- Our Courses
- About DCM Learning
- Inhouse Training
- Training Resources

Lean Six Sigma Project Examples | 17 Full Case Studies
Ready to begin your first Lean Six Sigma project? Looking for examples for inspiration or reference to get you started? Here are some project storyboards from different industries and from home. Remember, Lean Six Sigma can help you with more than just work!
- Reducing Underwriting Resubmits by Over 20%
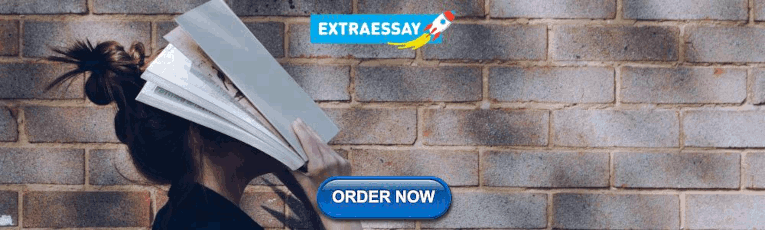
Governments
- A Call to Change: Pioneering Lean Six Sigma at Los Angeles County
- Can Lean Six Sigma Be Applied in County Government?
- How the City of San Antonio Increased Payments for Street Maintenance Using Lean Six Sigma
- Reducing Bid Tab Creation Cycle Time by 22%
- Reducing Cycle Time for Natural Disaster Response by 50%
Manufacturing
- Increasing First Run Parts From 60% to 90% With Lean Six Sigma
- Reducing Bent/Scratched/Damaged (BSD) Scrap for Building Envelopes
- Reducing Lead Time in Customer Replacement Part Orders by 41%
- Reducing Learning Curve Ramp for Temp Employees by 2 Weeks
- Reducing Purchase Order Lead Time by 33% Using Lean Six Sigma
- Herding Cats Using Lean Six Sigma: How to Plan for and Manage the Chaos of Parallel Processes
- Lean Six Sigma Increases Daily Meat Production by 25%
- Lean Six Sigma Helps Feed People In Need 45% Faster
- Accelerating Lean Productivity With Immersive Collaboration
- Reducing Incorrect Router Installations by 60% for Call One
- Reducing Software Bug Fix Lead Time From 25 to 15 Days
Lean Reviews: Stories from Our Customers
Over the past 2 years, over 2,000 learners (2,197 to be exact) have come to DCM to learn more about lean and get certified. Read (and watch) their reviews to see how our courses have helped them achieve their career goals.
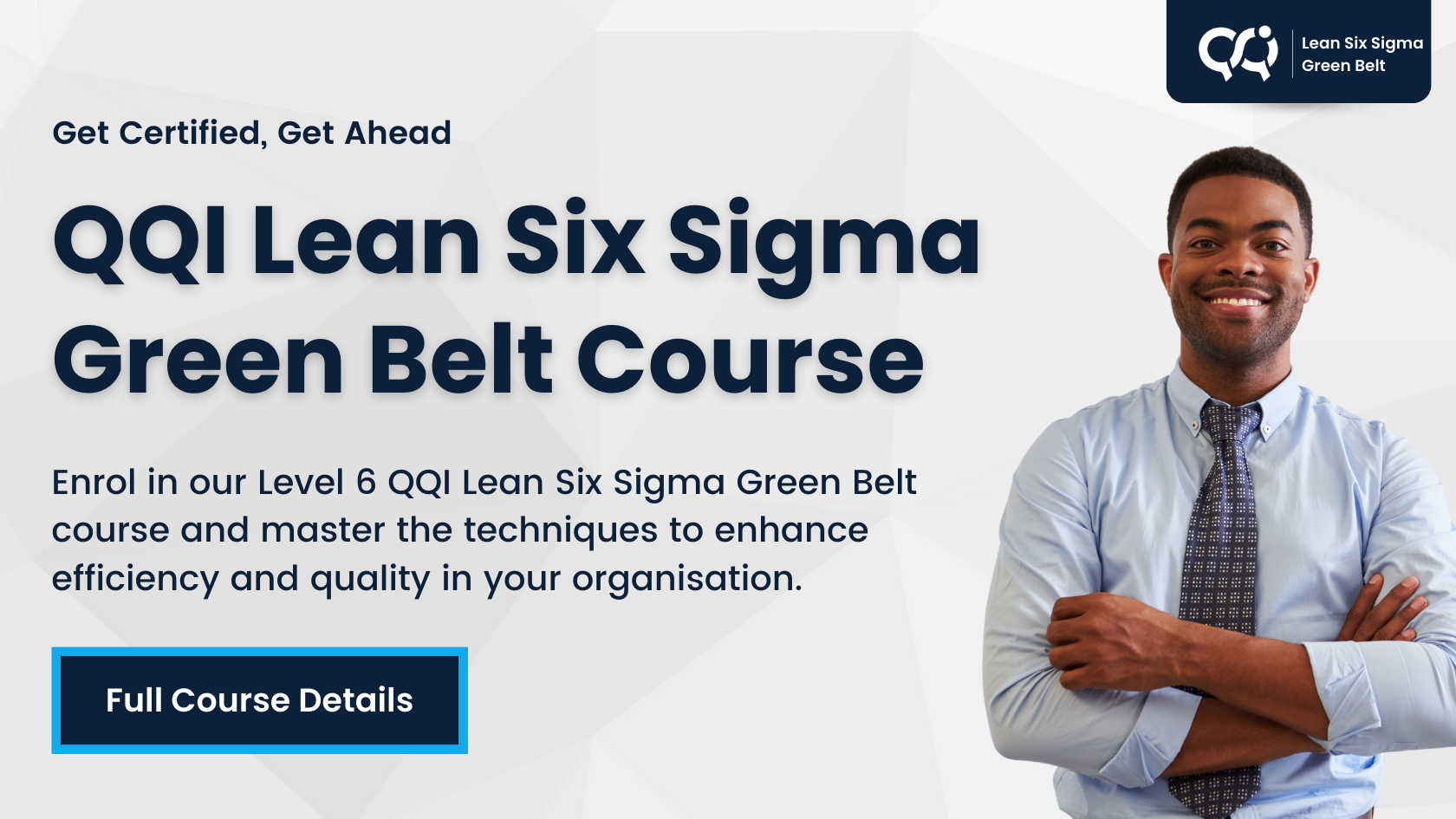
Inhouse Tailored Training for Your Team
We provide training programs that are developed by industry, for industry. Our range of programs can be delivered in a way that suits the needs of your business to offer your employees learning that is accessible and flexible.
We add value to your business by providing specialised, flexible and scalable training that meets your training needs. As your workforce grows and evolves, our globally certified and industry-validated learning solutions can assess, train and qualify your employees. For more information on how we can help please visit the in-house training page .
Membership, Stay Connected. Stay Relevant.
Completing a program is a point-in-time exercise that delivers huge value, but there is a next step to maintaining the currency of your skills in the ever-evolving professional world.
Membership is the next step .
A unique platform, membership is designed to ensure that you are in tune and up-to-date with the latest tools, trends and developments. Being a member provides just-in-time training and continuous professional development, and an exclusive and evolving content library informed by subject matter experts and industry leaders.
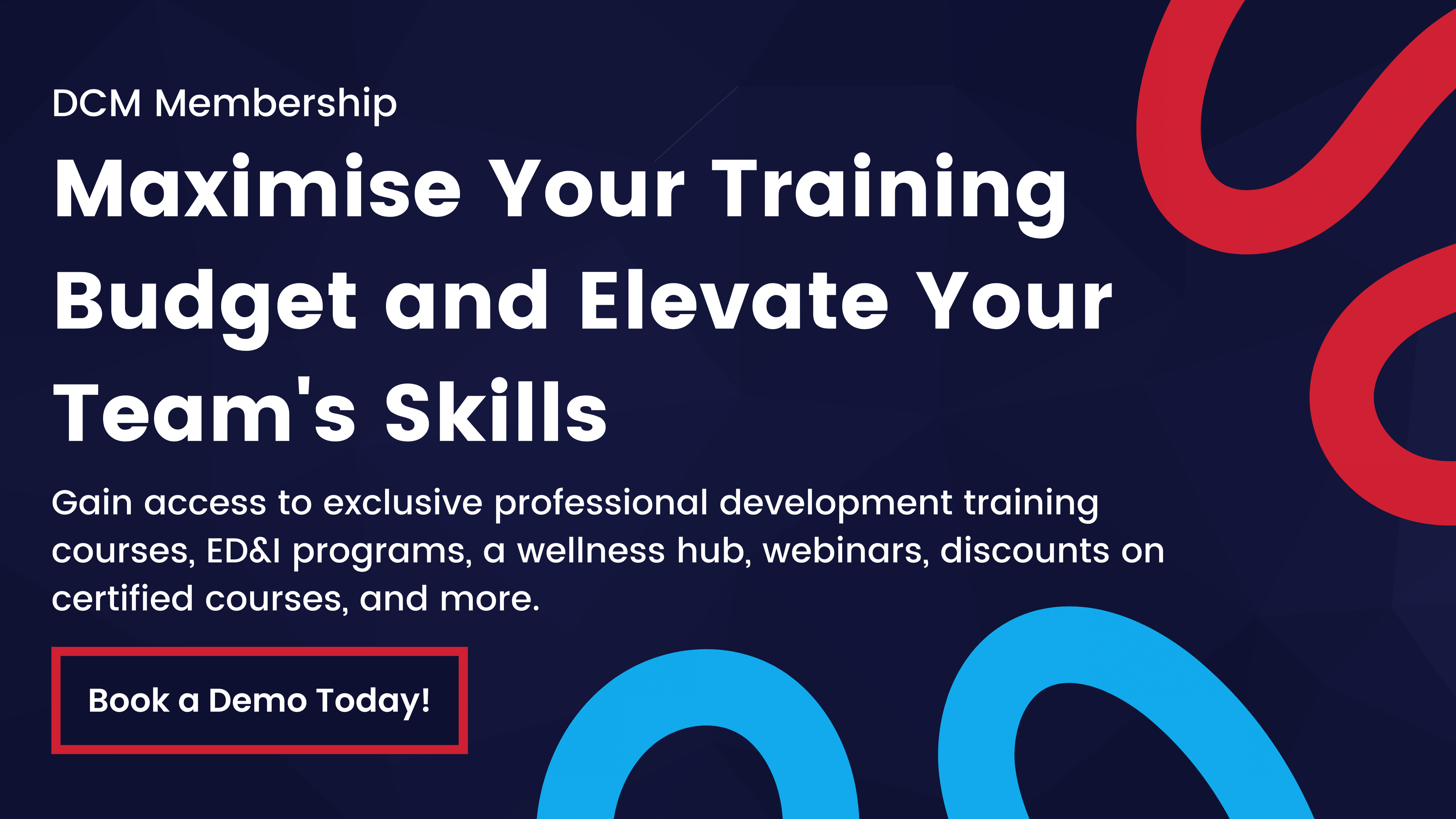
Our expert team is ready to support you from start to finish and answer any questions you have. Submit your email and we'll be in touch shortly to assist you.
Thanks for signing up. Here are some training courses for you to explore.
By clicking “Start Learning”, you agree to our terms and privacy policy .
Free Bitesize Courses
We have over 100 free courses available to explore, all created by expert trainers, packed full of practical exercises and real-world examples.
Make sure you Safeguard Your Training Investment . DCM offer courses accredited by:
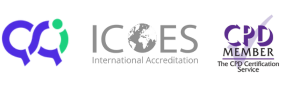
Course Categories

*Add your email and we will send you the full course directory to review at a time that suits you.
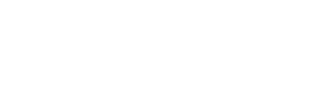
Open Your Brochure
Just to let you know, we are offering €200 credit for the course when you become a member with DCM.
We are very proud of our advisory team in DCM Learning. If you have any questions at all please feel free to ask our team. They will be more than happy to help.
We value your privacy and we will only get in touch about upcoming courses or events that are available to members.
It's so simple... We'll send you the €200 credit and access to the exclusive members area with a full list of the free courses.
By clicking “Get Your Voucher”, you agree to our terms and privacy policy .
- ASME Foundation
- Sections & Divisions
- Back to Main Menu
- Access Benefits
- Communication Preferences
- Digital Downloads
- Purchase History
- Committee History
- Sign In/Create Account
7 Examples of Lean Manufacturing in Action
- Topics & Resources
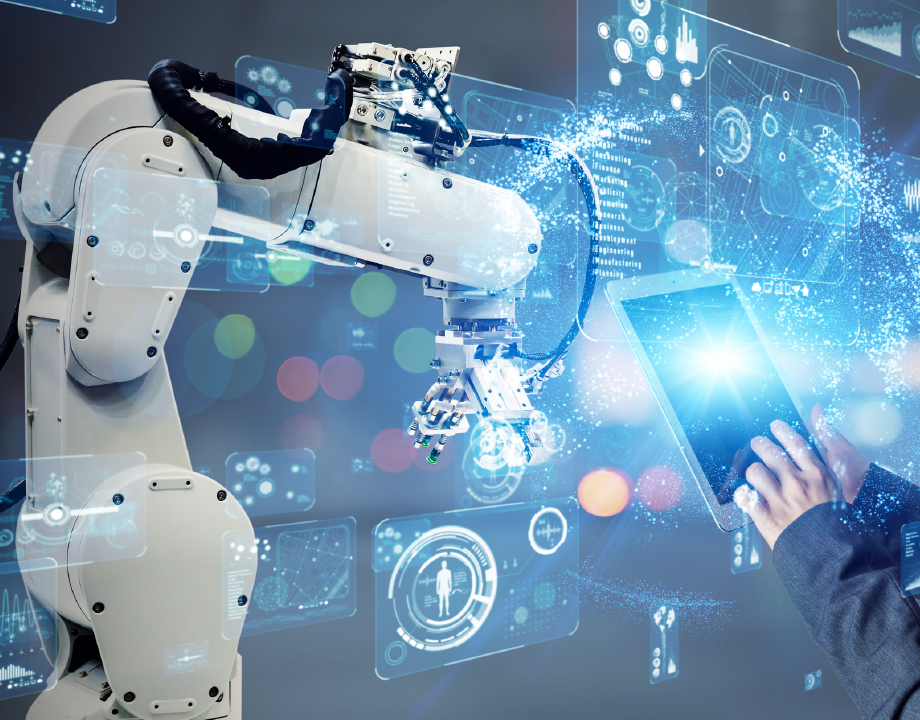
These seven real-life example of lean tools and techniques show how they can improve operational performance and reduce costs.
Date Published:
Aug 27, 2020
Mark Crawford
This story was updated on 10/18/2022.
Lean manufacturing has been around for decades, with implementation of lean tools and techniques resulting in impressive efficiency and production gains. When implemented correctly, lean is a comprehensive process that eliminates waste from manufacturing processes, thereby reducing cost and adding value to the customer.
Below are seven real-life examples of how simple lean techniques can improve manufacturing efficiency and production.
1. Cable Manufacturing
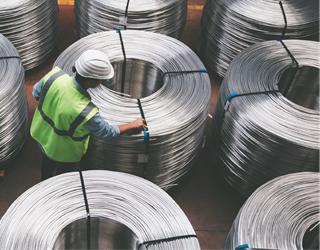
Results: Machine set-ups that once averaged five hours per machine were reduced to 35 minutes, adding about five hours of additional up-time per machine per day.
2. Truck Manufacturing
Dakota Bodies in South Dakota builds truck bodies for the service and industrial markets. To keep up with market demands, a lean team was established to work with company leaders to define their goals for the lean program. Lean 101 training was provided for supervisors, managers, and key operators, and a kanban system was installed to support just-in-time manufacturing and reduce inventory levels.
Results: Revenues improved by 20 percent, and overall productivity by five percent.
Editor’s Pick: 5 Key Lean Principles for Engineers
3. Printing Industry
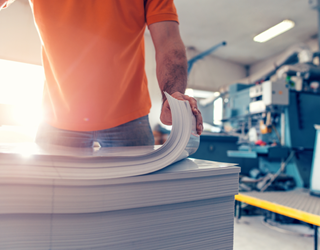
Results: On-time delivery increased to 95 percent with much-shortened lead times, and improved inventory management resulted in less waste of finished product.
4. Automotive Parts Manufacturing
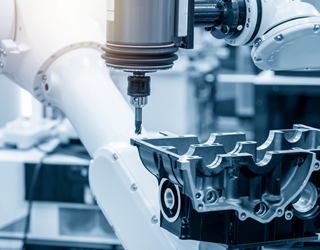
Results: The new changeover system resulted in 1.5 hours of added production up-time and increased throughput by more than $1 million annually.
5. Warehouse Management
A manufacturer used an incoming warehouse for large volumes of raw materials. Operational costs were high, including three full-time material stagers who unloaded, stored, and delivered the materials to assembly lines as needed. Management wanted to eliminate the warehouse without slowing down production, so a lean team worked with suppliers to design a point-of-use kanban system for just-in-time manufacturing. Staff was also trained in flow manufacturing and 5S workplace organization.
Results: The warehouse was no longer needed for raw-material storage, and thus converted for other value-added activities. The three stagers were trained for higher-level positions.
You May Also Like: 6 Lean Principles for an Industry 4.0 World
6. Customer Service
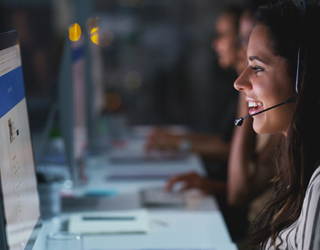
Results: Capacity increased by 20 percent, and on-time delivery increased to 95 percent, with fewer administrative steps. Because of improved efficiency, additional staff and office space were not required.
7. Heating and Air-Conditioning Manufacturing
MicroMetl, a Nevada-based manufacturer of heating and air conditioning equipment, wanted to increase efficiency and maintain high levels of product quality and consistency using lean. After analyzing workflow, management realized that a single heating and air conditioning part traveled 1.5 miles throughout the plant during assembly. The company cellularized the manufacturing process so that the part was instead assembled within an area of 100 feet.
Results: The lean improvements reduced indirect labor costs by 21 percent, which helped the company reduce prices, increase market share, and retain 25 positions.
Related Reading: What is Sustainable Manufacturing?
Next-Generation Lean
Lean tools are always valid. With the onset of Industry 4.0 and the Internet of Things (IoT), though, lean goals can be accomplished much more quickly. Lean principles can be integrated with cutting-edge technologies that enable constant, real-time monitoring, faster decision-making, improved efficiency, and the leanest processes possible.
“IoT intersects with lean methodology and has the potential to take lean to the next level,” pointed out Dean Hamilton, senior vice president for Acclerite, a provider of business-critical infrastructure software. “The information gleaned from connected devices, including user experiences with a variety of products, can be fed back to instrumented factories to provide unprecedented opportunities to enhance manufacturing processes and reduce waste.”
Mark Crawford is a technology writer based in Corrales, NM.
The latest engineering courses, now 25% off
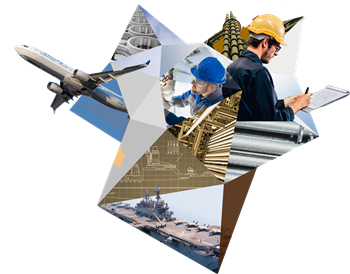
With hundreds of relevant courses to choose from, ASME’s accredited, skill-based learning solutions support the success of your employees and your business.
For a limited time, get 25% off our on demand courses when you buy for a group of 5 or more. Use code 5FOR25 at checkout to train on:
- Geometric Dimensioning and Tolerancing (GD&T)
- ASME BPVC Section VIII
- ASME B31 Piping
- Nuclear Power
When you’re ready to get started, you can browse our full course catalog here . And if you find that you have further questions about ASME’s learning options, don’t hesitate to get in touch .
Related Content
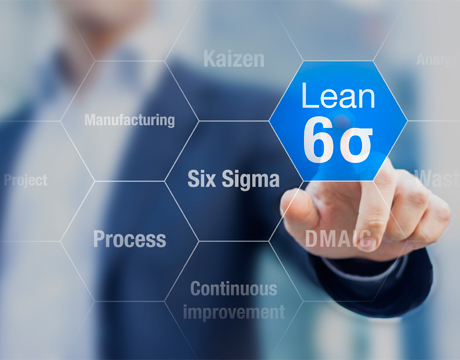
ASME Membership (1 year) has been added to your cart.
The price of yearly membership depends on a number of factors, so final price will be calculated during checkout.
You are now leaving ASME.org
Lean Events and Training / Forms and Templates
Forms and Templates
Downloads for A3 problem solving, standard work , project management, and value stream mapping .
Problem Solving Templates
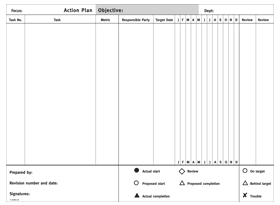
A3 Action Plan Form (from Getting the Right Things Done)
- The action plan template helps define the who, what, when, where, and how of a plan on one page.
- Helps track progress and highlight problems so action can be taken.
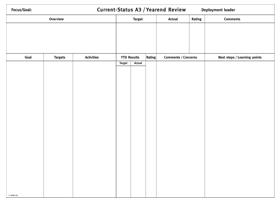
A3 Status Review Form (from Getting the Right Things Done)
- Top box provides an overview with respect to our critical end-of-pipe metrics.
- Second box provides an overview of activities, and usually reflects what’s been prescribed on the action plan of the right side of the strategy A3.
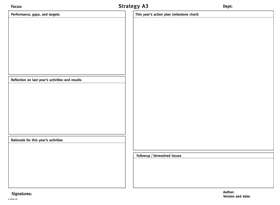
A3 Strategy Form (from Getting the Right Things Done)
- A strategy A3 is a one-page storyboard on 11-inch by 17-inch paper that helps tell the strategy “story.”
- Logic flows from top left to bottom right, and each box leads to the next one.
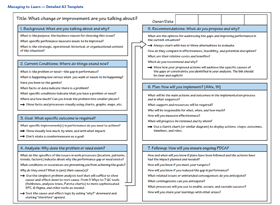
Detailed A3 Template (from Managing to Learn)
- Print this A3 template out to remind you of each section of the problem-solving A3 as you are creating your own.
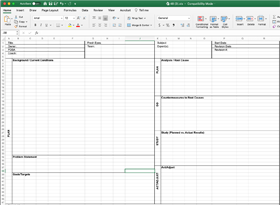
PDSA A3 Template (from On the Mend)
- A3 Template, in Excel, following the PDSA cycle.
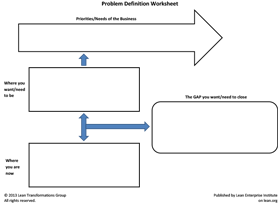
Problem Definition Worksheet
- This worksheet can help you breakdown the problem into a clearly defined gap as well as see how the problem aligns to the needs of the business or your True North purpose.
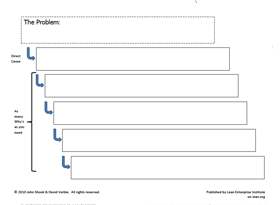
Root Cause Template
- This template gives you space to record the problem as well as the direct causes and underlying causes.
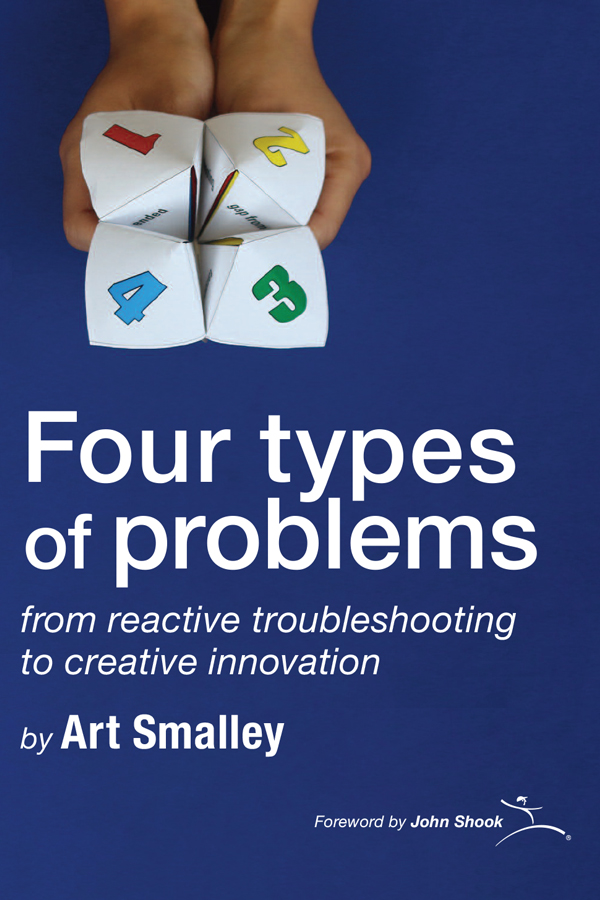
Four Types of Problems
Art Smalley
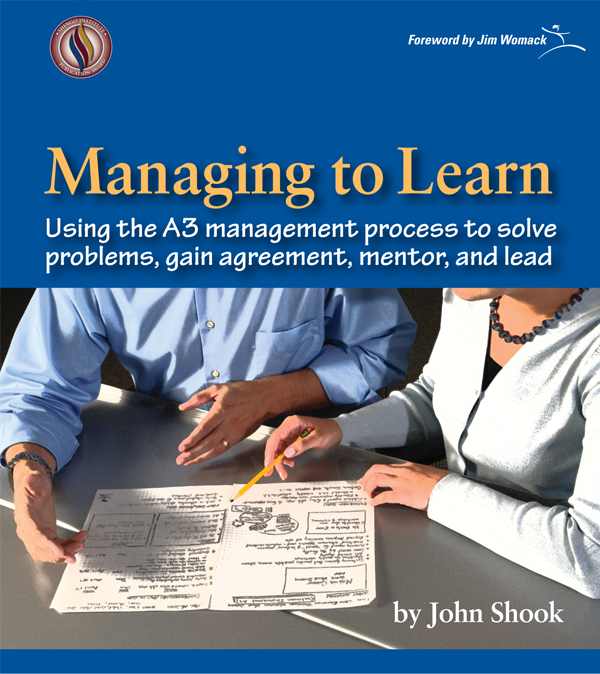
Managing to Learn: Using the A3 management process

Perfecting Patient Journeys
Beau Keyte , Tom Shuker and Judy Worth
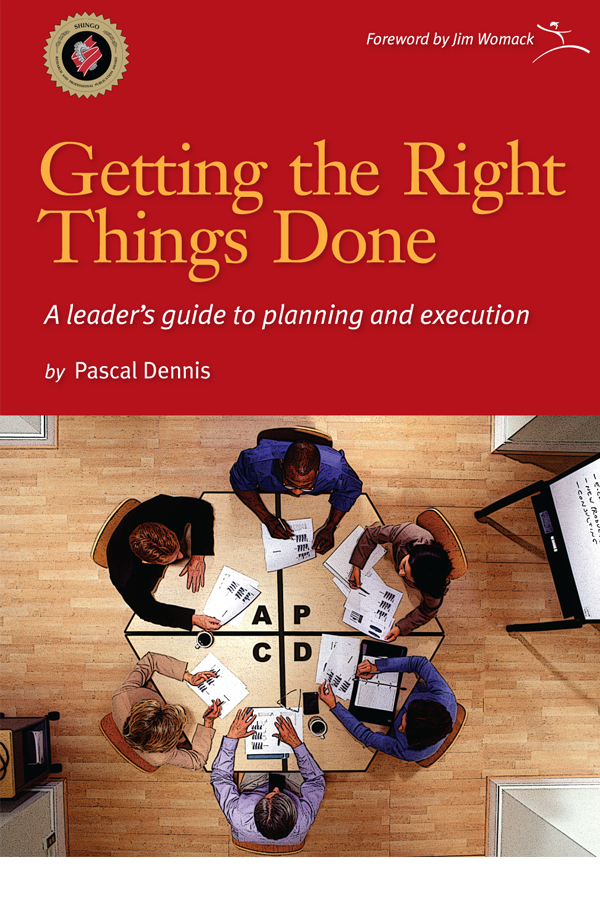
Getting the Right Things Done
Pascal Dennis
Standard Work Templates
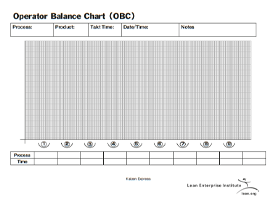
Standard Work Operator Balance Chart (OBC)
- The operator balance chart helps create continuous flow in a multi-step, multi-operator process by distributing operator work elements in relation to takt time.
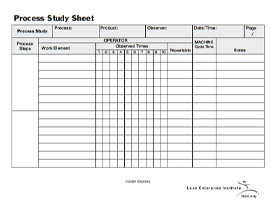
Standard Work Process Study Sheet
- The Process Study Sheet is used to define and record the time for work elements in a process.
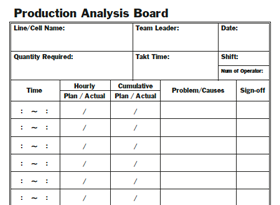
Standard Work Production Analysis Board
- A Production Analysis Board is a display that must be located at the exit of the cell (or the line) to show actual performance compared with planned performance on an hourly basis.
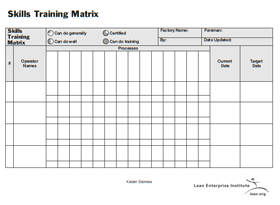
Standard Work Skills Training Matrix
- The Skills Training Matrix shows the required and attained skills of every operator.
- The training schedule also should be shown.
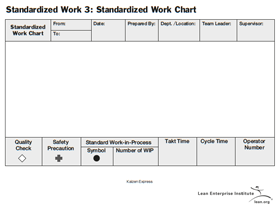
Standardized Work Chart
- The standardized work chart shows operator movement and material location in relation to the machine and overall process layout.
- It should show takt time, work sequence, and standard WIP.
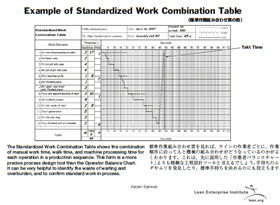
Standardized Work Combination Table
- The standardized work combination table shows the combination of manual work time, walk time, and machine processing time for each operation in a production sequence.
- This form is a more precise process design tool than the Operator Balance Chart.
- It can be very helpful to identify the waste of waiting and overburden, and to confirm standard.
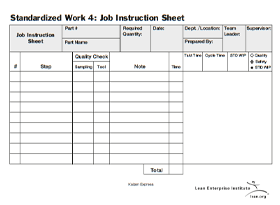
Standardized Work Job Instruction Sheet
- The job instruction sheet is used to train new operations.
- It lists the steps of the job, detailing any special knack that may be required to perform the job safely with utmost quality and efficiency.
- It can also be useful for experienced operators to reconfirm the right operations.
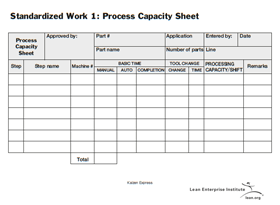
Standardized Work Process Capacity Sheet
- The Process Capacity Chart is used to calculate the capacity of each machine to confirm true capacity and to identify and eliminate bottlenecks.
- Processing capacity per shift will be calculated from the available production time, completion time, and tool-change time (and other factors as necessary) for each work piece.
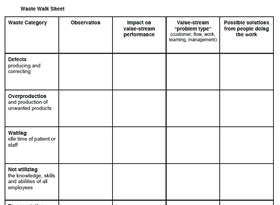
Waste Walk Template (from Perfecting Patient Journeys)
- Taking a “waste walk” is one way to make the waste visible again.
- A waste walk is simply a planned visit to where work is being performed to observe what’s happening and to note the waste. It differs from go-see activities in that you are specifically looking for waste.
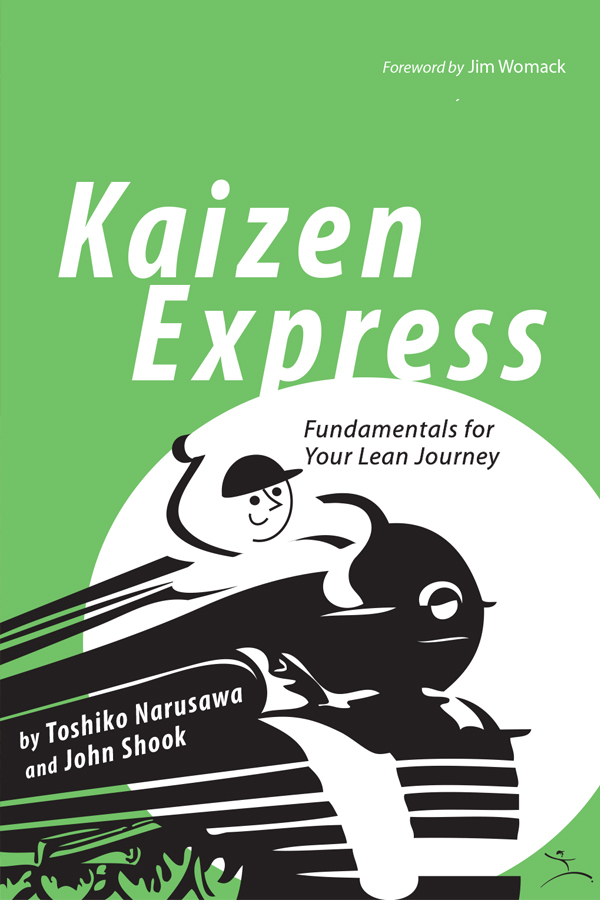
Kaizen Express
Toshiko Narusawa and John Shook
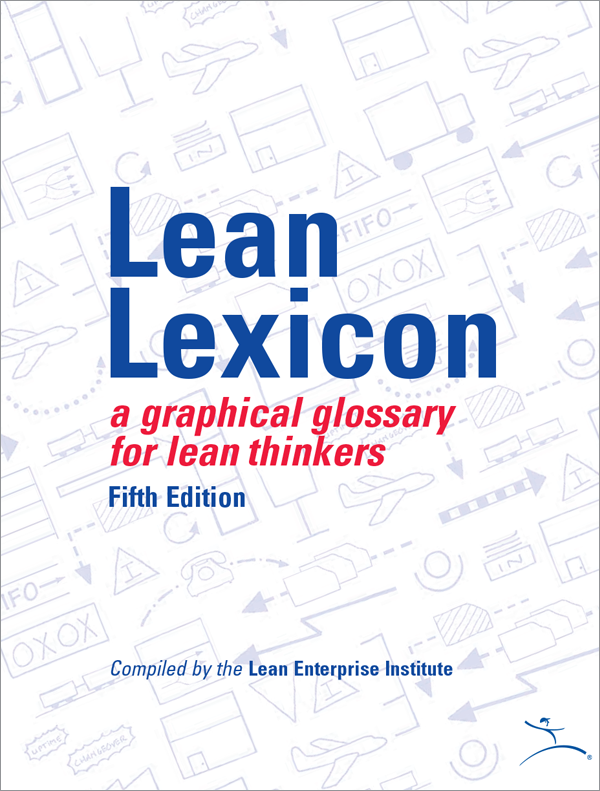
Lean Lexicon 5th Edition
Lean Enterprise Institute
Training Within Industry (TWI) Templates and Downloads
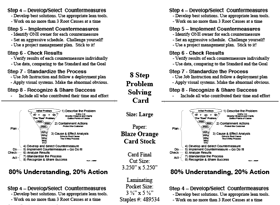
8-step TWI problem solving card - as presented by IBM
- 8-steps to problem solving handy pocket card printable.
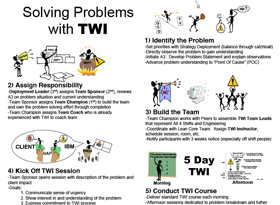
Solving Problems with TWI
- Solving problems with TWI deployment graphic.
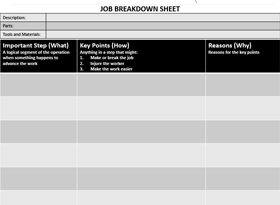
Template of Job Breakdown Sheet
- Job breakdown sheets are created to list the steps and highlight the main factors or key points that go into completing a job.
- It also provides reasons for these key points.
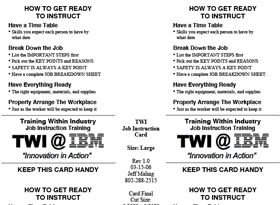
TWI Job Instruction Card
- TWI Job Instruction card in a handy pocket printable.
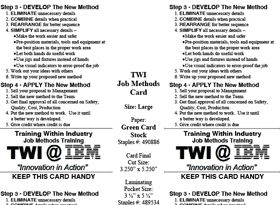
TWI Job Methods Card
- TWI Job Methods Card in a handy pocket printable.
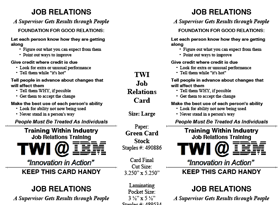
TWI Job Relations Card
- TWI Job Relations Card in a handy pocket printable.
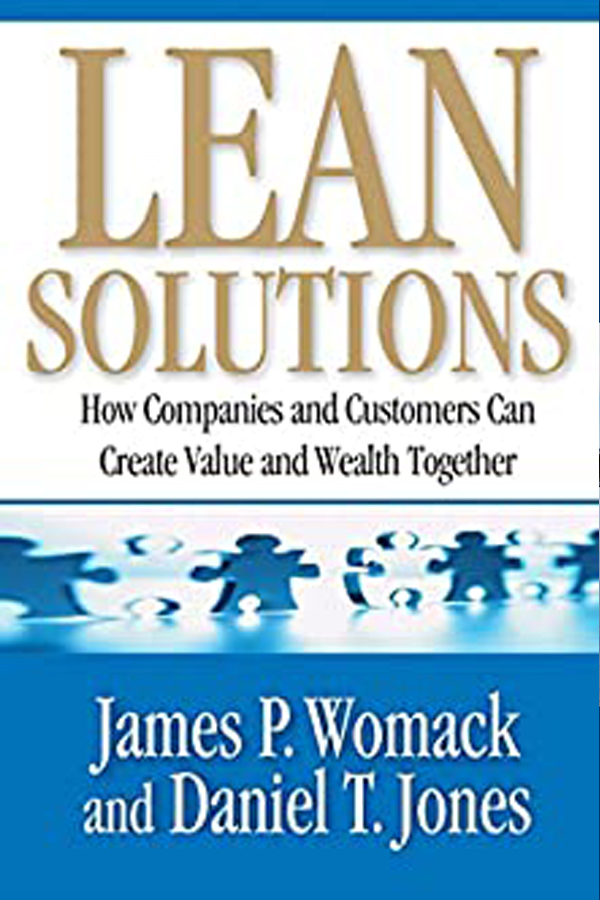
Lean Solutions
James (Jim) Womack, PhD and Dan Jones
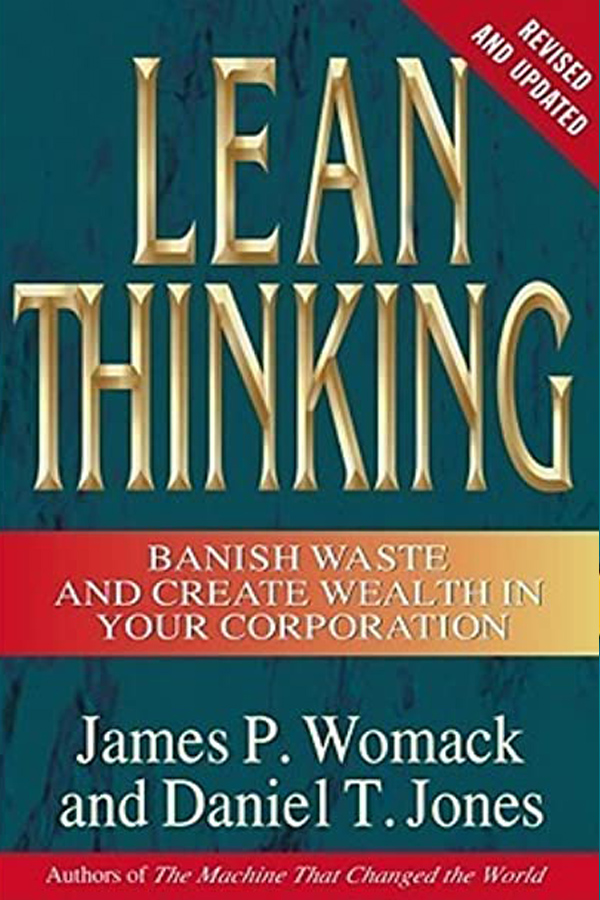
Lean Thinking, 2nd Edition
Project Management Templates
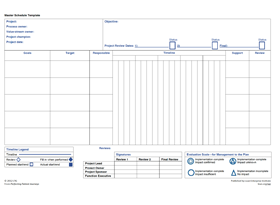
Master Schedule and Action Plan Template for One Goal (from Perfecting Patient Journeys)
- Use this template in your project tracking center so you can track both goals and action items on the same form.
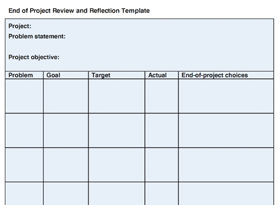
End of Project Review Template (from Perfecting Patient Journeys)
- The following template will help you capture your end-of-project reflections and make decisions about what to do next.
Master Schedule Template (from Perfecting Patient Journeys)
- This template will help you answer this question by letting you include the project goals with space to indicate whether each goal is on track as originally planned and whether the scheduled progress review has taken place.
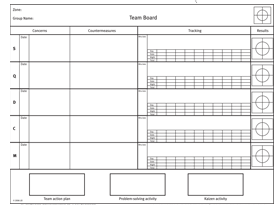
Team Board Form (from Getting the Right Things Done)
- A team board is a window on both routine and improvement work.
- The board on this template addresses both daily production and strategic issues, and is organized according to SQDCM—safety, quality, delivery, cost, and morale.
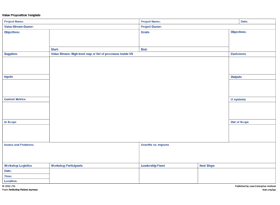
Value Proposition Template (from Perfecting Patient Journeys)
- Align the stakeholders around what will be included in addressing the problem,
- Identify the stakeholders who will be added to the project team and actively engaged in creating the current- and future-state value-stream maps,
- Identify additional stakeholders necessary to drive the implementation of the future state,
- Serve as an agreement—a proof of consensus—on the specific problem to be solved, and with the problem statement serve as authorization for the entire project.
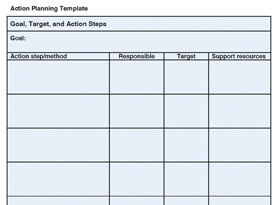
Action Planning Template (from Perfecting Patient Journeys)
- Identify the specific changes that need to be made and translate those changes into clearly stated goals and actions (i.e., the means) to achieve those goals.
- Identify the specific methods and action steps you think will help you achieve the goals. These action steps and targets constitute the action plan to achieve a specific goal.
Value-Stream Mapping Templates

Value-stream Mapping Icons for Excel
- At the request of some of our readers we have posted the most commonly used mapping icons so that they can be downloaded for Excel spreadsheets.
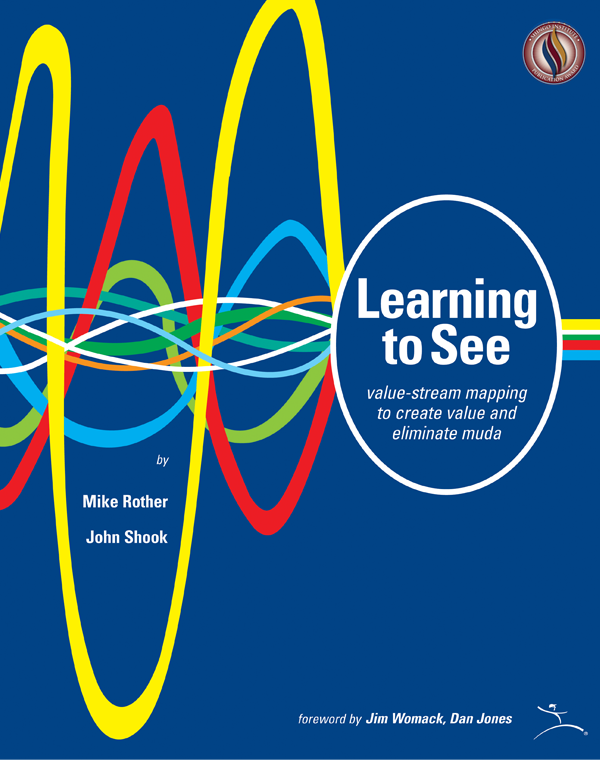
Learning to See
Mike Rother and John Shook
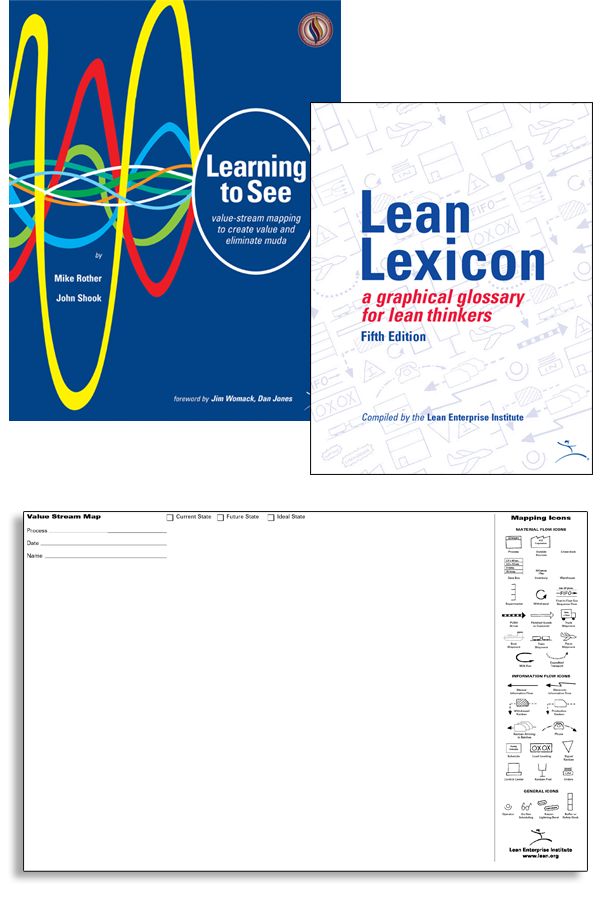
VSM Getting Started Set
Lean Enterprise Institute , Mike Rother and John Shook
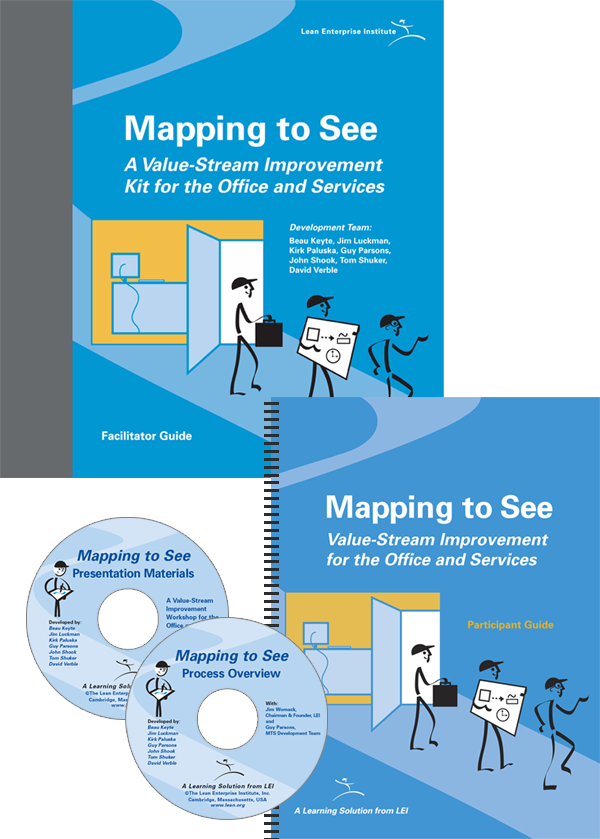
Mapping to See: Value-Stream Improvement Workshop
Beau Keyte , Jim Luckman , Kirk Paluska , Guy Parsons , John Shook , Tom Shuker and David Verble
Improvement Kata / Coaching Kata
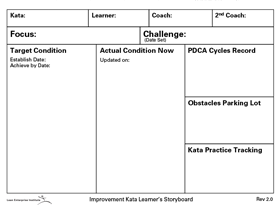
Improvement Kata Learner's Storyboard
Subscribe to get the very best of lean thinking delivered right to your inbox
Privacy overview.
A Lean Approach for Reducing Downtimes in Healthcare: A Case Study
- Conference paper
- First Online: 12 February 2023
- Cite this conference paper
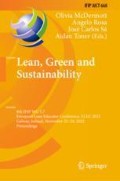
- Stefano Frecassetti ORCID: orcid.org/0000-0002-9649-314X 19 ,
- Matteo Ferrazzi ORCID: orcid.org/0000-0001-9035-0773 19 &
- Alberto Portioli-Staudacher ORCID: orcid.org/0000-0002-9807-1215 19
Part of the book series: IFIP Advances in Information and Communication Technology ((IFIPAICT,volume 668))
Included in the following conference series:
- European Lean Educator Conference
405 Accesses
Lean Management is considered one of the most successful management paradigms for enhancing operational performance in the manufacturing environment. However, it has been applied throughout the years to several sectors and organisational areas, such as service, healthcare, and office departments. After the Covid-19 outbreak, increasing attention has been given to potential performance improvements in healthcare organisations by leveraging Lean. This paper intends to add further knowledge to this field by presenting a case study in a hospital. In this paper, a pilot project is presented carried out in a healthcare organisation. Lean methods were used to improve the operating room performance, particularly by reducing the operating room changeover time. The A3 template was used to drive the project and implement a new procedure using the Single Minute Exchange of Die (SMED) method. With the implementation of the new procedure, the changeover time between two different surgeries in the operating room was significantly reduced, together with a more stable and reliable process.
- Lean thinking
This is a preview of subscription content, log in via an institution to check access.
Access this chapter
- Available as PDF
- Read on any device
- Instant download
- Own it forever
- Available as EPUB and PDF
- Compact, lightweight edition
- Dispatched in 3 to 5 business days
- Free shipping worldwide - see info
- Durable hardcover edition
Tax calculation will be finalised at checkout
Purchases are for personal use only
Institutional subscriptions
Amati, M., et al.: Reducing changeover time between surgeries through lean thinking: an action research project. Front. Med. 9 (2022). https://doi.org/10.3389/fmed.2022.822964
Bharsakade, R.S., Acharya, P., Ganapathy, L., Tiwari, M.K.: A lean approach to healthcare management using multi criteria decision making. Opsearch 58 (3), 610–635 (2021). https://doi.org/10.1007/s12597-020-00490-5
Article Google Scholar
Costa, F., Kassem, B., Staudacher, A.P.: Lean office in a manufacturing company. In: Powell, D.J., Alfnes, E., Holmemo, M.D.Q., Reke, E. (eds.) Learning in the Digital Era. IFIP Advances in Information and Communication Technology, pp. 351–356. Springer, Cham (2021). https://doi.org/10.1007/978-3-030-92934-3_36
Chapter Google Scholar
Costa, F., Kassem, B., Portioli-Staudacher, A.: Lean thinking application in the healthcare sector. In: Powell, D.J., Alfnes, E., Holmemo, M.D.Q., Reke, E. (eds.) Learning in the Digital Era. IFIP Advances in Information and Communication Technology, pp. 357–364. Springer, Cham (2021). https://doi.org/10.1007/978-3-030-92934-3_37
Curatolo, N., Lamouri, S., Huet, J.C., Rieutord, A.: A critical analysis of Lean approach structuring in hospitals. Bus. Process Manag. J. 20 (3), 433–454 (2014)
D’Andreamatteo, A., Iannia, L., Lega, F., Sargiacomo, M.: Lean in healthcare: a comprehensive review. Health Policy 119 (9), 1197–1209 (2015)
Guercini, J., et al.: Application of SMED methodology for the improvement of operations in operating theatres. The case of the Azienda Ospedaliera Universitaria Senese. Mecosan 24 (98), 83–203 (2016). https://doi.org/10.3280/mesa2016-098005
Henrique, D.B., Godinho Filho, M.: A systematic literature review of empirical research in Lean and Six Sigma in healthcare. Total Qual. Manag. Bus. Excell. 31 (3–4), 429–449 (2020)
Henrique, D.B., Filho, M.G., Marodin, G., Jabbour, A.B.L.D.S., Chiappetta Jabbour, C.J.: A framework to assess sustaining continuous improvement in lean healthcare. Int. J. Prod. Res. 59 (10), 2885–2904 (2020)
Holweg, M.: The genealogy of lean production. J. Oper. Manag. 25 (2), 420–437 (2007). https://doi.org/10.1016/j.jom.2006.04.001
Sales-Coll, M., de Castro, R., Hueto-Madrid, J.A.: Improving operating room efficiency using lean management tools. Prod. Plan. Control 1–14 (2021). https://doi.org/10.1080/09537287.2021.1998932
Matos, I.A., Alves, A.C., Tereso, A.P.: Lean principles in an operating room environment: an action research study. J. Health Manag. 18 (2), 239–2577 (2016)
Portioli-Staudacher, A.: Lean healthcare. An experience in Italy. In: Koch, T. (ed.) APMS 2006. ITIFIP, vol. 257, pp. 485–492. Springer, Boston, MA (2008). https://doi.org/10.1007/978-0-387-77249-3_50
Rosa, A., Marolla, G., Lega, F., et al.: Lean adoption in hospitals: the role of contextual factors and introduction strategy. BMC Health Serv. Res. 21 , 889 (2021). https://doi.org/10.1186/s12913-021-06885-4
Rosa, C., Silva, F.J.G., Ferreira, L.P., Campilho, R.D.S.G.: SMED methodology: the reduction of setup times for Steel Wire-Rope assembly lines in the automotive industry. Procedia Manuf. 13 , 1034–1042 (2017)
Shah, R., Ward, P.T.: Lean manufacturing: context, practice bundles, and performance. J. Oper. Manag. 21 (2), 129–149 (2003)
Sunder, M.V., Mahalingam, S., Krishna, M.S.N.: Improving patients’ satisfaction in a mobile hospital using Lean Six Sigma – a design-thinking intervention. Prod. Plan. Control 31 (6), 512–526 (2020)
Torri, M., Kundu, K., Frecassetti, S., Rossini, M.: Implementation of Lean in IT SME company: an Italian case. Int. J. Lean Six Sigma (2021)
Google Scholar
Welsh, I., Lyons, C.M.: Evidence-based care and the case for intuition and tacit knowledge in clinical assessment and decision making in mental health nursing practice: an empirical contribution to the debate. J. Psychiatr. Ment. Health Nurs. 8 (4), 299–305 (2001)
Yin, R.K.: Case Study Research and Applications: Design and Methods, 6th edn. Sage, Los Angeles (2018)
Download references
Author information
Authors and affiliations.
Politecnico di Milano, Department of Management, Economics and Industrial Engineering, Milano, Italy
Stefano Frecassetti, Matteo Ferrazzi & Alberto Portioli-Staudacher
You can also search for this author in PubMed Google Scholar
Corresponding author
Correspondence to Stefano Frecassetti .
Editor information
Editors and affiliations.
University of Galway, Galway, Ireland
Olivia McDermott
LUM University "Giuseppe Degennaro", Casamassima, Italy
Angelo Rosa
Instituto Superior de Engenharia do Porto, Porto, Portugal
José Carlos Sá
Aidan Toner
Rights and permissions
Reprints and permissions
Copyright information
© 2023 IFIP International Federation for Information Processing
About this paper
Cite this paper.
Frecassetti, S., Ferrazzi, M., Portioli-Staudacher, A. (2023). A Lean Approach for Reducing Downtimes in Healthcare: A Case Study. In: McDermott, O., Rosa, A., Sá, J.C., Toner, A. (eds) Lean, Green and Sustainability. ELEC 2022. IFIP Advances in Information and Communication Technology, vol 668. Springer, Cham. https://doi.org/10.1007/978-3-031-25741-4_8
Download citation
DOI : https://doi.org/10.1007/978-3-031-25741-4_8
Published : 12 February 2023
Publisher Name : Springer, Cham
Print ISBN : 978-3-031-25740-7
Online ISBN : 978-3-031-25741-4
eBook Packages : Computer Science Computer Science (R0)
Share this paper
Anyone you share the following link with will be able to read this content:
Sorry, a shareable link is not currently available for this article.
Provided by the Springer Nature SharedIt content-sharing initiative
- Publish with us
Policies and ethics
Societies and partnerships

- Find a journal
- Track your research
- Worldwide standard certification
- Accredited Training Organizations
- LSS Training content
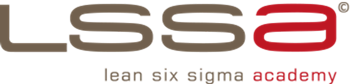
Lean Six Sigma Case Studies
Welcome to the Lean Six Sigma Academy’s Case Studies section! Here, you will find a collection of real-world examples of how companies have successfully implemented the Lean Six Sigma methodology to improve their business operations. Each case study includes an overview of the business challenge that was faced, the approach that was taken, the results that were achieved and feedback from the client on their experience. These case studies showcase the wide range of industries and organizations that have benefited from Lean Six Sigma, and serve as inspiration and guidance for those looking to implement the methodology in their own business.
OE Partners
Orrcon Steel
The toyota production system.
- Guide: A3 Problem Solving
Daniel Croft
Daniel Croft is an experienced continuous improvement manager with a Lean Six Sigma Black Belt and a Bachelor's degree in Business Management. With more than ten years of experience applying his skills across various industries, Daniel specializes in optimizing processes and improving efficiency. His approach combines practical experience with a deep understanding of business fundamentals to drive meaningful change.
- Last Updated: June 13, 2023
- Learn Lean Sigma
Problem-solving is one of the key tools a successful business needs to structure improvements and one I have been using to solve problems in a structured way in my career are Continental AG and other businesses over the years. When there is a problem in business that is leading to increased costs, waste , quality issues, etc., it is necessary to address these problems. A3 structured problem solving is a Lean Six Sigma methodology that has been designed and developed to support continuous improvement and solve complex business problems in a logical and structured process.
The guide will give you a full understanding of what A3 Problem solving is and a breakdown of all the steps of how to apply it within your business with an example of where I have made improvements with it previously.
Table of Contents
Importance of a3 in lean management.
The A3 problem-solving method is a key tool in Lean Six Sigma and continuous improvement in business, and in my experience, it is often the standard approach all improvement activities must follow and is particularly popular in the automotive industry. This is because of the following:
Focus on Root Causes : Rather than applying a quick fix to a problem or jumping to conclusions and solutionizing, A3 requires gaining a deep understanding of the root causes of the problem. By addressing these root causes, the chances of recurrence is reduced.
Standardization : With a consistent format, the A3 process ensures that problems are approached in a standardized way, regardless of the team or department. This standardization creates a common language and understanding across the organization and ensures all problems are addressed to the same standard and approach.
Team Involvement : An A3 isn’t an individual process. It requires a cross-functional team to work together on problem-solving, ensuring that a range of perspectives and expertise is considered. This collective approach builds a stronger understanding of the problem and ensures that solutions are well-rounded and robust.
Visual Storytelling : The A3 report serves as a visual storyboard, making it easier for stakeholders at all levels to understand the problem, the analysis, and the countermeasures. This visualization enhances communication and drives alignment.
The 6 Steps of A3 Problem Solving (With Real Example)
The A3 problem-solving process can initially seem difficult if you have never done one before and particularly if you have never been a team member in one. To help you with this we will break down the 6 steps into manageable activities, followed by a real-life example to help you apply this method within your business.
As a side note, the A3 problem-solving process was actually one of the first Lean Six Sigma tools I learned to use three weeks into my continuous improvement career after being thrown into the deep end due to resource availability, so I can understand how difficult it can be to understand.
Step 1: Describe the problem
Problem description.
The problem description is an important first step in the process as it ensures a common understanding with the team of what the issue is that needs to be addressed. This can be done by using a technique called the 5W1H Is/Is Not method to help gain a clear understanding of the problem.
To understand the 5W1H Is/Is Not the Process, check out our guide for details of that technique. However, in short, it’s about asking key questions about the problem, for example, “What IS the problem?” and “What IS NOT the problem?”
Let’s say you have been asked to look into a problem where “Machine downtime on the automotive assembly line has increased by 30% over the past three months, leading to production delays and increased costs.”
An example of a 5W1H Is/Is Not on this may result in the following output:
Based on this we can create a clear problem description as the focus of the project that give the team a clear and common understanding of the issue looking to be resolved in the next steps of the process. The problem description could then be written as:
“Over the past three months, machine downtime on Automotive Assembly Line No.3 has increased by 30%. This has predominantly affected the assembly line workers and leads, leading to production delays and higher labor costs. “
Current Condition
Next is demonstrating the current condition and demonstrating the impact on the business. This can often be done with data and charts to back up the problem that might show trends or changes in outputs.
This might look something like the below and demonstrate a good baseline for confirming the improvement at the end of the A3
Containment Actions
Next is containment actions. Since you have identified a problem, there is likely an impact on the business or the customer. As a team, you should consider what can be done to limit or eliminate this problem in the short term. Remember this is just a containment action and should not be seen as a long-term fix.
In our situation we decided to “Implement temporary overtime shifts to meet production goals, leading to an increase in labor costs.”
At this stage, the A3 should look similar to the one below; you can use charts and graphics to represent the current state as well if they fit within the limit area. Remember, we must include the content of the A3 within the 1-page A3 Document.
Step 2: Set the A3 Goals
The next step of the A3 is to, as a team, set the goal for the project. As we have a clear understanding of the current condition of the problem, we can use that as our baseline for improvement and set a realistic target for improvement.
A suggested method for setting the Target condition would be to use the SMART Target method.
If you are not familiar with SMART Targets , read our guide; it will cover the topic in much more detail. In short, a SMART target creates a goal statement that is specific, measurable, achievable, relevant and time-bound.
By doing this you make it very clear what the goal of the project is, how it will be measured, it is something that can be achived, relevant to the needs of the business and has a deadline for when results need to be seen.
For our A3 we decided that the goal would be “Our goal is to achieve at least a 20% reduction in machine downtime on Automotive Assembly Line No.3, lowering it from 90 minutes to no more than 72 minutes per day per machine, within the next 60 days. This reduction is crucial for increasing productivity and reducing labor costs, aligning with our overall business objectives.”
I also recommend using charts in this section to visualize the benefit or improvement to ensure you have stakeholder and sponsor support. Visuals are much easier and faster for people to understand.
At this point, your A3 might look something like the one below, with the first 1/4 or section complete. The next step is to move on to the root cause analysis to get to the root of the problem and ensure the improvement does not focus on addressing the symptoms of the problem.
Step 3: Root Cause Analysis
Root cause analysis is the next step in the process, often referred to as gap analysis, as this step focuses on how to get to the goal condition from the current condition.
Tip: If at this point you find the team going off-topic and focusing on other issues, Ask the question, “Is this preventing us from hitting our goal statement?” I have found this very useful for keeping on track in my time as an A3 facilitator.
For root cause analysis, a couple of key tools are usually used: a fishbone diagram and a five-why Analysis . Again, we won’t go into the full details of these tools within this guide, as they have been covered in extensive detail in their own guides.
But the aim at this point is as a team, to brainstorm what is preventing us from achieving our target condition. This is done by allowing all members of the team to input the reasons they think it is not being achieved. These inputs are often written on sticky notes and placed on the fishbone diagram. Following this, you may have results similar to the ones below. Note: it is important that the inputs are specific so they can be understood. e.g. “Calibration” alone is not specific to how it’s causing the problem; specify it with “Calibration: Inaccurate measurements affecting machine settings.”
After the fishbone diagram has been populated and the team has exhausted all ideas, the team should then vote on the most likely cause to explore with a 5 Whys analysis. This is done because, due to resource limitations, it is unlikely all of the suggestions can be explored and actioned.
In this situation the team decided the “lack of preventative machines: machines not being serviced regularly” was the cause of increased downtime. This was explored with the 5 Whys to get to the root cause of why Assembly line 3 did not have preventative maintenance implemented.
The result of this root cause analysis can be seen below, and you may end up with more ideas on the fishbone, as generally there are a lot of ideas generated by a diverse team during brainstorming.
Step 4: Solutions and Corrective Actions
Now that we understand what the root cause of the problem is, we need to address it with solutions and corrective actions. Again, as a team, consider the root cause of the problem and discuss what actions need to be taken by the team, who will do them, and when they will be done. The result should be an action plan, for example, like the one below:
This action plan needs to be carried out and implemented.
The result of this section will likely just be an action list and look like the below section.
Step 5: Validate Solution and Standardize
Within step 5 it is time to collect data to validate and confirm the actions that have been implement resulted in solving the problem and met the target state of the problem. This is done by continuing to collect data that demonstrated the problem in the baseline to see if the problem is being reduced.
For example, below, the project team continued to collect Assembly Line 3 downtime data on a weekly basis. Initially, there was a steady reduction, likely due to the focus of the project on the problem, which had some impact. However, once the majority of the action was implemented, a huge drop in product downtime was seen, exceeding the target. This showed the actions has been successful
If, in the validation stage, you find that the improvement required is not being made, you should go back to step 3 and reconsult the root cause analysis with the team, pick another area to focus on, and create an action plan for that following the same steps.
Step 6: Preventive Actions and Lessons Learned
In step 6 after the confirmation of project sucess you should look at preventive actions and lessons learned to be shared from this project:
- Preventive Action: The new preventive maintenance schedule will be standardized across all assembly lines. This will prevent other lines having similar issues and make further improvements
- Lessons Learned: A formal review will be conducted to document the process, including challenges faced and how they were overcome, which will then be archived for future reference.
In our project, this looked like the below and will be used as a reference point in the future for similar issues.
And that is the successful completion of a structured A3 problem-solving technique.
The complete A3 looks like the below image. Yours may slightly differ as the problem and information vary between projects.
Downloadable A3 Reporting Template
To support you with your A3 problem solving, you can download our free A3 problem solving report from the template section of the website.
Problem-solving is important in businesses, specifically when faced with increased costs or quality issues. A3 Structured Problem Solving, rooted in Lean Six Sigma, addresses complex business challenges systematically.
Originally from Toyota’s lean methodology, A3, named after the 11″x17″ paper size, visually maps problem-solving processes. This method ensures concise communication and focuses on crucial details, as illustrated by the provided example.
Emphasized in Lean Management, A3 stresses understanding root causes, standardization across teams, team collaboration, and visual representation for clarity. This tool is not only a guide to understanding the issue but is a standardized format ensuring robust solutions. Particularly for novices, breaking down its six steps, from problem description to setting A3 goals and root cause analysis, provides clarity. Visual aids further enhance comprehension and alignment across stakeholders.
- Sobek II, D.K. and Jimmerson, C., 2004. A3 reports: tool for process improvement. In IIE Annual Conference. Proceedings (p. 1). Institute of Industrial and Systems Engineers (IISE).
- Matthews, D.D., 2018. The A3 workbook: unlock your problem-solving mind . CRC Press.
Q: What is A3 problem solving?
A: A3 problem solving is a structured approach used to tackle complex problems and find effective solutions. It gets its name from the A3-sized paper that is typically used to document the problem-solving process.
Q: What are the key benefits of using A3 problem solving?
A: A3 problem solving provides several benefits, including improved communication, enhanced teamwork, better problem understanding, increased problem-solving effectiveness, and the development of a culture of continuous improvement.
Q: How does A3 problem solving differ from other problem-solving methods?
A: A3 problem solving emphasizes a systematic and structured approach, focusing on problem understanding, root cause analysis, and the development and implementation of countermeasures. It promotes a holistic view of the problem and encourages collaboration and learning throughout the process.
Q: What are the main steps in the A3 problem-solving process?
A: The A3 problem-solving process typically involves the following steps: problem identification and description, current condition analysis, goal setting, root cause analysis, countermeasure development, implementation planning, action plan execution, and follow-up and evaluation.
Q: What is the purpose of the problem identification and description step?
A: The problem identification and description step is crucial for clarifying the problem, its impact, and the desired outcome. It helps establish a common understanding among the team members and ensures everyone is working towards the same goal.
Daniel Croft is a seasoned continuous improvement manager with a Black Belt in Lean Six Sigma. With over 10 years of real-world application experience across diverse sectors, Daniel has a passion for optimizing processes and fostering a culture of efficiency. He's not just a practitioner but also an avid learner, constantly seeking to expand his knowledge. Outside of his professional life, Daniel has a keen Investing, statistics and knowledge-sharing, which led him to create the website learnleansigma.com, a platform dedicated to Lean Six Sigma and process improvement insights.
Free Lean Six Sigma Templates
Improve your Lean Six Sigma projects with our free templates. They're designed to make implementation and management easier, helping you achieve better results.
Other Guides
To read this content please select one of the options below:
Please note you do not have access to teaching notes, lean monitoring: action research in manufacturing.
International Journal of Lean Six Sigma
ISSN : 2040-4166
Article publication date: 4 September 2023
Issue publication date: 3 November 2023
This study aims to study the implementation of lean thinking at the strategic level of an Italian manufacturing company. Companies implementing continuous improvement (CI) projects in their production processes often take the monitoring phase for granted. This research deploys an A3 lean thinking project in the monitoring phase of strategic KPIs upon completion of several ongoing improvement projects.
Design/methodology/approach
The research methodology is action research aiming at disseminating the problems that the company is facing. The study relies on the lean action plan developed by Womack and Jones (2003): Planning for lean and Lean action. Lean planning consists of the following steps: find a change agent; get the knowledge; find a lever. Lean action uses the A3 lean approach.
The company reached high-performance improvements due to the proposed lean action plan.
Research limitations/implications
This study contributes by presenting a lean action plan in the monitoring phase, highlighting the importance of the lean thinking-monitoring continuum in reducing time waste for faster diagnosis and using action research to analyze and instill reflective learning.
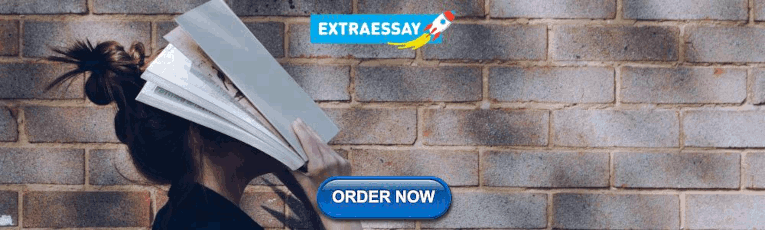
Originality/value
The research relies on the A3 methodology to showcase the benefits that a mature paradigm, often coined to production, still has unexplored potentials.
- KPI generation
- Action research
- Continuous improvement
Kassem, B. , Rossini, M. , Costa, F. and Portioli-Staudacher, A. (2023), "Lean monitoring: action research in manufacturing", International Journal of Lean Six Sigma , Vol. 14 No. 6, pp. 1280-1296. https://doi.org/10.1108/IJLSS-06-2022-0124
Emerald Publishing Limited
Copyright © 2023, Emerald Publishing Limited
Related articles
We’re listening — tell us what you think, something didn’t work….
Report bugs here
All feedback is valuable
Please share your general feedback
Join us on our journey
Platform update page.
Visit emeraldpublishing.com/platformupdate to discover the latest news and updates
Questions & More Information
Answers to the most commonly asked questions here
.css-s5s6ko{margin-right:42px;color:#F5F4F3;}@media (max-width: 1120px){.css-s5s6ko{margin-right:12px;}} Join us: Learn how to build a trusted AI strategy to support your company's intelligent transformation, featuring Forrester .css-1ixh9fn{display:inline-block;}@media (max-width: 480px){.css-1ixh9fn{display:block;margin-top:12px;}} .css-1uaoevr-heading-6{font-size:14px;line-height:24px;font-weight:500;-webkit-text-decoration:underline;text-decoration:underline;color:#F5F4F3;}.css-1uaoevr-heading-6:hover{color:#F5F4F3;} .css-ora5nu-heading-6{display:-webkit-box;display:-webkit-flex;display:-ms-flexbox;display:flex;-webkit-align-items:center;-webkit-box-align:center;-ms-flex-align:center;align-items:center;-webkit-box-pack:start;-ms-flex-pack:start;-webkit-justify-content:flex-start;justify-content:flex-start;color:#0D0E10;-webkit-transition:all 0.3s;transition:all 0.3s;position:relative;font-size:16px;line-height:28px;padding:0;font-size:14px;line-height:24px;font-weight:500;-webkit-text-decoration:underline;text-decoration:underline;color:#F5F4F3;}.css-ora5nu-heading-6:hover{border-bottom:0;color:#CD4848;}.css-ora5nu-heading-6:hover path{fill:#CD4848;}.css-ora5nu-heading-6:hover div{border-color:#CD4848;}.css-ora5nu-heading-6:hover div:before{border-left-color:#CD4848;}.css-ora5nu-heading-6:active{border-bottom:0;background-color:#EBE8E8;color:#0D0E10;}.css-ora5nu-heading-6:active path{fill:#0D0E10;}.css-ora5nu-heading-6:active div{border-color:#0D0E10;}.css-ora5nu-heading-6:active div:before{border-left-color:#0D0E10;}.css-ora5nu-heading-6:hover{color:#F5F4F3;} Register now .css-1k6cidy{width:11px;height:11px;margin-left:8px;}.css-1k6cidy path{fill:currentColor;}
- Create an action plan that drives resul ...
Create an action plan that drives results
An action plan outlines precisely how you’re planning to accomplish your goals. It’s the perfect way to approach goals systematically and keep your team on target. In this article, we will cover how to create an action plan in six steps and how to implement it successfully. Plus, learn more about the differences between action plans, project plans, and to-do lists.
It can feel good to make goals. After all, you’re defining what you want to accomplish. But goals won’t do much without clear action steps. An action plan is a popular project management technique that lists your action steps so you know exactly how you’re going to accomplish your goals.
We’re going to show you how to create this clear roadmap step by step and other tools you should utilize to get the most out of your action plan. Let’s dive in.
What is an action plan?
An action plan is a list of tasks or steps you need to complete to achieve your goals. An effective action plan works like a management plan for your company’s initiatives, outlining the steps you need to take to make these larger goals a success. Once you go through the goal-setting process, create an action plan with specific tasks and timeframes to reach each goal.
Who needs an action plan?
An action plan is useful for anyone who needs a step-by-step planning process. When you create an action plan, you detail exactly what actions you'll take to accomplish your project goals. These plans can help you organize your to-dos and ensure you have the necessary information and resources to accomplish your goals.
But you can create action plans for more than just strategic planning. Use this tool to reach any specific goals in a systematic way. Try setting up:
Business action plan
Marketing action plan
Corrective action plan
Sales action plan
Project action plan
Personal development action plan
Regardless of the type of action plan you create, make sure you create it in task management software . That way, you can easily share action items and timelines with your team to track progress. Instead of manual status updates and unclear deliverables, your team has one central source of truth for everything they need to do in order to hit their goals.
Now let’s get into how you can create an action plan that increases your team’s efficiency and accountability.
6 steps to create an action plan
Step 1: set a smart goal.
When it comes to setting goals, clarity is the single most important quality. With the SMART goal method, your goal is clearly defined and attainable. Set specific, measurable, achievable, realistic, and time-bound goals to benefit from this tactic.
For example, your goal could be to deliver your current project (measurable) in four months (time-bound) without overspending (specific). Assuming this goal is both achievable and realistic based on your available resources, it’s a great SMART goal to set for yourself.
Step 2: Identify tasks
Now that your goal is clearly defined and written down, you’ll want to identify the steps you have to take to reach it. Identify all of the tasks that you and your team need to complete to reach milestones and, eventually, the main objective.
Here are a few action plan examples with tasks for different kinds of goals:
Goal: Expand team from seven to nine team members by June.
Meet with Human Resources to discuss the recruitment campaign.
Create a template project to track candidates.
Schedule three interviews per week.
Goal: Select and onboard new work management software to the entire company by the end of Q2.
Apply for the budget.
Create a roll-out plan for Q2.
Schedule training for team members.
Goal: Host 5k charity run in May to raise $15,000 for the local food bank.
Find volunteers and determine responsibilities
Prepare marketing materials and PR plans
Secure sponsors
Step 3: Allocate resources
Once you’ve outlined all of your tasks, you can allocate resources like team members, project budget, or necessary equipment. Whether it’s assigning team members to certain tasks, applying for a budget, or gathering helpful tools—now is the time to plan and prepare.
Sometimes, you can’t allocate all of your resources before you put your action plan in motion. Perhaps you have to apply for funding first or need executive approval before you can move on with a task. In that case, make the resource an action item in your plan so you can take care of it later.
Step 4: Prioritize tasks
When your team is clear on their priorities, they know what work to do first and what work they can reschedule if necessary. No action plan is set in stone, so the best way to empower your team is to let them know what tasks have a high priority and which ones are a bit more flexible.
To make this clear, sort all of your action items by priority and sequence:
Priority: Important and less important tasks.
Sequence: Order in which tasks have to be completed so others can start.
When you’re organizing and prioritizing your action items , you’ll notice that some action items are dependent on others. In other words, one task can’t begin until the previous task is completed. Highlight these dependencies and factor the sequence into your prioritization. This reduces bottlenecks , removing obstacles that would make a less important action item delay a high-priority item.
Step 5: Set deadlines and milestones
When your team knows what they're working towards, they have the context to effectively prioritize work and the motivation to get great work done. Team members tend to be more motivated when they directly understand how their work is contributing to larger goals.
To engage your teammates from the get go, assign deadlines to all action items and define milestones . Milestones mark specific points along your project timeline that identify when activities have been completed or when a new phase starts
Create a timeline or Gantt chart to get a better overview of your prioritized tasks, milestones, and deadlines. Your timeline also serves as a visual way to track the start and end dates of every task in your action plan. You can use it as a baseline to make sure your team stays on track.
Step 6: Monitor and revise your action plan
Your ability to stay on top of and adapt to changes is what makes you a great project manager. It’s crucial that you monitor your team’s progress and revise the plan when necessary.
Luckily, your action plan isn’t set in stone. The best way to track potentially changing priorities or deadlines is to use a dynamic tool like a work management software . That way, you can update to-dos and dependencies in real time, keep your team on the same page, and your action plan moving.
Action plan vs. plan B vs. project plan vs. to-do list
So how exactly does an action plan differ from all these other plans and lists? To clear this up once and for all, we’re going to explain what these plans are and when to use which plan to maximize your team’s efforts.
Action plan vs. plan B
You may have heard the terms action plan and plan B used interchangeably. But in fact, an action plan and plan B are two completely different types of plans. Here’s how to tell them apart:
Your action plan outlines actions in much detail so you and your team know exactly what steps to take to reach your goal.
A plan B is a secondary action plan, an alternative strategy, that your team can apply if your original plan fails. Whether that’s because of an internal issue or an external factor—having a plan B is a great way to be prepared for the worst case scenario.
Action plan vs. project plan
A project plan is a bit more complicated than an action plan. Project plans are blueprints of the key elements your team needs to accomplish to successfully achieve your project goals. A project plan includes seven elements:
Goals and project objectives
Success metrics
Stakeholders and roles
Scope and budget
Milestones and deliverables
Timeline and schedule
Communication plan
Once you’ve created a project plan, use an action plan to outline and document how your team will execute your tasks and hit your goals. This will ensure that everyone on your team knows what their responsibilities are and what to get done by when.
Action plan vs. to-do list
A to-do list is typically used to write down single tasks that don’t necessarily lead to one common goal. To-do lists can change daily and are much less organized than action plans. An action plan will follow specific steps and include tasks that all lead to the completion of a common goal.
How to implement your action plan successfully
You know how to create an action plan, but in order to implement it successfully, you need to use the right tools and use them correctly. Here are our top five tips to ensure your action plan is effective:
Use task management software
Streamline your action plan by keeping all of your tasks and timelines in one central source of truth. Task management software, like Asana , is perfect for your action plan because it allows you to keep track of pending tasks, declare task ownership, assign dependencies, and connect with your team in real time or asynchronously .
Use or create templates
Create or use a template that lists all the action items with notes, status, priority, and ownership. When you create a template that fits your project type, you can reuse it time and time again.
Set up real-time alerts and assign dependencies
Make sure all action items are time-bound and that you assign dependencies. That way, your team can react when an item is ready for them and easily track what other items depend on theirs.
Check action items off as you complete them
When action items are completed, check them off! Make sure it’s visible to everyone and happens in real time so the person responsible for the next action item can start their work as soon as possible.
Discuss late or pending tasks
If you run into issues or delays, talk to your team to uncover potential bottlenecks and find solutions that keep the action plan on track. You can add notes directly into your action plan or set up calls to discuss more complex issues.
Ready, set, action plan
Like Benjamin Franklin once said: “If you fail to plan, you are planning to fail.” Creating an action plan helps you stay focused, on track, and brings your goals to life.
Plan to succeed with a structured action plan and helpful tools like Asana’s task management software. Connect and align with your team in a central source of truth while staying flexible enough to revise your action plan when necessary.
Related resources
Unmanaged business goals don’t work. Here’s what does.
How Asana uses work management to effectively manage goals
Beat thrash for good: 4 organizational planning challenges and solutions
Use critical success factors to support your strategic plan
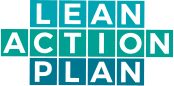
ZBIÓR LEAN CASE STUDY
Case study 211 analityka rentowności sprzedaży na allegro .
Ocena zyskowności/straty na poszczególnych produktach w sprzedaży.
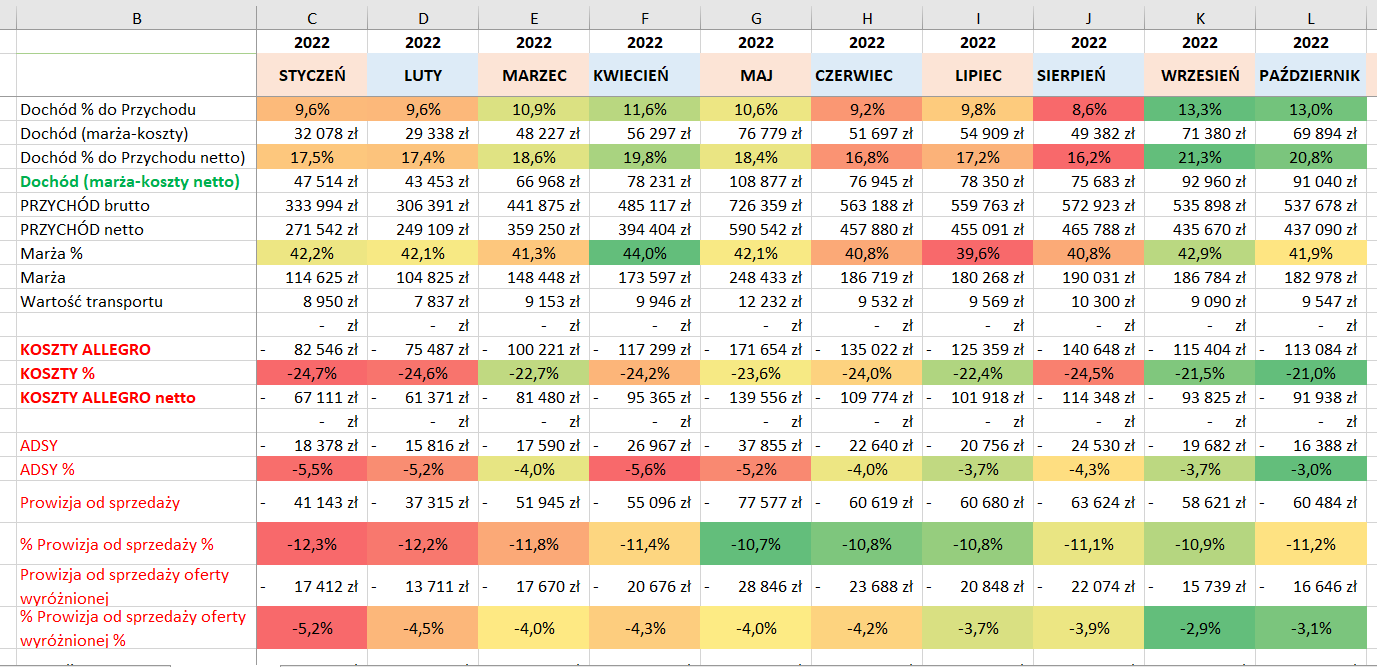
CASE STUDY 9 Diagnoza – branża stalowa
Uwolnienie przestrzeni na hali produkcyjnej, skrócenie całkowitego czasu realizacji zlecenia oraz wskazanie priorytetowych obszarów do optymalizacji.
CASE STUDY 53 Diagnoza – branża produkcji okien
Analiza efektywności procesów produkcyjnych, określenie możliwości obniżenia poziomu zapasów oraz poprawa planowania produkcji.
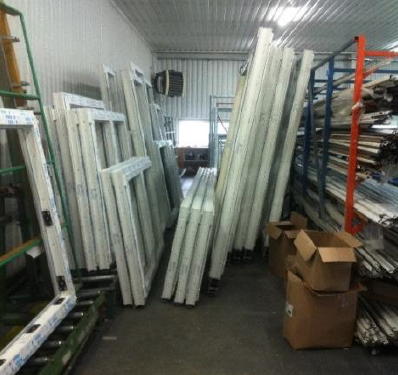
CASE STUDY 7 Mapowanie Strumienia Wartości
Optymalizacja oszczędności w grupie elementów wchodzących w skład głównej rodziny produktowej. Zakładany 150% wzrost popytu w nadchodzących 5 latach.
CASE STUDY 25 Opracowanie Layout’u
Opracowanie Layoutu stanu obecnego w formie *.cad.
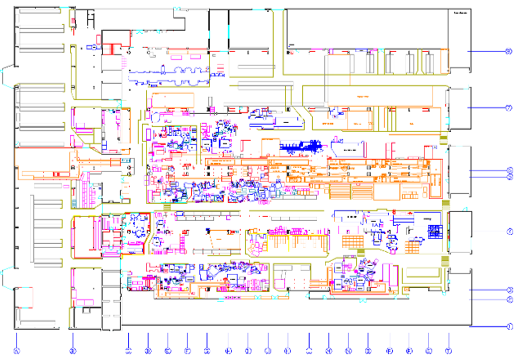
CASE STUDY 202 Narzędzie do planowania zakupów
Analiza sprzedaży, estymacja sprzedaży, analiza trendów, plan sprzedaży, składanie zamówień i generowanie zamówień.
CASE STUDY 92 Analiza przepływu materiału
Analiza przepływu materiału na hali produkcyjnej oraz propozycja przyszłego ustawienia maszyn, zmniejszenie nadmiernego transportu.
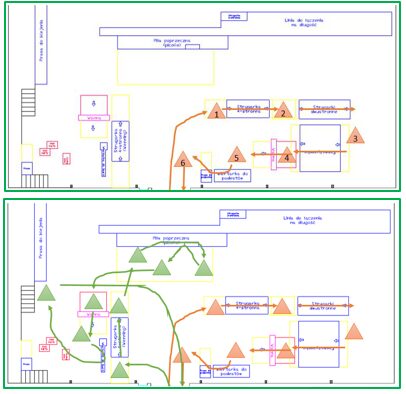
CASE STUDY 18 Gniazdo produkcyjne
W wyniku mapowania strumienia wartości rodziny produktów stanowiącej 11% całego wolumenu produkcji, opracowano propozycję ciągłego przepływu między trzema procesami. Pierwotnie procesy odbywały się w trzech oddalonych od siebie działach, co wymuszało produkcję w partiach oraz nadmierny transport.
CASE STUDY 201 Zarządzanie reklamami na Amazon ADS
Automatyzacja zarządzania płatnymi reklamami na Amazon ADS.
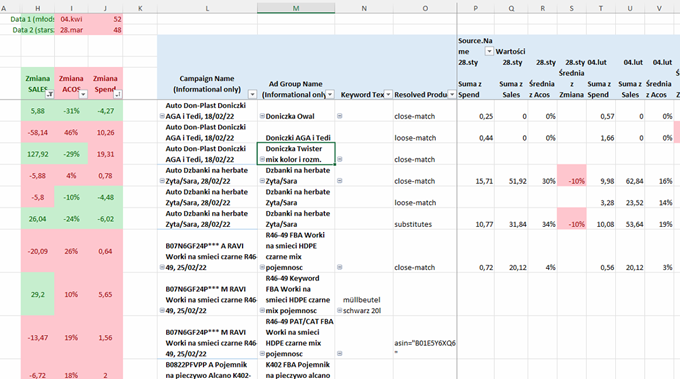
CASE STUDY 8 5S na spawalni
Na hali znajduje się 15 kabin spawalniczych, w których pracują spawacze na pierwszej i drugiej zmianie. Każda kabina ma swoje wyposażenie w zależności od wykonywanego detalu. Podczas wykonywania badań migawkowych wykryto duży udział czynności zbędnych – głównie szukania narzędzi.
CASE STUDY 111 Standaryzacja pracy
Opracowanie optymalnego sposobu wykonywania operacji, podniesienie wydajności, eliminacja błędów, redukcja poziomu braków.
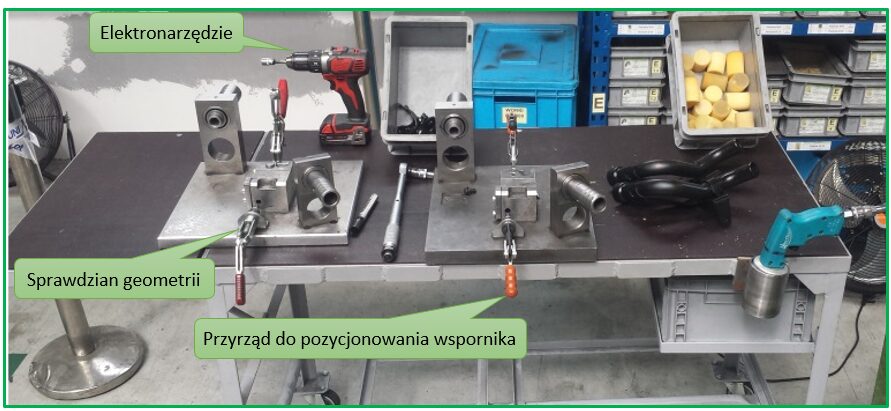
CASE STUDY 31 FIFO – branża lotnicza
Eliminacja nadmiernego planowania poszczególnych obszarów, likwidacja ciągłego nadawania priorytetów, zmniejszenie nadprodukcji, wyrównanie Lead Time (czasu realizacji zleceń).
CASE STUDY 106 Tablica FIFO
Zapewnienie zachowania zasady FIFO (pierwsze weszło, pierwsze wyszło), eliminacja możliwości popełnienia błędu przy 40 różnych rodzajach rur, eliminacja potencjalnych reklamacji, ułatwienie identyfikacji rur.
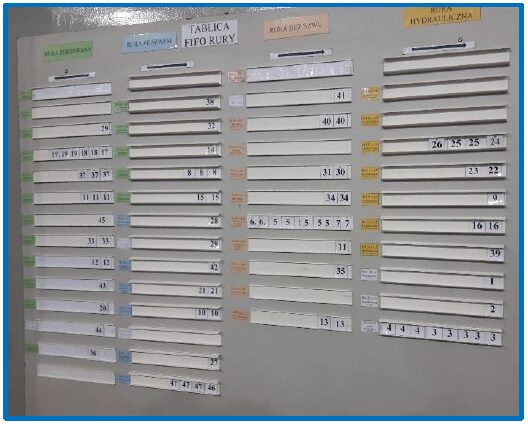
CASE STUDY 23 SMED – branża spożywcza
Zwiększenie dostępności maszyn do produkcji, podniesienie wydajności w środowisku wysokiej sezonowości, opracowanie planu na skrócenie procesu przezbrojenia.
CASE STUDY 52 SMED – drukarnia
Podniesienie wydajności, zwiększenie dostępności urządzeń do produkcji, zmniejszenie kosztów przezbrojenia, stabilizacja czasu przezbrojenia na potrzeby procesu planowania produkcji.
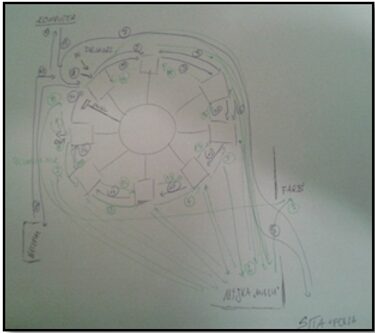
CASE STUDY 13 Kanban
Zapewnienie 100% dostępności dobrych komponentów, zagwarantowanie ciągłości procesu, brak angażowania pracowników magazynu do procesu, eliminacja nadmiernej komunikacji na linii Pakowanie – Magazyn.
CASE STUDY 81 Planowanie – analiza obciążeń stanowisk
Określenie pracochłonności oraz kosztów niestandardowych i niepowtarzających się zleceń.
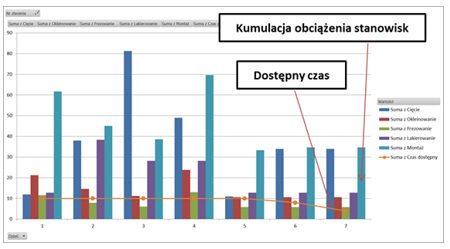
CASE STUDY 204 Planowanie wysyłek na FBA (Fulfilment by Amazon)
Analiza procesu sprzedaży pod kątem sprzedaży detalicznej i hurtowej.
CASE STUDY 83 Analiza sprzedaży
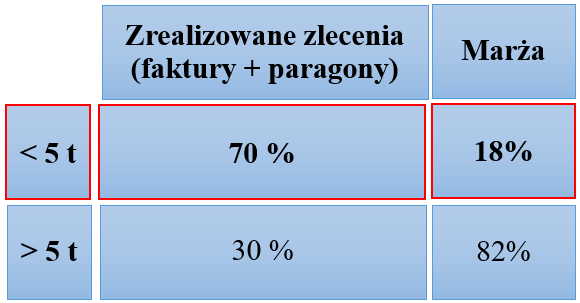
CASE STUDY 125 Capacity – planowanie zdolności produkcji
Określenie zdolności produkcyjnych poszczególnych maszyn i urządzeń
CASE STUDY 107 Gniazdo produkcyjne – tokarki
Wdrożenie gniazd produkcyjnych do procesu tłoczenia. Wzrost efektywności produkcji dla kluczowych rodzin produktów.
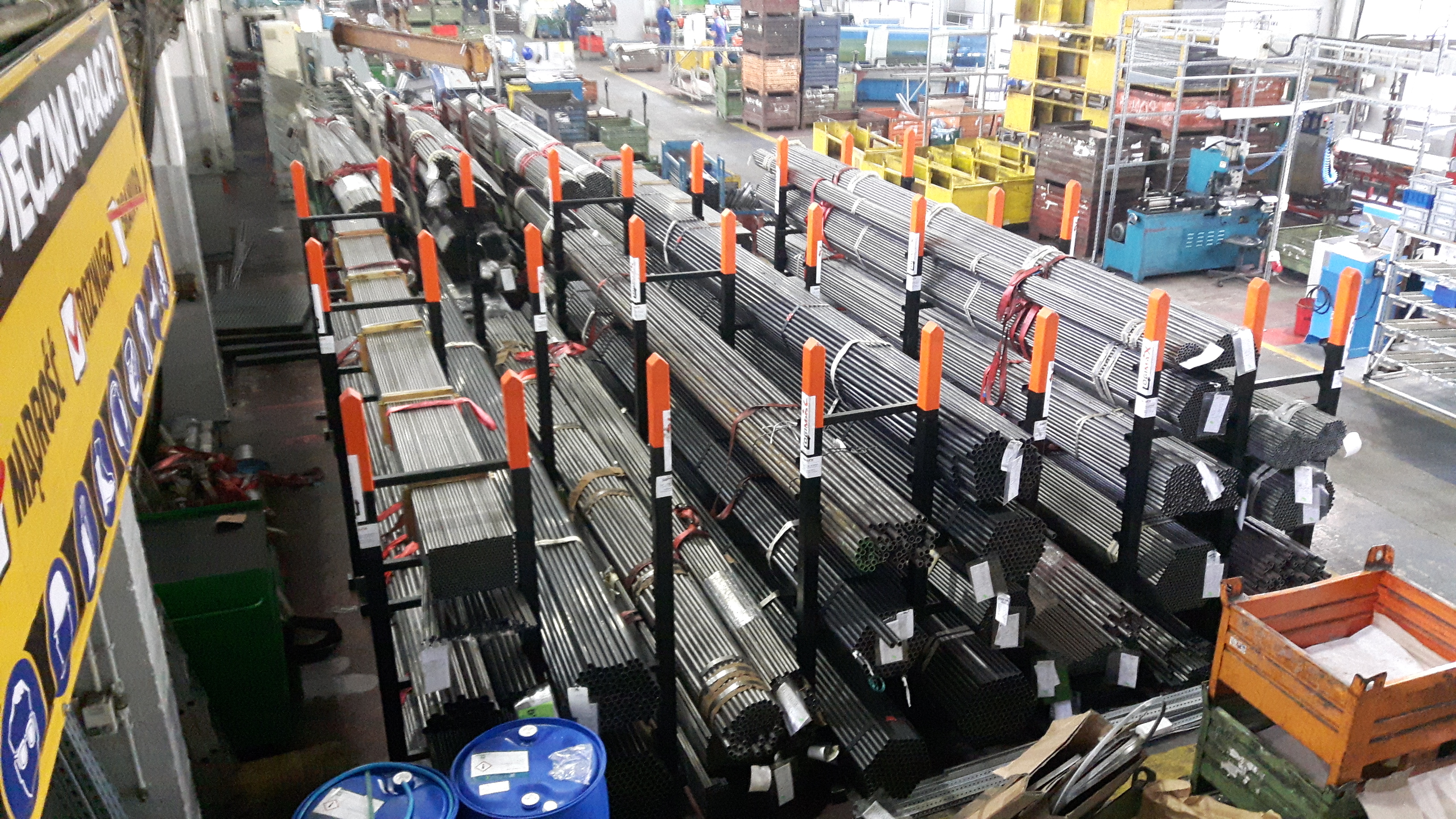
CASE STUDY 108 Layout produkcji – złożenia rurowe
Redukcja powierzchni produkcyjnej, poprawienie przepływu materiału, uwolnienie przestrzeni dla procesu cięcia – przeniesienie piły z odległej lokalizacji.
CASE STUDY 109 Layout hali produkcyjnej
Optymalizacja ustawienia maszyn z założeniem zakupu 10 maszyn.
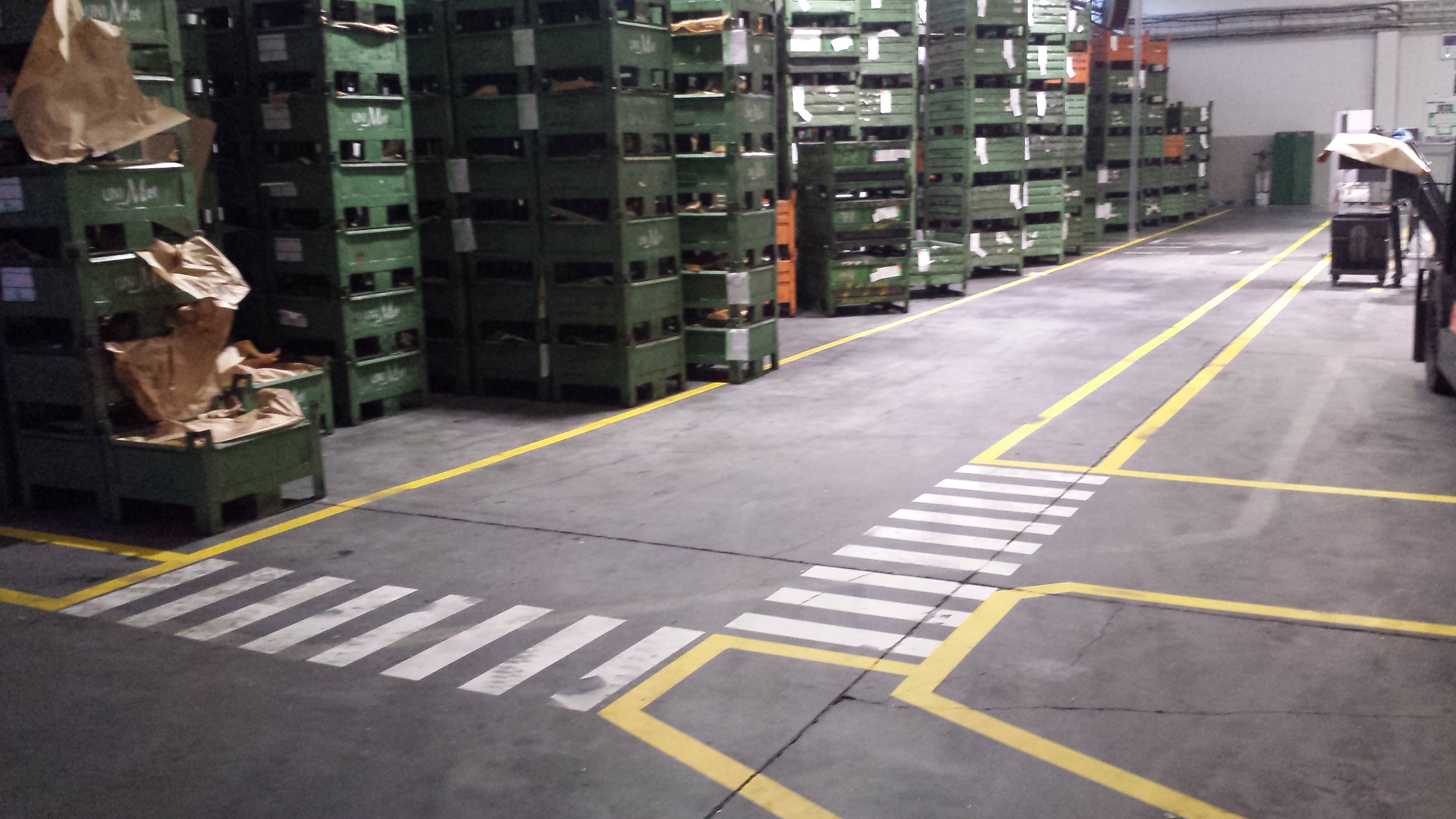
CASE STUDY 113 Mapowanie procesów usługowych
Eliminacja strat podczas realizacji projektów. Ujednolicenie prowadzenia projektów o niskiej seryjności oraz powtarzalności. Usprawnienie przepływu informacji.
CASE STUDY 114 Wskaźniki – zarządzanie produkcją
Monitorowanie efektywności produkcji, umożliwienie podejmowania decyzji biznesowych na bazie wskaźników.
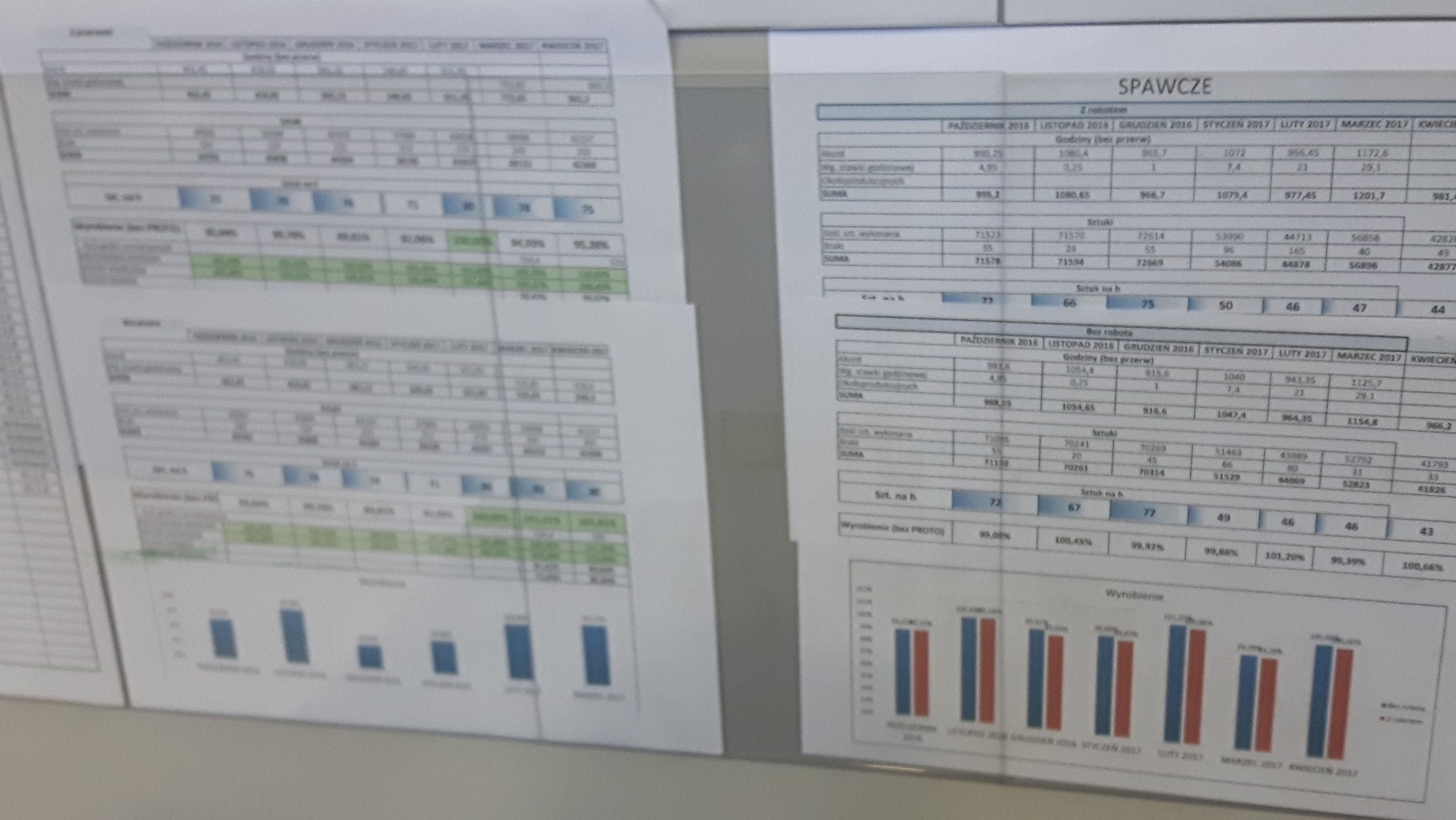
CASE STUDY 122 Rejestr kart pomiarowych
Brak systemowego podejścia do archiwizacji dokumentacji kontrolnej powodował błędy i pominięcia przy zapisywaniu danych. Wyniki pomiarów zapisywane były w formie kart, których szablony opracowano na bazie arkuszy excel.
CASE STUDY 124 5S na drukarni
Wdrożenie systemu 5S w celu poprawy organizacji miejsca pracy.
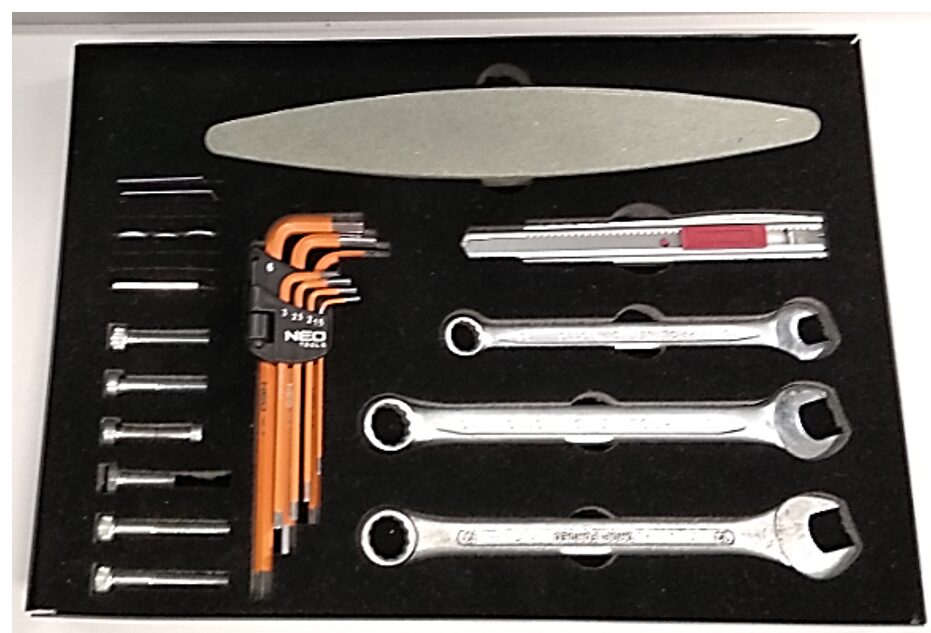
CASE STUDY 101 Kalkulator kosztów produkcji
Kalkulator kosztów produkcji to konieczne narzędzie do monitorowania rentowności zleceń i produktów.
CASE STUDY 123 Rejestr reklamacji
Brak systemowego prowadzenia procedur obsługi reklamacji powodował szereg problemów takich jak: pominięcia, niedotrzymane terminy, problemy komunikacyjne na linii firma – klient, a tak że problemy komunikacyjne wewnątrz zespołu.
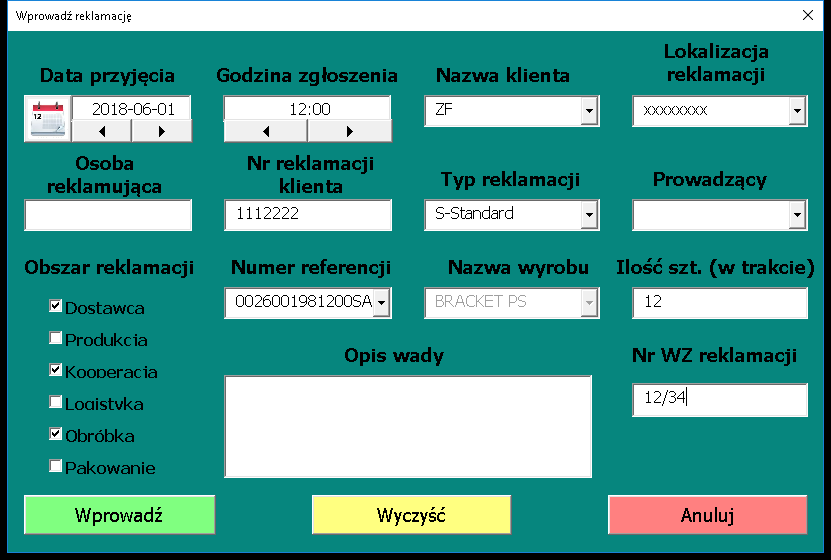
CASE STUDY 125 Capacity – planowanie zdolności produkcyjnych
- Uzupełnij formularz, jeśli masz jakiekolwiek pytania dotyczące rozwoju firmy, przeprowadzenia szkolenia, wspólnych warsztatów lub czy innej formy współpracy. Jeżeli możesz podaj jak najwięcej szczegółów.
- Twoja wiadomość jest dla nas ważna, odpowiemy na nią maksymalnie kolejnego dnia roboczego.
- W zależności od pytania poprosimy Cię o niezobowiązującą rozmowę telefoniczną lub spotkanie online. Taka forma kontaktu pozwoli nam najlepiej zrozumieć potrzeby i oczekiwania.
NAPISZ DO NAS
Kontakt bezpośredni.
Obsługa klienta Anna Etgens Specjalistka ds. zadowolenia klienta
+48 729 831 085
ul. Wrocławska 87, 30-011 Kraków
pl. Solny 14 lok. 3, 50-062 Wrocław
Działamy na terenie całej Polski.
Przeanalizuj kluczowe obszary firmy produkcyjnej!
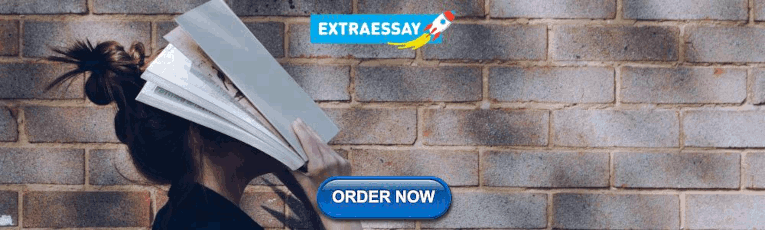
IMAGES
VIDEO
COMMENTS
The following case studies of lean management principles in action show you how a variety of real businesses solved real business problems under diverse conditions. We've arranged the stories in 16 categories to help you find the examples you need. There is some overlap. For instance, a "Lean Manufacturing" case study may also appear with ...
This case study is one of three highlighting successes identified as part of the Operational Excellence in Government Project . The purpose of the case studies is to elevate and document the successes, and in doing so to provide a greater amount of detail than is typically available about such efforts . The case studies explain the
case study research of a UK tea company. An action research approach was adopted to study the lean process and diagnose the problems which occurred during lean implementation. The present study developed a lean action plan with three stages: (a) Planning for lean; (b) Interim lean diagnosis; and (c) Lean operations and control.
The present study developed a lean action plan with three stages: (a) Planning for lean (b) interim lean diagnosis and (c) Lean Operations and control. The first ... the types and sources of evidence and presents briefly the case study. The findings from the action research are reported in Section 4. Section 5 discusses the
This case study reports on the replacement of Hospital 3 with a new hospital that opened in May 2011 with 73 additional beds. ... The action plan serves to keep the team accountable; the process owner is responsible for ensuring that the items in the action plan are completed. ... In our other case studies of Lean, barriers were usually ...
Increasing First Run Parts From 60% to 90% With Lean Six Sigma. Reducing Bent/Scratched/Damaged (BSD) Scrap for Building Envelopes. Reducing Lead Time in Customer Replacement Part Orders by 41%. Reducing Learning Curve Rampu0003 for Temp Employees by 2 Weeks. Reducing Purchase Order Lead Time by 33% Using Lean Six Sigma.
Introduction to the Case Studies Project Background Lean is an organizational redesign approach that is increasingly being used in health care. The term "Lean Production" was coined by an MIT research team studying leading automotive manufacturers around the world.1 At its core, Lean focuses on the elimination of waste, with
Pre-Action Plan for 5S Lean. Before you execute 5S, work through the following activities for effective implementation. Start with a single issue that needs Process Optimization. Once you successfully execute 5S to rectify this problem, you can then look at deploying the principles across other processes.
Here is a case study on using the A3 problem solving process. ... A management practice for understanding the current situation through direct observation and inquiry before taking action. Lean uses "gemba" to mean "where the real work happens", in Japanese it means "actual place". ... Kaizen is part philosophy and part action plan. As ...
This Lean Enterprise Institute case study explores how lean can take root and transform the performance of a small (less than 250 employees), privately-held distribution business that bears very little resemblance to the automotive assembly line typically associated with lean management. The Building Is Paid For
3.2.2 Value Stream Mapping (VSM). According to Rother and Shook (), value stream mapping is a tool that helps to see and understand the flow of material and information as a product makes its way through the value stream.What we mean by value stream mapping is simple: Follow a product´s production path from customer to supplier and carefully draw a visual representation every process in the ...
LHC is a nonprofit, comprehensive health care system. It comprises four hospitals, an ambulatory care center, physician offices, rehabilitation services, long-term care centers, home care services, physical therapy services, and mobile intensive care units. LHC was established in 1998 when four hospitals merged.
When implemented correctly, lean is a comprehensive process that eliminates waste from manufacturing processes, thereby reducing cost and adding value to the customer. Below are seven real-life examples of how simple lean techniques can improve manufacturing efficiency and production. 1. Cable Manufacturing.
The methodology used was a case study research of a UK tea company. An action research approach was adopted to study the lean process and diagnose the problems which occurred during lean implementation. This study developed a lean action plan with three stages: (a) planning for lean; (b) interim lean diagnosis and (c) lean operations and control.
A3 Action Plan Form (from Getting the Right Things Done) The action plan template helps define the who, what, when, where, and how of a plan on one page. Helps track progress and highlight problems so action can be taken. Download.
3.2 Case Study Deployment. Since the improvement project was driven using the A3 template, the case study will be descripted by using its structure. Thus, the eight sections of the A3 template will be presented. Also, the relationship of the sections with the PDCA (Plan-Do-Check-Act) cycle will be made explicit, as some other authors did .
The study relies on the lean action plan developed by Womack and Jones (2003): Planning for lean and Lean action. Lean planning consists of the following steps: find a change agent; get the ...
Welcome to the Lean Six Sigma Academy's Case Studies section! Here, you will find a collection of real-world examples of how companies have successfully implemented the Lean Six Sigma methodology to improve their business operations. Each case study includes an overview of the business challenge that was faced, the approach that was taken ...
A3 Problem solving or A3 Structured Problem Solving as it is often referred to, is a systematic approach to identifying, analyzing, and solving complex business problems. It was originally developed by Toyota as part of its lean methodology. The A3 is a problem-solving tool that encourages a collaborative and systematic approach to problem-solving.
The research methodology is action research aiming at disseminating the problems that the company is facing. The study relies on the lean action plan developed by Womack and Jones (2003): Planning for lean and Lean action. Lean planning consists of the following steps: find a change agent; get the knowledge; find a lever.
In this case study, participants from two construction companies, a leading lean contractor and a non-lean contractor, were interviewed to evaluate the different lean construction "journeys" taken by each company. The interviews and analysis in this study primarily focus on the lean culture, use of lean construction tools, common barriers ...
Step 6: Monitor and revise your action plan. Your ability to stay on top of and adapt to changes is what makes you a great project manager. It's crucial that you monitor your team's progress and revise the plan when necessary. Luckily, your action plan isn't set in stone.
CASE STUDY 85S na spawalni. Na hali znajduje się 15 kabin spawalniczych, w których pracują spawacze na pierwszej i drugiej zmianie. Każda kabina ma swoje wyposażenie w zależności od wykonywanego detalu. Podczas wykonywania badań migawkowych wykryto duży udział czynności zbędnych - głównie szukania narzędzi.