
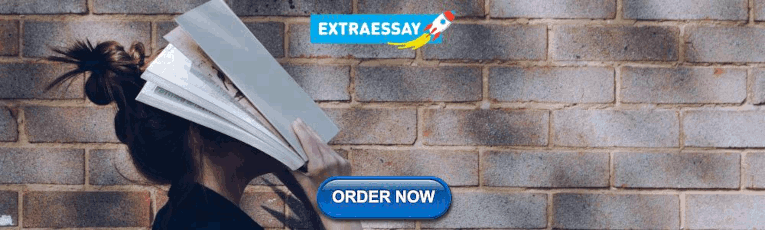
Understanding the Occupational Health and Safety Act - OHS Act

The Occupational Health and Safety Act (The OHS Act) was written in the interest of workers in South Africa. Understand your rights by reading our summary of the OHS Act here.
Who does the Occupational Health and Safety Act Protect? This guide was written in the interest of the health and safety of workers in South Africa. It is not intended as a substitute for the Occupational Health and Safety Act, 1993. It is intended to explain the Act in simple, non-legal terms to all the role players in the South African occupational health and safety field. What does the act entail? The Occupational Health and Safety Act, 1993, requires the employer to bring about and maintain, as far as reasonably practicable, a work environment that is safe and without risk to the health of the workers. This means that the employer must ensure that the workplace is free of hazardous substances, such as benzene, chlorine and micro organisms, articles, equipment, processes, etc. that may cause injury, damage or disease. Where this is not possible, the employer must inform workers of these dangers, how they may be prevented, and how to work safely, and provide other protective measures for a safe workplace. Does the employee have any say in the matter? The Act is based on the principle that dangers in the workplace must be addressed by communication and cooperation between the workers and the employer. The workers and the employer must share the responsibility for health and safety in the workplace. Both parties must pro-actively identify dangers and develop control measures to make the workplace safe. In this way, the employer and the workers are involved in a system where health and safety representatives may inspect the workplace regularly and then report to a health and safety committee, who in turn may submit recommendations to the employer. What is a Safety Inspection? Inspections are usually planned on the basis of accident statistics, the presence of hazardous substances, such as the use of benzene in laundries, or the use of dangerous machinery in the workplace. Unplanned inspections, on the other hand, usually arise from requests or complaints by workers, employers, or members of the public. These complaints or requests are treated confidentially. What power do safety inspectors have? If an inspector finds dangerous or adverse conditions at the workplace, they may issue the employer with a prohibition notice (prohibit a particular action, process, or the use of a machine or equipment), a contravention notice (immediate prosecution, but in the case of a contravention of a regulation, the employer may be given the opportunity to correct the contravention within a time limit specified in the notice which is usually 60 days), or an improvement notice (require the employer to bring about more effective measures). The inspector may also enter any workplace or premises where machinery or hazardous substances are being used and question or serve a summons on persons to appear before them. The inspector may request that any documents be submitted, investigate and make copies of the documents, and demand an explanation about any entries in such documents. The inspector may also inspect any condition or article and take samples of it, and seize any article that may serve as evidence. What must the employer do to ensure that the work environment is safe and without risk to the health of his or her workers? The employer must provide and maintain all the equipment that is necessary to do the work, and all the systems according to which work must be done, in a condition that will not affect the health and safety of workers. Before personal protective equipment may be used, the employer must first try to remove or reduce any danger to the health and safety of his workers. Only when this is not practicable, should personal protective equipment be used. The employer must take measures to protect his or her workers health and safety against hazards that may result from the production, processing, use, handling, storage or transportation of articles or substances, in other words, anything that workers may come into contact with at work. To ensure that these duties are complied with, the employer must: Identify potential hazards. Establish the precautionary measures. Provide the necessary information, instructions, training and supervision Not permit anyone to carry on with any task unless the necessary precautionary measures have been taken. Take steps to ensure that every person under his or her control complies with the requirements of the Act. Enforce the necessary control measures in the interest of health and safety. See to it that the work being done and the equipment used, is under the general supervision of a worker who has been trained to understand the hazards associated with the work. Such a worker must ensure that the precautionary measures are implemented and maintained. For more information, check out the Dept. Of Labour website: Labour Guide
Check out these other articles
- Are People More Complicated Than Technology?
- Get Your Hands On These Discounted Courses From Colleen Osorio
- Top Tips For Retail Training Success
- Vocational Training Goes Online: Greater Accessibility For Prospective Students
- Toolmaker Artisan Training Programme
- Improving Staff Training In The Retail Environment
- How To Disagree With Someone More Powerful Than You
- How To Map Out Your Online Study Programme
- Top 5 Places To Do Your Skills Training
- Eight Steps Towards POPIA Compliance
Advertisement
Related Articles
South africa's most in-demand jobs for 2024.

Millions of people want to pursue careers with job security. The scarce skills list informs individuals which skills are most needed in the country.
All service providers who have applied to be listed on the Department of Labour database, should confirm registration
Related content.

Interesting Read: How To Check Your Sassa R350 Grant Appeal Status
Advertisement i
Other People Were Also Interested In

If you're interested in pursuing education at a South African university, you'll be pleased to learn that applications for the year 2025 are now open at several universities in South Africa. Here are the details we have gathered thus far.

As the 2024 academic year starts, thousands of students will be registering in academic programmes at institutions of higher education around South Africa. The registration period for the country's largest university has now been extended.

Millions of people rely on Sassa grants to survive every month. The agency responsible for paying the grants have revealed its grant payment plan for the next twelve months.

Millions of people will receive Sassa grants in April 2024. The grant payment agency has confirmed that all grants to be distributed in April will be increased.
Advertisement m
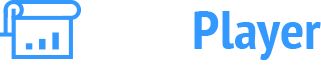
- My presentations
Auth with social network:
Download presentation
We think you have liked this presentation. If you wish to download it, please recommend it to your friends in any social system. Share buttons are a little bit lower. Thank you!
Presentation is loading. Please wait.
To view this video please enable JavaScript, and consider upgrading to a web browser that supports HTML5 video
Theme 7: Occupational Health and Safety Act 85 of 1993
Published by Phillip Rogers Modified over 8 years ago
Similar presentations
Presentation on theme: "Theme 7: Occupational Health and Safety Act 85 of 1993"— Presentation transcript:
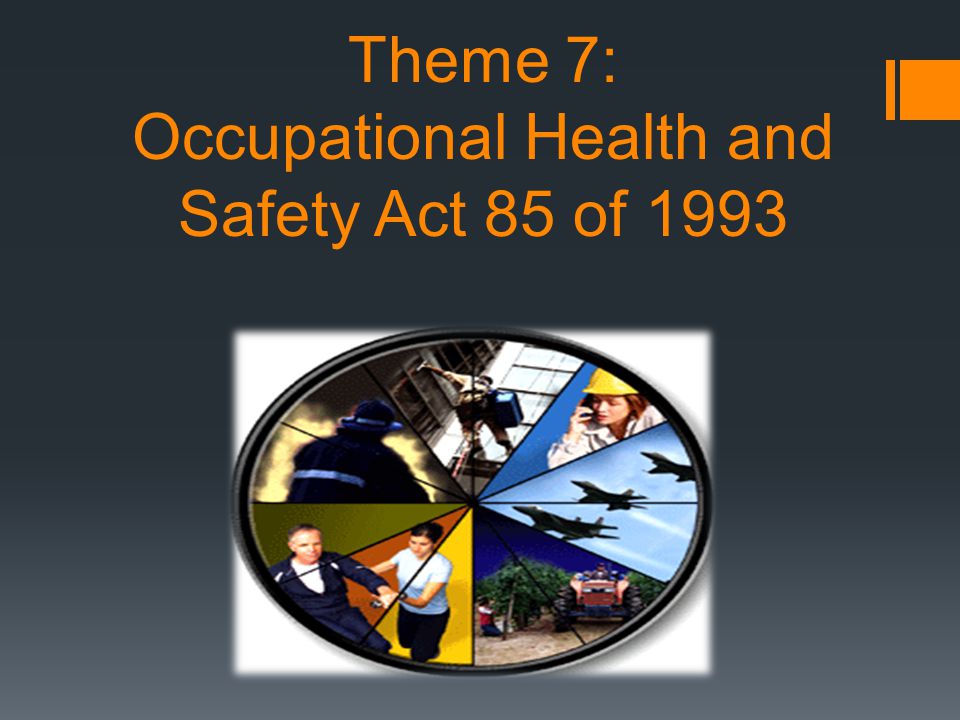
Working Safely in an Engineering Environment Element 1 - Comply with statutory regulations and organisational requirements Page 2File ref:
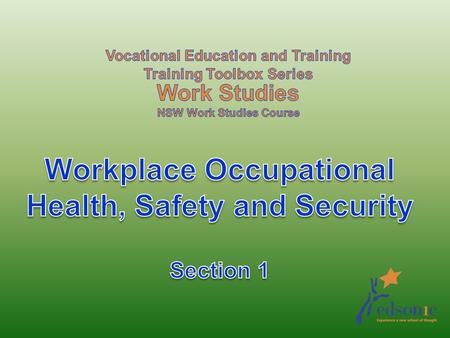
Workplace Occupational Health, Safety and Security
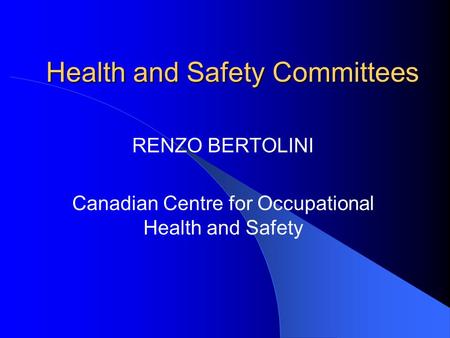
Health and Safety Committees RENZO BERTOLINI Canadian Centre for Occupational Health and Safety.
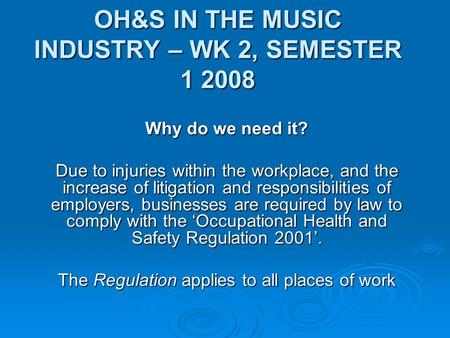
OH&S IN THE MUSIC INDUSTRY – WK 2, SEMESTER Why do we need it? Due to injuries within the workplace, and the increase of litigation and responsibilities.
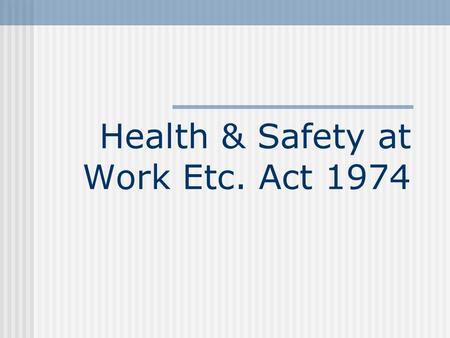
Health & Safety at Work Etc. Act 1974
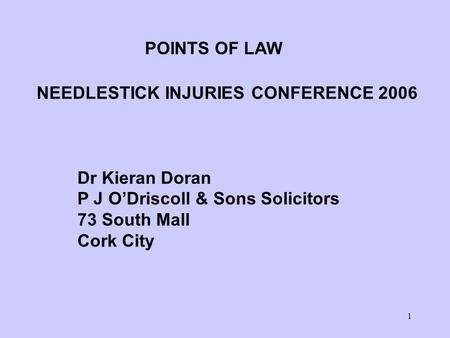
1 POINTS OF LAW NEEDLESTICK INJURIES CONFERENCE 2006 Dr Kieran Doran P J O’Driscoll & Sons Solicitors 73 South Mall Cork City.
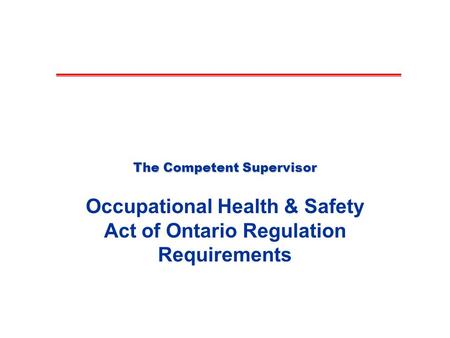
The Competent Supervisor
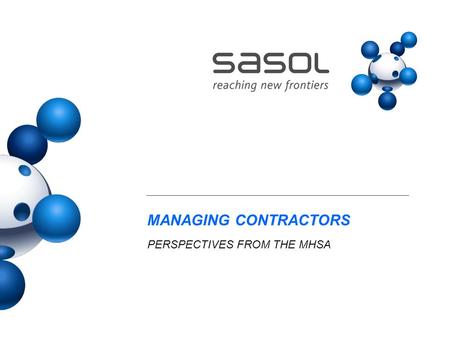
MANAGING CONTRACTORS PERSPECTIVES FROM THE MHSA. copyright reserved 2003, department, company INTRODUCTION More work is being outsourced to contractors.
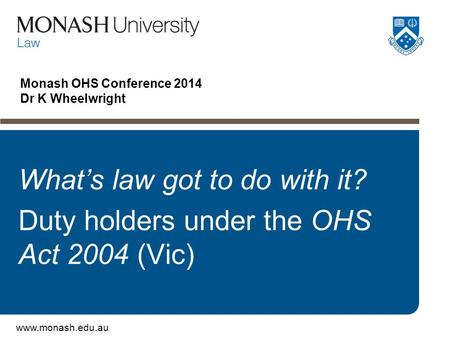
Monash OHS Conference 2014 Dr K Wheelwright What’s law got to do with it? Duty holders under the OHS Act 2004 (Vic)
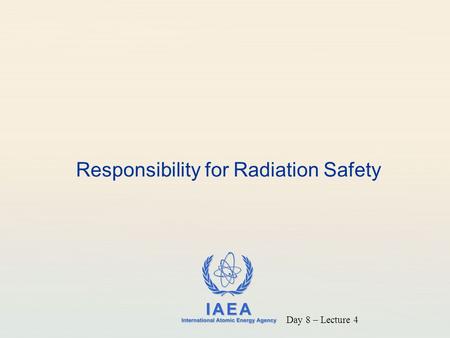
IAEA International Atomic Energy Agency Responsibility for Radiation Safety Day 8 – Lecture 4.
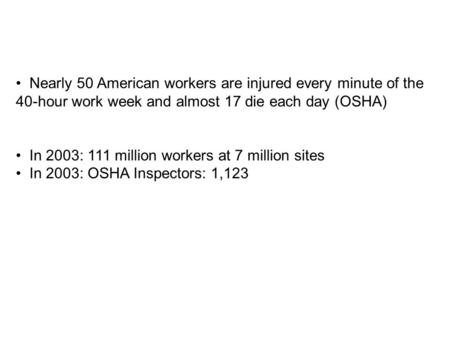
Nearly 50 American workers are injured every minute of the 40-hour work week and almost 17 die each day (OSHA) In 2003: 111 million workers at 7 million.
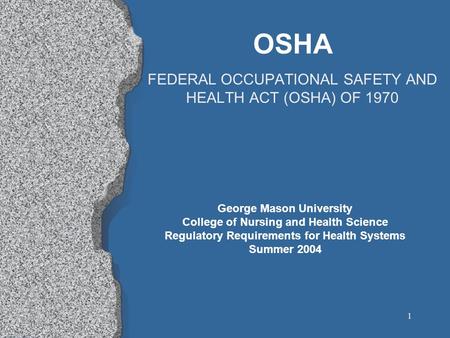
1 OSHA FEDERAL OCCUPATIONAL SAFETY AND HEALTH ACT (OSHA) OF 1970 George Mason University College of Nursing and Health Science Regulatory Requirements.
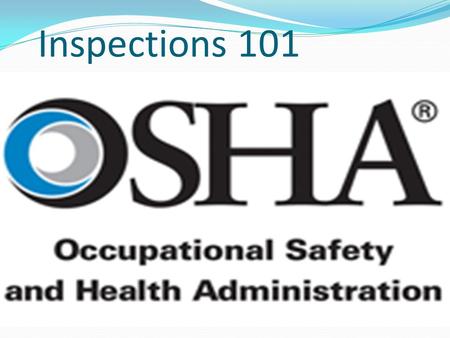
Inspections 101. The OSHA Mission… To assure safe and healthful working conditions for working men and women, by authorizing enforcement of the standards.
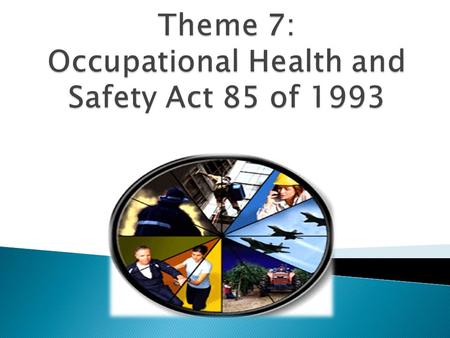
To provide for the health and safety of persons at work and for the health and safety of persons in connection with the use of plant and machinery;
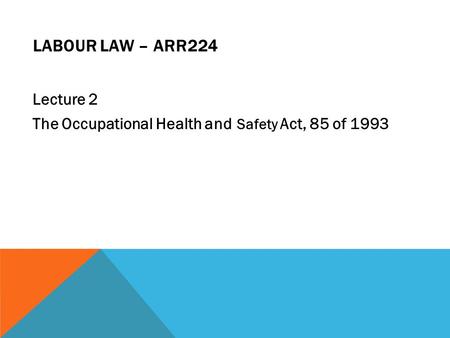
LABOUR LAW – ARR224 Lecture 2 The Occupational Health and Safety Act, 85 of 1993.
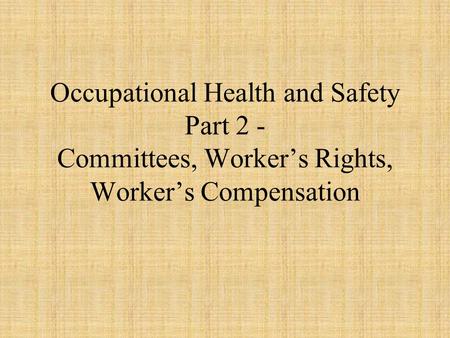
Occupational Health and Safety Part 2 - Committees, Worker’s Rights, Worker’s Compensation.
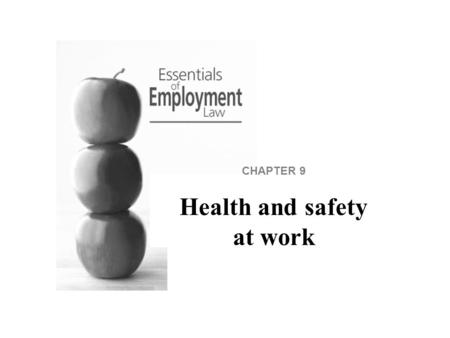
Health and safety at work
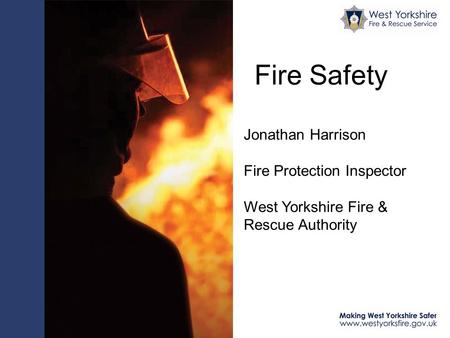
Fire Safety Jonathan Harrison Fire Protection Inspector West Yorkshire Fire & Rescue Authority.
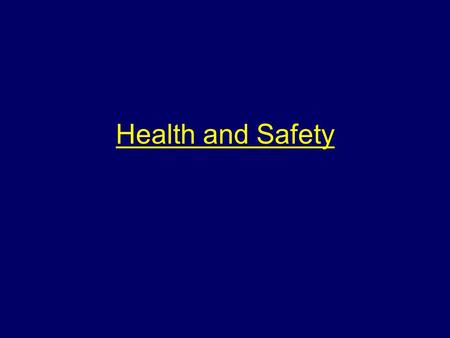
Health and Safety.
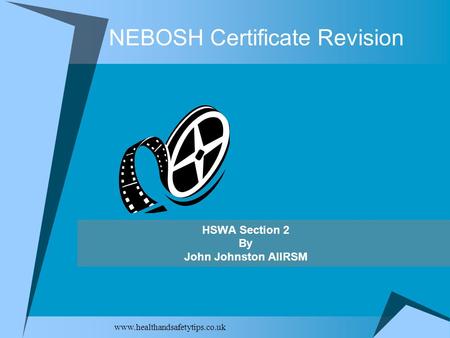
NEBOSH Certificate Revision HSWA Section 2 By John Johnston AIIRSM.
About project
© 2024 SlidePlayer.com Inc. All rights reserved.
- Online tools
- About MOSH and the learning hub
- Adoption system
- Leading practices
- Initiatives
- Dust risk bowtie analysis
- Critical Noise Equipment Screening Tool
- FOG industry bow tie
- Presentations and videos
- Behavioural matters
- Falls of ground
- Transport and machinery
- Contact details
Presentations
Coal leadership forum occupational health dialogue with academia - 15 april 2021, escalation of black lung in the us and approach for controlling respirable dust (niosh).
2021-05-07 | (2.64 MB)
Noise Control of Mining Machines (NIOSH)
2021-05-07 | (3.98 MB)
Noise Reduction of Mining Equipment in the SAMI (UP)
Overview of respirator fit - limitations & challenges.
2021-05-07 | (1.08 MB)
MOSH Indaba - 8 June 2016
Mosh indaba phakisa mine case study.
2019-05-10 | (1.43 MB)
MOSH Indaba 2016 Fact sheet
2019-05-10 | (1.06 MB)
MOSH Indaba Kuthala Colliery case study
2019-05-10 | (736.32 KB)
MOSH Indaba Bambanani mine case study
2019-05-10 | (2.24 MB)
Presentation to CMEE Workshop
2019-05-10 | (825.62 KB)
Industry wide Buy Quiet Initiative
2019-05-10 | (814.53 KB)
Presentation to Dr JS
2019-05-10 | (847.24 KB)
Presentation to Hernic Ferrochrome
2019-05-10 | (838.21 KB)
Opening Address by Mr Lucky Kgatle
![occupational health and safety powerpoint presentation south africa Opening Address by Mr Lucky Kgatle [thumbnail]](https://www.mosh.co.za/images/mosh/opening-address-by-mr-lucky-kgatle.png)
Closing Address by Mr Kgabi Masia
![occupational health and safety powerpoint presentation south africa Closing Address by Mr Kgabi Masia [thumbnail]](https://www.mosh.co.za/images/mosh/closing-address-by-mr-kgabi-masia.png)
MOSH welcome & introduction
![occupational health and safety powerpoint presentation south africa MOSH welcome & introduction [thumbnail]](https://www.mosh.co.za/images/mosh/mosh-welcome-and-introduction.png)
MOSH Sietse van der Woude
![occupational health and safety powerpoint presentation south africa MOSH Sietse van der Woude [thumbnail]](https://www.mosh.co.za/images/mosh/mosh-sietse-van-der-woude.png)
MOSH Phakisa Mine
![occupational health and safety powerpoint presentation south africa MOSH Phakisa Mine [thumbnail]](https://www.mosh.co.za/images/mosh/mosh-phakisa-mine.png)
MOSH Falls of ground Andre van ZyL
![occupational health and safety powerpoint presentation south africa MOSH Falls of ground Andre van ZyL [thumbnail]](https://www.mosh.co.za/images/mosh/mosh-falls-of-ground-andre-van-zyl.png)
MOSH Panel discussion
![occupational health and safety powerpoint presentation south africa MOSH Panel discussion [thumbnail]](https://www.mosh.co.za/images/mosh/mosh-panel-discussion.png)
MOSH leading practice adoption system
![occupational health and safety powerpoint presentation south africa MOSH leading practice adoption system [thumbnail]](https://www.mosh.co.za/images/mosh/mosh-leading-practice-adoption-system.png)
MOSH Dalisu Mkhize
![occupational health and safety powerpoint presentation south africa MOSH Dalisu Mkhize [thumbnail]](https://www.mosh.co.za/images/mosh/mosh-dalisu-mkhize.png)
MOSH Closing Stanford Malatji
![occupational health and safety powerpoint presentation south africa MOSH Closing Stanford Malatji [thumbnail]](https://www.mosh.co.za/images/mosh/mosh-closing-stanford-malatji.png)
In this section
- Days of learning
- Hard rock sector
- Coal sector
- Open cast sector
This site uses cookies to enhance your website experience. By clicking the Accept All button, you consent to these cookies. You can learn more about cookies and how we use them by viewing our Cookie Policy .
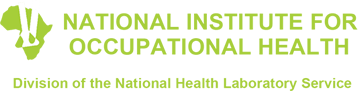
Presentations
Disclaimer: The views and opinions expressed in these webinars are those of the speakers and do not necessarily reflect the views or positions of the NIOH.
Note: This content may only be reproduced in full, with nothing excluded. Where an abridged form of the content is required, prior written approval must be obtained from the NIOH. All data and statistics referred to are applicable on the date of publication.
COVID-19 Policy Updates: The Code of Practice Webinar held on 6 October 2022
Covid-19 nedlac/nioh webinar held on 16 august 2022, covid-19 centenary webinar – held 21 april 2022, covid-19: the evolution of workplace directives (12 april 2022) , covid-19: vaccines in the workplace (25 march 2022) , ergonomics and covid-19: what are the lessons learnt (24 march 2022) , occupational health surveillance system (ohss): update on reporting (10 march 2022) , occupational health surveillance system (ohss): csv new platform & data submission demo (20 august 2021) , covid-19 occupational health services for covid-19 in the health sector (29 july 2021) , covid-19 droplets versus aerosols & ventilation – the role of ventilation in the workplace (22 july 2021) , covid-19 and skin conditions in the workplace (15 july 2021) , occupational health surveillance system – an update on changes (14 july 2021) , south african ergonomics regulations 2019: implications for the construction industry (09 july 2021) , long covid and the workplace – an update (08 july 2021) , working from home – ohs policy and reasonable accommodation during covid-19 (01 july 2021) , basic ventilation requirements, covid-19 directions & national building regulations & other guidelines (03 june 2021) , occupational health and safety workplace systems and covid-19 (27 may 2021) , workers’ rights in the era of covid-19 and the workplace (18 may 2021) , mental health resilience for health care workers (04 may 2021) , workplace risk assessment, cleaning, decontamination, storage & transportation (29 april 2021) , covid-19: long covid and the workplace (22 april 2021) , launch: regulations for hazardous chemical agents (20 april 2021) , covid-19: what are the responsibilities of employers (15 april 2021) , covid-19 & vaccination in the workplace – an overview – repeat session (25 march 2021) , covid-19 and travel medicine (18 march 2021) , covid-19 vaccines in the workplace – an overview (04 march 2021) , ohss data submission using cmore – creating your own reports (02 march 2021) , covid-19 risk assessment training update (24 february 2021) , occupational health surveillance system (ohss) for south african workplaces: update (11 february 2021), the triple burden of covid-19, hiv and tb in the workplace (29 october 2020), occupational health surveillance of covid-19 in sa workplaces – guidance for ohss data submission (20 october 2020), working from home during covid-19 & beyond: an ergonomics perspective (15 october 2020), legionella and covid-19: building water safety during pandemics and beyond (08 october 2020), covid-19 & the built environment (06 october 2020), fitness for work considerations post covid-19 (01 october 2020), ask the expert: the use of fabric masks and masks with vents (18 september 2020), ethical considerations of h&s personnel in workplaces – covid-19 (10 september 2020).
Ethics Guidance Documents for Occupational Health Practice
OHS in Urban Public Workspaces – for Workers in the Informal Economy (27 August 2020)
Compensation for workplace acquired covid-19: a practical approach (20 august 2020), the impact of covid-19 on mental health (13 august 2020), management of puis for covid-19: experiences across sectors (4 august), medical screening and testing for covid-19 in different workplaces (30 july & 6 august), management of persons under investigation (puis)for covid-19: experiences across sectors (17 july), discussion on covid-19 health care worker (hcw) surveillance for nehawu (16 july), return to work post covid-19 illness/lockdown (14 july), workplace health risk assessment & ppe effectiveness (10 july), vulnerable employees risk assessment – covid-19 (07 july), what useful ohs information resources are available for covid-19 – workplace preparedness (02 july), what to do when an employee tests positive for covid-19 in the workplace (26 june & 01 july), available control measures for covid-19 in specific workplaces (23 & 30 june), what are the responsibilities of employers during covid-19 (09 & 12 june), covid-19: construction work & return-to-work (04 june), implications of covid-19 on the workplace – training for shop stewards (26 & 29 may), covid-19 training of employees in the food industry (06 may), addressing questions on “return to work preparedness” (21 & 23 april), step-by-step risk assessment for covid-19 (04 may), covid-19 training for environmental health practitioners (24 april), labour relations during covid-19, covid-19 training for health care workers – train-the-trainer (09 march), covid-19 nhls staff training (26 march), covid-19 training for the health care worker [hcw] (09 march), covid-19 workplace preparedness for education officials and teachers (16 march), covid-19 – preparing gp’s and dentists’ practices (31 march), biorisk assessment for frontline workers (02 aril), workplace preparedness ohs practitioners – civitas (24 march), looking after your emotional well-being during this time: thinking about health care workers (08 april), management roles & responsibilities during covid-19 (09 april), addressing questions of return to work readiness (23 april|).
- Skip to top
Advancing social justice, promoting decent work
Ilo is a specialized agency of the united nations, occupational safety and health country profile: south africa, international labour standards, ratification of ilo conventions.
Database on international labour standards
Provides access to the latest information on ILO international labour standards on OSH (such as ratification information, reporting requirements, comments of the ILO's supervisory bodies, etc.).
Laws and regulations
National regulatory framework.
Global database on OSH legislation
Provides a picture of the regulatory framework of the main elements of OSH legislation. Contains comprehensive legal information and analysis.
National legislation
National labour legislation database
Includes abstracts of OSH legislation and citation information. Full text of laws or a relevant source is linked to the records, when available.
Authorities and bodies
Responsible authorities, occupational injuries.
Database of labour statistics
Contains annual data collected mainly through the ILO yearly questionnaire. It covers a wide range of topics including occupational injuries.
Information and advisory services
Ilo-cis centre.

- Preferences
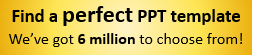
OCCUPATIONAL HEALTH AND SAFETY ACT - PowerPoint PPT Presentation

OCCUPATIONAL HEALTH AND SAFETY ACT
Occupational health and safety act & ohh policyreview department of labour occupational health and safety m ruiters historical account of the acts the very first ... – powerpoint ppt presentation.
- DEPARTMENT OF LABOUR
- OCCUPATIONAL HEALTH AND SAFETY
- The very first legislation introduced into South Africa covered both Industrial safety and conditions of employment
- The very first Act was the Factories Act 28 of 1918
- In terms of CHAPTER I of the aforementioned Act, the general administration of this Act was vested in the Minister of Mines and Industries originally before it was transferred to the Department of Labour in 1924.
- Factory and Building Work Act, 22 of 1941
- A further shift came about during the 1983 period, where legislation focussed purely on OHS and did not include the Conditions of Employment
- Machinery and Occupational Safety Act, Act 6 of 1983
- Introduction of Self regulation functions increased for OHS representatives and committees and focus placed on Occupational Health
- Occupational Health and Safety Act, Act 85 of 1993
- Is the current legislation sufficient?
- What do we want to achieve with any changes we want to make?
- What is the current philosophy? (self/co-regulation introduction of AIA concept DoL inspectors has short reach.
- What is the philosophy/theme moving forward!
- What do we want to achieve in the next 5 to 10 years
- Expectations of employers?
- Expectations of employees?
- Expectations of public and ?
- Expectations of specialists?
- Additional issues
- Registration of workplaces for permit?
- Higher penalties (compliance has not moved)?
- Safety Management Systems reports annually?
- Special conditions imposed where fatal incidents?
- Structural issues
- Administrative issues
- The Occupational Health and Safety Act predates the Constitution which provides that any law or conduct inconsistent with the Constitution is invalid and any obligation imposed by the Constitution must be fulfilled.
- The redrafting of the Act therefore became necessary to ensure consistency with the spirit and provision of the constitution dealing with the right to life, human dignity, right to fair labour practice, access to information and lawful, reasonable, and procedurally fair administrative decision making.
- Over and above the fact that the current OHS Act predated the Constitution, the legislation has not kept abreast with the legal landscape in the Republic South Africa technology and OHS around the world.
- Occupational Health and Safety in South Africa therefore remains fragmented with various Government Departments claiming jurisdiction over various areas leading to confusion at times for clients.
- The Bill seeks to provide for the health and safety of persons at work and for the health and safety of persons in connection with the activities of persons at work, and to provide a common framework to guide for the prevention of accidents and ensure safety at the workplace, alignment of the Act with the constitution and other employment laws
- Move forward with current Act that must be reviewed.
- Administrative Management of OHS
- Safety Management System and includes
- Risk Management
- Health and Safety Representatives and Committees
- Responsibilities
- appointments
- A total turnaround on the enforcement capability which includes
- Administrative Fines
- Alignment of legislation
- Definitions - changes
- Section 10 expanded upon to address deficiencies in terms of GHS and HCS
- Substantial increases in penalties i.e. up to R5 000 000 and/or 5 years in prison (max.)
- It is now entrenched in the new Bill that Employees have a right to leave a dangerous place of work
- Very little change has been effected to the old Section 16 Chief Executive Officer charged with certain duties see change made to the issue of assigning certain duties
- Some work have been done on Functions of health and safety representatives
- New Regulations have in the mean time been promulgated after the promulgation of the Constitutional Act, while the OHS Act has never been brought in line with it until today.
- Due to the new Regulations pursuing a newer, different concept or theme, different to that which existed with the coming into force of the existing OHS Act, i.e. self regulation and Occupational Health, etc., the new Regulations are not in synch with the OHS Act and it has and is creating problems with the development of newer Regulations.
- AIA Guideline document
- WHAT IS AN APPROVED INSPECTION AUTHORITY (AIA)?
- REASONS FOR APPROVING AIA
- CRITERIA FOR APPROVAL
- EXAMINATION ON LEGISLATION
- DOCUMENTATION (17020)
- INVESTIGATION OF COMPLAINTS AND DEVIATIONS (17020)
- PROCEDURES FOR APPROVAL
- APPROVAL CERTIFICATES
- AUDITS BY THE DEPARTMENT OF LABOUR
- REPORTING TO THE CHIEF INSPECTOR
- LIST OF APPROVED INSPECTION AUTHORITIES
- SANAS accreditation of AIAs
- Legal knowledge
- Approached tertiary institutions and 6 are will to present the course
- Workshop 30 and 31 July 2012
- Environmental regulations for workplaces
- AIAs more scope
- Physical stressors ( Thermal, ventilation, vibration.)
- Regulations
- Workshop (September/October)
- HCS, GHS and Asbestos
- Risk Assessments??????
- All regulations will have to be brought in line with the key changes in the Act
- A guideline is a must to be published when the Bill is promulgated to ensure that all grey areas are addressed as far as possible.
- All unintended consequences will, as far as possible be dealt with during the Public Comment phase.
- review and strengthen the enforcement provisions
- ensure that the legislation is in line with current international and local industry developments
- simplify the administrative system for issuing fines and shorten the enforcement procedures
- reinforce the offences and penalties
- change in OHH Regulations
- Establishment of technical committee's
- AIAs reporting twice per year
- SANAS Accreditation
PowerShow.com is a leading presentation sharing website. It has millions of presentations already uploaded and available with 1,000s more being uploaded by its users every day. Whatever your area of interest, here you’ll be able to find and view presentations you’ll love and possibly download. And, best of all, it is completely free and easy to use.
You might even have a presentation you’d like to share with others. If so, just upload it to PowerShow.com. We’ll convert it to an HTML5 slideshow that includes all the media types you’ve already added: audio, video, music, pictures, animations and transition effects. Then you can share it with your target audience as well as PowerShow.com’s millions of monthly visitors. And, again, it’s all free.
About the Developers
PowerShow.com is brought to you by CrystalGraphics , the award-winning developer and market-leading publisher of rich-media enhancement products for presentations. Our product offerings include millions of PowerPoint templates, diagrams, animated 3D characters and more.

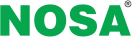
- My NOSA Login
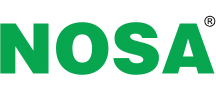
COVID-19 services and solutions

Occupational Health & Safety Training
NOSA is South Africa’s leading occupational health, safety and environmental training provider, offering more than 100 safety-related training courses, skills programmes and qualifications which hold various local and international accreditations.

Popular courses
All our courses.
NOSA specialised courses
Legislation training
- Safety in mining
- Dangerous goods training
- Learnerships
ISO certification courses
Emergency safety training
Driver training
- Driven machinery regulatory training
- Food safety training
Working at height training
- Warehousing and logistics training
Testimonials

- Jobs on offer
- Community Involvement
- NOSA 5 Star Auditing and Grading
- ISO certification training
- Legislation Training
- Emergency Safety Training
- Working at heights training
- Driver Training
- Success stories
- Training centres
- Client portal
- Student portal
- E-learning courses
NOSA course enquiry form
Course option
SAMTRAC Compliance Warehousing & Logistics Learnerships E-learning
Where did you hear about us?
IsoMetrix Miracles Training Audit Testing LinkedIn Website Cold Call New Clients Other Twitter Trade Show LinkedIn Sponsored Form
NOSA COURSE ENQUIRY FORM
I am enquiring about the following course:
I am enquiring as:
An individual A company
I am interested in:
E-learning Classroom

An official website of the United States government
The .gov means it’s official. Federal government websites often end in .gov or .mil. Before sharing sensitive information, make sure you’re on a federal government site.
The site is secure. The https:// ensures that you are connecting to the official website and that any information you provide is encrypted and transmitted securely.
- Publications
- Account settings
Preview improvements coming to the PMC website in October 2024. Learn More or Try it out now .
- Advanced Search
- Journal List
- Int J Environ Res Public Health

Occupational Health and Safety Statistics as an Indicator of Worker Physical Health in South African Industry
Oscar rikhotso.
1 Department of Environmental Health, Tshwane University of Technology, Private Bag X680, Pretoria 0001, South Africa; az.ca.tut@jtidorom
Thabiso John Morodi
Daniel masilu masekameni.
2 Occupational Health Division, School of Public Health, University of Witwatersrand, Johannesburg 2193, South Africa; [email protected]
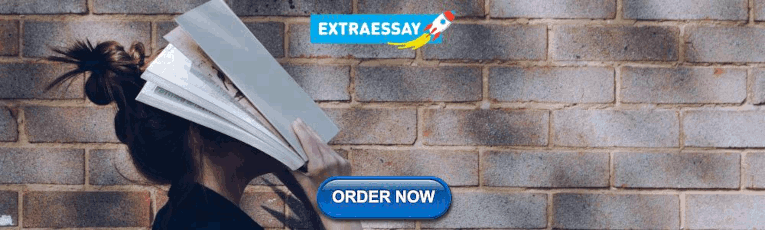
Associated Data
Compensation fund annual reports: https://www.labour.gov.za/DocumentCenter/_layouts/15/touchapp.aspx?Mode=DocLibs&Page=%7B94AA76909%2DF4B3%2D4E83%2D869E%2DB2F4B16F68EF%7D (accessed on 9 December 2021). Employment statistics: http://www.statssa.gov.za/ (accessed on 9 December 2021).
Operations in general industry, including manufacturing, expose employees to a myriad of occupational health hazards. To prevent exposure, occupational health and safety regulations were enacted, with both employers and workers instituting various risk reduction measures. The analysis of available occupational disease and injury statistics (indicators of worker physical health) can be used to infer the effectiveness of risk reduction measures and regulations in preventing exposure. Thus, using the READ approach, analyses of occupational disease and injury statistics from South African industry, derived from annual reports of the Compensation Fund, were conducted. The publicly available database of occupational disease and injury statistics from the South African general industry is unstructured, and the data are inconsistently reported. This data scarcity, symptomatic of an absence of a functional occupational disease surveillance system, complicates judgement making regarding the effectiveness of implemented risk reduction measures, enacted occupational health and safety regulations and the status of worker physical health from exposure to workplace hazards. The statistics, where available, indicate that workers continue to be exposed to occupational health impacts within general industry, notwithstanding risk reduction measures and enacted regulations. In particular, worker physical health continues to be impacted by occupational injuries and noise-induced hearing loss. This is suggestive of shortcomings and inefficiencies in industry-implemented preventive measures and the regulatory state. A robust national occupational disease surveillance system is a regulatory tool that should detect and direct policy responses to identified occupational health hazards.
1. Introduction
Economic sectors such as the manufacturing and utilities sectors are cardinal in that their products are used for daily human sustenance as well as for supporting national economies [ 1 , 2 ]. Certain chemicals, for instance, are applied in medicinal formulations for disease prevention and control in humans, fertilisers to increase crop yields and pesticides that reduce plant disease in agriculture [ 3 ], allowing scope for their existence in spite of their inherent hazards [ 4 ]. According to the International Labour Organisation [ 5 ], both sectors are also a major source of employment globally. Besides the noted societal benefits, workers in these sectors are exposed to inherent occupational health hazards [ 5 ]. The expansion of these sectors requires the assessment and management of health risks from exposure [ 3 ].
Historically, the various industrial revolutions have brought about advancements in the machinery and manufacturing processes, which were and still are used for the mass production of goods in factories [ 6 , 7 ]. Advancements in mechanisation have resulted in unsafe work conditions [ 6 , 8 ], which create occupational health hazards, directly affecting workers [ 9 , 10 ]. Unsafe work conditions manifest themselves in observed occupational diseases (ODs) such as phossy jaw, a result of phosphorus fume exposure and clay dust poisoning in potteries, all having deadly outcomes on workers [ 6 ]. According to the United Nations Human Rights Commission 2018 special report, workers continue to face challenges in inadequate protection standards, slow progress in exposure prevention, fragmented occupational and environmental health strategies and gaps in exposure monitoring and enforcement [ 11 ]. Currently, occupational hazards are no longer limited to factories and mines but are even found in office buildings [ 12 ]. The regulatory response for exposure to occupational health hazards was through the enactment of occupational health and safety (OHS) laws, exposure limits and regulations prescribing how these hazards should be controlled [ 13 , 14 , 15 ]. From a South African perspective, the non-exhaustive historical list of OHS legislation enacted for exposure prevention is highlighted in Appendix A . The development of OHS legislation in South Africa had a historical foundation on the Factories, Machinery and Building Works Act 1941 [ 16 ]. The non-exhaustive, historical views shown in Appendix A attest that OHS regulation has been continually developed and refined over the years in South African general industry. Appendix A also shows the commencement date and purpose of each legislative instrument.
The OHS legislation in Appendix A incorporates the primary (hierarchy of control), secondary (screening and periodic medical screening) and tertiary prevention (medical treatment) methods for health and risk hazards [ 2 , 17 , 18 , 19 ]. The OHS legislation in Appendix A is enforced on self-regulation and regulator-enforced regulatory approach [ 20 , 21 ]. In this regard, the Inspectors of the Department of Employment and Labour are tasked with the enforcement of legislative pieces on the one hand [ 13 , 21 ]. While on the other hand, employers implement these OHS laws as a demonstration of legal compliance [ 13 ]. Although the Department of Employment and Labour’s annual reports indicates that the OHS inspectorate is conducting enforcement and inspections, the reports are scant on specificity relating to the violated legislation [ 22 , 23 , 24 ] ( Appendix A ). The reporting of ODs for compensation, initiated by the regulated industry, is directed by the Compensation Fund, a separate reporting structure of the Department of Employment and Labour [ 13 , 25 , 26 ].
In addition to the highlighted legislative instruments, South Africa is also a signatory of the International Labour Organization (ILO) Convention 155, “Occupational Safety and Health Convention”. However, the ILO conventions and recommendations are not binding unless ratified by a member country [ 27 ].
Despite the positive advancement in human development brought by industry and the enactment of OHS legislation, workers have paid a supreme price for contracting ODs and incurring physical injuries resulting from workplace exposures [ 28 ]. In particular, the occupational injury and disease burden for workers in low- and middle-income countries continue to rise [ 29 ]. The severity of such health impacts remains difficult to predict, however, as they occur gradually and cumulatively in the case of ODs [ 30 ].
The reported injuries and ODs from industry point employers and regulators to specific focus areas for prevention [ 31 ]. Accordingly, the most commonly reported OD is noise-induced hearing loss (NIHL), a nagging burden for compensation systems worldwide [ 32 ]. In spite of a strong knowledge base regarding OD occurrence and workplace regulation, it is apparent that current injury and OD incidence rates indicate a lapse in the application of this knowledge. However, complications arise from emerging issues such as concurrent exposure to chemicals, heat and cold stress, noise and vibration [ 3 ]. To judge the effectiveness of enacted legislative instruments, a review of national injury and OD statistics was necessary to shed light on the subject matter. The long-term prevention of injuries and ODs in occupational health programmes comes from hazard identification and risk assessments [ 33 , 34 , 35 , 36 , 37 , 38 ]. The aforementioned scholarly paper reviews publicly available injury and OD statistics to infer the state of the health of the workforce within South African general industry. This inference indirectly attests to the effectiveness of OHS regulations enacted to prevent ODs and injuries.
2. Materials and Methods
2.1. conceptual framework.
The OHS regulations in Appendix A have not fully eliminated workplace hazards; however, data from other countries indicate that the implementation of similarly structured regulations has reduced some workplace injuries and ODs, largely attributable to regulator enforcement and inspection [ 39 , 40 , 41 ]. This thus indicates the need for a strong labour inspection regime to ensure a high level of compliance on the part of the regulated industry [ 20 ]. In this regard, Gray and Jones [ 42 ] posit that an increase in the number of regulatory inspections conducted in the United States’ manufacturing sector has resulted in a decrease in the number of citations and worker exposure levels.
The microanalysis of OD and injury reports and the statistics released by the relevant institutions becomes necessary in order to gain insight into the subject matter. From a South African perspective, annual reports of the Compensation Fund, where available, are applicable. The conceptual framework employed for this review, adapted from Hongoro and Kumaranayake [ 43 ], is shown in Figure 1 .

Conceptual framework adopted [ 43 ].
The observed low OD and injury incidence rates would infer the effectiveness of the OHS legislation in relation to the total employed population since inception. The absence of a functioning OD and injury surveillance can, however, make such adjudication cumbersome. This review focused on the microanalysis of annual reports of the Compensation Fund for injury and OD statistical information relevant for this study.
2.2. Search Strategy
2.2.1. occupational disease and injury statistics.
An online search for the annual reports of the Compensation Fund from 2002 to 2020 was conducted. Historically, these annual reports have provided high-level summaries of total OD and occupational injury counts with limited detail in regards to specifics, such as industry origin, race and gender; this is against a backdrop of an absent national OD and injury surveillance system.
2.2.2. Employment Statistics
Against the backdrop of an absent national OD and injury surveillance system, an online search of the employment statistics from Statistics South Africa was used to shed light on the contributory factors of workforce characteristics and total employment in resultant OD and injury statistics. The employment statistics covered the period from the year 2001 to December 2019. The lag in the statistics relates to the retrospective nature of such data.
2.3. Document Analysis
With a view of extracting meaning from the retrieved reports, document analysis was employed as a qualitative research method [ 44 ], with the perspective of obtaining quantitative data on OD and injury and employment statistics. Bowen [ 44 ] conceptualised document analysis as a research method that can be systematically applied in the evaluation or review of documents in print or electronic form. Document analysis enables the study to extract meaning from the data through examination and interpretation, which subsequently leads to a greater understanding of the subject matter [ 44 ]. Within the context of scientific research, document analysis denotes the analysis of any written material containing information about the topic of concern [ 45 ]. The READ approach [ 46 ] to document analysis was used in extracting meaningful data from the enrolled reports. The steps of the READ approach are: (1) readying the materials, (2) extracting the data, (3) analysing the data and (4) distilling the findings [ 46 ]. The READ approach to document analysis has been previously used in [ 47 ]. Figure 2 , Figure 3 and Figure 4 and Appendix B present the results derived through the READ approach.

Sectoral employment in South Africa (excludes mining, private households).

Male employment in South Africa (excludes mining, private households).

Female employment in South Africa (excludes mining, private households).
The literature search returned results that limited the data in this study to annual reports published by the Compensation Fund. In general, the data was fragmented, difficult to locate and differed structurally, year to year. Reports relevant data to the study covered the years 2001 to 2019. No data for the reporting periods of 2014 and 2015 were located within the reports or any other public sources.
Occupational accidents, including both ODs and injuries, are reported to the Compensation Fund in line with the requirements of Section 24 of the Occupational Health and Safety Act [ 13 ], as well as Regulation 8 of the General Administrative Regulations [ 26 ]. Broadly, compensated injuries and ODs are regulated through the Compensation of Occupational Injuries and Diseases Act within South African general industry [ 25 ].
Due to an apparent absence of a national occupational disease and hazard surveillance system, statistical information from Statistics South Africa provides useful information on employment patterns. Thus, a background analysis of the number of workers employed in general industry was pertinent for this study.
3.1. Employment and Exposure Trends in South Africa
Statistics South Africa publishes quarterly labour market conditions for the country. In this regard, Figure 2 provides an overview of the sectoral employment in South Africa, whose occupational accidents are reported to the Compensation Fund for compensation purposes, covering the period between the fourth quarter of 2001 to the fourth quarter of 2019. Whereas Figure 2 , Figure 3 and Figure 4 provide the gender and population group profiles of the workers employed in sectors indicated in Figure 2 .
Figure 2 shows that between 2001 and 2019, trade and community services provided the majority of employment for the South African workforce. Employment from the manufacturing, utilities, construction, agriculture and transport sectors remained stable for the quoted period. The business sector (finance) did, however, see an increase in employment trends during the same period. The sectoral employment in Figure 2 provides evidence of employment shifts in the number of workers exposed to prevailing occupational health and safety hazards per industry type. Thus, the trade and community services industries constitute the highest number of workers exposed to inherent occupational health and safety hazards. The severity and scale of these hazards, however, differ from industry to industry, with the manufacturing sector cited as the most hazardous [ 10 ].
Figure 3 and Figure 4 show the gender distribution of the workers in each sector. The construction, manufacturing and trade industries employed more males combined. Meanwhile, the community service and finance industries provided more employment, combined, for females. Comparably, the South African labour market had more males in employment compared to females. This has historic underpinnings, wherein specific jobs were exclusively reserved for males. Anecdotally, males are the gender whose physical health from workplace exposure is most impacted by occupational hazards inherent in each respective industry under consideration.
On a different perspective of race at South African workplaces, the country’s labour laws differentiate the racial profile into Black African, White, Coloureds and Indians/Asians [ 48 , 49 ]. Generally, the South African population profile is predominantly Black African, with Whites, Coloureds and Indian/Asians making up the other percentage. This skewed demographic profile has also translated into workplace demographic disparities, wherein Black Africans constitute 70% of the employed population. Other race groups such as White, Coloured and Indians/Asians constitute 18%, 7% and 4% of the employed population, respectively. Anecdotally, Black Africans are the most exposed population group whose physical health from workplace exposure is greatly impacted by occupational hazards. However, exposure to inherent occupational health and safety hazards will largely depend on the industry type and tasks performed in the main. From a historic perspective, the white population exclusively occupied reserved managerial or supervisory positions, often seen as having less exposure compared to the physical tasks associated with manual work assigned to Black Africans, Coloureds and Indians/Asians [ 50 , 51 ].
3.2. Occupational Accidents in South Africa
The employment statistics for general industry and the total reported occupational accidents, including injuries and ODs, are shown in Appendix B . Between 2001 and 2019, a 19-year view, 3,852,071 occupational accidents were reported for compensation consideration, 3,808,177 of which were occupational injuries and 44,014 were ODs. The source industries of these occupational accidents are shown in Figure 2 , and were reported to the Compensation Fund.
The total number of occupational accidents for the considered periods show that occupational injuries far outweighed ODs and closely tracked the total reported accidents. In general, ODs have both short and long latency, whereas occupational injuries are acute and have short-term latency [ 9 ]. The occupational injuries and OD disparity are unsurprising when considering the latency periods associated with each accident type. Notably, however, the total reported ODs excludes musculoskeletal disorders, an outcome of legal mechanisations in the administration of the Compensation for Occupational Injuries and Diseases Act [ 25 ]. Comparably, the lowest number of occupational accidents were reported at 81,995 in 2019, concurrent with a decrease in employment numbers within the manufacturing and construction sectors, as shown in Figure 2 . The highest peak of reported accidents was recorded at 310,710 during 2013, concurrent with an increase in employment numbers from the agriculture, transport, construction and community service sectors. Of the periods under consideration, accident declines were noted during the reporting years of 2002, 2006, 2011, 2014, 2015 and 2019.
The data also shows that the majority of workers, in general, have jobs with low exposure and risk probability. In spite of the delayed latency of ODs, this is unsurprising as the dominant industries providing major employment for the South African labour market are trade, finance and community services. Business activities conducted in these sectors expose workers to mainly sedentary and ergonomic health and safety hazards. This, therefore, implies that the source industries for the reported occupational accidents include agriculture, manufacturing, construction and transport. However, in the absence of a national occupational disease and injury surveillance system capturing these indicators, such disambiguation is impossible.
The annual compensation fund reports considered in this study do not specify the nature of the specific occupational injuries reported, thus highlighting the paucity of such data on the one hand. Whilst, on the other hand, OD types were specified, though inconsistently, on some of the annual reports under consideration.
3.3. Occupational Diseases in South African General Industry
Table 1 differentiates specific ODs as a fraction of occupational accidents, as alluded to in Section 3.2 . These ODs, accepted and subsequently compensated, cover diverse exposures resulting from workplaces that have physical, chemical and biological hazard types. These hazard types are regulated through the Environmental Regulations for Workplaces, Noise-Induced Hearing Loss-, Hazardous Chemical Agents- and the Hazardous Biological Agents-Regulations; legislative instruments reported in Appendix A [ 33 , 34 , 35 , 36 , 37 , 38 ]. The data in Table 1 show that workers continue to be exposed to physical, chemical and ergonomic health hazard impacts in spite of enacted workplace regulations; reported in Appendix A .
Compensated ODs in South Africa [ 23 , 24 , 53 , 54 , 55 , 56 , 57 , 58 ].
1 OD name not specified. na Not available.
Of the compensated ODs, NIHL, a result of exposure to unprotected excessive noise levels, had the highest incidence in proportion to other diseases for the reporting periods, 2001 to 2019. All the recorded ODs show a decreasing trend for the covered period. Due to the lack of publicly available scientific literature investigating the effectiveness of the various legislative instruments in South Africa, it remains difficult to determine whether the OD decline can be attributable to OHS laws in Appendix A . Furthermore, it is inconceivable that legislation on its own has had such an impact on the decline in OD trends without effective enforcement and inspection regime [ 39 , 40 , 41 ], constantly cited as a hindrance to achieving the goals of OHS laws in most underdeveloped and developing countries.
No data were available in regards to OD specificity for the reporting years 2010 to 2013, as well as general data for all accidents for the periods 2014 to 2015. These ODs are preventable [ 52 ]. Comparably, the nature, cause and sources of occupational injuries remain unknown to the general public.
The source industries of the ODs in Table 1 are indicated in Figure 2 , including activities as defined per the Statistics South Africa industry classification of economic activities [ 59 ].
4. Discussion
This study evaluated the status of worker physical health in South African general industry through the analysis of OD and injury statistics reported by the Compensation Fund. Additionally, employment statistics published by Statistics South Africa were considered in the analysis providing contextual background to ensuing discussions. The quoted statistics from South African general industry show that injuries far outweigh ODs, in part due to their short latency periods. The long latency of ODs, on the other hand, offers governments, employers and workers worldwide room for their elimination through the establishment of effective OD and hazard surveillance systems [ 60 ]. In this regard, the OD morbidity rates can direct policymakers to specific occupational hazards requiring urgent policy intervention.
The OD statistics for the quoted periods showed a declining trend. This decline and noticeable aggregate low levels of OD morbidity levels have seeming peculiarities, however, which relate to the increasing proportion of workers potentially exposed to occupational health hazards against registered ODs and injuries [ 61 ]. The statistics indicate that increases in employment have had a corresponding increase in occupational injuries, concurrent with a decline in OD morbidity. Thus, the noted increase in the number of occupationally exposed workers may well underestimate unreported cases [ 62 , 63 ]. This is symptomatic of a developmental state of occupational health services [ 63 ], South Africa included.
Another peculiarity in the noted declining OD morbidity stems from the noted backlog and carry-over accidents in some of the analysed Compensation Fund reports [ 53 , 54 , 55 , 64 ]. Once finalised, these carry-over accidents may reverse the current “seeming” declining outlook. The reduction in NIHL cases, in particular, is questionable amidst the dearth of information on studies relating to the prevalence of NIHL and industry noise reduction efforts in South African industry. The available field studies [ 65 , 66 , 67 ] indicate that workers are still exposed to excessive noise levels. Specifically, the implementation of hearing conservation programmes in South Africa is largely fragmented [ 67 , 68 ]. Further doubt is cast on the reported declining NIHL cases, from a legislative perspective, as the country has had no changes in the legislative framework governing noise exposure at work since 2003, for which the decline can be ascribed.
Undoubtedly, when OHS laws, such as those in Appendix A , are fully implemented by employers and enforced by inspectorates, a reduction in OD and injury rates can be expected [ 69 ]. However, Table 1 indicates that employer compliance and regulatory enforcement have not entirely eliminated OD and injury morbidity. From this perspective, evidence of enforcement and inspection exists in South Africa via the Department of Employment and Labour annual reports detailing all the department’s activities. However, these reports are adjudged as scant in detail relating to the specific violations noted during enforcement and inspection activities. As an example, in the 2015/2016 annual report, 20,476 notices were issued to the industry for health and safety violations during 23,678 workplace inspections [ 22 ]. Although the decreasing trend in OD is positive and can somewhat be anecdotally ascribed to employer compliance and regulatory enforcement [ 39 , 41 , 69 ], ascribing the decrease entirely to compliance and regulatory inspection is currently a challenge. A challenge admittedly acknowledged by the Department of Employment and Labour relating to the country’s enforcement regime [ 70 ]. From a scientific and technical perspective, to ascribe the reduction in OD morbidity requires measurement of statistics comparing changes in OD rates for both inspected and non-inspected workplaces [ 71 ]; data currently absent in South Africa.
The declining trend in OD morbidity is a positive development; however, the above discourse indicates that South Africa needs to focus more energy on data collection initiatives related to occupational hazards, OD and injury morbidity. The discourse also indicates that the physical health and life of workers is still afflicted by occupational hazards and manifested by ODs and injuries. The full and realistic extent of the affliction, however, remains unknown due to the fragmentation in data collection and the paucity of publicly available statistics. To compound the problem, South Africa currently has an absent national occupational health and safety policy and strategy, a loophole acknowledged by the Department of Employment and Labour [ 70 ].
4.1. Employment and Exposure Trends in South Africa
The employment landscape in South Africa shows that community services and finance are the largest employers. However, the manufacturing, utilities, agriculture and trade sectors are often cited as the most hazardous [ 10 ], compared to office-based work associated with community service and finance. Employees at these industries are often exposed to physical, chemical and biological occupational health hazard types [ 10 , 19 , 72 , 73 , 74 , 75 ], which are all linked to the ODs in Table 1 . The paucity of the Compensation fund-derived OD and injury statistics complicates the process of attributing the specific sectors from which these accidents emanated. With regard to the manufacturing sector, however, occupational health hazards continue to feature in the modern production processes employed in the various industry types [ 76 ]. The transfer of manufacturing to developing countries from developed countries, some with untreated occupational health hazards, consequently sees the cross-border transit of these hazards inherent of such processesWatterson [ 77 ]. Coupled with poor OHS regulation and enforcement [ 78 , 79 , 80 ], workers employed at these facilities in developing countries are severely impacted compared to developed countries [ 76 , 77 ]. The somewhat low impact of occupational hazards in developed countries has been credited to public awareness leading to protest as well as media publicitySellers and Melling [ 76 ].
The prevalence of exposure to occupational health hazards is, however, not limited to South Africa; Watterson [ 77 ] posited that Romanian industries had far worse and unacceptable working conditions relating to occupational hazards compared to their Hungarian and Slovenian counterparts. Similarly, industries in Latin American countries were also reported to have exposure to unacceptable working conditions [ 81 ].
Indigenous ethnic groups across a range of different countries, including Blacks and Hispanics, are the most exposed to these occupational hazards owing to task distribution and task segregation [ 82 , 83 ]. In South Africa, race at the workplace is topical and legally regulated due to past injustices [ 48 , 49 ]. The historic apartheid economic planning concentrated the manufacturing base mainly in Gauteng, Kwazulu-Natal and the western Cape Provinces. Due to the high concentration of the population in these three provinces, it is thus unsurprising that a 2017 Statistics South Africa report indicated that these provinces accounted for 63% of deaths reported in the country, some of which are due to accidental injury from exposure to occupational health hazards. The black population accounted for the majority of the reported deaths due to the high population proportion compared to whites. Of the reported deaths in the same report, accidental poisoning by and exposure to noxious substances; exposure to electric current, radiation and extreme ambient air; and contact with heat and hot surfaces were attributable to occupational health and safety hazards [ 84 ]. Combined, the formal employment sector in South Africa, excluding agriculture, employed some 15 million workers. Of this total, Black Africans, Coloureds and Indians/Asians, excluding whites, were at 11 million. Of the specific occupations, plant and machine operators, craft and related trade and elementary occupations accounted for approximately six million workers in direct contact with occupational health hazards in their daily tasks [ 85 ]. This, therefore, highlights the racial disparity in the distribution of occupations with subsequent exposure to occupational health and safety hazards in South Africa, an important consideration that any future hazard and disease surveillance system should account for.
The above discourse highlights that occupational race/ethnicity and gender segregation have consequential outcomes in the areas of hierarchal authority and wages [ 86 ], applicable to South Africa. As an example, a study conducted in New Zealand found that the ethnic Maori workforce was more likely to be exposed to chemical, physical, organisational and stress factors compared to the non-Maori workforce [ 83 ]. Eng et al. [ 83 ] postulated that the exposure disparity is also a result of over-representation within the manufacturing sector of the ethnic workforce in low-skilled manual jobs. Immigrant workers of different ethnicities in particular, due to their perceived low skill levels, are exposed to hazardous work such as handling toxic products [ 87 , 88 ], leading to high incidence OD rates [ 82 ]. This racial and ethnic disparity also extends to the biased reporting of occupational injuries and ODs. To this effect, Sabbath, Boden [ 89 ] and Ning, Zhou [ 88 ] postulated that the underreporting of occupational injuries is higher among black and migrant workers, leading to underestimations of injuries along racial lines. Murray [ 90 ], however, cautions that further studies are required to grasp the extent of racial/ethnic disparities on occupational health. Notwithstanding the discourse above, risk perception by these exposures is an important consideration in preventing ODs along racial and ethnic lines [ 75 ].
Occupational Health Hazards, Exposure and Latency
The main picture presented by the ODs in Table 1 confirms worker exposure and health impacts inflicted in South African general industry [ 91 ]. The ODs are attributable to exposure from physical agents such as noise [ 8 , 65 , 92 , 93 ], an array of hazardous chemical agents [ 92 , 94 , 95 , 96 , 97 , 98 , 99 , 100 , 101 ] and hazardous biological agents such as mycobacterium tuberculosis [ 92 , 102 , 103 , 104 , 105 ]. Tint [ 19 ] and Ashford [ 30 ] postulated, for instance, that a single worker is exposed to a combination or a part of these hazards, depending on the type of process and job category. The cumulative effects of some of these hazards, even at low exposure levels, can result in chronic health impacts [ 10 , 106 ].
Worker exposure to occupational health hazards is also commonplace in other developing countries [ 63 ]. On this point, a survey carried out by local health inspectors in Estonia revealed that 16% of industrial workers were exposed to chemical, physical and biological agents [ 19 ]. Physical hazards and hazardous chemical substances were also identified in an occupational hygiene survey of 99 small Finnish workplaces [ 73 ] and Sri Lankan medium- and large-scale industrial sectors [ 72 ]. The extent of these hazards varies depending on the industry type, locality and precautionary measures taken by the worker and the employer [ 107 , 108 , 109 ]. The extent of chemical hazards, for example, occurs due to unreacted feedstocks and other process inputs, such as fillers, stabilisers, pigments, inhibitors and initiators, all added to a finished product [ 110 ]. To compound the problem, there are in excess of 100,000 hazardous chemicals in various workplaces, with new chemicals introduced yearly, all affecting workers [ 111 ]. From another perspective, in China, for example, Brown [ 108 ] reported that approximately 60% of businesses have “minimal industrial safety measures”, such as employee training and personal protective equipment. Similarly, in the Philippines, specific OHS issues reported to be grossly violated or disregarded by most employers included occupational health and environmental control, general ventilation and personal protective equipment [ 112 ]. This, therefore, points to shortcomings in actions taken to provide a safe and healthy workplace [ 113 ]. Some of the reasons for the exposure of workers are related to worker oversight in safe operating procedures and neglect of using preventive safety equipment [ 114 ]. Therefore, workers have a moral duty of protecting themselves against risks and hazards [ 109 ]. Gerkin and Doyon-Martin [ 115 ] assert that national governments are to blame, along with corporations, for repeatedly creating workplace conditions that lead to routine violations of OHS regulations associated with occupational health hazards.
Given the context, it is apparent that a safe and healthy workplace is a fundamental worker right to physical health, which is somewhat threatened by occupational hazard presence [ 108 , 112 ]. This state of affairs shows that employers ought to disclose the health risks posed by hazards during pre-employment to afford workers an opportunity to make informed decisions in respect to compensation and performing dangerous work [ 116 ]. In this regard, employers and workers should understand that no amount of economic gain can compensate a workers’ death or serious injury [ 117 ].
From a different perspective, the ODs in Table 1 are a result of cumulative exposure at sufficient exposure doses with different latency periods. In this regard, certain respiratory and skin diseases have long latency durations compared to exposure to allergic chemical hazards, which may trigger immediate responses amongst exposed susceptible workers, regardless of whether exposure concentrations complied with set regulatory limits or not. In view of the long latency of ODs and the associated complex diagnosis of disease aetiology, it is thus apparent that hazard surveillance would allow for targeted intervention on the primary causes of the respective diseases [ 60 ]. The effectiveness of industry-implemented hazard prevention measures with long latency periods, as prescribed in OHS legislation worldwide, currently has limitations in historic biological exposure indices and exposure levels, and their linkages to future ODs remains elusive [ 118 ]—for chemical hazard types, for example. The enacted OHS legislation [ 118 ], technological advancements, improved work practices and a decreasing trend in exposure over the decades should, however, be lauded for its stated intention to eliminate ODs, though quoted statistics indicate that they have not entirely attained this intended goal [ 118 , 119 ].
4.2. Occupational Disease Trends in South African General Industry
The reported ODs in Table 1 are a result of statutory health surveillance for workers occupationally exposed to corresponding hazards in South African general industry [ 33 , 34 , 35 , 37 , 38 , 60 ]. In total, 43,485 ODs were reported and compensated for between the quoted periods of 2001 and 2019 in South African general industry, which showed a declining trend. Noise-induced hearing loss was by far the highest compensated OD in relation to the total proportion of reported diseases in South Africa, a trend also reported in the Russian Federation [ 120 ] and Brazil [ 63 ], and to a lesser extent in China [ 121 ]. Occupational disease morbidity and mortality indicate an urgent need for effective workplace exposure prevention programmes [ 122 ]. An active and effective OD surveillance system can be quick to address emerging mortality and morbidity trends [ 123 ]. These disease surveillance systems record both fatal and non-fatal sentinel ODs, which are linked to occupations.
Of the identified ODs, NIHL is the most pervasive and prevalent inherent of some processes in the manufacturing sector [ 73 , 124 ]. The manufacturing sector consequently has the highest number of noise-exposed workers [ 125 , 126 ]. Workers in different industries, such as coal-fuelled power plants, textile mills, chemical manufacturing plants and steel plants, are also exposed to noise levels above the regulated exposure limits during routine activities [ 19 , 74 , 112 , 126 , 127 , 128 , 129 , 130 ]. Maximum noise levels measured in these sectors can reach 120 dB [ 128 ] and contain different spectral frequencies [ 131 ]. Publicly available noise records show a general reduction in industry noise levels since the late 1970s [ 124 , 132 ]. However, statistics from the US Bureau of Labour Statistics and South African Compensation Fund indicate that NIHL incidence rates still remain high within the manufacturing sector, regardless of the noted reduction [ 23 , 24 , 53 , 54 , 55 , 56 , 57 , 129 , 133 , 134 ], as well as process automation in some operations [ 129 ]. Contrarily, in the United Kingdom, the NIHL incidence rate has remained consistently low [ 135 ], whereas hearing loss is much more prevalent in the Asian manufacturing sector [ 136 ].
In view of the above discourse, it is thus apparent that to detect the impact of occupational hazards on workers, a hazard and disease surveillance system is a necessity and should form part of a country’s capacity-building efforts in OD prevention efforts [ 119 , 137 ]. In South Africa, a data gap remains with regards to the availability of exposure data, national information on employment, total number of occupationally-exposed workers and corresponding exposure levels [ 119 ].
The reviewed South African compensation reports also indicate that the fund continually disburses finances to workers suffering from occupation-induced disabilities. No statistics are available that indicate the actual number of workers under this continuing compensation system. However, the annual costs related to disablement, as indicated on the compensation fund annual reports (where available), ranged between ZAR 1.8 to ZAR 2.5 billion for the reporting period 2001 to 2019. This, therefore, indicates the additional burden placed on the financials of the compensation in South Africa.
Occupational Diseases and Mortality
Exposure to some of the attributable occupational health hazards in Table 1 , specifically carcinogens and poisons, has led to mortality and maiming of workers [ 112 , 121 , 138 ], the extent of which remains largely unknown in part due to an absent population-based occupational health surveillance system. To shed light on this matter, a 2017 Statistics South Africa report on mortality and causes of death in South Africa indicated that tuberculosis, a communicable disease, was the main underlying cause of occupation-related deaths amongst males [ 84 ], which, in general, has historical links to the mining sector. The report further stated that a total of 34,325 deaths were attributable to accidental injury or exposure [ 84 ]. This then highlights the importance of OD prevalence statistics and mortality rates in providing alternative information sources on the subject matter. In this regard, a case study analysing the mortality rate associated with pneumoconiosis in South Africa indicated that workers in the manufacturing sector had an odds ratio of 4.77. In particular, engineers and machinery mechanics were occupations with increased pneumoconiosis deaths, with an odds ratio calculated at 6.85 [ 100 ].
To highlight the prevailing mortality and morbidity trends associated with workplace exposure on an international scale, studies from the United States [ 139 ], China [ 138 ] and Italy [ 140 ] linked historic worker chemical exposure to mortality [ 139 , 140 ]. Of the physical stressors, analysis of statistics from the United States Bureau of Labour Statistics showed that heat exposure accounted for some 32% of exposure-related fatalities between 2000 and 2010 [ 122 ]. The increase in mortality rate points to priority areas of disease prevention [ 141 ].
Mortality and morbidity rates are themselves influenced by factors such as duration of employment at a job [ 142 , 143 ] and regional and lifestyle factors [ 143 ]. Amidst the above discourse, there is, however, a pressing need for methodological alignment for studies investigating exposure/outcome links [ 144 ], which can be fulfilled by a national OD and injury surveillance system. Mortalities and morbidities linked to historic workplace exposure indicate that afflicted workers are paying the ultimate price from these chronic and oft-cumulative exposures.
5. Conclusions
Despite the enactment of occupational health and safety legislation, some occupational health and safety hazards remain unabated, as it is an accepted reality that it is impossible to eliminate all occupational health hazards. Thus, hazardous workplaces and occupations should be prioritised for hazard control, training and occupational health services [ 90 ]. Workplace studies reporting noncompliance to hazards, such as noise, thermal stresses, vibration, electromagnetic fields, ionising radiation, chemical substances and dust should spring labour inspectorates into intensive enforcement activities [ 19 ].
As all occupational diseases and injuries are man-made and preventable [ 145 ], their prevalence thereof points to shortcomings in industry-implemented preventive measures, inclusive of health and safety laws, exposure limits and protective measures. Workers employed in industry bear the economic and disease burden associated with exposure. Workplace morbidity and mortality statistics in South Africa indicate that workers exposed to identified occupational hazards continue to pay the ultimate price through fatalities, for example, in cases of diagnoses related to carcinogens, apart from poisonings. Of the occupational diseases, noise-induced hearing loss incidence remains high in general industry amidst technological advancement in the design of quieter equipment; this finding is most revealing. Even though the impact of noise on workers and its control is well researched, exposure continues. Thus, innovative interventions to curb this problem are required [ 146 ]. Even though the quoted OD statistics indicate a declining trend, a welcomed development, such a decline has unresolved peculiarities.
A national hazard and disease surveillance system is a necessary policy tool that can inform efforts in worker protection, such as the identification of high-risk industries inclusive of those with high noise levels. The disease prevalence rates drawn from the system can be used by regulators for targeted intervention programmes [ 147 , 148 ]. Another governmental strategy can be the incentivisation of organisations to implement hazard control initiatives in exchange for a reduction in compensation fund contributions. The positive effects of this incentive scheme were reported by Elsler, Treutlein [ 149 ]. Conclusively, occupational health and safety within South African general industry require urgent reformation and improvements on a regulatory level. This is in view of the paucity of OD and injury statistics from the compensation fund.
Recommendation for the establishment of a national occupational disease and injury surveillance system
In South Africa, the responsible agency for repositing ODs is unclear, but is supposedly and generally accepted as a function of the Compensation Fund, which records ODs emanating from general industry. However, publicly available OD statistics are inconsistently reported with minimal detail. On the other hand, developed countries have national disease surveillance systems in place for collecting and disseminating OD statistics to inform policy intervention. A lack of, or an inefficient, OD surveillance system has been cited by Ding et al. [ 138 ] as a major stumbling block in disease prevention.
Against this backdrop, a systemic national occupational health surveillance system underpinned by preventive policies and registry systems is recommended to enable targeted intervention [ 137 , 150 , 151 ]. The system will collect, tabulate and interpret OD data, which will be a useful input in setting national priorities for the attainment of safe and healthy workplaces [ 152 , 153 ]. Available OD statistics in countries like South African general industry do not have limits to their usefulness. The system can be used to trend OD prevalence, aggregate sectors, categories of exposed workers and health outcomes [ 150 , 151 , 154 ]. Data derived from the surveillance system can further be used for different purposes in both the private and public sectors. As an example, the ensuing data can be used for formulating arguments for and against legislation impact, identification of areas requiring special emphasis by employers, development of regulatory policy, standards and guidance by government agencies, use by analysts and researchers in the evaluation of regulatory effectiveness and identification of factors associated with ODs amongst others [ 155 ]. An added benefit of the system is that it would also contribute to the prevention and management of the economic and societal burdens associated with ODs [ 150 , 151 ]. Collected data from the system could also serve as evidence of the efficacy of introduced preventive measures [ 137 , 152 ], whilst also being applicable in improving worker and employer understanding of occupational risks [ 156 ].
Acknowledgments
This paper is the outcome of a Doctoral Degree in the Environmental Health project, registered with the Tshwane University of Technology, South Africa, as part of a national initiative for training academics, managed by the National Department of Higher Education and Training. The primary researcher was an nGAP-funded student. No limitations were placed on the study.
Non-exhaustive OHS legislative history from South Africa.
* Date and/or month unavailable from reviewed historic documents.
Employment, total accidents, injuries and occupational diseases, 2001-2019 in South African industry.
* Difference in data from Table 1 due to carry-over cases.
Author Contributions
O.R. conceptualised the study, conducted the literature study, drafted and edited the manuscript. T.J.M. and D.M.M. reviewed the technical content and layout of the manuscript. All authors have read and agreed to the published version of the manuscript.
This research received no external funding.
Institutional Review Board Statement
The results presented in this paper form part of a study for which ethical clearance was obtained from the Tshwane University of Technology (TUT) Ethics Committee: FCRE 2020/10/015 (FCPS 02) (SCI).
Informed Consent Statement
Not applicable.
Data Availability Statement
Conflicts of interest.
The authors declare no conflict of interest.
Publisher’s Note: MDPI stays neutral with regard to jurisdictional claims in published maps and institutional affiliations.
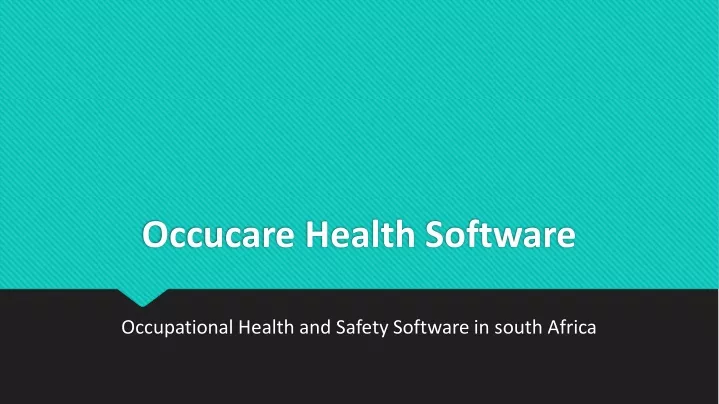
Occupational Health and Safety Software in south Africa
Oct 10, 2022
60 likes | 61 Views
Occucare offers the best occupational health and safety software in South Africa. Cut down the wastage of resources & optimize the use of resources with our health and safety management software.https://www.occucare.co.in/ehs-management-system-software/occupational-health-and-safety-software-south-africa<br><br>
Share Presentation

Presentation Transcript
Occucare Health Software Occupational Health and Safety Software in south Africa
Digitalize the occupational Health and Safety Policies in South Africa With World’s Leading Safety Software! With the advancement of time, the industrial sector is reshaping it’s polices and spreading awareness about the worker’s safety and well-being. The aid of technology is playing a significant role in this transforming journey. South African industries are not exceptions and they also take necessary steps to make a perfect. The South African Institute of occupational Health and Safety is Regulating the compliance process and making necessary amendments to existing Policies. Our 100% client retention speaks stories of our excellence and surely help you to open doors of the safest workplace for your workers. Handle all the safety related issues with ease and design a well-developed roadmap to control and eliminate occupational incidences and their consequences.
Create a Safeguard for your Assets in South Africa With Occucare’s Occupational Health and Safety Software! South Africa is emerging as a new address for the industrial hub in various sectors like mining, energy , and manufacturing. Various reasons like amply supply of semiskilled and unskilled labour , political stability , and infrastructural development attract new-age businesses to lay the foundations stone in this region. Cities like Cape Town, Durban, Pretoria, Port Elizabeth, and others are revamping themselves so that the industries get global exposure. To match the international standards, these industries require a sophisticated approach for providing flawless occupational health and safety in South Africa! Ace software providers like OccuCare, grab this opportunity to launch their products in this southernmost country of the African continent.
Optimize the Use of Resources with Occucare’s Occupational Health And Safety Software! Cut down the wastage of resources and optimize them to provide an efficient and safe workplace in South Africa. Protect your employees from accidental hazards and keep them fit by being proactive in implementing the safety regulations. Let the features like incidence management, permit management, and medical surveillance of OccuCare’s Occupational health and safety software make your workplace more efficient than ever! Provide a cover for not only your employees but also the physical assets and keep them safe with the features like HIRA!
Contact Us Occucare Health Software Address : C/102-103, Ganesh Meridian, Opp. Kargil Petrol Pump, Nr. Gujarat High Court, S.G Highway, Ahmedabad -380060, Gujarat ,India. Mo : 9426442424 Email Id : [email protected]
Thank You For Watching
- More by User
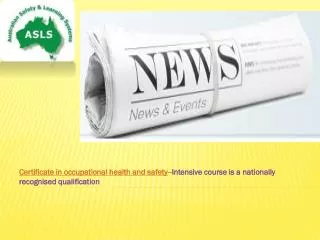
Certificate in occupational health and safety
ASLS has a comprehensive scope of registration for nationally recognised qualifications and accredited short courses as well as developing client specific courses to meet targeted needs.Call us 1300260300 (within Australia),Overseas +61738896600.
202 views • 5 slides
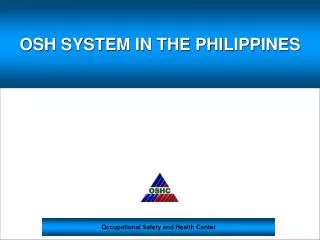
Occupational Safety and Health Center
OSH SYSTEM IN THE PHILIPPINES. Occupational Safety and Health Center. OSH System in the Philippines. At the end of this session, participants will be able to: discuss the OSH system in the country and its components; discuss the key laws and policies to implement OSH system in the country;
2.52k views • 28 slides
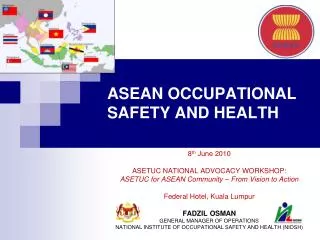
ASEAN OCCUPATIONAL SAFETY AND HEALTH
ASEAN OCCUPATIONAL SAFETY AND HEALTH. 8 th June 2010 ASETUC NATIONAL ADVOCACY WORKSHOP: ASETUC for ASEAN Community – From Vision to Action Federal Hotel, Kuala Lumpur FADZIL OSMAN GENERAL MANAGER OF OPERATIONS NATIONAL INSTITUTE OF OCCUPATIONAL SAFETY AND HEALTH (NIOSH).
709 views • 25 slides

OCCUPATIONAL SAFETY AND HEALTH IN GHANA
OCCUPATIONAL SAFETY AND HEALTH IN GHANA. Ghana has a mixed economy dominated by agriculture, commerce, service and industry. . The emerging oil sector will provide significant impetus to the economy in the foreseeable future.
760 views • 26 slides
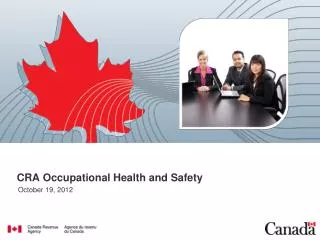
CRA Occupational Health and Safety
CRA Occupational Health and Safety. October 19, 2012. Agenda. OHS Structure & Network Within the CRA OHS Program Focus Work Place Health and Safety Committees CRA Based Resources. OHS Structure. Following OHSAS 18001:2007 Standard. OHS Policy Identify Hazards Accident trends. Reporting
513 views • 17 slides
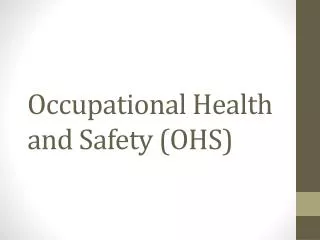
Occupational Health and Safety (OHS)
Occupational Health and Safety (OHS). It is also expected that they can give at least six occupational health and safety (OHS) that are related to computer hardware servicing. The following are the examples of OHS that is related to computer hardware servicing.
1.78k views • 39 slides
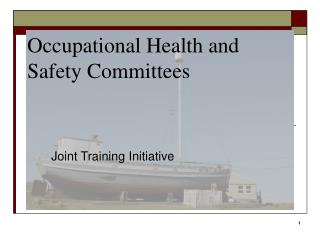
Occupational Health and Safety Committees
Occupational Health and Safety Committees. Joint Training Initiative. Introduction. Your name? Your workplace? Member of OHS Committee for how long? Your role as a committee member? Previous OHS training or experience?.
2.06k views • 156 slides
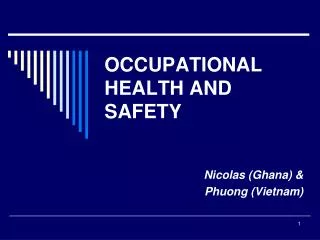
OCCUPATIONAL HEALTH AND SAFETY
OCCUPATIONAL HEALTH AND SAFETY. Nicolas (Ghana) & Phuong (Vietnam). STRATEGIES FOR PHM. 1. Capacity Building on Occupation Health & Safety - Identification of existing national policy/regulation on occupational health and safety - Linkage with any international organization- eg ISO –(EMS)
1.12k views • 8 slides
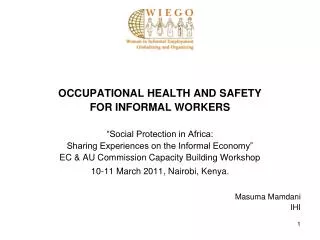
OCCUPATIONAL HEALTH AND SAFETY FOR INFORMAL WORKERS “Social Protection in Africa:
OCCUPATIONAL HEALTH AND SAFETY FOR INFORMAL WORKERS “Social Protection in Africa: Sharing Experiences on the Informal Economy” EC & AU Commission Capacity Building Workshop 10-11 March 2011, Nairobi, Kenya. Masuma Mamdani IHI. WIEGO.
553 views • 35 slides
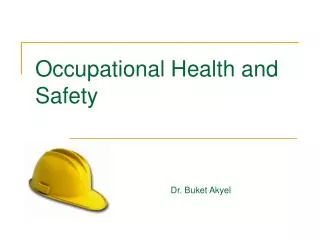
Occupational Health and Safety
Occupational Health and Safety. Dr. Buket Akyel. Occupational Safety and Health Act. OSHA covers private-sector employers with its mission to “ send every worker home whole and healthy every day” Enforces safety and health regulations and provides education and compliance assistance
2.21k views • 11 slides
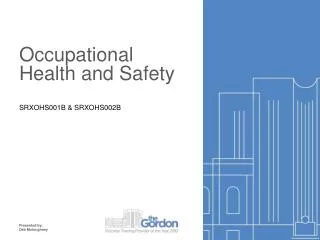
Occupational Health and Safety. SRXOHS001B & SRXOHS002B. Presented by: Deb Moloughney. Types of Laws. Legislation: Victorian: Occupational Health and Safety Act 2004 Commonwealth Occupational Health and Safety ( Cwlth Employment) Act 1991 Others: Transport of Dangerous Goods Acts
1.3k views • 27 slides
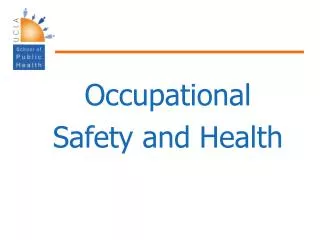
Occupational Safety and Health
Occupational Safety and Health. Public Health. Saves Lives Prevents Disease and Disability Improves the Quality of Health Care Helps Reduce Health Care Costs. Public Health. The field of public health strives to create healthier communities
917 views • 47 slides
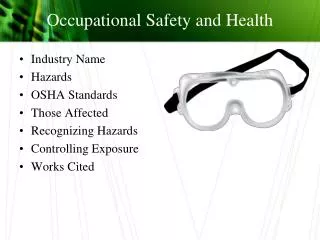
Occupational Safety and Health. Industry Name Hazards OSHA Standards Those Affected Recognizing Hazards Controlling Exposure Works Cited. Industry Name. Enter the name of your industry. Hazards. What are at least three known hazards found in the industry. OSHA Standards.
494 views • 8 slides
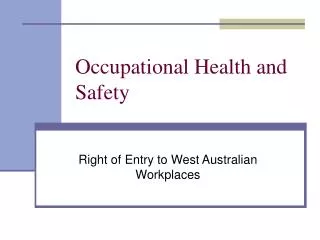
Occupational Health and Safety. Right of Entry to West Australian Workplaces. Relevant Legislation in WA. Workplace Relations Act, 1996 (Workchoices) and Regulations; WA Industrial Relations Act, 1979; WA Occ. Safety and Health Act, 1984: and WA Mines Safety and Inspection Act, 1994.
687 views • 10 slides
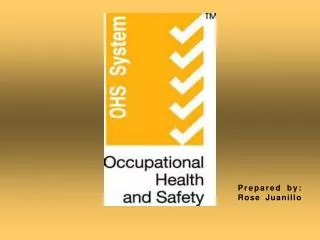
Ensuring worker safety has been one of the ILO’s fundamental missions. The presentation includes comparative items among country members of ASEAN focusing on the Occupational Safety and Health with ILO conventions as the fundamental framework.
2.83k views • 42 slides
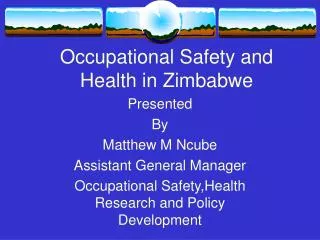
Occupational Safety and Health in Zimbabwe
Occupational Safety and Health in Zimbabwe. Presented By Matthew M Ncube Assistant General Manager Occupational Safety,Health Research and Policy Development. NATIONAL PROGRAM FOCUS. WORKER WORK ENVIRONMENT COMMUNITY ENVIRONMENT. CORE OPERATIONAL PROGRAM OBJECTIVES.
618 views • 14 slides
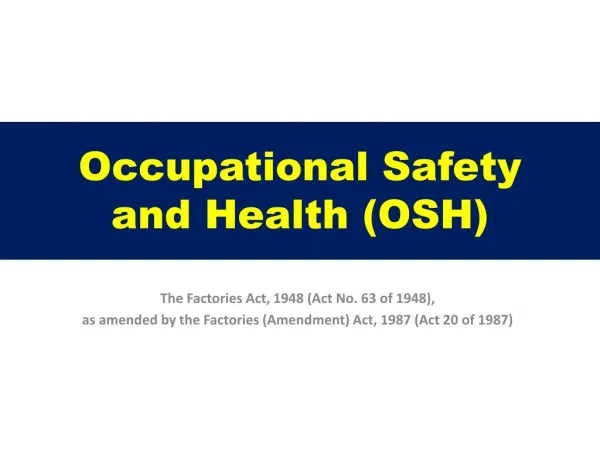
To train the workmen on industrial safety and adherence of safety rules.
2.79k views • 66 slides
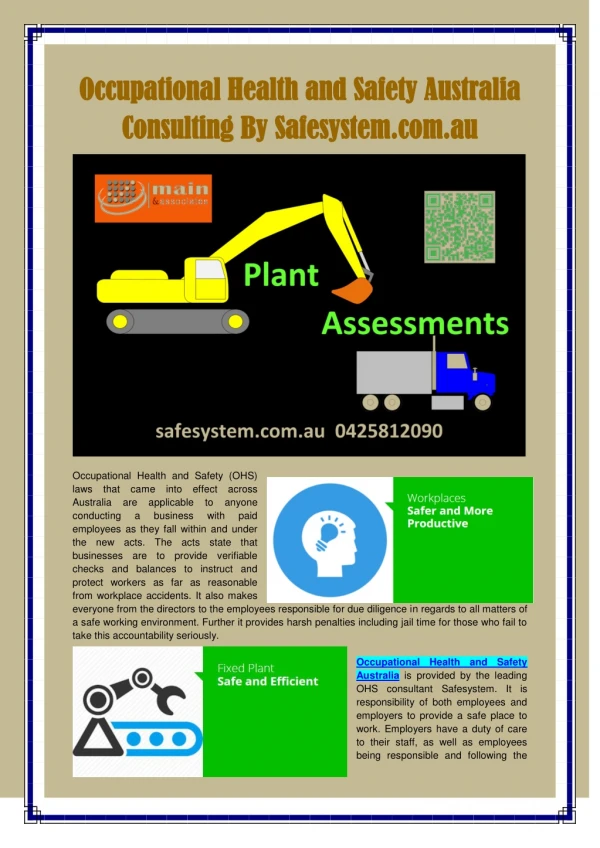
Occupational Health And Safety Australia
Main & Associates are experts in risk management and compliance. We tailor and strategies specific OHS systems for small to medium businesses and develop compliant processes that will save you time and money. http://safesystem.com.au/
92 views • 2 slides
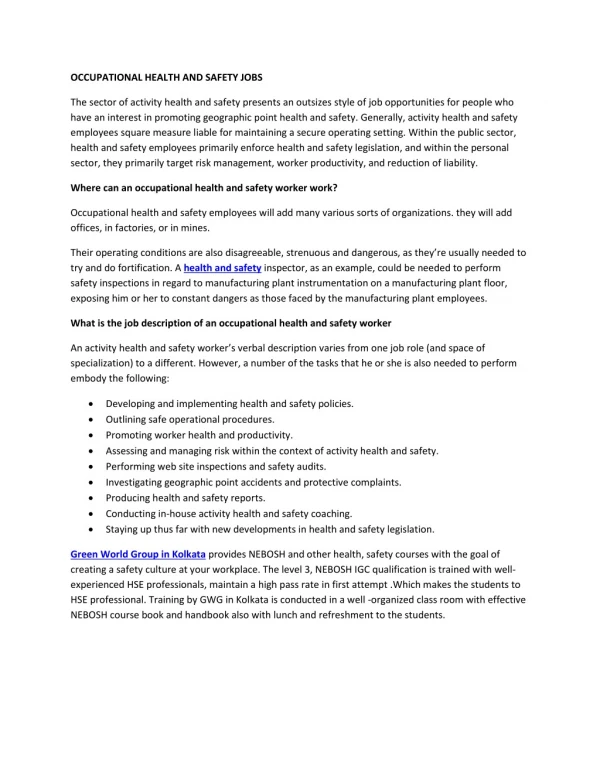
Career in Occupational Health and Safety
Occupational health and safety employees will add many various sorts of organizations. they will add offices, in factories, or in mines. Their operating conditions are also disagreeable, strenuous and dangerous, as they’re usually needed to try and do fortification.
45 views • 1 slides
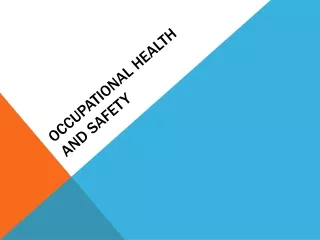
Occupational Health and Safety . Time Table Semester One. “The Safe Workplace”. Legislative Framework. Victorian workplaces are covered by the OHS Act 2004 OHS Act 2004 Regulations eg. Confined Space Entry Codes of Practice Compliance Codes Australian Standards Guidelines and Advice.
2.01k views • 111 slides
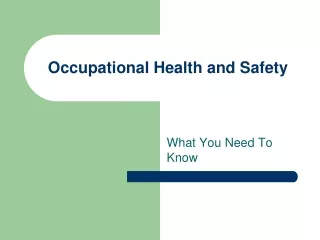
Occupational Health and Safety. What You Need To Know. Before we begin here’s something to think about. We all deserve to go home safe at the end of each day. TRUE OR FALSE. DO YOU THINK YOU HAVE THE RIGHT TO A SAFE WORKPLACE?. BOTH.
1.4k views • 29 slides
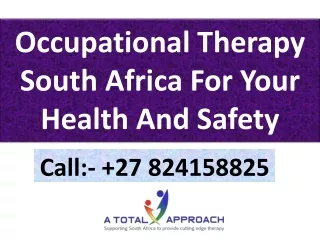
Occupational Therapy South Africa For Your Health And Safety
Occupational therapists and occupational therapy South Africa assist people across the lifetime to participate in the things they want and need to go through the healing use of regular activities. Occupational therapists help patients recover their ability to perform duties in living situations.
61 views • 6 slides
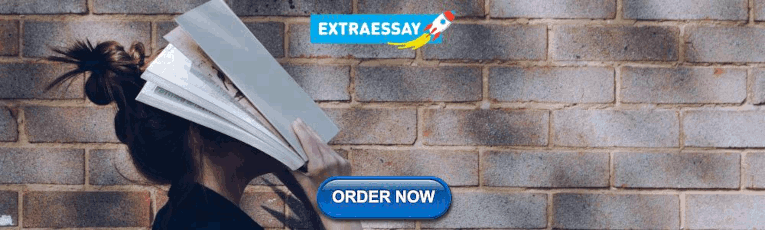
IMAGES
VIDEO
COMMENTS
The Occupational Health and Safety Act no. 85 of 1993, requires every employer to take all necessary steps that all persons at work receive first aid treatment in case of injury or emergency. Fire Control Security Service commits itself to: The General Safety Regulations (3) on First Aid, Emergency Equipment and Procedures.
Occupational health and safety in the Republic of South Africa is more than a century old with inspectors operating in health and safety towards the end of the 19th century. This coincided with the rapid development of the industry after the discovery of diamonds in the 1860's and the discovery of gold in the 1880's.
The Occupational Health and Safety Act, 1993, requires the employer to bring about and maintain, as far as reasonably practicable, a work environment that is safe and without risk to the health of the workers. This means that the employer must ensure that the workplace is free of hazardous substances, such as benzene, chlorine and micro ...
Download ppt "Theme 7: Occupational Health and Safety Act 85 of 1993". Purpose of the Act To provide for the health and safety of persons at work and for the health and safety of persons in connection with the use of plant and machinery; the protection of persons other than persons at work against hazards to health and safety arising out of or ...
View Occupational Health And Safety South Africa PPTs online, safely and virus-free! Many are downloadable. Learn new and interesting things. Get ideas for your own presentations. Share yours for free!
Presentation Transcript. OCCUPATIONAL HEALTH AND SAFETY ACT & OHH POLICYREVIEW DEPARTMENT OF LABOUR OCCUPATIONAL HEALTH AND SAFETY M ruiters. Historical account of the Acts The very first legislation introduced into South Africa covered both Industrial safety and conditions of employment: • The very first Act was the Factories Act 28 of 1918 ...
The Minerals Council South Africa established the Learning Hub in 2009 to encourage mining companies to learn from the pockets of excellence that exist in the i ... Coal Leadership Forum Occupational Health Dialogue with Academia - 15 April 2021 ... Occupational Safety & Health. This website and its content is copyright of the MOSH.
COVID-19 Centenary Webinar - held 21 April 2022. S-10) Prof Daan Kocks - SASOM presentation. S-07) Mr David Msiza - DMRE presentation (21.04.2022) S-12) Prof Cas Badenhorst - SAIOH presentation (21.04.2022) S-18+19) Prof Mohamed Jeebhay & Prof Rajen Naidoo - Recommendations (21.04.2022) Prof Koleka Mlisana: NHLS Response to Pandemic.
All downloads are provided by the department of labour Legislation No. 85 of 1993: Occupational Health and Safety Act as amended by Occupational Health and Safety Amendment Act, No. 181 Of 1993 Regulations Driven machinery regulation (word) Construction regulation (word) Asbestos Regulations (word) Lift escalator and passenger conveyer regulations (word) Electrical Installation Regulations ...
Poverty. Safety and health at work. Areas of work. OSH is a FPRW. National OSH Frameworks. OSH Management Systems. Biological Hazards and Risks. Occupational Health. Chemical Safety and the Environment.
Occupational Health and Safety in South Africa therefore remains fragmented with various Government Departments claiming jurisdiction over various areas leading to confusion at times for clients. 13. The Bill seeks to provide for the health and safety of persons at work and for the health and safety of persons in connection with the
1.2 The Occupational Health and Safety Act . Health and safety in the workplace is guided primarily by the Occupational Health and Safety Act (85 of 1993). We call it the OHS Act. 1.2.1 Purpose of the OHS Act "To provide for the health and safety of persons at work and for the health and safety of persons in connection
• Macun I, The Regulation of Health and Safety in South Africa's Manufacturing, University of Cape Town, 1989. • Myers J.E and Macun I. The Sociologic Context of Occupational Health in South Africa ., Am J Public Health 1989; 79:213-221 • Zwi, A et al, Occupational Health and Safety in South Africa :The perspectives of Capital , State and
General Machinery Regulations, 1988. General Safety Regulations: General Safety Regulations, 1986. First aid, 2021. Hazardous Biological Agents Regulations: Hazardous Biological Agents, 2022. Hazardous Biological Agents Managing the Risks on the Health Care Premises. Hazardous Chemical Agents Regulations: RHCA, 2021.
The South African Qualifications Authority (SAQA) has confirmed that the South African Institute of Occupational Safety and Health (Saiosh) is the recognised professional body for Occupational Health and Safety in South Africa. Saiosh was approved by SAQA as a Professional Body for the purpose of the NQF Act, Act 67 of 2008.
Background: Globally, access to occupational health and safety (OHS) by workers has remained at very low levels. The organization and implementation of OHS in South Africa, Zimbabwe, Zambia, and ...
Occupational Health & Safety Training. NOSA is South Africa's leading occupational health, safety and environmental training provider, offering more than 100 safety-related training courses, skills programmes and qualifications which hold various local and international accreditations.
Conclusively, occupational health and safety within South African general industry require urgent reformation and improvements on a regulatory level. This is in view of the paucity of OD and injury statistics from the compensation fund. ... South Africa Occupational Health and Safety Act and Regulations (85 of 1993) [(accessed on 28 November ...
act85of1993.pdf. 2.2 MB. 85 of 1993. The Occupational Health and Safety Act 85 of 1993 intends: to provide for the health and safety of persons at work and for the health and safety of persons in connection with the use of plant and machinery; the protection of persons other than persons at work against hazards to health and safety arising out ...
Occupational Health and Safety Software in south Africa An Image/Link below is provided (as is) to download presentation Download Policy: Content on the Website is provided to you AS IS for your information and personal use and may not be sold / licensed / shared on other websites without getting consent from its author.
Occupational Health Safety jobs now available in Dormerton, KwaZulu-Natal 4138. Product Consultant, Human Resources Specialist, Resident Engineer and more on Indeed.com. ... (South Africa) Purpose of Position: To supply clients with an efficient And professional service. To co-ordinate workflow of specimens in order to ensure effective service ...