
Diagram Tool
Business Use
Individual Use
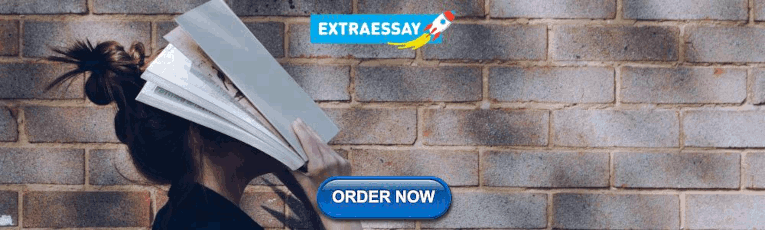
Learn What is 4M Root Cause Analysis Element and Know How to Use and Create One
Throwing ourselves into the world of business comes with a huge responsibility. Business people must focus on improving and developing the process of production. The growth of specific tactics and services of a company has a vital role and significant contributions to make the profit grow. That is why the people who incorporate the world must require proper research about what they need to do to make it possible. In line with that, this article can help you with possible methods in building a solid production in your business. Join us to discuss the definition and purpose of 4M root cause analysis and its example . Let us dig deep into what ability it can offer that we can use in improving our business. In addition, we will know the great tool that we can use in creating a 4M analysis method. Without further ado, buckle up and see the possibility of making your business better.
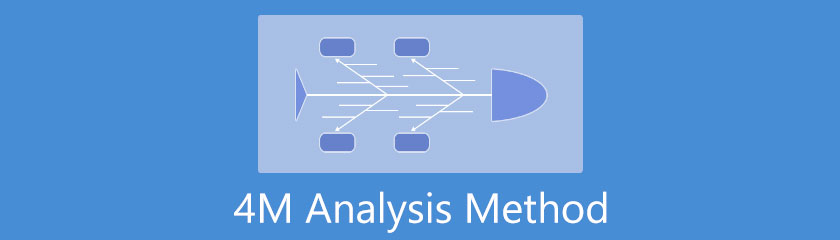
4M Method – How to Preapare a Checklist?
- Lean Management
Nenad Marcetic
- April 28, 2022
- Post Views: 3,087
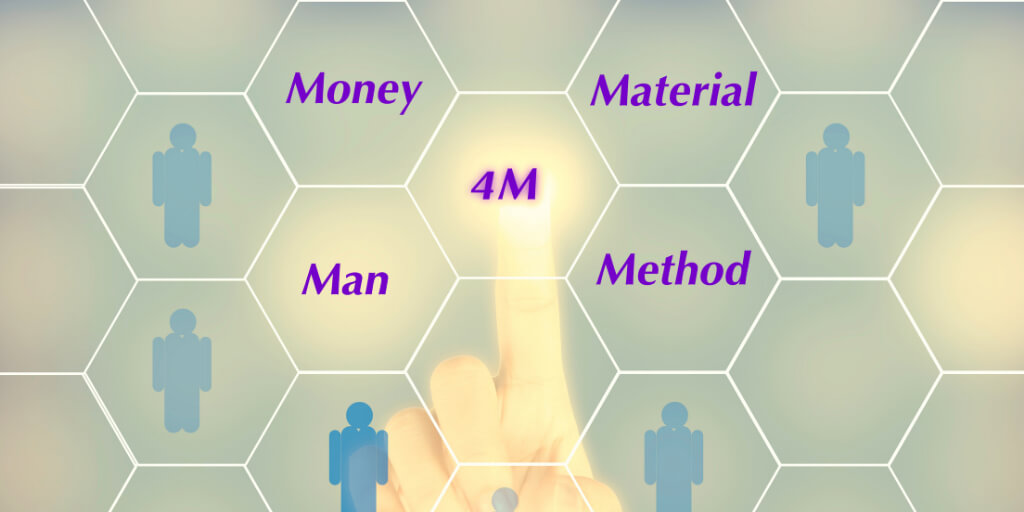
The 4M method is a simple problem-solving tool that allows us to brainstorm, identify, and group potential factors that cause problems. To be more effective during the implementation of 4M method ( Ishikawa ), we could use an additional Checklist. The 4M Checklist is an essential part of completing the perfect implementation of the 4M method. There is a standard set of questions that you should ask and review during the brainstorming phase. These questions have a goal to help you identify potential causes, but also to drive you systematically through the problem-solving process. Usage of the checklist is prevention to not forgetting some of the hidden or not-so-obvious causes.
Table of Contents
The 4M Checklist
The checklist should cover questions from each 4M section:
- MEN – Set of questions related to direct & indirect labor and their responsibilities, knowledge & experiences, training, hiring, compensation, benefits, motivation, etc.
- METHOD – Set of questions related to working methods – standards, instructions, specifications, guidelines, control plans, etc.
- MATERIAL – Set of questions to discover the status, quality, quantity, conditions, flow, and handling of both direct & indirect materials.
- MACHINE – Set of questions related to equipment, jigs, gauges, fixtures, calibrations, tables, racks, trolleys, tools, etc.
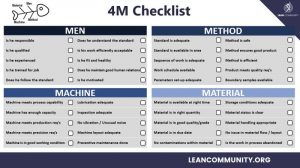
4M Checklist
Benefits of Using the Checklist
- Problem-Solving : By categorizing potential problem areas, it becomes easier to systematically analyze and address issues.
- Process Improvement : Helps in identifying inefficiencies and areas for improvement in the process.
- Quality Control : Enhances the ability to maintain consistent quality by identifying and mitigating variables that could affect the output.
- Risk Management : Proactively identifies areas where risks could emerge, allowing for preemptive action.
The 4M checklist is a testament to the timeless principles of thoroughness, systematic analysis, and continuous improvement in business operations. In a rapidly evolving corporate landscape, the relevance of this checklist transcends its initial quality management application, permeating various aspects of organizational strategy and operational excellence.
- Adaptability to Diverse Sectors : The universality of the 4M framework allows it to be adapted across diverse industries, from manufacturing to services, healthcare to information technology.
- Promoting a Holistic View : The framework encourages managers and teams to look beyond the surface-level symptoms of problems, urging a more holistic examination of underlying causes.
- Facilitating Collaborative Problem-Solving : The 4M checklist fosters a culture of collaborative problem-solving .
- Educational and Training Utility : The checklist serves as an excellent educational tool, grounding employees in the fundamentals of systematic analysis and quality management.
- Aligning with Modern Technologies and Data Analytics : In an age dominated by big data and advanced analytics, the 4M checklist provides a structured framework for data interpretation.
The 4M checklist, a cornerstone of quality management and process analysis, continues to hold significant relevance in today’s complex business environment. Its ability to adapt, drive collaboration, foster continuous improvement, and integrate with modern technologies underscores its enduring value. As businesses navigate the challenges of the 21st century, the principles embedded in the 4M checklist remain as crucial as ever, guiding organizations toward operational excellence and sustained success.
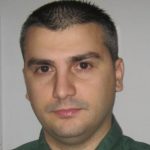
Nenad Marcetic is CIO at Lean Community. He has over 15 years of experience in Lean Management. He is a graduate of Quality Management. He has conducted more than 250 management system audits in various companies and industries (manufacturing, food and beverage, agriculture, IT services, finance, retail, mining). Since 2015 in a global automotive company, where he is responsible for process standardization and the implementation of the IATF standard.
Related posts
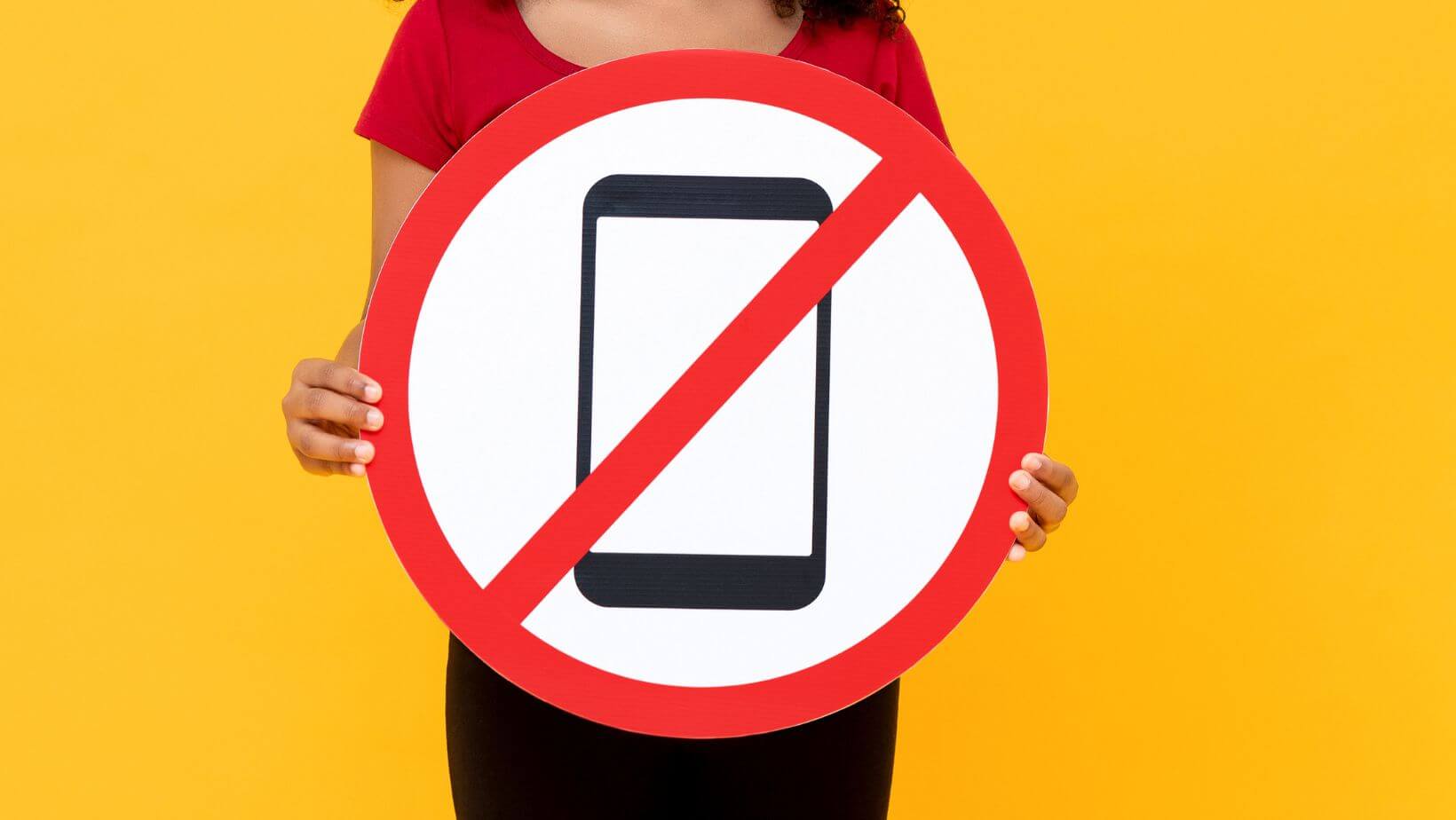
Effective Meetings – Phone Free
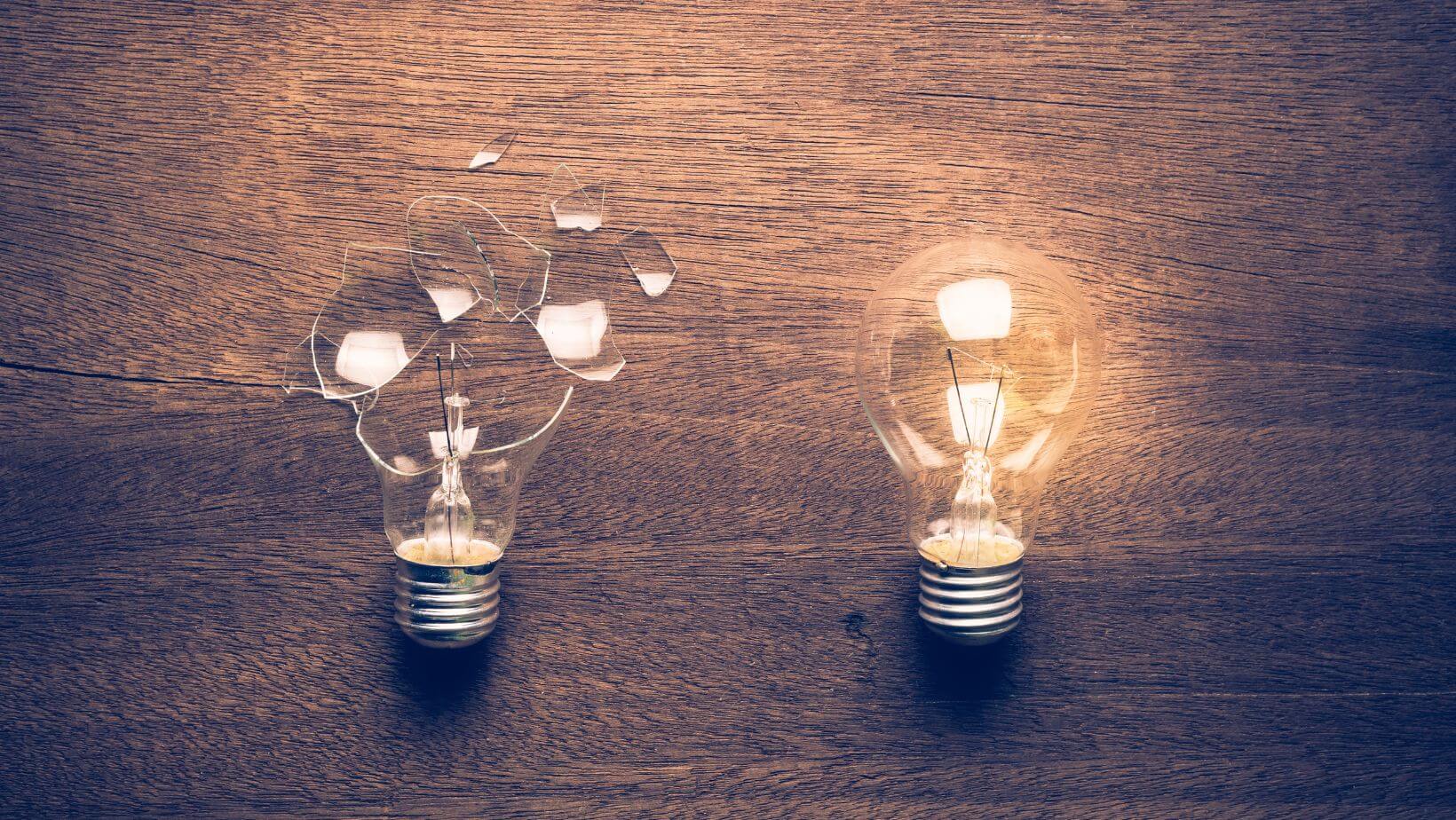
Fault Reporting System – Is it Worth It?
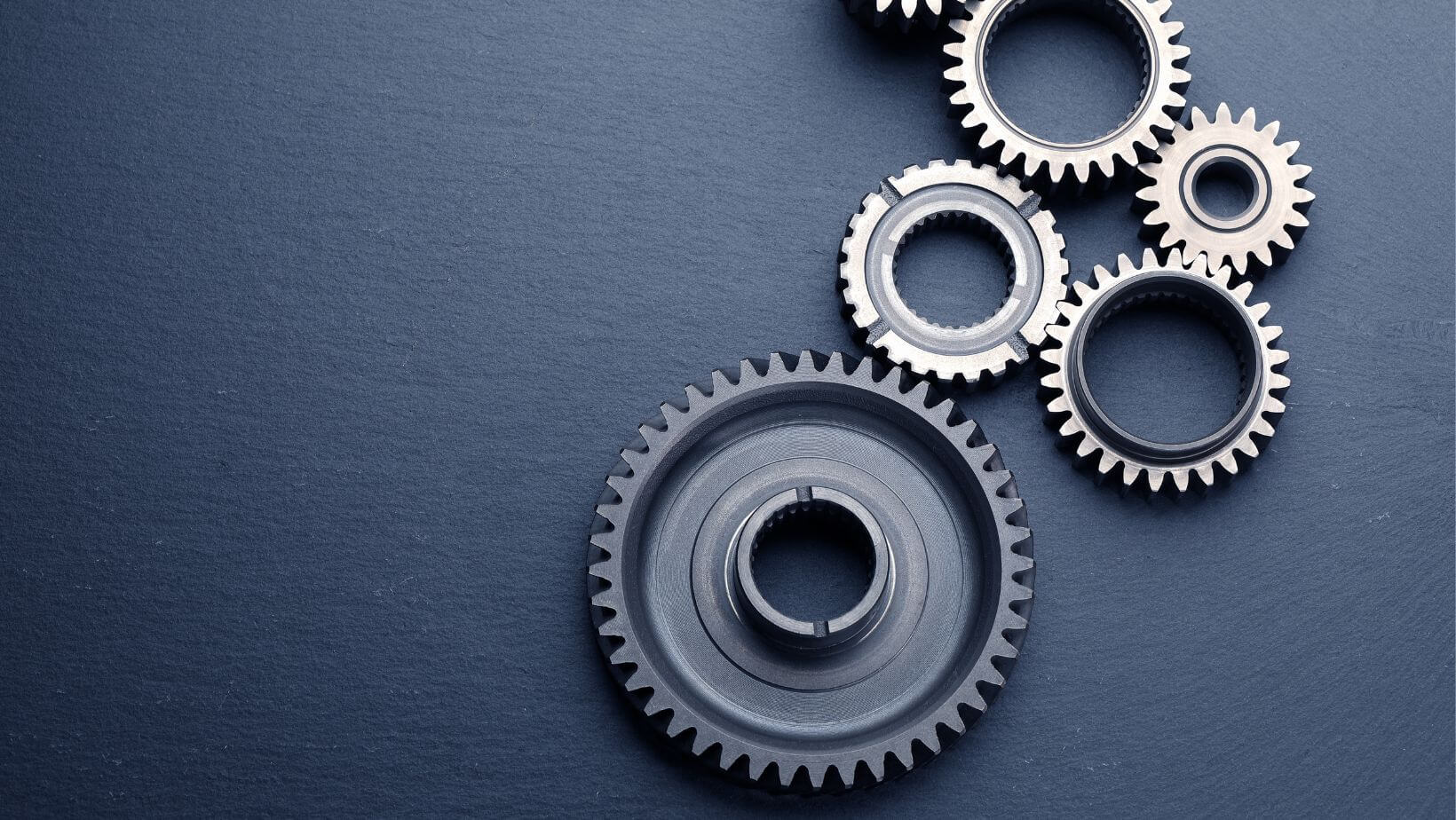
Machine Downtime – How to Reduce?
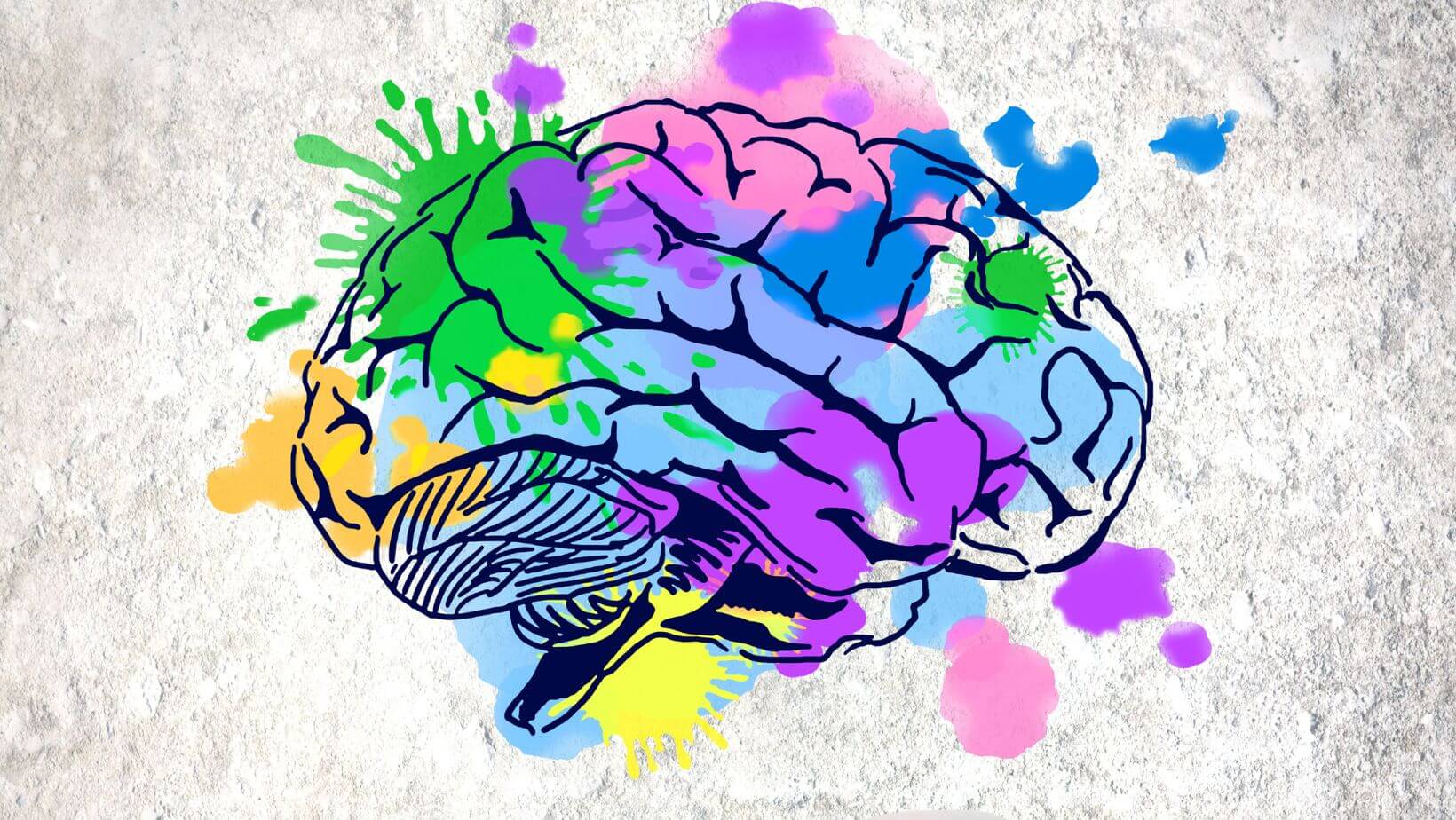
Creativity – The Business Success Key
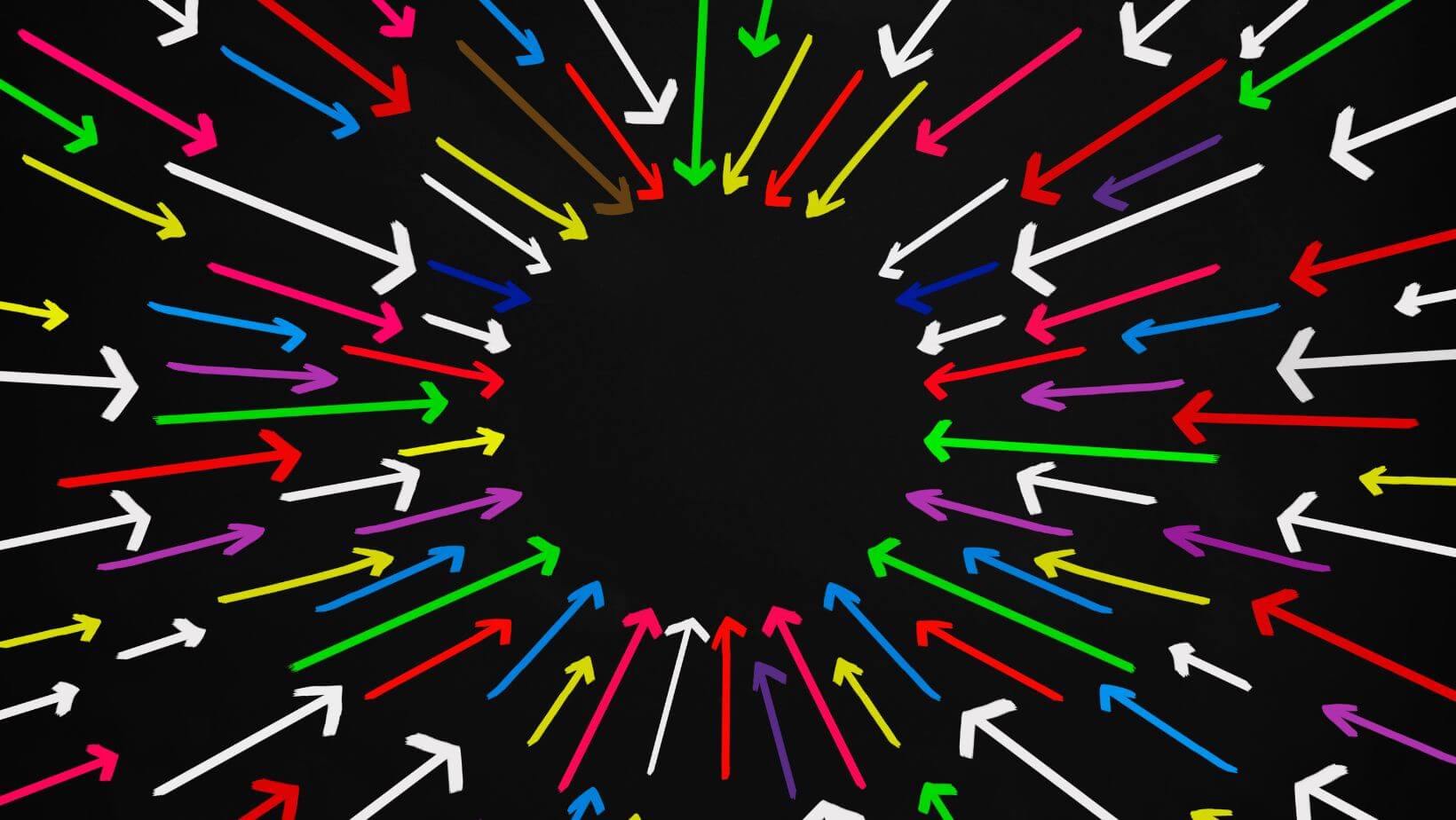
Creating Instruction – The Gemba Approach
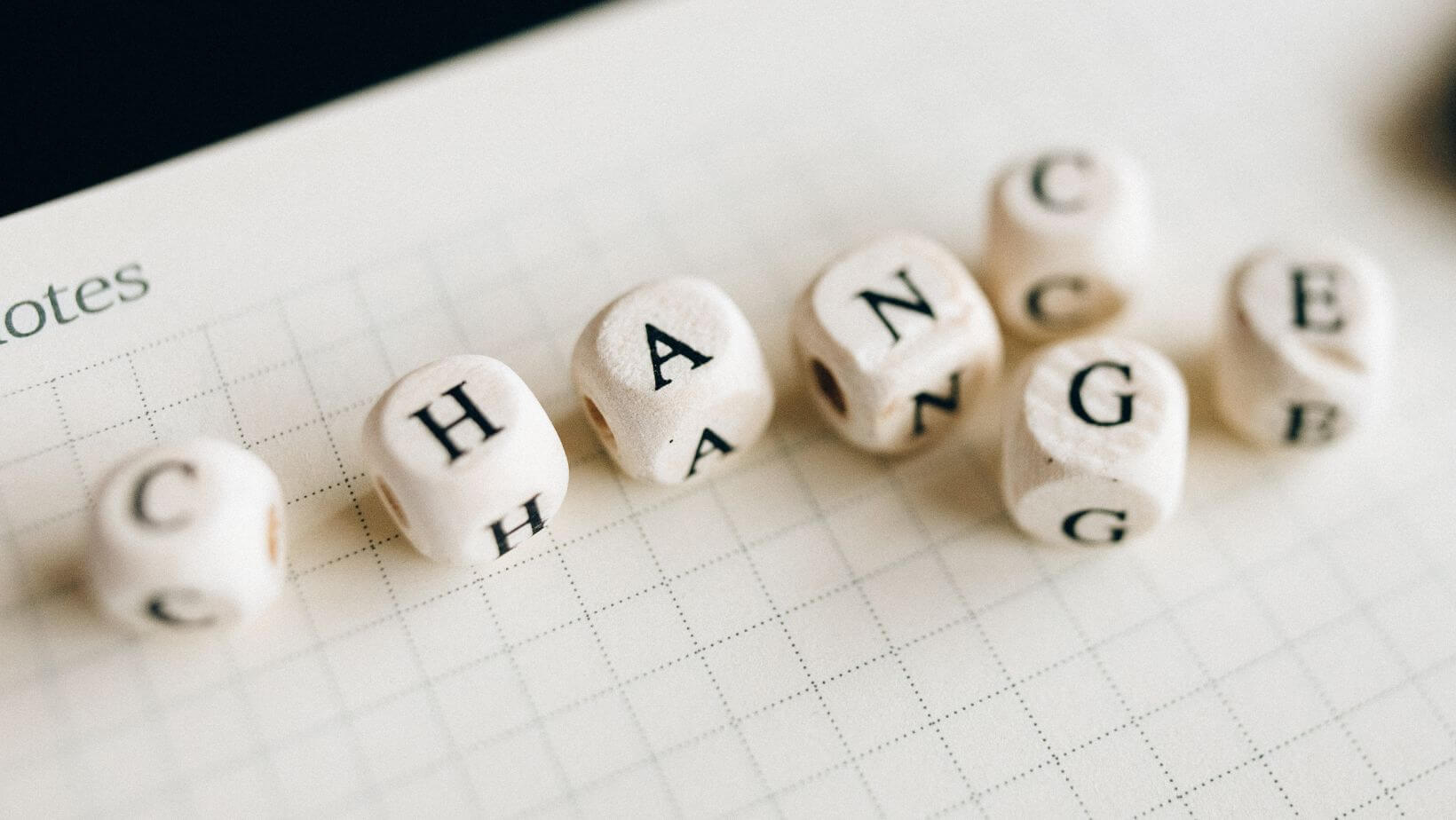
Change Management – A Three-Level Approach
Easily create, update and manage digital SOPs and Work Instructions and Training Skill Matrices to support the development process of your employees.
For Readers
- Discuss with the Authors
- Join the LinkedIn Group
For Authors
- Publish a work in the Library
- Sell a work in the Marketplace
- Business & Financial
- Education & Lifestyle
- HR & Leadership
- Strategy & Operations
- Technology & IT

Privacy Overview
SUPPLY CHAIN
HUMAN RESOURCE
PRODUCTIVITY
BY BUSINESS OPERATION
BY INDUSTRY
- Viindoo SaaS
- Training on using Viindoo Solution
- Implementation & Consultancy Service
- Customizing and Developing features on demand
- Odoo Upgrade Service
COLALBORATES
- What is 4M in manufacturing? How to effectively apply and improve 4M
- Business management
Your business wants to apply the principle of 4M in production . Businesses do not know what elements the 4M rules include and how to apply and improve. The following article by Vindoo will help businesses answer all the questions above. Let's find out now!
1. What is 4M in production?
4M in production is understood as a rule determining factors affecting business processes created by Kaoru Ishikawa (Japanese philosopher). The application of the 4M rules helps businesses find the causes and solutions to improve work quality and productivity. This rule consists of 4 main elements: Materials, Man, Machine, and Methods.
>>>> See more: Exploring Batch Production : Definition, Strategies and How to Implement

>>>> Read More About: 7 principles of quality management in ISO 9001:2015
2. Materials
Materials are understood as materials used in the production process. In order not to disrupt the product process, the source of raw materials must be ensured that the supply is just enough, there is no shortage or excess, causing disruption to the production process. In addition, the supply of sufficient materials also helps businesses reduce costs to pay for inputs, increasing revenue.
2.1 How to apply
Because raw materials are an important factor affecting the quality of products and account for about 50% of the cost of production Therefore, enterprises need to strictly check on quantity and quality. To apply In this factor, businesses need to solve problems such as:
- Determine the materials needed for the production process
- Amount of materials needed
- How to handle materials properly?
- How to handle product inventory
- Sorting materials in a scientific warehouse
>>>> Read About: 7 quality management tools What is that? The content, purpose of use

>>> See more:
- Materials Management in Manufacturing: How to Streamline Your Supply Chain
- Material Consumption in Manufacturing: Technology application
- Material Loss : Efficient management guide for Manufacturers
2.2 How to improve
To improve the Materials factor, businesses can do the following ways:
- Develop conditions to check the quality of incoming materials
- In order to avoid falling into the situation of running out of raw materials, businesses need to find and create New materials can replace old materials. In addition, this can also help businesses save resources, protect the environment ... increase the professionalism and competitiveness of products.
- Businesses need to learn about the history and reputation of the supplier before choosing to cooperate. In addition, businesses should also choose to cooperate with suppliers of quality raw materials to be able to create the best products.
3. Man (Human Resources)
Human resources are considered the most important factor in the rule 4M in production, which has a direct impact on the quality of the finished product. This factor includes all members of the business, from management to employees. In general, no matter how modern and advanced technology is, humans are still the factors that control them, playing an essential role.
In order to have quality human resources, enterprises need to focus on recruitment and internal training. In addition, businesses also need to build professional processes to facilitate management.
3.1 How to apply
Man is the key to the success of the production process. However, to apply the Man factor in the 4M principle, businesses need to solve problems such as:
- Define job goals
- Recruiting personnel with high ability and sense of responsibility, bringing effective productivity
- Develop policies to reward and handle violating employees
In addition, businesses also need to answer questions such as:
- What are the recruitment criteria for the vacant positions?
- Measure employee performance?
- Policies to retain and attract employees to stick with the business?
- How to train and guide new employees?

>>>> See More: What is Poka Yoke? How to apply Defect Prevention in production
3.2 How to improve
Enterprises can use some of the following methods to improve the Man factor, creating a sustainable competitive advantage in the market such as:
- Organize internal training sessions to improve employees' qualifications and skills
- Allocate appropriate working positions: Managers need to grasp the capabilities of each employee, identify their strengths and weaknesses to allocate appropriate working positions.

4. Machines (Equipment)
Machines is understood as the ability that enterprises invest in equipment and machines that directly affect product quality and work efficiency. Enterprises always have to improve the quality of machines, especially for units using automated production lines.
Without updating modern technologies into the production process, businesses will not be able to create quality products that meet the needs of users. In addition, enterprises also need to pay attention to the maintenance and maintenance of equipment to avoid problems of damage and interruption of the production process.
4.1 How to apply
If in the production process there is a problem with the machine, it will affect the working progress and revenue of the enterprise. Therefore, the inspection and maintenance of machines is a very important job.
To limit the occurrence of machinery damage, businesses need to solve problems such as:
- How to check the machine
- Arrange and use machines to maximize working productivity
- How and when to maintain machines
- Assigned to employees for certain types of machines
- Arrange and arrange space to place all kinds of machines to facilitate the use process

- What Is OEE ? Leveraging OEE with Viindoo Manufacture Software
- Applying IoT in manufacturing
4.2 How to improve
Ways to improve the Machines factor:
- Develop a suitable maintenance plan: The time of work interruption due to damaged machinery will reduce revenue, increase operating costs... Therefore, building a suitable maintenance plan not only helps to increase the age. machine life, but also to limit production interruptions.
- Using production management software: Currently, there are many modern management software that support businesses in monitoring, maintenance, and predicting damage of machines...
- Using modern machines: Using modern machines will help businesses improve work productivity, improve product quality, and meet consumer demand. In addition, investment in modern machinery also contributes to creating quality products with cheaper and more suitable prices.
5. Methods (Technology - Methods)
Methods is the use of methods of technology, management, and energy in the production process of an enterprise to make full use of the benefits and resources, contributing to increasing productivity and revenue of the unit.
5.1 How to apply
To apply the Methods factor, employees need to work together to create synchronization in the production process. In addition, managers must make employees aware that improving product quality is a common task of all employees.
When applying Methods, businesses need to well address aspects such as:
- % error occurred when applying methods
- The effectiveness of the method
- How to build charts to track progress
- Instructions for operating the machine

5.2 How to improve
Ways to improve the Methods element:
- Develop a detailed, clear, scientific strategy, and identify activities to be done to achieve the set goals.
- Assign appropriate tasks to each employee and department.
- Authorization for each specific employee
- Using management software: Technology is an effective way to support people in management. The use of ERP software also helps businesses plan and manage human resources effectively. The dashboard will help businesses visualize the overall business picture. From there, businesses can make the most informed and quick decisions.

Apply the principle 4M in production will help businesses save a lot of costs and bring high revenue. However, in order to have the highest production efficiency, businesses should use software Viindoo MRP - Comprehensive production management solution in the 4.0 era. Please contact hotline 0225 730 9838 to get more detailed advice on this software.
>>>> Continue With:
- What is a scatter chart? How to draw a scatter diagram
- What is a Pareto chart? Meaning and how to draw Pareto chart
SHARE THIS POST
- Viindoo Solution
- Digital Transformation
Viindoo Events
INDUSTRIAL TRAINER
Learn Professional
- Facebook Page
4M Principle
Table of Contents
The 4M principle is a management concept that stands for Man, Machine, Material, and Method. It refers to the four essential elements that are required for any production process to take place. The 4M principle provides a framework for identifying and addressing the key factors that contribute to the efficiency and effectiveness of a process or system.

Man refers to the human element, including the skills, knowledge, and attitudes of the people involved in the process. Machine refers to the tools and equipment used in the process. Material refers to the raw materials and resources that are required to complete the process. Method refers to the procedures and processes used to carry out the work, including the techniques and steps involved.

By focusing on each of these four elements, managers can identify and address any issues that may be hindering the productivity and efficiency of a process. By improving one or more of the 4M elements, it is possible to improve the overall performance of the process and achieve better results.
Over time, additional M’s have sometimes been added to the normal 4Ms. Whether to direct more industry-specific thinking, to demonstrate the evolution or improvement of the tool, or to easily make it more complex as a part of the rebranding. However, the large 4 are still the same:
Man (Skill, Technology, Organization, Resources)
In the context of the 4M principle, “Man” refers to the human element in a productive process. This includes the skills, knowledge, and attitudes of the people involved in the process. It is the human component that determines the quality of the output and plays a critical role in the success of the process.
Effective management of the “Man” aspect of the 4M principle involves selecting and training the right people for the job, ensuring that they have the necessary skills and knowledge, and creating a supportive work environment that fosters motivation, creativity, and collaboration. This can help to ensure that the people involved in the process are able to perform their jobs effectively and efficiently, leading to improved results.
It’s important to note that the “Man” element is not limited to just employees, but can also include managers, supervisors, and other stakeholders who have an impact on the process.
Machine (Equipment)
In the context of the 4M principle, “Machine” refers to the tools and equipment used in a productive process. This includes any machinery, technology, or equipment that is required to complete the process. The machines used can have a significant impact on the efficiency and effectiveness of the process.
Effective management of the “Machine” aspect of the 4M principle involves selecting the right equipment for the job, ensuring that it is properly maintained and in good working condition, and keeping it up-to-date with the latest technology. This can help to ensure that the machines are working effectively and efficiently, reducing downtime and increasing productivity.
In addition to the physical machinery, the “Machine” aspect of the 4M principle can also include computer systems and software that are used in the process. Effective management of these systems can help to ensure that they are functioning optimally and that they provide the necessary support to the process.
Material (Information, Raw Materials, Consumables, Quality)
In the context of the 4M principle, “Material” refers to the raw materials and resources required to complete a productive process. This includes any supplies, components, or other resources that are needed to carry out the work. The quality and availability of the materials used can have a significant impact on the efficiency and effectiveness of the process.
Effective management of the “Material” aspect of the 4M principle involves selecting the right materials for the job, ensuring that they are of high quality, and managing their availability and delivery to the production process. This can help to ensure that the right materials are available when they are needed, reducing downtime and increasing productivity.
In addition to physical materials, the “Material” aspect of the 4M principle can also include information and data that are used in the process. Effective management of this information and data can help to ensure that it is accurate, up-to-date, and available when it is needed, providing the necessary support to the process.
Method (Process, Schedule, Procedure)
In the context of the 4M principle, “Method” refers to the procedures and processes used to carry out a productive process. This includes the techniques, steps, and workflows involved in completing the work. The methods used can have a significant impact on the efficiency and effectiveness of the process.
Effective management of the “Method” aspect of the 4M principle involves defining and documenting the procedures and processes used in the work, ensuring that they are clear, concise, and easy to follow. This can help to ensure that the work is carried out consistently and in accordance with best practices, reducing the risk of errors and improving the overall quality of the output.
In addition to the procedures and processes used in the work, the “Method” aspect of the 4M principle can also include the tools and systems used to support and manage the work. Effective management of these tools and systems can help to ensure that they are functioning optimally and that they provide the necessary support to the process. By improving the methods used in a process, it is possible to increase its efficiency and effectiveness, leading to improved results.
Useful Links:
- Productivity Tools
- Quality Tools
- Process optimization Tools
- Lean Manufacturing Tools
- How to Apply for MNC Jobs
Significance of the 4M principle
The significance of the 4M principle lies in its ability to provide a framework for managing and improving the efficiency and effectiveness of a productive process. By focusing on the four essential elements of Man, Machine, Material, and Method, managers can identify and address any issues that may be hindering the productivity and performance of a process.
The 4M principle helps managers to:
- Identify the key factors that contribute to the success of a process
- Assess the strengths and weaknesses of a process
- Identify opportunities for improvement
- Prioritize areas for improvement
- Implement changes that lead to improved performance
By using the 4M principle as a guide, managers can take a systematic approach to process improvement, ensuring that they are addressing the most critical factors that affect the efficiency and effectiveness of a process. This can lead to improved results, increased productivity, and a more competitive operation.
In summary, the significance of the 4M principle lies in its ability to provide a structured approach to process improvement, enabling managers to make data-driven decisions and to continuously improve their processes.
The necessity of the 4M principle
The necessity of the 4M principle arises from the need to manage and improve the efficiency and effectiveness of productive processes in today’s fast-paced and competitive business environment. With the increasing demands for higher quality products and services and the need to operate more efficiently, it is important for organizations to continuously improve their processes.
The 4M principle provides a simple, yet comprehensive framework that enables managers to understand and manage the key factors that affect the performance of a process. By focusing on the four essential elements of Man, Machine, Material, and Method, managers can identify areas for improvement, prioritize changes, and implement effective solutions that lead to improved results.
The use of the 4M principle can help organizations to:
- Reduce costs by improving the efficiency of processes
- Increase productivity by reducing downtime and minimizing errors
- Improve the quality of products and services by ensuring that processes are carried out consistently and in accordance with best practices
- Stay competitive by continuously improving processes and adapting to changing market conditions
In conclusion, the necessity of the 4M principle arises from the need to manage and improve processes in a rapidly changing and competitive business environment. By using the 4M principle as a guide, organizations can take a systematic approach to process improvement, leading to improved results, increased productivity, and a more competitive operation.
Also Read:-
- 3G Gemba, Gembutsu, Genjitsu
- 3K 3M 3R 4M
- 4M Analysis
- Avoid These Common Mistakes in a Job Interview
- Continual Improvement Process
- Difference Between Cycle Time And Lead Time
- Importance of daily work management
What does each of the 4Ms represent in the 4M principle?
Man refers to the people involved in the process. Machine refers to the equipment and technology used in the process. Material refers to the raw materials and resources required to complete the process. Method refers to the procedures and processes used to carry out the work.
What is the significance of the 4M principle?
The significance of the 4M principle lies in its ability to provide a framework for managing and improving the efficiency and effectiveness of a productive process. By focusing on the four essential elements, managers can identify and address any issues that may be hindering the productivity and performance of a process.
Why is the 4M principle necessary?
The necessity of the 4M principle arises from the need to manage and improve the efficiency and effectiveness of productive processes in today’s fast-paced and competitive business environment. The use of the 4M principle helps organizations to reduce costs, increase productivity, improve the quality of products and services, and stay competitive.
How can organizations implement the 4M principle?
Organizations can implement the 4M principle by first identifying the key factors that affect the performance of a process, assessing the strengths and weaknesses of the process, identifying opportunities for improvement, prioritizing areas for improvement, and implementing changes that lead to improved performance.
Share this:
- Click to share on Facebook (Opens in new window)
- Click to share on Twitter (Opens in new window)
- Click to share on WhatsApp (Opens in new window)
- Click to share on LinkedIn (Opens in new window)
- Click to share on Pinterest (Opens in new window)
- Click to share on Telegram (Opens in new window)
- Click to print (Opens in new window)
- Click to email a link to a friend (Opens in new window)
Enter your active email address to subscribe to this blog and receive notifications of new updates by email.
Email Address
Recent Posts
- Manufacturing Automation: An overview and significance
- Project Management: Tools & Techniques for Project Managers
- Best Practices Industrial Asset Management
- Techniques for materials handling and transporting
- Techniques for fostering innovation and entrepreneurship
- Apply MNC Jobs
- Financial Management
- Industrial Trainer
- Lean Manufacturing
- Personality development
- Process Optimization
Best Practice
3G PRINCIPLE 3K PRINCIPLE 3M PRINCIPLE 3R 4M PRINCIPLE Avoid These Common Mistakes on a Job Interview Benefits of Kaizen Business Analysis capacity management Continual improvement Cybersecurity Cycle Time daily work management Examples gemba gembutsu genjitsu Industrial Trainer KAIZEN Kaizen continuous improvement Kaizen principles Kanban Lead Time Lean meaning Muda Mura Muri Objectives philosophy Process Process Analysis Quality Circle R&D RECYCLE Reduce Research and Development REUSE Rockwell hardness Significance Six Sigma Supply Chain Optimization The Secret of Standardization The Toyota 3M Model Total Productive Maintenance What is Capacity Management?
P-M or 4M analysis
Chronic & s poradic losses.
- Sporadic losses occur suddenly and infrequently, they result from a single cause that is relatively easy to identify and solve;
- Chronic losses, on the other hand, live up to their name by resisting a wide variety of corrective measures .
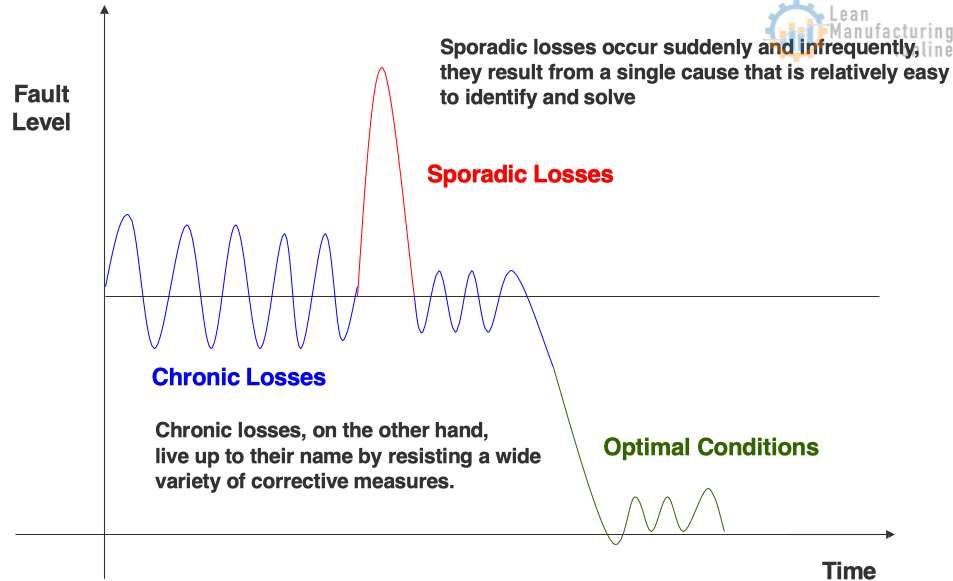
P-M Analysis
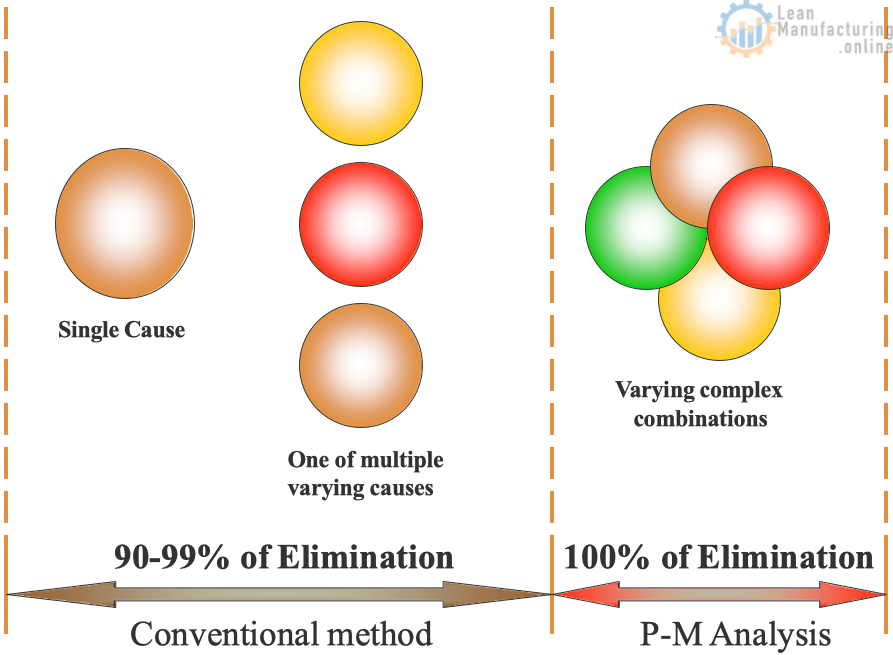
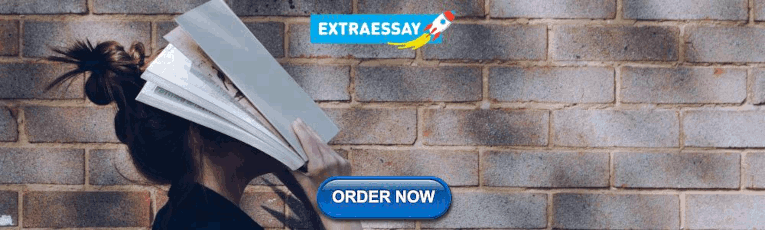
Single causes that vary constantly
Suppose for a given problem there are ten potential causes and each time the problem occurs the cause is different. Some time it may be A, some time C or D and so on. Consequently, measures focused on only specific cause cannot control the problem.
Varying combination of causes
In some case a combination of multiple and overlapping causes generates the problems. To make matters worse, each time the problem occurs, a different combination of factors may be involve. Today it may be factors A, B and C; tomorrow A, C, G and H.
Problem in reducing chronic losses
To archive a lasting reduction in chronic losses we must do three things;
- Identify all factors that conceivably contribute to a loss
- Thoroughly investigate each factor
- Eliminate any malfunctions or suboptimal conditions discovered in the process
P-M analysis is more than an improvement methodology, it is a different way of thinking about problem and context in which they occur.

- Look at phenomenon analytically and systematically
- Review all causal factors
- Identify all abnormalities and reduce them to ZERO
Levels of causal factor
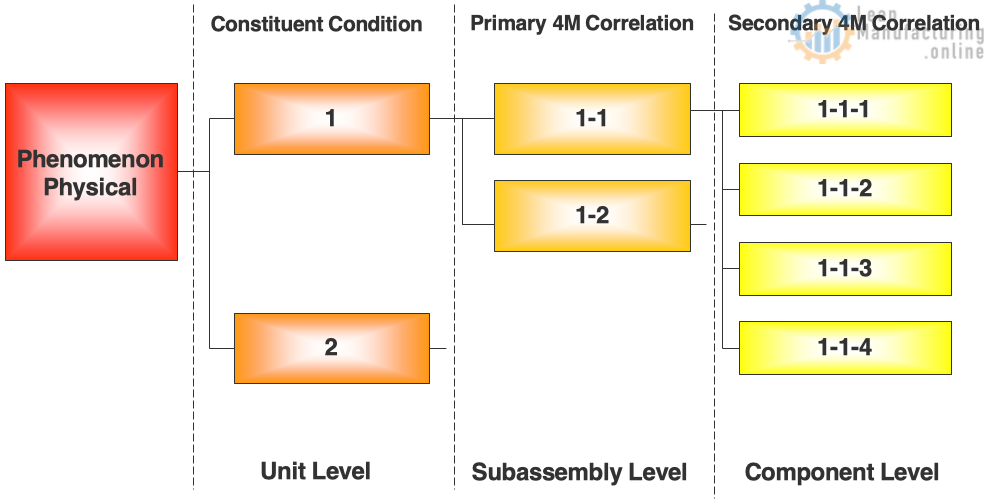
P-M Analysis steps

Step 1. Clarify the Phenomenon
Breakdown information.
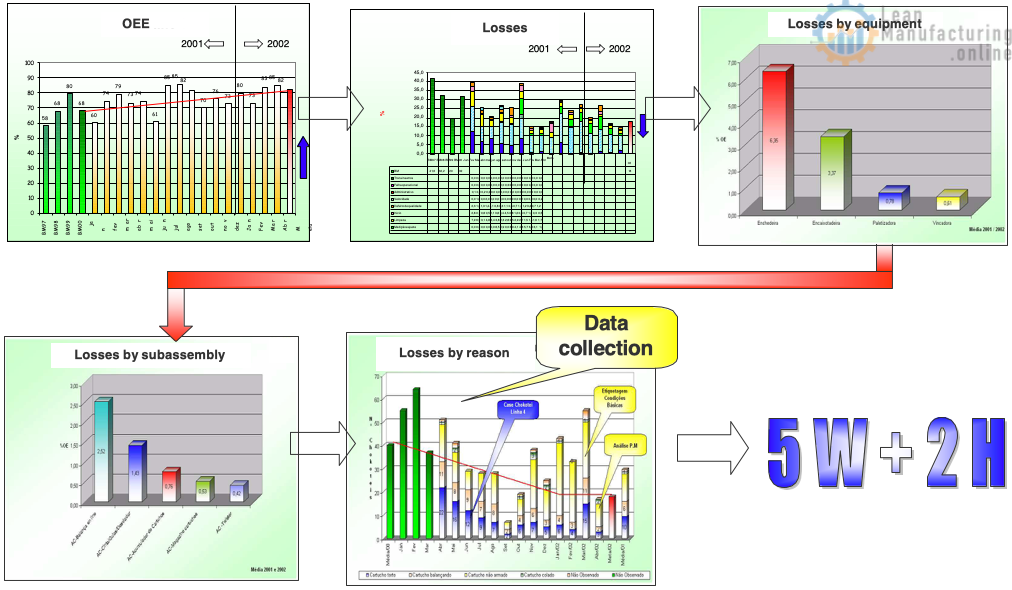
Data Collection
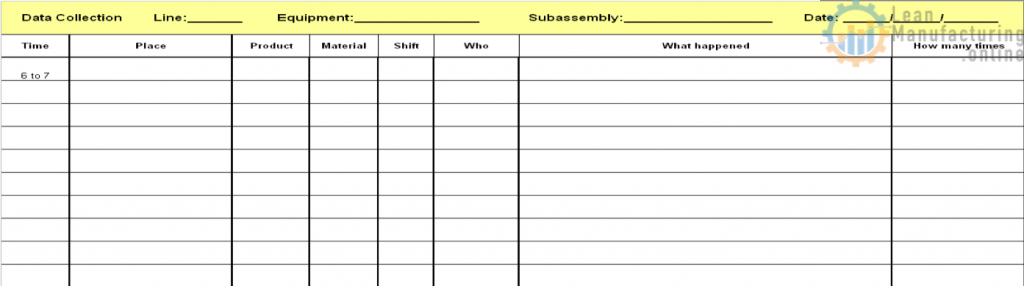
Phenomenon is insufficiently stratified and analyzed
It is all too easy to find manufacturing facilities where defects and failures are not carefully observed and sufficiently stratified, or broken down into discrete and differing aspects. In failing to observe the relevant phenomena carefully, people often do not notice the defect Patterns (HOW), elements (WHERE), and periods (WHEN and HOW OFTEN) that characterize them. For example, there are several ways:
- During morning startup
- Before and after blade replacement
- Before and after changeover
- During normal operation
Clarify the Ph e no me n o n
- What : What is it happening? (what the operation is seeing)
- Where: Where is it happening? (equipment or component)
- When : Any variation related to time or period?
- Who : Any variation among the people involved in the operation?
- Which : Is there any characteristic trend over time ?
How : How the situation goes from normal to abnormal condition
How Much : Total of Loss (money, product, complains, so on)
Write the phenomenon according to following:
How – What – Where – When – Which – Who and How Much
Step 2 . Physical Analysis of phenomenon
Think visually.
Some people may feel ill – equipped to express themselves in technical terms, but physical analysis does not require fancy words or complicated expressions. In fact, such words would only obscure the phenomenon. The best and simplest approach is to think visually. Consider drawing of how product and equipment elements interact to bring about the defect or functional failure.
Key Steps in Physical Analysis
- Identify operating principles: Review machine diagrams and manuals to understand the equipment basic operating principles.
- Identify operating standards: Learn the functions and mechanisms of equipment and Devices by sketching simple machine diagrams.
- Identify interacting elements: Draw contact diagrams to identify what relationships define the phenomenon.
- Quantify the physical change involved: Identify appropriate physical quantities and change in those quantities.
- ABCD Methodology: help us to write the phenomenon
The importance of understanding the mechanisms and its functions
Understanding the mechanisms and structure of the equipment involved is important as defining the phenomenon. Intimate Knowledge of equipment helps clarify what happens to produce particular malfunctions or defects. Mechanisms means a group of equipment elements with a single function and how it functions. Structure refers to how all the equipment elements are put together or assembled
Key Steps for understand them
- Draw the process flow
- Draw the equipment mechanisms
- Use materials to facility the comprehension , such as; technical manuals, pictures drawings so on…
- Make OPL to multiply the knowledge
Study, understand the working of system and mechanism
Analyze the phenomenon in physical term, it means, use physical principle to define the relationship the contact point between equipment and product.
A- B – C- D methodology
- A – Physical measurements involved (pressure, vacuum, temperature, distance, etc)
- B – Variation of dimension physical (increase, decrease, high, low, etc)
- C – Product (box, carton, bottle, etc)
- D – Component (guide, belt, etc)
Sequence of phenomenon description: B – A – C – D
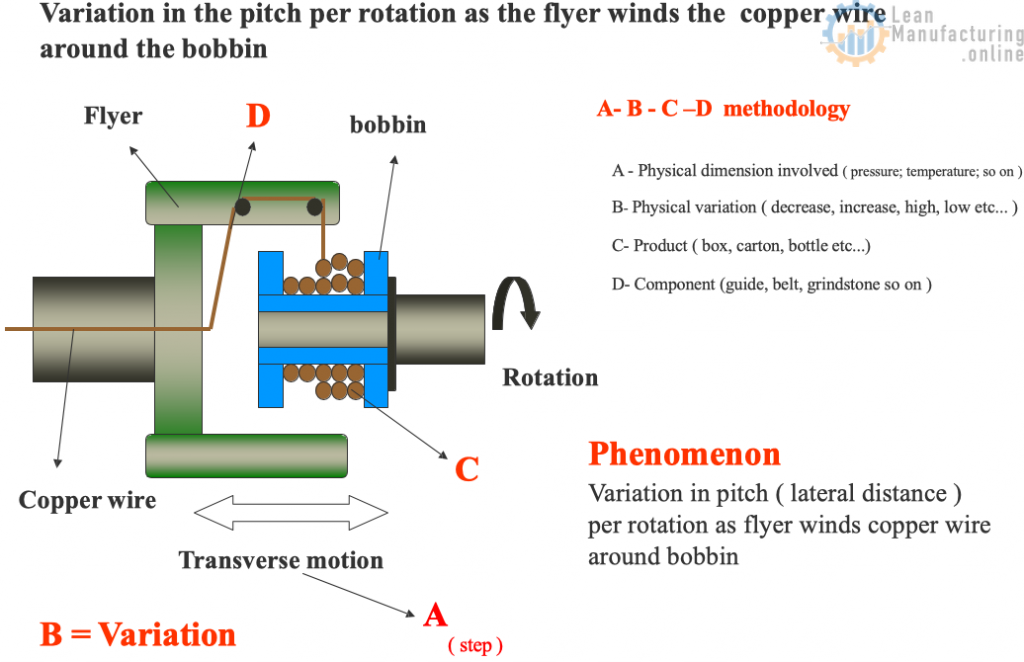
Step 3. Constituent Conditions
Procedure for checking constituent conditions.
The steps shown in table below are helpful when checking each of the 4Ms to see whether off-standard conditions may be linked to defect phenomenon. The table provides a simple example of approach.
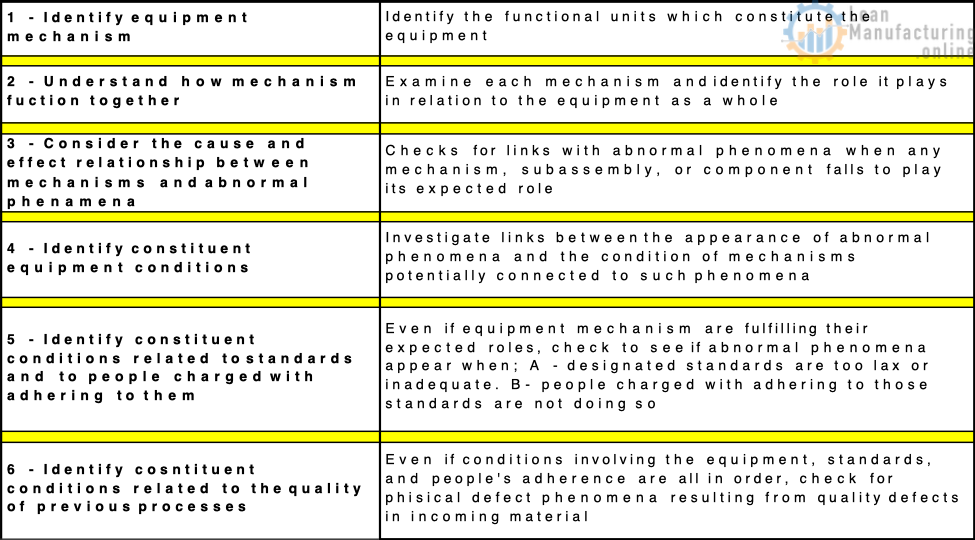
Identify and understand the system and mechanisms
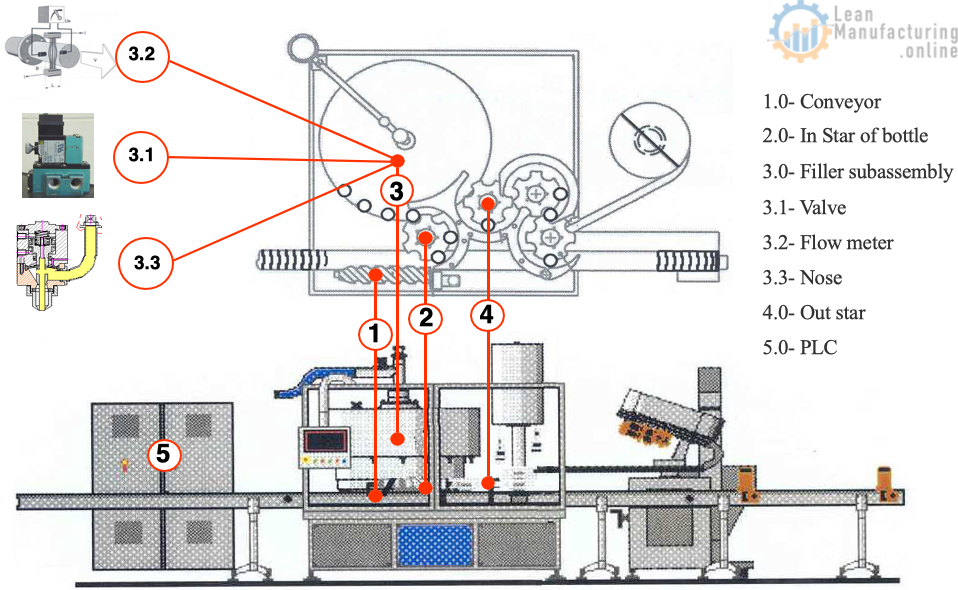
Step 5, 6 and 7.
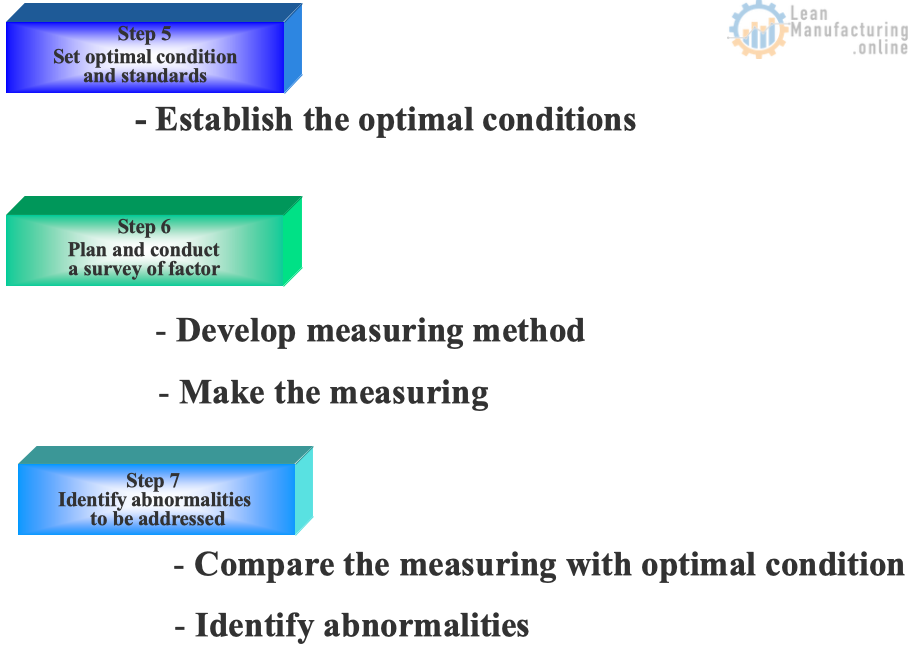
Study 4Ms for causal factors
List and investigate any correlation between the constituent condition identified in the previous step and the basic production inputs or 4Ms ( equipment, people, materials, methods ). Put another way, this means identifying cause-and-effect relationships between constituent condition specific and 4M elements. The constituent condition becomes the effect and we review 4Ms elements for potential causes. Identify all logically conceivable elements necessary to generate the constituent conditions.
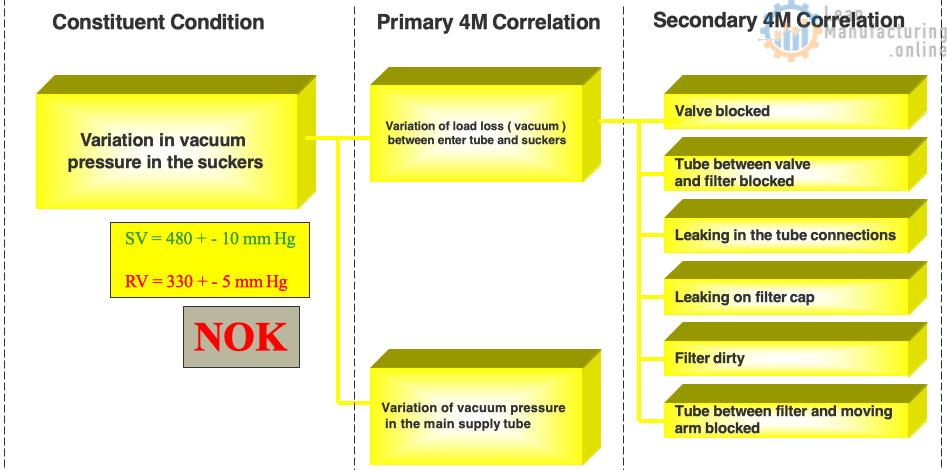
Step 8. Restoration – Improvements and Maintenance Control
Propose and make improvements.
In this eighth and final P-M Analysis step, teams propose make any correlations and improvements required for each abnormality, then plan and institute appropriate preventive measures.
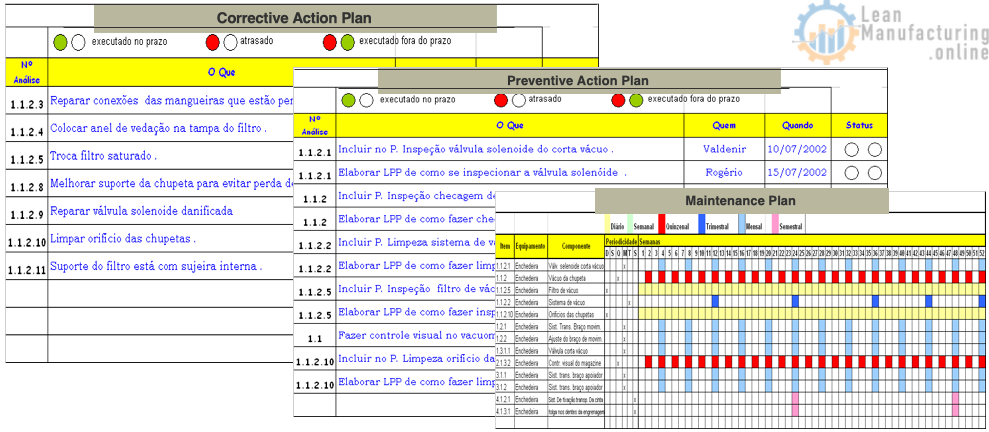
- Review the operational Procedures
- Review the cleaning procedures
- Review the inspection procedures
- Training for changes
- Record the improvement
- Review the Skill Matrix
- More By sensei
- More In Blog

Maximize Efficiency with the Right Plant Layout: A Comprehensive Guide
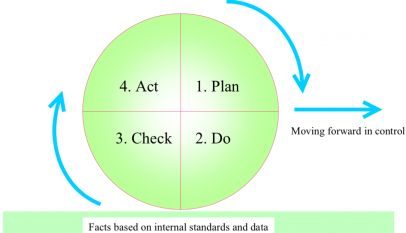
Harnessing Business Excellence in Manufacturing Through the PDCA Approach
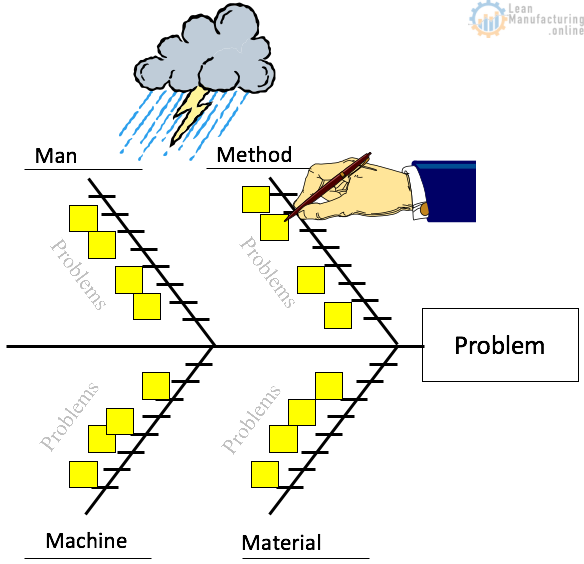
The Fishbone Diagram

Unlock the Power of Continuous Learning with Udemy’s Frequent Sales
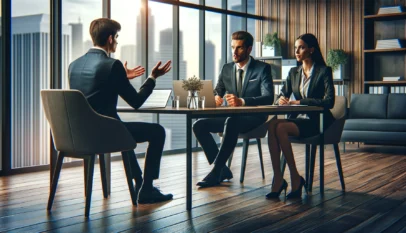
How to Ace Your Next Job Interview: Expert Insights and Strategies
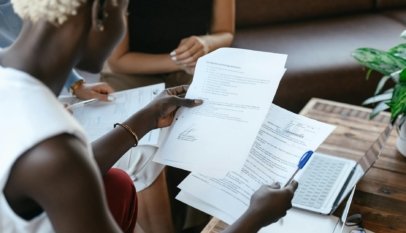
Mastering the Trio: Project, Program & Portfolio Management

Behaviors that kill employee motivation
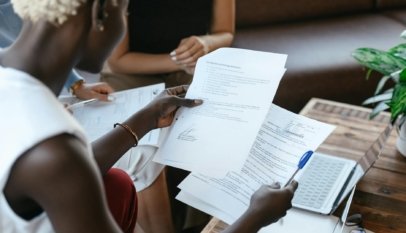
Common Interview Questions for Project Management Roles
Very good explanation. May I get copy of trg material ? mail Id : [email protected]
Leave a Reply Cancel reply
Your email address will not be published. Required fields are marked *
Most Popular
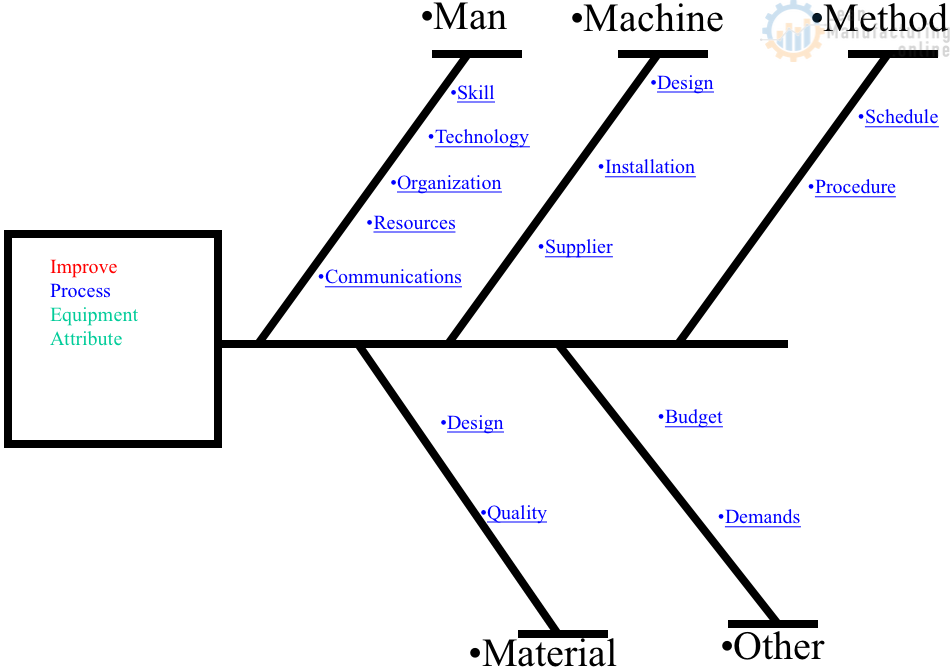
4M Analysis Process
The purpose of this procedure is to define the steps to do a 4M …
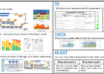
PDCA – A Process Approach

OPL – One Point Lesson Template – Free Download
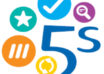
5S Audit Checklist and Report

Why-Why Analysis
Blog Search
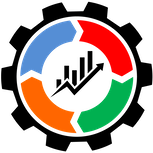
- Terms of Use
- Privacy Policy
- About Our Ads
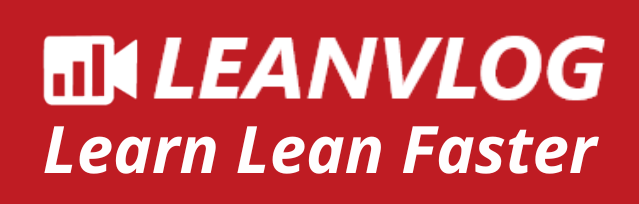
No videos yet!
Click on "Watch later" to put videos here
Lean Manufacturing Terms – 4M
4M (Man, Machine, Material, Method): Common structure for potential causes for Problem Solving methods , for example as the bones of the fish-bone diagram (see Ishikawa Diagram).
This is often expanded into 8M, including additionally management, milieu, measurement, and money.

Session expired
Please log in again. The login page will open in a new tab. After logging in you can close it and return to this page.
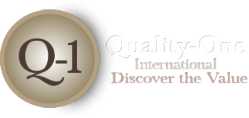
Eight Disciplines of Problem Solving (8D)
– Eight Disciplines of Problem Solving –
⇓ Introduction to 8D
⇓ What is 8D
⇓ Why Apply 8D
⇓ When to Apply 8D
⇓ How to Apply 8D
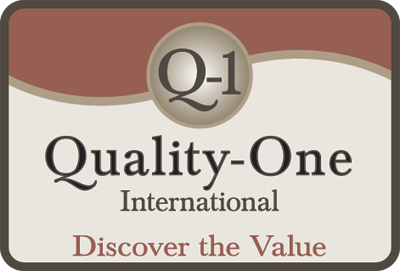
Introduction to Eight Disciplines of Problem Solving (8D)
The Eight Disciplines of Problem Solving (8D) is a problem solving methodology designed to find the root cause of a problem, devise a short-term fix and implement a long-term solution to prevent recurring problems. When it’s clear that your product is defective or isn’t satisfying your customers, an 8D is an excellent first step to improving Quality and Reliability.
Ford Motor Company developed this problem solving methodology, then known as Team Oriented Problem Solving (TOPS), in the 1980s. The early usage of 8D proved so effective that it was adopted by Ford as the primary method of documenting problem solving efforts, and the company continues to use 8D today.
8D has become very popular among manufacturers because it is effective and reasonably easy to teach. Below you’ll find the benefits of an 8D, when it is appropriate to perform and how it is performed.
What is Eight Disciplines of Problem Solving (8D)
The 8D problem solving process is a detailed, team oriented approach to solving critical problems in the production process. The goals of this method are to find the root cause of a problem, develop containment actions to protect customers and take corrective action to prevent similar problems in the future.
The strength of the 8D process lies in its structure, discipline and methodology. 8D uses a composite methodology, utilizing best practices from various existing approaches. It is a problem solving method that drives systemic change, improving an entire process in order to avoid not only the problem at hand but also other issues that may stem from a systemic failure.
8D has grown to be one of the most popular problem solving methodologies used for Manufacturing, Assembly and Services around the globe. Read on to learn about the reasons why the Eight Disciplines of Problem Solving may be a good fit for your company.
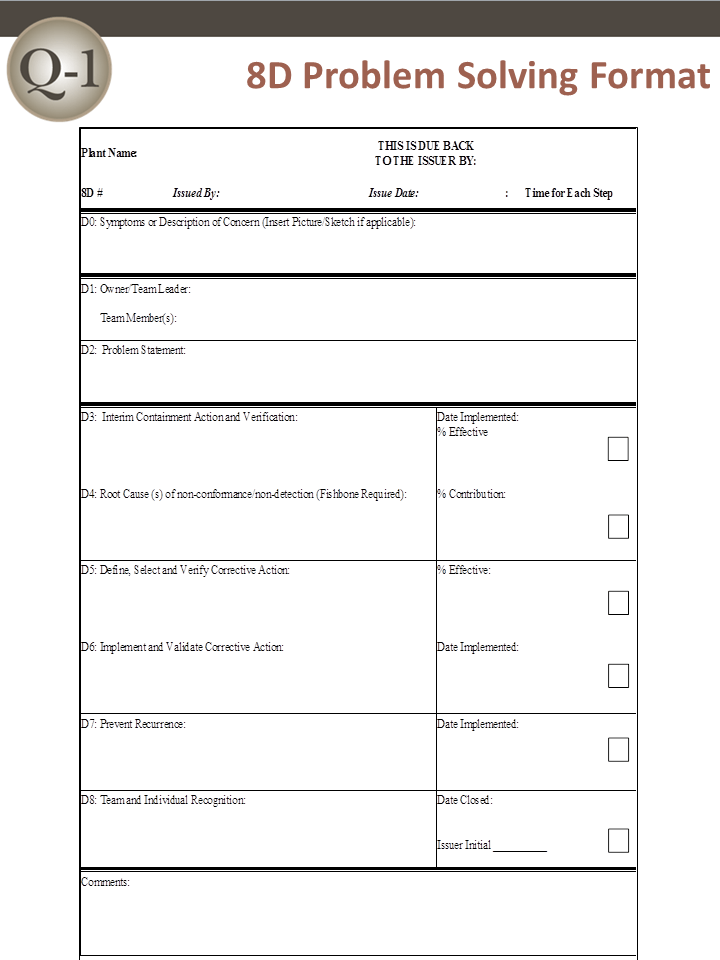
Why Apply Eight Disciplines of Problem Solving (8D)
The 8D methodology is so popular in part because it offers your engineering team a consistent, easy-to-learn and thorough approach to solving whatever problems might arise at various stages in your production process. When properly applied, you can expect the following benefits:
- Improved team oriented problem solving skills rather than reliance on the individual
- Increased familiarity with a structure for problem solving
- Creation and expansion of a database of past failures and lessons learned to prevent problems in the future
- Better understanding of how to use basic statistical tools required for problem solving
- Improved effectiveness and efficiency at problem solving
- A practical understanding of Root Cause Analysis (RCA)
- Problem solving effort may be adopted into the processes and methods of the organization
- Improved skills for implementing corrective action
- Better ability to identify necessary systemic changes and subsequent inputs for change
- More candid and open communication in problem solving discussion, increasing effectiveness
- An improvement in management’s understanding of problems and problem resolution
8D was created to represent the best practices in problem solving. When performed correctly, this methodology not only improves the Quality and Reliability of your products but also prepares your engineering team for future problems.
When to Apply Eight Disciplines of Problem Solving (8D)
The 8D problem solving process is typically required when:
- Safety or Regulatory issues has been discovered
- Customer complaints are received
- Warranty Concerns have indicated greater-than-expected failure rates
- Internal rejects, waste, scrap, poor performance or test failures are present at unacceptable levels
How to Apply Eight Disciplines of Problem Solving (8D)
The 8D process alternates inductive and deductive problem solving tools to relentlessly move forward toward a solution. The Quality-One approach uses a core team of three individuals for inductive activities with data driven tools and then a larger Subject Matter Expert (SME) group for the deductive activities through brainstorming, data-gathering and experimentation.
D0: Prepare and Plan for the 8D
Proper planning will always translate to a better start. Thus, before 8D analysis begins, it is always a good idea to ask an expert first for their impressions. After receiving feedback, the following criterion should be applied prior to forming a team:
Collect information on the symptoms
Use a Symptoms Checklist to ask the correct questions
Identify the need for an Emergency Response Action (ERA), which protects the customer from further exposure to the undesired symptoms
D1: Form a Team
A Cross Functional Team (CFT) is made up of members from many disciplines. Quality-One takes this principle one step further by having two levels of CFT:
- The Core Team Structure should involve three people on the respective subjects: product, process and data
- Additional Subject Matter Experts are brought in at various times to assist with brainstorming, data collection and analysis
Teams require proper preparation. Setting the ground rules is paramount. Implementation of disciplines like checklists, forms and techniques will ensure steady progress. 8D must always have two key members: a Leader and a Champion / Sponsor:
- The Leader is the person who knows the 8D process and can lead the team through it (although not always the most knowledgeable about the problem being studied)
- The Champion or Sponsor is the one person who can affect change by agreeing with the findings and can provide final approval on such changes
D2: Describe the Problem
The 8D method’s initial focus is to properly describe the problem utilizing the known data and placing it into specific categories for future comparisons. The “Is” data supports the facts whereas the “Is Not” data does not. As the “Is Not” data is collected, many possible reasons for failure are able to be eliminated. This approach utilizes the following tools:
- Problem Statement
- Affinity Diagram (Deductive tool)
- Fishbone/Ishikawa Diagram (Deductive tool)
- Problem Description
D3: Interim Containment Action
In the interim, before the permanent corrective action has been determined, an action to protect the customer can be taken. The Interim Containment Action (ICA) is temporary and is typically removed after the Permanent Correct Action (PCA) is taken.
- Verification of effectiveness of the ICA is always recommended to prevent any additional customer dissatisfaction calls
D4: Root Cause Analysis (RCA) and Escape Point
The root cause must be identified to take permanent action to eliminate it. The root cause definition requires that it can be turned on or off, at will. Activities in D4 include:
- Comparative Analysis listing differences and changes between “Is” and “Is Not”
- Development of Root Cause Theories based on remaining items
- Verification of the Root Cause through data collection
- Review Process Flow Diagram for location of the root cause
- Determine Escape Point, which is the closest point in the process where the root cause could have been found but was not
D5: Permanent Corrective Action (PCA)
The PCA is directed toward the root cause and removes / changes the conditions of the product or process that was responsible for the problem. Activities in D5 include:
- Establish the Acceptance Criteria which include Mandatory Requirements and Wants
- Perform a Risk Assessment / Failure Mode and Effects Analysis (FMEA) on the PCA choices
- Based on risk assessment, make a balanced choice for PCA
- Select control-point improvement for the Escape Point
- Verification of Effectiveness for both the PCA and the Escape Point are required
D6: Implement and Validate the Permanent Corrective Action
To successfully implement a permanent change, proper planning is essential. A project plan should encompass: communication, steps to complete, measurement of success and lessons learned. Activities in D6 include:
- Develop Project Plan for Implementation
- Communicate the plan to all stakeholders
- Validation of improvements using measurement
D7: Prevent Recurrence
D7 affords the opportunity to preserve and share the knowledge, preventing problems on similar products, processes, locations or families. Updating documents and procedures / work instructions are expected at this step to improve future use. Activities in D7 include:
- Review Similar Products and Processes for problem prevention
- Develop / Update Procedures and Work Instructions for Systems Prevention
- Capture Standard Work / Practice and reuse
- Assure FMEA updates have been completed
- Assure Control Plans have been updated
D8: Closure and Team Celebration
Teams require feedback to allow for satisfactory closure. Recognizing both team and individual efforts and allowing the team to see the previous and new state solidifies the value of the 8D process. Activities in D8 include:
- Archive the 8D Documents for future reference
- Document Lessons Learned on how to make problem solving better
- Before and After Comparison of issue
- Celebrate Successful Completion
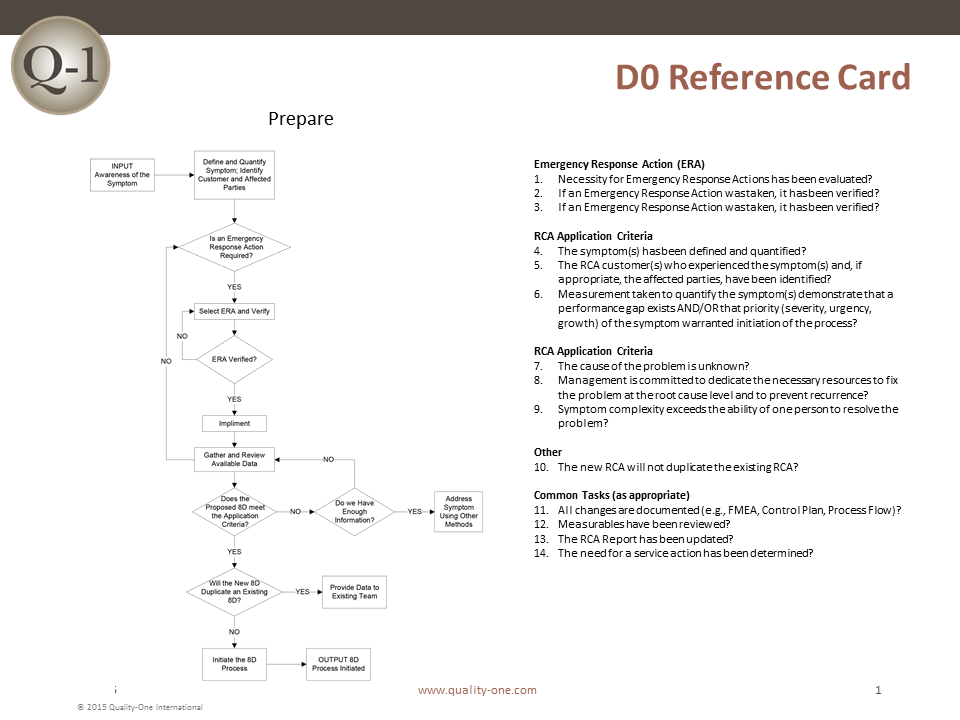
8D and Root Cause Analysis (RCA)
The 8D process has Root Cause Analysis (RCA) imbedded within it. All problem solving techniques include RCA within their structure. The steps and techniques within 8D which correspond to Root Cause Analysis are as follows:
- Problem Symptom is quantified and converted to “Object and Defect”
- Problem Symptom is converted to Problem Statement using Repeated Whys
- Possible and Potential Causes are collected using deductive tools (i.e. Fishbone or Affinity Diagram)
- Problem Statement is converted into Problem Description using Is / Is Not
- Problem Description reduces the number of items on the deductive tool (from step 3)
- Comparative Analysis between the Is and Is Not items (note changes and time)
- Root Cause theories are developed from remaining possible causes on deductive tool and coupled with changes from Is / Is Not
- Compare theories with current data and develop experiments for Root Cause Verification
- Test and confirm the Root Causes
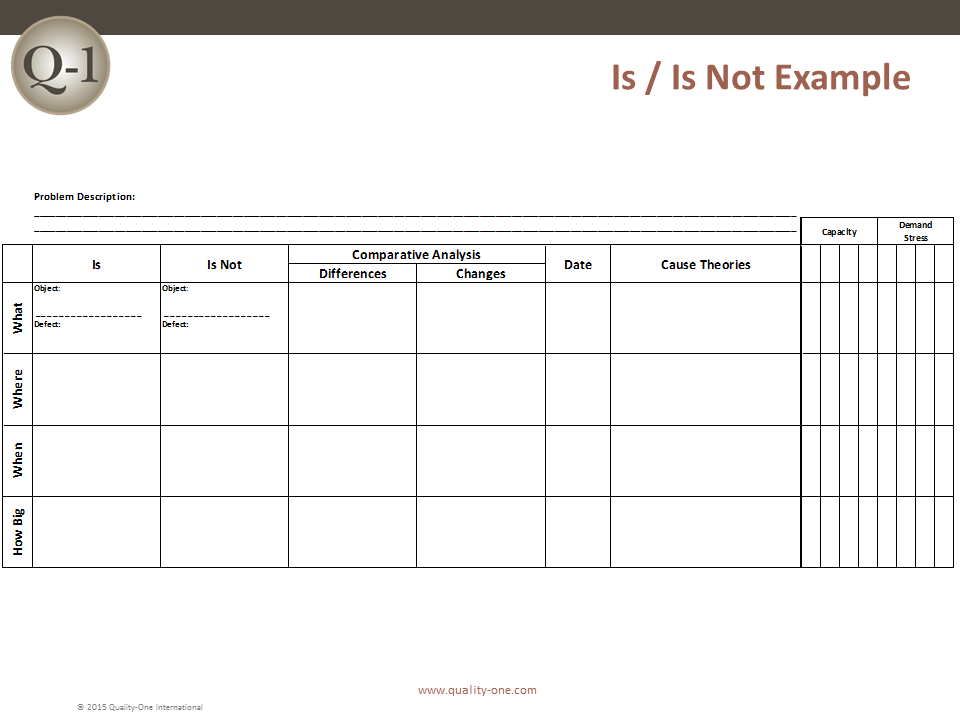
Example: Multiple Why Technique
The Multiple / Repeated Why (Similar to 5 Why) is an inductive tool, which means facts are required to proceed to a more detailed level. The steps required to determine problem statement are:
- Problem Symptom is defined as an Object and Defect i.e. “Passenger Injury”
- Why? In every case “SUV’s Roll Over”
- Why? In every case, it was preceded by a “Blown Tire”
- Why? Many explanations may be applied, therefore the team cannot continue with another repeated why past “Blown Tire”
- Therefore, the Problem Statement is “Blown Tire”
- Why? Low (Air) Pressure, Tire Defect (Degradation of an Interface) and High (Ambient) Temperature
- Counter measures assigned to low pressure and tire defect
This example uses only 4 of the 5 Whys to determine the root causes without going further into the systemic reasons that supported the failure. The Repeated Why is one way to depict this failure chain. Fault Tree Analysis (FTA) could also be used.
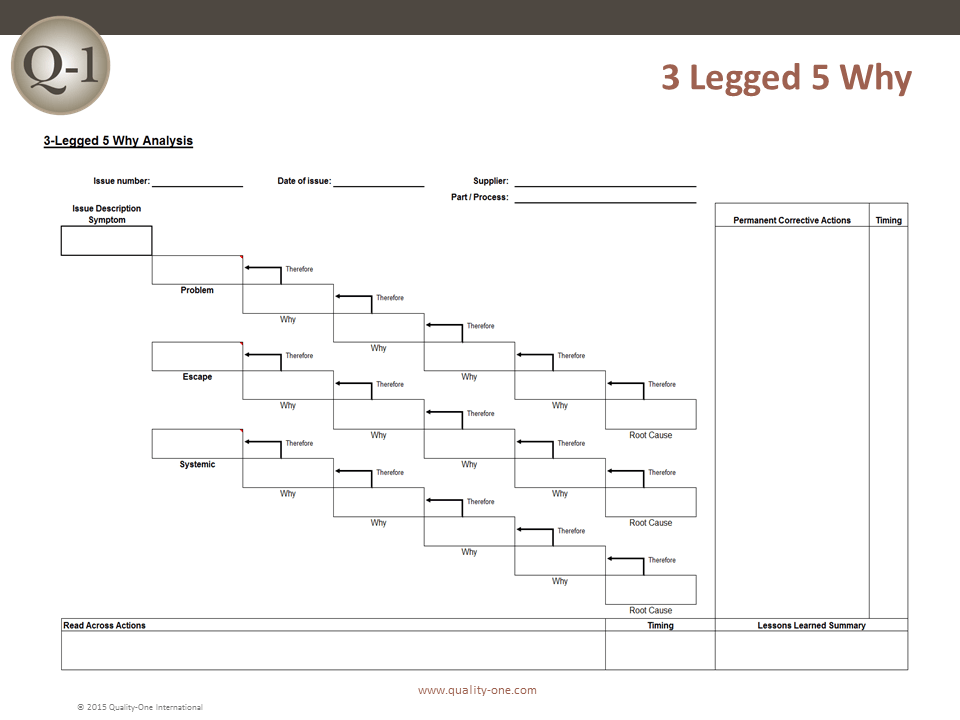
Learn More About Eight Disciplines of Problem Solving (8D)
Quality-One offers Quality and Reliability Support for Product and Process Development through Consulting, Training and Project Support. Quality-One provides Knowledge, Guidance and Direction in Quality and Reliability activities, tailored to your unique wants, needs and desires. Let us help you Discover the Value of 8D Consulting , 8D Training or 8D Project Support .
Contact Us | Discover the Value!
(248) 280-4800 | [email protected]
Remember Me
- Don't have an account? Register
- Lost your password? Click here
- Already have an account? Log in
- Submit an inquiry. We will answer all your questions!

Ishikawa Diagram – how effectively perform root cause analysis
Ishikawa Diagram, also known as the “fishbone”, is a qualitative tool that is often used during problem solving by the production plant.
Usually it’s used in the quality area, but it can also be successfully carried out in logistic, health and safety (ergonomics, accidents at work, etc.) and production analysis .
Most often, we can deal with it when using:
- 8D reports in step D4 – root cause analysis
- Kaizen methodology – with this approach, is used as 4M (Man, Machine, Method, Material) or 4M + 1D (Design)
It’s a great tool for the correct verification of the problem root cause, and thus, it determines its effectiveness. An additional benefit of using the Ishikawa diagram is that it is easy to learn and simple to use.
We must also remember that group problem-solving is a good practice, eliminating the pathology of the pseudo-one man show strategy. In the long run, this solution can lead to a reoccurrence of the problem and OEM client escalation.
Why are we mentioning this? Because the Ishikawa diagram strengthens teamwork, stimulating creative thinking. Its additional advantage is that it can be used immediately when a problem occurs and where it occurs (often referred to in the automotive industry as “gemba”).
Ishikawa Diagram – Category description
In the Ishikawa diagram, the most common are six categories that should be considered. Belong to them following areas:
- Man – in this category we verify qualifications, habits, job satisfaction, internship, well-being of the person or employee whose work led to the occurring problem
- Machine – in this category, we verify all aspects relating to the machine, which include among others, license, durability, modernity, efficiency, precision, safety and working conditions
- Material – here we consider components at the entrance to the production process and semi-finished products that occur in the inter-operational areas (named also as WIP – work in progress)
- Method – refers, among other things, to verification of procedures, instructions, specifications, standards, laws, rules, know-how and technology
- Measurements / Measurement system – in which it’s worth taking into account the incorrect or distorted indication of the measuring instrument
- Environment – that is the area where the following factors should be considered: temperature, humidity, pressure, lighting, noise, radiation
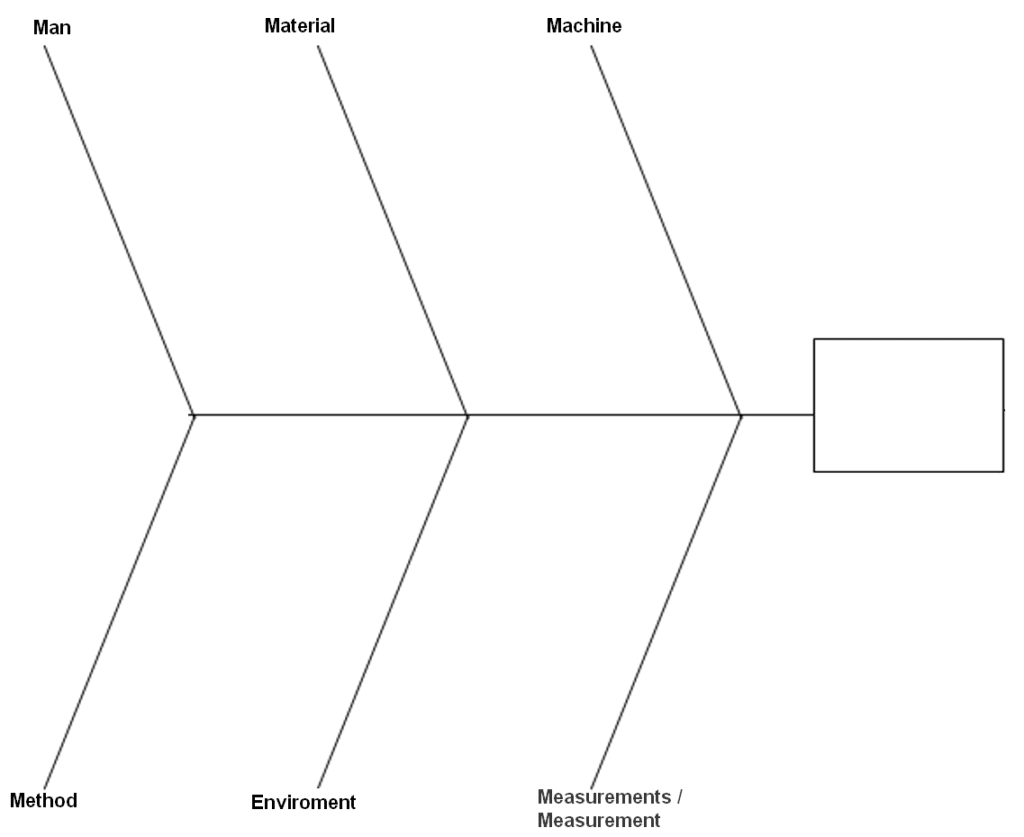
Figure 1. Ishikawa diagram – graphic presentation
More information on the practical application of the Ishikawa diagram is presented during dedicated training courses on the 8D and Kaizen methodology , to which we cordially invite you.

Download for FREE our E-BOOKS
- Members Login
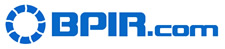
4M Problem Solving Method
Bpir categories, unlock this article and 10,000+ more.
To get the most out of our extensive resources, please login or become a member below.
Username or email address *
Password *
Forgot your password?
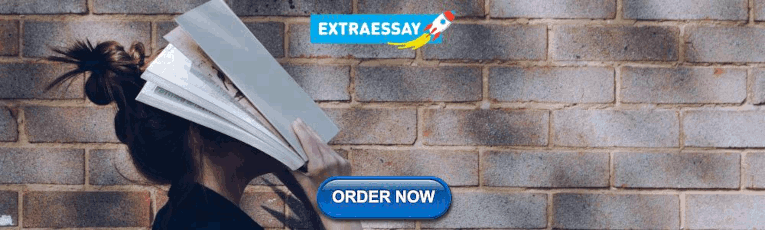
IMAGES
VIDEO
COMMENTS
For this information, using a 4M is about improving a specific problem even outside a corporate world or any aspect. Part 3: Examples of 4Ms. This part will see the different kinds of 4M methods. A few of these examples are the 4M's Operation Management, 4M's Quality Management, and 4M's continuous Skill Development.
The 4M analysis is a problem-solving method used to identify the root cause of a problem or defect in a process. It is based on the premise that most problems can be traced back to one or more of the following four elements: Man: This refers to the human factors involved in the process, such as operators, supervisors, or other personnel.
4M Analysis Process. The purpose of this procedure is to define the steps to do a 4M Analysis of a system or subsystem. The goal of this 4M Analysis Procedure is to reduce losses in the factory by using the Equipment Attributes as a guideline to achieve this end. Focused Improvement training can be taken here.
4M Analysis is an example industrial use case method of problem-solving and risk management. This type of use case is very common in manufacturing and allows you to identify and classify the causes of a problem that impact a specific theme: Material, Method, Machine, Man.
The 4M method is a testament to the power of simplicity and structure in problem-solving. By systematically addressing issues related to Man, Method, Material, and Machine, organizations can demystify complex problems, transforming them into manageable elements, actionable insights, and eventually, effective solutions.
The 4M method is a simple problem-solving tool that allows us to brainstorm, identify, and group potential factors that cause problems. To be more effective during the implementation of 4M method (), we could use an additional Checklist.The 4M Checklist is an essential part of completing the perfect implementation of the 4M method.
4M Analysis. The 4M analysis is a method for evaluation which of the 4M conditions is responsible for a defect mode. Most commonly practiced is the Fishbone / Ishikawa Diagram. This is a tool designed to identify, explore, and graphically display the possible causes related to a problem or condition.
4M in production is understood as a rule determining factors affecting business processes created by Kaoru Ishikawa (Japanese philosopher). The application of the 4M rules helps businesses find the causes and solutions to improve work quality and productivity. This rule consists of 4 main elements: Materials, Man, Machine, and Methods.
4M Principle. The 4M principle is a management concept that stands for Man, Machine, Material, and Method. It refers to the four essential elements that are required for any production process to take place. The 4M principle provides a framework for identifying and addressing the key factors that contribute to the efficiency and effectiveness ...
The 4M method is widely used in manufacturing for troubleshooting and risk management. It categorizes issues impacting operations into Materials, Methods, Machines, or Manpower. Any 4M-related problem can result in errors or downtime, emphasizing the need for clear improvement definitions, identification of potential issues, and prompt resolution.
Propose and Make Improvements. In this eighth and final P-M Analysis step, teams propose make any correlations and improvements required for each abnormality, then plan and institute appropriate preventive measures. Review the operationalProcedures. Review the cleaningprocedures. Review the inspection procedures. Training for changes.
method was to examine in detail the analysed problem, before the next stage of the analysis, i.e. looking for the cause or causes of the problem using the 4M method. The result of applying the 5W1H method to the analysed problem was shown in Table 1. Table 1. 5W1H Analysis Sheet to Describe the Problem in the Quality Control Process in more detail.
By conducting a 4M Analysis it is possible to analyse all four main factors that contribute to the success or failure of a specific industrial process. 4M Analysis Benefits Examining all 4M's will help to understand a particular problem and obtain valuable insights about in which areas improvements can be made.
Design for Assembly (DfA) is a well-known technique that supports in the reduction of manufacturing costs. Traditional DfA methods are generally focused on the product design lacking of a holistic view. The proposed 4 M approach takes into account all the most important aspects involved in the manual assembly: Method, Machine, Man and Material.
An excellent example of the use of the 4M Problem Solving Method. After retirement a Quality Management expert took on the responsibility of handling the household laundry. In this article he describes how he used the 4M Problem Solving methodology to address problems he encountered. The Cause and Effect Fishbone diagram is included in the article.
The 4M methodology is a simple, versatile, and practical problem-solving approach that can help startups improve their processes and achieve better outcomes. Whether you're dealing with a minor ...
Lean Manufacturing Terms - 4M. 13,446 views. 1 min read. 4M (Man, Machine, Material, Method): Common structure for potential causes for Problem Solving methods, for example as the bones of the fish-bone diagram (see Ishikawa Diagram). This is often expanded into 8M, including additionally management, milieu, measurement, and money.
Ishikawa diagrams (also called fishbone diagrams, herringbone diagrams, cause-and-effect diagrams) are causal diagrams created by Kaoru Ishikawa that show the potential causes of a specific event.. Common uses of the Ishikawa diagram are product design and quality defect prevention to identify potential factors causing an overall effect. Each cause or reason for imperfection is a source of ...
The 8D problem solving process is a detailed, team oriented approach to solving critical problems in the production process. The goals of this method are to find the root cause of a problem, develop containment actions to protect customers and take corrective action to prevent similar problems in the future. The strength of the 8D process lies ...
The article presents a case study on the use of specially prepared 5W-1H and 4M sheets for the analysis of the problem during the visual inspection process of the electric device, in order to ...
by Kaufman Global. The 6Ms of production - Manpower, Method, Machine, Material, Milieu and Measurement - is a mnemonic representing the characteristic dimensions [1] to consider when brainstorming during "cause and effect" problem-solving sessions. Capture and bin the issues (causes) under the 6M categories.
Kaizen methodology - with this approach, is used as 4M (Man, Machine, Method, Material) or 4M + 1D (Design) ... We must also remember that group problem-solving is a good practice, eliminating the pathology of the pseudo-one man show strategy. In the long run, this solution can lead to a reoccurrence of the problem and OEM client escalation. ...
4M Problem Solving Method. A Problem Solving Tool BPIR Categories 10.2.4 Use analytical (predictive/ text / statistics) techniques on data 14.1.5 Analyse performance data. Unlock this article and 10,000+ more. To get the most out of our extensive resources, please login or become a member below.