Academia.edu no longer supports Internet Explorer.
To browse Academia.edu and the wider internet faster and more securely, please take a few seconds to upgrade your browser .
Enter the email address you signed up with and we'll email you a reset link.
- We're Hiring!
- Help Center
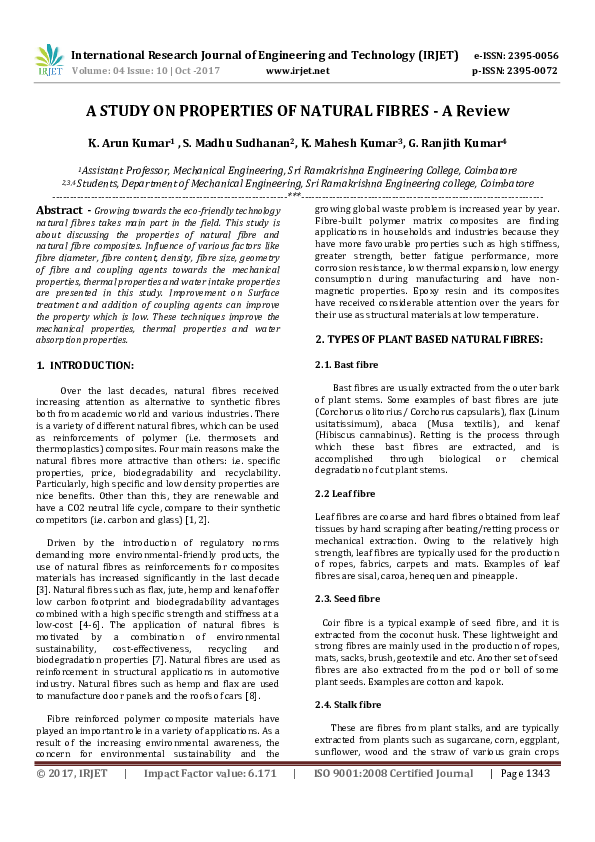
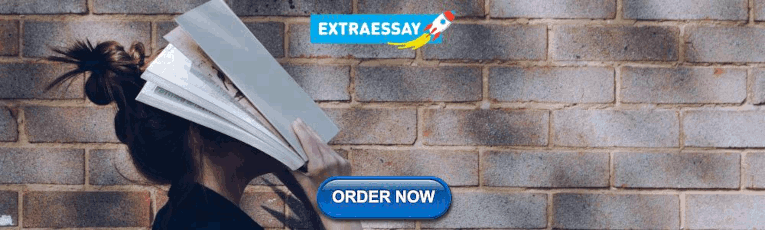
A STUDY ON PROPERTIES OF NATURAL FIBRES -A Review

https://irjet.net/archives/V4/i10/IRJET-V4I10244.pdf
Related Papers
International Journal for Research in Applied Science & Engineering Technology (IJRASET)
IJRASET Publication
Fibre is a long, thin strand or thread of material made by weaving or knitting threads together. Fibre is a hair like strand of material. A fibre is the smallest visible unit of any textile product. Fibres are flexible and may be spun into yarn and made into fabric. Natural fibres are taken from animals, vegetables or mineral sources. A few examples of widely used natural fibres include animal fibre such as wool and silk vegetables fibres, especially cotton and flax and asbestos, a mineral. Natural fibers are more important part in our human environment. Natural fibers are ecofriendly and inexpensive which are readily available in nature. In this chapter we discuss about the overview of natural fiber and their characteristic. this paper also deals with the impact of natural fibers over the synthetic fibers and also the application of natural fiber in various fields.
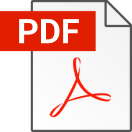
Conference Papers in Materials Science
Mike Clifford , Nesma Aboulkhair , Nicola Everitt
ARYAMAN SINGH
Various analysis has been completed every where the world for creating completely different reasonably natural fibres As a strengthening substance for the preparation of the varied varieties of composites. The material is typically composed of two elements, i.e. matrix and filler chemical therapies in the manner of fibre will clean Stop the absorption of wetness by the fiber surface, with chemicals Modify and raise the surface of the mechanical properties. These studies square measure targeted on developing composition and characterization of mechanical, rheological and structural analysis of obtained composites with completely different plant fillers. Variation of the natural part superimposed in fibre material and analyse its mechanical behaviour to get best style of fibre. These applications square measure principally their strong ratio-to-weight strength magnitude relation, high durability High temperatures, elevated creep resistance and high intensity. Testing of mechanical pro...
Jornual of AL-Farabi for Engineering Sciences
Noor Sabaah
Natural fibers are playing a major role in so many applications such as biomedical applications, aerospace Industry, structural applications, and automotive. This review aims to provide an overview of technological process (chemical treatment), availability, and the most prominent applications of natural fibers that made them preferable to be employed in these applications.
This paper is based on a study of natural fiber, its properties and its application in Today's world Natural fiber composite is the vastest field of research for engineers, professionals and scientists due to its countless properties like biodegradability, less-cost material, low weight, biodegradable, good mechanical properties, ease of availability and microstructural properties. A literature survey has been done on natural fibers (jute, sisal, kenaf, cotton, cotton straw, coir, abaca banana, hemp, neem, etc) and their utilization. This paper represents a review of various natural fibers (Sisal, Abaca and Hemp), their mechanical properties and their application.
Morphological and physicomechanical characterization of synthetic and natural fibers
Aleksey Blaznov , Zakhar S A K O S H E V Germanovich
Green and renewable materials are becoming promising worldwide. Here, we compared morphological and mechanical strength characteristics of natural plant-based bast fibers (flax, hemp and nettle) with those of synthesized fibers (glass, basalt, carbon, polyacrylonitrile (PAN), polycaproamide (PCA) and viscose). The industrial bast fibers from hemp and nettle were extracted by chemical treatment with a sodium carbonate solution. The natural fibers were comparable in size to the synthetic ones. The PCA fibers had the largest diameter of 23–28 µm. The carbon monofiber had the lowest diameter of 7–8 µm. The dimension of the natural elementary fibers was 10–25 µm. The natural fibers had a better interfacial bonding to an epoxy matrix than PCA. Moreover, the specific strength of the unimpregnated and epoxy-impregnated fibers was determined. The natural fibers were superior in strength performance to some of synthetic fibers (viscose), while the specific strength of the impregnated flax fiber was commensurate with that of the impregnated PAN and PCA fibers. The specific strength of the flax and hemp fibers once impregnated with the matrix increased four- and twofold, respectively. The impregnated flax fibers exhibited the best mechanical strength behavior among the hemp and nettle bast fibers. The natural fibers are biodegradable, have a low density, and are more eco-benign than the mineral fibers. The selected natural fibers can be used to fabricate composites therefrom.
Sandeep Bhardwaj
ankit manral
Natural fibers are being used as reinforcement in poly mer based composites to fabricate various high-end application components. Light weight, high strength to weight ratio and bio-degradability are key features of natural fibers. Mechanical propert ies, as well as thermal properties of the components developed using polymer co mposites depend on various microconstituent present in natural fiber. Every constituent present in natural fiber has individual characteristic fo r influencing the properties of the natural fiber reinforced co mposite. The present paper explores the effects of the different constituent present in natural fibers on thermal and mechanical properties of the fibers.
IOP Conference Series: Materials Science and Engineering
Timex Mascaranta
RELATED PAPERS
Erwin Seydel
Proceedings of the National Academy of Sciences
Elaine Ruth Boe
Asian Pacific Journal of Cancer Prevention
Alireza Zade
Human Rights Documents online
Jenny Parkes
International journal of advances in scientific research and engineering
Israel Udoh
Zekayi Kutlubay
Bulletin of the American Physical Society
Ilya Grigorenko
Computer Algebra and Geometric Algebra with Applications
Dr. Ernest Osei , Sphamandla Nkambule
Forensic Science International: Genetics Supplement Series
Havva Altuncul
Applied Solar Energy
Siamak Hoseinzadeh
Revista Brasileira de Direito Internacional
Joel Duarte
fifty fifty
Paula Ponce
MARIA EUGENIA DIAZ OSPINA
Heinrich KLEFENZ
Microorganisms
Gloria Sánchez
Deta Desvitasari
Noa Shashar
Luca Tonetti
Luigi Rolli
christiana Retnaningsih
Laksmita Firdaus
Chemical Science
Brett Ullman
See More Documents Like This
RELATED TOPICS
- We're Hiring!
- Help Center
- Find new research papers in:
- Health Sciences
- Earth Sciences
- Cognitive Science
- Mathematics
- Computer Science
- Academia ©2024
- Reference Manager
- Simple TEXT file
People also looked at
Review article, natural fibers as sustainable and renewable resource for development of eco-friendly composites: a comprehensive review.
- Department of Mechanical and Process Engineering, The Sirindhorn International Thai–German Graduate School of Engineering, King Mongkut's University of Technology North Bangkok, Bangkok, Thailand
The increase in awareness of the damage caused by synthetic materials on the environment has led to the development of eco-friendly materials. The researchers have shown a lot of interest in developing such materials which can replace the synthetic materials. As a result, there is an increase in demand for commercial use of the natural fiber-based composites in recent years for various industrial sectors. Natural fibers are sustainable materials which are easily available in nature and have advantages like low-cost, lightweight, renewability, biodegradability, and high specific properties. The sustainability of the natural fiber-based composite materials has led to upsurge its applications in various manufacturing sectors. In this paper, we have reviewed the different sources of natural fibers, their properties, modification of natural fibers, the effect of treatments on natural fibers, etc. We also summarize the major applications of natural fibers and their effective use as reinforcement for polymer composite materials.
Introduction
Material selection in design and manufacturing of a sustainable product plays a vital role in the field of engineering design. The materials are used to explore their physical properties along with their mechanical properties to make the product better one and reach its customer satisfaction levels. The polymer composite materials are one of such materials which provide the ease of processing, productivity, and cost reduction ( Faruk et al., 2012 ; Al-Oqla and Sapuan, 2014 ; Sanjay and Suchart, 2019 ). The composites are tailor-made materials which have a unique quality where the properties can be altered by varying the different reinforcement and matrix phase ( Bledzki and Gassan, 1999 ; Yogesha, 2017 ). Compared with the synthetic fibers, the natural fibers have many advantages due to their abundance, availability, and low cost ( Arpitha et al., 2017 ; Madhu et al., 2019b ). The natural fibers are introduced instead of synthetic fibers to make the composites lighter. The density of natural fibers (1.2–1.6 g/cm 3 ) is lower than glass fiber (2.4 g/cm 3 ), which leads to the making of the light-weight composites. As a result, there is an increase in the demand for the commercial use of natural fiber-based composites in various industrial sectors. Therefore, natural fibers such as hemp, jute, sisal, banana, coir, and kenaf are extensively used in the production of the lightweight composites ( Sreekala and Thomas, 2003 ; Thakur et al., 2014 ; Oksman et al., 2016 ). The natural fiber-based composites have been used in automotive interior linings (roof, rear wall, side panel lining), furniture, construction, packaging, and shipping pallets, etc. ( Oksman, 2001 ; Lau et al., 2018 ; Sood and Dwivedi, 2018 ; Santhosh Kumar and Hiremath, 2019 ). Natural fibers are extracted from different plants and animals (chicken feather, hair, etc.) ( Aziz and Ansell, 2004 ; Huda et al., 2006 ; Kicinska-Jakubowska et al., 2012 ). The plant fibers are made up of constituents like cellulose, lignin, hemicellulose, pectin, waxes, and water-soluble substances, which is represented in Figure 1 . The presence of cellulose which is hydrophilic in nature affects the interfacial bonding between the polymer matrix and the fibers because the matrix is hydrophobic. Chemical treatment of the natural fibers is one of the ways to optimize the interaction between the fibers and polymer matrix. As it reduces the OH functional groups present on the fiber surface and also it increases the surface roughness and hence enhances the interfacial interaction between the matrix and the fibers ( Liu et al., 2005 ; Mahjoub et al., 2014 ; Manimaran et al., 2017 ; Athith et al., 2018 ; Sanjay et al., 2019a ). The study of natural fibers is very essential to develop eco-friendly composites.
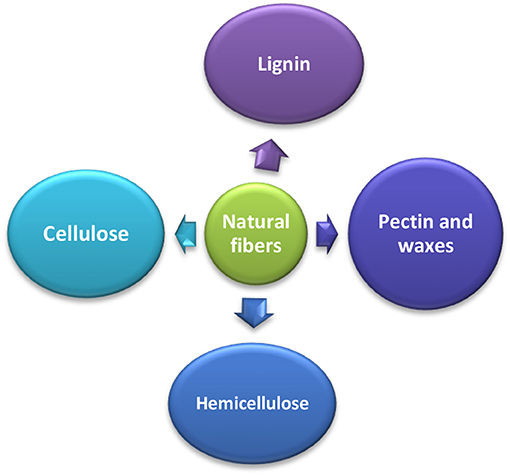
Figure 1 . Constituents of plant fibers ( Faruk et al., 2014 ).
Source, Properties, and Applications of Natural Fibers
Kenaf ( hibiscus cannabinus ).
The kenaf fibers are one of the important fibers belongs to bast fibers and it is mainly used for paper and rope production ( Hamidon et al., 2019 ; Omar et al., 2019 ). Kenaf is a fibrous plant. They are stiff, strong, and tough and have high resistance to insecticides. These plants are cultivated 4,000 years ago in Africa, Asia, America, and some parts of Europe ( Saba et al., 2015 ; Zamri et al., 2016 ; Shahinur and Hasan, 2019b ). The fibers are extracted from flowers, outer fiber, and inner core. The outer fiber is known as bast which makes 40% of the stalks dry weight and the inner core comprises of 60% of stalks dry weight. The kenaf plants upon harvesting are processed by using a mechanical fiber separator and the whole stalk is used in pulping. The extracted fibers must be treated chemically or bacterially to separate it from the non-fibrous substances like wax, pectin, and other substances ( Suharty et al., 2016 ; Arjmandi et al., 2017 ). These fibers can be converted into fine woven fabrics. Kenaf fibers are environmentally friendly as they are completely biodegradable. In the olden days, these fibers were used for textiles, cords, ropes, storage bags, and Egyptians used it for making boats. Nowadays these fibers are made as composites along with other materials and are used in automotive, construction, packaging, furniture, textiles, mats, paper pulp, etc. ( Nishino et al., 2003 ; Anuar and Zuraida, 2011 ; Atiqah et al., 2014 ; Kipriotis et al., 2015 ).
Hemp ( Cannabis sativa )
The Hemp is one of the kinds of plants species grown mainly in Europe and Asia. It grows up to 1.2–4.5 m and 2 cm in diameter ( Bhoopathi et al., 2014 ; Réquilé et al., 2018 ). The inner girth is surrounded by core, and the outer layer is the bast fiber and it is attached to the inner layer by glue-like substance or pectin. These fibers are used in rope, textiles, garden mulch, the assortment of building material and animal beddings. In recent developments, it is used to fabricate different composites ( Li et al., 2006 ; Martin et al., 2013 ; Väisänen et al., 2018 ). The hemp plants are harvested, and the woody core from bast fibers is separated by a sequence of mechanical process. The woody core is cleaned to obtain the required core content and sometimes they are cut to the desired size. While the separated bast fibers are further processed to form yarn or bundles ( Clarke, 2010 ; Duval et al., 2011 ; Fang et al., 2013 ; Raman Bharath et al., 2015 ; Sam-Brew and Smith, 2015 ).
Jute ( Corchorus capsularis )
The jute an important natural fiber grown in parts of Asia including India, Bangladesh, China, and Myanmar ( Khan and Khan, 2014 ; Das, 2017 ; Shahinur and Hasan, 2019a ). The jute plant grows up to 15–20 cm in 4 months, and the fibers are extracted after harvesting which is about 4 months from cultivation. The retting process is done either with the help of chemicals (N 2 H 8 C 2 O 4 , Na 2 SO 3 , etc.) or biologically ( Rahman, 2010 ). In biological retting, the stalks which are harvested are arranged in bundles and allowed to soak in water for about 20 days ( Banik et al., 2003 ; Behera et al., 2012 ). This removes the pectin between the bast and the wood core which helps in the separation of the fibers. Then these fibers are allowed to dry.
Flax ( Linum usitatissimum )
The flax fibers are produced from the prehistoric period. These fibers are separated from the stems of the plant Linum usitatissimum is mainly used to produce linen ( Ruan et al., 2015 ; De Prez et al., 2018 ; Bourmaud et al., 2019 ). These are cellulosic plants but they are more in crystalline form. These fibers measure up to 90 cm length and diameter of 12–16 μm. Netherlands, Belgium, and France are the leading manufacturers of these fibers. These fibers are used in furniture materials, textiles bed sheets, linen, interior decoration accessories, etc. ( Van de Weyenberg et al., 2003 ; Charlet et al., 2010 ; Angelini and Tavarini, 2013 ; Ramesh, 2019 ). The fiber extraction involves the retting, and scorching both this process will make some alterations in the properties of the fibers. The retting involves the enzymes which degrade the pectin around the flax fibers which results in separation of fibers. Canada is the largest flax producer and exporter in the world, produced about 872,000 tons ( Bos et al., 2006 ; Zafeiropoulos and Baillie, 2007 ; Martin et al., 2013 ; Zhu et al., 2013 ).
Ramie ( Boehmeria nivea )
Ramie is one of the herbaceous perennial plants cultivated extensively in the region native to China, Japan, and Malaysia where it has been used for over a century as one of the textile fabrics ( Nam and Netravali, 2006 ; Rehman et al., 2019 ; Yang et al., 2019 ). Ramie is a non-branching, fast-growing plant which grows up to 1–2 m height. The fibers extracted from the stem are the strongest and longest of the natural bast fibers. They are used to make sweaters in combination with cotton, also it is used in upholstery, gas mantle, fishing nets, and marine packings, etc. ( Cengiz and Babalik, 2009 ; Marsyahyo et al., 2009 ; Sen and Jagannatha Reddy, 2011b ). In addition to this attempt has been made for developing bio-based products by utilizing them in the field of automotive, furniture, construction, etc. The ramie fibers are extensively used for the production of a wide range of textiles, pulp, and paper, agrochemicals, composites, etc. The processing of the ramie fibers is similar to linen from flax ( Angelini and Tavarini, 2013 ; Bunsell, 2018 ).
Nettle ( Urtica dioica )
Nettle is the commonly grown herbaceous plant consists of 35–40 different species generally grown in Europe, Asia, Northern Africa, and North America ( Bacci et al., 2009 ; Akgül, 2013 ; Lanzilao et al., 2016 ). The plant usually grows up to 2 m in length, the leaves are soft and green which are 3–15 cm long. The leaves and stems are generally hairy and have stinging hairs on them ( Cummings and Olsen, 2011 ; Fang et al., 2013 ; Bourgeois et al., 2016 ). The fiber extraction is done by harvesting the plants during the flowering period. The fiber is extracted either by retting the stalks or by decorticating. The typical applications of nettle fibers are in the textile industry, bioenergy, animal housing, etc. Nowadays attempts have been made to use the nettle fibers on an industrial scale ( Bacci et al., 2009 ; Mortazavi and Moghaddam, 2010 ).
Pineapple Leaf ( Ananas comosus )
The pineapple plant is one of the abundantly cultivated plants which is easily available. The pineapple leaf fiber is crop waste after pineapple cultivation. It is a short tropical plant grows up to 1–2 m and the leaves are in cluster form consists of 20–30 leaves of about 6 cm wide. Approximately, 90–100 tons of pineapple leaves are grown per hectare. Among the different natural fibers, pineapple leaf fibers show good mechanical properties. Pineapple leaf fibers are multicellular and lingo-cellulosic. The fibers were extracted by hand using the scrapers ( Kengkhetkit and Amornsakchai, 2012 ; Laftah and Abdul Rahaman, 2015 ; Todkar and Patil, 2019 ). The various applications are in automobiles, textile, mats, construction, etc. The treated and surface-modified fibers are used for making conveyor belt cord, air-bag, advanced composites, etc. ( Paridah et al., 2004 ; Jawaid and Abdul Khalil, 2011 ; Reddy and Yang, 2015 ; Al-Maharma and Al-Huniti, 2019 ).
Sisal ( Agave sisalana )
The sisal is one of the most used natural fibers and Brazil is one of the largest producers of this fiber. It is a species native to south Mexico consists of the rosette of leaves grows up to 1.5–2 m tall ( Naveen et al., 2018 ; Sanjay et al., 2018 ; Senthilkumar et al., 2018 ; Devaraju and Harikumar, 2019 ). The sisal produces about 200–250 commercially usable leaves in the life span of 6–7 years. The sisal fibers are having good range of mechanical properties and are used in the automotive industry, shipping industry (for mooring small craft and handling cargo), civil constructions, used as fiber core of the steel wire cables of elevators, agricultural twine or baler twine, etc. ( Mihai, 2013 ; Ramesh et al., 2013 ; Nirmal et al., 2015 ; Aslan et al., 2018 ).
Date Palm ( Phoenix dactylifera )
The date palm is known as palm extensively grown for its fruit. The biodiversity of the date palm is all over the world comprising around 19 species with more than 5,000 cultivators all around the world ( Wales and Blackman, 2017 ; Alotaibi et al., 2019 ; Rivera et al., 2019 ). The date palm trees ( Phoenix dactylifera L.) are the tallest among the Phoenix species and can grow up to 23 m height ( Al-Oqla and Sapuan, 2014 ; Gheith et al., 2018 ; Masri et al., 2018 ). The date palm rachis and leaves are accumulated in large quantity after the harvesting of the date farm fruits every year in the farming lands of different countries. These fibers can be used as the potential cellulosic fiber sources. These fibers from leaves and rachis can be used as the reinforcement for thermoplastic and thermosetting polymers. Some researchers have found ways to use the date palm fibers in the automotive application ( Alawar et al., 2009 ; Arunachalam, 2012 ; Liu et al., 2018 ).
Cotton (Gossypium)
Cotton belongs to the sub-tribe Hibisceae and family of Malvaceae is an important agricultural crop ( Elmogahzy and Farag, 2018 ). It is the commonly used natural fiber for the production of cloths. The cotton is grown in tropical and subtropical regions, and China is the largest producer of cotton followed by India and the United States ( Mwaikambo et al., 2000 ; Colomban and Jauzein, 2018 ). Among the various species of cotton, upland cotton ( Gossypium hirsutum ) and pima cotton ( Gossypium barbadense ) are the most popular ( Zou et al., 2011 ; Al-Oqla et al., 2015 ; Sharma et al., 2017 ). The leaves of the cotton are removed and are collected and compressed into truckload-sized “modules.” Later the modules are transported to processing plant known as the cotton gin. The gin separates the seeds, sticks, burrs, etc. from the cotton fibers. The cotton fiber is used extensively in textile industries, and recently attempts have been made to develop the composites for industrial applications ( Cheung et al., 2009 ; Gupta and Srivastava, 2016 ; Balaji and Senthil Vadivu, 2017 ).
Coconut Fiber ( Cocos nucifera )
The coconut fiber is obtained from the husk of the coconut fruit. Among the different natural fibers, coconut fiber is the thickest. Coconut trees are mainly grown in tropical regions ( Nair, 2010 ; Arulandoo et al., 2016 ; Danso, 2017 ). The major share of the commercially produced coconut fiber comes from India, Sri Lanka, Indonesia, Philippines, and Malaysia ( Pham, 2016 ). Coir fiber, in particular, is a light and strong fiber that has been attracted scientific and commercial importance due to their specific characteristics and availability ( Sen and Jagannatha Reddy, 2011a ). Compared to other typical natural fibers, coconut fiber has higher lignin and lower cellulose and hemicellulose, together with its high microfibrillar angle, offers various valuable properties, such as resilience, strength, and damping, wear, resistance to weathering, and high elongation at break. The coir fiber is used for making ropes, mats, mattresses, brushes, in the upholstery industry, agriculture, construction, etc. ( Al-Oqla and Sapuan, 2014 ; Verma and Gope, 2014 ; Sengupta and Basu, 2016 ; dos Santos et al., 2018 ).
Kapok ( Ceiba pentandra )
Kapok belongs to the Bombacaceae family. It grows in tropical regions ( Arumugam, 2014 ; Zheng et al., 2015 ). Kapok fiber is silk cotton and the color of the fiber is yellowish or light brown. The fibers enclose the kapok seeds. Kapok fibers are cellulosic fibers, light-weight, and hydrophobic ( Prachayawarakorn et al., 2013 ; Wang et al., 2019 ). Conventionally, kapok fiber is used as buoyancy material, oil-absorbing material, reinforcement material, adsorption material, biofuel, etc. ( Tye et al., 2012 ; Dong et al., 2015 ; Zheng et al., 2015 ).
Bamboo (Bambusoideae)
Bamboo fiber is also known as natural glass fiber due to the alignment of fibers in the longitudinal directions ( Zakikhani et al., 2014 ; Wang and Chen, 2016 ). It is one of the extensively available trees in the dense forests especially in China, about 40 families, and 400 species are found ( Fan and Weclawski, 2016 ; Van Dam et al., 2018 ). Bamboo fiber is used as reinforcement in polymeric materials due to its light-weight, low cost, high strength, and stiffness. Bamboo has been traditionally used for making houses, bridges, traditional boats, etc. The fibers extracted from bamboo are used as reinforcement for making advanced composites in various industries ( Deshpande et al., 2000 ; Osorio et al., 2011 ; Zakikhani et al., 2014 ).
Silk ( Bombyx mori )
Silk fibers are extracted from silkworms for the clothing purpose since ancient times. Silk is produced largely in China, South Asia, and Europe ( Das and Natarajan, 2019 ; Shera et al., 2019 ). Fibers are extracted from the Cocoons which are the larvae of the insects undergoing complete metamorphosis. Silk fibers possess good mechanical properties such as high strength, extensibility, and compressibility ( Yuan et al., 2010 ; Murugesh Babu, 2016 ; Castrillón Martínez et al., 2017 ; McGregor, 2018 ).
Possibilities to Enhance the Properties of Natural Fibers
The disadvantage of natural fiber composites includes poor fiber-matrix interfacial bonding, poor wettability, water absorption, and moisture absorption. The hydrophilic nature of the natural fibers caused poor interfacial interaction between the polymer matrix and the fiber. Hence, it is required to optimize the fibers by chemical treatments and surface treatments ( Gassan and Bledzki, 1999 ; George et al., 2001 ; Li et al., 2007 ; Manimaran et al., 2018 ; Rangappa and Siengchin, 2018 ; Sanjay et al., 2018 ; Yashas Gowda et al., 2018 ).
Chemical Treatments
The recent trends in the development of the newer materials have led in replacing materials like glass and carbon reinforced composites with the natural fibers reinforced composites, for example in automobile interior, pedestrian bridge, shipping pallets, composite roof tiles, furniture, toys, etc. ( Senthamaraikannan et al., 2016 ; Senthamaraikannan and Kathiresan, 2018 ; Madhu et al., 2019a ; Sanjay et al., 2019b ). However, the main drawback of natural fibers as reinforcement is that they are incompatible with thermoplastics due to their hydrophilic nature which results in the poor interfacial interaction between the fibers and matrix. This result in the poor mechanical properties of the composites. Therefore, the modification of natural fibers is required to make them less hydrophilic. Here an attempt is made to brief about various chemical treatments on natural fibers ( Sepe et al., 2018 ).
Alkaline Treatment
The natural fiber consists of lignin, pectin, waxy materials, and natural oils which covers the outside layer of the fiber cell wall ( Liu et al., 2004 ; Edeerozey et al., 2007 ; Hamidon et al., 2019 ). The chemical treatment alters the structure of the natural fibers, and sodium hydroxide (NaOH) is one of the chemical reagent used for this process ( Rong et al., 2001 ; Baiardo et al., 2002 ; Sgriccia et al., 2008 ). The alkaline reagent is used to alter the structure of the cellulose in the plant fibers by cleaning the surface and the process called alkalization. Mwaikambo and Ansell treated hemp, jute, sisal, and kapok fibers with the NaOH at 20°C for about 48 h and washed using distilled water and acetic acid to neutralize the excess of NaOH. The thermal properties, surface morphology, and crystallinity index of the treated and untreated fibers were studied. The studies revealed that the chemically treated fibers showed the better fiber-resin adhesion lead to an increase in interfacial energy and thus enhancing the thermal and mechanical properties of the composites ( Mwaikambo and Ansell, 2002 ). Kenaf fiber mats were treated with the NaOH solution for 24 h at a temperature of 45°C. The mats were washed with tap water after the chemical treatment and were immersed in the distilled water containing 1% acetic acid to neutralize the excess of NaOH and the mats were dried for 12 h at 45°C in an oven. The mats were then treated with 5% aminopropyl triethoxysilane diluted with an aqueous solution of methanol. The authors observed a significant increase in mechanical properties for the treated kenaf fiber modified PP composites ( Asumani et al., 2012 ). In an interesting work, the retting process was used to extract the fibers from Napier grass and the aqueous sodium hydroxide solution, about 2–5% is used to treat the Napier grass fibers at room temperature for about 30 min to remove the hemicelluloses and to clean the fibers. The fibers then washed with distilled water repeatedly and dried at 100°C. The alkalization has reduced the amount of hemicellulose in fiber, thus resulting in better mechanical property than that of untreated fiber ( Reddy et al., 2012 ). The Carica papaya fibers were treated with the 5% concentration of NaOH by varying the soaking time from 15 to 90 min at the room temperature. The excess of NaOH from the surface was washed repeatedly using distilled water and was dried for about 56 h. The fibers treated at 60 min with 5% alkaline solution showed the optimum results which showed that complete elimination of hemicelluloses and lignin ( Saravanakumaar et al., 2018 ).
Silane Treatment
The sugar palm fibers are treated with 2% saline and 6% NaOH for 3 h. The authors observed an improved interfacial interaction between the fiber and thermoplastic polyurethane after the treatment ( Atiqah et al., 2018 ). Kabir et al. reviewed the treatment of silane on the surface of natural fibers. They stated that the silane groups act as a coupling agent between the fiber and the matrix and hence improvement's in mechanical properties are observed ( Kabir et al., 2012 ). In an interesting work, Bodur et al. studied the changes in tensile strength and Young's modulus of composites treated with silane for different soaking times. The results were compared with untreated fiber composites. The authors observed significant improvement in strength when compared with untreated fibers. The improvement in strength is due to the formation of silanol (Si-OH) groups that form strong bonds with the –OH groups of the fibers. The remaining Si-OH undergo condensation with adjacent Si-OH groups. The hydrophobic polymerized silane thus formed can attach to the polymer matrix via van der Waals forces. As a result, silane groups form an interface between the fiber and polymer and provides a good interfacial interaction. The high tensile strength of the low-density polyethylene composites is due to good interfacial interaction between the fiber and polymer matrix ( Bodur et al., 2016 ).
Acetylation Treatment
Acetylation of the natural fibers is the process of introducing an acetyl group on the surface of the fibers. This process was used to reduce the hydrophilic nature of fibers providing stability to the composites. The acetylation increases the fiber-matrix adhesion properties, hence the strong bond provides good properties to the natural fiber-based composites ( Hill et al., 1998 ; Rong et al., 2001 ; Sreekala and Thomas, 2003 ). The OH groups of the fibers react with the acetyl groups thus making the fibers more hydrophobic. Generally, lignin and hemicellulose which contain the hydroxyl group react with acetyl groups to become hydrophobic. Normally, before treatment with glacial acetic acid, the natural fiber is alkali-treated. The alkali-treated fibers were soaked in glacial acetic acid for 1 h and later soaked for 2–5 min in acetic anhydride containing two drops of concentrated H 2 SO 4 . The fibers were then washed and dried at 80°C using an oven for 6 h ( Paul et al., 1997 ; Manikandan Nair et al., 2001 ; Mishra et al., 2003 ).
Peroxide Treatment
The impact of peroxide treatment on the mechanical properties of the cellulose fibers reinforced polymer composites has been studied by various researchers. The peroxides decomposed to form free radicals. The generated free radicals react with the hydrogen group of the cellulose fibers and polymer matrix. The peroxide treatment of natural fibers is carried out after alkalization. The alkaline treated fibers were immersed in ca. 6% concentration of benzoyl peroxide or dicumyl peroxide in acetone for about 30 min ( Sreekala et al., 2000 , 2002 ; Li et al., 2007 ).
Benzoylation Treatment
Benzoylation is used to decrease the hydrophilic nature of the fibers ( Ali et al., 2016 ). The fiber-matrix bonding is improved by this treatment which increases the strength of the composites. For benzoylation, the fibers are first treated with NaOH followed by benzoyl chloride (C 6 H 5 COCl) treatment for 15 min. Later the fibers were isolated and treated with ethanol for 1 min and finally washed with distilled water and dried in an oven at 80°C for 24 h ( Manikandan Nair et al., 2001 ; Zhang et al., 2005 ). The thermal stability of the treated fibers was higher than that of the untreated fibers.
Potassium Permanganate (KMnO 4 ) Treatment
The potassium permanganate is used as the chemical reagent to modify the interfacial interaction between the fiber and matrix. Different treatment methodologies are introduced. In one of the studies, the alkaline treated fibers were treated with potassium permanganate for different concentration (0.005–0.205 %) for 1 min and dried using the oven ( Khan et al., 2006 ). Zaman et al. treated the jute fabrics with KMnO 4 along with acetone for different concentration (0.02, 0.03, 0.05, and 0.5%) and soaking times (1, 2, 3, and 5 min) and was dried in the oven ( Zaman et al., 2010 ).
Stearic Acid Treatment
The non-woven jute fibers were immersed in different concentration of stearic acid in anhydrous ethanol from 1 min to up to 4 h and dried at 100°C for 1 h ( Dolez et al., 2017 ). The 1% stearic acid mixed in ethyl alcohol and poured to a steel vessel containing alkali-treated short Sansevieria fibers along with stirring. Then the fibers were dried in woven at 80°C for 45 min ( Sreenivasan et al., 2012 ). Table 1 summarizes the different chemical treatments used for natural fibers.
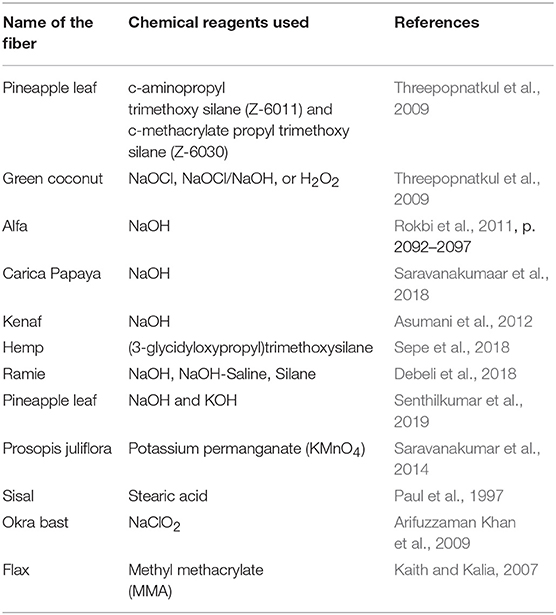
Table 1 . Chemical treatments for different natural fibers.
Effect of Treatments on Natural Fibers
The chemical treatments of the natural fibers mainly enhance the properties of the fiber by modifying their microstructure along with improvement in wettability, surface morphology, chemical groups and tensile strength of the fibers ( Saba et al., 2014 ; Dolez et al., 2017 ; Preet Singh et al., 2017 ; Halip et al., 2018 ; Yu et al., 2019 ). The chemical treatment of the fiber improved the interfacial adhesion between the fiber surface and polymer matrix thereby the thermomechanical properties of the composites. The chemical treatment on ramie fibers has shown that the treatment of fibers with alkaline or saline or the combined treatment results in the improvement of the tensile strength ( Gassan and Bledzki, 1997 ; Thakur and Thakur, 2014 ; Varghese and Mittal, 2017 ; Debeli et al., 2018 ; Sanjay et al., 2019a ). The chemical treatment is one of the important techniques used to reduce the hydrophilic nature of the natural fibers also it improves the adhesion with the matrix. The structural and morphological changes can be observed with the treatment of the fibers, and this is mainly due to the removal of non-cellulosic substances from the natural fibers. The significant improvements of the properties of the composites are reported after different chemical treatments along with the increase in the thermal stability of the composites reinforced with natural fibers ( Singh et al., 1996 ; Xie et al., 2010 ; Xu et al., 2013 ; Chen et al., 2018 ).
Natural Fibers as Reinforcement for Composites Materials
Over the past few decades, attempts have been made in developing the materials which replace the existing materials to have better mechanical and tribological properties for various applications ( Arpitha and Yogesha, 2017 ; Abdellaoui et al., 2019 ). In view of this the monolithic materials are replaced by the fibers and materials such as carbon, glass, aramid fibers which are extensively used in aerospace, automotive, construction, and sporting industries, etc. ( Balakrishnan et al., 2016 ; Pickering et al., 2016 ; Asim et al., 2018 ). However, these materials have some disadvantages like non-biodegradability, non-renewability, high-energy requirement for production, and also harmful to the environment as the production of these materials releases enormous amounts of carbon dioxide into the atmosphere. Therefore, to overcome all these drawbacks researchers has made an attempt to study on the different natural fiber-reinforced composites which have better properties so that they can replace synthetic fibers in various applications ( Wambua et al., 2003 ; Li et al., 2007 ; Sanjay et al., 2015 ; Mochane et al., 2019 ). As the demand for the newer materials which have better properties than the existing ones upsurges, the researchers have tried different types of natural materials with different natural fibers obtained from fruits, seeds, leaves, stem, animals, etc. ( Sanjay et al., 2019a ). The properties of a few important natural fibers are presented in Table 2 . As discussed above, the natural fibers are modified by using different chemical treatments thus modifying the properties and increasing the properties of natural fiber composites. Also, the polymers and other synthetic materials have been used along with the natural fibers to enhance the properties of the natural fibers and these ideas have led to the development of several hybrid composites reinforced with natural fibers, and filler materials ( Sawpan et al., 2011 ; Boopalan et al., 2013 ; Pickering et al., 2016 ; Sanjay et al., 2016 ; Madhu et al., 2018 ).
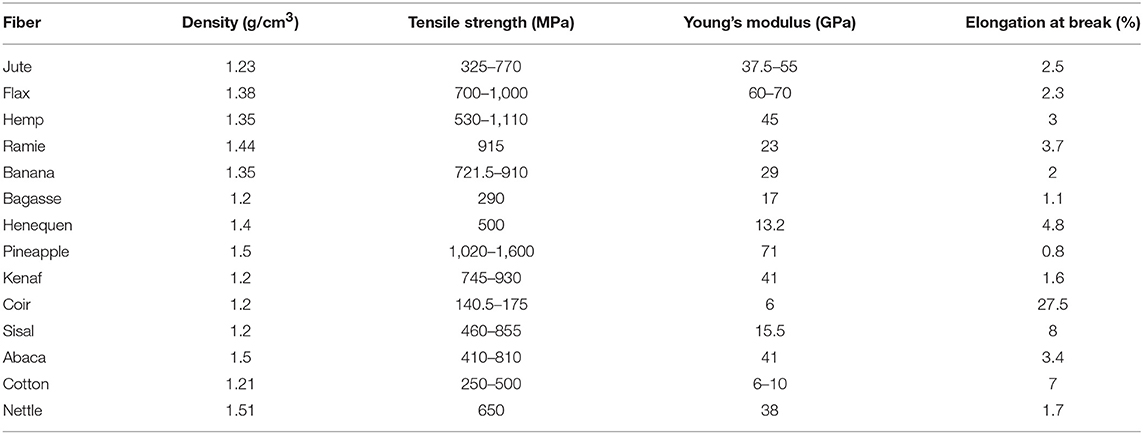
Table 2 . Properties of natural fibers ( Pandey et al., 2010 ; Ku et al., 2011 ; Komuraiah et al., 2014 ; Gurunathan et al., 2015 ).
Properties of Natural Fiber Composites
Environmental awareness has attracted researchers to make new composites with more than one reinforcement of natural resources by hybridization. Hybridization involves a combination of fillers and natural fiber that results in increased mechanical properties of the composites ( Khan et al., 2005 ; Borba et al., 2013 ). Many numbers of literature are available which shows the mechanical properties of the natural fiber composites. The mechanical performance of fiber-reinforced composites can be affected by many factors including the volume or weight fraction of the reinforcement, the orientation of the fibers, the fiber aspect ratio, fiber-matrix adhesion, fiber alignment, distribution, use of additives, and chemical treatment of fibers. It is important to add that the moisture absorption of the composites also affects the mechanical behavior of the composites which leads to the poor interfacial bonding between fiber and hydrophobic matrix polymer ( Zakikhani et al., 2014 ; Biswas et al., 2015 ; Kinloch et al., 2015 ; Pickering et al., 2016 ; Dixit et al., 2017 ).
In the automotive industry, asbestos-based brake pads and lining couplings, etc., are not preferred due to its carcinogenic nature. The replacements to asbestos fiber include ceramic fiber, steel fiber, alumina fiber, glass fiber, carbon fiber, aramid fiber, and their combinations. However, the production cost of these fibers is very high and are not environmentally friendly. Xin et al. studied the friction and wear properties of treated sisal fiber reinforced composites as a substitute for asbestos-based brake pads. The treated sisal fiber reinforced composite exhibits properties equivalent to the commercial friction composite. The authors recommend treated sisal is an ideal substitute of asbestos for brake pads ( Xin et al., 2007 ).
The thermal stability is vital and at present is recognized to be one of the most important elements in the use of fibers as reinforcement for the composite. The chemical treatment of the natural fibers will improve the interfacial bonding between the matrix and fibers leads to improvement in thermal property of the composites ( Panaitescu et al., 2016 ; Balan et al., 2017 ; Zegaoui et al., 2018 ).
Joseph et al. studied the thermal stability and crystallization behavior of sisal/polypropylene composites. The sisal fibers were treated with a urethane derivative of polypropylene glycol (PPG/TDI), maleic anhydride-modified polypropylene (MAPP) and KMnO. The thermal properties of the composites were measured using thermogravimetric analysis and differential scanning calorimetry. The authors observed superior thermal properties for the treated fiber reinforced composites ( Joseph et al., 2003 ). The crystallinity also influences the thermal stability of the natural fiber composites. As the crystallinity of the material increased the thermal degradation temperature also increased ( Nasser et al., 2016 ). The thermogravimetry analysis of date palm trunk (DPTRF), leaf stalk (DPLST), sheath or leaf sheath (DPLSH), and fruit bunch stalk (DPFBS) fibers was carried out and analysis revealed that DPFBS and DPLST fibers have good thermal stability and might be applied in industrial manufacture of composites, which require high thermal resistance ( Alotaibi et al., 2019 ).
The pineapple reinforced polyethylene composites were studied for the electrical properties and found that due to the increased interfacial polarization and orientation with an increase in the number of fibers in composites the dielectric property increases ( Jayamol et al., 1997 ). Similarly, the composites prepared with using the sisal fiber showed electric anisotropic behavior ( Chand and Jain, 2005 ). It is observed that the chemical treatments like alkali, stearic acid, peroxide, acetylation, and permanganate decrease the dielectric property of composites due to the decrease in hydrophilicity of the composite ( Li et al., 2000 ). The electrical properties of phenol formaldehyde composites modified with banana fiber have been studied. The dielectric constant decreased with fiber loading and fiber treatment. For hybrid composites with glass fiber, the dielectric constant decreased with increasing glass fiber concentration ( Joseph and Thomas, 2008 ).
Applications
Automotive and aircraft industries have been actively manufacturing different kinds of natural fibers parts for their interior components ( Sanjay et al., 2016 ; Puttegowda et al., 2018 ). Insulation materials are also made from natural fibers for different application areas, such as blowing insulation, pouring insulation, impact sound insulation materials and ceiling panels for thermal insulation, and acoustic soundproofing ( Akin, 2010 ). Natural fibers show a sustainable future in architecture, with a vast variety of building materials, shapes, and even improving current commonly used materials. The use of synthetic fibers in the field of architecture could be substituted with natural fibers. It is used as material for sunscreens, cladding, walling, and flooring ( Steffens et al., 2017 ). The natural fibers such as flax, hemp, sisal, and wool are now used in Mercedes-Benz components ( Holbery and Houston, 2006 ). The coir/polyester-reinforced composites were used in the mirror casing, paperweights, voltage stabilizer cover, projector cover, helmet, and roof ( Khondker et al., 2005 ). The flax fibers were used in GreenBente24 boat ( Ticoalu et al., 2010 ). Rice husk fiber, cotton, ramie, jute fiber, kenaf are used in various applications like building materials, furniture industry, clothing, ropes, sewing thread, fishing nets, packing materials, and paper manufacture ( Sen and Jagannatha Reddy, 2011b ). Lots of efforts have been made to increase the use of natural fiber composites in the automotive industry, particularly in car interiors. Besides the use for car interior parts, it also used for manufacturing exterior auto body components ( Shuit et al., 2009 ; Monteiro et al., 2010 ; Shinoj et al., 2011 ; Mohammed et al., 2015 ).
Degradation of the Natural Fibers Reinforced Polymers
In the present scenario, there is an increase in awareness regarding the environmental pollutions due to industrial waste which has led to replacing the harmful synthetic materials with more eco-friendly materials. The use of plastics is increased especially for household and commercial use. The use of plastic products leads to the accumulation of non-biodegradable wastes and are a threat to the ecological system. Therefore, extensive research has been carried out over the last decade on the biodegradation of plastics. Natural fibers along with the synthetic biodegradable materials can be used to develop biocomposites which have benefits toward the environment like biodegradability, renewability of base material, and reduction in emission of greenhouse gasses. Degradation offers a lot of advantages such as the reduction of plastic waste and reduction in the cost of waste management ( Fakhrul and Islam, 2013 ; Gunti et al., 2018 ).
Degradation of the composite occurs with the breakdown of the composite materials, as well as with the loss of mechanical properties. In the outdoor environment, the degradation of natural fiber reinforced composites is influenced by atmospheric moisture, temperature, ultraviolet light and activities of microscopic organisms. The degradation occurs by the breakdown of hemicelluloses, lignin, and cellulose of the fiber. This can cause damage to the bonding between fibers and polymer matrix. Thus, leads to the lowering of the mechanical properties of the composites ( de Melo et al., 2017 ). The kenaf/POM composites were subjected to weathering by exposing to moisture, water spray, and UV light in an accelerated weathering chamber and the materials showed lower tensile strength and this result was attributed to the degradation of the cellulose, hemicelluloses, and lignin of kenaf fibers ( Abdullah et al., 2013 ). The effect of weathering on the degradation of jute/phenolic composites was investigated by Azwa et al. (2013) . It shows that 2 years of UV exposure on jute/phenolic composites has decreased the tensile strength by about 50%. The authors observed resin cracking, bulging, fibrillation, and black spots after exposure to weathering.
It is necessary to promote the use of natural fibers as reinforcement in the polymer so that the materials become biodegradable to some extent. Proper degradation of the plastics must be a better way to avoid the harmful effects on the environment. Therefore, one must always look for the plastics which are compostable or degradable. However, this cannot be implemented for every material but can be reduced with the use of biopolymers to some extent ( Chauhan and Chauhan, 2015 ; Thiagamani et al., 2019 ).
Future Market Trends
In current market trends, natural fibers reinforced polymers are experiencing comprehensive growth with good prospects in automotive and construction industries. Bast fiber such as hemp, kenaf, flax, etc., are preferred for automotive applications. On the other hand, wood plastic composite is the material of choice for construction industries. Looking at the developments of the current trends Europe is predicted to remain as the largest market for natural fiber-reinforced composites due to the high acceptance level of environmentally friendly composite materials by automotive industries, government agencies, and growth in small scale environmentally friendly industries. The improvement in materials performance will drive the growth of natural fiber reinforced polymer composites in new potential areas. Natural fiber composites are new in electrical, electronics and sporting segments, however, it has the potential to capture a good market share in the future.
Conclusions
Increased environmental awareness has resulted in the utilization of natural fiber as an effective reinforcement material in polymer matrix composites. Natural fibers are proficient materials which can replace the existing synthetic fibers. The fibers are usually extracted from plants and animals often offer poor resistance to moisture and incompatible nature of fibers become the main disadvantage. Therefore, modification of material properties has done through chemical treatments of natural fibers which improve the adhesion between the fibers and matrix and enhance the mechanical properties of the composites. In the near future, the natural fiber will become one of the sustainable and renewable resources in the composite field which can replace synthetic fibers in many applications.
Author Contributions
All authors listed have made a substantial, direct and intellectual contribution to the work, and approved it for publication.
This research was partly supported by the King Mongkut's University of Technology North Bangkok with Grant No. KMUTNB-63-KNOW-001.
Conflict of Interest Statement
The authors declare that the research was conducted in the absence of any commercial or financial relationships that could be construed as a potential conflict of interest.
Abdellaoui, H., Raji, M., Essabir, H., Bouhfid, R., and el kacem Qaiss, A. (2019). “Mechanical behavior of carbon/natural fiber-based hybrid composites,” in Mechanical and Physical Testing of Biocomposites, Fibre-Reinforced Composites and Hybrid Composites , eds M. Jawaid, M. Thariq, and N. Saba (Woodhead Publishing), 103–122. doi: 10.1016/B978-0-08-102292-4.00006-0
CrossRef Full Text | Google Scholar
Abdullah, M. Z., Dan-mallam, Y., Sri, P., and Megat, M. (2013). Effect of environmental degradation on mechanical properties of kenaf/polyethylene terephthalate fiber reinforced polyoxymethylene hybrid composite. Adv. Mater. Sci. Eng. 2013:671481. doi: 10.1155/2013/671481
Akgül, M. (2013). Suitability of stinging nettle ( Urtica dioica L.) stalks for medium density fiberboards production. Compos. Part B Eng. 45, 925–929. doi: 10.1016/j.compositesb.2012.09.048
Akin, D. E. (2010). “Chemistry of plant fibres,” in Industrial Applications of Natural Fibres: Structure, Properties and Technical Applications , ed J. Müssing (West Sussex: John Wiley & Sons Ltd.), 13–22.
Google Scholar
Alawar, A., Hamed, A. M., and Al-Kaabi, K. (2009). Characterization of treated date palm tree fiber as composite reinforcement. Compos. Part B Eng. 40, 601–606. doi: 10.1016/j.compositesb.2009.04.018
Ali, A., Shaker, K., Nawab, Y., Jabbar, M., Hussain, T., Militky, J., et al. (2016). Hydrophobic treatment of natural fibers and their composites — a review. J. Ind. Text. 47, 1–31. doi: 10.1177/1528083716654468
Al-Maharma, A., and Al-Huniti, N. (2019). Critical review of the parameters affecting the effectiveness of moisture absorption treatments used for natural composites. J. Compos. Sci. 3:27. doi: 10.3390/jcs3010027
Al-Oqla, F. M., and Sapuan, S. M. (2014). Natural fiber reinforced polymer composites in industrial applications: feasibility of date palm fibers for sustainable automotive industry. J. Clean. Prod. 66, 347–354. doi: 10.1016/j.jclepro.2013.10.050
Al-Oqla, F. M., Sapuan, S. M., Anwer, T., Jawaid, M., and Hoque, M. E. (2015). Natural fiber reinforced conductive polymer composites as functional materials: a review. Synth. Met. 206, 42–54. doi: 10.1016/j.synthmet.2015.04.014
Alotaibi, M. D., Alshammari, B. A., Saba, N., Alothman, O. Y., Sanjay, M. R., Almutairi, Z., et al. (2019). Characterization of natural fiber obtained from different parts of date palm tree ( Phoenix dactylifera L.). Int. J. Biol. Macromol. 135, 69–76. doi: 10.1016/j.ijbiomac.2019.05.102
PubMed Abstract | CrossRef Full Text | Google Scholar
Angelini, L. G., and Tavarini, S. (2013). Ramie [ Boehmeria nivea (L.) Gaud.] as a potential new fibre crop for the Mediterranean region: growth, crop yield and fibre quality in a long-term field experiment in Central Italy. Ind. Crops Prod. 51, 138–144. doi: 10.1016/j.indcrop.2013.09.009
Anuar, H., and Zuraida, A. (2011). Improvement in mechanical properties of reinforced thermoplastic elastomer composite with kenaf bast fibre. Compos. Part B Eng. 42, 462–465. doi: 10.1016/j.compositesb.2010.12.013
Arifuzzaman Khan, G. M., Shaheruzzaman, M., Rahman, M. H., Abdur Razzaque, S. M., Islam, M. S., and Alam, M. S. (2009). Surface modification of okra bast fiber and its physico-chemical characteristics. Fibers Polym. 10, 65–70. doi: 10.1007/s12221-009-0065-1
Arjmandi, R., Hassan, A., and Zakaria, Z. (2017). “Rice husk and kenaf fiber reinforced polypropylene biocomposites,” in Lignocellulosic Fibre and Biomass-Based Composite Materials , eds M. Jawaid, M. T. Paridah, and N. Saba (Woodhead Publishing), 77–94. doi: 10.1016/B978-0-08-100959-8.00005-6
Arpitha, G. R., Sanjay, M. R., Senthamaraikannan, P., Barile, C., and Yogesha, B. (2017). Hybridization effect of sisal/glass/epoxy/filler based woven fabric reinforced composites. Exp. Tech. 41, 577–584. doi: 10.1007/s40799-017-0203-4
Arpitha, G. R., and Yogesha, B. (2017). Science direct an overview on mechanical property evaluation of natural fiber reinforced polymers. Mater. Today Proc. 4, 2755–2760. doi: 10.1016/j.matpr.2017.02.153
Arulandoo, X., Sritharan, K., and Subramaniam, M. (2016). The Coconut Palm, 2nd Edn . Elsevier. doi: 10.1016/B978-0-12-394807-6.00237-9
Arumugam, V. (2014). A preliminary investigation on Kapok/polypropylene nonwoven composites for sound absorption. Ind. J. Fibre Text. Res. 37, 385–388.
Arunachalam, V. (2012). Date palm. Genomics Cultiv. Palms , 49–59. doi: 10.1016/B978-0-12-387736-9.00004-2
Asim, M., Saba, N., Jawaid, M., and Nasir, M. (2018). “Potential of natural fiber/biomass filler-reinforced polymer composites in aerospace applications,” in Sustainable Composites for Aerospace Applications , eds M. Jawaid and M. Thariq (Elsevier Ltd.), 253–268. doi: 10.1016/B978-0-08-102131-6.00012-8
Aslan, M., Tufan, M., and Küçükömeroglu, T. (2018). Tribological and mechanical performance of sisal-filled waste carbon and glass fibre hybrid composites. Compos. Part B Eng. 140, 241–249. doi: 10.1016/j.compositesb.2017.12.039
Asumani, O. M. L., Reid, R. G., and Paskaramoorthy, R. (2012). The effects of alkali–silane treatment on the tensile and flexural properties of short fibre non-woven kenaf reinforced polypropylene composites. Compos Part A Appl. Sci. Manufact. 43, 1431–1440. doi: 10.1016/j.compositesa.2012.04.007
Athith, D., Sanjay, M. R., Yashas Gowda, T. G., Madhu, P., Arpitha, G. R., Yogesha, B., et al. (2018). Effect of tungsten carbide on mechanical and tribological properties of jute/sisal/E-glass fabrics reinforced natural rubber/epoxy composites. J. Ind. Text. 48, 713–737. doi: 10.1177/1528083717740765
Atiqah, A., Jawaid, M., Ishak, M. R., and Sapuan, S. M. (2018). Effect of alkali and silane treatments on mechanical and interfacial bonding strength of sugar palm fibers with thermoplastic polyurethane. J. Nat. Fibers 15, 251–261. doi: 10.1080/15440478.2017.1325427
Atiqah, A., Maleque, M. A., Jawaid, M., and Iqbal, M. (2014). Development of kenaf-glass reinforced unsaturated polyester hybrid composite for structural applications. Compos. Part B 56, 68–73. doi: 10.1016/j.compositesb.2013.08.019
Aziz, S. H., and Ansell, M. P. (2004). The effect of alkalization and fibre alignment on the mechanical and thermal properties of kenaf and hemp bast fibre composites: part 1 - polyester resin matrix. Compos. Sci. Technol. 64, 1219–1230. doi: 10.1016/j.compscitech.2003.10.001
Azwa, Z. N., Yousif, B. F., Manalo, A. C., and Karunasena, W. (2013). A review on the degradability of polymeric composites based on natural fibres. Mater. Des. 47, 424–442. doi: 10.1016/j.matdes.2012.11.025
Bacci, L., Baronti, S., Predieri, S., and di Virgilio, N. (2009). Fiber yield and quality of fiber nettle ( Urtica dioica L.) cultivated in Italy. Ind. Crops Prod. 29, 480–484. doi: 10.1016/j.indcrop.2008.09.005
Baiardo, M., Frisoni, G., Scandola, M., and Licciardello, A. (2002). Surface chemical modification of natural cellulose fibers. J. Appl. Polym. Sci. 83, 38–45. doi: 10.1002/app.2229
Balaji, V., and Senthil Vadivu, K. (2017). Mechanical characterization of coir fiber and cotton fiber reinforced unsaturated polyester composites for packaging applications mechanical characterization of coir fiber and cotton fiber reinforced. J. Appl. Packag. Res. 9, 12–19.
Balakrishnan, P., John, M. J., Pothen, L., Sreekala, M. S., and Thomas, S. (2016). “Natural fibre and polymer matrix composites and their applications in aerospace engineering,” in Advanced Composite Materials for Aerospace Engineering , eds S. Rana and R. Fangueiro (Elsevier Ltd.), 365–383. doi: 10.1016/B978-0-08-100037-3.00012-2
Balan, A. K., Mottakkunnu Parambil, S., Vakyath, S., Thulissery Velayudhan, J., Naduparambath, S., and Etathil, P. (2017). Coconut shell powder reinforced thermoplastic polyurethane/natural rubber blend-composites: effect of silane coupling agents on the mechanical and thermal properties of the composites. J. Mater. Sci. 52, 6712–6725. doi: 10.1007/s10853-017-0907-y
Banik, S., Basak, M. K., Paul, D., Nayak, P., Sardar, D., Sil, S. C., et al. (2003). Ribbon retting of jute - a prospective and eco-friendly method for improvement of fibre quality. Ind. Crops Prod. 17, 183–190. doi: 10.1016/S0926-6690(02)00097-3
Behera, A. K., Avancha, S., Basak, R. K., Sen, R., and Adhikari, B. (2012). Fabrication and characterizations of biodegradable jute reinforced soy based green composites. Carbohydr. Polym. 88, 329–335. doi: 10.1016/j.carbpol.2011.12.023
Bhoopathi, R., Ramesh, M., and Deepa, C. (2014). Fabrication and property evaluation of banana-hemp-glass fiber reinforced composites. Proc. Eng. 97, 2032–2041. doi: 10.1016/j.proeng.2014.12.446
Biswas, S., Shahinur, S., Hasan, M., and Ahsan, Q. (2015). Physical, mechanical and thermal properties of jute and bamboo fiber reinforced unidirectional epoxy composites. Proc. Eng. 105, 933–939. doi: 10.1016/j.proeng.2015.05.118
Bledzki, A. K., and Gassan, J. (1999). Composites reinforced with cellulose based fibres. Prog. Polym. Sci. 24, 221–274. doi: 10.1016/S0079-6700(98)00018-5
Bodur, M. S., Bakkal, M., and Sonmez, H. E. (2016). The different chemical treatment methods. J. Compos. Mater. 50, 3817–3830. doi: 10.1177/0021998315626256
Boopalan, M., Niranjanaa, M., and Umapathy, M. J. (2013). Study on the mechanical properties and thermal properties of jute and banana fiber reinforced epoxy hybrid composites. Compos. Part B Eng. 51, 54–57. doi: 10.1016/j.compositesb.2013.02.033
Borba, P. M., Tedesco, A., and Lenz, D. M. (2013). Effect of reinforcement nanoparticles addition on mechanical properties of SBS/curauá fiber composites. Mater. Res. 17, 412–419. doi: 10.1590/S1516-14392013005000203
Bos, H. L., Müssig, J., and van den Oever, M. J. A. (2006). Mechanical properties of short-flax-fibre reinforced compounds. Compos. Part A Appl. Sci. Manuf. 37, 1591–1604. doi: 10.1016/j.compositesa.2005.10.011
Bourgeois, C., Leclerc, É. A., Corbin, C., Doussot, J., Serrano, V., Vanier, J. R., et al. (2016). L'ortie ( Urtica dioica L.), une source de produits antioxidants et phytochimiques anti-âge pour des applications en cosmétique. Comptes Rendus Chim. 19, 1090–1100. doi: 10.1016/j.crci.2016.03.019
Bourmaud, A., Siniscalco, D., Foucat, L., Goudenhooft, C., Falourd, X., Pontoire, B., et al. (2019). Evolution of flax cell wall ultrastructure and mechanical properties during the retting step. Carbohydr. Polym. 206, 48–56. doi: 10.1016/j.carbpol.2018.10.065
Bunsell, A. R. (ed.). (2018). “Introduction to the science of fibers,” in Handbook of Properties of Textile and Technical Fibres (Woodhead Publishing), 1–20. doi: 10.1016/B978-0-08-101272-7.00001-8
Castrillón Martínez, D. C., Zuluaga, C. L., Restrepo-Osorio, A., and Álvarez-López, C. (2017). Characterization of sericin obtained from cocoons and silk yarns. Proc. Eng. 200, 377–383. doi: 10.1016/j.proeng.2017.07.053
Cengiz, T. G., and Babalik, F. C. (2009). The effects of ramie blended car seat covers on thermal comfort during road trials. Int. J. Ind. Ergon. 39, 287–294. doi: 10.1016/j.ergon.2008.12.002
Chand, N., and Jain, D. (2005). Effect of sisal fibre orientation on electrical properties of sisal fibre reinforced epoxy composites. Compos. Part A Appl. Sci. Manuf. 36, 594–602. doi: 10.1016/j.compositesa.2004.08.002
Charlet, K., Jernot, J. P., Breard, J., and Gomina, M. (2010). Scattering of morphological and mechanical properties of flax fibres. Ind. Crops Prod. 32, 220–224. doi: 10.1016/j.indcrop.2010.04.015
Chauhan, A., and Chauhan, P. (2015). Natural fibers and biopolymer. J. Chem. Eng. Process Technol. 6, 1–4. doi: 10.4172/2157-7048.S6-001
Chen, Y., Su, N., Zhang, K., Zhu, S., Zhu, Z., Qin, W., et al. (2018). Effect of fiber surface treatment on structure, moisture absorption and mechanical properties of luffa sponge fiber bundles. Ind. Crops Prod. 123, 341–352. doi: 10.1016/j.indcrop.2018.06.079
Cheung, H., Ho, M., Lau, K., Cardona, F., and Hui, D. (2009). Natural fibre-reinforced composites for bioengineering and environmental engineering applications. Compos. Part B Eng. 40, 655–663. doi: 10.1016/j.compositesb.2009.04.014
Clarke, R. C. (2010). Traditional fiber hemp (Cannabis) production, processing, yarn making, and weaving strategies-functional constraints and regional responses. Part 2. J. Nat. Fibers 7, 229–250. doi: 10.1080/15440478.2010.504043
Colomban, P., and Jauzein, V. (2018). “Silk: fibers, films, and composites-types, processing, structure, and mechanics,” in Handbook of Properties of Textile and Technical Fibres , ed A. R. Bunsell (Woodhead Publishing), 137–183. doi: 10.1016/B978-0-08-101272-7.00005-5
Cummings, A. J., and Olsen, M. (2011). Mechanism of action of stinging nettles. Wilderness Environ. Med. 22, 136–139. doi: 10.1016/j.wem.2011.01.001
Danso, H. (2017). Properties of coconut, oil palm and bagasse fibres: as potential building materials. Proc. Eng. 200, 1–9. doi: 10.1016/j.proeng.2017.07.002
Das, S. (2017). Mechanical properties of waste paper/jute fabric reinforced polyester resin matrix hybrid composites. Carbohydr. Polym. 172, 60–67. doi: 10.1016/j.carbpol.2017.05.036
Das, S., and Natarajan, G. (2019). “Silk fiber composites in biomedical applications,” in Materials for Biomedical Engineering , eds V. Grumezescu and A. Mihai Grumezescu (Elsevier), 309–338. doi: 10.1016/B978-0-12-816872-1.00011-X
de Melo, R. P., Marques, M. F. V., Navard, P., and Duque, N. P. (2017). Degradation studies and mechanical properties of treated curauá fibers and microcrystalline cellulose in composites with polyamide 6. J. Compos. Mater. 51, 3481–3489. doi: 10.1177/0021998317690446
De Prez, J., Van Vuure, A. W., Ivens, J., Aerts, G., and Van de Voorde, I. (2018). Enzymatic treatment of flax for use in composites. Biotechnol. Rep. 20:e00294. doi: 10.1016/j.btre.2018.e00294
Debeli, D. K., Qin, Z., and Guo, J. (2018). Study on the pre-treatment, physical and chemical properties of ramie fibers reinforced poly (Lactic Acid) (PLA) biocomposite. J. Nat. Fibers 15, 596–610. doi: 10.1080/15440478.2017.1349711
Deshpande, A. P., Bhaskar Rao, M., and Lakshmana Rao, C. (2000). Extraction of bamboo fibers and their use as reinforcement in polymeric composites. J. Appl. Polym. Sci. 76, 83–92 doi: 10.1002/(SICI)1097-4628(20000404)76:1<83::AID-APP11>3.0.CO;2-L
Devaraju, A., and Harikumar, R. (2019). “Life cycle assessment of sisal fiber,” in Reference Module in Materials Science and Materials Engineering (Elsevier Ltd.). doi: 10.1016/B978-0-12-803581-8.10552-1
Dixit, S., Goel, R., Dubey, A., Shivhare, P. R., and Bhalavi, T. (2017). Natural fibre reinforced polymer composite materials - A review. Polym. Renew. Resour. 8, 71–78. doi: 10.1177/204124791700800203
Dolez, P. I., Arfaoui, M. A., Dub,é, M., and David, É. (2017). Hydrophobic treatments for natural fibers based on metal oxide nanoparticles and fatty acids. Proc. Eng. 200, 81–88. doi: 10.1016/j.proeng.2017.07.013
Dong, T., Xu, G., and Wang, F. (2015). Adsorption and adhesiveness of kapok fiber to different oils. J. Hazard. Mater. 296, 101–111. doi: 10.1016/j.jhazmat.2015.03.040
dos Santos, J. C., Siqueira, R. L., Vieira, L. M. G., Freire, R. T. S., Mano, V., and Panzera, T. H. (2018). Effects of sodium carbonate on the performance of epoxy and polyester coir-reinforced composites. Polym. Test. 67, 533–544. doi: 10.1016/j.polymertesting.2018.03.043
Duval, A., Bourmaud, A., Augier, L., and Baley, C. (2011). Influence of the sampling area of the stem on the mechanical properties of hemp fibers. Mater. Lett. 65, 797–800. doi: 10.1016/j.matlet.2010.11.053
Edeerozey, A. M. M., Akil, H. M., Azhar, A. B., and Ariffin, M. I. Z. (2007). Chemical modification of kenaf fibers. Mater. Lett. 61, 2023–2025. doi: 10.1016/j.matlet.2006.08.006
Elmogahzy, Y., and Farag, R. (2018). “Tensile properties of cotton fibers: importance, research, and limitations”, in Handbook of Properties of Textile and Technical Fibres , ed A. R. Bunsell (Woodhead Publishing), 223–273. doi: 10.1016/B978-0-08-101272-7.00007-9
Fakhrul, T., and Islam, M. A. (2013). Degradation behavior of natural fiber reinforced polymer matrix composites. Proc. Eng. 56, 795–800. doi: 10.1016/j.proeng.2013.03.198
Fan, M., and Weclawski, B. (2016). “Long natural fibre composites,” in Advanced High Strength Natural Fibre Composites in Construction , eds M. Fan and F. Fu (Woodhead Publishing), 141–177. doi: 10.1016/B978-0-08-100411-1.00006-6
Fang, H., Zhang, Y., Deng, J., and Rodrigue, D. (2013). Effect of fiber treatment on the water absorption and mechanical properties of hemp fiber/polyethylene composites. J. Appl. Polym. Sci. 127, 942–949. doi: 10.1002/app.37871
Faruk, O., Bledzki, A. K., Fink, H. P., and Sain, M. (2012). Biocomposites reinforced with natural fibers: 2000-2010. Prog. Polym. Sci. 37, 1552–1596. doi: 10.1016/j.progpolymsci.2012.04.003
Faruk, O., Bledzki, A. K., Fink, H. P., and Sain, M. (2014). Progress report on natural fiber reinforced composites. Macromol. Mater. Eng. 299, 9-26. doi: 10.1002/mame.201300008
Gassan, J., and Bledzki, A. K. (1997). The influence of fiber-surface treatment on the mechanical properties of jute-polypropylene composites. Compos. Part A Appl. Sci. Manuf. 28, 1001–1005. doi: 10.1016/S1359-835X(97)00042-0
Gassan, J., and Bledzki, A. K. (1999). Possibilities for improving the mechanical properties of jute/epoxy composites by alkali treatment of fibres. Compos. Sci. Technol. 59, 1303–1309. doi: 10.1016/S0266-3538(98)00169-9
George, J., Sreekala, M. S., and Thomas, S. (2001). A review on interface modification and characterization of natural fiber reinforced plastic composites. Polym. Eng. Sci. 41, 1471–1485. doi: 10.1002/pen.10846
Gheith, M. H., Aziz, M. A., Ghori, W., Saba, N., Asim, M., Jawaid, M., et al. (2018). Flexural, thermal and dynamic mechanical properties of date palm fibres reinforced epoxy composites. J. Mater. Res. Technol. 8, 853–860. doi: 10.1016/j.jmrt.2018.06.013
Gunti, R., Ratna Prasad, A. V., and Gupta, A. V. S. S. K. S. (2018). Mechanical and degradation properties of natural fiber-reinforced PLA composites: jute, sisal, and elephant grass. Polym. Compos. 39, 1125–1136. doi: 10.1002/pc.24041
Gupta, M. K., and Srivastava, R. K. (2016). Mechanical properties of hybrid fibers-reinforced polymer composite: a review. Polym. Plast. Technol. Eng. 55, 626–642. doi: 10.1080/03602559.2015.1098694
Gurunathan, T., Mohanty, S., and Nayak, S. K. (2015). A review of the recent developments in biocomposites based on natural fibres and their application perspectives. Compos Part Appl. Sci. Manuf. 77, 1–25. doi: 10.1016/j.compositesa.2015.06.007
Halip, J. A., Hua, L. S., Ashaari, Z., Tahir, P. M., Chen, L. W., and Uyup, M. K. A. (2018). “Effect of treatment on water absorption behavior of natural,” in Mechanical and Physical Testing of Biocomposites, Fibre-Reinforced Composites and Hybrid Composites , eds M. Jawaid, M. Thariq, and N. Saba (Woodhead Publishing), 141–156. doi: 10.1016/B978-0-08-102292-4.00008-4
Hamidon, M. H., Sultan, M. T. H., Ariffin, A. H., and Shah, A. U. M. (2019). Effects of fibre treatment on mechanical properties of kenaf fibre reinforced composites: a review. J. Mater. Res. Technol. 8, 3327–3337. doi: 10.1016/j.jmrt.2019.04.012
Hill, C. A. S., Khalil, H. P. S. A., and Hale, M. D. (1998). A study of the potential of acetylation to improve the properties of plant fibres. Ind. Crops Prod. 8, 53–63. doi: 10.1016/S0926-6690(97)10012-7
Holbery, J., and Houston, D. (2006). Natural-fiber-reinforced polymer composites in automotive applications. JOM 58, 80–86. doi: 10.1007/s11837-006-0234-2
Huda, M. S., Drzal, L. T., Mohanty, A. K., and Misra, M. (2006). Chopped glass and recycled newspaper as reinforcement fibers in injection molded poly(lactic acid) (PLA) composites: a comparative study. Compos. Sci. Technol. 66, 1813–1824. doi: 10.1016/j.compscitech.2005.10.015
Jawaid, M., and Abdul Khalil, H. P. S. (2011). Cellulosic/synthetic fibre reinforced polymer hybrid composites: a review. Carbohydr. Polym. 86, 1–18. doi: 10.1016/j.carbpol.2011.04.043
Jayamol, G., Bhagawan, S. S., and Thomas, S. (1997). Electrical properties of pineapple fibre reinforced polyethylene composites. J. Polym. Eng. 17, 383–404. doi: 10.1515/POLYENG.1997.17.5.383
Joseph, P. V., Joseph, K., Thomas, S., Pillai, C. K. S., Prasad, V. S., Groeninckx, G., et al. (2003). The thermal and crystallization studies of polypropylene composites. Compos. Part A Appl. Sci. Manufact. 34, 253–266. doi: 10.1016/S1359-835X(02)00185-9
Joseph, S., and Thomas, S. (2008). Electrical properties of banana fiber reinforced phenol formaldehyde composites. J. Appl. Polym. Sci. 109, 256–263. doi: 10.1002/app.27452
Kabir, M. M., Wang, H., Lau, K. T., and Cardona, F. (2012). Chemical treatments on plant-based natural fibre reinforced polymer composites: an overview. Compos. Part B Eng. 43, 2883–2892. doi: 10.1016/j.compositesb.2012.04.053
Kaith, B. S., and Kalia, S. (2007). Grafting of flax fiber ( Linum usitatissimum ) with vinyl monomers for enhancement of properties of flax-phenolic composites. Polym. J. 39, 1319–1327. doi: 10.1295/polymj.PJ2007073
Kengkhetkit, N., and Amornsakchai, T. (2012). Utilisation of pineapple leaf waste for plastic reinforcement: 1. A novel extraction method for short pineapple leaf fiber. Ind. Crops Prod. 40, 55–61. doi: 10.1016/j.indcrop.2012.02.037
Khan, J. A., and Khan, M. A. (2014). “The use of jute fibers as reinforcements in composites”, in Biofiber Reinforcements in Composite Materials , eds O. Faruk and M. Sain (Woodhead Publishing), 3–34. doi: 10.1533/9781782421276.1.3
Khan, M. A., Hassan, M. M., and Drzal, L. T. (2005). Effect of 2-hydroxyethyl methacrylate (HEMA) on the mechanical and thermal properties of jute-polycarbonate composite. Compos. Part A Appl. Sci. Manufact. 36, 71–81. doi: 10.1016/S1359-835X(04)00178-2
Khan, M. A., Hassan, M. M., Taslima, R., and Mustafa, A. I. (2006). Role of pretreatment with potassium permanganate and urea on mechanical and degradable properties of photocured coir (cocos nucifera) fiber with 1,6-hexanediol diacrylate. J. Appl. Polym. Sci. 100, 4361–4368. doi: 10.1002/app.23863
Khondker, O. A., Ishiaku, U. S., Nakai, A., and Hamada, H. (2005). Fabrication and mechanical properties of unidirectional jute/PP composites using jute yarns by film stacking method. J. Polym. Environ. 13, 115–126. doi: 10.1007/s10924-005-2943-y
Kicinska-Jakubowska, A., Bogacz, E., and Zimniewska, M. (2012). Review of natural fibers. Part I—vegetable fibers. J. Nat. Fibers 9, 150–167. doi: 10.1080/15440478.2012.703370
Kinloch, A. J., Taylor, A. C., Techapaitoon, M., Teo, W. S., and Sprenger, S. (2015). Tough, natural-fibre composites based upon epoxy matrices. J. Mater. Sci. 50, 6947–6960. doi: 10.1007/s10853-015-9246-z
Kipriotis, E., Heping, X., Vafeiadakis, T., Kiprioti, M., and Alexopoulou, E. (2015). Ramie and kenaf as feed crops. Ind. Crops Prod. 68, 126–130. doi: 10.1016/j.indcrop.2014.10.002
Komuraiah, A., Kumar, N. S., and Prasad, B. D. (2014). Chemical composition of natural fibers and its influence on their mechanical properties. Mech. Compos. Mat . 50, 359–376. doi: 10.1007/s11029-014-9422-2
Ku, H., Wang, H., Pattarachaiyakoop, N., and Trada, M. (2011). A review on the tensile properties of natural fiber reinforced polymer composites. Compos. Part B Eng. 42, 856–873. doi: 10.1016/j.compositesb.2011.01.010
Laftah, W. A., and Abdul Rahaman, W. A. W. (2015). Chemical pulping of waste pineapple leaves fiber for kraft paper production. J. Mater. Res. Technol. 4, 254–261. doi: 10.1016/j.jmrt.2014.12.006
Lanzilao, G., Goswami, P., and Blackburn, R. S. (2016). Study of the morphological characteristics and physical properties of Himalayan giant nettle ( Girardinia diversifolia L.) fibre in comparison with European nettle ( Urtica dioica L.) fibre. Mater. Lett. 181, 200–203. doi: 10.1016/j.matlet.2016.06.044
Lau, K., Hung, P., Zhu, M. H., and Hui, D. (2018). Properties of natural fibre composites for structural engineering applications. Compos. Part B Eng. 136, 222–233. doi: 10.1016/j.compositesb.2017.10.038
Li, X., Tabil, L. G., and Panigrahi, S. (2007). Chemical treatments of natural fiber for use in natural fiber-reinforced composites: a review. J. Polym. Environ. 15, 25–33. doi: 10.1007/s10924-006-0042-3
Li, Y., Mai, Y., and Ye, L. (2000). Sisal ® bre and its composites : a review of recent developments IM PA US AS DO ME US EX ON AS. Compos. Sci. Technol. 60, 2037–2055. doi: 10.1016/S0266-3538(00)00101-9
Li, Z., Wang, X., and Wang, L. (2006). Properties of hemp fibre reinforced concrete composites. Compos. Part A Appl. Sci. Manuf. 37, 497–505. doi: 10.1016/j.compositesa.2005.01.032
Liu, R., Lv, W., Wang, X., Zhai, M., Dong, P., and Wang, Z. (2018). Carbonization and combustion characteristics of palm fiber. Fuel 227, 21–26. doi: 10.1016/j.fuel.2018.02.088
Liu, W., Mohanty, A. K., Drzal, L. T., Askeland, P., and Misra, M. (2004). Effects of alkali treatment on the structure, morphology and thermal properties of native grass fibers as reinforcements for polymer matrix composites. J. Mater. Sci. 39:1051. doi: 10.1023/B:JMSC.0000012942.83614.75
Liu, W., Mohanty, A. K., Drzal, L. T., and Misra, M. (2005). Novel biocomposites from native grass and soy based bioplastic: processing and properties evaluation. Ind. Eng. Chem. Res. 44, 7105–7112. doi: 10.1021/ie050257b
Madhu, P., Sanjay, M. R., Pradeep, S., Subrahmanya Bhat, K., Yogesha, B., and Siengchin, S. (2019a). Characterization of cellulosic fibre from Phoenix pusilla leaves as potential reinforcement for polymeric composites. J. Mater. Res. Technol. 8, 2597–2604. doi: 10.1016/j.jmrt.2019.03.006
Madhu, P., Sanjay, M. R., Senthamaraikannan, P., Pradeep, S., Saravanakumar, S. S., and Yogesha, B. (2019b). A review on synthesis and characterization of commercially available natural fibers: Part II. J. Nat. Fibers 16, 25–36. doi: 10.1080/15440478.2017.1379045
Madhu, P., Sanjay, M. R., Senthamaraikannan, P., Pradeep, S., Siengchin, S., Jawaid, M., et al. (2018). Effect of various chemical treatments of prosopis juliflora fibers as composite reinforcement: physicochemical, thermal, mechanical, and morphological properties. J. Nat. Fibers 00, 1–12. doi: 10.1080/15440478.2018.1534191
Mahjoub, R., Yatim, J. M., Mohd Sam, A. R., and Hashemi, S. H. (2014). Tensile properties of kenaf fiber due to various conditions of chemical fiber surface modifications. Constr. Build. Mater. 55, 103–113. doi: 10.1016/j.conbuildmat.2014.01.036
Manikandan Nair, K. C., Thomas, S., and Groeninckx, G. (2001). Thermal and dynamic mechanical analysis of polystyrene composites reinforced with short sisal fibres. Compos. Sci. Technol. 61, 2519–2529. doi: 10.1016/S0266-3538(01)00170-1
Manimaran, P., Senthamaraikannan, P., Murugananthan, K., and Sanjay, M. R. (2018). Physicochemical properties of new cellulosic fibers from Azadirachta indica Plant. J. Nat. Fibers 15, 29–38. doi: 10.1080/15440478.2017.1302388
Manimaran, P., Senthamaraikannan, P., Sanjay, M. R., Marichelvam, M. K., and Jawaid, M. (2017). Study on characterization of furcraea foetida new natural fiber as composite reinforcement for lightweight applications. Carbohydr. Polym. 181, 650–658. doi: 10.1016/j.carbpol.2017.11.099
Marsyahyo, E., Jamasri, H. S. B., and Soekrisno (2009). Preliminary investigation on bulletproof panels made from ramie fiber reinforced composites for NIJ Level II, IIA, and IV. J. Ind. Text. 39, 13–26. doi: 10.1177/1528083708098913
Martin, N., Mouret, N., Davies, P., and Baley, C. (2013). Influence of the degree of retting of flax fibers on the tensile properties of single fibers and short fiber/polypropylene composites. Ind. Crops Prod. 49, 755–767. doi: 10.1016/j.indcrop.2013.06.012
Masri, T., Ounis, H., Sedira, L., Kaci, A., and Benchabane, A. (2018). Characterization of new composite material based on date palm leaflets and expanded polystyrene wastes. Constr. Build. Mater. 164, 410–418. doi: 10.1016/j.conbuildmat.2017.12.197
McGregor, B. A. (2018). “Physical, chemical, and tensile properties of cashmere, mohair, alpaca, and other rare animal fibers” in Handbook of Properties of Textile and Technical Fibres , ed A. R. Bunsell (Woodhead Publishing), 105–136. doi: 10.1016/B978-0-08-101272-7.00004-3
Mihai, M. (2013). Novel polylactide/triticale straw biocomposites : processing, formulation, and properties. Polym. Eng. Sci. 54. doi: 10.1002/pen.23575
Mishra, S., Mohanty, A. K., Drzal, L. T., Misra, M., Parija, S., Nayak, S. K., et al. (2003). Studies on mechanical performance of biofibre/glass reinforced polyester hybrid composites. Compos. Sci. Technol. 63, 1377-1385. doi: 10.1016/S0266-3538(03)00084-8
Mochane, M. J., Mokhena, T. C., Mokhothu, T. H., Mtibe, A., Sadiku, E. R., Ray, S. S., et al. (2019). Recent progress on natural fiber hybrid composites for advanced applications: a review. Express Polym. Lett. 13, 159–198. doi: 10.3144/expresspolymlett.2019.15
Mohammed, L., Ansari, M. N. M., Pua, G., Jawaid, M., and Islam, M. S. (2015). A review on natural fiber reinforced polymer composite and its applications. Int. J. Polym. Sci. 2015, 1–15. doi: 10.1155/2015/243947
Monteiro, S. N., Satyanarayana, K. G., Ferreira, A. S., Nascimento, D. C. O., Lopes, F. P. D., Silva, I. L. A., et al. (2010). Selection of high strength natural fibers. Rev. Mater. 15, 488–505. doi: 10.1590/S1517-70762010000400002
Mortazavi, S. M., and Moghaddam, M. K. (2010). An analysis of structure and properties of a natural cellulosic fiber (Leafiran). Fibers Polym. 11, 877–882. doi: 10.1007/s12221-010-0877-z
Murugesh Babu, K. (2016). “Silk from silkworms and spiders as high- performance fibers,” in Structure and Properties of High-Performance Fibers , ed G. Bhat (Woodhead Publishing), 27–366. doi: 10.1016/B978-0-08-100550-7.00013-9
Mwaikambo, L. Y., and Ansell, M. P. (2002). Chemical modification of hemp, sisal, jute, and kapok fibers by alkalization. J. Appl. Polym. Sci. 84, 2222–2234. doi: 10.1002/app.10460
Mwaikambo, L. Y., Martuscelli, E., and Avella, M. (2000). Kapok/cotton fabric-polypropylene composites. Polym. Test. 19, 905–918. doi: 10.1016/S0142-9418(99)00061-6
Nair, K. P. P. (ed.). (2010). “The coconut palm (Cocos nucifera L.),” in The Agronomy and Economy of Important Tree Crops of the Developing World (Elsevier Ltd.), 67–109. doi: 10.1016/B978-0-12-384677-8.00003-5
Nam, S., and Netravali, A. N. (2006). Green composites. I. Physical properties of ramie fibers for environment-friendly green composites. Fibers Polym. 7, 372–379. doi: 10.1007/BF02875769
Nasser, R. A., Salem, M. Z. M., Hiziroglu, S., Al-Mefarrej, H. A., Mohareb, A. S., Alam, M., et al. (2016). Chemical analysis of different parts of date palm ( Phoenix dactylifera L.) using ultimate, proximate and thermo-gravimetric techniques for energy production. Energies 9:374. doi: 10.3390/en9050374
Naveen, J., Jawaid, M., Amuthakkannan, P., and Chandrasekar, M. (2018). “Mechanical and physical properties of sisal and hybrid sisal fiber-reinforced polymer composites,” in Mechanical and Physical Testing of Biocomposites, Fibre-Reinforced Composites and Hybrid Composites , eds M. Jawaid, M. Thariq, and N. Saba (Woodhead Publishing), 427–440. doi: 10.1016/B978-0-08-102292-4.00021-7
Nirmal, U., Hashim, J., and Megat Ahmad, M. M. H. (2015). A review on tribological performance of natural fibre polymeric composites. Tribol. Int. 83, 77–104. doi: 10.1016/j.triboint.2014.11.003
Nishino, T., Hirao, K., Kotera, M., Nakamae, K., and Inagaki, H. (2003). Kenaf reinforced biodegradable composite. Compos. Sci. Technol. 63, 1281–1286. doi: 10.1016/S0266-3538(03)00099-X
Oksman, K. (2001). High quality flax fibre composites manufactured by the resin transfer moulding process. J. Reinf. Plast. Compos. 20, 621–627. doi: 10.1177/073168401772678634
Oksman, K., Aitomäki, Y., Mathew, A. P., Siqueira, G., Zhou, Q., Butylina, S., et al. (2016). Review of the recent developments in cellulose nanocomposite processing. Compos. Part A Appl. Sci. Manuf. 83, 2–18. doi: 10.1016/j.compositesa.2015.10.041
Omar, M. F., Jaya, H., and Zulkepli, N. N. (2019). “Kenaf fiber reinforced composite in the automotive industry,” in Module in Materials Science and Materials Engineering (Elsevier Ltd.). doi: 10.1016/B978-0-12-803581-8.11429-8
Osorio, L., Trujillo, E., Van Vuure, A. W., and Verpoest, I. (2011). Morphological aspects and mechanical properties of single bamboo fibers and flexural characterization of bamboo/ epoxy composites. J. Reinf. Plast. Compos. 30, 396–408. doi: 10.1177/0731684410397683
Panaitescu, D. M., Nicolae, C. A., Vuluga, Z., Vitelaru, C., Sanporean, C. G., Zaharia, C., et al. (2016). Influence of hemp fibers with modified surface on polypropylene composites. J. Ind. Eng. Chem. 37, 137–146. doi: 10.1016/j.jiec.2016.03.018
Pandey, J. K., Ahn, S. H., Lee, C. S., Mohanty, A. K., and Misra, M. (2010). Recent advances in the application of natural fiber based composites. Macro Mater. Eng. 295, 975–989. doi: 10.1002/mame.201000095
Paridah, M. T., Arib, R. M. N., Sapuan, S. M., Zaman, H. M. D. K., and Ahmad, M. M. H. M. (2004). Mechanical properties of pineapple leaf fibre reinforced polypropylene composites. Mater. Des. 27, 391–396. doi: 10.1016/j.matdes.2004.11.009
Paul, A., Joseph, K., and Thomas, S. (1997). Effect of surface treatments on the electrical properties of low-density polyethylene composites reinforced with short sisal fibers. Compos. Sci. Technol. 57, 67–79. doi: 10.1016/S0266-3538(96)00109-1
Pham, L. J. (2016). Coconut (Cocos nucifera). AOCS Press. doi: 10.1016/B978-1-893997-98-1.00009-9
Pickering, K. L., Efendy, M. G. A., and Le, T. M. (2016). A review of recent developments in natural fibre composites and their mechanical performance. Compos. Part A Appl. Sci. Manuf. 83, 98–112. doi: 10.1016/j.compositesa.2015.08.038
Prachayawarakorn, J., Chaiwatyothin, S., Mueangta, S., and Hanchana, A. (2013). Effect of jute and kapok fibers on properties of thermoplastic cassava starch composites. Mater. Des. 47, 309–315. doi: 10.1016/j.matdes.2012.12.012
Preet Singh, J. I., Dhawan, V., Singh, S., and Jangid, K. (2017). Study of effect of surface treatment on mechanical properties of natural fiber reinforced composites. Mater. Today Proc. 4, 2793–2799. doi: 10.1016/j.matpr.2017.02.158
Puttegowda, M., Rangappa, S. M., Jawaid, M., Shivanna, P., Basavegowda, Y., and Saba, N. (2018). “Potential of natural/synthetic hybrid composites for aerospace,in applications,” in Sustainable Composites for Aerospace Applications , eds M. Jawaid and M. Thariq (Woodhead Publishing), 315–351. doi: 10.1016/B978-0-08-102131-6.00021-9
Rahman, M. S. (2010). “Jute-a versatile natural fibre. Cultivation, extraction and processing,” in Industrial Applications of Natural Fibres Industrial Applications of Natural Fibres: Structure, Properties and Technical Applications , ed J. Müssig (Wiley), 135–161. doi: 10.1002/9780470660324.ch6
Raman Bharath, V. R., Vijaya Ramnath, B., and Manoharan, N. (2015). Kenaf fibre reinforced composites: a review. ARPN J. Eng. Appl. Sci. 10, 5483–5485.
Ramesh, M. (2019). Flax ( Linum usitatissimum L.) fibre reinforced polymer composite materials: a review on preparation, properties and prospects. Prog. Mater. Sci. 102, 109–166. doi: 10.1016/j.pmatsci.2018.12.004
Ramesh, M., Palanikumar, K., and Reddy, K. H. (2013). Mechanical property evaluation of sisal-jute-glass fiber reinforced polyester composites. Compos. Part B Eng. 48, 1-9. doi: 10.1016/j.compositesb.2012.12.004
Rangappa, S. M., and Siengchin, S. (2018). Natural fibers as perspective materials. KMUTNB Int. J. Appl. Sci. Technol. 11:2018. doi: 10.14416/j.ijast.2018.09.001
Reddy, K. O., Maheswari, C. U., Shukla, M., and Rajulu, A. V. (2012). Chemical composition and structural characterization of Napier grass fibers. Mater. Lett. 67, 35–38. doi: 10.1016/j.matlet.2011.09.027
Reddy, N., and Yang, Y. (2015) “Bacterial cellulose fibers,” in Innovative Biofibers from Renewable Resources (Berlin; Heidelberg: Springer), 307–329. doi: 10.1007/978-3-662-45136-6_61
Rehman, M., Gang, D., Liu, Q., Chen, Y., Wang, B., Peng, D., et al. (2019). Ramie, a multipurpose crop: potential applications, constraints and improvement strategies. Ind. Crops Prod. 137, 300–307. doi: 10.1016/j.indcrop.2019.05.029
Réquilé, S., Le Duigou, A., Bourmaud, A., and Baley, C. (2018). Peeling experiments for hemp retting characterization targeting biocomposites. Ind. Crops Prod. 123, 573–580. doi: 10.1016/j.indcrop.2018.07.012
Rivera, D., Obón, C., Alcaraz, F., Laguna, E., and Johnson, D. (2019). Date-palm (Phoenix, Arecaceae) iconography in coins from the Mediterranean and West Asia (485 BC−1189 AD). J. Cult. Herit. 37, 199–214. doi: 10.1016/j.culher.2018.10.010
Rokbi, M., Osmani, H., Imad, A., and Benseddiq, N. (2011). Effect of chemical treatment on flexure properties of natural fiber-reinforced polyester composite. Proc. Eng. 10, 2092–2097. doi: 10.1016/j.proeng.2011.04.346
Rong, M. Z., Zhang, M. Q., Liu, Y., Yang, G. C., and Zeng, H. M. (2001). The effect of fiber treatment on the mechanical properties of unidirectional sisal-reinforced epoxy composites. Compos. Sci. Technol. 61, 1437–1447. doi: 10.1016/S0266-3538(01)00046-X
Ruan, P., Du, J., Gariepy, Y., and Raghavan, V. (2015). Characterization of radio frequency assisted water retting and flax fibers obtained. Ind. Crops Prod. 69, 228–237. doi: 10.1016/j.indcrop.2015.02.009
Saba, N., Paridah, M. T., and Jawaid, M. (2015). Mechanical properties of kenaf fibre reinforced polymer composite: a review. Constr. Build. Mater. 76, 87–96. doi: 10.1016/j.conbuildmat.2014.11.043
Saba, N., Tahir, P. M., and Jawaid, M. (2014). A review on potentiality of nano filler/natural fiber filled polymer hybrid composites. Polymers (Basel). 6, 2247–2273. doi: 10.3390/polym6082247
Sam-Brew, S., and Smith, G. D. (2015). Flax and Hemp fiber-reinforced particleboard. Ind. Crops Prod. 77, 940–948. doi: 10.1016/j.indcrop.2015.09.079
Sanjay, M. R., Arpitha, G. R., Naik, L. L., Gopalakrishna, K., and Yogesha, B. (2016). Applications of natural fibers and its composites: an overview. Nat. Resour. 7, 108–114. doi: 10.4236/nr.2016.73011
Sanjay, M. R., Arpitha, G. R., Senthamaraikannan, P., Kathiresan, M., Saibalaji, M. A., and Yogesha, B. (2019a). The hybrid effect of jute/kenaf/e-glass woven fabric epoxy composites for medium load applications: impact, inter-laminar strength, and failure surface characterization. J. Nat. Fibers 16, 600–612. doi: 10.1080/15440478.2018.1431828
Sanjay, M. R., Arpitha, G. R., and Yogesha, B. (2015). Study on mechanical properties of natural - glass fibre reinforced polymer hybrid composites : a review. Mater. Today Proc. 2, 2959–2967. doi: 10.1016/j.matpr.2015.07.264
Sanjay, M. R., Madhu, P., Jawaid, M., Senthamaraikannan, P., Senthil, S., and Pradeep, S. (2018). Characterization and properties of natural fiber polymer composites: a comprehensive review. J. Clean. Prod. 172, 566-581. doi: 10.1016/j.jclepro.2017.10.101
Sanjay, M. R., Siengchin, S., Parameswaranpillai, J., Jawaid, M., Pruncu, C. I., and Khan, A. (2019b). A comprehensive review of techniques for natural fibers as reinforcement in composites: preparation, processing and characterization. Carbohydr. Polym. 207, 108–121. doi: 10.1016/j.carbpol.2018.11.083
Sanjay, M. R., and Suchart, S. (2019). Lightweight natural fiber composites. J. Appl. Agric. Sci. Technol. 3:178. doi: 10.32530/jaast.v3i2.108
Santhosh Kumar, S., and Hiremath, S. S. (2019). “Natural fiber reinforced composites in the context of biodegradability: a review,” in Reference Module in Materials Science and Materials Engineering (Elsevier Ltd.). doi: 10.1016/B978-0-12-803581-8.11418-3
Saravanakumaar, A., Senthilkumar, A., Saravanakumar, S. S., and Sanjay, M. R. (2018). Impact of alkali treatment on physico-chemical, thermal, structural and tensile properties of Carica papaya bark fibers. Int. J. Polym. Anal. Charact. 23, 529–536. doi: 10.1080/1023666X.2018.1501931
Saravanakumar, S. S., Kumaravel, A., Nagarajan, T., and Moorthy, I. G. (2014). Effect of chemical treatments on physicochemical properties of Prosopis juliflora fibers. Int. J. Polym. Anal. Charact. 19, 383–390. doi: 10.1080/1023666X.2014.903585
Sawpan, M. A., Pickering, K. L., and Fernyhough, A. (2011). Improvement of mechanical performance of industrial hemp fibre reinforced polylactide biocomposites. Compos. Part A Appl. Sci. Manuf. 42, 310–319. doi: 10.1016/j.compositesa.2010.12.004
Sen, T., and Jagannatha Reddy, H. N. (2011a). Application of sisal, bamboo, coir and jute natural composites in structural upgradation. Int. J. Innov. Manag. Technol. 2:186.
Sen, T., and Jagannatha Reddy, H. N. (2011b). Various industrial applications of hemp, kinaf, flax and ramie natural fibres. Int. J. Innov. Manag. Technol. 2.
Sengupta, S., and Basu, G. (2016). Properties of coconut fiber. Ref. Modul. Mater. Sci. Mater. Eng. doi: 10.1016/B978-0-12-803581-8.04122-9
Senthamaraikannan, P., and Kathiresan, M. (2018). Characterization of raw and alkali treated new natural cellulosic fiber from Coccinia grandis .L. Carbohydr. Polym. 186, 332–343. doi: 10.1016/j.carbpol.2018.01.072
Senthamaraikannan, P., Saravanakumar, S. S., Arthanarieswaran, V. P., and Sugumaran, P. (2016). Physico-chemical properties of new cellulosic fibers from the bark of Acacia planifrons. Int. J. Polym. Anal. Charact. 21, 207–213. doi: 10.1080/1023666X.2016.1133138
Senthilkumar, K., Saba, N., Rajini, N., Chandrasekar, M., Jawaid, M., Siengchin, S., et al. (2018). Mechanical properties evaluation of sisal fibre reinforced polymer composites: a review. Constr. Build. Mater. 174, 713–729. doi: 10.1016/j.conbuildmat.2018.04.143
Senthilkumar, K., Saba, N. R. N., Jawaid, M. C. M., and Siengchin, S. (2019). Effect of alkali treatment on mechanical and morphological properties of pineapple leaf fibre/polyester composites. J. Polym. Environ. 27, 1191–1201. doi: 10.1007/s10924-019-01418-x
Sepe, R., Bollino, F., Boccarusso, L., and Caputo, F. (2018). Influence of chemical treatments on mechanical properties of hemp fiber reinforced composites. Compos. Part B Eng. 133, 210–217. doi: 10.1016/j.compositesb.2017.09.030
Sgriccia, N., Hawley, M. C., and Misra, M. (2008). Characterization of natural fiber surfaces and natural fiber composites. Compos. Part A Appl. Sci. Manuf. 39, 1632–1637. doi: 10.1016/j.compositesa.2008.07.007
Shahinur, S., and Hasan, M. (2019a). “Jute/coir/banana fiber reinforced biocomposites: critical review of design, fabrication, properties and applications,” in Reference Module in Materials Science and Materials Engineering (Elsevier Ltd.). doi: 10.1016/B978-0-12-803581-8.10987-7
Shahinur, S., and Hasan, M. (2019b). Natural fiber and synthetic fiber composites: comparison of properties, performance, cost and environmental benefits,” in Reference Module in Materials Science and Materials Engineering (Elsevier Ltd.). doi: 10.1016/B978-0-12-803581-8.10994-4
Sharma, P., Pandey, A. K., and Srivastava, A. (2017). “Tensile and impact strength analysis of cotton fiber reinforced polymer composites,” in Arimpie. Available online at: https://www.elkjournals.com/microadmin/UploadFolder/3781paper%2042.pdf .
Shera, S. S., Kulhar, N., and Banik, R. M. (2019). “Silk and silk fibroin-based biopolymeric composites and their biomedical applications,” in Materials for Biomedical Engineering , eds V. Grumezescu and A. Mihai Grumezescu (Elsvier), 339–374. doi: 10.1016/B978-0-12-816872-1.00012-1
Shinoj, S., Visvanathan, R., Panigrahi, S., and Kochubabu, M. (2011). Oil palm fiber (OPF) and its composites: a review. Ind. Crops Prod. 33, 7–22. doi: 10.1016/j.indcrop.2010.09.009
Shuit, S. H., Tan, K. T., Lee, K. T., and Kamaruddin, A. H. (2009). Oil palm biomass as a sustainable energy source: a Malaysian case study. Energy 34, 1225–1235. doi: 10.1016/j.energy.2009.05.008
Singh, B., Gupta, M., and Verma, A. (1996). Influence of fiber surface treatment on the properties of sisal-polyester composites. Poly. Compos. 17, 910–918. doi: 10.1002/pc.10684
Sood, M., and Dwivedi, G. (2018). Effect of fiber treatment on flexural properties of natural fiber reinforced composites: a review. Egypt. J. Pet. 27, 775–783. doi: 10.1016/j.ejpe.2017.11.005
Sreekala, M. S., Kumaran, M. G., Joseph, S., Jacob, M., and Thomas, S. (2000). Oil palm fibre reinforced phenol formaldehyde composites: influence of fibre surface modifications on the mechanical performance. Appl. Compos. Mater. 7, 295–329. doi: 10.1023/A:1026534006291
Sreekala, M. S., Kumaran, M. G., and Thomas, S. (2002). Water sorption in oil palm fiber reinforced phenol formaldehyde composites. Compos. Part A Appl. Sci. Manuf. 33, 763–777. doi: 10.1016/S1359-835X(02)00032-5
Sreekala, M. S., and Thomas, S. (2003). Effect of fibre surface modification on water-sorption characteristics of oil palm fibres. Compos. Sci. Technol. 63, 861–869. doi: 10.1016/S0266-3538(02)00270-1
Sreenivasan, V. S., Ravindran, D., Manikandan, V., and Narayanasamy, R. (2012). Influence of fibre treatments on mechanical properties of short Sansevieria cylindrica/polyester composites. Mater. Des. 37, 111–121. doi: 10.1016/j.matdes.2012.01.004
Steffens, F., Steffens, H., and Oliveira, F. R. (2017). Applications of natural fibers on architecture. Proc. Eng. 200, 317–324. doi: 10.1016/j.proeng.2017.07.045
Suharty, N. S., Ismail, H., Diharjo, K., Handayani, D. S., and Firdaus, M. (2016). Effect of kenaf fiber as a reinforcement on the tensile, flexural strength and impact toughness properties of recycled polypropylene/halloysite composites. Proc. Chem. 19, 253–258. doi: 10.1016/j.proche.2016.03.102
Thakur, V. K., and Thakur, M. K. (2014). Processing and characterization of natural cellulose fibers/thermoset polymer composites. Carbohydr. Polym. 109, 102–117. doi: 10.1016/j.carbpol.2014.03.039
Thakur, V. K., Thakur, M. K., and Gupta, R. K. (2014). Review: raw natural fiber-based polymer composites. Int. J. Polym. Anal. Charact. 19, 256–271. doi: 10.1080/1023666X.2014.880016
Thiagamani, S. M. K., Krishnasamy, S., and Siengchin, S. (2019). Challenges of biodegradable polymers: an environmental perspective. Appl. Sci. Eng. Prog. 12, 2019. doi: 10.14416/j.asep.2019.03.002
Threepopnatkul, P., Kaerkitcha, N., and Athipongarporn, N. (2009). Composites: Part B Effect of surface treatment on performance of pineapple leaf fiber – polycarbonate composites. Compos. Part B 40, 628–632. doi: 10.1016/j.compositesb.2009.04.008
Ticoalu, A., Aravinthan, T., and Cardona, F. (2010). “A review of current development in natural fiber composites for structural and infrastructure applications,” in Southern Region Engineering Conference 11–12 November 2010, Toowoomba, Australia , 1–5.
Todkar, S. S., and Patil, S. A. (2019). Review on mechanical properties evaluation of pineapple leaf fibre (PALF) reinforced polymer composites. Compos. Part B Eng. 2019:106927. doi: 10.1016/j.compositesb.2019.106927
Tye, Y. Y., Lee, K. T., Wan Abdullah, W. N., and Leh, C. P. (2012). Potential of Ceiba pentandra (L.) Gaertn. (kapok fiber) as a resource for second generation bioethanol: effect of various simple pretreatment methods on sugar production. Bioresour. Technol . 116, 536–539. doi: 10.1016/j.biortech.2012.04.025
Väisänen, T., Batello, P., Lappalainen, R., and Tomppo, L. (2018). Modification of hemp fibers ( Cannabis sativa L.) for composite applications. Ind. Crops Prod. 111, 422–429. doi: 10.1016/j.indcrop.2017.10.049
Van Dam, J. E. G., Elbersen, H. W., and Daza Montaño, C. M. (2018). “Bamboo production for industrial utilization,” in Perennial Grassesfor Bioenergy and Bioproducts , ed E. Alexopoulou (Academic Press; Elsvier), 175–216. doi: 10.1016/B978-0-12-812900-5.00006-0
Van de Weyenberg, I., Ivens, J., De Coster, A., Kino, B., Baetens, E., and Verpoest, I. (2003). Influence of processing and chemical treatment of flax fibres on their composites. Compos. Sci. Technol. 63, 1241–1246. doi: 10.1016/S0266-3538(03)00093-9
Varghese, A. M., and Mittal, V. (2017). “Surface modification of natural fibers,” in Biodegradable and Biocompatible Polymer Composites , ed N. Gopal Shimpi (Woodhead Publishing), 115–155. doi: 10.1016/B978-0-08-100970-3.00005-5
Verma, D., and Gope, P. C. (2014). “The use of coir/coconut fibers as reinforcements in composites,” in Biofiber Reinforcements in Composite Materials , eds O. Faruk and M. Sain (Elsevier Ltd.), 285–319. doi: 10.1533/9781782421276.3.285
Wales, N., and Blackman, B. K. (2017). Plant domestication: wild date palms illuminate a crop's sticky origins. Curr. Biol. 27, R702–R704. doi: 10.1016/j.cub.2017.05.070
Wambua, P., Ivens, J., and Verpoest, I. (2003). Natural fibres: can they replace glass in fibre reinforced plastics? Compos. Sci. Technol. 63, 1259–1264. doi: 10.1016/S0266-3538(03)00096-4
Wang, G., and Chen, F. (2016). “Development of bamboo fiber-based composites,” in Advanced High Strength Natural Fibre Composites in Construction , ed M. Fan and F. Fu (Elsevier Ltd.), 235–255. doi: 10.1016/B978-0-08-100411-1.00010-8
Wang, H., Memon, H., Hassan, E. A. M., Miah, S., and Ali, A. (2019). Effect of jute fiber modification on mechanical properties of jute fiber composite. Materials (Basel) 12:E1226. doi: 10.3390/ma12081226
Xie, Y., Hill, C. A. S., Xiao, Z., Militz, H., and Mai, C. (2010). Silane coupling agents used for natural fiber/polymer composites: a review. Compos. Part A Appl. Sci. Manuf. 41, 806–819. doi: 10.1016/j.compositesa.2010.03.005
Xin, X., Xu, C. G., and Qing, L. F. (2007). Friction properties of sisal fibre reinforced resin brake composites. Wear 262, 736–741. doi: 10.1016/j.wear.2006.08.010
Xu, Y., Salmi, J., Kloser, E., Perrin, F., Grosse, S., Denault, J., et al. (2013). Feasibility of nanocrystalline cellulose production by endoglucanase treatment of natural bast fibers. Ind. Crops Prod. 51, 381–384. doi: 10.1016/j.indcrop.2013.09.029
Yang, G., Park, M., and Park, S.-J. (2019). Recent progresses of fabrication and characterization of fibers-reinforced composites: a review. Compos. Commun. 14, 34–42. doi: 10.1016/j.coco.2019.05.004
Yashas Gowda, T. G., Sanjay, M. R., Subrahmanya Bhat, K., Madhu, P., Senthamaraikannan, P., and Yogesha, B. (2018). Polymer matrix-natural fiber composites: an overview. Cogent Eng. 5, 1–13. doi: 10.1080/23311916.2018.1446667
Yogesha, B. (2017). ScienceDirect studies on natural / glass fiber reinforced polymer hybrid composites : an evolution. Mater. Today Proc. 4, 2739–2747. doi: 10.1016/j.matpr.2017.02.151
Yu, H., Wang, X., and Petru, M. (2019). The effect of surface treatment on the creep behavior of flax fiber reinforced composites under hygrothermal aging conditions. Constr. Build. Mater 208, 220–227. doi: 10.1016/j.conbuildmat.2019.03.001
Yuan, Q., Yao, J., Chen, X., Huang, L., and Shao, Z. (2010). The preparation of high performance silk fiber/fibroin composite. Polymer (Guildf). 51, 4843–4849. doi: 10.1016/j.polymer.2010.08.042
Zafeiropoulos, N. E., and Baillie, C. A. (2007). A study of the effect of surface treatments on the tensile strength of flax fibres: Part II. Application of Weibull statistics. Compos. Part A Appl. Sci. Manuf. 38, 629–638. doi: 10.1016/j.compositesa.2006.02.005
Zakikhani, P., Zahari, R., Sultan, M. T. H., and Majid, D. L. (2014). Extraction and preparation of bamboo fibre-reinforced composites. Mater. Des. 63, 820–828. doi: 10.1016/j.matdes.2014.06.058
Zaman, H. U., Khan, M. A., Khan, R. A., Rahman, M. A., Das, L. R., and Al-Mamun, M. (2010). Role of potassium permanganate and urea on the improvement of the mechanical properties of jute polypropylene composites. Fibers Polym. 11, 455–463. doi: 10.1007/s12221-010-0455-4
Zamri, M. H., Akil, H. M., and MohdIshak, Z. A. (2016). Pultruded kenaf fibre reinforced composites: effect of different kenaf fibre yarn tex. Proc. Chem. 19, 577–585. doi: 10.1016/j.proche.2016.03.056
Zegaoui, A., Ma, R., Dayo, A. Q., Derradji, M., Wang, J., Liu, W., et al. (2018). Morphological, mechanical and thermal properties of cyanate ester/benzoxazine resin composites reinforced by silane treated natural hemp fibers. Chinese J. Chem. Eng. 26, 1219–1228. doi: 10.1016/j.cjche.2018.01.008
Zhang, M. Q., Rong, M. Z., and Lu, X. (2005). Fully biodegradable natural fiber composites from renewable resources: all-plant fiber composites. Compos. Sci. Technol. 65, 2514–2525. doi: 10.1016/j.compscitech.2005.06.018
Zheng, Y., Wang, J., Zhu, Y., and Wang, A. (2015). Research and application of kapok fiber as an absorbing material: a mini review. J. Environ. Sci. (China) 27, 21–32. doi: 10.1016/j.jes.2014.09.026
Zhu, J., Zhu, H., Njuguna, J., and Abhyankar, H. (2013). Recent development of flax fibres and their reinforced composites based on different polymeric matrices. Materials 6, 5171–5198. doi: 10.3390/ma6115171
Zou, Y., Reddy, N., and Yang, Y. (2011). Reusing polyester/cotton blend fabrics for composites. Compos. Part B Eng. 42, 763–770. doi: 10.1016/j.compositesb.2011.01.022
Keywords: natural fiber, sustainable and renewable resource, eco-friendly composites, applications of natural fibers, reinforcement for composites materials, treatments on natural fibers
Citation: Thyavihalli Girijappa YG, Mavinkere Rangappa S, Parameswaranpillai J and Siengchin S (2019) Natural Fibers as Sustainable and Renewable Resource for Development of Eco-Friendly Composites: A Comprehensive Review. Front. Mater. 6:226. doi: 10.3389/fmats.2019.00226
Received: 26 June 2019; Accepted: 03 September 2019; Published: 27 September 2019.
Reviewed by:
Copyright © 2019 Thyavihalli Girijappa, Mavinkere Rangappa, Parameswaranpillai and Siengchin. This is an open-access article distributed under the terms of the Creative Commons Attribution License (CC BY) . The use, distribution or reproduction in other forums is permitted, provided the original author(s) and the copyright owner(s) are credited and that the original publication in this journal is cited, in accordance with accepted academic practice. No use, distribution or reproduction is permitted which does not comply with these terms.
*Correspondence: Suchart Siengchin, suchart.s.pe@tggs-bangkok.org
This article is part of the Research Topic
Biodegradable Matrices and Composites
- Garden Planning
- Garden Tools
- Gardening Techniques
- Ornamentals
- Pest Control
- Raising Cattle
- Raising Pigs
- Raising Rabbits
- Raising Sheep And Goats
- Raising Chickens
- Raising Ducks And Geese
- Raising Turkeys
- Power Equipment
- Self Reliance
- Sustainable Farming
- Food Policy
- Food Preservation
- Homemade Bread
- Homemade Cheese
- Seasonal Recipes
- Garden And Yard
- Herbal Remedies
- Energy Policy
- Other Renewables
- Solar Power
- Wood Heaters
- Green Cleaning
- Green Home Design
- Natural Building
- Environmental Policy
- Sustainable Communities
- Biofuel & Biodiesel
- Fuel Efficiency
- Green Vehicles
- Energy Efficiency
- Home Organization
- Natural Home
- Free Guides
- Give A Gift
- Gardening Tools
- Raising Ducks and Geese
- Garden and Yard
- Other Home Renewables
- Fuel Efficiency News, Blog, & Articles
- Green Vehicles News, Blog, & Articles
- Energy Efficiency News, Blog, & Articles
- Home Organization News, Blog, & Articles
- Give a Gift
- Land For Sale
- Diversity Commitment
- Privacy Policy
- Terms of Service
Natural Fibers Pros and Cons

Encourage a more sustainable textile market by choosing natural fibers that protect the environment, honor producer health, and support your needs.
Which kind of fabric is best for the planet? Unfortunately, trying to choose might leave you with decision paralysis. While it’s well-advised to avoid the petroleum-based synthetic fibers such as polyester (which can burn through millions of barrels of oil), knowing what kinds of fabric to buy instead is hardly clear. Are you better off with breathable but resource-hungry cotton, or is fast-growing but heavily processed bamboo a smarter choice for the environment? Let’s look closer at the growing and processing methods of six of today’s most popular natural fibers to find out.

Cotton (Gossypium spp.)
Durable, breathable, and easy to wash, what’s not to like about cotton? For starters, this fluffy fiber is one of the most polluting products on the planet. The plant’s almost insatiable thirst means that it takes just shy of 5,300 gallons of water to produce about 2 pounds of cotton. Furthermore, the production of one cotton T-shirt requires a third of a pound of pesticides, many of which are classified by the Environmental Protection Agency (EPA) as carcinogens .

Is organic cotton an improvement? Not entirely. The product does come from non-genetically modified organisms (non-GMOs), is produced without synthetic fertilizers or pesticides, and isn’t processed with bleaches or artificial colors. Plus, organic cotton is typically grown in ways that replenish soil fertility, foster biological diversity, and prevent chemicals from entering the water system.
However, organic certification standards allow for the use of naturally occurring fertilizers and pesticides, many of which are still toxic to soil organisms and non-target species. Compounding these growing difficulties for organic farmers, cotton plants are notoriously vulnerable to insect damage , much of which is best managed with non-organic pesticides or by growing GMO varieties.

For use in final products, organic cotton tends to be regarded as higher quality than conventional. Several studies have also shown that consumers will choose organic cotton over conventional, especially when they have an understanding of the environmental implications. If you choose to buy cotton, organic still beats conventionally grown, but be aware that there are still drawbacks to the organic ways of processing.
Cotton Care Instructions
Dry cotton at low temperatures to avoid shrinkage, preferably on a clothesline. For the first wash, add 1/4 cup vinegar to the final rinse to set natural dyes and to prevent color from bleeding.
Linen (Linum usitatissimum )
Linen comes from flax ( Linum usitatissimum ), a fibrous plant famously cultivated by the ancient Egyptians. This time-tested fabric is used for everything from home furnishings to fashionable men’s suits, but is it sustainable?

From an environmental perspective, linen makes sense. It requires few inputs, is gentle on farm soil, and can be incorporated into crop rotations. Flax grows quickly, requires less water and pesticides than cotton, and the entire plant can be used for fabric production. Because flax plants can handle cold temperatures, it grows well in climates that are unsuitable for other fiber plants, such as cotton or bamboo. Likewise, flax yarn is strong enough that it doesn’t require chemical starching during the spinning and weaving stages.

However, linen processing often leads to water pollution, as flax plants are traditionally soaked in large holding ponds to start the decomposition process before the fiber is removed. Some alternative processing methods can reduce this pollution, including allowing plants to decompose directly in fields (field retting), though this could lead to poorer flax quality. In order to avoid potential toxic fertilizers and pesticides involved in linen processing, look for organic suppliers.
Linen Care Instructions
Linen is easy to care for, and consistent washing makes the fabric softer. Make sure you use cold or lukewarm water and a gentle machine cycle with a mild detergent that won’t harm the fibers. Low-temperature tumble drying works well, as does line drying.
Hemp (Cannabis sativa )
Regarded as one of the world’s most durable natural fibers, hemp fabric is lightweight, absorbent, and rivals the strength of cotton. While the material might sound strange today, close to 80 percent of cloth in the United States contained hemp before 1920. America’s first hemp plantings may have been in Jamestown, and the fibrous plant was used for manufacturing everything from work pants to pioneer wagon covers.

Hemp thrives in a variety of climates and soil types, grows tightly spaced, outcompetes weed species, and requires little water and no pesticides. The plant’s long taproot holds soil in place, pulls nutrients to the surface, and prevents erosion. Hemp fabric is entirely biodegradable, UV- and mold-resistant, and cost-effective to produce.
However, hemp has some drawbacks when it comes to versatility. On its own, the fiber creates a material that lacks the soft and supple texture of cotton, for example, so it’s often blended with other fabrics. Hemp fibers also tend to “bunch up” if not treated with anti-wrinkle agents. This occasionally leads to weak points in the fabric that can create holes. Buying hemp fabric blends that are advertised as “relaxed fit” will eliminate this problem, though that does raise concerns about introducing harmful chemicals.

Hemp Care Instructions
Use a gentle wash cycle with a natural detergent, and wash dyed hemp in cold water to prevent colors from fading. Make sure to watch the drying time, as over-drying can lead to broken fibers and a weakened fabric. Likewise, wringing out wet hemp can break the fibers and produce permanent wrinkles in the material.
Bamboo (Phyllostachys edulis )
Considered one of the world’s most renewable materials, bamboo-fiber fabrics have surged in popularity in recent years. Fast-growing, soil-enhancing, and naturally pest-resistant, it takes bamboo plants less than four years to go from seed to full size, and the plant’s dense root network eliminates the need to replant after harvesting.

While little bamboo is certified organic, most is grown organically because it needs few inputs. China is the most significant country to cultivate bamboo on a commercial scale, yet there is a struggle to include bamboo in specific and strong environmental standards to help monitor its production. Thus, because of this oversight, farmers can raise it as a monoculture, which can put native forests at risk for clear-cutting to make space for bamboo farms. This also takes up valuable habitat space which otherwise could promote biodiversity.
Turning raw bamboo fibers into a silky-soft fabric requires an intensive chemical process that involves carbon disulfide and sodium hydroxide, more commonly known as lye. The fiber is made by dissolving bamboo’s cellulose material in the chemical solution before “spinning” it through heavy machinery to produce thread. Many of these chemicals can be toxic for humans, and while some bamboo is processed in less chemically intensive ways, the resulting fabric isn’t as soft or versatile.
Bamboo Care Instructions
Bamboo fabrics will retain their shape when washed in cold or lukewarm water with a gentle detergent. A clothes dryer set at a cool temperature is safe, and don’t forget, material that contains vegetable dyes should not be dried in direct sunlight.
This 10,000-year-old textile remains popular for a reason. Thanks to its complex internal structure, wool is springy yet resilient, providing structure to clothes without compromising their warmth. Not only is wool more absorbent and insulating than cotton, but it tends to last longer and need less washing. Wool can absorb large amounts of water without feeling damp — an advantage to wearing this fabric in the snow — and it’s naturally mold- and mildew-resistant.

The overall environmental footprint of wool is low. Natural wool is a renewable, biodegradable resource, and well-managed herds of sheep can improve their pasture space and local environment while also providing wool.
However, not all wool is produced sustainably. Many commercial flocks are packed into tight quarters and are applied with pesticides, some of which contain toxic organophosphorus compounds that can harm the human nervous system as well as the reproductive systems of fish and amphibians. Several of these chemicals, including the sheep “dip” that is applied externally on the animals to prevent parasites, often runs off into the water system, damaging water quality and harming aquatic life.

The wool manufacturing process requires bleaches and harsh chemical scouring agents to whiten the wool. Additionally, wool dyes often include toxic heavy metals and even suspected carcinogens. To combat these concerns and promote the care of healthy sheep, buy organic wool whenever possible.
Wool Care Instructions
Handwashing or gentle machine washing is best for wool. Take care not to create too much friction, and get rid of excess water by rolling the garment in a towel before letting it dry flat, preferably in the sun.
Considered the queen of textiles, silk is prized for its stunning sheen and endless versatility. While silkworms get all the credit for this lustrous fabric, certain species of bees, beetles, mayflies, and silverfish can also produce silk-like fibers.

Silk is a naturally hypoallergenic textile that is robust, breathable, and resistant to odor. This insect-made fabric tends to be less environmentally damaging than other fibers, as silkworms feed only on mulberry tree leaves, a fast-growing plant that doesn’t require pesticides or fertilizers to grow. Silk is also considered biodegradable.
Some people consider the silk cultivation process to be gruesome, however. Today’s silkworm moths are so domesticated that they have lost the ability to fly, see, or even survive without direct human intervention. The caterpillars live just five days before creating cocoons out of silk threads and are then boiled alive so that the cocoons remain intact before being processed into silk. Concerns about killing silkworms have increased the popularity of alternative silk production methods that don’t rely on traditional production practices.

Globally, silk production has environmental repercussions. Cleaning silk requires the use of harsh chemical solvents that pollute groundwater, and with the expectation that the market will grow in the coming years, the increased silk demand may take a larger toll on resources and the environment. Though it may be revered within the textile consumer industry, silk’s environmental impact during processing reveals how even a versatile and biodegradable fabric can still do harm.
Silk Care Instructions
Silk is notoriously difficult to care for. Dry cleaning is best, but you can hand wash your garments with a silk-specific detergent or mild soap. Never bleach or excessively soak the fabric, and all silk should be air-dried flat.
From a social and environmental perspective, there is no perfect natural fiber. Even seemingly sustainable fabrics have drawbacks when they are produced on a global scale. However, the more locally a product is sourced, the better the chances are that production methods are safer and the environment is healthier. Companies and groups of people are stepping up to lead the way in this locally sourced venture. Fibershed , an organization founded in 2010, is one such example, where the vision is to create regional fiber production systems across the world that will decrease global pollution.
To make the best decision for your health and the planet when purchasing natural fibers, you need to be a conscientious consumer. It’s important to carefully evaluate the life cycle, manufacturing process, and overall environmental impact of a fabric before you buy it so that you can make the right choice for your situation.
What’s the Deal with Tencel®?
A new eco-friendly fiber recently hit the market, and it promises to offer a sustainable fabric solution for the planet. Tencel, the brand name for Lenzing AG’s lyocell fiber , is a form of rayon cloth made from regenerated cellulose fiber in a nontoxic, nonpolluting manufacturing process.

Tencel fibers come from sustainably harvested eucalyptus trees that are processed into a durable rayon fabric. The material is made in a closed-loop process that recycles almost 100 percent of its inputs and decomposes the rest in environmentally beneficial ways. Tencel earned the European Award for the Environment from the European Union for its manufacturing process, and the Forest Stewardship Council (FSC) Certification for its forest management system.
Bright colors might be a cause for concern, as Tencel’s surface is too slippery for natural dyes; chemical solutions, enzyme baths, and dye treatments are used to make them adhere. To try this fabric, seek out brands manufactured in Europe or the United States to ensure the smallest ecological footprint.
Eco-Friendly Apparel Companies
- Alternative Apparel
- Earth Creations
- EcoVibe Apparel
- Groceries Apparel
- HOPE Made in the world
- Indigenous
- People Tree
- Wallis Evera
Eco-Friendly Textile Companies
- Aurora Silk
- Birch Organic Fabrics
- Earth Protex
- EnviroTextiles LLC
- Hemp Traders
- Updated on Apr 4, 2023
- Originally Published on Apr 10, 2018

Subscribe Today to Mother Earth News!
50 years of money-saving tips.
- Spend less cash on groceries by growing and preserving your own food
- Shave off your energy bill and reduce your reliance on the grid with DIY hacks anyone can achieve
- Explore small-scale animal husbandry for provisions, profit, and land management

Canadian Subscribers • International Subscribers
Canadian subscriptions: 1 year (includes postage & GST)

Membership Subtotal
Total savings
Shipping and taxes calculated at checkout.
Clear cart or Continue Shopping →

An official website of the United States government
The .gov means it’s official. Federal government websites often end in .gov or .mil. Before sharing sensitive information, make sure you’re on a federal government site.
The site is secure. The https:// ensures that you are connecting to the official website and that any information you provide is encrypted and transmitted securely.
- Publications
- Account settings
Preview improvements coming to the PMC website in October 2024. Learn More or Try it out now .
- Advanced Search
- Journal List
- Polymers (Basel)

Current Development and Future Perspective on Natural Jute Fibers and Their Biocomposites
Sweety shahinur.
1 Department of Testing and Standardization, Bangladesh Jute Research Institute, Manik Mia Avenue, Dhaka 1207, Bangladesh
M. M. Alamgir Sayeed
2 Dyeing and Printing Division, Bangladesh Jute Research Institute, Manik Mia Avenue, Dhaka 1207, Bangladesh; moc.liamg@07deeyasamm
Mahbub Hasan
3 Department of Materials and Metallurgical Engineering, Bangladesh University of Engineering and Technology, Dhaka 1000, Bangladesh; db.ca.teub.emm@hbubham
Abu Sadat Muhammad Sayem
4 Fashion Institute, Manchester Metropolitan University, Cavendish Street, Manchester M15 6BG, UK; [email protected]
Julfikar Haider
5 Department of Engineering, Manchester Metropolitan University, Chester Street, Manchester M1 5GD, UK
Sharifu Ura
6 Division of Mechanical and Electrical Engineering, Kitami Institute of Technology, 165 Koen-cho, Kitami 090-8507, Hokkaido, Japan; pj.ca.ti-imatik.liam@hallu
Associated Data
The data presented in this study are available within the article.
The increasing trend of the use of synthetic products may result in an increased level of pollution affecting both the environment and living organisms. Therefore, from the sustainability point of view, natural, renewable and biodegradable materials are urgently needed to replace environmentally harmful synthetic materials. Jute, one of the natural fibers, plays a vital role in developing composite materials that showed potential in a variety of applications such as household, automotive and medical appliances. This paper first reviews the characterization and performance of jute fibers. Subsequently, the main focus is shifted towards research advancements in enhancing physical, mechanical, thermal and tribological properties of the polymeric materials (i.e., synthetic or biobased and thermoplastic or thermoset plastic) reinforced with jute fibers in a variety of forms such as particle, short fiber or woven fabric. It is understood that the physio-mechanical properties of jute-polymer composites largely vary based on the fiber processing and treatment, fiber shape and/or size, fabrication processes, fiber volume fraction, layering sequence within the matrix, interaction of the fiber with the matrix and the matrix materials used. Furthermore, the emerging research on jute fiber, such as nanomaterials from jute, bioplastic packaging, heavy metal absorption, electronics, energy device or medical applications and development of jute fiber composites with 3D printing, is explored. Finally, the key challenges for jute and its derivative products in gaining commercial successes have been highlighted and potential future directions are discussed.
1. Introduction
Due to their low carbon footprint, natural fiber-based products are attracting significant attention among academic and industrial researchers for sustainable product development. Amongst the commonly used natural fibers, more recently, a renewed research interest was noticed in the published scientific work on jute plant cultivation (such as diseases and pest identification and control, plant varieties development, seed and plant entomology variation observation at different conditions, genome sequence, soil and fertilizer management and retting process) as well as multidimensional applications of jute fiber in product development including fiber-reinforced polymer composite, micro-crystalline cellulose (MCC), nano cellulose, activated carbon, jute pulp production, 3D printing using the jute fiber as shown in Figure 1 . The growing interest in jute fibers can be well attributed to all three aspects of sustainability, that is, environmental, economic and social.

Trend of research on jute plant and fiber.
Jute plants grow in grassy soil, requiring 125–150 mm of rainfall per month, mild to moderate temperatures (20–40 °C) and high relative humidity (70–80%) for the best growth. Jute is a bast fiber and grown in plantations, where it is collected once the plant matures. The plants are then typically retted in slow running water so that the fibers can be more easily extracted. Other processes to extract the fibers without retting can be used if required. The jute fibers are then dried and marketed for further processing [ 1 , 2 ]. Yarn is often produced from jute fibers and jute fabrics are produced from jute yarn. Some facts and figures about the jute fiber are shown in Figure 2 . In some cases, jute is treated [ 3 , 4 ] via different media to enhance its functional properties. Furthermore, jute is a sustainable raw material for conventional textile products (hessian, carpet backing cloth (CBC), sacking, shopping bag, geo-textile and nursery pot), chemical products (namely carboxy methyl cellulose (CMC), microcrystalline cellulose (MCC) and pulp) and composite products for structural applications (beam, plate, bar). From the sustainability and mechanical properties points of view, jute fiber is better than many natural or synthetic fibers [ 5 ]. The development of structural material in the form of thermosets, as well as thermoplastic-based fiber-reinforced composites, has attracted the most attention. The incorporation of jute fibers in a synthetic polymer matrix could improve its strength but at the same time contribute to environmental sustainability through reduced use of synthetic polymer materials.

Facts and figures about jute. (Information taken from [ 6 , 7 , 8 , 9 ]).
Even though significant research work has been carried out on jute fibers and relevant review papers have been published [ 6 , 8 , 10 , 11 , 12 , 13 , 14 , 15 , 16 , 17 , 18 , 19 , 20 , 21 , 22 ], they were dedicated to jute as a sustainable raw material for mainly composite material development without detailing much about the recent advances in other jute-based research such as nanoparticles from jute, jute fiber engineering by nanoparticles or modern 3D printing of jute-based composites. This review starts with summarizing the characteristics and performance of the jute fiber and functional fiber treatment ( Section 2 ). Section 3 describes the fabrication process of the jute reinforced composites and their characteristics. Section 4 highlights the future potential of jute fiber in terms of research and product development. Challenges and potential future research directions are discussed in Section 5 . Finally, Section 6 draws a few conclusions based on the review. It is believed that this review would provide useful guidance on the current development and future potential of jute-based products.
2. Jute Fiber Characterization
Like any other natural fiber, the performance of the jute fiber varies due to the natural variability in surface and internal microstructural characteristics, which can be influenced by a number of factors including growing conditions (i.e., temperature, humidity, soil condition), retting (water, dew or enzymatic) and fiber extraction processes, fiber length and diameter, chemical constituents and their proportional amounts [ 6 , 12 , 23 ]. Microstructural characteristics again contribute to the physical, mechanical and thermal performance of the fiber. This section starts with some general morphology of the jute fiber followed by examples of its performance in the form of fiber, yarn and fabric either woven or nonwoven. Finally, examples of functional treatment of the jute fiber in order to improve its performance for a specific application are discussed.
2.1. Morphology and Microstructure of Jute Fiber
The fiber morphology is characterized by a scanning electron microscope (SEM) after applying a gold coating on a small portion of the fiber. The related SEM fractured and fiber surfaces are shown in Figure 3 . The cross-sectional geometry is characterized by an irregular shape. Furthermore, the cross-section size varies along the length of the fiber [ 24 ]. The surface morphology is generally rougher in nature with evidence of random micro pores. The surface morphology of different portions of the jute fiber was found dissimilar due to their variations in diameter and maturity (immature, fully mature and overmature) [ 9 ]. Less micropores in the surface morphology generally indicate immature fiber. Further details about the jute morphology can be found in the literature [ 25 , 26 , 27 ].

Jute fiber morphology: ( a ) cross-section and ( b ) surface [ 9 ].
Figure 4 presents X-Ray diffraction (XRD) and Fourier transforms infrared (FTIR) spectroscopy spectra of raw jute fiber. The distinctive large XRD peak indicated the cellulose crystallographic plane (002) with a 92.02% degree of crystallinity [ 28 ]. FTIR spectra confirmed the presence of functional groups on the jute fiber surface. Several broad peaks across the spectrum indicated the presence of hydrate and hydroxyl (OH), which represented cellulose and hemicellulose elements in the jute fiber [ 4 ].

Microstructural characteristics of jute: ( a ) X-Ray diffraction and ( b ) FTIR spectra [ 28 ].
2.2. Jute Fiber/Yarn/Fabric Performance
A tensile test is carried out to evaluate the performance of jute fiber/yarn/fabric. Some of the test results available in the literature are shown in Table 1 .
Tensile properties of jute fiber/yarn/fabric.
2.2.1. Single Jute Fiber
Although, in practical applications, jute fibers are agglomerated as bundles, for standardization, evaluation of single fiber properties is important. Shahinur et al. [ 9 ] conducted single fiber tensile testing using an Instron™ universal testing machine (Norwood, MA, USA) by varying the span length (5 mm, 15 mm, 25 mm and 35 mm) with a crosshead speed and load cell of 5 mm/min and 5N respectively. The fibers were then stacked between two paper frames [ 29 ] to conform good gripping to the clamps of the test machine and to provide straight direction during the test as shown in Figure 5 . Tensile strength, Young’s modulus and strain to failure were determined from the test. The whole jute fiber was cut into three portions—top, middle and cutting/bottom. With an increase in the span length, tensile strength decreased, tensile modulus increased and strain to failure decreased. Furthermore, tensile properties of the middle portion of the jute fiber displayed better performance compared to the top and bottom portions. Although the tensile strength of the jute fiber varies between 200–800 MPa, there are other manmade fibers such as glass fiber (2400 MPa) or more recently developed Forcespinning ® NCST fiber showed record-high tensile strength (13.7 ± 3.2 GPa) [ 36 ].

Single jute fiber characterization. TS: Tensile strength, E: Young’s modulus.
2.2.2. Jute Yarn
As jute is a natural fiber, its mechanical properties would vary, indicating that uncertainty exists in obtaining fibers with consistent mechanical properties. The way mechanical tests are conducted on jute might influence the distribution of its mechanical properties. A number of studies were reported in the literature to understand these variations with statistical distribution.
For example, samples were prepared by varying gauge length of the jute yarns samples and stress, strain at failure and Young’s modulus were tested under static tension [ 37 ] according to the standard ASTM D578 using 50 mm gauge length. Wide dispersion in mechanical properties of the jute yarn was found and this dispersion becomes steady after testing 200 samples. The experimental data matched well with the data obtained from a two-parameter Weibull analysis.
Smail, et al. studied the mechanical properties of jute yarn at different loading rates (0.3, 1.2, 2.0 and 4.0 mm/min) under static tensile test conditions [ 38 ]. The results indicated that loading rate affected stress, elongation and Young’s modulus without any clear trend. However, the best mechanical properties were attained at a loading rate of 2 mm/min.
Ullah et al. [ 2 , 39 ] employed statistical analyses and possibility distributions to ascertain the uncertainty associated with mechanical properties (tensile strength, modulus of elasticity and strain to failure) of jute yarns and fibers by conducting tensile tests. Typically, the jute yarns showed linear behavior until failure in a load versus elongation graph as shown in Figure 6 . Although, in another study, this behavior was stepwise due to the gradual failure of the weaker fibers in the yarn during the tensile testing [ 37 ]. The uncertainty associated with the jute fibers was found higher than that of the jute yarn. Therefore, it was recommended to use the mechanical properties related to the jute yarn in order to develop jute-fiber-based products.

Typical load-elongation plots for jute yarn [ 2 ].
2.2.3. Jute Woven/Nonwoven Fabric
Jute fabrics come in different weave structures, of which 1/1 plain weave is the most common and such fabric is commercially known as hessian ( Figure 7 ), whose specification is presented in Table 2 . In practice, the structure and weight of jute fabric are determined using the standards BS EN 1049-2:1994 and BS 2471:2005, respectively. The breaking force and elongation of the fabric were analyzed following the test standard BS ENISO 13934 and using a tensile tester (e.g., Testometric Micro 500, Rochdale, UK). The breaking forces in the wrap direction were higher than in the weft direction due to the higher number of ends per unit length [ 40 , 41 ]. Minor differences also existed in different batches of fabrics possibly due to the variations in manufacturing or fiber quality.

( a ) Hessian Jute fabric with schematic representation of plain weave and ( b ) differences in tensile breaking forces of the jute fabrics in different directions from two different batches.
Specification of jute fabric.
Meanwhile, jute nonwoven fabrics are generally made from raw jute fiber or jute waste using the needle-punching process. The performance of the nonwoven fabric is evaluated by tensile strength, bursting strength, compressibility, bending modulus, air permeability. Further details can be found in a review on nonwoven fabric [ 42 ].
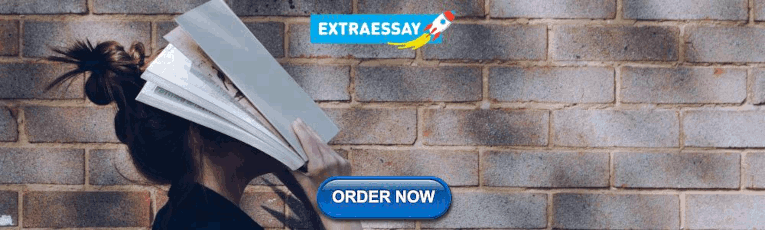
2.3. Functional Treatment of Jute Fiber
Being a natural fiber, jute possesses several weaknesses such as easily rotten, flammable, thermal degradation and high affinity to moisture, which make it unsuitable in raw condition for functional use in products. Therefore, they require additional modification for use in sustainable product development [ 4 , 28 , 43 , 44 ]. Several modifications have been suggested in the literature to improve the functional performance of the jute fiber alone or jute as a reinforcement in composite materials ( Figure 8 ).

Types of treatments on jute fiber and their effects on fiber performance [ 4 ].
Jute fibers were treated with rot- (RT), fire- (FT) and water-retardant (WT) chemicals and FTIR analysis evidenced the presence of constituents related to the treatment chemicals. Higher bacteria inhibition zone diameters against several bacteria such as Acinetobacter sp., Bacillus cereus and Pseudomonas sp. indicated the effectiveness of rot retardancy treatment. On the other hand, fire- and water-retardant treatments slowed down the burning rate against fire and reduced contact angles in contact with water when compared with the untreated jute fibers. Thermal characterization of the RT, FT and WT jute fibers was conducted using Thermo-gravimetric analysis (TGA) and differential scanning calorimetric (DSC) analysis [ 44 ]. Lower heat absorption was observed by the treated fibers when compared to the raw jute fiber. The ranking of the treated fibers in terms of heat absorption (lowest to the highest) was as follows: Raw jute < RT < WT < FT. This indicated that all the treated fibers showed better thermal characteristics than the raw jute fiber, but the FT treated fiber showed the best thermal characteristics.
Natural fiber has high affection for the water but lower affinity to the polymer matrix materials and this drawback can be minimized using chemical treatment and incorporating the treated fiber into the polymer composite. Chemical modification techniques such as alkali or coupling agents like silane are most commonly applied to improve interfacial bond strength in the composites by reducing the hydrophilic nature of the jute fiber to make it compatible with hydrophobic polymer matrix, encouraging chemical bonding and increasing fiber surface roughness to promote mechanical interlocking. These changes make the resulting composite with improved mechanical properties [ 45 ]. However, other physical techniques such as plasma or Gama radiation are effective in improving mechanical properties. Furthermore, jute fiber treatment might help in accommodating higher fiber volume in the composites in order to make them lighter and more sustainable. Jute fiber treatment in itself is a huge topic for review, which is outside the scope of this paper. However, further details about different types of jute fiber surface treatment are summarized in recent publications [ 7 , 25 ] and other reviews on plant fiber treatments [ 46 , 47 , 48 ]. When treated and non-treated jute fibers are incorporated into the matrix, the performance of the composite might change.
Other than changing the chemical structure of the jute fiber to a favorable state by surface treatment, physical and mechanical properties might be affected. It was reported that alkali treatment of jute fiber could reduce its diameter by 8% whereas the tensile strength could be increased by 44% [ 49 ].
3. Jute Based Composites: Processing and Performance
Natural fibers are incorporated into polymeric materials to form composites with improved and customized properties. A multitude of parameters related to the type of fiber used, pre-processing of fiber, composite manufacturing techniques and internal condition of the composite can affect the performance of the composites as shown in Figure 9 . In this section, a brief overview of the fiber forms used in different matrix materials is provided. Performance evaluations of both the thermosetting and thermoplastic composites were reviewed with examples of different forms of fibers. Finally, the progress on the hybrid jute composite development is briefly discussed.

Factor influencing natural fiber reinforced composites [ 40 ].
3.1. Matrixes for Jute Fiber Reinforced Composite
The mechanical performance of the composite materials depends on the polymer matrix materials such as thermoplastics and thermoset or biobased plastics. Properties of some commonly used matrix materials are presented in Table 3 .
Physio-mechanical properties of common thermoplastics and thermoset matrix materials.
TS = Tensile strength, TM = Tensile Modulus, BS = Bending Strength, BM = Bending modulus.
3.1.1. Thermoset Matrix
Thermoset matrix materials such as epoxy, phenolics, polyester, bakelite, melamine formaldehyde, and polyurethane come in liquid form at room temperature, and they are mainly sourced from non-renewable resources. Once the matrix material is fully cured, it cannot be reheated, recycled or reused nor can it be biodegraded. They can be processed by hand lay-up, spray-up, vacuum infusion, vacuum bagging, prepag, resin transfer molding (RTM), filament winding, pultrusion, extrusion, resin impregnation and cold press as shown in Figure 10 . However, endeavors are made to develop bio-based thermosets from vegetable oils, natural phenolic complexes and other sources, which might possess better thermal stability compared to thermoplastic [ 52 ]. Some progress has also been made toward developing biodegradable thermoset plastics with similar characteristics as the traditional thermoset such glycix, titan and hydro [ 53 ]. Mass scale manufacturing techniques such as plastic molding of biodegradable thermosets are also being explored in order to get a sustainable thermoset, which can contribute toward reducing carbon footprint.

Thermoset matrix material in composite fabrication.
3.1.2. Thermoplastic Matrix
Thermoplastics can be available in the form of granules, plates, sheets or powder. Polyethylene (LDPE/HDPE), polylactic acid (PLA), polyvinylchloride (PVC), polystyrene, polypropylene (PP), Nylon and polycarbonate are commonly used matrix materials ( Figure 11 ). These types of plastics are recyclable, some of them are biodegradable and as well processed from biobased resources such as PLA. The thermoplastics are processed by compression molding, extrusion, injection molding and sheet molding.

Different categories of thermoplastics and their popular applications.
3.2. Jute Fiber as Reinforcement in Composites
Jute fibers in the form of particles (macro, micro or nano), fiber (short < 5 mm; semi long > 5 mm; long), fabrics (Plaine, twill and Satin) and nonwoven can be used to manufacture composites depending on the applications and performance requirements. Figure 12 presents different forms of the jute fiber, that will influence the properties of the resulting composite material.

Different forms of jute fiber reinforcements used for fabricating polymer composite: ( a ) Particles, ( b ) Short ( c ) Semi-long ( d ) Long ( e ) Fabrics ( f ) Nonwoven.
When jute fiber is incorporated into the matrix material, the resulting composite strength would be higher than the matrix material but lower than the jute fiber as shown in Figure 13 [ 41 , 43 ]. Moreover, in the case of thermoplastic composite, there is no crosslinking in the matrix whereas only Vander walls force is present. However, crosslinking is available in the thermoset polymer material itself. Therefore, there is a low possibility of the presence of crosslinking between the fiber and matrix for thermoset composites and a higher possibility in the case of thermoplastic composites.

( a )Effect of the fiber in the matrix materials ( b ) cross-linking between the fiber and two types of matrix materials. Control: pure polypropylene; J-PP: Jute-polypropylene composite [ 54 ].
3.3. Processing of Jute Fiber Composite
A number of techniques are used for fabricating jute reinforced composite including molding techniques such as compression molding, injection molding, resin transfer molding, extrusion, pultrusion, hand lay-up and spray lay-up. Processing techniques are mainly selected depending on the type of polymer, requirement of labor, mold condition (open or closed), the form of fiber (short, long, particle), presence of multiple fibers, quality of the end product, speed and cost of processing, capital investment and so on [ 13 , 50 , 54 , 55 ]. The popular techniques for fabricating thermoplastics and thermoset plastic composite are hot compression and hand lay-up, respectively, as shown in Figure 14 . The details of the jute composite processing techniques have already been reviewed in a recent paper [ 18 ]. As the focus of this paper is more on new areas of jute research, interested readers are directed to the article for further details.

Composite fabrication using the hot press and hand lay-up techniques.
3.4. Jute Thermoset Composite
Thermoset polymer has high tensile properties particularly tensile strength and young’s modulus whereas poor ductility. By incorporating natural fiber, the strength, as well as ductility, can be further improved. Meanwhile, the thermoset materials are cheap, easily available and, after curing, they become harder at room temperature. In addition, the thermoset plastics are amorphous whereas, after the incorporation of the fiber, the composite possesses both amorphous and semi-crystalline phases [ 3 ], which lead to higher strength and strain to failure. In general, nonwoven and woven jute fibers are incorporated in the most commonly used epoxy matrix. Although many examples exist in the literature [ 18 , 56 ], example performances of the jute thermoset composite including the authors’ previous work are discussed.
3.4.1. Jute Fiber-Thermoset Composite
The unidirectional fibers can be incorporated into the thermoset matrix materials. For such types of composite fabrication, hand lay-up is the simplest and easiest way. Biswas, et al. [ 57 ] worked on developing unidirectional jute epoxy composite and mechanical performance is listed in Table 4 . The composites displayed higher tensile strength and flexure strength compared to the epoxy matrix. Moreover, fiber distribution was not found uniform in the composites as shown in Figure 15 .

( a ) Tensile and ( b ) flexural fracture surfaces of jute-epoxy composite [ 57 ].
Tensile and mechanical properties of jute epoxy composite.
Note: TS: tensile strength; TM: Tensile modulus; BS: Bending strength and BM: Bending modulus.
Rahman et al. [ 58 ] studied the effect of fiber orientation and jute volume fraction in jute polyester composites on mechanical and thermal properties with a maximum volume fraction of 30%. With a suitable combination of fiber orientation and fiber volume fraction improved mechanical properties were obtained and this type of composite can replace wood-based structures and potential to be used as a thermal insulation material.
Liquid thermoset resins can easily penetrate through the fibers. However, when pressure is applied for uniform penetration, the fiber orientation might change affecting the load-bearing capacity of the composite. In order to overcome this limitation, jute fabrics are incorporated into the thermoset matrix for obtaining uniform properties in different directions.
3.4.2. Jute Fabric-Thermoset Composite
The fibers are highly interlocked with each other in the woven fabrics compared to individual fiber or bundle fiber and their corresponding composites show higher strength. Therefore, when the number of jute fabric layers is increased within the matrix with good bonding, the corresponding composite shows increased performance. Different layers of jute fabrics [ 59 ] were incorporated into polyester through the hand lay-up technique and the findings are depicted in Figure 16 a–c. It was clearly observed that tensile strength and modulus increased with an increase in the number of layers in the composite. However, with a higher number of layers, water uptake increased. A balanced approach should be adopted to get good mechanical properties without absorbing excessive water, which might affect the long-term mechanical performance.

Performance of jute-thermoset composites ( a ) Tensile strength ( b ) Young’s modulus ( c ) water uptake of different layers jute polyester composite; ( d ) thermal conductivity and ( e ) water absorption of jute cotton polyester composites; ( f ) jute polyster composite with treated and untreated jute fiber [ 3 , 59 , 60 ].
Due to the presence of hydroxyl and other polar groups in various constituents of the natural fiber, the moisture uptake of the jute fabric-reinforced composite was higher compared to the synthetic polyester. This could lead to poor wettability of the fiber with the matrix, weak interfacial bonding and increased void content. Therefore, water repellant treatment of the jute fabrics or adding other fillers might reduce the water uptake. Jute based polyester composites targeted for a rooftop and fence for poultry were fabricated with different layers of jute-cotton blended fabrics (Jute/cotton: 50/50, 60/40, 70/30 and 100/0) and additives such as cashew nut shell (CNSL), nano-cellulose/nano-clay, and MEKPO hardener using a simple hand lay-up technique and their performance were analyzed [ 60 ]. With the increase of layer numbers, thermal conductivity increased except for 50/50 jute-cotton Figure 16 d,e. A similar trend was also found in the case of water uptake behavior. However, the treatment with the nanoparticles brought a positive impact by reducing the thermal conductivity and water absorption. In order to further improve the jute polyester composite performance, the jute fiber was treated with alkali and nano-clay [ 3 ] and the results are shown in Figure 16 f. A nano incorporation of 1% was found to be the optimum value for obtaining the maximum strength.
Jute fabric treatment by 10 to 15% NaOH was recommended to obtain the best mechanical properties in jute fabric-based epoxy composites [ 61 ]. Nath, et al. [ 62 ] incorporated the cenosphere from fly ash in woven jute-epoxy bio-composite to convert industrial waste into a value-added composite material. Addition of 5wt. % filler increased the tensile, flexural, interlaminar shear strength (ILSS) and hardness of the composite whereas the water absorption and thermal conductivity values showed an opposite trend. Nonwoven thermoset composites exhibit superior sound and heat insulation characteristics [ 63 ] as the fibers contain hollow lumen in their structure.
3.5. Jute Thermoplastics Composite
3.5.1. jute fiber-thermoplastic composite.
Jute is a cellulosic material and has free OH-, which leads them to absorb moisture. As a result, they can be easily affected by bacteria and fungus and rot easily. Furthermore, the cellulosic fiber easily burns. Therefore, jute fibers were processed with water, fire and water retardant treatments and composites were formed with Maleic anhydride–grafted polypropylene (MAgPP) using a hot press machine. In all cases, with the increase of fiber content (wt.%) in the composites, the mechanical properties improved as shown in Figure 17 . However, the treatments caused degradation of the tensile strength properties compared to the untreated jute composite. Fiber breakage and pull-out were evident in the tensile fracture surfaces. Uniform fiber distribution within the matrix could be a major contributing factor in terms of obtaining better composite properties.

Mechanical properties and fractured surface characteristics of jute fiber reinforced thermoplastics composite fire-retardant (FRM), rot-retardant (RRM) and water-retardant (WRM) treatments on the jute fiber. Control M indicates no fiber treatment [ 43 ].
Short jute fiber (~5 mm) was chemically treated with alkali, potassium permanganate, and silane and mixed with PP to develop composites that can resist moisture absorption. All composites with the treated fibers showed better mechanical properties than that with the untreated fiber. Silane-treated jute-PP composite showed the lowest water absorption characteristics but the potassium permanganate-treated one showed the best mechanical properties. Depending on the application requirements, a suitable choice can be made [ 64 ]. Compared to other treatments, MAgPP and silane-treated jute–PP composites exhibited lower creep strains at longer durations [ 65 ].
3.5.2. Jute Fabrics Thermoplastic Composite
There are varieties of woven fabrics (e.g., plain, satin and twill) where the fibers are highly interlinked are used to fabricate thermoplastic composites in a layered structure. Figure 18 a shows the cross-section of a six-layer plain-weave jute fabric composite where the layers were fully embedded within the matrix with the layered structure [ 41 ]. Tensile strength and flexural strength increased with the number of layers ( Figure 18 b,c). During tensile failure, some fiber surfaces within the yarn showed not much evidence of matrix adhesion indicating a lack of fiber wetting by the matrix material. In some cases, evidence of poor adhesion was also noticed by a clear gap between the matrix and fiber. Other layered composites using different matrix materials such as polypropylene and nylon were also developed [ 41 ]. In the case of woven thermoplastic composite, the mechanical properties depend on a number of factors such as fabric weight, fabric structure, yarn count, types of fiber, processing technique, as well as the type of matrix material used.

Mechanical properties jute-HDPE composites with varying number of jute layers: ( a ) layered composite cross-section ( b ) tensile strength ( c ) flexural strength and ( d ) tensile fracture surface [ 41 ].
Nonwoven jute fabric was also combined with thermoplastics as a promising reinforcement due to its flexible, lightweight and low-cost characteristics when compared to conventional woven fabrics. Sayeed et al. developed jute/polypropylene nonwoven reinforced composites using compression molding technique following film stacking strategy [ 49 , 66 ]. With alkali treatment of fiber, the composite showed improved mechanical properties. Tensile and flexural moduli could be maximized by tailoring the structure with the preferential and non-preferential alignment of the fibers with jute content between 23 and 33 wt.%. However, the layering sequence showed an insignificant effect on the tensile strength and elongation before breaking. Similarly, the rise in jute content enhanced the storage and loss moduli but the damping parameter showed a declining trend. Again, the layering sequence appeared as an influential factor in reaching the peak storage modulus [ 67 ].
3.6. Jute Based Polymer Biocomposite
Similar to other natural fibers, the major problem with the jute-based composite is that it cannot be easily recycled or biodegraded when compounded with the traditional non-biodegradable polymer matrixes. This only reduces the consumption of synthetic polymeric materials. However, in order to develop an eco-friendly green composite, both the fibers and the matrix materials must be biodegradable. Biodegradable composites with PLA films and jute nonwovens were developed by employing a film-stacking design in compression molding. Excellent tensile and flexural strengths were achieved by the composites but compared to the pure PLA, the composites showed slightly poorer thermal stability [ 68 ]. Meanwhile, completely degradable bio-composites have been made by Hu et al. [ 69 ] using short jute fiber for the automotive industry by increasing the volume fraction up to 70%. A higher volume fraction of jute fiber can effectively reduce the cost of the composite significantly. Short jute fibers and short PLA fibers were mixed with a jute volume fraction ranging between 60% and 70% and felt was made via carding and needle punching. The hot pressed molding process then used the felt as the starting material to fabricate the jute/PLA composite. The mechanical strength of the composites increased with the fiber volume fraction and good formability and processability were realized in manufacturing life-size truck liners for automotive applications. Other biobased jute composites using PLA have been recently reviewed [ 20 ]. Though the bio-based polymer composites are biodegradable, the strength is limited for a particular fiber, process and matrix, which can be tailored by hybridization and sandwich structure.
3.7. Hybridization with Jute Fiber
3.7.1. fiber/filler/matrix combinational structure.
It is well known that the mechanical properties of the jute fiber-based composites are still inferior to synthetic fiber-based composites such as Glass Fiber Reinforced Composite (GFRP) or Carbon Fiber Reinforced Composite (CFRP) [ 70 ]. Jute fibers are mixed with other natural or synthetic fibers or fillers to obtain improved properties by exploiting the strength of multiple fibers/fillers. In some cases, the hybrid composites can add multifunctional characteristics suitable for certain applications. Hybridization can occur in the case of fiber as well as matrix material such as different polymer matrixes in the forms of liquid, granule, plate or sheet. Figure 19 presents some conceptual designs for hybrid composites with different combinations of fibers, fillers and matrixes or their arrangements with some cost estimation. Furthermore, fiber arrangements can be oriented at different angles (e.g., 0°, 45°, and 90°) or the fiber itself can be changed to different forms (e.g., particle, short fiber, long fiber, whisker, webbed fiber woven or nonwoven).

Schematic diagrams of hybrid composite designs and some cost estimation [ 54 ].
There are number of studies available in the literature on the hybrid composites with the addition of another natural fiber such as coir and wool in different types of matrix materials in combination with the jute fiber [ 71 , 72 , 73 , 74 , 75 , 76 ]. In general, the fibers are chopped into short fibers and mixed with a predefined ratio before adding to the matrix material. Figure 20 presents the hybridization effect on jute thermoplastic composites with different combinations of fibers (Jute, J; Coir, C and Wool, W) and matrixes (Polyethylene, PE; Polypropylene, PP). PE-based composites showed lower strength possibly due to the weaker matrix. On the other hand, the effect of wool fiber was more influential than the coir fiber when the matrix and fiber were fixed to PP and jute. The overall fiber content and the ratio between the fibers could affect the strength of the resulting composites. From the fracture surface of the composites, different fibers can be clearly identifiable and fiber breakage, fiber pull out, and weak bonding was also observed. Favorable entanglement between the fibers and better interaction with the matrix could be considered as the reason for improved strength in the hybrid composites. With a combination of multiple compatible natural fibers and a biobased matrix, a sustainable composite with tailored properties can be developed.

Effect of natural fiber hybridization on jute composite [ 71 , 72 , 73 ].
Synthetic glass/carbon fiber reinforced polymer composites are mostly used due to their uniform properties, high strength, durability but their non-biodegradability and non-renewability forces efforts to find alternatives. Natural fibers like jute can be incorporated with the GFRP/CFRP to minimize the use of synthetic fibers while maintaining reasonably good mechanical strength [ 70 , 77 , 78 , 79 , 80 ]. The content of synthetic fiber is more influential in defining the mechanical performance than the stacking sequence between the synthetic and jute fibers [ 81 ]. Therefore, appropriate tailoring of jute fiber composites with synthetic fibers could provide a balance between cost, performance and environmental impact [ 82 ].
Some nanofiller (carbon nanotube, graphene,) incorporation in the jute composite can increase performance which will create a new area of research [ 83 , 84 ]. Hybrid jute composites with a mixture of two matrixes such as reinforced polyvinyl chloride (PVC) and polypropylene (PP) were also prepared by compression molding. A mixture of 60% PP and 40% PVC matrixes was recommended for the best performance [ 85 ].
3.7.2. Sandwich Structure
Jute fiber can also be used in the hybrid sandwich structure where the core part is thicker and lightweight and outer skins/panels are thin but stronger to provide necessary stiffness. A number of designs could be possible with nonwoven jute being the core or jute composite as the skin or even jute composite with hollow structure (lattice/corrugated) as the core as shown in Figure 21 . These types of designs can provide lightweight structures with environmentally friendly jute material. Endless other designs are possible to use jute in sandwich composite simply expanding the imagination of the designers.

Some examples of sandwich type jute-based composite design ( a ) jute as core ( b ) jute composite as skin and ( c ) jute composite lattice/corrugated structure as the core.
Aly-Hassan et al. [ 86 ] suggested an innovative composite design to be used as smart inclined roofs for houses in the snowiest countries. The sandwich structure was comprised of a nonwoven jute core with glass fiber reinforced composite (GFRP) skins. The key benefits of this design were that it is strong but lightweight, thermal insulator and noise suppressor. Furthermore, the structure was equipped with a heating element and a snow-repellent nanocoating system in the skin to break the contact layer between the accumulated snow and the roof for quick and automatic removal of the snow. Another sandwich design based on jute fiber was proposed for energy absorption in body armor application [ 87 ]. Jute-epoxy (JE) and Jute-epoxy with rubber core (JRE) composites were developed, and their energy absorption capacities were evaluated. The results revealed that the JRE composite absorbed 71% higher energy than the JE. The experimental damage patterns matched well with Finite Element Analysis (FEA).
In another design, epoxy-jute composite plates were arranged in a grid structure to be considered as the core where spruce wood acted as the skin [ 88 ]. Failure tests showed a number of modes including shear, panel fracture, separation of the core from the panel. Fiber pull-out and splitting were attributed to the underlying mechanism for the shear failure.
Similarly, a corrugated lattice sandwich structure made of epoxy-jute fiber was used as the core in another design [ 89 , 90 ]. Bending tests identified the shear buckling failure mainly in sandwich struts. Another example of the sandwich structure was given in [ 91 ] where Jute/PP composite plates reinforced with jute/PP commingled nonwoven fabrics were used as the facing materials and balsa wood, PET foam and PP honeycomb as the core materials with balsa wood being the best core under bending loading condition. This jute-based sandwich could be considered an eco-friendly, low-cost and lightweight structure for various engineering applications.
4. Emerging Applications of Jute Fiber
For the past many years, scientific research is mainly focused on developing jute fiber reinforced polymer composites and characterizing their physical, mechanical, and structural properties for various applications in a number of sectors such as textile products, automotive, construction, defense, packaging, home furnishing, fashion, transportations, and sports [ 18 , 21 , 92 ]. As jute fiber absorbs CO 2 , emits O 2 and consumes relatively less energy during product development, hence from the sustainability viewpoint, jute-based products can be considered better than synthetic products. However, more recently jute fiber is being researched for diversifying the application areas. The following examples demonstrate the potential of jute fiber for future product development.
4.1. Nanomaterials from Jute
Jute fiber has now been converted into nanoparticles using chemical treatment and mechanical processing. CMC, MCC, CNC, and charcoal can be converted into nanoparticles to be used in different sectors such as heavy metal absorption, food packaging, drug delivery, etc. ( Figure 22 ) either as an individual particle or by incorporating it into polymer matrix [ 93 , 94 , 95 , 96 , 97 , 98 , 99 , 100 , 101 , 102 , 103 , 104 , 105 ].

Examples of product development with jute nanoparticles.
Nanocellulose has some distinct characteristics including high surface area, promising rheological properties, ability to absorb water, crystalline structure, favorable surface chemistry, barrier properties and nontoxicity, which make it suitable to be used in packaging film and food applications [ 103 ]. Jute itself, as well as its constituents, have absorbing capacity and therefore absorbing materials can be developed for efficiently separating heavy metals using jute-based nanomaterials [ 98 ]. Furthermore, when nanocellulose is incorporated into the matrix material, the nanocomposite film showed superior strength and physical properties [ 97 , 106 ]. An appropriate level of cellulose nanofibril content can improve the interaction with the matrix leading to better mechanical properties. Possible other prospects of jute fiber in a host of other nanotechnological applications are discussed in recent literature [ 102 ].
4.2. 3D Printing with Jute
3D printing has found applications in producing products with complex shapes eliminating the need for assembling, though limited by the choice of materials and speed of production [ 107 , 108 , 109 , 110 ]. Initially, 3D printing was limited to only a handful of polymeric materials but thanks to the scientific research in making materials such as metals, ceramics and composites in different forms including powder or filament. Conventional composite fabrication is difficult for complex shapes; therefore, 3D printing opens up new opportunities. Jute fiber can be used to develop composite filament for printing jute-based products. Figure 23 shows process steps in manufacturing 3D printed biobased jute composite.

Natural fiber incorporation in 3D printing filament.
Matsuzaki et al. [ 111 ] invented a unique method of 3D printing of continuous jute fiber-based PLA thermoplastic composite using fused-deposition modeling where both the polymer filament and the twisted jute yarns were individually fed to the printer. The fibers were unfirmly embedded within the matrix as a reinforcing material. Carbon fiber-based PLA composite was also produced following the same procedure for comparison. Although jute fiber-reinforced composite showed slightly better tensile strength than the pure polymer but was inferior to the carbon fiber-based composite. The volume fraction of the jute fiber was quite low (6.1%). However, some success was achieved when continuous flax fiber/PLA (cFF/PLA) composite filaments were made by coating the fiber with PLA using an extrusion process and printed by the composite filament in a simple 3D printer [ 112 ]. Unform distribution of the yarn with the matrix was observed in the printed samples. Significant improvement in tensile strength and modulus was achieved compared to the published results on 3D printed continuous natural fiber printed composites.
Perez et al. [ 113 ] compared the strength and fracture behavior of FDM 3D printed ABS with different fillers including 5 wt.% jute fiber. Although the jute fibers were embedded within the ABS matrix but the strength of the jute-ABS composite was slightly lower than the pure ABS. Evidence of higher porosity and poor bonding might be the cause of the poor result.
Other than composite filament or individual fiber-polymer filament feeding to the printer, an alternative approach was explored by Franco-Urquiza et al. [ 114 ]. PLA-fused filament was deposited onto jute fabrics. The jute fabric was modified with flame retardant additives, and adhesives to gain improvement in mechanical properties. However, the composite did not show any improvement over the pure PLA in terms of stiffness or strength even though fabrics were well organized and bonded with the matrix. A further detailed investigation was suggested by the authors to obtain a better composite.
Nano fiber/cellulose or activated carbon collected from the jute fiber can be added to the 3D printer filament for applications in aerospace, packaging, and medical appliance such as scaffolding [ 115 ]. Jute fiber treated with an antibacterial agent can be encapsulated in polymers for providing a slow-release antibacterial effect over a long period of time. Therefore, jute fiber-based 3D printed products can lead to completely new research directions.
4.3. Electronics, Energy Storage and Sensing
Jute fiber containing cellulose, hemicelluloses, lignin and a small amount of ash makes it a suitable raw material for activated or non-activated carbon preparation utilizing a number of methods such as pyrolysis with or without chemical and physical activations. Having a fine porous structure and a large specific surface area, carbon-derived from jute could be used in a number of applications such as energy storage, water treatment, and sensing [ 116 , 117 , 118 , 119 ] due to its capacitance, filtering and electronic properties respectively.
Activated carbon was synthesized from jute fibers with KOH activation at a high temperature of 700 °C for hydrogen storage application [ 120 ]. The activated carbon retained channel-like fibrous structures with increased surface area and micropore volume showed promises of an increased hydrogen storage capacity. Another study investigated the potential of micro-mesoporous carbon material derived from jute fiber as an anode in lithium-ion batteries [ 121 ]. Manjakkal et al. [ 122 ] designed and developed an energy-autonomous system containing a jute fiber-based supercapacitor (SC) and temperature and humidity sensors. The SC was charged using a solar cell while the biobased sensor was powered using the SC. This system showed huge potential as an eco-friendly solution in applications like wearables and smart packaging for food quality monitoring. Biodegradable conducting polymer composites were developed by adding jute fiber to Polyvinyl Alcohol (PVA)/multi-layer graphene (MLG)/multi-wall carbon nanotube (MWCNT) [ 123 ]. The composites retained viscoelastic nature as found in a dynamic mechanical analysis. Furthermore, the composite showed high electrical conductivity and effectiveness in shielding electromagnetic interference.
Success was made in developing Transparent jute fiber (TJF) from delignified jute fiber as a replacement for transparent wood as the TJF has the ability to match the properties of the transparent wood [ 124 ]. Owing to the processing simplicity and lower processing cost along with good optical and mechanical properties, the TJF might find applications in smart devices, for example, light-emitting diodes (LEDs) and solar cells [ 125 ]. Multiple recyclable transparent film was also produced from waste jute fabrics using the ionic liquid (IL) assisted regeneration process [ 126 ]. This film has the potential to be used in packaging materials or in electronic devices for information storage. Therefore, these types of jute base advanced material will lead to a novel area of research in the near future.
4.4. Biodegradable Packaging
4.4.1. sonali bag—solution to single-use plastic.
Single-use synthetic plastics for instance plastic carrier bags have become an integrated part of daily life over the past many years. However, there is a growing concern worldwide that their uncontrolled release into environment can cause significant damage to marine life, plastic pollution on the earth and imbalance in the ecosystem. In many countries in the world particularly in Europe, single-use plastic will be banned in the future, and it will be replaced by more environmentally friendly biobased and biodegradable materials [ 127 ]. More recently, a team in Bangladesh developed an alternative low-cost biodegradable solution to polyethene bags named the “Sonali Bag” from modified jute cellulose, which can be biodegraded in soil within three months and showed similar or better mechanical and physical properties compared to the synthetic polyethene bags [ 128 ]. This new biobased packaging can revolutionize the packaging industry worldwide and solve the increasing problem of plastic pollution ( Figure 24 ). For this type of product, mass manufacturing at a low cost would bring commercial success.

Jute-based biodegradable polybag production.
4.4.2. Bioactive Jute for Food Packaging
Due to increasing demand for sustainable food packaging materials, jute fiber was treated with Red Grape Pomace Extract (RGPE) as an activation material [ 129 ]. The RGPE impregnated jute fiber showed antioxidant and antimicrobial properties against a number of microorganisms such as Pseudomonas aeruginosa , Escherichia coli , Staphylococcus aureus indicating its potential as a food packaging material with better preservation capacity. These types of natural reagent-based research need to be flourished for sustainable product development.
4.5. Cotton/Wool Replacement
4.5.1. absorbent cotton for medical disposables and sanitary products.
Owing to the increasing demand for hygiene and wound dressing products, jute can be considered a cheaper replacement option for cotton fiber in disposable absorption products ( Figure 25 ). Through chemical treatment, lower grade jute can be transformed into absorbent cotton which can be further modified to be used as wound healing bandages, sanitary napkins or baby napkins. To develop these types of products, the jute fiber needs to be treated with anti-bacterial and anti-fungal agents. Based on this contemplation, AgNO 3 and Co can be used for increasing their anti- bacterial activity. Therefore, such types of feasibility studies have already been undertaken by certain researchers [ 130 , 131 ]. Sharma et al. [ 132 ] developed disposable pads using waste jute blended with Superabsorbent polymer (SAP) in order to increase water absorbency. Various functional tests demonstrated the potential of jute blended with SAP as sanitary pads at an affordable cost. In a recent survey [ 133 ], it was found that women are inclined to adopt jute-based sanitary pads. Further studies are required to commercialize jute-based absorbent product concepts. Therefore, this is an open research topic for the advanced development of medical appliances.

Jute fiber converted into an absorbent cotton-like product for medical accessories and personal hygiene products.
4.5.2. Jute-Cotton Blending
Recent research shows that blending jute with cotton could produce sustainable textile products. The blended textile has already found applications in durable products like denim and polo knitwear [ 134 ]. In general, chemical modification and bleaching are applied to the jute fiber to make it softer. Research is being carried out on jute-cotton blended textiles to bring certain functional properties by applying different surface treatments for instance atmospheric plasma treatment for improving wicking and dyeability properties whereas chitosan treatment for incorporating antibacterial property [ 135 , 136 ]. Natural fibers like jute can produce less ecological, water and CO 2 footprints [ 137 ], which will have an overall positive environmental impact. Other benefits of jute-cotton blending include reducing dependency on cotton, producing textiles at a lower cost, diversifying the use of jute, contributing to the local economy of the jute-producing countries [ 138 ] and helping in strengthening the already established garment sector in lower-middle-income countries like Bangladesh. The people in western countries are gradually becoming inclined toward using garments made of more sustainable materials. Therefore, a significant growth in jute-cotton blended products is expected in the near future.
4.5.3. Woolenization
The idea of jute fiber woolenization has been explored by converting the jute fiber into wool-like material simply using alkali treatment. It was found that with 15% NaOH treatment, a significant modification in the jute structure was possible to make such transformation [ 139 ]. The effectiveness of this technique was demonstrated by developing commercial prototypes like handbags. Further efforts are needed to identify the market opportunities and to diversify the use of jute in the fashion industry.
4.6. Jute Engineered with Nanomaterials
The lower strength of jute, sensitiveness to moisture and poor interaction with polymer matrix material in composite compared to other synthetic fibers are still some of the weaknesses that hinder the progress towards mass use of jute fiber. Among different strategies, many researchers suggested the functionalization of jute fibers with nanoparticles (NPs) to overcome the challenges. Some examples of NP functionalization of jute fibers are found in the literature.
4.6.1. Graphene
In recent years, a number of studies reported on the functionalization of jute fiber with graphene or graphene-like materials particularly by a research group at the University of Manchester [ 140 , 141 , 142 , 143 , 144 ]. The modified jute fiber and epoxy composite showed improved mechanical properties than other natural composites. Stiffness and tensile strength were improved by ~324% and ~110%, respectively, when compared to the untreated jute fiber composites. This improvement was assigned to various reasons such as individualization of jute fibers, improved fiber packing and new fiber structure within the composites and strong adhesion of the fibers with the matrix. Graphene oxide nanoplatelets (GONPs)-grafted jute fiber was used to develop thermoplastic (polypropylene) based composite [ 145 ]. The results showed significant improvement in mechanical and thermal properties of the composites, which was attributed to effective interlocking between the surface treated jute fiber and the matrix. This type of composite might attract commercial interest in several fields such as automotive, aerospace, architecture, and household products and possesses the potential to substitute the conventional synthetic fiber-based composites such as GFRP or CFRP. Following a similar process of jute fiber functionalization by graphene, the development of composites with other matrix materials can be explored. The nanoengineered jute fiber might find applications, particularly, in electronic devices. Therefore, this will open up a new era of jute research and might attract a renewed interest among the researchers.
4.6.2. Carbon Nanotubes (CNT)
Carbon nanotubes can be deposited on the jute fibers to make them conductive by using the dip-drying method [ 146 ] with the assistance of oxygen plasma. This technique produces uniform and efficient coating strongly attached to the surface of the jute fibers. The coating enhances the crystallinity and mechanical strength of the modified fibers. The functionalization of the jute fiber further improved electrical conductivity, thermal stability and flame retardancy. Therefore, jute fiber functionalized with CNT could open up opportunities to use in smart electrical and electronic devices.
4.6.3. SiO 2 Nanoparticles
Jute fiber and polyamide 11 (PA11)-based novel biodegradable composites were developed by modifying the jute fiber with SiO 2 nanoparticles of approximately 100 nm [ 147 ]. Clear evidence of the nanoparticles attached to the fiber was found. The modification of jute fibers enhanced their tensile strength, Young’s modulus and impact strength by 58.3%, 45.9% and 11.7%, respectively, indicating better stiffness and toughness than the unmodified jute fiber-reinforced composite. Furthermore, significant improvements in thermal stability and water absorption characteristics were also found due to strong interaction and adhesion between the fibers and the matrix surface. Therefore, engineered jute fiber with SiO 2 nanoparticles showed great potential as a biobased composite in real-life applications.
Another study was performed by Araújo et al. [ 148 ], where jute was treated with CaO and SiO 2 nanoparticles in order to embed multifunctional characteristics such as UV protection, hydrophobicity, antibacterial activity and wash durability. The combination of CaO and SiO 2 instead of CaO only showed improvement in incorporating the multifunctional characteristics. The treated fabric might find potential applications in the area of personal protective equipment.
5. Challenges and Potential Future Directions
More recently, jute fiber, its derivatives and associated composites have enjoyed major successes in research and commercially in several application areas. A SWOT (Strength, Weakness, Opportunity, and Threat) analysis of the jute fiber as a technical raw material is presented in Figure 26 . By no means this is a complete list of all strengths, weaknesses, opportunities and threats. It is expected that in the future, the items in strength and opportunity parts will grow whereas the items in weakness and threat parts will decrease. In this section, some of the important challenges of natural fibers [ 149 ], particularly, jute fibers and possible actions that can be considered are briefly discussed.

SWOT analysis of jute fiber and its associated products.
5.1. Inferior Properties of Jute Fiber
Despite having a number of favorable characteristics, the jute fiber is facing a number of challenges to enter into the global market as a preferred biobased sustainable fiber. However, some of the challenges such as lower strength than some natural fibers (e.g., flax), thermal degradation at low temperature, sensitiveness to water absorption and variations in fiber quality and performance needs to be addressed. Fiber modifications with a variety of innovative chemical or physical treatments such as engineering fibers with different nanoparticles would provide some solutions towards improving the functional characteristics of the jute fiber.
5.2. Challenges in Composite Processing
With the traditional composite manufacturing techniques, reliability on the quality of the jute-based composite products still remains a major issue. New composite processing techniques should be developed to obtain high-quality and consistent products with high fiber content with an emphasis on optimizing processing conditions. One option could be changing the traditional granule, sheet or plate forms of matrix to fiber, which can increase the fiber volume ratio within the composite. New technologies need to be developed for ensuring composite quality. While improving the quality of the products, the cost of processing or the product cost per unit product has to be kept minimum. Some attempts have been made to print jute composite by the 3D printing technique, but still, void formation and low fiber content problems must be resolved.
5.3. Issues with Composite Performance
Some of the inherent weaknesses of the jute fiber are also transferred to its associated composites. Jute composites still show poorer strength than the popular synthetic fiber and some natural fiber composites. The issues in the composite are attributed to poor bonding with the matrix. Furthermore, limited fiber volume (20% to 40%) in the composite hinders it from achieving lightweight but strong and greener composites. The idea of hybridization along with fiber surface treatment, which can help in improving the properties of the composites by promoting a strong bonding of the fiber can allow it to compete with other high-performing synthetic-fiber-reinforced composites. Nanoparticle treatment of the fiber can also help in facilitating jute-polymer bonding, which can accommodate high fiber volume within the composites. At the moment, a limited number of biobased and biodegradable polymer matrixes are available. Further research efforts are required in developing new biobased polymer matrixes. The chemicals used in fiber treatment might cause some environmental impacts. Therefore, research in finding feasible natural biobased extracts and natural dyes for fiber treatment needs to be explored. A combination of biobased and biodegradable polymer matrix and jute fiber treated with biobased chemicals or other environmentally friendly but less energy-intensive physical treatments can make a truly green composite.
Water uptake by the composite could cause swelling of jute fiber leads to fiber detachment from the matrix interface and eventually affects the performance. New technologies for waterproof coating could minimize this issue [ 59 ]. Studies are still lacking in assessing the mechanical performance of the composites after physical or thermal aging or long-term performances like creep behavior [ 65 ].
5.4. Lack of Product Diversification
The quantity of jute-related products and their share of the global market still remains small possibly due to inadequate international promotion and lack of product diversification. New ideas need to be generated with target applications for both high-value and mass-consumed products. Although several new ideas for jute-based products such as cotton replacement and nanocomposite development have attracted considerable research interest, the knowledge gained in research needs to be transferred to the industry for commercialization. Extensive marketing efforts are required to present the jute products to international customers and traders such as displaying in international exhibitions like Dubai Expo in 2021–2022. This will attract international entrepreneurs to investing in jute-based product development and create opportunities for new research projects with international collaborators. Countries like Bangladesh and India, which are the major jute exporters, should conduct collaborative research to develop novel ideas to support diversification of the jute products in the international markets. Combined policy development by the jute producing countries can contribute to its widespread use in both local and international markets. It is expected that the emergence of new technologies in fiber and composite processing will support the quality improvement and market development for the diversified jute products.
5.5. Recycling, Biodegradability and Circular Economy Issues
In spite of significant environmental and cost benefits, mismanagement of the end-of-life of natural fiber-reinforced composites raises a lot of concern for the industry possibly due to the fact that a large amount of plastics get incinerated or go into landfills, particularly, thermoset plastics, which cannot be recycled easily. Even it is recycled, the cost of recycling could be higher than the value of the material recovered. Therefore, innovative recycling processes or strategies need to be developed. Biopolymer-based jute composites are subjected to biodegradation rather than extending the composite life either by recycling or reusing or remanufacturing. This area needs special attention for further research. The circular economy approach advocates for transforming waste into resources in a cost-effective manner. The circular economy system should be applied in managing composite end-of-life through effective material recovery and applying new technologies for recycling wide varieties of jute composites. Recycling of industrial waste of jute and polypropylene fibers from the carpet industry showed some promising results [ 150 ]. In order to implement the circular economy paradigm for biobased composites, the life cycle framework has to be considered [ 151 , 152 ]. Assessing the environmental impact and life cycle cost at every stage of the product life cycle would help in making decisions for sustainable product development [ 153 ].
6. Conclusions and Outlook
In this paper, current progress in the research about jute fiber and its associated materials such as fiber-reinforced polymer composites has been reviewed and its future potential for product diversification has been critically analyzed. As a natural fiber, wide variations in microstructural and mechanical properties exist in the jute fiber, yarn or fabric. It is clear that other than traditional applications of jute as mainly a woven packaging material, it has found wide applications from macro to nanoscale particularly as a reinforcing fiber for polymer composite products due to the increasing demand for using sustainable materials.
Composite materials can be developed using combinations of both thermoset and thermoplastic materials with different forms of jute such particles, short fibers, long fibers and woven/nonwoven fabrics. Different types of chemical and physical treatments of the fiber have been developed to improve the compatibility between the fiber and matrix, which can improve the performance of the fiber or associated composites. Combining jute with a biobased polymer matrix made it possible to develop eco-friendly and green composites. Hybridization of jute-based composites by adding other natural fibers or synthetic fibers or particles shows further improvement in performance.
Overall, the jute fiber has the ability to replace environmentally harmful man-made fiber (e.g., glass fiber) and, in the near future, diversified high-value applications of the jute fiber and its derivative nanomaterials in biodegradable packaging, fashion, electronics, medical and energy sector are expected to increase significantly. Hopefully, jute will find its glory again by capturing new markets with the offerings of fashionable and eco-friendly products for the growing number of environment-conscious customers.
Acknowledgments
The authors acknowledge the support from Bangladesh Jute Research Institute, Bangladesh, Manchester Metropolitan University, UK and Bangladesh University of Engineering and Technology, Dhaka, Bangladesh.
Author Contributions
Conceptualization, S.S., J.H., M.M.A.S., A.S.M.S., M.H. and S.U.; methodology, S.S. and J.H. formal analysis, S.S. and J.H.; investigation, S.S., J.H., M.M.A.S., A.S.M.S., M.H. and S.U.; resources, S.S., J.H., M.M.A.S., A.S.M.S., M.H. and S.U.; data curation, S.S., J.H., M.M.A.S., A.S.M.S., M.H. and S.U.; writing—original draft preparation, S.S., J.H.; writing—review and editing, S.S., J.H., M.M.A.S., A.S.M.S., M.H. and S.U.; visualization, S.S. and J.H.; supervision, J.H.; project administration, S.S., J.H., M.M.A.S., A.S.M.S. and M.H. All authors have read and agreed to the published version of the manuscript.
This research received no external funding.
Institutional Review Board Statement
Not applicable.
Informed Consent Statement
Data availability statement, conflicts of interest.
The authors declare no conflict of interest.
Publisher’s Note: MDPI stays neutral with regard to jurisdictional claims in published maps and institutional affiliations.
Natural and Synthetic Fibres and Their Properties
Natural fibres, introduction.
Different fibres have a number of differentiating characteristics, in terms of their properties, which are sometimes similar to each other (Cook 1984). For the purpose of quality development in textiles and fibres, there is a need to study and analyze these properties, as well as comparing them. In addition, there is a need to analyse the properties of these materials, so as to meet the environmental safety requirements. Such environmental requirements include the negative impacts of the manufacturing processes of the fibres, on the environment. The most common fibres currently used in the world, are natural fibres, such as cotton, bamboo and hemp, which are found in most parts of the world (Humphries 2004).
Properties of cellulose fibres
Cotton fibre.
Due to the high quality of the cotton and its characteristics, it has the desirable properties, which include softness, high absorbent and static resistance. In addition, it has other good properties, which make it a good fibre material, which can be used in a number of industrial processes to manufacture quality textiles. These qualities include its ability to maintain its quality when it has been dried. It is also easy to wash the cotton textile material, and it can withstand thermal washing, as well as dry cleaning, in environments with thermal conditions (Waite 2009).
Bamboo fibre
Bamboo fibres, on the other hand, have a number of characteristics, which make them a good option. These properties include its smooth and cool texture for handling, which makes it an equal option as an alternative for cotton. Also, bamboo has an excellent wear comfort property, which makes it special to use. These properties are attributed to the fact that the bamboo fibre, comes from the cellulose, which has been made from bamboo plant pulp. The advantage of using bamboo fibre is that it does not hold any chemical additives, and it has other properties that make it a better material to use (Robyn 2003).
Hemp fibres are more resistant to alkalis than Bamboo. Also, hemp fibres do not favour micro-organisms, which can be attributed to the ability of these fibres, to absorb more water. This property of high absorbance discourages odours, as well as life sustainability of microorganisms (Abu-Rous, Ingolic & Schuster 2006). Hemp can be used for producing soft, lustrous, and cool fabric.
Comparing the performance characteristics between Cotton, Bamboo and Hemp
Major properties that need comparison amongst these fibres include structure, length, fineness and way of handling. To start with, the cotton fibre is short and stable, usually with an average of 50mm. Also, the cotton fibre is stiff and hard. On the contrary, the bamboo fibre is a regenerated cellulose fibre, made from bamboo pulp. Bamboo fibre has a variety of lengths, ranging from the longest of 80-90mm, and the shortest of about 30-40mm. In addition, bamboo fibre has a smooth surface. Moreover, bamboo fibre has a round shape and a high whiteness and thinness level, as compared to cotton and hemp. Unlike cotton, the bamboo fibre has a softer touch, silky look, and a breathable feeling (Liese 2001; Barber 1992).
Cotton, bamboo and hemp, have different effects in acids, sunlight, alkalis and micro-organisms. In alkalis, cotton has higher resistance than hemp, but hemp, can with some alkaline environment less than PH 14, lead to the destruction of the fibre. Bamboo can be affected by it. In sunlight, cotton and hemp have good resistance, compared to the poor reaction of bamboo to direct sunlight. On the other hand, if cotton is attacked by acid fumes, there are high chances that the material will get damaged quickly. Hemp can be damaged easily by strong acids, like cotton. On the contrary, Bamboo has a higher resistance to the acidic fumes than Hemp and cotton.
Hemp is fairly resistant to micro-organisms attacks, compared to cotton, but in watery environments, the fibre gives poor environments, that favour micro-organism’s survival. This is due to the fact that when the hemp fibre has high water content, it does not support micro-organism growth, since it does not have odour formation. The manufacturing process for these materials are different, thus the price for production for all the materials is different, in that cotton production is cheaper than that of bamboo and hemp.
Although these materials have a number of differences, there are some similarities which make the materials comparable as alternatives to cotton. All the materials have good quality in strength, but bamboo and hemp are stronger. Hemp fibres can withstand high temperatures. Cotton fibre based textile materials have good thermal properties, while bamboo has good ironing properties, which make the materials an equal alternative to cotton fibres. In terms of thermal properties, cotton is a good conductor of heat (Barber 1994).
Performance and characteristics for approval end use
In most cases, the most preferable fibre material for the manufacture of tops and T-shirts is Cotton fibre. This is attributable to a number of performance characteristics that are in these fibre-based fabrics. These characteristics that make the material suitable include easy to machine wash, dyes well, and have medium strength.
In addition, cotton-based fibre T-shirts and Tops can absorb moisture when worn. Lastly, naturally coloured cotton-based fibre T-shirts and Tops, are unique and they are different from white cotton, hence they do not require dying. With the advance in technology and price comparison, other materials such as hemp and bamboo based fibres have been to manufacture T-shirts and Tops that have the same performance characteristics as the cotton.
In essence, hemp, when used in the manufacture of T-shirts and Tops, it has warmth and softness, which makes it comparable to other materials. These performance characteristics that make it better for the manufacture of T-shirts and Tops, include material property to allow aeration to the body and softness. Hemp has natural softness and strength, which makes it a better blend with the cotton to manufacture a new design with more desirable characteristics. This characteristic makes hemp an option for use in T-shirts, other than cotton based textiles.
Naturally, bamboo fabrics are resistant to odour and bacteria, which makes bamboo-based T-shirts better to wear. In addition, bamboo textile-based fabrics, that is, the T-shirts and Tops, are absorbent, porous, and breathable. Therefore, due to these performance characteristics as well as the strength of the bamboo fibres, fabrics made of bamboo fibre are generally strong and durable; this makes it a replacement material for cotton fibre material.
Environmental consideration for fibres
In agricultural conditions, cotton plant destroys the ecology when planted. This is due to the reason that for proper maintenance of cotton plantations, proper chemicals must be used to control pests and diseases since this plant is chemical dependant. Therefore, most farmers use different types of chemicals, which have a negative impact on the soil, as well as the environment. The only alternative that the cottoning can apply, is the use of organic farming, which helps in protecting the environment, as well as promoting environmental health and improving the general bio-enhancement. Bamboo and hemp are environmentally friendly, thus they promote the ecological-economic relationship.
This is because of the sustainability of these materials. The hemp fibre has cellulose, which is equivalent to that of cotton, and has nontoxic processing since it has methyl morpholine chemicals that are safe to humans. Almost, 96% of the chemicals in the hemp fibre material, are captured and recycled before being released to the ambient, with less harm to the ambient.
It is clear to note that, although cotton fibre materials have high absorbent, comfortable touch, static resistance, as well as a cool, soft and comfortable feel on hands, bamboo fibre has many excellent properties. These excellent properties favour the production processes. On the other hand, hemp fibre has almost equal properties, that equate to those of cotton, which include good absorbent characteristics, soft and very strong, when wet or dry. Lastly, it is clear to note that all the above fibres are cellulose-based fibres, and thus they are environmentally friendly.
Synthetic Fibres
Basically, polyester fibre is a stable fibre, which has good handling properties, due to its smooth touch in hands. In addition, this fibre has a good lustre, which makes it good for handling. On the other hand, olefin has poor thermal properties, as well as having high crystal properties. This can lead to lower texture of the material and high flammability, making it vulnerable to burning and melting like wax. On the contrary, acrylic materials differ from polyester, in that they have a smooth surface, which is soft lustre, silky and warm in touch.
Comparing the performance characteristics between Polyester, Olefin and Acrylic
The three fibres have a number of differences, which makes them to have a preferable taste from different users. These differences include reaction to thermal properties, melting, and crystallization, ironing and burning. Polyester fibres are materials with good thermal insulating properties, but they can burn when ignited and during warm ironing. Unlike polyester, olefin has low melting and crystallization point, so, during ironing, low temperature is ideal. On the other hand, acrylic fibre has the best thermal property, as compared to polyester and olefin, and thus, it has good ironing properties without burning easily.
Maintenance characteristics for these fibres, need a consideration of a number of factors, which include bleaching and reaction, when exposed to sunlight. Polyester fibres bleaching characteristics are different from those of acrylic, which bleaches easily. On the other hand, olefin can bleach easily. While acrylic do not normally require bleaching. In addition, when exposed to sunlight, polyester has a good resistance to sunlight, and thus its usage in sunlight is safe. For the olefin to survive in sunlight, it needs stabilizers to be added in the production process, to ensure that they do not have problem in relation to the sunlight. Acrylic is much similar to these two (polyester and olefin), in that, acrylic are the most resistant to day sunlight exposure.
Focusing on the use of polyester and its performance in sports such as athletics, its fibre based material has taken a big trend as an active sportswear, due to a number of performance characteristics. These include the fact that athletes wear and sportswear made of this material fibre, dry faster. This is because of the wicking characteristics of the material, which enable transportation to the fabric’s surface, thus cooling the wearer.
The acrylic fibre has high performance, based on the fact that, its performance has taken an apparel performance in the sports and athletics world. These applications in sports are attributable to Acrylic’s moisture control, shape retention, and elasticity. In sports, the acrylic fibre absorbs moisture from the wearer’s skin to the surface, making the wearer confortable. Other characteristics that make acrylic suitable for sports include excellent colour, quick drying time, luxurious touch and drape warmth, which makes it to have resistance to extra weathering and maintain shape, stain resistance, resistance to shrinking and wrinkle, oils, fungus and mildew.
The greatest environmental concern currently pressuring the textile industry is in terms of safety and pollution. In essence, production of these materials has negative impacts on the ambient, which include air pollution and soil degradation, due to acid rain. The major challenge that faces the production of this material in the industry, is the idea of green economy, and this has greater depth, in the production processes. The only way to cub the environmental degradation, is through safe manufacturing processes, that involve recycling as well as use of green and clean energy sources in production.
Olefin fibre has 10-50% rate of biodegradation in the environment. The use of olefin has a number of great advantages, which makes it a good material. Olefin has not reached its peak in use in the modern world, therefore, olefin use and distribution in the market is greatly increasing. Amongst the number of end uses for olefin, include home furnishing uses, such as making carpets, upholstery, making carpet cleaner bags, making house wraps; automotive uses such as making hammered vehicle door panels, design of car interior; recreational uses such as furnishings of boats; and industrial uses, such as making geotextiles, ropes, bags, courier envelopes and non-woven fabrics.
Acrylic fibre contains at least 85% of acrylonitrile. It is a man-made wool, since it contains a fibre that makes people feel good. Acrylic fibre has a number of advantages, which include resistance to static electricity, mildew, staining, sun damage and moisture, as well as durability in high traffic areas. Use of acrylic materials in the environment, has no negative impacts. In that sense, it is highly biodegradable, compared to other materials mentioned in this discussion (Kadolph 2007).
Synthesized polymers are the main materials in polyester manufacturing. Due to its origin as a synthesized material, polyester has a number of properties, which makes it ideal to use in many textile applications. These properties include quick drying, resilience to the environment, easy to wash, and resistance to biological damage. However, polyester fibre material is highly flammable. Therefore, a lot of care is necessary, when planning to use polyester, as most of the synthetic fibre based textile materials, are highly flammable.
Olefin, gives comfort when worn, due to its quick recovery from wrinkles. Other properties of olefin material include good chemical resistance, to both acids and alkalis, as well as high resistance to abrasion. Lastly, acrylic fibre based textile materials are soft, warm, and have a silky touch on the skin.
Abu-Rous, M, Ingolic, E & Schuster, K C 2006, “Visualisation Of The Nano-Structure Of Tencel,” Lenzinger Berichte , 31, pp. 37- 85.
Barber, E 1992, Prehistoric Textiles: The Development of Cloth in the Neolithic and Bronze Ages with Special Reference to the Aegean , Princeton University Press, New Jersey.
Barber, E 1994, Prehistoric Textiles: The Development of Cloth in the Neolithic and Bronze Ages with Special Reference to the Aegean , Princeton University Press, New Jersey.
Cook, J G 1984, Handbook of textile fibres; Natural Fibres, Woodhead Publishing, Cambridge.
Humphries, M 2004, Fabric Reference, Pearson/Prentice Hall, Upper Saddle River.
Kadolph, J 2007, Textile , Upper Saddle River, New Jersey.
Liese, M P 2001, “Resisting Reproduction: Reconsidering Slave Contraception in the Old South,” Journal of American Studies , 35 (2), pp. 255–274.
Robyn, J M 2003, Textiles of Southeast Asia: tradition, trade and transformation , Tuttle Publishing, London.
Waite, M 2009, “Sustainable Textile: the role of Bamboo and a Comparison of Bamboo Textile Properties,” Journal of Textile and Apparel,Technology and Management, 2 (4), pp. 34-35.
Cite this paper
- Chicago (N-B)
- Chicago (A-D)
StudyCorgi. (2021, February 10). Natural and Synthetic Fibres and Their Properties. https://studycorgi.com/natural-and-synthetic-fibres-and-their-properties/
"Natural and Synthetic Fibres and Their Properties." StudyCorgi , 10 Feb. 2021, studycorgi.com/natural-and-synthetic-fibres-and-their-properties/.
StudyCorgi . (2021) 'Natural and Synthetic Fibres and Their Properties'. 10 February.
1. StudyCorgi . "Natural and Synthetic Fibres and Their Properties." February 10, 2021. https://studycorgi.com/natural-and-synthetic-fibres-and-their-properties/.
Bibliography
StudyCorgi . "Natural and Synthetic Fibres and Their Properties." February 10, 2021. https://studycorgi.com/natural-and-synthetic-fibres-and-their-properties/.
StudyCorgi . 2021. "Natural and Synthetic Fibres and Their Properties." February 10, 2021. https://studycorgi.com/natural-and-synthetic-fibres-and-their-properties/.
This paper, “Natural and Synthetic Fibres and Their Properties”, was written and voluntary submitted to our free essay database by a straight-A student. Please ensure you properly reference the paper if you're using it to write your assignment.
Before publication, the StudyCorgi editorial team proofread and checked the paper to make sure it meets the highest standards in terms of grammar, punctuation, style, fact accuracy, copyright issues, and inclusive language. Last updated: February 10, 2021 .
If you are the author of this paper and no longer wish to have it published on StudyCorgi, request the removal . Please use the “ Donate your paper ” form to submit an essay.

- Jun 16, 2023
Natural Fibers: The Journey from Farm to Fabric
Natural fibres play a significant role in the textile industry, offering a sustainable and versatile fabric option. but have you ever wondered about the journey of these fibres, from their origins on farms to becoming the fabrics we love to wear in this blog post, we will explore the fascinating journey of natural fibres, shedding light on their cultivation, harvesting, processing, and transformation into the fabrics that adorn our lives..
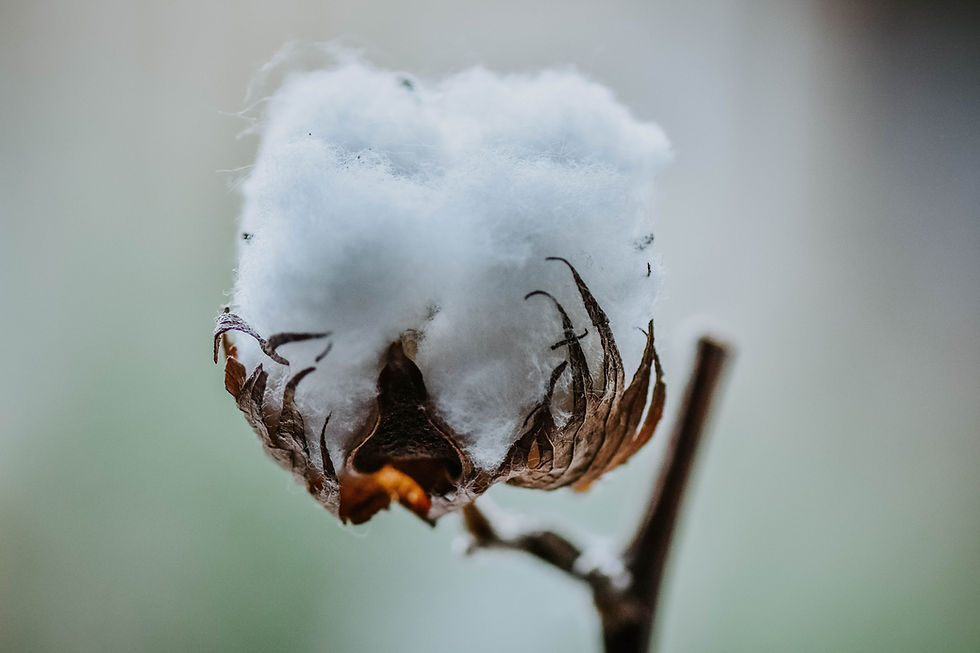
Nature's bounty unfolds, weaving a tapestry of fibers from farm to fabric, showcasing the beauty and sustainability of our interconnected world.
Cultivation and Harvesting
Natural fibres come from various sources, including plants and animals. Cotton, for example, is cultivated through careful farming practices, while silk is derived from the cocoons of silkworms. Explore the diverse methods of growing and harvesting natural fibres, understanding each fibre type's unique characteristics and requirements.
Fibre Extraction and Processing
Once harvested, the fibres undergo extraction and processing to prepare them for textile production. The raw fibres must be separated from the plant material for plant fibres like cotton or flax. Animal fibres like wool or silk undergo shearing, washing, and further processing to obtain usable fibres. Learn about the techniques and machinery involved in these processes.
Spinning and Yarn Production
Spinning is transforming fibres into yarns. Discover the different spinning techniques employed, such as ring spinning or open-end spinning, which determine the characteristics of the resulting yarn. Explore the creation of different types of yarn, including single-ply, multi-ply, and blended yarns, each offering unique qualities for fabric production.
Fabric Weaving and Knitting
The spun yarns are woven or knitted to create fabrics. Learn about weaving, where threads are interlaced to form a stable fabric structure. Explore various weaving patterns and loom types, including traditional handlooms and modern automated looms. Additionally, I understand the art of knitting, where yarns are looped together to create fabric.
Finishing and Textile Treatments
After weaving or knitting, fabrics undergo finishing processes to enhance their characteristics and aesthetics. This may involve treatments like bleaching, dyeing, printing, or adding unique texture or water resistance finishes. Discover the vast array of finishing techniques employed in the textile industry to create the desired properties and visual appeal.
Sustainable Practices and Innovations
Delve into sustainable practices and innovations within the natural fibre industry. Explore organic farming methods, fair trade initiatives, and efforts to reduce environmental impacts. Learn about advancements in fibre processing technologies, such as water-saving techniques and natural dyeing methods, that contribute to a more sustainable and eco-friendly journey of natural fibres.
Understanding the journey of natural fibres, from farm to fabric, provides a deeper appreciation for the craftsmanship and processes involved in creating the textiles we use daily. Each step contributes to the rich and diverse world of natural fibre fabrics, from cultivation and harvesting to spinning, weaving, and finishing. Embrace the beauty and sustainability of natural fibres, and recognize the efforts of farmers, artisans, and innovators who bring these fibres to life.
(Note: This blog post provides an overview of the journey of natural fibres and may not cover all specific fibre types or processes. Further exploration and research are encouraged to delve deeper into individual fibres and their unique characteristics.)
- Fabric Manufacturing
- Global Textile Industry
Related Posts
The Future of the Fabric Industry
Exploring Different Types of Looms
- Switch skin

Advantages and Disadvantages of Natural and Manmade Fibres

A. Advantages and Disadvantages of Natural Fibre
I. advantages of natural fibre.
- Comfortable: Clothes made by natural fibres are more comfortable than those made of synthetic fibres.
- Environment: Producing materials from natural fibres are less harmful to our environment.
- Non allergic to skin
ii. Disadvantages of Natural Fibre
- Expensive: Materials produced by natural fibres are generally expensive as synthetic fibres can be made easily by manufacturing.
- Shrink: Natural fibres might shrink due to aggressive washing.
- Unlike manmade fibres, natural fibres are not available in high tenacity (HT) and medium tenacity (MT).
- Natural fibres do not possess a high degree of resiliency as compared to manmade fibres, hence the fabrics made out of them do get wrinkles from ‘baggy knees’, possess less crease recovery.
- Production of natural fibres cannot be completely controllable. Therefore, from year to year quantities of specific qualities vary and this tends to cause price fluctuations according to variations in demand which cannot be foreseen until the fibres have been produced.
- Variation in length, fineness, etc. of the natural fibre causes less regular and uniform yarn than that obtained from manmade fibres.
- The availability of natural fibres is affected by natural calamities and vagaries of nature.
- The production of natural fibres involves the use of land which is also required for growing the agriproducts. With the availability of limited amount of land on the surface of the earth, the demand for land for food and housing on one hand and that for the growth of natural fibres on the other is to be balanced.
B. Advantages and Disadvantages of Synthetic Fibre
I. advantages of synthetic fibre.
- Strong: Synthetic fibres are strong so they can take up heavy things easily.
- Retain their original shape: Synthetic fibres retain their original shape so it’s easy to wash and wear.
- Elastic: Can easily be stretched out.
- Soft: Synthetic fibres are generally soft so they are used in clothing materials.
- Colour: Varieties of colours are available as they are manufactured.
- Cost: Clothes made by synthetic fibres are generally cheaper than those made by natural fibres.
- Specific qualities of fibres can be produced deliberately and quickly in accordance with the demand.
- The filaments can be produced as fine or as coarse as required, staple lengths can be cut exactly to order. Fibres can be produced with a high degree of lustre, with reduced or completely dull lustre, as required.
- Unlike natural fibres, the final product of manmade fibres does not require cleaning.
- Most of the fibres are pure white or colourless when produced, but if necessary, colour can be incorporated during the production of the manmade fibres.
- The growth and utility of manmade fibres are mainly influenced by its positive qualities, viz. wrinkle resistance, crease recovery, easy care properties, etc. Manmade fibre fabrics bring out substantial saving on laundry costs; unlike cotton, it can be washed in a basin in the evening, hung up to dry and be worn without ironing the following morning.
- The light weight characteristic of manmade fibre fabrics gives more mobility because of less weight and quantity—a tourist can take along with, him a few clothes. Hence, these fibres are referred to as Easy-Care fibre fabrics.
- Most of the synthetic fibres possess high resistance to moth, mildew, insects, mould, which simplify the storage problems, the economy of little loss from these causes.
ii. Disadvantages of Synthetic Fibre
- Does not absorb moistures: Synthetic fibres do not absorb sweat, trapping heat in our body.
- Rough feel: Synthetic fibres may give the rough feel, making it unsuitable for pyjamas, underwear, etc.
- Some individuals are often prone to skin allergy, because of the dermatological action of manmade fibres. This puts a restriction on its use (such problems do not arise in the case of natural fibres).
- In general, the manmade fibres are generally hydrophobic in nature; this is necessarily a disadvantage when their products have to be worn next to the skin.
- These fabrics fail to absorb the perspiration ; thus the wearer feels discomfort in a hot climate.
- Manmade fibre fabrics are a little difficult to sew. Seams do not hold tight as in natural fibre fabrics. So, stitching charges were higher. But this is compensated for by durability and wash and wear properties.
What is Perspiration Fastness? | Perspiration Test for Textile
How to write abstract | guidelines for writing abstract, related articles, morphological structure of cotton fibre, polynosics fibres.

Characteristics/Requirements of Fibre Forming Polymers
Cotton fibre morphology.
- Cultivation of Cotton July 14, 2017
- Spinning Process of Filament Yarns | Melt spinning | Dry spinning | Wet spinning July 8, 2017
Adblock Detected
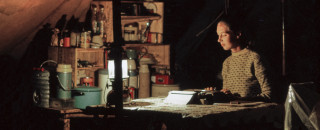
Each evening in her tent, researcher Jane Goodall would write up data from her field notebooks, recounting the chimpanzee behavior she observed that day. Immerse yourself in a replica of Jane’s research camp at “Becoming Jane: The Evolution of Dr. Jane Goodall,” an exhibition organized by National Geographic and the Jane Goodall Institute. The exhibition is open at the Natural History Museum of Utah in Salt Lake City, UT from December 7, 2023 through May 27, 2024. Photo by Hugo Van Lawick, Jane Goodall Institute
Murray 7th Grade Student Wins Opportunity to Meet Dr. Jane Goodall
Lily Peterson was selected as the winner of the “Inspired by Jane” Essay Contest
SALT LAKE CITY, April 1, 2023 – On March 30, Lily Peterson, a Mountain Heights Academy 7th grader from Murray, Utah, was ushered backstage to meet her inspiration, the world-renowned Dr. Jane Goodall, DBE founder of the Jane Goodall Institute and UN Messenger of Peace. In the meeting, Peterson presented an issue she hopes to address in Utah, and Peterson then wished Goodall a happy 90 th birthday on April 3. This rare opportunity came about after the Utah student won an essay contest hosted by the Natural History Museum of Utah and its partners, the Jane Goodall Institute and my529 Utah’s Educational Savings Plan ,
As the winner of NHMU’s "Inspired by Jane" Essay Contest, Peterson’s essay, which highlights challenges faced by wild mustangs in the Mountain West, rose to the top of more than 280 submissions from 6th, 7th, and 8th graders in Utah who were asked to respond to the writing prompt: “Knowing all that Dr. Jane Goodall as accomplished in her life so far. tell us what positive impact you hope to make in the world by your 90th birthday.”
“The Natural History Museum of Utah congratulates Lily Peterson for her outstanding accomplishment and wishes her continued success in her academic and professional endeavors,” said Dr. Jason Cryan, The Sarah B. George Executive Director of NHMU. “Lily's passion and determination serve as an inspiration to her peers and the whole community, reminding us all of the power of youth in making a difference.”
Peterson’s winning essay showcases her passion for veterinary science and her commitment to advocating for the well-being of mustangs in and around Utah. Her dedication is evident in her completion of an online class in equine welfare and management with UC Davis, a remarkable achievement for a student of her age. Peterson’s achievement in winning the "Inspired by Jane" Essay Contest is a testament to her exceptional talent in writing and critical thinking.
“Being given the opportunity to meet Dr. Jane Goodall has been an incredible experience,” said Peterson. “I admire her because of all she has done as a scientist, conservationist, and activist. As an animal lover I am thankful that she has proven that animals have feelings and emotions too. I loved being able to talk with her one on one about her own childhood experience with horses. It was so special to meet someone who worked so hard to make their own big childhood dreams come true. It is a moment I will never forget, and for which I am very thankful.”
For her first-place prize, Lily traveled to Seattle, WA, on an all-expenses-paid trip to attend Goodall’s public lecture on March 30 and meet her after the event. In addition to this once-in-a-lifetime experience, Lily will also receive a $1,000 college savings certificate provided by my529, empowering her to continue her educational journey. my529 Utah’s Educational Savings Plan is designed to assist families, friends, and individuals in investing for a beneficiary’s future higher education.
Goodall’s legacy in the fields of science and conservation are celebrated in Becoming Jane: The Evolution of Dr. Jane Goodall , a special exhibition open at the Natural History Museum of Utah until May 27, 2024. As featured in the exhibition, Goodall is now as famous for her work inspiring hope and action among the youth of the world, as she is for her groundbreaking research of wild chimpanzees.
As the world wishes Goodall a 90 th birthday on April 3, NHMU is happy to celebrate her ongoing inspiration on the youth of the world, like Peterson and her own vision for change.
Becoming Jane is free with the cost of admission to the Museum and always free to members. For tickets and more information about Becoming Jane , please visit: nhmu.utah.edu/jane.
About the Natural History Museum of Utah
The Natural History Museum of Utah is one of the leading scientific research and cultural institutions in the country. Established in 1963, the museum’s 10 permanent exhibitions are anchored by its state-of-the-art collections and research facilities containing almost 2 million objects. These collections are used in studies on geological, biological, and cultural diversity, and the history of living systems and human cultures within the Utah region. The museum hosts approximately 300,000 general visitors a year and provides one of the most spectacular private event settings in the Salt Lake City area. NHMU also broadens the reach of its mission through a variety of science-based outreach programs to communities and schools throughout Utah, reaching every school district in the state every other year.
Download Media
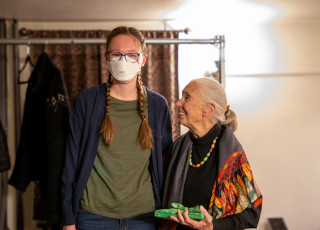
Lily Peterson and Dr. Jane Goodall Eliza Petersen
Lily Peterson's Winning Essay Lily Peterson
Press contacts and links
Press Contact
Margaret Chamberlain
Public Relations
Press Links
- Learn more about the Jane Goodall Institute
- Learn more about my529 Utah's Educational Savings Plan
- Read the winning essay
Related Press Releases
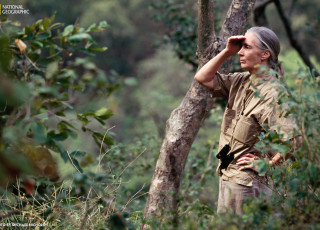
Anthropology
NHMU to Open “Becoming Jane” an Immersive Multimedia Exhibition on the Legacy of Dr. Jane Goodall
Becoming Jane: The Evolution of Jane Goodall is open at NHMU from December 7, 2023 - May 27, 2024 celebrating Dr. Goodall's legacy of science and conservation.
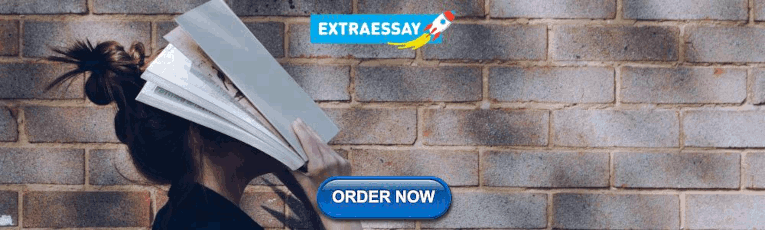
IMAGES
VIDEO
COMMENTS
natural fibre, any hairlike raw material directly obtainable from an animal, vegetable, or mineral source and convertible into nonwoven fabrics such as felt or paper or, after spinning into yarns, into woven cloth. A natural fibre may be further defined as an agglomeration of cells in which the diameter is negligible in comparison with the length. . Although nature abounds in fibrous materials ...
1. Introduction. Scientists, researchers, and practitioners around the world have recently been working to maximize the potential of natural fibers to create the most sustainable, biodegradable, and high-quality natural fiber products [1,2,3].Natural fibers, which are renewable and ecologically acceptable sources of raw materials for producing environmentally friendly products, have played a ...
ISSN:2581-4915. 1. A Review On Natural Fiber And Its Char acteristics. A Mani Kandan 1 and Prof. S Rajakumar 2. 1 PG Scholar, Department of Mechanical Engineering, Anna University Regional Campus ...
Natural fibres with their long history of serving mankind are very important in a wide range of applications, and they compete and coexist in the 21st century with man-made fibres, especially as ...
Fibre is a long, thin strand or thread of material made by weaving or knitting threads together. Fibre is a hair like strand of material. A fibre is the smallest visible unit of any textile product. Fibres are flexible and may be spun into yarn and made into fabric. Natural fibres are taken from animals, vegetables or mineral sources.
Natural fibers or natural fibres (see spelling differences) are fibers that are produced by geological processes, or from the bodies of plants or animals. They can be used as a component of composite materials, where the orientation of fibers impacts the properties. Natural fibers can also be matted into sheets to make paper or felt.. The earliest evidence of humans using fibers is the ...
Fig. 1 presents a general configuration of a natural fiber structure and its microstructural organization covering the three main structural components, i.e. the cellulose, hemicellulose and lignin (Kabir, Wang, Lau, & Cardona, 2012; Rong, Zhang, Liu, Yang, & Zeng, 2001).The plant fiber consists of a primary cell at the peripheral and three secondary walls at the interior and a lumen in the ...
Asian countries have abundant resources of natural fibers, but unfortunately, they have not been optimally utilized. The facts showed that from 2014 to 2020, there was a shortfall in meeting national demand of over USD 2.75 million per year. Therefore, in order to develop the utilization and improve the economic potential as well as the sustainability of natural fibers, a comprehensive review ...
Aloe vera, banana, sisal, hemp, jute, bamboo, milk fibre, corn, soya, groundnut shell, arecanut, coffee bean waste, lyocell and eucalyptus were few among them. Each year, more synthetic fibres and ...
3 Fiber preference scale from 0 to 2, where values below 1 indicate avoidance, 1 is for no opinion and values above 1 indicate a preference of the specific fiber. 4 Combined fiber preference scale 0 = synthetic, 2 = no opinion, 4 = natural. 5 Fiber sustainability scale: 1 = no environmental impact, 5 = very large impact.
The potential role of natural textile fibres like cotton and wool, as an environmental pollutant, has been speculated on by some environmental scientists, but there has been a general consensus ...
The increase in awareness of the damage caused by synthetic materials on the environment has led to the development of eco-friendly materials. The researchers have shown a lot of interest in developing such materials which can replace the synthetic materials. As a result, there is an increase in demand for commercial use of the natural fiber-based composites in recent years for various ...
The plant's almost insatiable thirst means that it takes just shy of 5,300 gallons of water to produce about 2 pounds of cotton. Furthermore, the production of one cotton T-shirt requires a ...
Figure 1. Trend of research on jute plant and fiber. Jute plants grow in grassy soil, requiring 125-150 mm of rainfall per month, mild to moderate temperatures (20-40 °C) and high relative humidity (70-80%) for the best growth. Jute is a bast fiber and grown in plantations, where it is collected once the plant matures.
Bamboo fibre. Bamboo fibres, on the other hand, have a number of characteristics, which make them a good option. These properties include its smooth and cool texture for handling, which makes it an equal option as an alternative for cotton. Also, bamboo has an excellent wear comfort property, which makes it special to use.
Conclusion. Understanding the journey of natural fibres, from farm to fabric, provides a deeper appreciation for the craftsmanship and processes involved in creating the textiles we use daily. Each step contributes to the rich and diverse world of natural fibre fabrics, from cultivation and harvesting to spinning, weaving, and finishing.
This research aims to analyze the environmental impact of six fibers in the textile industry: conventional and organic cotton, silk, jute, flax, and polyester. The study used a life cycle assessment (LCA) methodology with a cradle-to-gate system boundary and analyzed the stages of agriculture, spinning, weaving, and dyeing. In agriculture production, five impact categories (i.e., fossil ...
Environment: Producing materials from natural fibres are less harmful to our environment. Non allergic to skin. ii. Disadvantages of Natural Fibre. Expensive: Materials produced by natural fibres are generally expensive as synthetic fibres can be made easily by manufacturing. Shrink: Natural fibres might shrink due to aggressive washing.
Wool is different to other fibres because of its chemical structure. This chemical structure influences its texture, elasticity, staple and crimp formation. Wool is a protein fibre, composed of more than 20 amino acids. These amino acids form protein polymers. Wool also contains small amounts of fat, calcium and sodium.
Essay On Carbon Fiber 657 Words | 2 Pages. There have been many means and methods in the past decade, fostered to ensure that the construction of buildings, complexes and many enormous structures are made with energy saving measures such as heat dispersal during the summer, and to also ensure the promotion of environmental sustainability such as the control of carbon emissions and greenhouse ...
Cashmere is a natural fibre and comes from the fine hairs of the Changthangi goat's underbelly. Being a natural material, Cashmere is biodegradable. Hence, it can decompose naturally without leaving harmful residues. This contrasts with synthetic materials which contribute to environmental pollution and persist in landfills for extended periods.
Natural fibres are those which originate from plant, animal and mineral sources. Natural fibres can be classified as following: (a) Animal fibre (b) Mineral fibre (c) Plant fibre Animal Fibre Animal fibre are made up of protiens such as silk, wool, cashmere etc. 1. Animal hair (wool or hair): Fibre extracted from animals or hairy mammals . E.g.
Lily Peterson was selected as the winner of the "Inspired by Jane" Essay Contest. SALT LAKE CITY, April 1, 2023 - On March 30, Lily Peterson, a Mountain Heights Academy 7th grader from Murray, Utah, was ushered backstage to meet her inspiration, the world-renowned Dr. Jane Goodall, DBE founder of the Jane Goodall Institute and UN ...
SHARE. In compliance with the Open Meetings Law, the Natural Fiber Textile Development Workgroup gives notice that it will conduct a meeting on April 8, 2024 at 1:00 pm. The public has the right to attend the meeting at any location included herein. All reasonable efforts will be made to ensure the meeting is held in a facility that permits ...