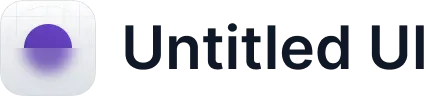
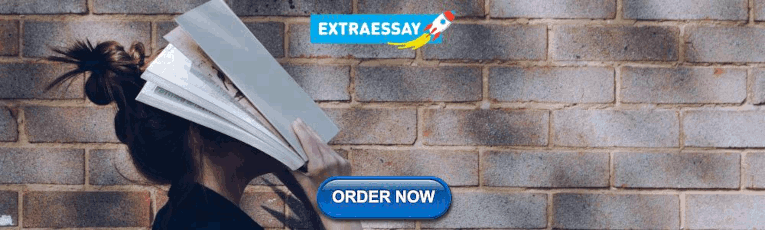
How Zara’s strategy made her the queen of fast fashion
Table of contents, here’s what you’ll learn from zara's strategy study:.
- How to come up with disruptive ideas for your industry.
- How finding the right people is more important than developing the best strategy.
- How best to address the sustainability question.
Zara is a privately held multinational clothing retail chain with a focus on fast fashion. It was founded by Amancio Ortega in 1975 and it’s the largest company of the Inditex group.
Amancio Ortega was Inditex’s Chairman until 2011 and Zara’s CEO until 2005. The current CEO of Zara is Óscar García Maceiras and Marta Ortega Pérez, daughter of the founder, is the current Chairwoman of Inditex.
Zara's market share and key statistics:
- Brand value of $25,4 billion in 2022
- Net sales of $19,6 billion in 2021
- 1,939 stores worldwide in 2021
- Over 4 billion annual visits to its website
- Inditex employee count of 165,042 in 2021
{{cta('ba277e9c-bdee-47b7-859b-a090f03f4b33')}}
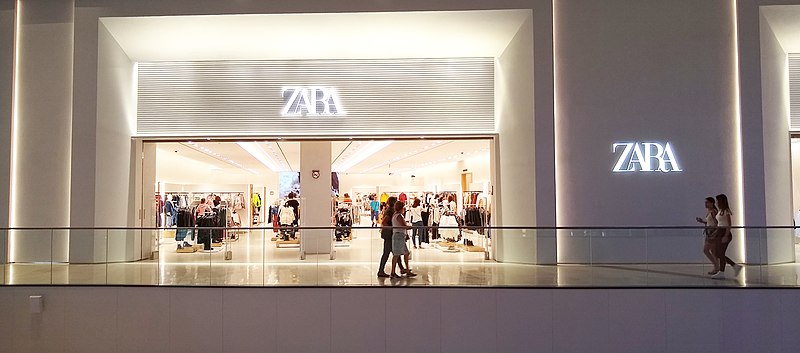
Humble beginnings: How did Zara start?
Most people date Zara’s birth to 1975, when Amancio Ortega and Rosalia Mera, his then-wife, opened the first shop. But, it’s impossible to study the company’s first steps, its initial competitive advantage, and strategic approach by starting at that point in time.
When the first Zara shop opened, Amancio Ortega already had 22 years of industry experience, ten years as a clever and hard-working employee, and 12 years as a business owner. Rosalia Mera also had 20 years of industry experience.
As an employee , Ortega worked in the clothing industry, first as a gofer and then as a delivery boy. He quickly demonstrated great talent for recognizing fabrics, understanding and serving customers, and making sound business suggestions. Soon, he decided to use his insights to develop his own business instead of his boss’s.
As a business owner , he started GOA Confecciones in 1963, along with his siblings, his wife, and a close friend. They started with a humble workshop making women’s quilted dressing gowns, following a trend at the time Amancio had noticed. Within ten years, that workshop had grown to support a workforce of 500 people.
And then, the couple opened the first Zara shop.
Zara’s competitive positioning strategy in its first year
The opening of the first Zara shop in 1975 wasn’t just a new store to sell clothes. It was the final big move of a carefully planned vertical integration strategy.
To understand how the strategy was formulated , we need to understand Amancio’s first steps. His first business, GOA Confecciones, was a manufacturing business. He was supplying small stores and businesses with his products, and he wasn’t in contact with the end customer.
That brought two challenges:
- A lack of insight into market trends and no direct consumer feedback about preferences.
- Very low-profit margins compared to the 70-80% profit margin of retailers.
Amancio developed several ideas to improve distribution and get a direct relationship with the final purchaser. And he was always updating his factories with the latest technological advancements to offer the highest quality of products at the lowest possible price. But he was missing one essential part to reap the benefits of his distribution practices: a store .
So, in 1972 he opened one under the brand name Sprint . An experiment that quickly proved unsuccessful and, seven years later, was shut down. Although it’s unknown the extent to which Amancio put his ideas to the test, Sprint was a private masterclass in the retail world that gave Amancio insights that would later turn Zara into a global success.
Despite Sprint’s failure, Amancio didn’t abandon the idea of opening his own store mainly because he believed that his advanced production model was vulnerable and the rise of a competitor who could replicate and improve his system was imminent.
Adding a store to his vertical integration strategy would have a twofold effect:
- The store would operate as a direct feedback source. The company would be able to test design ideas before going into mass production while simultaneously getting an accurate pulse of the needs, tastes, and fancies of the customers. The store would simultaneously reduce risk and increase opportunity spotting.
- The company would have reduced operating costs as a retailer. Since the group would control all aspects of the process (from manufacturing to distribution to selling), it would solve key retail challenges with stocking. The savings would then be passed on to the customer. The store would have an operational competitive advantage and become a potential cash cow for the company.
The idea was to claim his spot in prime commercial areas (a core and persistent strategic move for Zara) and target the rising middle class. The market conditions were tough, though, with many family-owned businesses losing their customer base, giant players owning a huge market share, and Benetton’s franchising shops stealing great shop locations and competent potential managers.
So the first Zara store had these defining characteristics that made it the successful final piece of Amancio’s strategy:
- It was located near the factory = delivery of products was optimized
- It was in the city’s commercial heart = more expensive, but with access to affluence
- It was located in the city where Ortegas had the most customer experience = knowing thy customer
- It was visibly attractive = expensive, but a great marketing trick
Amancio’s team lacked experience and expertise in one key factor: display window designing . The display window was a massive differentiator and had to be bold and attractive. So, Amancio hired Jordi Bernadó, a designer with innovative ideas whose work transformed display windows and the sales process.
The Zara shop was a success, laying the foundations for the international expansion of the Inditex group.
Key Takeaway #1: Challenge your industry’s conventional wisdom to create a disruptive strategy
Disrupting an industry isn’t an easy task nor a frequent occurrence.
To do it successfully, you need to:
- Understand the prominent business mode of your industry and the forces that contributed to its development.
- Challenge the assumptions behind it and design a radically different business model.
- Develop ample space for experimentation and failures.
The odds of instantly conquering the industry might be low (otherwise, someone would have already done it), but you’ll end up with out-of-the-box ideas and a higher sensitivity to potential disruptors in your competitive arena.
Recommended reading: How To Write A Strategic Plan + Example
How Zara’s supply chain strategy is at the core of its business strategy
According to many analysts, the Zara supply chain strategy is its most important innovative component.
Amancio Ortega and other senior members of the group disagree. Nevertheless, the Inditex logistics strategy is extraordinarily efficient and plays a crucial role in sustaining its competitive advantage. Most companies in the clothing retail industry take an average of 4-8 weeks between inception and putting the product on the shelf. The group achieves the same in an average of two weeks. That’s nothing short of extraordinary.
Let’s see how Zara developed its logistics and business strategy.
Innovative logistics: how Zara’s supply chain evolved
The logistics methods developed by companies are highly dependent on external factors.
Take, for example, infrastructure. In the early days of Zara, when it was expanding through Spain, the company considered using trains as a transportation system. However, the schedule couldn’t keep up with Zara’s needs, which had the goal of distributing products twice a week to its shops. So transportation by road was the only way.
However, when efficiency is a high priority, it shapes logistics processes more than anything else.
And for Zara, efficient logistics was – and still is – of the highest priority.
Initially, leadership tried outsourcing logistics, but the experiment failed and the company assigned a member of the house with a thorough knowledge of the company's operating philosophy to take charge of the project. The tactic of entrusting important big projects to employees imbued with the company’s philosophy became a defining characteristic.
So, one of Zara’s early strategic decisions was that each shop would make orders twice a week. Since the first store was opened, the company has had the shortest stock rotation times in the industry. That’s what drove the development of its logistics methods. The whole strategy behind Zara relied on quick production and distribution. And the proximity of manufacturing and distribution was essential for the model to work. So Zara had these two centers in the same place.
Even when the brand was expanding around the world, its logistics center remained in Arteixo, Spain, despite being a less-than-ideal location for international distribution. At some point, the growth of the brand, and Inditex as a whole, outpaced Arteixo’s capacity, and the decentralization question came up.
The debate was tough among leadership, but the arguments were strong. Decentralization was necessary because of:
- Safety and security. If there was a fire or any other crippling disaster there (especially on a distribution day), then the company would face serious troubles on multiple fronts.
- Arteixo’s limitations. The company’s center in Arteixo was reaching its capacity limits.
So the company decided to decentralize the manufacturing and distribution of its brands.
Initially, the group made the decision to place differentiated logistics centers where the management of its chain of stores was based, i.e. Bershka would have a different logistics center than Pull&Bear, although they were both part of the Inditex Group. That idea emerged after Massimo Dutti and Stradivarius became part of Inditex. Those brands already had that geographical structure, and since the group integrated them successfully into its strategy and logistics model, it made sense to follow the same pattern with its other brands.
Besides, the proximity of the distribution centers to the headquarters of each brand allowed them to consolidate them based on the growth strategy and purpose of each brand (more on this later).
But just a few years after that, the group decided to build another production center for Zara that forced specialization between the two Zara centers. The specialization was based on location, i.e. each center would manufacture products that would stock the shelves of stores in specific locations.
Zara’s supply chain strategy is so successful because it’s constantly evolving as the group adapts to external circumstances and its internal needs. And just like its iconic fashion, the company always stays ahead of the logistics curve.
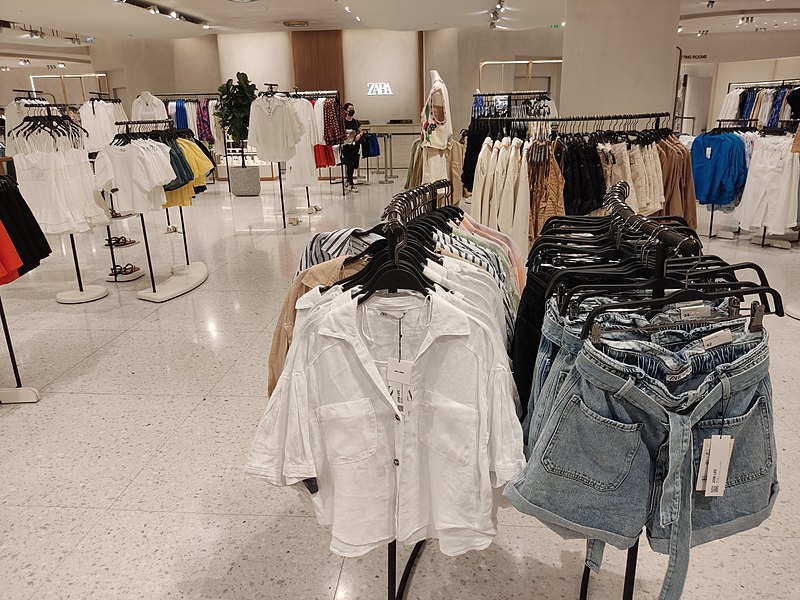
Zara’s business strategy transcends its logistics innovations
Zara’s business strategy relies on four key pillars:
- Flexibility of supply
- Instant absorption of market demand
- Response speed
- Technological innovation
Zara is the only brand in the Inditex group that is concerned with manufacturing. It’s the first brand in the clothing sector with a complete vertical organization. And the production model requires the adoption or development of the latest technological innovations.
This requirement is counterintuitive in the clothing sector.
Most people believe that making big investments in a market as mature as clothing is a bad idea. But the Zara production model is very capital and labor intensive. The technological edge derived from that investment gave the company, in the early days, the capability to manufacture over 50% of its own products while maintaining an extremely high stock rotation frequency.
Zara might be one of the best logistics companies in the world, but that particular excellence is a supporting factor, or at least a highly contributing factor, to its successful business strategy.
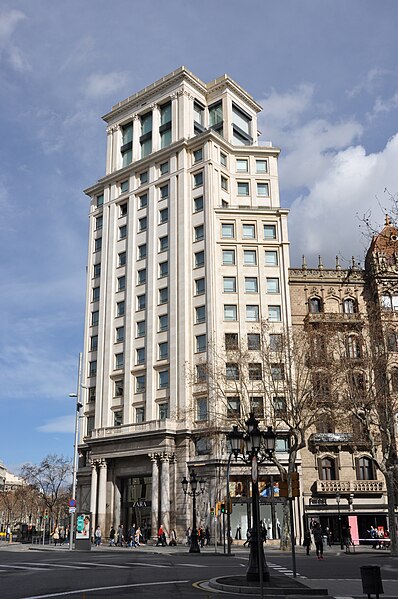
Zara’s business strategy is so much more than its supply chain strategy.
The company created the “fast fashion” term and industry. When other companies were manufacturing their collections once per season, Zara was adapting its collection to suit what people asked for on a weekly basis. The idea was to offer fashionable items at a fair price and faster than everybody else.
Part of its cost-cutting strategic priority was its marketing strategy. Zara didn’t – and still doesn’t – advertise like the rest of the clothing industry. Its marketing strategy starts with choosing the location of the stores and ends with advertising that the sales period has started. In the early years of the brand’s expansion, Amancio would visit potential store locations himself and choose the site to build the Zara shop.
The price was never an issue. If the location was in a commercial center, Zara would build its store there no matter how high the cost was because the company expected to recoup it quickly with increased sales.
Zara’s marketing is its own stores.
The strategy of Zara and her Inditex sisters
Despite Zara’s success (or because of it), Amancio Ortega created – or bought – multiple other brands that he included in the Inditex group, each one with a specific purpose.
- Zara was targeting middle-class women.
- Pull&Bear was targeting young people under twenty-five years old with casual clothing.
- Bershka was targeting rebel teens, especially girls, with hip-hop-style clothing.
- Massimo Dutti was targeting both sexes with more affluence.
- Stradivarius was competing with Bershka, giving Inditex two major brands in the teenage market.
- Oysho was concentrating on women's lingerie.
- Zara Home manufactures home textiles and decor.
Pull&Bear was initially targeting young males between the ages of 14 and 28. Later it extended to young females of the same age and focused on selling leisure and sports clothing. It has the slowest stock turnaround time in the group.
Bershka’s target group was girls between 13 and 23 years of age with highly individualized tastes. Prices were low, but the quality average. Almost a fiasco in the beginning, it underwent a successful strategic turnaround becoming today one of the biggest growth opportunities for the group. And out of all the Inditex chains, Bershka has the most creative designs.
Massimo Dutti was the first retail brand Amancio bought and didn’t create himself. Its strategy is very different from Zara, producing high-quality products and selling them at a high price. It’s an extension of the group’s offer to the higher end of the price spectrum in the fashion industry. It’s also the only Inditex chain brand that advertises regularly.
Stradivarius was the second acquired brand, with the purchase being a defensive move. The chain shares the same target group with Bershka, making it, to this day, a direct competitor.
Oysho started as an underwear and lingerie company. Its product lines evolved to include comfortable night and homewear along with swimwear and a very young children’s line. The brand’s strategy was aggressive from its conception, opening 286 stores in its first six years of existence.
Zara Home is the youngest brand in the Group and the only one outside the clothing sector, though still in the fashion industry. It was launched with the least confidence and with immense prior research. An experiment to extend the Zara brand beyond clothing, it was based on the conservative view that Zara could extend its product categories only to textile items for the home. But it turned out that customers were more accepting of Zara Home selling a wide variety of domestic items. So the brand made a successful strategic pivot.
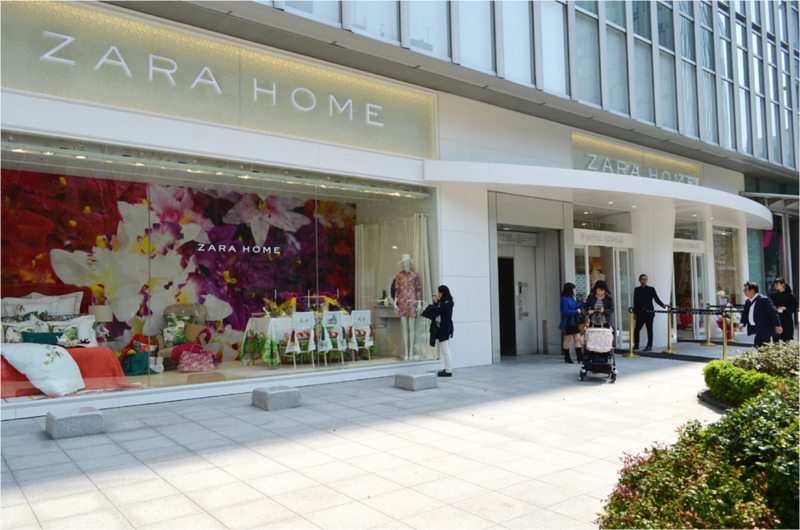
Key Takeaway #2: The right people are more important than the best strategy
It might not be obvious in the story, but a key reason for Zara's and Inditex’s success has been the people behind them.
For example, a vast number of people in various positions from inside the group claim that Inditex cannot be understood without Amancio Ortega. Additionally, major projects like the development of Zara’s logistics systems and the group's international expansion had such a success precisely because of the people in charge of them.
Zara’s radically different model was a breakthrough because:
- Its leadership had a clear vision and a real strategy to execute it.
- People with a deep understanding of the company’s philosophy led Its largest projects.
Sustainability: Zara’s strategy to make fast fashion sustainable
Building a sustainable business in the fast fashion industry is a tough nut to crack.
To achieve it, Inditex has made sustainability a cornerstone of its business model. Its strategy revolves around the values of collaboration , transparency, and innovation . The group’s ambition is to make a positive impact with a vision of prosperity for the planet and its people by transforming its value chain and industry.
Inditex’s sustainability commitments and strategy to achieve them
Inditex has developed a sustainability roadmap that extends up to 2040 with ambitious goals. Specifically, it has committed to
- 100% consumption of renewable energy in all of its facilities by 2022 (report pending).
- 100% of its cotton to originate from more sustainable sources by 2023.
- 100% of its man-made cellulosic fibers to originate from more sustainable sources by 2023.
- Zero waste from its facilities by 2023.
- 100% elimination of single-use plastic for customers by 2023.
- 100% collection of packaging material for recycling or reuse by 2023.
- 100% of its polyester to originate from more sustainable sources by 2025.
- 100% of its linen to originate from sustainable sources by 2025.
- 25% reduction of water consumption in its supply chain by 2025.
- Net zero emissions by 2040.
The group’s commitments extend beyond environmental issues to how its manufacturing and supplying partners conduct their business . To bring its strategy to fruition, it has set up a new governance and management structure.
The Board of Directors is responsible for approving Inditex’s sustainability strategy. The Sustainability Committee oversees and controls all the proposals around the social, environmental, health, and safety impact of the group’s products, while the Ethics Committee makes sure operations are compliant with the rules of conduct. There is also a Social Advisory Board that includes external independent experts that advises Inditex on sustainability issues.
Finally, Javier Losada, previously the group’s Chief Sustainability Officer and now promoted to Chief Operations Officer, will be leading the sustainability transformation of the group. Javier Losada first joined Inditex back in 1993 and ascended its rank to reach the C-suite.
Inditex is dedicated to its commitment to reducing its environmental impact and seems to be headed in the right direction. The only question is whether it’s fast enough.
Key Takeaway #3: Integrating sustainability with business strategy is a present-day necessity
Governments and international bodies around the world are implementing more stringent environmental regulations, forcing companies to commit to ambitious goals and developing a realistic strategy to achieve them.
The companies that are impacted the least are those that always had sustainability as a high priority .
From the companies that require significant changes in their operations to comply with the new regulations, only those who integrate sustainability into their business strategy and model will succeed.
Why is Zara so successful?
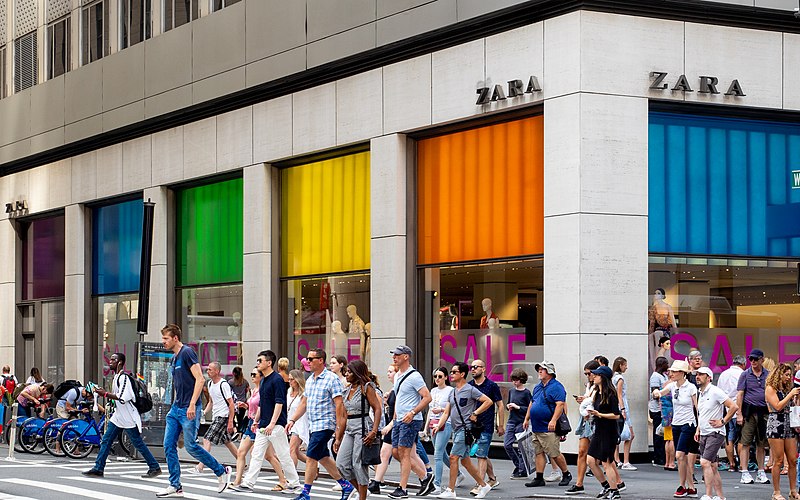
Zara is the biggest Spanish clothing retailer in the world based on sales value. Its success is due to its fast fashion strategy that is based on a strong supply chain and quick market feedback loops.
Zara's customer-centric approach places a strong emphasis on understanding and responding to customer needs and preferences. This is reflected in the company's product design, marketing, and customer service strategies.
Zara made fashionable clothes accessible to the middle class.
Zara’s vision guides its future
Zara's vision, as part of the Inditex Group, is to create a sustainable fashion industry by promoting responsible consumption and production, respecting the environment and people, and contributing to the communities in which it operates.
The company aims to offer the latest fashion trends to its customers at accessible prices while continuously innovating and improving its operations and processes.
Growth by numbers (Inditex)

How ZARA Revolutionized the Fashion Industry with Lean Practices
Updated: August 27, 2023 by Lori Kinney

ZARA changes its clothing designs every two weeks on average, offering upwards of 11,000 distinct garments every year. In comparison, competitors change their designs every three or four months and product 3-4,000 distinct pieces.
This is fast fashion: the business model of replicating high-fashion, luxury-brand pieces quickly and cheaply, making them available to customers while the trend and demand are at their highest. With nearly 3,000 stores in 96 counties, and an estimated net-worth around $20 billion, ZARA has merged fast and traditional fashion into a popular market space it also dominates.
Problems in the fashion industry: speed, price, and predictability
Amancio Ortega was born in Leon, Spain in 1936 to a railroad worker father and a mother who worked as a maid. Eight years later, on the northwest coast of Spain four hours away, Rosalia Mera was born in La Coruna.
Both would find themselves working in the clothing industry at early ages – Ortega first as an assistant to a shirt-maker, than a tailor himself, then a clothing store manager; and Mera worked as a seamstress from age 11 to help her family with money – and 1966 would find them married to each other, at 30 and 22 years of age, respectively.
In 1975, they founded ZARA together, opening their first location that same year in A Coruña, Spain. Ortega – an unknown with little retail experience – named it Zorba after his favorite film, Zorba The Greek. A neighborhood bar had already beat him to that name, so Ortega and Mera changed the name to ZARA.
His experience prior to ZARA allowed him to recognize inefficiencies in the fashion industry’s business model at the time. For example:
The process of moving a garment from designer to factory to store was long and slow. The costs associated with that process – including expensive advertising campaigns – were ever-increasing; only the rich could afford to buy “high fashion” or enjoy trends.
There needed to be more ability to control the supply chain, and more flexibility within the supply chain.
Ortega recognized there was an untapped market, and he wanted ZARA to tap into it.
They decided to try JIT, Kanban, Kaizen, and more
Ortega knew from his previous jobs that the fashion industry as a whole operated by a less-than-ideal business model. He wanted the Zara experience to be different.
He wanted to be fast, affordable, and innovative, and do it all efficiently. He wanted to invest more of his budget into higher pay for local work forces. And ultimately, he wanted to provide a carefully engineered, predictable, and repeatable fully customer-centric experience.
These are the practices and philosophies that ZARA started building on all those years ago, and that drives their success still today.
1. Just-in-time production
Just-in-time (JIT) production is a Lean business model where only what is needed – and only at the time it is needed, and in the amount it is needed – is produced. Used correctly, it results in the elimination of waste and inconsistencies from the production process. With productivity improved as a result, ZARA stores can maintain a very low inventory of merchandise while continuously updating collections with the newest trends.
Stores place orders twice weekly – this is what drives factory scheduling. Because order cycles are focused on short runs, forecasting becomes very accurate for ZARA, creating a competitive edge in an industry where bi-weekly or monthly orders are the norm (and forecasts therefore less accurate). Because they do not need to place big bets on yearly fashion trends, ZARA can make many smaller bets on short term trends that are easier to predict.
ZARA’s short production runs also mean any given design is limited, which encourages customers to buy quickly while inventory is available. As a consequence, stores have little excess inventory and can avoid having to do big markdowns on their items. New items are designed and sent out to the stores in four to six weeks, whereas existing items are modified in only two weeks.
Agile businesses count on and are therefore prepared to adapt to changes or disruptions in their manufacturing processes. Because fast fashion by it’s very nature is about change, learning to be agile and highly responsive has taken ZARA to the next level.
3. Kanban Pull Systems
Push and pull systems are the two methods most commonly used when business are looking to organize their inventory and regulate their manufacturing practices. Push systems are designed to push inventory out to the customer, and pull systems exist to respond to customer demand.
ZARA uses a pull system, They only fill inventory when a customer places an order, replacing exactly what was ordered and how many. Nothing more, nothing less.
Kaizen, loosely translated, means good change; or, in other words, continuous improvement. ZARA uses Kaizen as a tool to meet or exceed every aspect of their customers’ expectations , down to the last detail.
They are constantly obtaining, analyzing, and responding to customer feedback.Their entire adapted process of doing so is automated by a cutting edge IT infrastructure, for the utmost in efficiency.
5. One-piece Flow
One-piece flow is the opposite of mass production. Instead of large quantities of something being produced, small quantities are produced to match the pace of customer demand. This method reduces and removes all types of waste from the process and allows ZARA to be much more agile.
By implementing these five core tenets of Lean business practices, ZARA perfected their best practices and found their best, most efficient way to achieve their business goals.
ZARA’s 4 Best Lean Business Practices
1. don’t be afraid to change procurement methods..
ZARA’s supply chain approach is unique partly because their procurement teams do not work on the number of finished clothes but rather the number of raw materials used in manufacturing those clothes.
ZARA buys extensive quantities of fabric, but does not commit to a particular color or pattern until customer feedback is analyzed and trending patterns are identified. A piece of clothing that doesn’t meet expectations cannot be resold, but fabric can be re-used. This is both budget- and environment-friendly.
2. Build close supplier relationships.
This means “close” as-in geography, and “close” as-in collaboratively. Relationships with suppliers that are located close to their factories mean ZARA can order on an everyday-need basis. This is unparalleled supply chain control and flexibility These relationships are the key to the successful execution of the entire business model, so it is imperative that they are built on mutual senses of trust and deep collaboration.
3. Obtain and listen to customer feedback.
All day, everyday, ZARA stores are gathering customer feedback. Customer purchases, returns, and item reviews are all entered into a database accessed by ZARA’s design teams, who use the information to determine how designs are performing. Decisions as to discontinuations or alterations are made. The information is also used to update future designs accordingly.
This level of customer data analysis is fully automated and customized to ZARA’s specific goals; the system is the heart of their cutting edge IT infrastructure. Listening to customer feedback is a pillar of ZARA’s business framework that has cut the time they deliver new styles to market from six months to two weeks. It’s how they remain quick and agile when responding to the changing market.
4. Do your manufacturing in-house, and do it locally.
The heart of ZARA and its famous supply chain is a massive distribution center called “The Cube.” ZARA’s factories are connected to The Cube via a network of underground tunnels home to a high-speed monorail system that transports cut fabric (bulk quantities of which that can be delivered directly and quickly to the distribution center) to these factories for dyeing and assembly. The entire process is automated.
This level of control, when managed correctly, means production rates can be quickly increased or decreased, resulting in less inventory in the supply chain (and less need to finance that inventory with working capital). This also means that ZARA does about 50% of their manufacturing in advance versus the 80-90% done by competitors. Interestingly, ZARA tries to keep about 85% of its plants idle in order to optimize the response time to demand changes around the world.
ZARA: Leaner, Better, Faster, Stronger
ZARA was fortunate to come to life at the time it did, after Ortega had already learned some valuable lessons about what was and was not working in the fashion industry. There was a golden opportunity for someone to do what no one else was doing, and be the best at it. While there are examples all throughout business of companies successfully implementing Lean Six Sigma and Lean business practices, outside of the car industry, no company provides a better example of how to properly execute a Lean business model than ZARA.
About the Author
Lori Kinney
Brought to you by:

By: David J. Arnold
Fashion retailer ZARA has achieved spectacular growth via a distinctive design-on-demand operating model. This case describes this model and outlines a number of challenges facing the company, with a…
- Length: 26 page(s)
- Publication Date: Mar 11, 2003
- Discipline: Marketing
- Product #: 503050-PDF-ENG
What's included:
- Teaching Note
- Educator Copy
$4.95 per student
degree granting course
$8.95 per student
non-degree granting course
Get access to this material, plus much more with a free Educator Account:
- Access to world-famous HBS cases
- Up to 60% off materials for your students
- Resources for teaching online
- Tips and reviews from other Educators
Already registered? Sign in
- Student Registration
- Non-Academic Registration
- Included Materials
Fashion retailer ZARA has achieved spectacular growth via a distinctive design-on-demand operating model. This case describes this model and outlines a number of challenges facing the company, with a particular emphasis on its international expansion. Includes color exhibits.
This case is available in only hard copy format (HBP does not have digital distribution rights to the content). As a result, a digital Educator Copy of the case is not available through this web site.
Learning Objectives
To understand the key elements of a distinctive retail model and to examine the challenges facing retailers as they internationalize.
Mar 11, 2003
Discipline:
Geographies:
Industries:
Apparel industry, Retail trade
Harvard Business School
503050-PDF-ENG
We use cookies to understand how you use our site and to improve your experience, including personalizing content. Learn More . By continuing to use our site, you accept our use of cookies and revised Privacy Policy .
- Harvard Business School →
- Faculty & Research →
- January 2020 (Revised October 2021)
- HBS Case Collection
Zara: An Integrated Store and Online Model (A)
- Format: Print
- | Language: English
- | Pages: 32
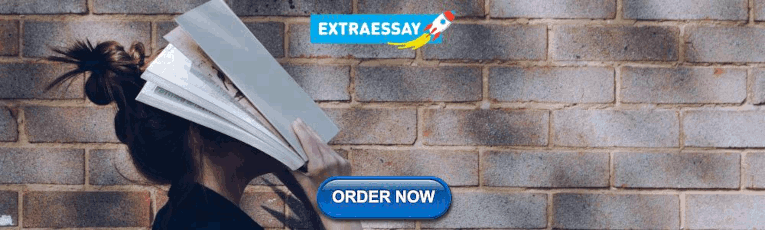
About The Author
Antonio Moreno
Related work.
- January 2020
- Faculty Research
Zara: An Integrated Store and Online Model (B)
- May 2021 (Revised October 2021)
Zara: An Integrated Store and Online Model (A) and (B)
- Zara: An Integrated Store and Online Model (B) By: Antonio Moreno
- Zara: An Integrated Store and Online Model (A) and (B) By: Antonio Moreno and Anibha Singh
- Zara: An Integrated Store and Online Model (A) By: Antonio Moreno

Zara Case Study: How Zara Lead The Fast Fashion Market?
Supti Nandi
Updated on: March 5, 2024
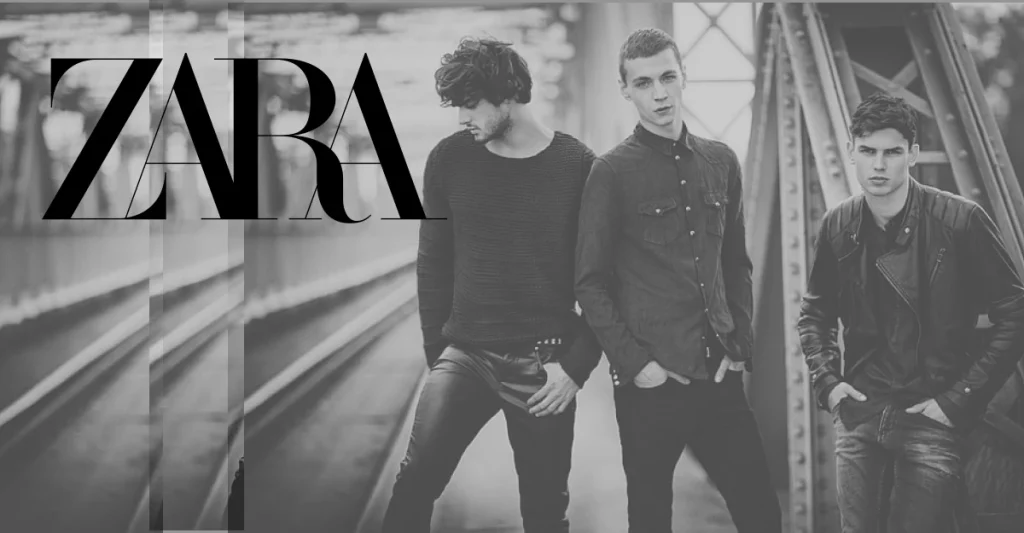
You asked, and we listened! Get ready to dive into the fascinating world of Zara with our highly requested Zara Case Study.
Recently, Zara has been trending in Instagram reels and YouTube shorts for its funky model poses. You must have seen it too! Have you wondered what made this Spanish brand so famous?
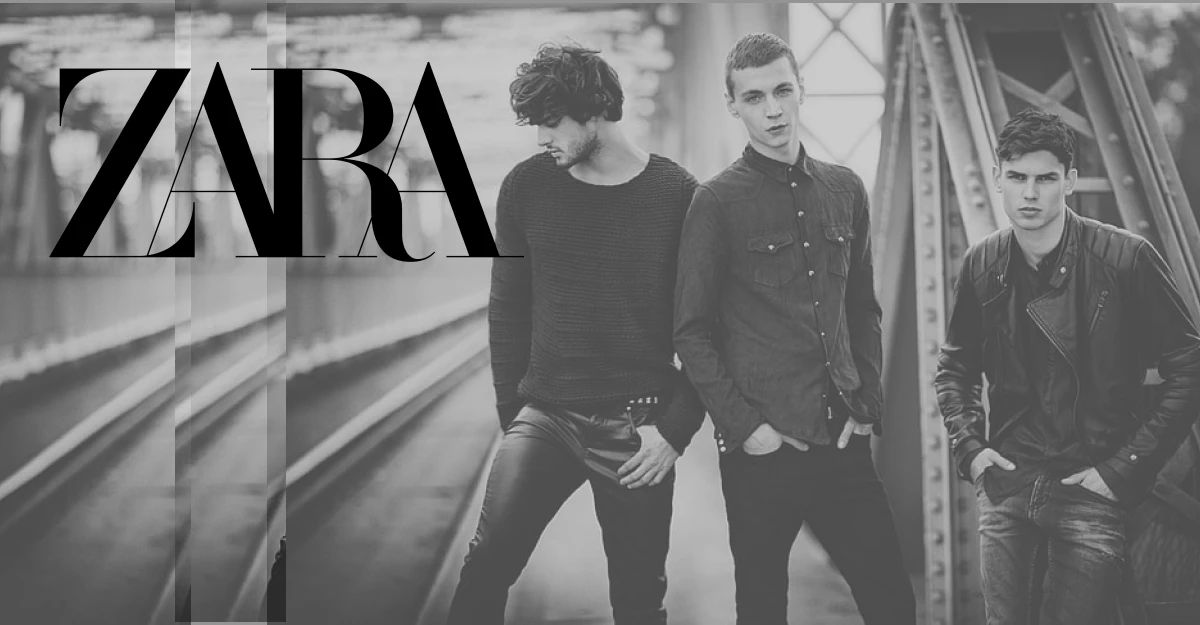
You may say that Zara works on the concept of fast fashion, which makes it win in the competitive market.
Well, that’s true but it is not the only reason. Let’s uncover the secrets behind Zara’s success through the Zara Case Study.
Let’s begin!
(A) Zara: A Brief Overview
Zara, a notable name in the fashion industry, is a Spanish retailer known for its distinctive approach to clothing and accessories. Operating on a fast fashion model, Zara excels in swiftly adapting to evolving fashion trends, setting it apart in the market. With a vertically integrated process, the brand manages everything from design to production in-house, allowing for efficient and responsive operations.
You’ll find Zara stores globally, each offering a diverse range of trendy and affordable clothing for men, women, and children. The brand’s commitment to delivering fashion-forward pieces at accessible prices caters to a broad audience, reflecting its significance in the industry.
Do you know what is fast fashion?
Fast fashion is a business model characterized by quickly producing affordable, trendy clothing items to meet rapidly changing consumer demands.
Zara works in the same way. We will look into its details in the upcoming section. Before that, let’s delve into the profile of Zara-
What makes Zara stand out is its ability to balance responsiveness in manufacturing, a well-structured supply chain, and a keen understanding of consumer preferences. This combination has established Zara as a trendsetting and influential player in the fashion landscape. Its adaptability and dedication to making fashion trends accessible have solidified Zara’s place as a recognizable and influential name in the fashion industry.
(B) Zara Case Study: History & Evolution
Zara’s journey began with a dress-making factory called Inditex, established by Ortega in 1963. Over the years, Zara expanded its presence from Spain to Portugal and eventually to other European countries, the United States, and France.
Today, Zara boasts nearly 6,500 stores across 88 countries worldwide.
Let’s dive into the history of Zara in detail-
Zara is the flagship brand of the Inditex group, which is one of the world’s largest fashion retail conglomerates.
The head office of Zara is located in Arteixo, in the province of A Coruña, Galicia, Spain. Inditex also owns other popular brands like Massimo Dutti, Pull&Bear, Bershka, and Stradivarius.
(C) Brand Philosophy of Zara
Do you know why Zara stands out among its competitors? Due to its brand philosophy! Sara’s success hinges on several key principles-
Zara’s strategy is strikingly different from traditional fashion retailers. Reason? Fast fashion concept and in-house production of clothes! Go through the next section for detailed information.
(D) Zara Business Model: Effective Working Strategies
In this section, we will dive into the business model of Zara to determine its working strategies that played a huge role in its success-
Let’s dive into the details-
(D.1) Fast Fashion Model
Zara is known for its “ Fast Fashion ” approach. It releases new collections frequently, sometimes launching over 22 new product lines per year. This agility allows Zara to respond swiftly to changing trends and customer preferences.
- Rapid Trend Replication: Harnessing cutting-edge information technology, Zara excels at swiftly replicating prevailing fashion trends. This enables the brand to stay ahead of the curve, delivering the latest styles to customers promptly.
- Group Design Approach: Departing from the conventional individual designer model, Zara adopts a collaborative approach. Teams of designers work in synergy, fostering enhanced creativity and efficiency in product development. This collective effort ensures a diverse range of products aligned with dynamic market demands.
- Cost-Effective Materials: Zara strategically utilizes affordable materials without compromising on quality. This approach allows the brand to maintain competitive pricing while delivering products that meet or exceed industry standards. The focus on cost-effective yet quality materials contributes to Zara’s accessibility and broad customer appeal.
- Competitive Pricing: Zara optimizes its production costs by outsourcing to countries with cost-effective labor. This global approach not only supports competitive pricing but also facilitates the brand’s ability to swiftly adapt to market demands. The combination of efficient production and competitive pricing reinforces Zara’s position as a leader in the fast fashion landscape.
(D.2) Product Range
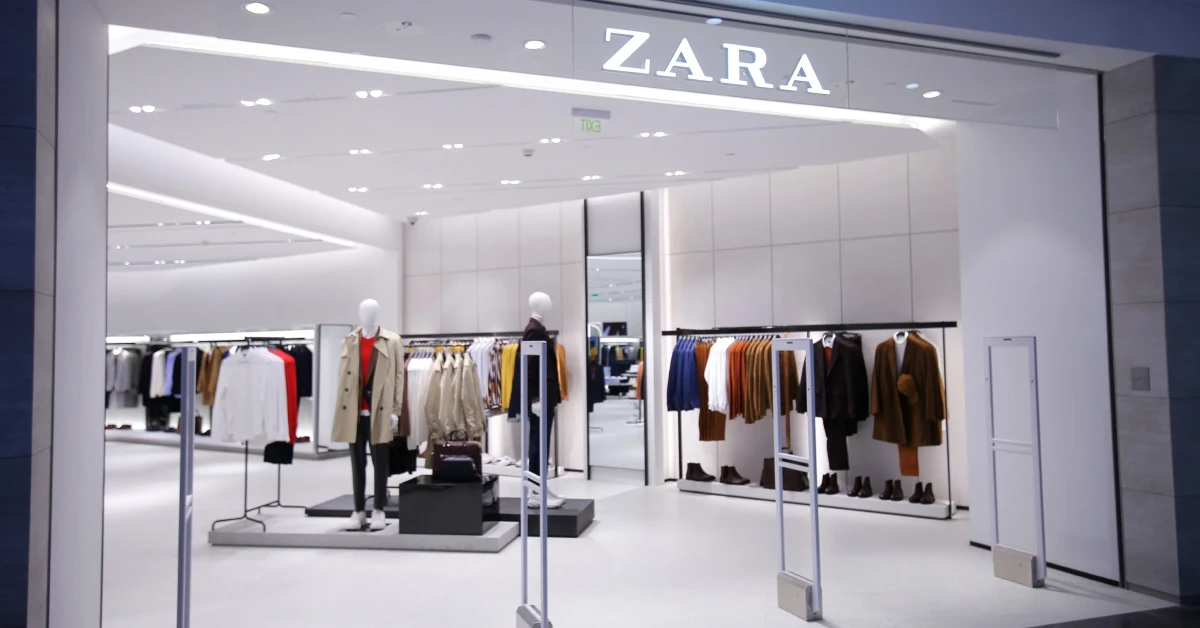
Let’s briefly look at its product range too-
- Clothing: From chic dresses and tailored suits to casual wear and activewear.
- Accessories: Including bags, shoes, belts, and jewelry.
- Beauty Products: Fragrances and cosmetics.
- Perfumes: Zara has its line of fragrances.
(D.3) Vertical Integration: In-House Operations & Logistics
Zara’s way of doing business centers on something called vertical integration. Here is how it works-
- Design: Zara takes charge of creating its designs, meaning it controls how its clothes look and stay on-trend. This ensures that what you find in Zara stores reflects the latest fashion trends.
- Manufacturing: Zara doesn’t just design; it also makes its clothes in-house. This is a big deal because it lets Zara make changes to its products fast. If there’s a new trend or customer feedback, Zara can respond quickly, which is pretty cool.
- Shipping and Distribution: Zara doesn’t stop at making the clothes; it handles everything from getting them to the store to making sure they’re sent to the right places. This full control of the supply chain ensures that the clothes you see in Zara are not only stylish but also reach the stores efficiently.
In short, the fast fashion concept, vertical integration, and supply chain efficiency helped Zara to achieve impressive milestones.
(E) Revenue Model of Zara: How does Zara make money?
Do you know Zara earned Rs.2,562.50 crore in India? That’s not all. It earned over 23 billion euros from its stores worldwide.
That’s quite amazing! Isn’t it?
But how does Zara earn such a whopping amount of money? Due to its impressive revenue model.
Let’s go through them one by one-
Let’s briefly dive into Zara’s finances for the years 2022 & 2021-
That’s how Zara is going through its purple patch in terms of revenues!
(F) Zara Marketing Strategies
Zara, the renowned Spanish fashion retailer, has crafted a distinctive marketing strategy that contributes to its global success. In this section, we will delve into the key elements of Zara’s marketing approach-
(F.1) Fast Fashion Strategy
The fast fashion model functions as a highly effective marketing strategy for Zara in several ways. First and foremost, the rapid turnover of collections, with over twenty product lines per year, creates a sense of urgency and novelty for customers. This continual introduction of fresh styles not only keeps Zara top-of-mind but also fosters a dynamic shopping experience, encouraging frequent visits to discover the latest trends.
Moreover, the quick response to changing trends and customer preferences positions Zara as a trendsetter, appealing to fashion-conscious consumers. The ability to swiftly translate runway trends into accessible and affordable pieces reinforces Zara’s image as a go-to destination for staying in vogue.
Additionally, the limited production batches contribute to an atmosphere of exclusivity, prompting customers to make timely purchases to secure unique and in-demand items. This scarcity-driven approach enhances the perceived value of Zara’s offerings.
In essence, the fast fashion model serves as a powerful marketing tool for Zara by creating a sense of immediacy, exclusivity, and trend relevance, fostering customer loyalty and consistently attracting a diverse audience seeking the latest in fashion.
(F.2) In-Store Experience
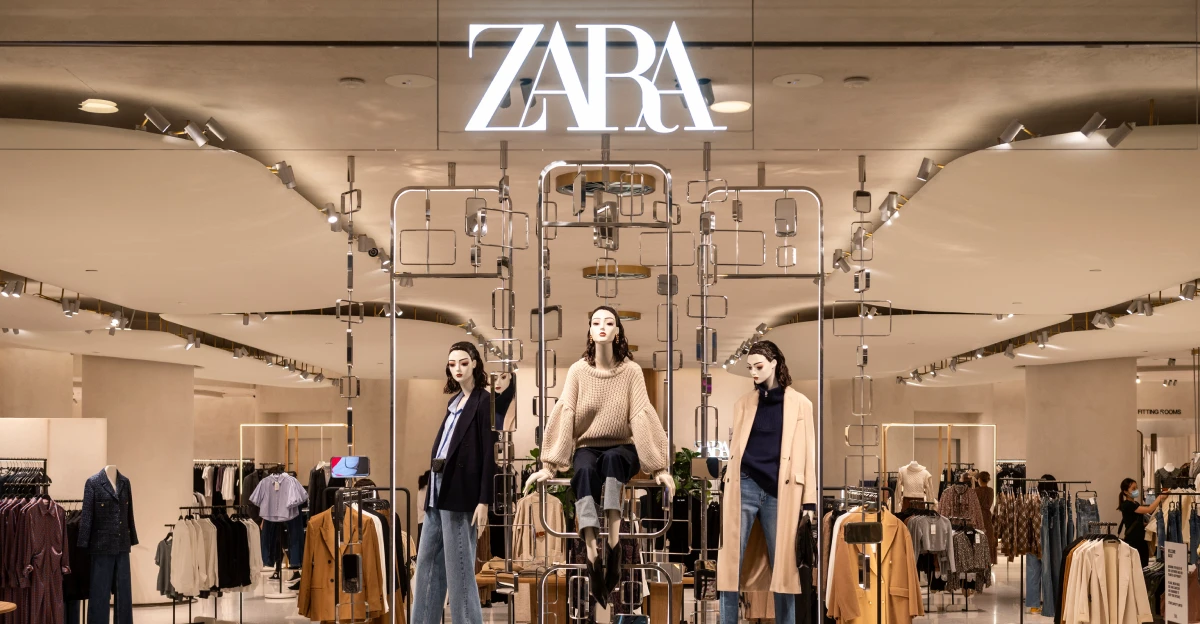
Zara places a strong emphasis on crafting an exceptional in-store experience, carefully curating showrooms to exude an atmosphere that is both exclusive and professional. The meticulous design choices contribute to an ambiance that goes beyond a mere shopping space, creating an environment where customers feel engaged and inspired.
The meticulous attention to detail is aimed at ensuring that every aspect of the in-store setting is carefully considered, from layout to lighting.
This focus on the in-store ambiance goes beyond aesthetics—it becomes a vital part of Zara’s marketing strategy. The thoughtfully designed physical stores act as powerful marketing tools in themselves, drawing in customers by providing a memorable and immersive shopping environment.
By enticing shoppers to explore the latest trends in this carefully curated setting, Zara not only enhances the overall customer experience but also reinforces its brand image as a trendsetting and sophisticated fashion destination!
(F.3) Affordability & Differentiation
Zara strategically positions itself by prioritizing affordable pricing while maintaining a commitment to quality. This dual emphasis allows the brand to resonate with a wide range of customers. By providing stylish clothing at reasonable prices, Zara ensures accessibility, making fashion-forward designs attainable for a diverse audience.
The effectiveness of this marketing strategy lies in Zara’s ability to differentiate itself in the market. The brand stands out not only for its trendsetting designs but also for its adept balance of fashion-forward aesthetics and accessible costs.
This unique blend positions Zara as a go-to destination for those seeking both style and value, enhancing the brand’s appeal and solidifying its market presence. The affordability and differentiation strategy contribute to Zara’s ability to capture a broad customer base and maintain its status as a leading player in the competitive fashion landscape.
(F.4) Word of Mouth and Limited Advertising
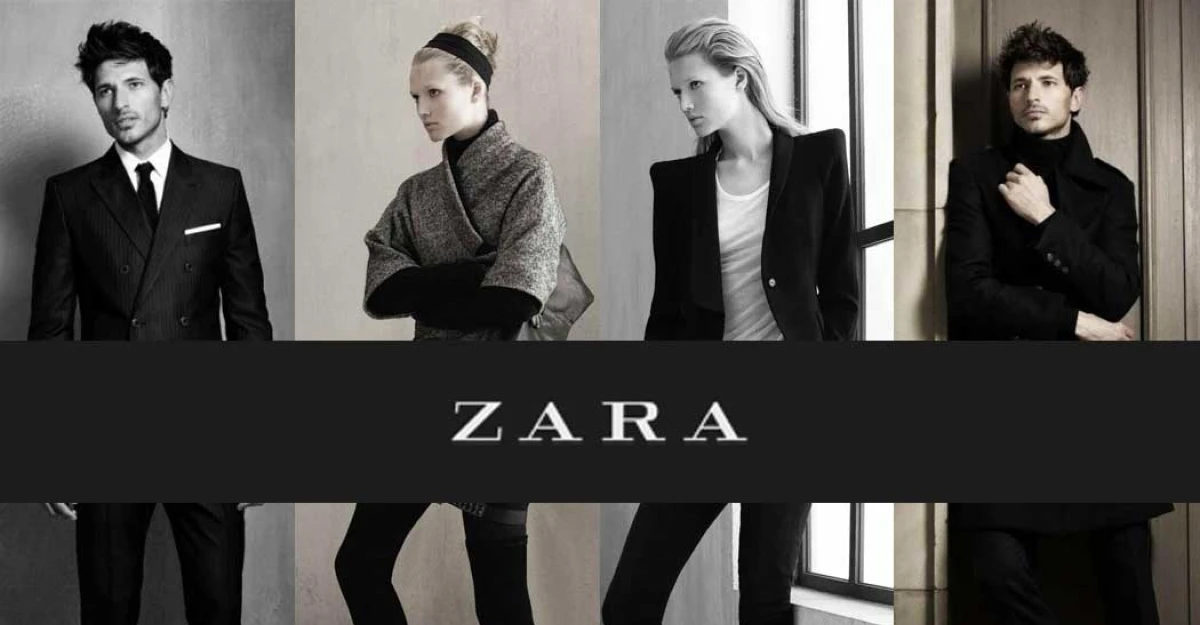
Zara strategically leverages the power of word of mouth and customer recommendations as primary drivers of its marketing efforts. In a departure from traditional advertising-heavy approaches, Zara relies on the subtlety of customer satisfaction and positive experiences to promote its brand.
This unique strategy involves cultivating a strong and positive buzz around Zara’s collections, encouraging customers to share their experiences and recommendations. The reliance on word of mouth creates an authentic and organic promotion of the brand, fostering a sense of trust and credibility among potential customers.
The limited advertising approach doesn’t diminish Zara’s impact; rather, it aligns with the brand’s commitment to providing an outstanding in-store experience and quality products. The positive buzz generated by satisfied customers becomes a powerful force, driving foot traffic to Zara’s stores and contributing to the brand’s sustained success in the competitive fashion market.
(F.5) Social Media Marketing
Zara actively embraces social media platforms as a crucial component of its marketing strategy. The brand leverages platforms like Instagram, Facebook, and Twitter to engage directly with its audience, creating a dynamic online presence.
The strategy involves regular updates across these platforms, keeping followers informed about the latest arrivals, ongoing trends, and behind-the-scenes glimpses into Zara’s fashion world. By maintaining an active and visually appealing presence, Zara not only stays connected with its audience but also cultivates a sense of anticipation and excitement around its offerings.
In addition to direct engagement, Zara strategically collaborates with influencers. These collaborations amplify Zara’s reach, tapping into the influencers’ follower base and creating a ripple effect of brand awareness.
Through this multi-faceted approach, Zara effectively utilizes social media not just as a promotional tool but as a means to foster a dynamic and interactive relationship with its audience, contributing to the brand’s overall success in the digital landscape.
(F.6) Personalization & Community Engagement
Zara adopts a customer-centric strategy by customizing its offerings to cater to local tastes and preferences. This personalization ensures that Zara’s collections resonate with diverse communities, creating a more inclusive and relatable shopping experience.
Community engagement takes center stage in Zara’s approach. Events like fashion shows or store openings play a pivotal role in fostering a sense of belonging among customers. By actively involving the community in these events, Zara goes beyond being a retailer and becomes an integral part of the local fabric.
Crucially, Zara prioritizes customer feedback. Actively listening to what customers have to say, the brand adapts and evolves its offerings based on this valuable input. This responsiveness not only enhances the overall customer experience but also reinforces a sense of collaboration between Zara and its community.
In essence, Zara’s commitment to personalization and community engagement contributes to a brand image rooted in customer satisfaction and a genuine connection with the diverse communities it serves.
(G) Sustainability Efforts: Crucial Part of Zara Case Study
Do you know what Zara is famous for apart from fashion? Its sustainability efforts to preserve mother nature! Let’s look at the sustainability efforts of Zara-
Thus, Zara is increasingly conscious of sustainability. The brand aims to reduce its environmental impact by using eco-friendly materials and promoting recycling. Such initiatives resonate with socially aware consumers.
(H) Challenges Faced by Zara
The journey of Zara was not free of challenges. Let’s look at some of the major challenges of Zara-
Zara brilliantly addressed those challenges to produce effective results that ultimately helped them grow their business.
(I) Summing Up: Zara Case Study
Zara’s remarkable success in leading the fashion market can be attributed to its unique blend of rapid fashion cycles, vertical integration, and a customer-centric approach. By staying ahead of trends with its fast fashion model, ensuring control over the entire production process, and tailoring offerings to local tastes, Zara captures a diverse and loyal customer base.
The brand’s commitment to affordability, engaging in-store experiences, and strategic use of social media further solidify its market leadership. Zara’s story showcases the power of adaptability, responsiveness, and a strong connection with customers in navigating the dynamic landscape of the fashion industry!
Related Posts:

Contact Info: Axponent Media Pvt Ltd, 706-707 , 7th Floor Tower A , Iris Tech Park, Sector 48, Sohna Road, Gurugram, India, Pin - 122018
© The Business Rule 2024
- Study Guides
- Homework Questions
MKTG Zara delivers fast fashion
MBA Knowledge Base
Business • Management • Technology
Home » Management Case Studies » Case Study: Zara’s Entry into Indian Retail Fashion Market
Case Study: Zara’s Entry into Indian Retail Fashion Market
Zara is an extremely renowned brand, known for its latest designs and is among the top 100 best global brands in 2010 .It uses the unusual strategy of zero advertising and instead invests the revenue in opening new stores across the world. Zara is popular amongst old and young generations too because it is affordable fashion. It is crystal clear that Zara is successfully living upto the standard of its two winning retail trends firstly, it is fashionable and secondly it is low in price thus resulting in a very effective mixture out of it.

The first store of Zara was opened in a central street in Spain in 1977 by Amancio Ortega who also owns, other brands such as Massimo Dutti, Pull and Bear and many others. Spain is the headquarter of Zara. Zara have opened 95 stores around the world in quarter 1 of year 2009 alone, bringing the total to 4359 stores in 73 countries worldwide.
The Louis Vuitton fashion director Daniel Piette also described Zara as “possibly the most innovative and devastating retailer in the world.” They control most of the steps in the supply chain and also it designs, produces and supplies itself.
Taking into consideration the amount of competition and the need for sustainability in the human race, running a business or a brand is not an easy task. With existing big brands and busy markets around the world, it takes more than what is required to make a name for oneself and to succeed in it. Proper management and marketing strategies are required along with the detailed knowledge of the economy and the earning and spending of the locality or the country’s GDP (Gross Domestic Product) which measures the country’s economy and their ability to spend and grow should be known before taking a leap and spreading the arms around the world. This essay discusses about which mode of entry strategy Zara adapted to entered into the Indian market and whether the strategy proved to be beneficial for the company and the benefits/disadvantage sit is going tackling and lastly it also analyses in which country it is doing better and why.
Zara adopts a ‘Fast Fashion’ supply chain model. The latest fashions are supplied from design to delivery in just 2 weeks, compared to the 6 month industry average. They operate a vertical supply chain, so they themselves undertake everything from design, manufacture, sourcing and distribution. This allows them total control over the business, and leaves them less vulnerable to accusations of unethical practices such as sweatshop labor.
Entry strategy of Zara in India
While Zara owns a majority of its stores in Spain, the international expansion has adopted three different entry modes: Own subsidiaries, Joint ventures and Franchising.
According to the Indian policy on foreign direct investment (FDI) , Zara teamed up with the Tata Group, India, to form a joint enterprise in February 2009. Inditex has a share of fifty one percent of this collaboration while Tata’s subsidiary Trent Limited holds forty nine percent. Owing to several issues the Corporation undergoes, their extension of the store will stay slow, with just one additional store open Zara is the following Spanish Retailer to come into India, after Mango, even though Mango adopted the contract route to enter into the Indian market.
Jesus Echevarria Hernandez, Chief Communication Officer at Inditex Group. Says that “The entry in the Indian market has a significant strategic importance for Inditex. India is one of the top priorities in the Asia region when our retail offering has been very well received,” .
To enter the market in India, Inditex (the company behind Zara) used the strategy of pursuing a joint venture with Trent Limited, a Tata Group company, a highly recognized clothing line distributor. Zara took up joint ventures as its mode of entry in India because this is a co-operative strategy in which the manufacturing facilities and know-how of the local company are combined with the expertise of the foreign firm in the market, especially in large, competitive markets where it is difficult to acquire property to set up retail outlets or where there are other kinds of obstacles that require co-operation with a local company to which Zara regards its stores as one of the related elements in its business sculpt. The shop is regarded as the boundary among the buyer and the motor of the whole business – mode design, development, logistics and finally retail.
The main concerns that Zara had wile entering into the Indian market were Demography and cultural concerns. Speaking of demography India has a population of about 1.2 billion people and the target market would be no doubt wide than what is expected. As the income become larger in India, there will be more demand in the quality and fashionable clothing. Cultural Concerns: it is the major concern that has to be given tremendous attention when entering into a foreign market. It must accept the perspectives and beliefs of the role of culture in influence and as in India social security is given special attention.
In order to effectively achieve their goals, Zara pursued a strategy of selling a variety of its local clothing lines and international clothing lines, but maintaining Zara as the primary brand in India. Zara also targeted the larger positions including either the first or second positions in the Indian market of clothing lines. Any of these positions would be sufficient enough for Zara to create an outstanding level with regards to manufacturing, marketing and distribution. These positions can set up a stage from which Zara can sell their clothing lines and other special fashion products .
To promote the organization and its clothing lines, Zara utilized video advertisements, print ads and the idea of e-marketing which fulfilled the varying needs of consumers from India and beyond; particularly those priority Indian markets or the consumers in the urban India areas. For this promotion campaign, the perfect information that Zara Company utilizes is “Providing quality and fashionable clothing lines that fulfills your needs. Zara has been able to set up its reputation as one of Spain’s primary clothing line companies for several years now. It is able to rise up to the challenges in most of its markets directly . This is made possible through the efficient promotional and positional strategies established in order to maintain not only large profits, but also on establishing the foundations of Zara’s clothes and fashion trends. The promotional strategies of Zara in India are easily implemented by the local employees themselves which enables the organization to vastly improve without the burden of implementing costly technologies. These initiatives can also lead in improved financial profit for the organization and will enable the foundation of networks for Zara clothing lines in India.
Target Market
Zara has maintained a reputation for targeting the teenagers, those in their twenties and even the individuals considered young at heart. This is a customer sector that other clothing companies have previously ignored in place of the adult consumers. Zara Company also has the unique strategy of portraying the generations in their campaigns. These campaigns in India will tell that Zara Company is not a mere simple clothing line for the next generation; its users are also a generation ahead of their competitors. Zara Company can establish an image for itself in India as the clothing line for the present generation. It has discovered that the purchasing power of the youth and the marketing power of celebrities were similar. They have garnered significant profit gains out of this strategy, and there is no reason why this won’t also work in India.
Nevertheless Zara undergoes quite a few hurdles like the existing rules on FDI in India require that foreign single-brand suppliers are obliged to surpass a 49% stake to a resident associate. This includes the vendor to share its organizations information and data it would usually not reveal. Moreover, franchising stores means that the merchant loses certain jurisdiction over how these are operated, which numerous businesses worry that it might harm their brand name. As a result, single-brand retailers are regularly cautious of entering the Indian market. For a apparel seller akin to Zara, further considerations contain the relative need of seasonal modification and the separate, consolidated manner of dress amongst Indian females that differs significantly to Zara’s offered ranges.
Related Posts:
- Case Study: MNC Fast Food Chains Go ”Local”
- Zara's Lean Operation: Source of Competitive Advantage
- Case Study of GUCCI: Transformation of Luxury Branding
- Case Study: Inventory Management Practices at Walmart
- Case Study of Zara: Sustainability in Fast Fashion Industry
- Case Study: Tesco's US Grocery Market Entry
- Case Study: How Netflix Took Down Blockbuster
- Case Study of Zara: Use of Technology to Improve Operational Responsiveness
- Case Study: Wal-Marts Competitive Advantage
- Case Study: Zara's Supply Chain Success Story
Leave a Reply Cancel reply
Your email address will not be published. Required fields are marked *
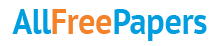
- Browse Papers
Zara Apparel Manufacturing and Retail - Case Study
Autor: asmaliyana23 • March 14, 2016 • Case Study • 1,139 Words (5 Pages) • 6,614 Views
ZARA: Apparel Manufacturing and Retail
Zara is a chain of fashion stores owned by Inditex, Spain’s largest apparel manufacturer and retailer. Zara has grown rapidly with a strategy to be highly responsive to changing trends with affordable prices. While the design-to-sales cycle times in the apparel industry normally averaged more than six months, Zara has managed to achieve the cycle times of only four to six weeks, which allows Zara to introduce new designs every week and to change 75 percent of its merchandise display every three to four weeks.
Zara manufactures its apparel using a combination of flexible and quick sources in Europe (mostly Portugal and Spain) and low-cost sources in Asia. About 40 percent of the manufacturing capacity is owned by Inditex, with the rest outsourced.
In 2012, Inditex distributed to stores all over the world from eight distribution centers (DC) located in Spain. The group claimed an average delivery of 24 to 36 hours for European stores and up to a maximum of 48 hours for stores in America or Asia from the time the order was received in the DC to the time it was delivered to the stores, while shipments from the DCs to stores were made several times a week. This allowed store inventory to closely match customer demand.
Question 1: What advantage does Zara gain against the competition by having a very responsive supply chain?
Zara has gained advantages over its competitors by responding quickly and on time towards the fast-moving trends in the market through their responsive supply chain. It also allows Zara to match customers’ demand for fickle trends more accurately. Zara practices the strategy of limiting the design-to-sales cycle times within four to six weeks, which enables it to introduce new designs every week. Thus, the apparels in its stores are always fresh and from the latest collection, which will satisfy the customers’ preferences and demand. This in return means that Zara can sell its products at full prices and thus increase their sales and profit margins. It will also increase customer loyalty to the brand as Zara builds a reputation for being up-to-date on trends which increases demand in its products. Zara also uses the strategy of making in-house production after the start of the sales season. This responsiveness, together with the postponement of decision until the trend is known, allows Zara to reduce inventory cost and forecast error.
Question 2: Why has Inditex chosen to have both in-house manufacturing and outsourced manufacturing? Why has Inditex maintained manufacturing capacity in Europe even though manufacturing in Asia is much cheaper?
In the case study, it is mentioned that about 40 percent of the manufacturing capacity is owned by Inditex, with the rest outsourced. While Zara manufactures its apparel using a combination of flexible and quick sources in Europe (mostly Portugal and Spain) and low-cost sources in Asia. In-house manufacturing is used as it provides flexible and quick sources for Zara, which will help Zara to maintain its practice of design-to-sales cycle times of four to six weeks. The in-house manufacturing is important for production after the sales season has started as a way for Zara to quickly respond to the latest trends and demand. It can also serve as the head manufacturer that deals with returned or incomplete products made by the outsourced manufacturers and turn them into complete finished goods to be distributed in the market.
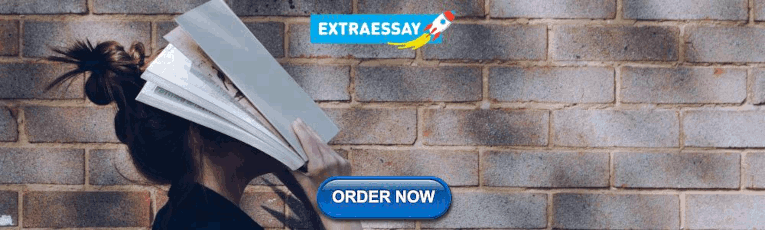
IMAGES
COMMENTS
Zara: Apparel Manufacturing and retail. This study source was downloaded by 100000756627845 from CourseHero on 03-18-2022 22:45:58 GMT -05: ZARA: Apparel Manufacturing and Retail. Zara is a chain of fashion stores owned by Inditex, Spain's largest apparel manufacturer and retailer. Zara has grown rapidly with a strategy to be highly ...
The Far East, which was viewed as a low-cost manufacturing source for Zara, also became a consumer of its Fast-Fashion so much so that China had the largest number of Zara stores in the world by 2016.
A case study of Zara's business operations, including location strategy, advertisement strategy, and supply chain logistics. ... supply chain management. But again, Inditex does more than one thing differently that enables it to stand out in the retail clothing industry. In this paper, we analyze the operations vital to Inditex's success ...
Manufacturing In-House. One pillar of Zara's supply chain strategy that keeps things moving quickly is investing in in-house production processes. These can allow for greater flexibility and better oversight, reducing the risk of errors, delays, and inefficiencies. To achieve this, Zara does much of its production in-house.
Zara is a privately held multinational clothing retail chain with a focus on fast fashion. It was founded by Amancio Ortega in 1975 and it's the largest company of the Inditex group. Amancio Ortega was Inditex's Chairman until 2011 and Zara's CEO until 2005. The current CEO of Zara is Óscar García Maceiras and Marta Ortega Pérez ...
ZARA's 4 Best Lean Business Practices. 1. Don't be afraid to change procurement methods. ZARA's supply chain approach is unique partly because their procurement teams do not work on the number of finished clothes but rather the number of raw materials used in manufacturing those clothes.
Fashion retailer ZARA has achieved spectacular growth via a distinctive design-on-demand operating model. This case describes this model and outlines a number of challenges facing the company, with a particular emphasis on its international expansion. ... Apparel industry, Retail trade. Source: Harvard Business School. Product #: 503050-PDF-ENG ...
specialty apparel chain, Zara, as an example of excellence in supply chain practices. This research on the European apparel industry emphasizes the economic and supply chain aspects of Zara's operation. The case study analyses the strategic, operational and supply chain processes that have contributed to the success of Zara's retail ...
In 2010, amidst the growth of ecommerce and the emergence of new, purely online, fashion players, Zara launched its first online store, Zara.com. Since then, Zara's online business had grown at a fast pace. By 2018, 12% of Inditex Group's total sales came from the online channel. Since the inception of the first online store, Inditex ...
2000-2001, the Spanish Zara also rose to prominence as an exception (Christian Science Monitor, 2001). At a time when most retailers were outsourcing the bulk of their manufacturing to partially industrialized countries, where labor is significantly cheaper, Benetton and Zara, with their manufacturing facilities in Italy and Spain, respectively,
ZARA'S CASE STUDY: The Strategy of the Fast Fashion Pioneer Page | 1 1. Case Study 1.1. Introduction Zara has always been an interesting case study for many retailers and many other fashion brands around the world. Fashion Apparel industry is constantly changing, and for a
In the first half of the 1990s, Zara's supply chain consisted of problems of inconsistency, imbalances and market saturation for three of the store chains of Zara, plus the inefficient launch of fashion position had created difficulties in joining the U.S. garments market. It has suffered from a significant financial loss in 2001 and a ...
Zara, a notable name in the fashion industry, is a Spanish retailer known for its distinctive approach to clothing and accessories. Operating on a fast fashion model, Zara excels in swiftly adapting to evolving fashion trends, setting it apart in the market. With a vertically integrated process, the brand manages everything from design to ...
Zara Case Study Tanner Jules Gordon-Smith Brand Image Marketing Dr. Woods July 26, 2022. ... Although Zara is a strong retail store they rely very little on promotion. They do ... the company outsources its products. By manufacturing the apparel in a different country they are able to save money on labor and other expenses. Nike manufactures ...
Case Study - Zara: Apparel Manufacturing And Retail - Free download as PDF File (.pdf), Text File (.txt) or read online for free. Scribd is the world's largest social reading and publishing site.
Zara satisfies the needs of style-conscious customers by swiftly bringing in new patterns and styles to its retail locations. This strategy reduces the possibility of products going stale or old, improving the purchasing experience for consumers. Furthermore, Zara's effective inventory control procedures guarantee product availability and ...
THIS IS CASE STUDY ANSWER ACCORDINGLY Zara: Apparel Manufacturing and Retail Zara is a chain of fashion stores owned by Inditex, Spain's largest apparel manufacturer and retailer. In 2012, Inditex reported sales of about 16 billion euros from more than 6,000 retail outlets in about 86 countries. In an industry in which customer demand is ...
Case Study: Zara's Entry into Indian Retail Fashion Market. Zara is an extremely renowned brand, known for its latest designs and is among the top 100 best global brands in 2010 .It uses the unusual strategy of zero advertising and instead invests the revenue in opening new stores across the world. Zara is popular amongst old and young ...
In the case study, it is mentioned that about 40 percent of the manufacturing capacity is owned by Inditex, with the rest outsourced. While Zara manufactures its apparel using a combination of flexible and quick sources in Europe (mostly Portugal and Spain) and low-cost sources in Asia. In-house manufacturing is used as it provides flexible and ...
ZARA: Apparel Manufacturing and Retail Zara is a chain of fashion stores owned by Inditex, Spain's largest apparel manufacturer and retailer. Zara has grown rapidly with a strategy to be highly responsive to changing trends with affordable prices. While the design-to-sales cycle times in the apparel industry normally averaged more than six months, Zara has managed to achieve the cycle times ...
QUESTION ONE [55] Read the case study, and then answer the questions that follow: ZARA: APPAREL MANUFACTURING AND RETAIL Zara is a chain of fashion stores owned by Inditex, Spain's largest apparel manufacturer and retailer. In 2004, Inditex reported sales of 13 billion euros from more than 2,200 retail outlets in 56 countries.