industry. Int J Prod Qual Manag. https://doi.org/10.1504/ijpqm.2020.10033290
Potdar P, Rane S (2017) Exploring success factors for effective implementation of business analytics. National conference on Changing Technology and Rural Development -2017. ISSN [ONLINE]: 2395-1052. 156–163. https://ijsart.com/Home/IssueDetail/20732
Prashar A (2014) Process improvement in farm equipment sector (FES): a case on six sigma adoption. Lean Six Sigma J 5:62–88. https://doi.org/10.1108/IJLSS-08-2013-0049
Rane SB, Kirkire MS (2016) Analysis of barriers to medical device development in India: an interpretive structural modelling approach. Int J Syst Assur Eng Manag 7:356–369. https://doi.org/10.1007/s13198-016-0497-0
Rane SB, Kirkire MS (2017) Interpretive structural modelling of risk sources in medical device development process. Int J Syst Assur Eng Manag 8:451–464. https://doi.org/10.1007/s13198-015-0399-6
Rane SB, Mishra N (2018) Roadmap for business analytics implementation using DIPPS model for sustainable business excellence: case studies from the multiple fields. Int J Bus Excell 15:308–334. https://doi.org/10.1504/IJBEX.2018.092574
Rane SB, Narvel YAM (2016) Reliability assessment and improvement of air circuit breaker (ACB) mechanism by identifying and eliminating the root causes. Int J Syst Assur Eng Manag 7:305–321. https://doi.org/10.1007/s13198-015-0405-z
Rane SB, Narvel YAM (2021) Data-driven decision making with Blockchain-IoT integrated architecture: a project resource management agility perspective of industry 40. Int J Syst Assur Eng Manag. https://doi.org/10.1007/s13198-021-01377-4
Rane S, Potdar P (2020) Blockchain-IoT based risk management approach for Project Procurement process of Asset Propelled Industries (API). Int J Procure Manag 1:1. https://doi.org/10.1504/ijpm.2020.10032403
Rane SB, Thakker SV (2020) Green procurement process model based on blockchain–IoT integrated architecture for a sustainable business. Manag Environ Qual Int J 31:741–763. https://doi.org/10.1108/MEQ-06-2019-0136
Rane SB, Narvel YAM, Khatua N (2017) Development of mechanism for mounting secondary isolating contacts (SICs) in air circuit breakers (ACBs) with high operational reliability. Int J Syst Assur Eng Manag 8:1816–1831. https://doi.org/10.1007/s13198-017-0678-5
Rane SB, Potdar PR, Rane S (2019a) Accelerated life testing for reliability improvement: a case study on Moulded Case Circuit Breaker (MCCB) mechanism. Int J Syst Assur Eng Manag 10:1668–1690. https://doi.org/10.1007/s13198-019-00914-6
Rane SB, Potdar PR, Rane S (2019) Development of Project Risk Management framework based on Industry 40 technologies. Benchmarking Int J 28:1451–1481. https://doi.org/10.1108/BIJ-03-2019-0123
Rane SB, Potdar PR, Mewada M (2021) Implementation of a Six Sigma strategy for process improvement in the wiper motor manufacturing industry. Int J Six Sigma Compet Adv 13:241–270. https://doi.org/10.1504/IJSSCA.2021.120219
Rehman A, Ramzan MB, Shafiq M, Rasheed A, Naeem MS, Savino MM (2019) Productivity improvement through time study approach: a case study from an apparel manufacturing industry of Pakistan. Proced Manuf 39:1447–1454. https://doi.org/10.1016/j.promfg.2020.01.306
Reosekar RS, Pohekar SD (2014) Six Sigma methodology: a structured review. Lean Six Sigma J 5:392–422. https://doi.org/10.1108/IJLSS-12-2013-0059
Schiermoch PD, Beisheim B, Rahimi-Adli K, Engell S (2020) A methodology for data based root-cause analysis for process performance deviations in continuous processes. In: Pierucci S, Manenti F, Bozzano GL, Manca D (eds.) Computer aided chemical engineering, 30 European Symposium on Computer Aided Process Engineering. Elsevier, pp. 1873–1878. https://doi.org/10.1016/B978-0-12-823377-1.50313-X
Schuh G, Potente T, Wesch-Potente C, Weber AR, Prote J-P (2014) Collaboration mechanisms to increase productivity in the context of industrie 4.0. Proced CIRP 19:51–56. https://doi.org/10.1016/j.procir.2014.05.016
Selvam G, Prince SAD, Prakash VS, Rohit T (2018) Quality and productivity improvement through spot welding process optimisation in automobile body shop. IJPQM 23:110–127. https://doi.org/10.1504/IJPQM.2018.088611
Siddiqui SQ, Ullah F, Thaheem MJ, Gabriel HF (2016) Six sigma in construction: a review of critical success factors. Lean Six Sigma J 7:171–186. https://doi.org/10.1108/IJLSS-11-2015-0045
Singh M, Rathi R, Garza-Reyes JA (2021) Analysis and prioritization of Lean Six Sigma enablers with environmental facets using best worst method: a case of indian MSMEs. J Clean Prod 279:123592. https://doi.org/10.1016/j.jclepro.2020.123592
Sommer AC, Blumenthal EZ (2019) Implementation of lean and six sigma principles in ophthalmology for improving quality of care and patient flow. Surv Ophthalmol 64:720–728. https://doi.org/10.1016/j.survophthal.2019.03.007
Steenwinckel B, De Paepe D, Vanden Hautte S, Heyvaert P, Bentefrit M, Moens P, Dimou A, Van Den Bossche B, De Turck F, Van Hoecke S, Ongenae F (2021) FLAGS: a methodology for adaptive anomaly detection and root cause analysis on sensor data streams by fusing expert knowledge with machine learning. Futur Gener Comput Syst 116:30–48. https://doi.org/10.1016/j.future.2020.10.015
Steere L, Rousseau M, Durland L (2018) Lean Six Sigma for intravenous therapy optimization: a hospital use of lean thinking to improve occlusion management. J Assoc Vasc Access 23:42–50. https://doi.org/10.1016/j.java.2018.01.002
Sunder MV (2016) Lean Six Sigma project management—a stakeholder management perspective. TQM J 28:132–150. https://doi.org/10.1108/TQM-09-2014-0070
Swarnakar V, Singh AR, Tiwari AK (2020) Effect of Lean Six Sigma on firm performance: a case of Indian automotive component manufacturing organization. Mater Today Proc. https://doi.org/10.1016/j.matpr.2020.07.115
Tenera A, Pinto LC (2014) A Lean Six Sigma (LSS) project management improvement model. Proced Soc Behav Sci 119:912–920. https://doi.org/10.1016/j.sbspro.2014.03.102
Thangaiah ISS, Sharma V, Sundharam VN (2018) Analysing of customer feedback on critical quality parameters to improve productivity in manufacturing—a case study. IJPQM 23:349–368. https://doi.org/10.1504/IJPQM.2018.089805
Timans W, Ahaus K, Antony J (2014) Six Sigma methods applied in an injection moulding company. Lean Six Sigma J 5:149–167. https://doi.org/10.1108/IJLSS-07-2013-0037
Titmarsh R, Assad F, Harrison R (2020) Contributions of Lean Six Sigma to sustainable manufacturing requirements: an industry 4.0 perspective. Proced CIRP 90:589–593. https://doi.org/10.1016/j.procir.2020.02.044
Uddin MA, Stranieri A, Gondal I, Balasubramanian V (2021) A survey on the adoption of blockchain in IoT: challenges and solutions. Blockchain Res Appl. https://doi.org/10.1016/j.bcra.2021.100006
Waibel MW, Steenkamp LP, Moloko N, Oosthuizen GA (2017) Investigating the effects of smart production systems on sustainability elements. Proced Manuf 8:731–737. https://doi.org/10.1016/j.promfg.2017.02.094
Wang S, Wan J, Li D, Zhang C (2016) Implementing smart factory of industrie 4.0: an outlook. Int J Distrib Sens Netw 12(1):3159805. https://doi.org/10.1155/2016/3159805
Wang J, Yang Z, Su J, Zhao Y, Gao S, Pang X, Zhou D (2018) Root-cause analysis of occurring alarms in thermal power plants based on Bayesian networks. Int J Electr Power Energy Syst 103:67–74. https://doi.org/10.1016/j.ijepes.2018.05.029
Wu C, Yi D, Weng W, Li S, Zhou J, Zheng F (2015) Arc erosion behavior of Ag/Ni electrical contact materials. Mater Des 85:511–519. https://doi.org/10.1016/j.matdes.2015.06.142
Yadav S, Luthra S, Garg D (2022) Internet of things (IoT) based coordination system in Agri-food supply chain: development of an efficient framework using DEMATEL-ISM. Oper Manag Res 15:1–27. https://doi.org/10.1007/s12063-020-00164-x
Yang J, Zhan Z, Chou CC, Yang R-J, Zheng L, Guo G (2018) Root cause analysis strategy for robust design domain recognition. Eng Optim 50:1325–1346. https://doi.org/10.1080/0305215X.2017.1391241
Yue W, Chen X, Huang K, Zeng Z, Xie Y (2018) Knowledge modeling for root cause analysis of complex systems based on dynamic fuzzy cognitive maps. IFAC-PapersOnLine 51:13–18. https://doi.org/10.1016/j.ifacol.2018.09.385
Zahraee SM, Rohani JM, Wong KY (2018) Application of computer simulation experiment and response surface methodology for productivity improvement in a continuous production line: case study. J King Saud Univ 30:207–217. https://doi.org/10.1016/j.jksues.2018.04.003
Zhong X, Xu Y, Liu Y, Wu X, Zhao D, Zheng Y, Jiang J, Deng Z, Fu X, Li X (2020) Root cause analysis and diagnosis of solid oxide fuel cell system oscillations based on data and topology-based model. Appl Energy 267:114968. https://doi.org/10.1016/j.apenergy.2020.114968
Zu X, Fredendall LD (2009) Enhancing six sigma implementation through human resource management. Qual Manag J 16:41–54. https://doi.org/10.1080/10686967.2009.11918249
Download references
Author information
Authors and affiliations.
Sardar Patel College of Engineering, Mumbai, India
Santosh B. Rane & Sandesh Wavhal
Parul Institute of Technology, Vadodara, India
Prathamesh R. Potdar
You can also search for this author in PubMed Google Scholar
Corresponding author
Correspondence to Prathamesh R. Potdar .
Ethics declarations
Conflict of interest.
This research has no potential conflict of Interest.
Human and animals rights
This research involves human participation only for survey purposes and does not involve any animals.
Informed consent
This research does not require any informed consent.
Additional information
Publisher's note.
Springer Nature remains neutral with regard to jurisdictional claims in published maps and institutional affiliations.
Rights and permissions
Springer Nature or its licensor (e.g. a society or other partner) holds exclusive rights to this article under a publishing agreement with the author(s) or other rightsholder(s); author self-archiving of the accepted manuscript version of this article is solely governed by the terms of such publishing agreement and applicable law.
Reprints and permissions
About this article
Rane, S.B., Wavhal, S. & Potdar, P.R. Integration of Lean Six Sigma with Internet of Things (IoT) for productivity improvement: a case study of contactor manufacturing industry. Int J Syst Assur Eng Manag 14 , 1990–2018 (2023). https://doi.org/10.1007/s13198-023-01980-7
Download citation
Received : 03 May 2022
Revised : 04 April 2023
Accepted : 06 June 2023
Published : 04 July 2023
Issue Date : October 2023
DOI : https://doi.org/10.1007/s13198-023-01980-7
Share this article
Anyone you share the following link with will be able to read this content:
Sorry, a shareable link is not currently available for this article.
Provided by the Springer Nature SharedIt content-sharing initiative
- Productivity improvement
- Lean Six Sigma
- Internet of Things (IoT)
- Contactor manufacturing industry
- Electro magnetic contactor
- Find a journal
- Publish with us
- Track your research
Thank you for visiting nature.com. You are using a browser version with limited support for CSS. To obtain the best experience, we recommend you use a more up to date browser (or turn off compatibility mode in Internet Explorer). In the meantime, to ensure continued support, we are displaying the site without styles and JavaScript.
- View all journals
- Explore content
- About the journal
- Publish with us
- Sign up for alerts
Latest science news, discoveries and analysis
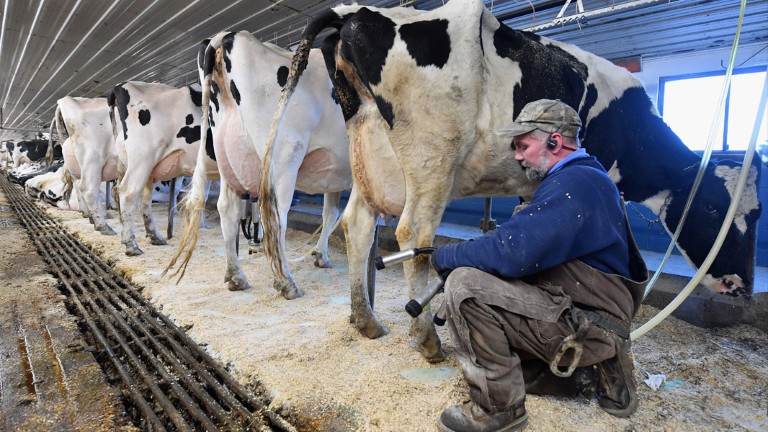
Bird flu in US cows: is the milk supply safe?
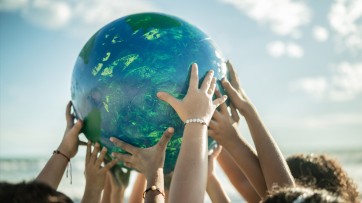
Future of Humanity Institute shuts: what's next for ‘deep future’ research?
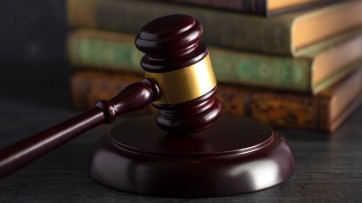
Judge dismisses superconductivity physicist’s lawsuit against university
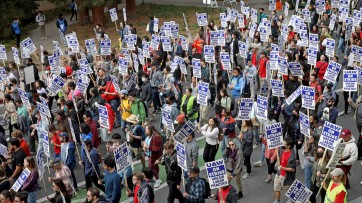
NIH pay raise for postdocs and PhD students could have US ripple effect
Hello puffins, goodbye belugas: changing arctic fjord hints at our climate future, china's moon atlas is the most detailed ever made, ‘shut up and calculate’: how einstein lost the battle to explain quantum reality, rat neurons repair mouse brains — and restore sense of smell, ecologists: don’t lose touch with the joy of fieldwork chris mantegna.
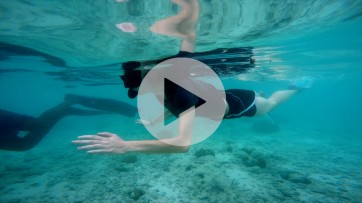
Should the Maldives be creating new land?
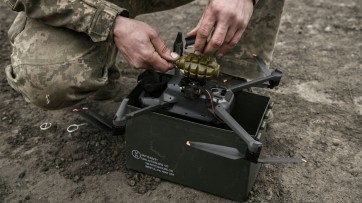
Lethal AI weapons are here: how can we control them?
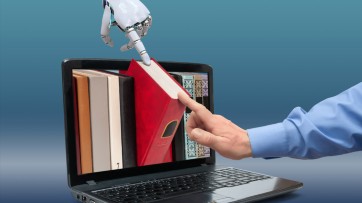
Algorithm ranks peer reviewers by reputation — but critics warn of bias
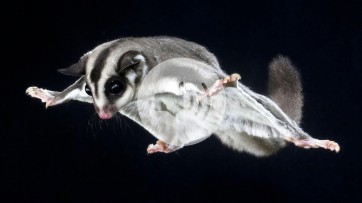
How gliding marsupials got their ‘wings’
Audio long read: why loneliness is bad for your health, could a rare mutation that causes dwarfism also slow ageing, nato is boosting ai and climate research as scientific diplomacy remains on ice, plastic pollution: three numbers that support a crackdown.
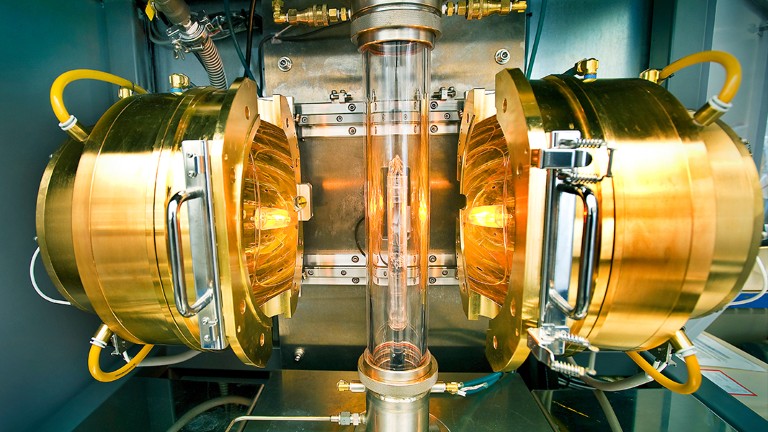
Retractions are part of science, but misconduct isn’t — lessons from a superconductivity lab
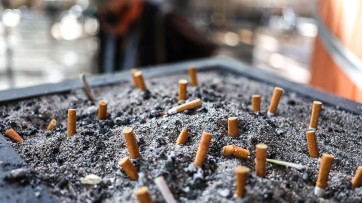
Any plan to make smoking obsolete is the right step
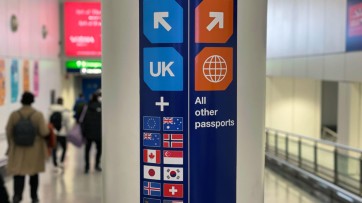
Citizenship privilege harms science
European ruling linking climate change to human rights could be a game changer — here’s how charlotte e. blattner, will ai accelerate or delay the race to net-zero emissions, current issue.
The Maldives is racing to create new land. Why are so many people concerned?
Surprise hybrid origins of a butterfly species, stripped-envelope supernova light curves argue for central engine activity, optical clocks at sea, research analysis.
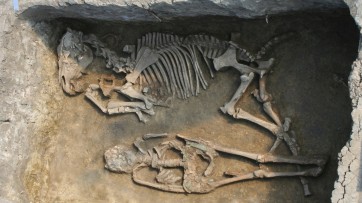
Ancient DNA traces family lines and political shifts in the Avar empire
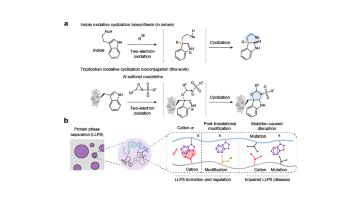
A chemical method for selective labelling of the key amino acid tryptophan
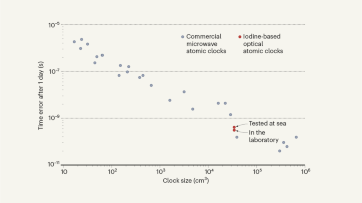
Robust optical clocks promise stable timing in a portable package
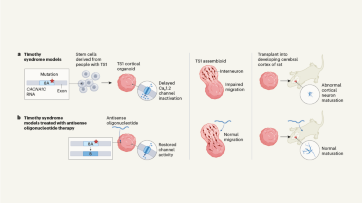
Targeting RNA opens therapeutic avenues for Timothy syndrome
Bioengineered ‘mini-colons’ shed light on cancer progression, galaxy found napping in the primordial universe, tumours form without genetic mutations, marsupial genomes reveal how a skin membrane for gliding evolved.
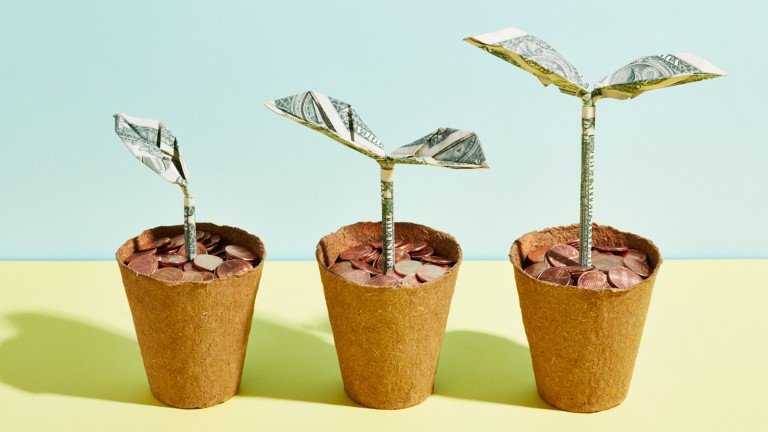
Scientists urged to collect royalties from the ‘magic money tree’
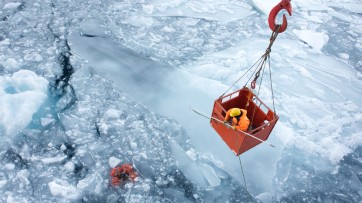
Breaking ice, and helicopter drops: winning photos of working scientists
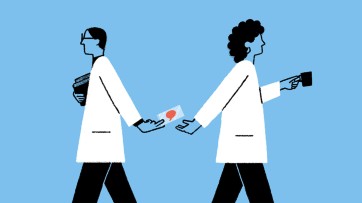
Shrouded in secrecy: how science is harmed by the bullying and harassment rumour mill
How ground glass might save crops from drought on a caribbean island, londoners see what a scientist looks like up close in 50 photographs, books & culture.
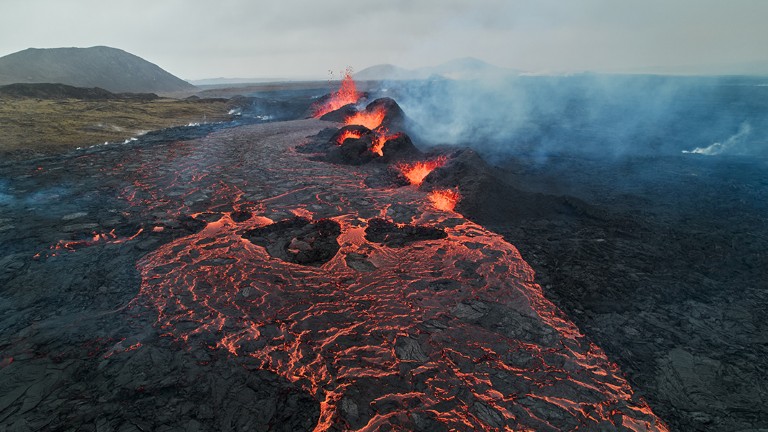
How volcanoes shaped our planet — and why we need to be ready for the next big eruption
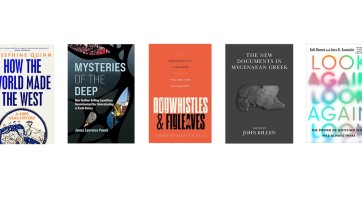
Dogwhistles, drilling and the roots of Western civilization: Books in brief
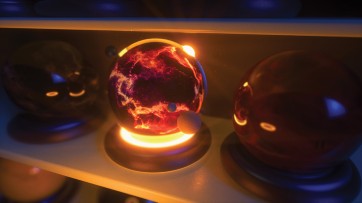
Cosmic rentals
Las borinqueñas remembers the forgotten puerto rican women who tested the first pill, dad always mows on summer saturday mornings, nature podcast.

Latest videos
Nature briefing.
An essential round-up of science news, opinion and analysis, delivered to your inbox every weekday.

Quick links
- Explore articles by subject
- Guide to authors
- Editorial policies
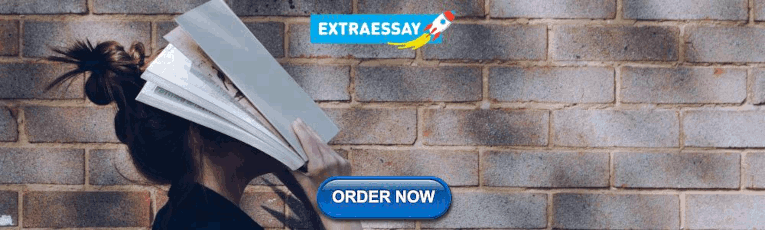
IMAGES
VIDEO
COMMENTS
There are three fundamental types of root causes: Environmental root cause. These are causes related to external factors such as moisture levels, weather, or geography. Individual root cause. These are causes related to an individual's behaviour, personal choices, ability, or circumstance. Organisational root cause.
The following root cause analysis example incidents demonstrate how Cause Mapping can be used to document problems and identify solutions in various industries. Select an industry on the left to view its case studies on the right. Each example has a downloadable PDF to accompany the write-up.
8 Essential Steps of an Organizational Root Cause Analysis. 1. Identify Performance or Opportunity Gaps. The first step in a root cause analysis is identifying the most important performance or opportunity gaps facing your team, department, or organization. Performance gaps are the ways in which your organization falls short or fails to deliver ...
The first goal of root cause analysis is to discover the root cause of a problem or event. The second goal is to fully understand how to fix, compensate, or learn from any underlying issues within the root cause. The third goal is to apply what we learn from this analysis to systematically prevent future issues or to repeat successes.
ANALYZE. Identify the mistakes, errors, and failures that directly led to the incident or failed to mitigate the consequences (Causal Factors). Effective root cause analysis for Causal Factor to find fixable root causes. Definition of a Root Cause : The absence of a best practice or knowledge that would have prevented the problem or ...
- Investigation reports, congressional testimony, etc. - Interviews with former members of the organizations . Case study selection: the who Case studies were selected to cover various: - Industries - Organizational structures ... •Based on root cause analysis Investigational (after accident) Finding II: responsibilities differ ...
A root cause is defined as a factor that caused a nonconformance and should be permanently eliminated through process improvement. The root cause is the core issue—the highest-level cause—that sets in motion the entire cause-and-effect reaction that ultimately leads to the problem (s). Root cause analysis (RCA) is defined as a collective ...
WEB Aruba called Sologic to help facilitate a root cause analysis. The investigation identified previously unknown technology and cultural issues, along with solutions designed not only to prevent the same problem from recurring, but to have a broader positive impact on the business. Read the case study.
Root cause analysis is a problem-solving approach that uses the analogy of roots and blooms to model cause-and-effect relationships. Rather than focusing on what's above the surface, root cause analysis troubleshoots solutions to problems by analyzing what is causing them. Note. Similarly to exploratory research, it's important to remember ...
By ensuring an effective incident reporting system is in place and engaging staff in root cause analysis (RCA), leaders can create a collaborative environment where nurses feel free to speak up about errors and participate in finding solutions. This article discusses reporting systems and uses a case study to illustrate RCA in action.
Root cause analysis, also known as RCA, is the investigation process following an incident. The incident may or may not have caused harm to a person or property. Incidents may not have occurred at all, but instead, someone reported a dangerous situation. Either way, a root cause analysis ought to find completion following any form of incident.
Root Cause Analysis, commonly abbreviated as RCA, is a systematic approach to identifying the main cause of a problem or failure. Instead of merely addressing the symptoms, RCA digs deeper, striving to uncover the underlying issues that are the real culprits. Think of it as a detective working tirelessly to solve a mystery, refusing to rest ...
in root cause analysis (RCA), leaders can cre-ate a collaborative environment where nurses feel free to speak up about errors and partici-pate in finding solutions. This article discusses reporting systems and uses a case study to il-lustrate RCA in action. Incident reporting system Nurses, who are among the highest reporters
The case studies from other industries described below provide tangible implementation examples and valuable lessons learned that can inform improvements in the food industry as well. ... and the root causes shared in incident reports posted on the network's ... Root cause analysis: A retrospective investigative tool used to identify who ...
5 Techniques of Root Cause Analysis Methods. Root Cause Analysis (RCA) employs various methods and techniques to identify and address the underlying causes of problems or failures. Here are some common methods used for Root Cause Analysis: 5 Whys: The 5 Whys technique involves asking "why" repeatedly to trace the causal chain back to its ...
A Cause Map, an intuitive method for performing a root cause analysis, can be built to visually layout the cause-and-effect relationships of the causes that contributed to the accident. The first step in Cause Mapping it to define the problem by filling in an Outline which includes listing the impacts to the organizational goals. The Cause Map ...
A. RCA Process, Step 1 & 2 - Problem Understanding and Cause Brainstorming. The goal of these steps is to scope the RCA and center on the preliminary identified problem causes. The performance matrix, Fig. 3, is used to rank the identified causes on their Importance and Performance.
WEB Aruba called Sologic to help facilitate a root cause analysis. The investigation identified previously unknown technology and cultural issues, along with solutions designed not only to prevent the same problem from recurring, but to have a broader positive impact on the business. Read the case study.
Download Root Cause Analysis Template Below. Excel | Word | PDF. This root cause analysis report template allows for a detailed examination of the event. Use it to record information on the incident's background and contributing factors, actions taken to reduce future risk, findings related to the identified root cause, as well as other notable findings that aren't directly related to the ...
A case study is a flexible research design that captures holistic and meaningful characteristics of actual life events . Case studies can provide a detailed understanding of what is happening and solid grounds for improvement . Case study research has a strong advantage in examining the relevant process . It can capture the complexity of a case ...
Step 1: Identify the Problem. Before diving into a 5 Whys analysis, it's crucial to clearly identify the problem or issue at hand. This step sets the stage for the entire process and ensures that the focus remains on addressing the right concern. Take the time to gather relevant data, observe patterns, and consult with team members or ...
In the case of medical error, this variation in performance may result in a sentinel event. ... This framework should be utilized as a general template when preparing the RCA report that will eventually be submitted to the Joint Commission after thorough evaluation. ... A root cause analysis was performed, and measures were taken to avoid this ...
Root cause analysis (RCA) emerged in the health care field almost 20 years ago. This technique is used worldwide to understand the remote and direct factors favouring the occurrence of an avoidable adverse event (AAE) [ 1 ], and improvement of patient safety [ 2 ]. Three studies have analysed the utility and limitations of this technique [ 3, 4 ...
Root Cause A ssesment (RCA) is the process of identifying. causal factors using a structured approach with techniques. designed to provide a focus for identifying and resolving. problems. Root ...
Root cause analysis (RCA) is an approach to identify the root causes of specific results and it is also helpful for impact analysis in information technology systems ... This case study considered only the aspects of the DMAIC methodology of Six Sigma for productivity improvement. In future directions, the consequence of the Design of ...
This study aimed to investigate the probable existence of a causal relationship between sleep phenotypes and proliferative diabetic retinopathy (PDR). Single nucleotide polymorphisms associated ...
Find breaking science news and analysis from the world's leading research journal.