How to prepare for JLPT
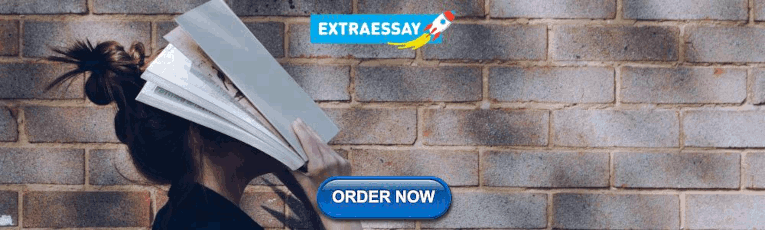
How to Say ‘I’m Confused’ and Discuss Confusion in Japanese
Confusion is a common human experience, and being able to express it in another language can facilitate effective communication and problem-solving. In Japanese culture, politeness and clarity in communication are highly regarded, even when discussing complex emotions like confusion. In this blog post, we’ll explore how to say ‘I’m confused’ and discuss confusion in Japanese, along with cultural nuances to ensure your conversations are both polite and constructive.
- Saying ‘I’m Confused’ in Japanese
1.1. 分からない (Wakaranai) – I don’t understand / I’m confused. This is a straightforward and commonly used expression to convey confusion in Japanese .
1.2. 混乱しています (Konran shiteimasu) – I’m in a state of confusion. Use this expression when you want to emphasize your confusion, especially in a more formal context.
- Discussing Confusion in Japanese
2.1. 混乱 (Konran) – Confusion When discussing confusion, this term is commonly used to describe the state of being confused.
2.2. 困惑 (Konwaku) – Perplexity This word can be used to express a deeper sense of confusion or bewilderment.
- Cultural Considerations
3.1. Politeness Politeness is essential in Japanese culture. When discussing confusion, it’s important to use polite expressions to convey your feelings respectfully.
3.2. Problem-Solving Japanese culture often emphasizes the importance of finding solutions to problems, even when discussing confusion.
3.3. Respect for Authority In formal or hierarchical situations, it’s important to express confusion respectfully, especially when dealing with authority figures.
- Using Confusion Phrases in Context
4.1. Expressing Confusion Use “分からない (Wakaranai)” or “混乱しています (Konran shiteimasu)” when you want to politely express that you don’t understand or you’re confused about something.
4.2. Describing Confusion When discussing confusion, use “混乱 (Konran)” to describe the state of being confused. For example, “その説明に混乱しました (Sono setsumei ni konran shimashita)” means “I became confused by that explanation.”
4.3. Expressing Perplexity Employ “困惑 (Konwaku)” to express a deeper sense of confusion or bewilderment. For instance, “彼の行動に困惑しています (Kare no koudou ni konwaku shiteimasu)” means “I’m perplexed by his actions.”
- Navigating Confusion in Japan
5.1. Seek Clarification In Japan, if you’re confused about something, it’s perfectly acceptable to politely ask for clarification or further explanation.
5.2. Problem-Solving Approach Embrace Japan’s problem-solving culture by working collaboratively with others to find solutions to confusing situations.
Discussing confusion in Japanese culture is an opportunity to engage in polite and constructive conversations about a common human experience. By using the appropriate phrases and expressions, you can convey your sense of bewilderment while respecting the cultural nuances related to politeness and problem-solving. Whether you’re seeking clarification, navigating confusion in Japan, or simply expressing your perplexity, adhering to Japanese customs for discussing confusion ensures your conversations are both polite and constructive.
My Recommendations for your Japanese learning
- Japanese Pod 101 My Honest Review Read more
- JLPT N5 Test Prep-course - The Expert Secret Check Out
Related Posts
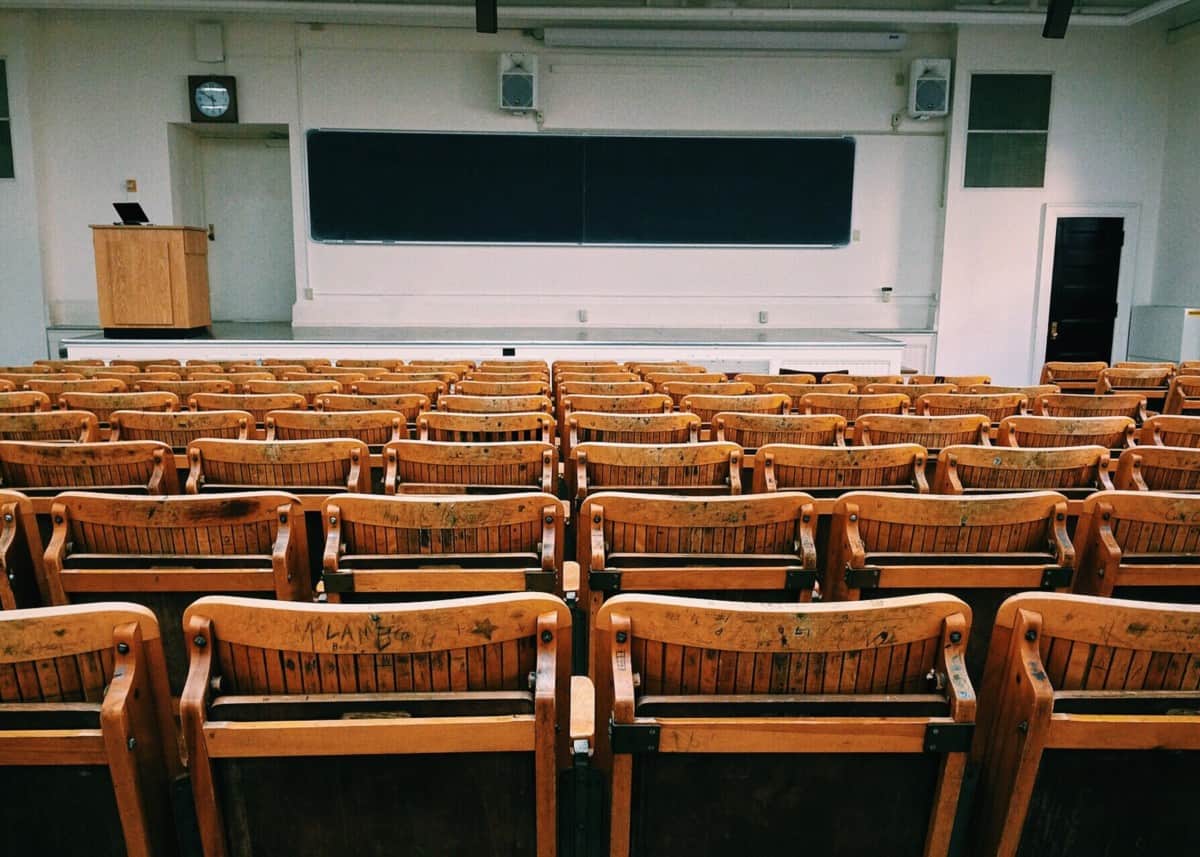
How to Prepare for JLPT N4 and Pass the Test in 6 Months
The Japanese Language Proficiency Test (JLPT) N4 refers to one of the series of tests that are conducted to evaluate…
JLPT N5 Grammar: の (no) Possessive Particle Meaning
It is essential to learn Japanese vocabulary when studying the language. In addition to words borrowed from other languages, Japanese…
Embracing Ambition: Saying ‘I’m Feeling Ambitious’ and Discussing a Strong Desire to Achieve in Japanese
Introduction Feeling ambitious is a state of determination and a strong desire to achieve one’s goals. In Japanese culture, acknowledging…

Japanese Multidimensional Problem Solving

In the West, the standard approach for problem solving is to take a good look a the problem, after which a solution approach will pop into someone’s head. This approach is then optimized until the problem is solved. However, while this often ends up with one solution, it usually is far from the best solution possible. In Japan, a very different multidimensional problem-solving approach is common. Rather than just use any solution that solves the problem, they aim for the best solution they can find.
There are a number of well-known Japanese problem-solving techniques for managing issues and finding their root cause. This post will focus on the multidimensional decision used to find a solution, which is surprisingly simple and highly successful but still mysterious to many westerners.
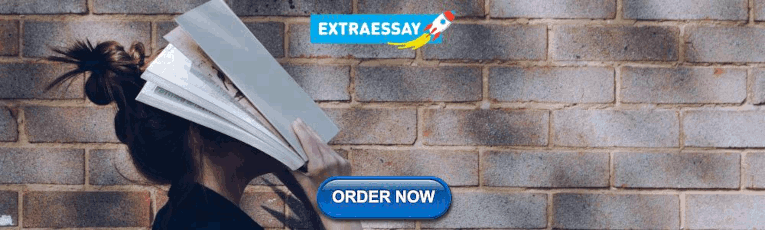
Problem-Solving Environment
Let’s first review a few of the well-known methods in the Japanese problem-solving toolbox:
Problem Solving Overview: A3
The A3 is named after an A3 sheet of paper, since the goal is to fit all information related to the problem solving on one sheet of paper. Ideally, the sheet should be a working document and hence handwritten, but in the West a computer document is often preferred. There is no fixed list of points that go on the A3, but it usually includes:
- A description of the problem
- The current state
- The goal of the problem solving
- A root cause analysis
- A progress status
- Confirmation of problem solution
- Organizational information like responsible parties, date, approval, etc.
Root Cause: 5 Whys
The 5 Whys method is based on Taiichi Ohno’s approach, at Toyota, of asking “Why?” five times in a row. The goal is not to accept the first answer but rather to dig deeper to fully understand the root cause of the problem.
Root Cause: Fishbone Diagram
Finally, there is the Fishbone Diagram , also known as the herring-bone diagram or cause-and-effect diagram . If you want to sound fancy, you could also say Ishikawa Diagram . Few people will understand, but it makes you look impressive. The aim is to address the problem from multiple different directions, graphically represented by a fishbone. The head is the problem, and the bones are the individual possible causes that are analyzed. The causes can be specific to the particular problem, but in industry, the following are also common:
- Measurement
- Mother Nature

As said above, in the Western world one problem solution is selected and then optimized until it solves the problem. However, in Japan, an approach with a multitude of different solutions is common. Especially for complex problems, this multidimensional approach yields much better results than a Western uni-dimensional way.
Let’s take, for example, the development of the Toyota Prius hybrid gasoline–electric vehicle. The goal of Toyota was to develop a new highly environmentally friendly vehicle. Western car makers had long ago decided to pursue the hydrogen fuel cell as the basis for such vehicles, and spent many years in vain trying to get those vehicles functioning well even as prototypes.
Toyota, on the other hand, did not decide what type of vehicle they wanted upfront. Rather, under the leadership of Takehisa Yaegashi, they evaluated different design possibilities. In their first round, they looked at a whopping eighty different possibilities to power the car, including electric, gasoline–electric hybrid, diesel–electric hybrid, high-efficiency diesel engines, high-efficiency gasoline engines, liquid hydrogen fuel cells, gaseous hydrogen fuel cells, and many more.
They evaluated each one to some extent before they selected around thirty design options that had more potential. These thirty designs then went into the next round, with more detailed analysis, simulations, and evaluations, and were narrowed down to the ten designs that went into the last round. Those ten designs were each looked at in even more detail with even more analyses, and then the gasoline–electric hybrid emerged as the winner and the power system for the Prius model.
The resulting product was a wild success for Toyota. While other well-established car companies with years of fuel-cell research initially laughed at the weird concept, they didn’t laugh for long. The Prius became a bestseller, within two years even a profitable bestseller, and it gave a huge boost to Toyota’s image as advanced and eco-friendly. Other car makers then scrambled to copy the success, but they are still one to two years behind Toyota with their vehicles.
Do I have to come up with eighty different solutions for all my problems now?
Of course, the size of the solution space and the effort put into has to be in reason with the size of the problem. The development of a new car costs between one and six billion dollars (that’s right, billion, not million). Hence, before investing enough money to buy a small country, it is well worth it to evaluate all options before placing your bet.
On the other hand, if your problem is smaller, you may work with fewer design evaluations. One problem where I have repeatedly used this approach with much success is organizing the layout of a plant or a plant section. Rather than moving all hardware around on a floor plan until it fits, I prefer to create different plans instead.
Using a multi-functional team with members from management, operations, planning, and production, I create multiple solutions. If the team is large enough, I even split them into groups of three to four people (a great size for teamwork) and have them create designs independently . Hence, I end up with two or thee designs in the first round. I intentionally keep the members on a very tight schedule, since at this stage I want only a rough sketch rather than a detailed and installation-ready plan. Thirty to sixty minutes is plenty for this purpose.
Next, we compare the designs, pushing people along the learning curve for this particular layout problem. Afterward the teams are mixed and given certain requirements for the second round. In my experience, after two rounds with four to six different designs, the teams have explored the possible design space much better than they possibly could have with a single design.
As a next step, we could either select the winner (inevitably one of the designs from the last row), or—my preference—have all team members come together and build the best design based on the four to six designs we have so far. Overall, with less than ten people and less than one workshop day, we create a new shop floor layout that everybody feels good with and that incorporates the best ideas out of multiple designs.
I have personally used this multidimensional approach to problem solving successfully for many different problems, including shop floor layout, part design, information flow design, efficiency improvements, and many more. This approach has never failed me.
I sincerely hope that this method will also help you with your daily work, and I wish you much success. Now, go out and improve your Industry.
6 thoughts on “Japanese Multidimensional Problem Solving”
This post very succinctly goes beyond the machine-like application of “success” tools and shows that it all depends on working together.
“succinctly” … such a beautiful word 🙂
Thanks for the praise!
Great effort and innovative techniques !! Welldone dear.
Great and insightful
Innovative techniques and just class
Easy solution techichque and just class
Leave a Comment
Notify me of new posts by email.
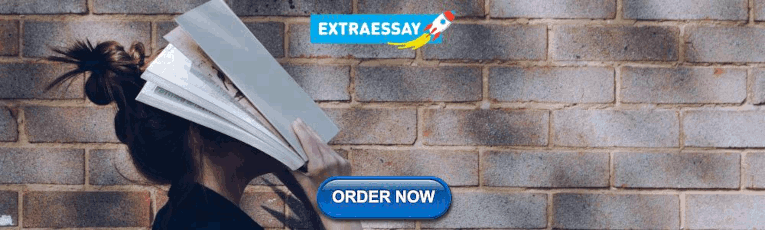
IMAGES
VIDEO
COMMENTS
5.2. Problem-Solving Approach Embrace Japan’s problem-solving culture by working collaboratively with others to find solutions to confusing situations. Conclusion. Discussing confusion in Japanese culture is an opportunity to engage in polite and constructive conversations about a common human experience. By using the appropriate phrases and ...
Problem-Solving Environment. Let’s first review a few of the well-known methods in the Japanese problem-solving toolbox: Problem Solving Overview: A3. The A3 is named after an A3 sheet of paper, since the goal is to fit all information related to the problem solving on one sheet of paper. Ideally, the sheet should be a working document and ...
What is the translation of "problem-solving" in Japanese? en. volume_up. problem-solving = ja 問題解決. Translations Translator Phrasebook open_in_new. EN.