- Business Essentials
- Leadership & Management
- Credential of Leadership, Impact, and Management in Business (CLIMB)
- Entrepreneurship & Innovation
- Digital Transformation
- Finance & Accounting
- Business in Society
- For Organizations
- Support Portal
- Media Coverage
- Founding Donors
- Leadership Team
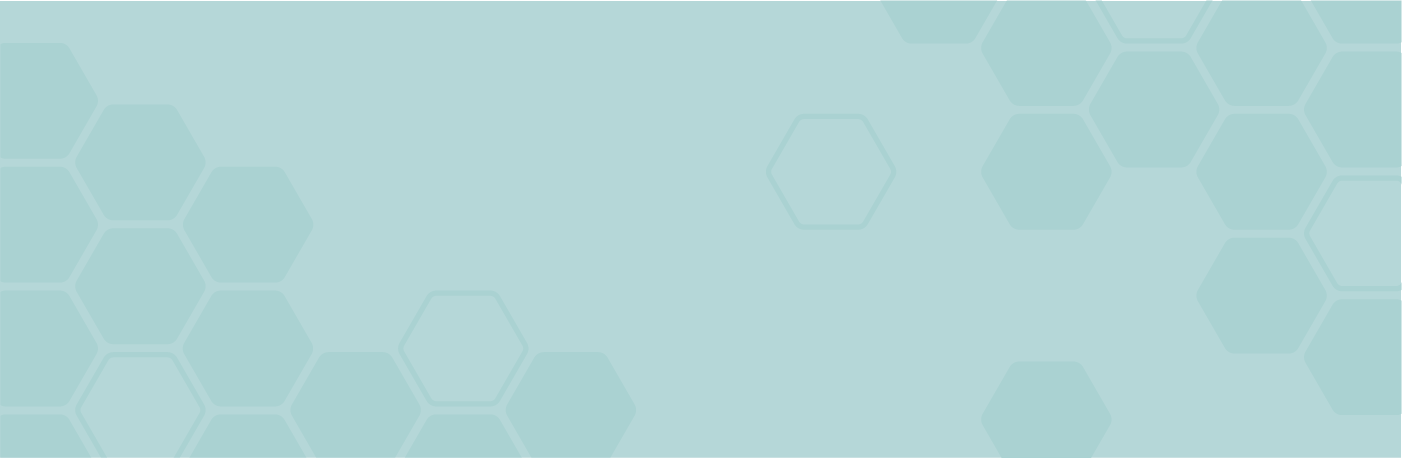
- Harvard Business School →
- HBS Online →
- Business Insights →
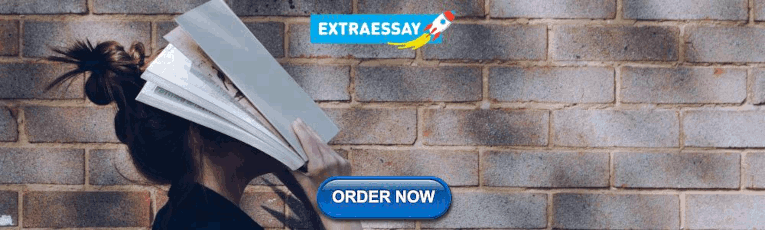
Business Insights
Harvard Business School Online's Business Insights Blog provides the career insights you need to achieve your goals and gain confidence in your business skills.
- Career Development
- Communication
- Decision-Making
- Earning Your MBA
- Negotiation
- News & Events
- Productivity
- Staff Spotlight
- Student Profiles
- Work-Life Balance
- AI Essentials for Business
- Alternative Investments
- Business Analytics
- Business Strategy
- Business and Climate Change
- Design Thinking and Innovation
- Digital Marketing Strategy
- Disruptive Strategy
- Economics for Managers
- Entrepreneurship Essentials
- Financial Accounting
- Global Business
- Launching Tech Ventures
- Leadership Principles
- Leadership, Ethics, and Corporate Accountability
- Leading with Finance
- Management Essentials
- Negotiation Mastery
- Organizational Leadership
- Power and Influence for Positive Impact
- Strategy Execution
- Sustainable Business Strategy
- Sustainable Investing
- Winning with Digital Platforms
Root Cause Analysis: What It Is & How to Perform One
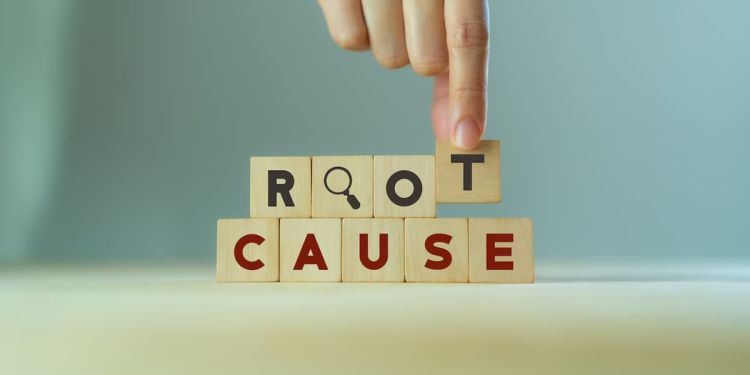
- 07 Mar 2023
The problems that affect a company’s success don’t always result from not understanding how to solve them. In many cases, their root causes aren’t easily identified. That’s why root cause analysis is vital to organizational leadership .
According to research described in the Harvard Business Review , 85 percent of executives believe their organizations are bad at diagnosing problems, and 87 percent think that flaw carries significant costs. As a result, more businesses seek organizational leaders who avoid costly mistakes.
If you’re a leader who wants to problem-solve effectively, here’s an overview of root cause analysis and why it’s important in organizational leadership.
Access your free e-book today.
What Is Root Cause Analysis?
According to the online course Organizational Leadership —taught by Harvard Business School professors Joshua Margolis and Anthony Mayo— root cause analysis is the process of articulating problems’ causes to suggest specific solutions.
“Leaders must perform as beacons,” Margolis says in the course. “Namely, scanning and analyzing the landscape around the organization and identifying current and emerging trends, pressures, threats, and opportunities.”
By working with others to understand a problem’s root cause, you can generate a solution. If you’re interested in performing a root cause analysis for your organization, here are eight steps you must take.
8 Essential Steps of an Organizational Root Cause Analysis
1. identify performance or opportunity gaps.
The first step in a root cause analysis is identifying the most important performance or opportunity gaps facing your team, department, or organization. Performance gaps are the ways in which your organization falls short or fails to deliver on its capabilities; opportunity gaps reflect something new or innovative it can do to create value.
Finding those gaps requires leveraging the “leader as beacon” form of leadership.
“Leaders are called upon to illuminate what's going on outside and around the organization,” Margolis says in Organizational Leadership , “identifying both challenges and opportunities and how they inform the organization's future direction.”
Without those insights, you can’t reap the benefits an effective root cause analysis can produce because external forces—including industry trends, competitors, and the economy—can affect your company’s long-term success.
2. Create an Organizational Challenge Statement
The next step is writing an organizational challenge statement explaining what the gap is and why it’s important. The statement should be three to four sentences and encapsulate the challenge’s essence.
It’s crucial to explain where your organization falls short, what problems that poses, and why it matters. Describe the gap and why you must urgently address it.
A critical responsibility is deciding which gap requires the most attention, then focusing your analysis on it. Concentrating on too many problems at once can dilute positive results.
To prioritize issues, consider which are the most time-sensitive and mission-critical, followed by which can make stakeholders happy.
3. Analyze Findings with Colleagues
It's essential to work with colleagues to gain different perspectives on a problem and its root causes. This involves understanding the problem, gathering information, and developing a comprehensive analysis.
While this can be challenging when you’re a new organizational leader, using the double helix of leadership —the coevolutionary process of executing organizational leadership's responsibilities while developing the capabilities to perform them—can help foster collaboration.
Research shows diverse ideas improve high-level decision-making, which is why you should connect with colleagues with different opinions and expertise to enhance your root cause analysis’s outcome.
4. Formulate Value-Creating Activities
Next, determine what your company must do to address your organizational challenge statement. Establish three to five value-creating activities for your team, department, or organization to close the performance or opportunity gap you’ve identified.
This requires communicating organizational direction —a clear and compelling path forward that ensures stakeholders know and work toward the same goal.
“Setting direction is typically a reciprocal process,” Margolis says in Organizational Leadership . “You don't sit down and decide your direction, nor do you input your analysis of the external context into a formula and solve for a direction. Rather, setting direction is a back-and-forth process; you move between the value you'd like to create for customers, employees, investors, and your grasp of the context.”

5. Identify Necessary Behavior Changes
Once you’ve outlined activities that can provide value to your company, identify the behavior changes needed to address your organizational challenge statement.
“Your detective work throughout your root cause analysis exposes uncomfortable realities about employee competencies, organizational inefficiencies, departmental infighting, and unclear direction from leadership at multiple levels of the company,” Mayo says in Organizational Leadership .
Factors that can affect your company’s long-term success include:
- Ineffective communication skills
- Resistance to change
- Problematic workplace stereotypes
Not all root cause analyses reveal behaviors that must be eliminated. Sometimes you can identify behaviors to enhance or foster internally, such as:
- Collaboration
- Innovative thinking
- Creative problem-solving
6. Implement Behavior Changes
Although behaviors might be easy to pinpoint, putting them into practice can be challenging.
To ensure you implement the right changes, gauge whether they’ll have a positive or negative impact. According to Organizational Leadership , you should consider the following factors:
- Motivation: Do the people at your organization have a personal desire for and commitment to change?
- Competence: Do they have the skills and know-how to implement change effectively?
- Coordination: Are they willing to work collaboratively to enact change?
Based on your answers, decide what behavior changes are plausible for your root cause analysis.
7. Map Root Causes
The next step in your analysis is mapping the root causes you’ve identified to the components of organizational alignment. Doing so helps you determine which components to adjust or change to implement employee behavior changes successfully.
Three root cause categories unrelated to behavior changes are:
- Systems and structures: The formal organization component, including talent management, product development, and budget and accountability systems
- People: Individuals’ profiles and the workforce’s overall composition, including employees’ skills, experience, values, and attitudes
- Culture: The informal, intangible part of your organization, including the norms, values, attitudes, beliefs, preferences, common practices, and habits of its employees
8. Create an Action Plan
Using your findings from the previous steps, create an action plan for addressing your organizational problem’s root cause and consider your role in it.
To make the action plan achievable, ensure you:
- Identify the problem’s root cause
- Create measurable results
- Ensure clear communication among your team
“One useful way to assess your potential impact on the challenge is to understand your locus of control,” Mayo says in Organizational Leadership , “or the extent to which you can personally drive the needed change or improvement.”
The best way to illustrate your control is by using three concentric circles: the innermost circle being full control of resources, the middle circle representing your ability to influence but not control, and the outermost circle alluding to shifts outside both your influence and control.
Consider these circles when implementing your action plan to ensure your goals don’t overreach.

The Importance of Root Cause Analysis in Organizational Leadership
Root cause analysis is a critical organizational leadership skill for effectively addressing problems and driving change. It helps you understand shifting conditions around your company and confirm that your efforts are relevant and sustainable.
As a leader, you must not only effect change but understand why it’s needed. Taking an online course, such as Organizational Leadership , can enable you to gain that knowledge.
Using root cause analysis, you can identify the issues behind your organization’s problems, develop a plan to address them, and make impactful changes.
Are you preparing to transition to a new leadership role? Enroll in our online certificate course Organizational Leadership —one of our leadership and management courses —and learn how to perform an effective root cause analysis to ensure your company’s long-term success. To learn more about what it takes to be an effective leader, download our free leadership e-book .

About the Author
Advisory boards aren’t only for executives. Join the LogRocket Content Advisory Board today →
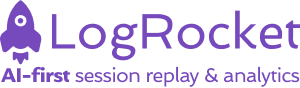
- Product Management
- Solve User-Reported Issues
- Find Issues Faster
- Optimize Conversion and Adoption
Better problem solving with root cause analysis (with template)
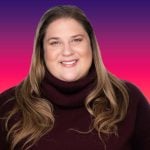
If you walk into your kitchen to find your favorite vase smashed on the floor, it might be safe to assume that the grinning cat nearby was the root cause of this problem. If only it was this simple in business and we could just say “the cat did it.” Product problems are often much more complex and connected to a variety of root causes.
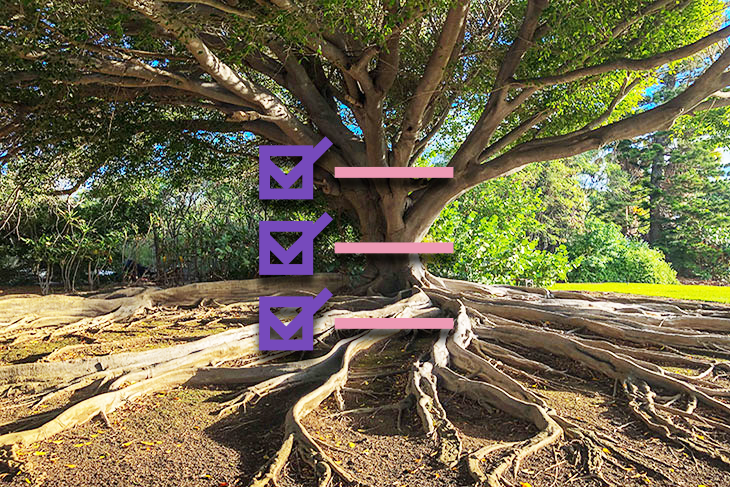
If you think of a weed, the surface is only the problem you can immediately see. However, if you cut the weed from the ground level, it’s likely to grow back from the root. This is just like fixing product problems with a band-aid with little to no investigation of a root cause — it’s likely to return.
These types of problems need a more thorough root cause analysis (RCA) to determine how, and why the problem happened, and how to prevent it in the future.
What is root cause analysis?
Root cause analysis is a tool you can utilize when determining the true cause of a problem. You might have assumptions about what the cause of a problem might be or experience biases towards one as the main cause.
Performing a root cause analysis can help you determine what the underlying causes of a problem are to help address a more impactful and valuable solution:
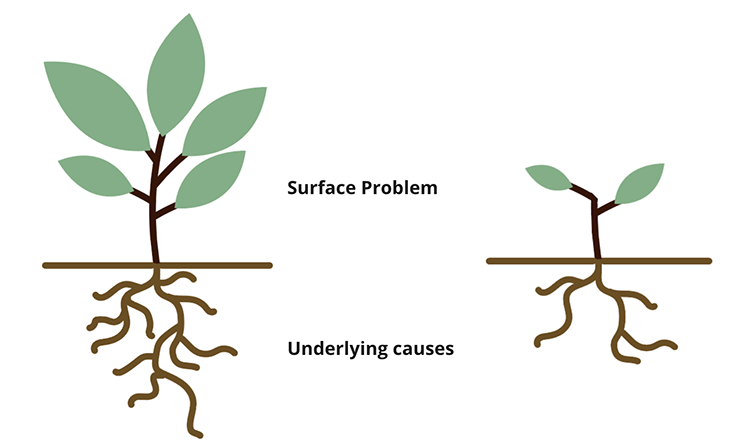
What are the 4 steps in a root cause analysis?
When you’re trying to uncover the roots of a problem, it can be daunting to figure out where to start. The process to conduct a root cause analysis can be broken down into a few easy steps:
- Define the problem
- Identify and map the problem causes
- Identify the evidence that supports your causes
- Create a root cause analysis report and set up your action plan
1. Define the problem
A clear definition of the problem is the first step. Sometimes problems are easy to identify, like a broken link. More often, problems can be abstract and need clarification, like a decrease in overall purchases through a site or an increase in bugs reported.
Here are some more examples of problems:
- A 20 percent drop in customer purchases placed from the shopping cart page from the previous week
- 60 percent of customers on hold end up dropping their call and, as a result, the company has experienced a decrease in NPS scores
- A 40 percent increase of customer reported issues with using the folders feature in a CRM
- A 15 percent decrease in user engagement with a core feature on a social media site
It’s also critical to understand how to define a problem:
2. Identify and map the problem causes
Using tools like a fishbone analysis and the Five Whys framework can help you put together causes and start to categorize themes of the problem. When going through a Five Whys diagram, try to come up with a few alternate pathways and you might notice overlapping areas.
Each example of a Five Whys diagram is accurate, but only looking at one cause can prevent you from understanding the fuller picture. For example, there was more than one reason why the Fyre Festival failed and it’s important to identify overlapping themes to avoid leaning on only one cause:
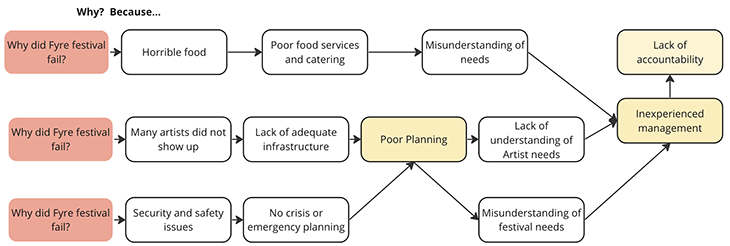
In a product example, there might be numerous reasons why session times have decreased, or user reported bugs are up.
After evaluating the size, impact, general cause themes, and urgency of the problem, you’ll have a better understanding of how much effort will be needed for the analysis. The larger the problem on the surface, the more underlying causes you might find. Even simple problems can sometimes have numerous causes to consider and you need to determine how in-depth you need to dig to “unroot” the causes.
It’s also critical to check all your bases. Once you have evaluated and categorized the different potential causes to a problem, use the following as a checklist to ensure you’re covering all areas of where and how this problem happened. Be sure to identify any changes or recent events that might have occurred that could have impacted the problem.
- Demographics : is the problem happening to one specific demographic? Only happening to iPhone users? Users in a specific location?
- Time specific : when did the problem happen? Is it continuing to happen? Did the problem only occur during a specific time? You might discover that the problem is related to a time-specific cause, like a release or outage
- User journey : did anything change within the user journey? Map the workflow to determine if any new developments have occurred
- External factors : is this an issue with a third party integration? Did a competitor launch a successful new feature that might be taking business from you? Some of these external factors could be out of your control, but important to recognize
- Internal factors : how many feature releases happened during this time frame? Was there any product downtime or maintenance at that time?
3. Identify the evidence that supports your causes
Collecting evidence is a key part of a root cause analysis. Without evidence, your problem causes are based on assumptions and potentially harmful biases.
Start evaluating any data you might have available. Using session replay tools like LogRocket can help you collect evidence of the problem. Here are a couple of examples of the type of data that can be used to collect evidence:
- User count — number of users impacted by the problem
- Usage — daily, weekly, or monthly active users and a decrease or increase in session time
- Decrease or increase in events — for example, a decrease in users selecting the Add to cart button from a page or an increase in error pages
- Error tracking and user frustration — tools like LogRocket can help track where things are going wrong in your product and surface critical issues
- Qualitative evidence — run user interviews or user-submitted feedback with tools like Loom. Are multiple users running into the same roadblock? Are you seeing the same complaint from multiple users in feedback tickets?
4. Create a root cause analysis report and set up your action plan
Collect your evidence and root cause evaluation into an RCA template. Once you have your causes identified and your discovery efforts into one root cause analysis report, you can start creating a plan to address the problem and prevent it from happening in the future.
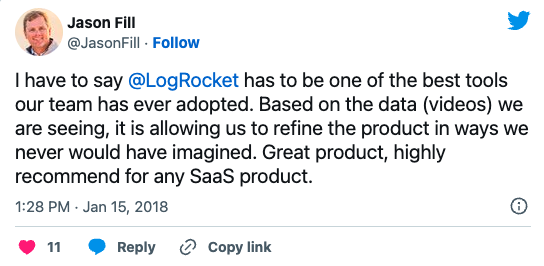
Over 200k developers and product managers use LogRocket to create better digital experiences

Collaborate with a team to brainstorm solutions and discuss which options might address multiple causes. Evaluate if you need both a short-term and long-term solution, depending on the level of effort and urgency required. As part of your analysis report, discuss how you can avoid this problem again in the future and any other risk mitigation plans.
Root cause analysis template
You can use this root cause analysis template on Google Sheets to organization your investigation, collect your evidence, and share with your team to determine next step solutions:
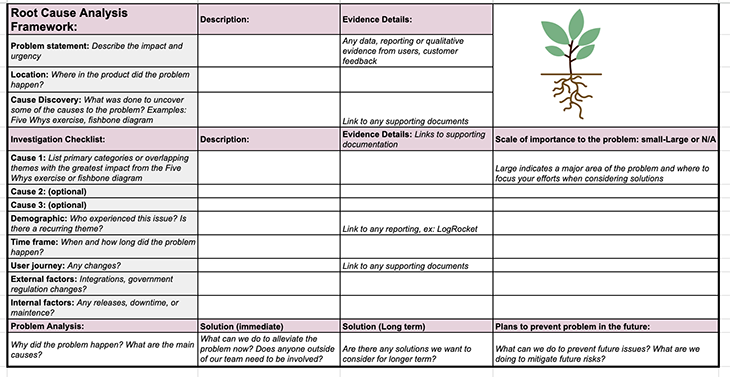
Root cause analysis example
Below is an RCA for Company B, a tax preparation product that experienced an increase in dropped customer calls.
Company B experienced an increase of 60 percent of customers on hold that ended up dropping their call. They also experienced an increase in NPS dissatisfaction and have concerns about losing customers.
After going through a root cause analysis, they discovered an 80 percent increase in user calls during tax season. This increase of call volume indicated much longer wait times to speak to a live agent.
After investigating some of the customer call reasons, they discovered that numerous customers had simple questions that could be answered quickly without too much support.
Company B gathered call logs that confirmed their suspicions. They brought the logs together that demonstrated the simplicity of repeated questions and gathered records of customers that dropped off after a certain amount of time on the phone.
Company B implemented a conversational AI chatbot that could answer generic questions and direct more complex questions to a live agent. Further, they implemented tooltips throughout the tax process flow to help users that appeared to be stuck.
Through the RCA process, you might discover that some parts of the user’s experience are confusing and create a plan to address minor UI challenges.
These solutions helped Company B improve their accessibility and scalability needs during an increase in call volume, without having to add more employee support. Going forward, Company B can plan to monitor call times and continuously evaluate customer service topics to determine where users might need further support and guidance in the future:
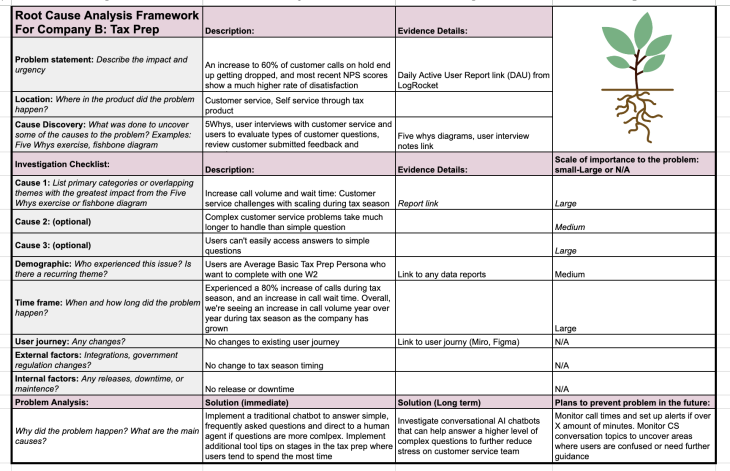
Common mistakes to avoid
There are a number of easy-to-fall-into traps when performing root cause analysis, including:
- Don’t rely on assumptions when determining root causes. Use evidence to support to disprove a cause
- Don’t limit your investigation. Go beyond one Five Why framework and be sure to exhaust all possibilities to avoid leaning on the first cause
- Don’t rely on the first idea — come up with multiple solutions to solve a problem
- Don’t work alone. Collaborating with a team will help you come up with a variety of potential solutions or new opportunities
- Don’t think this is a one-time thing. Prepare for the future and discuss risk management and mitigation if you expect this problem to happen again, especially with issues that might be related to factors out of your control. What’s the worst that can happen, and what can we do about it to make sure the problem is addressed quickly with minimal interruption?
Final thoughts
A root cause analysis can be a great tool to help you uncover the true causes of a problem and reduce any reliance on assumptions or biases. With the right investigation and evidence collection, you can learn more about how and why a problem happened and identify causes below the surface.
RCA can ensure your solutions address the root problem and help you better plan for the future.
Featured image source: IconScout
LogRocket generates product insights that lead to meaningful action
Get your teams on the same page — try LogRocket today.
Share this:
- Click to share on Twitter (Opens in new window)
- Click to share on Reddit (Opens in new window)
- Click to share on LinkedIn (Opens in new window)
- Click to share on Facebook (Opens in new window)
- #product strategy
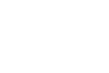
Stop guessing about your digital experience with LogRocket
Recent posts:.
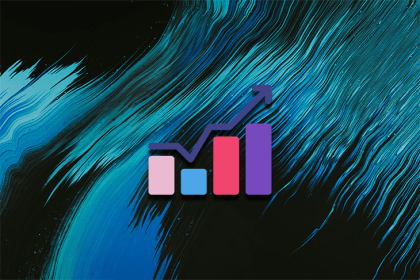
How to connect business metrics to customer opportunities
I often help product teams move from reactive, stakeholder-driven ways of working to strategic, outcome-driven ways. In this process, I […]
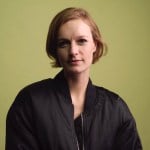
Essential leadership traits for modern product managers
Successful product managers are strategic thinkers, customer-focused innovators, adaptive problem solvers, and inspirational motivators.
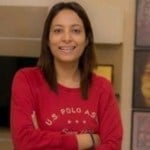
Leader Spotlight: Understanding the root of the strategy, with Angela Suthrave
Angela Suthrave talks about the importance of understanding the assumptions, foundations, and boundaries behind a strategy.
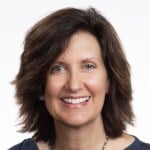
What is a pivot in business? Strategies and implications
A pivot helps organizations (established or start-ups) to seek better growth opportunities and respond swiftly to market feedback.
Leave a Reply Cancel reply
tableau.com is not available in your region.
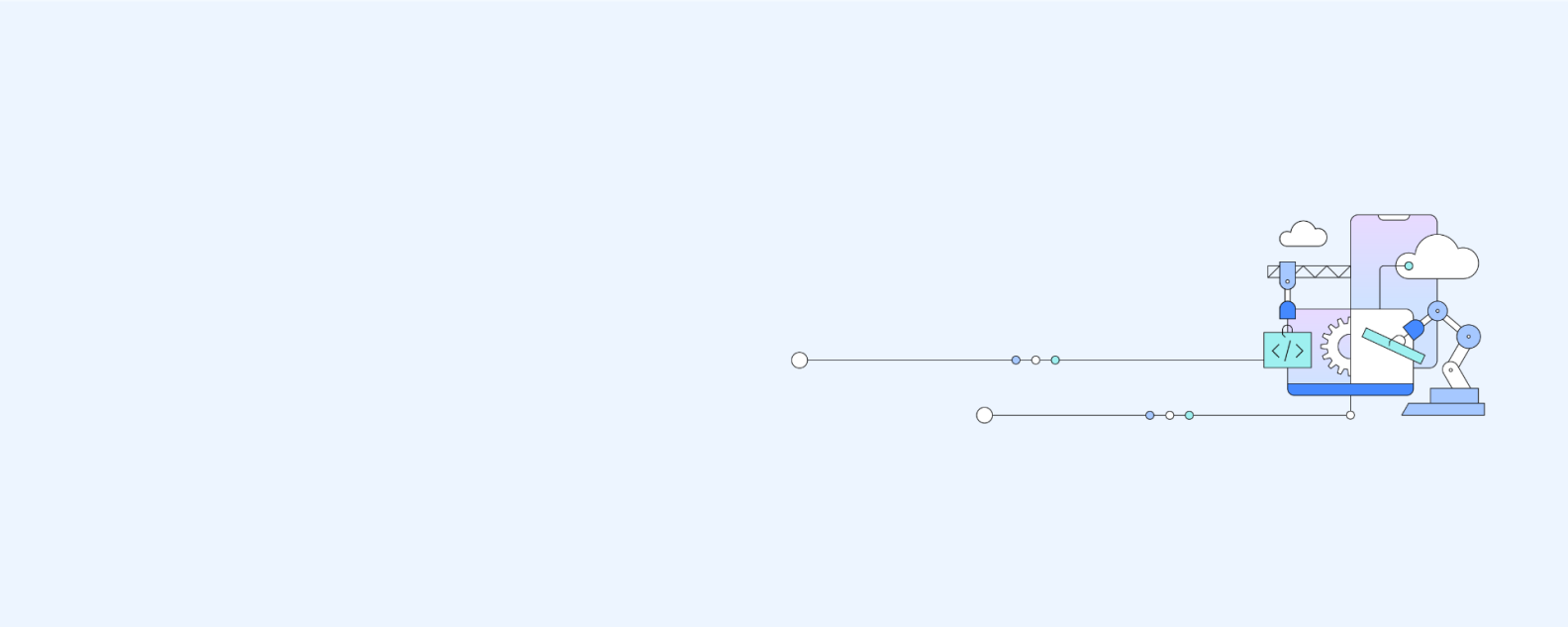
Root cause analysis (RCA) is the quality management process by which an organization searches for the root of a problem, issue or incident after it occurs.
Issues and mishaps are inevitable in any organization, even in the best of circumstances. While it could be tempting to simply address symptoms of the problem as they materialize, addressing symptoms is an inherently reactive process that all but guarantees a recurring—and often worsening—series of problems.
Ethical, proactive, well-run companies and organizations with a reactive approach will both encounter problems, but the former will experience fewer and recover faster because they prioritize root cause analyses.
Root cause analysis helps organizations decipher the root cause of the problem, identify the appropriate corrective actions and develop a plan to prevent future occurrences. It aims to implement solutions to the underlying problem for more efficient operations overall.
Learn how next-generation detection devices shift asset management services from routine maintenance regimes to predictive, AI-powered processes.
Delve into our exclusive guide to the EU's CSRD
Organizations perform root cause analyses when a problem arises or an incident occurs, but there are any number of issues that need an RCA. Triggers for a root cause analysis fall into three broad categories.
When real-world materials or equipment fails in some way (for example, a desktop computer stops working or a component from a third-party vendor delivers substandard performance).
When people make mistakes or fail to complete required tasks (for example, an employee fails to perform regular maintenance on a piece of equipment, causing it to break down).
A breakdown in a system, process or policy people use to make decisions (for example, a company fails to train team members on cybersecurity protocols, leaving the company vulnerable to cyberattacks ).
Organizations can conduct root cause analyses for a range or reasons, from commonplace email service disruptions to catastrophic equipment failures. Regardless of the nature or scope of the issue, performing root cause analysis should include the same fundamental steps.
If you have decided to conduct a root cause analysis, your department or organization is likely experiencing some acute issue, or at least looking to make substantive improvements to a particular process. Therefore, the first step of the root cause analysis process should be identifying and defining the problem that you want to address. Without a clearly defined problem, it is impossible to correctly identify the root causes.
When the department has a clear idea of the problem, it’s time to draft a problem statement spelling out the issue for everyone who will help with the RCA.
Once the issue is identified and clearly articulated to all involved parties, leadership should create a project charter, which will assemble a team to complete the analysis. The team should include a facilitator to lead the team through the analysis and any team members with either personal or professional knowledge of the systems, processes and incidents that you will investigate.
Data collection is the foundation of the problem-solving process. It is vital, at this stage, to find every piece of information that can help you identify contributing factors and ultimately the root causes of the issue. This can include collecting photographs and incident reports, conducting interviews with affected parties and reviewing existing policies and procedures. Some questions that you may want to ask during data collection:
- When did the problem start and how long has it been going on?
- What symptoms has the team observed?
- What documentation does the organization or department must prove that an issue exists?
- How will the issue affect employees and other stakeholders?
- Who is harmed or otherwise affected by the existence of this problem?
This is the most important step in the RCA process. At this point, the team has collected all necessary information and starts to brainstorm for causal factors. Effective root cause analyses require openness to all potential underlying causes of an issue, so everyone on the RCA team should enter the brainstorming stage with an open mind. Avoid attempts to determine root causes until every possibility is identified and vetted; starting the incident investigation process with preconceived notions may bias the results and make it more difficult to determine the real root cause.
Once the RCA team has an exhaustive list of possible causes and contributing factors, it is time to determine the root causes of the issue. Analyze every possible cause and examine the actual impact of each one to figure out which possibilities are the most problematic, which ones have similarities and which ones can be altogether eliminated. Be prepared for the possibility that there are multiple root causes to the issue.
After the team narrows the list of possibilities, rank the remaining potential root causes by their impact and the likelihood they are the root cause of the problem. Leadership will examine and analyze each possibility and collaborate with the RCA team to determine the actual root causes.
Once the team settles on root causes and has laid out all the details of the issue, they must start brainstorming solutions. The solution should directly address the root causes, with consideration for the logistics of executing the solution and any potential obstacles the team may encounter along the way. These elements will comprise the action plan that will help the team address the current problem and prevent recurrences.
While all RCAs will include the same basic steps, there are myriad root cause analysis methods that can help an organization collect data efficiently and effectively. Typically, a company will select a method and use root cause analysis tools, such as analysis templates and software, to complete the process.
The 5 Whys approach is rooted in the idea that asking five “Why?” questions can get you to the root cause of anything. 5 Whys implores problem solvers to avoid assumptions and continue to ask “why” until they identify the root cause of a problem. In the case of a formalized organizational root cause analysis, a team may only need to ask three whys to find the root cause, but they may also need to ask 50 or 60. The purpose of 5 Whys is to push the team to ask as many questions as is necessary to find the correct answers.
A failure mode and effects analysis is one of the most rigorous approaches to root cause analysis. Similar to a risk analysis, FMEA identifies every possibility for system/process failure and examines the potential impact of each hypothetical failure. The organization then addresses every root cause that is likely to result in failure.
Pareto charts combine the features of bar charts and line charts to understand the frequency of the organization’s most common root causes. The chart displays root causes in descending order of frequency, starting with the most common and probable. The team then addresses the root cause whose solution provides the most significant benefit to the organization.
An impact analysis allows an organization to assess both the positive and negative potential impacts of each possible root cause.
Change analyses are helpful in situations where a system or process’s performance changed significantly. When conducting this type of RCA, the department looks at how the circumstances surrounding the issue or incident have changed over time. Examining changes in personal, information, infrastructure, or data, among other factors, can help the organization understand which factors caused the change in performance.
An event analysis is commonly used to identify the cause of major, single-event problem, like an oil spill or building collapse. Event analyses rely on quick (but thorough) evidence-gathering processes to recreate the sequence of events that that led to the incident. Once the timeline is established, the organization can more easily identify the causal and contributing factors.
Also known as a causal factor analysis, a causal factor tree analysis allows an organization to record and visually display—using a causal factor tree—every decision, event or action that led to a particular problem.
An Ishikawa diagram (or Fishbone diagram) is a cause-and-effect style diagram that visualizes the circumstances surrounding a problem. The diagram resembles a fish skeleton, with a long list of causes grouped into related subcategories.
DMAIC is an acronym for the Define, Measure, Analyze, Improve and Control process. This data-driven process improvement methodology serves as a part of an organization’s Six Sigma practices.
This RCA methodology proposes finding the root cause of an issue by moving through a four-step problem solving process. The process starts with situation analysis and continues with problem analysis and solution analysis, concluding with potential problem analysis.
An FTA allows an organization to visually map potential causal relationships and identify root causes using boolean logic.
Barrier analyses are based on the idea that proper barriers can prevent problems and incidents. This type of RCA, often used in risk management, examines how the absence of appropriate barriers led to an issue and makes suggestions for installing barriers that prevent the issue from reoccurring.
Companies that use the RCA process want to put an end to “firefighting” and treating the symptoms of a problem. Instead, they want to optimize business operations, reduce risk and provide a better customer experience. Investing in the root cause analysis process provides a framework for better overall decision-making and allows an organization to benefit from:
Continuous improvement : Root cause analysis is an iterative process, seeking not only to address acute issues, but also to improve the entire system over time, starting with the underlying cause. The iterative nature of root cause analysis empowers organizations to prioritize continuous process improvement.
Increased productivity : Preventing downtime, delays, worker attrition and other production issues within an organization saves employees time, freeing up bandwidth to focus on other critical tasks.
Reduced costs : When equipment breaks down or software bugs cause delays, organizations lose money and workers get frustrated. Root cause analysis helps eliminate the cost of continually fixing a recurring issue, resulting in a more financially efficient operation overall.
Better defect detection : When companies fail to address underlying issues, they can inadvertently affect the quality of the end product. Addressing persistent problems before they snowball protects the organization from revenue and reputational losses that are associated with product defects down the line.
Reduced risks : Improving business processes and systems keeps equipment running safely and helps workers avoid safety hazards in the workplace.
Intelligent asset management, monitoring, predictive maintenance and reliability in a single platform.
AIOps Insights is a SaaS solution that addresses and solves for the problems central IT operations teams face in managing the availability of enterprise IT resources through AI-powered event and incident management.
Enhance your application performance monitoring to provide the context you need to resolve incidents faster.
IBM research proposes an approach to detect abnormality and analyzes root causes using Spark log files.
Learn how IBM Instana provides precision hybrid cloud observability, metrics, traces and logs.
Downer and IBM are using smart preventative maintenance to keep passengers on Australia's light and heavy rail systems moving safely, reliably, comfortably and more sustainably.
- Guide: Root Cause Analysis
Daniel Croft
Daniel Croft is an experienced continuous improvement manager with a Lean Six Sigma Black Belt and a Bachelor's degree in Business Management. With more than ten years of experience applying his skills across various industries, Daniel specializes in optimizing processes and improving efficiency. His approach combines practical experience with a deep understanding of business fundamentals to drive meaningful change.
- Last Updated: September 5, 2023
- Learn Lean Sigma
Root Cause Analysis (RCA) is a key tool in continuous improvement, acting as a systematic approach to identify and tackle the underlying issues behind problems. RCA aims not only to provide a temporary fix but to offer long-lasting solutions by addressing the root causes.
RCA, such as the Fishbone Diagram , the 5 Whys , and FMEA . Whether you’re looking to solve complex challenges or improve cost-efficiency, this guide will offer understanding of how to identify the root cause of problems with useful Lean Six Sigma tools.
Table of Contents
What is root cause analysis.
Root Cause Analysis, often referred to as RCA, is like being a detective for problems in your business or project. Imagine you have a leaking pipe in your house. You could keep mopping up the water every time it leaks, but that’s not really solving the issue. The right thing to do is find out why it’s leaking in the first place and fix that. RCA works the same way; it helps you find out the “why” behind a problem so you can fix it for good.
Structured Approach
When we say RCA is a “structured approach,” we mean it’s not just random guesswork. It’s a planned way to dig deep into a problem. You will follow certain steps and use specific tools to figure out what’s really going on. This makes sure you’re not just treating the “symptoms” of the problem, like mopping up water from a leak, but you’re finding out why the problem is happening in the first place.
Identify Underlying Reasons
The “underlying reasons” are the real culprits behind a problem. For example, if a machine in a factory keeps breaking down, simply repairing it each time isn’t enough. You need to find out why it’s breaking down. Is it old? Are people using it wrong? RCA helps you answer these kinds of questions.
Long-term Solutions
The coolest part about RCA is that it’s focused on long-term solutions. Once you know the root cause of a problem, you can create a fix that will (hopefully) make sure it never happens again. This is way better than just putting out fires all the time.
By understanding and using RCA, you’re not just stopping at “What is the problem?” You’re going the extra mile to ask, “Why did this problem happen?” and “How can we make sure it doesn’t happen again?” That’s a game-changer in making things better for the long run.
Importance of Root Cause Analysis
Understanding the “why” behind a problem isn’t just something that’s nice to do; it’s crucial for several reasons.
Problem Solving
Imagine you have a puzzle, but all the pieces are jumbled up. Trying to see the whole picture from this mess would be overwhelming, right? RCA is like sorting these puzzle pieces into groups; maybe by color or edge pieces versus middle pieces. When you break down a big, complex problem into smaller parts, it becomes much easier to solve. RCA helps you dissect a problem into its basic elements so you can tackle each one individually. This makes it easier to find out what’s really going wrong and fix it.
Cost-Efficiency
You know the saying, “Time is money”? Well, constantly fixing the same problem over and over again is like throwing both time and money down the drain. If you use RCA to get to the bottom of an issue and solve it at its root, that issue is less likely to come back. This means you spend less time, effort, and money on it in the future. For a business, this is a big deal because it means you can focus on growing and improving, rather than fixing the same old problems. This is where most businesses fail to progress as they spend the day to day activities fire fighting repreated problems.
Quality Improvement
Let’s say you run a bakery, and you notice that your chocolate chip cookies are coming out burnt too often. You could just toss the burnt cookies and make a new batch, but that doesn’t stop the next batch from burning too. If you use RCA to find out why they’re burning—maybe the oven temperature is wrong or the baking time is too long—you can fix that issue and make perfect cookies every time. This makes your customers happy and keeps them coming back. In the same way, RCA helps you improve the quality of your products or services by fixing the real issues, not just the symptoms. This leads to happier customers and better reviews, which are good for any business.
Types of Root Cause Analysis Methods
When it comes to finding the real reason behind a problem, one size doesn’t fit all. Different situations may require different approaches. That’s why there are several methods for conducting RCA. Let’s explore three of the most commonly used methods.
Fishbone Diagram (Ishikawa)
Imagine a fish. The head represents the problem you’re facing, and the bones branching off from the fish’s spine are the possible causes of the problem. This is what a Fishbone Diagram looks like. Also known as an Ishikawa Diagram or Cause and Effect Diagram, this method helps you visually break down a problem into different categories or “themes.”
For example, if you’re running a restaurant and customers are complaining about long wait times, you could use a Fishbone Diagram to categorize potential causes into themes like ‘Staffing,’ ‘Kitchen Efficiency,’ ‘Order Process,’ etc. Within each theme, you list out possible root causes. This helps you see the whole picture and makes it easier to identify where the real issue might be coming from.
You can learn more about the fishbone diagram process with our guide
Remember being a curious kid and asking “Why?” about everything? The 5 Whys method is pretty much the same. Start with the problem at hand and ask “Why did this happen?” Once you have an answer, ask “Why?” again, digging deeper. Keep asking “Why?” until you’ve asked it five times or until you reach a point where the root cause becomes clear.
For example, if a machine in a factory stops working, you could ask:
- Why did the machine stop? (Answer: The motor burned out.)
- Why did the motor burn out? (Answer: The motor was overloaded.)
- Why was the motor overloaded? (Answer: The machine was running at high capacity for too long.)
- Why was the machine running at high capacity for so long? (Answer: There was a backlog of orders.)
- Why was there a backlog of orders? (Root Cause: Poor planning and scheduling.)
- This helps you trace back the chain of events to find the root cause of the problem.
You can learn more about the 5 Whys process with our guide.
FMEA (Failure Modes and Effects Analysis)
FMEA is like looking into a crystal ball to see what could go wrong in the future. It’s a way to evaluate different ways a process or product could fail and to understand the impact of those failures. You list out all possible failure modes, how likely they are to happen, how bad the impact would be, and how well you could detect them before they cause problems. This helps you prioritize which potential issues need immediate attention.
Below is an example from a manufacturing business. The higher the RPN (risk priority number) the more important it is to address the issue.
You can learn more about the FMEA with our guide
Selecting an RCA method
If you are new to root cause analysis it can be difficult knowing which approach to use to solve your problem. This can be made simpler by considering the below
Is the problem simple and straightforward?
Use The 5 Whys Method
Is the problem complex with multiple factors?
Use Fishbone Diagram (Ishikawa)
Is a quantitative risk assessment needed?
Use FMEA (Failure Modes and Effects Analysis)
Use other specialized RCA techniques or hybrid methods
The Five-Step RCA Process
RCA isn’t something you can do haphazardly; it requires a structured approach to be effective. That’s where the Five-Step RCA Process comes in handy. It provides a roadmap to tackle your problem methodically. Let’s start by discussing the first step in detail.
Step 1: Define the Problem
Before you can find a solution to any problem, you need to know exactly what that problem is. You’d be surprised how often people jump to fixing things without clearly understanding what’s wrong in the first place. Defining the problem is like setting the GPS before going on a trip; it sets the direction for everything that follows. Here’s how to go about it:
Be Specific
Let’s say you’re running a coffee shop, and you notice that customers aren’t coming back. Simply saying, “Business is slow,” is too vague. A more specific problem statement would be, “Customer return rate has dropped by 20% in the last two months.”
Numbers don’t lie. Whenever possible, use data to define your problem. In the coffee shop example, you could look at sales records, customer surveys, or loyalty program participation to pinpoint the decline.
Consider the 5 Ws
- Who: Who is affected by this problem? Is it just one department, the whole company, or maybe your customers?
- What: What exactly is the issue? Try to describe it in one sentence.
- Where: Where is this problem occurring? Is it in a specific location or across various places?
- When: When did you first notice this problem? Is it a constant issue or does it happen only at certain times?
- Why: At this stage, you may not know the root cause, but you might have some initial thoughts on why the problem might be occurring.
Write it Down
Once you’ve gathered all this information, write down your problem statement. This serves as a reference point for everyone involved in the RCA process, making sure everyone is on the same page.
After gathering all the relevant information, the problem statement for RCA could be:
“The rejection rate for Widget A produced on Line 3 has increased by 15% in Q2 2023 compared to Q1 2023, predominantly due to ‘Cracked Surface’ defects. This issue first became apparent at the beginning of Q2 and has been consistent since. Initial observations suggest it may be due to material quality or machine calibration issues.”
Step 2: Gather Data
Once you’ve clearly defined the problem, the next step is like being a detective gathering clues. You’ll need to collect all the relevant information that will help you get to the bottom of the issue. This stage is crucial because the quality of your Root Cause Analysis depends on the quality of your data. Here’s how to go about it:
Identify Data Sources
First, figure out where you can get the information you need. This could be anything from company records and employee interviews to customer surveys and machine logs. For example, if your problem is a decrease in product quality, you might look at manufacturing data, quality control reports, and customer feedback.
Types of Data to Collect
- Quantitative Data : These are numerical data that can be measured. Examples include sales figures, production rates, and customer satisfaction scores.
- Qualitative Data : These are descriptive data that can be observed but not measured. Examples include employee morale, customer comments, and the observable state of machinery or processes.
Timing Matters
When did the problem start? Was it gradual or sudden? Understanding the timeline can offer important insights into potential causes. Collect historical data if possible, as this will help you see trends and patterns.
Use Tools to Collect Data
Depending on your needs, various tools can help in data collection. Spreadsheets can be useful for tracking numbers and metrics. Surveys and questionnaires can capture customer or employee feedback. Advanced organizations may use specialized software for data collection and analysis.
Document Everything
Make sure to keep a record of all the data you collect. Organize the data in a way that’s easy to understand and analyze. Charts, graphs, or tables can be helpful here.
Verify Your Data
Before you move on to analyzing the data, make sure it’s accurate and reliable. Double-check your numbers, verify survey results, and confirm any observations. The last thing you want is to make important decisions based on faulty information.
Gathering data might seem like a time-consuming step, but it’s essential for a successful Root Cause Analysis. The more thorough you are at this stage, the easier it will be to identify the actual root cause of the problem later on.
Example Collected Data
Here’s a snapshot of what some of the collected data could look like:
Machine Logs (June 2023)
Quality control reports (june 2023), employee interviews.
- Operators have noticed the machine making unusual noises.
- Quality control staff report an increase in defects that look like cracks on the surface.
Step 3: Identify Possible Causes
After you’ve defined your problem and collected all the relevant data, it’s time to roll up your sleeves and dig into the “why” behind the issue. This step is like brainstorming, but more structured. You’re trying to come up with a list of all the things that could possibly be causing the problem you’ve identified. Here’s how to do it:
Choose a Method
As mentioned earlier, there are various methods you can use to identify possible causes. Two of the most common are the Fishbone Diagram and the 5 Whys. The choice depends on the nature of your problem.
- Fishbone Diagram: This is good for complex problems where multiple factors could be at play. The diagram allows you to visually organize potential causes into different categories, making it easier to focus your investigation.
- The 5 Whys: This method is more straightforward and works well for simpler problems. By repeatedly asking “Why?” you dig deeper into the issue until you identify possible root causes.
Involve the Right People
Don’t try to do this all on your own. Involve team members who are familiar with the problem area. They can offer valuable insights you might not have considered. If you’re dealing with a technical issue, for instance, having an engineer in the room can be incredibly helpful.
Generate a List of Possible Causes
Using your chosen method, start listing down all the potential causes. Be as comprehensive as possible. If you’re using a Fishbone Diagram, for instance, you’d list potential causes under each category or “bone” of the fish. For the 5 Whys, you’d document the chain of reasoning that leads you to potential root causes.
Use Your Data
Remember the data you collected in Step 2? Now’s the time to use it. Align your list of possible causes with the data to see which ones are most likely. For example, if one of your potential causes is “Poor Training,” but your data shows that all employees have completed mandatory training, then you might want to reconsider that cause.
Prioritize Causes
Not all causes are created equal. Some are more likely than others to be the root cause of your problem. Use your team’s expertise and the data you’ve collected to prioritize which causes to investigate further.
By the end of this step, you should have a well-organized list of possible causes for your problem, backed by data and expert input. This sets the stage for the next steps, where you’ll zero in on the actual root cause and figure out how to fix it.
Example of Identifying Possible causes
Following on with the same example, as this is a more complex issue with multiple factors, it makes sense to conduct the root cause analysis using the Fishbone method. Therefore, we need to ensure to include the right people—a cross-functional team. In this case, that would comprise production engineers who understand the machinery, quality control experts who have the data on defects, and machine operators who can provide firsthand experience and observations.
The next step is to collectively brainstorm and categorize potential causes for the increased rejection rate in Widget A. Utilizing the Fishbone Diagram, the team breaks down the problem into six major categories: Machine, Method, Material, Manpower, Environment, and Measurement.
Identifying the possible causes in our example
Following on with the same example, as this is a more complex issue with multiple factors, it makes sense to conduct the root cause analysis using the Fishbone method. Therefore, we need to ensure to include the right people—a cross-functional team. In this case, that would comprise production engineers who understand the machinery, quality control experts who have the data on defects, and machine operators who can provide firsthand experience and observations. The next step is to collectively brainstorm and categorize potential causes for the increased rejection rate in Widget A. Utilizing the Fishbone Diagram, the team breaks down the problem into six major categories: Machine, Method, Material, Manpower, Environment, and Measurement.
Step 4: Determine the Root Cause
After identifying a list of possible causes, it’s time to put on your detective hat again and figure out which one is the real culprit—the root cause of your problem.
This is a critical step, as identifying the wrong cause can lead you down a path of ineffective solutions. Here’s how to go about it:
Review Your List of Possible Causes
Start by revisiting the list you made in the previous step. This will serve as your “suspect list” in identifying the root cause. At this point, you’ve already done some initial prioritization, so you have an idea of which causes are most likely.
Analyze the Data
Remember the data you collected in Step 2? Now is the time to dive deep into it. Compare each possible cause against the data to see if it holds up. Look for patterns, correlations, or anomalies that might point to one cause over the others.
For example, if you’re dealing with a decrease in product quality and one of your possible causes is “Faulty Raw Materials,” you could look at inspection reports, batch numbers, and supplier records to see if there’s a correlation.
Conduct Tests or Experiments
Sometimes, analyzing existing data isn’t enough. You might need to conduct additional tests or experiments to validate or rule out possible causes. For instance, if you suspect a machine is malfunctioning and causing a problem, you might run it under controlled conditions to see if the issue repeats.
Use Logical Reasoning
Sometimes the root cause isn’t obvious, even with data and testing. In such cases, logical reasoning can help. You might use deductive reasoning to rule out unlikely causes or inductive reasoning to generalize from specific observations.
Involve Experts
If you’re stuck or the root cause isn’t clear, don’t hesitate to consult experts. These could be internal team members with specific expertise or external consultants who specialize in the problem area you’re investigating.
Confirm the Root Cause
Before you move on to finding a solution, make sure you’ve found the real root cause and not just a symptom of a deeper issue. Validate your findings by asking:
- Does this cause explain most or all of the problem?
- If we fix this, is it likely that the problem will be solved?
- Do most team members agree that this is the root cause?
Once you’ve determined the root cause, document it clearly. You’ll use this information in the next step to develop and implement a solution that addresses the issue at its core, ensuring it’s less likely to recur in the future.
Determining the Root Cause of our Example
Continuing with our example, the cross-functional team now shifts its focus to determining the root cause of the increased rejection rate for Widget A. Armed with their prioritized list of possible causes and the data gathered, they delve into the next step of the RCA process.
The team begins by revisiting the “suspect list” generated using the Fishbone Diagram. Machine-related factors, particularly temperature fluctuations, pressure inconsistencies, and cycle time variability, are at the top of this list, followed by material quality concerns. Analyze the Data Digging deeper into the data collected, the team finds that the temperature, pressure, and cycle time increases directly correlate with the spike in the ‘Cracked Surface’ defect type. They also note that the unusual noises observed by machine operators started to occur around the same time the defects increased. Conduct Tests or Experiments To validate these observations, the team decides to run the molding machine under controlled conditions, varying one parameter at a time while keeping the others constant. After a series of tests, they discover that an increase in temperature directly leads to the ‘Cracked Surface’ defects in the widgets. Use Logical Reasoning Using deductive reasoning, the team rules out other possible causes. For instance, since all operators have completed mandatory training and the material batches show no signs of contamination, these are less likely to be the root causes. Confirm the Root Cause After careful consideration and validation, the team reaches a consensus that the root cause of the problem is “Temperature Fluctuations in the Molding Machine.” This conclusion satisfies the criteria for root cause identification: It explains most, if not all, of the ‘Cracked Surface’ defects. Fixing this issue is likely to resolve the problem. Most team members agree that this is the root cause. The team documents this root cause clearly and prepares for the next step in the RCA process: developing and implementing a solution that will fix this issue at its core, thereby preventing its recurrence in the future.
Step 5: Implement and Monitor Solutions
Congratulations, you’ve identified the root cause! But your journey doesn’t end here. The whole point of Root Cause Analysis (RCA) is to not just find the root cause but to fix it so the problem doesn’t happen again. This is where Step 5 comes in, where you implement solutions and make sure they actually work. Here’s how to go about it:
Develop a Solution Plan
The first thing you need to do is come up with a plan for how you’re going to fix the root cause you’ve identified. This should include:
- What needs to be done: The specific actions that will address the root cause.
- Who will do it: The people responsible for each action.
- When it will be done: A timeline for implementation.
- How it will be done: The resources and methods needed to implement the solution.
Gain Approval and Support
Before you start making changes, make sure you have the necessary approvals. This might mean getting a budget approved or getting buy-in from key stakeholders. The more support you have, the smoother the implementation process will be.
Implement the Solution
Now it’s time to roll up your sleeves and get to work. Follow the plan you’ve developed, and start implementing the solution. This could involve anything from retraining staff and revising procedures to repairing equipment or introducing new technology.
Monitor Effectiveness
You can’t just implement a solution and walk away. You need to monitor how well it’s working. This means going back to the data you collected in Step 2 and continuing to track those metrics. Are they showing improvement? If not, you may need to revisit your solution or even go back to earlier steps in the RCA process.
Make Adjustments as Needed
Sometimes a solution that looks great on paper doesn’t work out as well in the real world. If you find that your solution isn’t as effective as you’d hoped, be prepared to make adjustments. This could mean tweaking your current solution or going back to the drawing board to identify a different root cause.
Document the Process
Don’t forget to document everything you’ve done, from the solutions you implemented to the results you achieved. This documentation can be invaluable for future problem-solving efforts and for creating a knowledge base that can help prevent similar problems in the future.
Implementing and monitoring solutions of our example
After identifying “Temperature Fluctuations in the Molding Machine” as the root cause, the team crafts a detailed solution plan: What Needs to Be Done : Overhaul the machine’s cooling system and recalibrate temperature settings. Who Will Do It : A dedicated team of production engineers and machine operators. When It Will Be Done : To be completed within a two-week timeframe. How It Will Be Done : Allocate necessary resources like new cooling components and software for recalibration.
Gain Approval and Support Before proceeding, the team prepares a budget proposal and secures approval from management. They also consult with the quality control team and machine operators to gain their buy-in, ensuring a smoother implementation process. Implement the Solution The team then sets out to execute the plan. The cooling system is overhauled, and the machine is recalibrated. A pilot run is conducted to ensure that the new settings are effective in maintaining consistent temperature levels. Monitor Effectiveness After implementing the changes, the team goes back to the data. They continue to monitor the same metrics—temperature, pressure, cycle time, and defect count. Initial results show a significant reduction in the ‘Cracked Surface’ defect type. The temperature fluctuations have notably decreased. Make Adjustments as Needed While the initial results are promising, the team remains vigilant. They agree to meet bi-weekly to review the data and make any necessary adjustments to the solution. So far, no further modifications are required. Document the Process The entire RCA process, from problem identification to solution implementation and monitoring, is meticulously documented. This documentation will serve as a valuable resource for future troubleshooting and continuous improvement initiatives. By diligently following this five-step RCA process, the team has not only identified the root cause of the problem but has also successfully implemented a solution to prevent its recurrence.
RCA is more than just a problem-solving method; it’s a strategic approach that dives deep into issues to eliminate them at their source. By following the Five-Step RCA Process, organizations can not only identify the real culprits behind their problems but also develop and implement long-lasting solutions. This guide walked you through each step in detail, from defining the problem to monitoring the effectiveness of your solutions. Remember, the quality of your RCA is as good as the effort and attention to detail you put into it. Whether you’re looking to improve product quality, enhance customer satisfaction, or increase cost-efficiency, a well-executed RCA can be a game-changing tool in your continuous improvement arsenal. It’s not just about fixing what’s broken; it’s about building something better for the long term.
- Williams, P.M., 2001, April. Techniques for root cause analysis . In Baylor University Medical Center Proceedings (Vol. 14, No. 2, pp. 154-157). Taylor & Francis.
- Gangidi, P., 2018. A systematic approach to root cause analysis using 3× 5 why’s technique. International Journal of Lean Six Sigma , 10 (1), pp.295-310.
- Wong, K.C., Woo, K.Z. and Woo, K.H., 2016. Ishikawa diagram. Quality Improvement in Behavioral Health , pp.119-132.
Q: Why is Root Cause Analysis important?
A: Identifying and resolving the root cause of an issue is crucial for achieving sustainable improvements. Focusing only on symptoms can lead to temporary fixes that may mask the underlying problem. RCA helps you understand the systemic issues contributing to a problem, allowing you to put in place measures that result in lasting change.
Q: What are the common methods used for Root Cause Analysis?
A: Several methods are commonly used for Root Cause Analysis, including:
- 5 Whys : A simple technique that involves asking “why” multiple times until the root cause is identified.
- Fishbone Diagram (Ishikawa Diagram) : A visual tool used to categorize potential causes of a problem.
- Fault Tree Analysis : A graphical representation of various probable causes of an issue, arranged in a hierarchical manner.
- Pareto Analysis : Identifying the most significant factors contributing to a problem based on the Pareto principle.
- FMEA (Failure Modes and Effects Analysis) : A structured approach to identifying potential failure modes and their consequences.
Q: How do I start a Root Cause Analysis?
A: Initiating a Root Cause Analysis typically involves the following steps:
- Define the Problem : Clearly articulate what the issue is.
- Collect Data : Gather relevant information and evidence.
- Identify Possible Causes : List potential causes that could be contributing to the problem.
- Analyze : Use RCA methods like the 5 Whys or Fishbone Diagram to dig deeper.
- Identify Root Cause(s) : Through analysis, pinpoint the underlying cause(s).
- Develop and Implement Solutions : Create action plans to address the root cause(s).
- Review : Evaluate the effectiveness of the solutions and make adjustments as needed.
Q: Can Root Cause Analysis be applied to non-manufacturing sectors?
A: Absolutely, Root Cause Analysis is a versatile tool that can be applied in various sectors, including healthcare, IT, logistics, and even the public sector. The principles remain the same: identify the root cause to implement effective, long-term solutions.
Q: What are some common pitfalls to avoid in Root Cause Analysis?
A: Some common pitfalls to be aware of include:
- Rushing the Process : Skipping steps or rushing through them can lead to incorrect conclusions.
- Blaming Individuals : RCA should focus on systemic issues rather than blaming individual employees.
- Ignoring Data : Failing to consult data can result in assumptions that may not be accurate.
- Lack of Follow-Up : Without proper evaluation and adjustment, even good solutions may fail over time.
Daniel Croft is a seasoned continuous improvement manager with a Black Belt in Lean Six Sigma. With over 10 years of real-world application experience across diverse sectors, Daniel has a passion for optimizing processes and fostering a culture of efficiency. He's not just a practitioner but also an avid learner, constantly seeking to expand his knowledge. Outside of his professional life, Daniel has a keen Investing, statistics and knowledge-sharing, which led him to create the website learnleansigma.com, a platform dedicated to Lean Six Sigma and process improvement insights.
Free Lean Six Sigma Templates
Improve your Lean Six Sigma projects with our free templates. They're designed to make implementation and management easier, helping you achieve better results.
Other Guides

Root Cause Analysis (RCA) Methods for Effective Problem Solving
By Status.net Editorial Team on May 8, 2023 — 7 minutes to read
Imagine facing a problem in your organization that keeps recurring despite your best efforts to solve it. You might be addressing the symptoms, but not the underlying cause. This is where root cause analysis (RCA) comes into play. RCA is a systematic approach to identifying the root cause of problems or events, understanding how to fix or compensate for them, and applying the knowledge gained to prevent future issues or replicate successes. In this comprehensive guide to root cause analysis, you’ll learn various methods and techniques for conducting an RCA. You’ll understand how to gather and manage evidence, investigate the people, processes, and systems involved, and determine the key factors leading to the problem or event.
Whether you’re a project manager, a team leader, or simply someone looking to improve your problem-solving skills, this guide will help you grasp the fundamentals of RCA and apply them effectively in your work. As you delve deeper into the world of Root Cause Analysis, you’ll discover how it can turn challenges into opportunities for growth and pave the way for a more efficient and successful future.
Related: 3 Root Cause Analysis Templates (and Examples)
5 Whys: How to Uncover Root Causes [Examples]
Root Cause Analysis Fundamentals
Root Cause Analysis (RCA) is a systematic approach to identify the underlying cause of a problem. By focusing on the root cause, you can effectively address the issue and prevent recurrence. Generally, RCA is used to investigate incidents, eliminate defects, and enhance systems or processes.
RCA aims to achieve the following objectives:
- Determine the root cause of a problem or issue, not just its symptoms.
- Identify and implement solutions that address the root cause and prevent its recurrence.
- Improve understanding of the systems, processes, or components involved to avoid similar issues in the future.
- Foster a proactive and continuous improvement mindset within your organization.
When conducting RCA, maintain an open mind and avoid making assumptions. Utilize critical thinking and involve team members from various disciplines to achieve a comprehensive understanding of the problem.
The RCA Process
Problem identification.
To effectively utilize Root Cause Analysis (RCA), first identify the problem at hand. Determine the specific issue, incident, or failure that needs to be investigated. Clearly define the problem and its impact on your organization’s operations in order to establish a focused and valuable analysis.
Data Collection
Gather relevant data about the problem, including when and where it occurred, who was involved, what processes and systems were affected, and any other important context. Be thorough and systematic in your data collection, and make use of any available documentation, interviews, or observations to build a comprehensive understanding.
Cause Identification
Analyze the collected data to pinpoint potential causes of the problem. This could start with brainstorming and then using tools such as cause-and-effect diagrams or the “5 Whys” technique to delve deeper into the issue. Determine the causes that are most likely to have contributed to the problem and classify them as either root causes or contributing factors.
Solution Implementation
Once you have identified the root cause(s) of the problem, develop and execute an action plan to address the issue. Design solutions that specifically target the root cause(s) to eliminate them from your processes, rather than simply addressing the symptoms of the problem. Implement the appropriate changes to your processes or systems and ensure that all stakeholders are aware of these changes.
Follow-up and Monitoring
After implementing the solutions, monitor the results to ensure they are effective in addressing the root cause(s) and preventing the problem from reoccurring. Collect and analyze data regularly to evaluate the impact of the implemented solutions on your organization’s performance. Adjust and refine the solutions if necessary, and maintain ongoing vigilance in order to identify any future problems that may arise from the same root cause(s).
RCA Techniques
The 5 Whys technique is a straightforward method for identifying the root cause of a problem. To employ this approach, you simply ask “why” five times, with each question delving deeper into the issue. The process helps trace the problem to its origin by examining each level of cause and effect. Here’s an example:
- Why did the machine stop working?
- Why did the fuse blow?
- Why did the motor overheat?
- Why was there insufficient lubrication on the motor?
- Why was the lubrication schedule not followed?
In this case, the root cause is the failure to adhere to the lubrication schedule.
Learn more: 5 Whys: How to Uncover Root Causes [Examples]
Fishbone Diagram
The Fishbone Diagram, also known as the Ishikawa Diagram or cause-and-effect diagram, is a visual tool that helps you organize and sort potential root causes. To create a Fishbone Diagram:
- Write down the problem statement at the head of the fishbone structure.
- Identify major categories of causes, such as people, process, equipment, and environment. Draw lines connecting them to the problem statement.
- Assign specific causes under each category and draw smaller lines connecting them to the respective major categories.
- Analyze the diagram to find trends, patterns, or potential areas of focus.
By organizing information in this way, you can better assess the causes and identify the root cause of the problem.
Learn more: Fishbone Diagram (Components, Factors, Examples) and Ishikawa Diagram: Examples and Applications
Failure Modes and Effects Analysis (FMEA) is a systematic approach to identify potential failures and evaluate the consequences. FMEA processes typically involve these steps:
- Identify potential failure modes, which are the ways something could go wrong.
- Determine the potential effects of each failure mode, and how it could impact the overall system or process.
- Assign a risk priority number (RPN) to each failure mode, considering factors such as likelihood, severity, and detectability.
- Develop actions and strategies to mitigate high-risk failure modes.
By using FMEA, you can proactively address possible issues before they escalate, and maintain a more reliable process or system.
Barrier Analysis
Barrier Analysis focuses on preventing problems by examining the barriers in place to control risks. The objective is to identify vulnerabilities in these barriers and develop strategies for improvement. The steps of Barrier Analysis include:
- Identify hazards and risks associated with your system or process.
- Define the barriers in place that protect against these hazards.
- Evaluate the effectiveness, strength, and reliability of each barrier.
- Identify gaps or weaknesses in the barriers.
- Develop and implement improvements to strengthen the barriers.
This method provides a clear understanding of how existing safety measures perform and how they can be improved to better protect against potential issues.
See also: 3 Root Cause Analysis Templates (and Examples)
What is Poka-Yoke? [Examples, Principles, Methods]
Benefits of Root Cause Analysis
Quality improvement.
Root cause analysis can significantly enhance the quality of your products or services. By systematically identifying the root causes of issues and implementing corrective actions, you’ll prevent recurring problems and reduce the number of defects. In turn, this will help you maintain customer satisfaction, reduce costs associated with rework or returns, and improve your reputation in the market.
Risk Reduction
Reducing risk is another advantage of root cause analysis. When you identify the underlying causes of problems, you can take necessary measures to eliminate or mitigate those risks. This proactive approach can protect your business from potential losses or disruptions, such as regulatory penalties, customer dissatisfaction, or harm to employees or the environment. By addressing the sources of risk, you can maintain a safer and more profitable business.
Process Optimization
Root cause analysis supports continuous improvement by highlighting inefficiencies and areas for optimization in your operations. By examining your processes beyond the symptoms of a specific issue, you can uncover opportunities to streamline workflows, reduce waste or downtime, and better utilize resources. Implementing these improvements not only resolves the immediate problem but also enhances overall productivity and efficiency in your organization.
To attain the benefits of root cause analysis, apply it consistently and rigorously. Ensure that you involve relevant stakeholders, gather necessary data, and employ a systematic approach to identifying and addressing root causes.
Challenges of Root Cause Analysis
Common pitfalls.
When conducting Root Cause Analysis (RCA), you might face common pitfalls that can reduce the effectiveness of your investigation. Some of these pitfalls include:
- Rushing the process : It is important to allocate appropriate time and resources to conduct a thorough RCA.
- Overlooking small details : Make sure to pay attention to all possible contributing factors when investigating a problem. Small details can often hold the key to the root cause.
- Focusing on blame : RCA should focus on identifying systemic issues and providing solutions rather than blaming individuals or departments.
Addressing Human Factors
Human factors play a critical role in many problems. When conducting RCA, it is crucial to consider the human factors that may have contributed to the issue. Here are some tips to help you address human factors in your RCA:
- Consider psychological factors : Assess the mental state of the people involved in the incident, including their level of stress, fatigue, and emotions.
- Evaluate communication and collaboration : Analyze how effectively teams were communicating and working together at the time of the incident.
- Assess training and competency : Determine if the people involved had the appropriate training and knowledge to handle the situation.
Keep a neutral and non-blaming tone while assessing human factors. The aim is to uncover systemic issues that can be improved upon.
Fishbone Diagram (Components, Factors, Examples)
Ishikawa Diagram: Examples and Applications
- Advantages of SWOT Analysis (6 Benefits and 4 Limitations)
- Top Problem Solving Skills for Today's Job Market
- What is Problem Solving? (Steps, Techniques, Examples)
Root Cause Analysis Guide for Efficient Business Problem-Solving
Updated on: 5 January 2023
Sometimes things go wrong. Well-planned projects fail, processes break down and employees lose their productivity.
To understand what happened, you need to get to the bottom of things.
Many organizations use the root cause analysis when a problem or something unplanned happens that will interrupt their business processes. It helps dig deeper and find effective solutions.
In this post, we will look at what is root cause analysis, the root cause analysis steps, and root cause analysis tools.
What is Root Cause Analysis
Root cause analysis is a method that helps understand the primary cause of a problem or why a problem occurred in the first place.
It helps you to dig into the underlying causes of the situation, thus allowing you to find appropriate solutions for it.
There are several root cause analysis tools and techniques that can be used in the investigation of a problem. But before we get to that, let’s understand how to conduct a root cause analysis first.
Root Cause Analysis Steps
A root cause analysis may take several hours of your time.
It would be easier for you if you involve a team of relevant people; for example, if you are investigating bottlenecks in a process, it would help to have the process owner and other experts for the analysis.
Follow the steps below to conduct a successful root cause analysis.
Step 1: Define the problem
Define the problem your organization is facing and gather data and evidence relevant to it and necessary to understand the current situation.
Create a problem statement which should include information about the problem like the actual impact, potential impact, the focal point, etc. However keep the statement concise.
Step 2: Determine the factors that caused the problem.
Gather a team of people directly involved in the execution of the process and corrective actions, and experts whose input can help find solutions faster.
Together with the team, brainstorm the possible factors for the problem by asking ‘why?’. You can use a 5 whys diagram or a fishbone diagram here.
Step 3: Identify the root cause.
Dig deeper by continuing to ask why after the first layer of causal factors. Keep at it until finally you have discovered the fundamental cause for the problem at hand.
Step 4: Decide the corrective actions
Decide the corrective actions you need to take to eliminate the problem and prevent it from recurring. Make sure that you clearly communicate them to the people who will be involved.
Step 5: Review and evaluate
Review and evaluate the impact of the corrective actions. Make improvements as necessary.
Root Cause Analysis Tools
Many root cause analysis tools are out there. Following we have listed some that are widely used and more effective in problem-solving.
5 Whys Analysis
To carry out a 5 whys analysis, you need to gather a team of people who are affected by the problem.
As the name suggests, in the 5 whys analysis the question ‘why?’ is asked five times in the course of finding the root cause of a problem.
You can use a 5 whys template like the one below to facilitate the brainstorming session.
Once you have asked ‘why’ five times and figured out the root cause, come up with improvement measure you need to apply. Assign everyone the corrective actions that need to be taken.
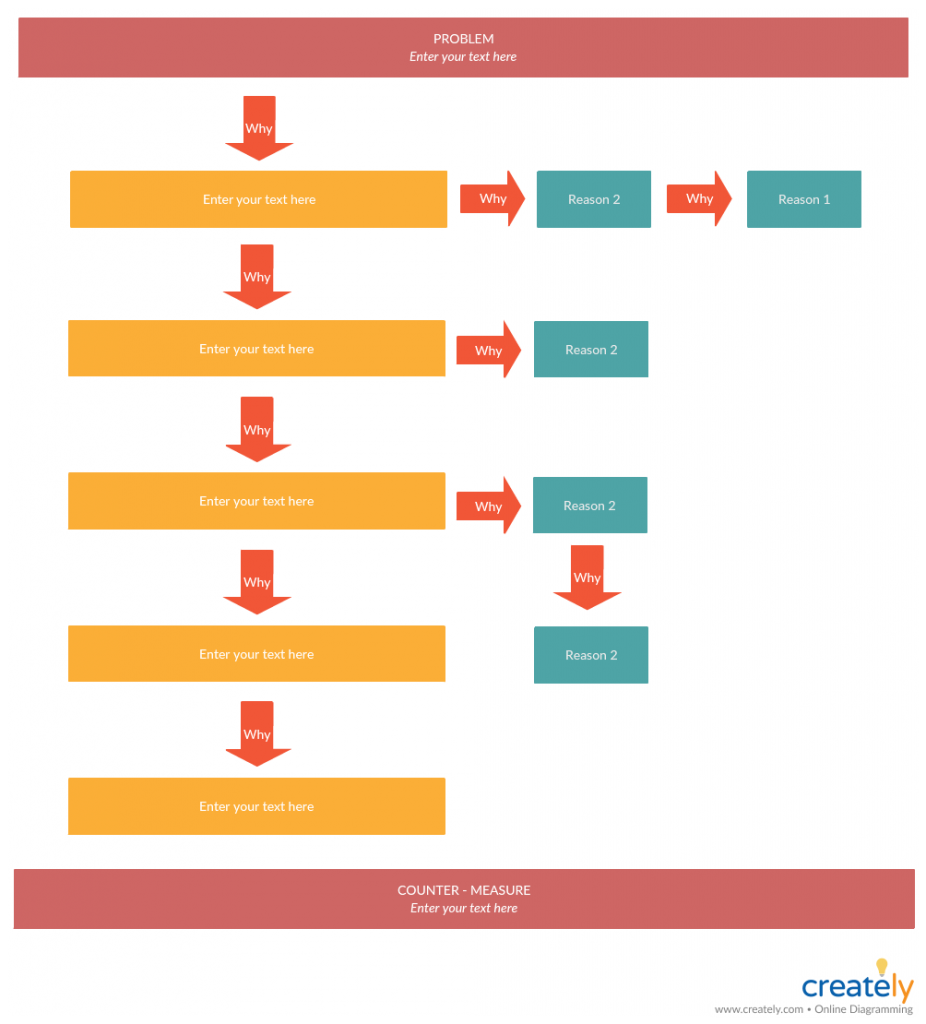
Cause and Effect Analysis
Once you have identified the problem, you can use the cause and effect analysis to explore the causes of a problem and its effects.
For the analysis, you can use a cause and effect diagram, which is also known as a fishbone diagram or the Ishikawa diagram.
Just as it helps explore the factors that are preventing an outcome, it can also be used to identify the factors needed to generate the desired outcome.
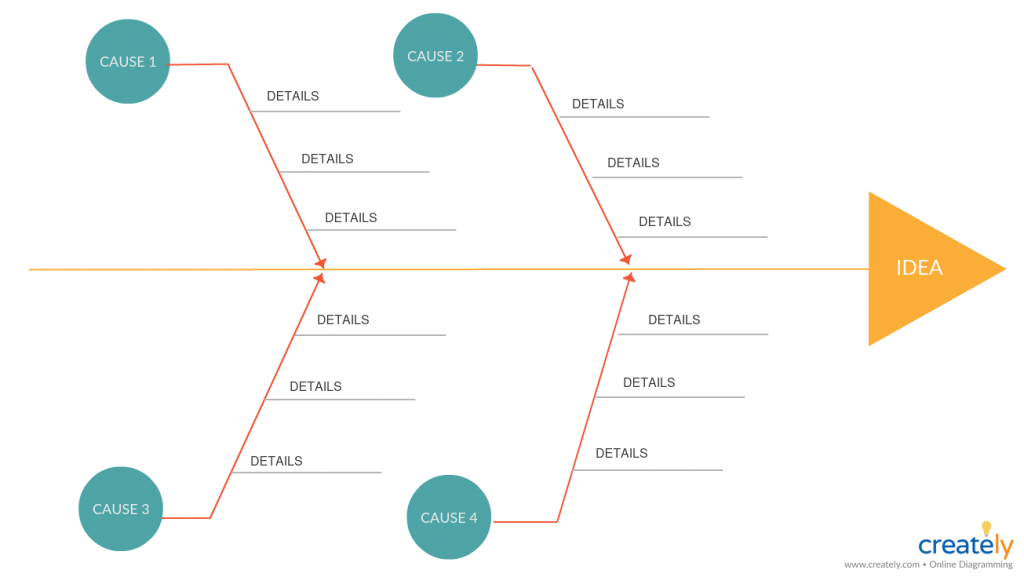
Here’s how to use the cause and effect analysis to solve business problems . You can also refer to our guide on fishbone diagrams to learn how to use the tool in more detail.
Pareto Chart
Pareto chart is a combination of a bar chart and a line graph. While the length of the bars represent the frequency or cost of faults, they are arranged in such a way that highlights the most frequent to least frequent. The chart helps prioritize your issues based on the cumulative effect they have on a system.
The Pareto chart is based on the theory that 80% of the total problems that occur are caused by 20% of problem causes. This means if you have solutions to your major problems, you can also solve a majority of your other smaller problems.
Learn how to create a Pareto chart step-by-step here .
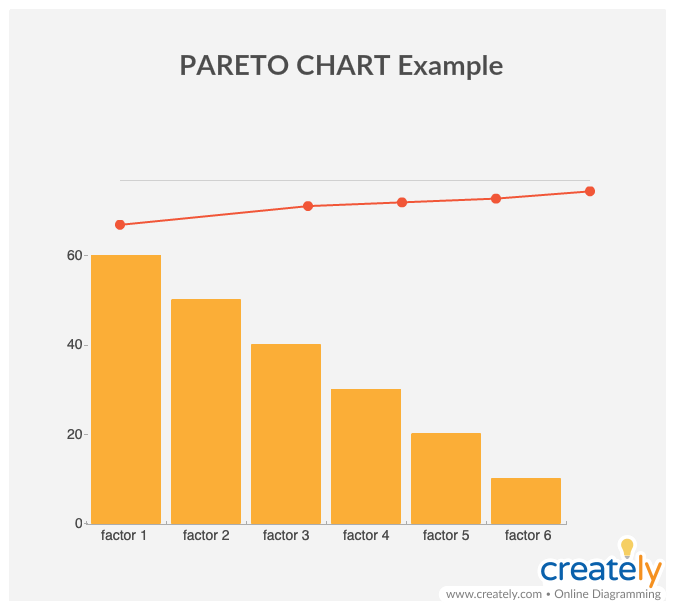
Scatter Diagram
Scatter diagrams or scatter plot diagrams can be used to visualize the relationship between two variables. Once you have created a cause and effect diagram and identified potential causes to your problem, you can use the scatter diagram to determine which causes are responsible for the variation.
While the independent variable is plotted along the horizontal axis, the vertical axis is for the dependent axis. Learn more here .
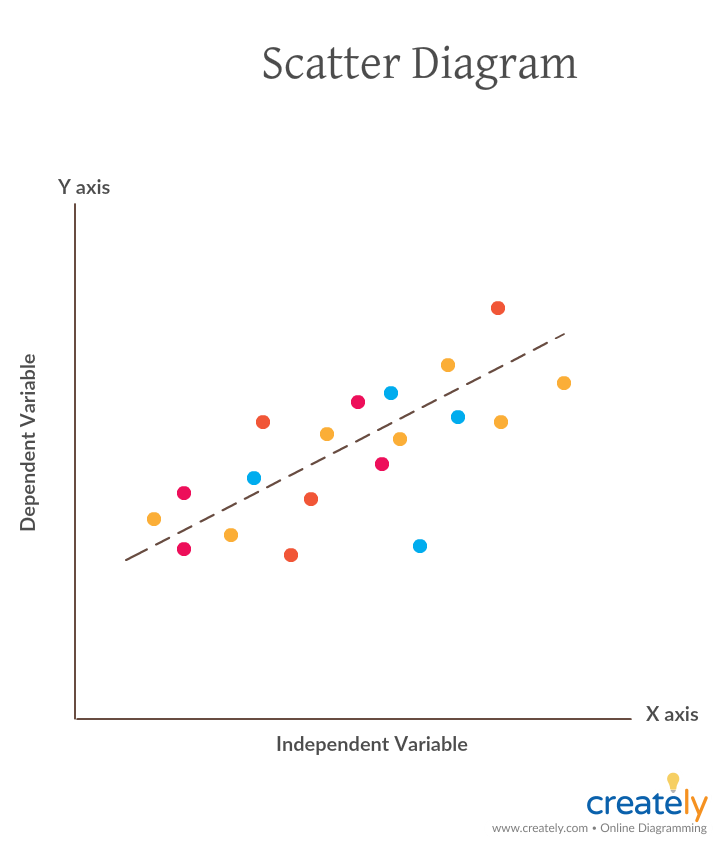
Fault Tree Analysis
Fault tree analysis is a deductive analysis to that visually represent the failure path. You can use the fault tree analysis to determine the possible causes of a problem or an event. The fault tree starts with the event at the top and the possible causes are placed below.
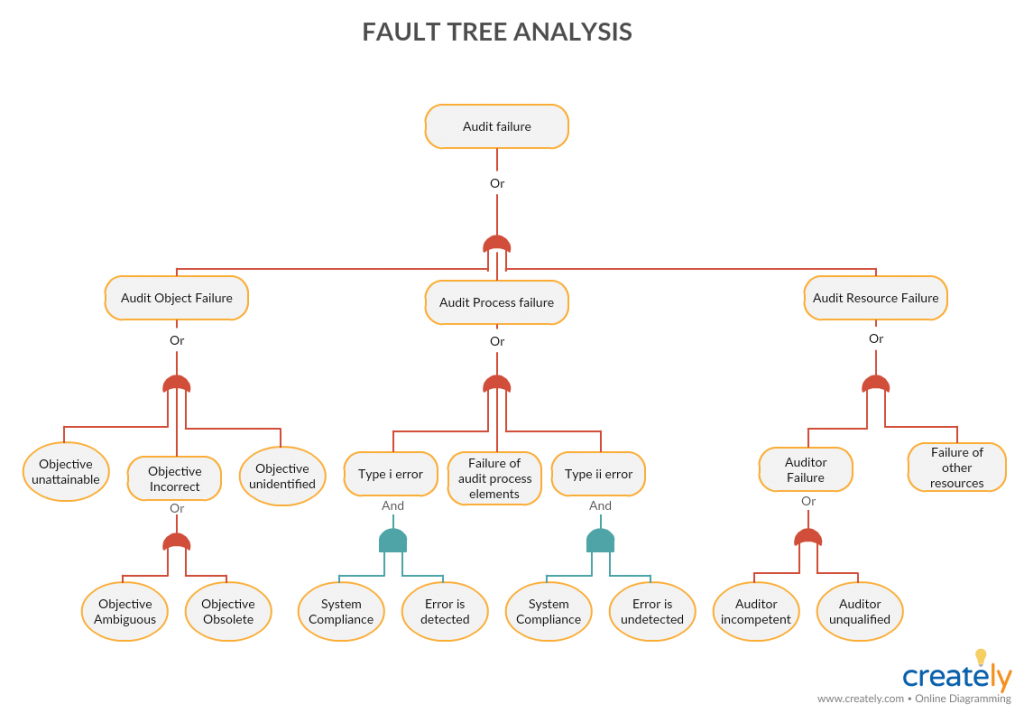
Anymore Root Cause Analysis Tools?
What other root cause analysis tools do you use? Have you got any more tips on accelerating the root cause analysis steps we have discussed above? Do share them with us in the comments below.
Join over thousands of organizations that use Creately to brainstorm, plan, analyze, and execute their projects successfully.
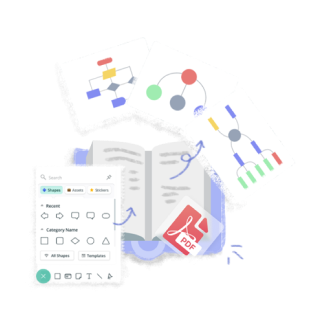
More Related Articles
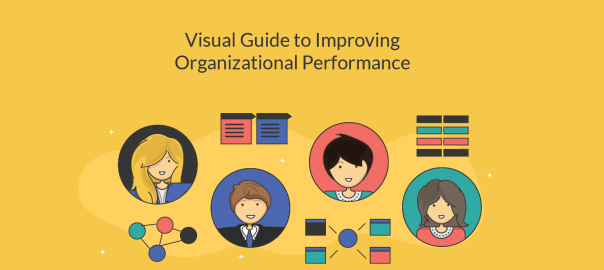
Leave a comment Cancel reply
Please enter an answer in digits: 2 × one =
Download our all-new eBook for tips on 50 powerful Business Diagrams for Strategic Planning.
Root Cause Analysis: A Complete Guide With Examples (2023)
Root Cause Analysis (RCA) is not just a structured method of problem-solving; it's a vital component of organisational leadership. The goal of RCA is to fully understand what caused an issue, allowing for effective corrective actions.
One of the first steps in a successful RCA is identifying performance or opportunity gaps within an organisation. These gaps reflect ways in which an organisation falls short or fails to deliver on its capabilities. RCA helps in pinpointing these gaps, thereby allowing for more targeted solutions.
This article will take you through the benefits of RCA and the three basic types of root causes behind workplace incidents. We’ll then explore the two popular methodologies for RCA and how you can use the RCA methodology to identify them.
Finally, we’ll share tools and best practices to help you implement a robust RCA framework so you can develop a comprehensive problem-solving process for safety and risk management in your organisation.
Read on to discover how RCA can revolutionise your approach to problem-solving and risk management.
The benefits of Root Cause Analysis (RCA)
Without a structured RCA framework for resolving incidents, organisations risk implementing superficial quick fixes that may address some of the symptoms but not the core problems.
An effective RCA methodology helps an organisation's Health & Safety (H&S) team to identify the root causes of a reported incident in the workplace, which is essential to assign effective preventive or corrective actions . Implementing this framework have many benefits:
- Save time, money, and resources because they can identify and invest in the right preventive and corrective actions.
- Prevent the incident from recurring because they can correct the factors causing the issues.
- Prevent more damage or injury caused by a recurring incident.
- Prevent more downtime caused by a recurring incident.
- Boost productivity because they don’t have to revisit the same incident and spend extra time trying to solve the underlying issues.
The three basic types of root cause
There are three fundamental types of root causes:
- Environmental root cause These are causes related to external factors such as moisture levels, weather, or geography.
- Individual root cause These are causes related to an individual’s behaviour, personal choices, ability, or circumstance.
- Organisational root cause These are causes involving internal organisational structure or processes.
The two popular RCA frameworks
A study by Baylor University Medical Center Proceedings identified two popular RCA frameworks. We will cover each one with an example.
#1: The "5 Whys" Method
This is perhaps the most popular RCA technique because of its simplicity. The method is to ask why something happened at least five times. Here’s an example of how it works.
Incident: A construction worker fell and broke his arm.
- “Ask Why” #1: Why did he fall? Answer: He tripped on a wire
- “Ask Why” #2: Why was the wire on the ground? Answer: It was an extension wire needed to supply power to a tool on the other side.
- “Ask Why” #3: Why was the wire pulled across a thoroughfare? Answer: There was no power socket on the other side.
- “Ask Why” #4: Why is there only one power socket in that area? Answer: There aren’t enough portable generators on the site.
- “Ask Why” #5: Why aren’t enough portable generators on the site? Answer: The application requesting the budget to rent a few more portable generators is pending approval.
Using this RCA technique, we’ve identified the actual root cause to be an organisational root cause. The solution for the organisation is to improve the process of approving budgets.
Speeding up the process of approving budgets doesn’t just help prevent future similar incidents. It may also bring the added benefit of improving productivity when construction workers can quickly get what they need to perform their tasks.
Without using this RCA technique, one could have soon concluded that it was solely an environmental or individual root cause. Any corrective actions in these areas are likely to be ineffective or short-term.
#2: Causal Tree
A causal tree is used to evaluate other possible causes that contributed to the incident. This can help organisations identify other possible preventive or corrective actions. Here’s an example of how a causal tree could look like for the same incident example above:
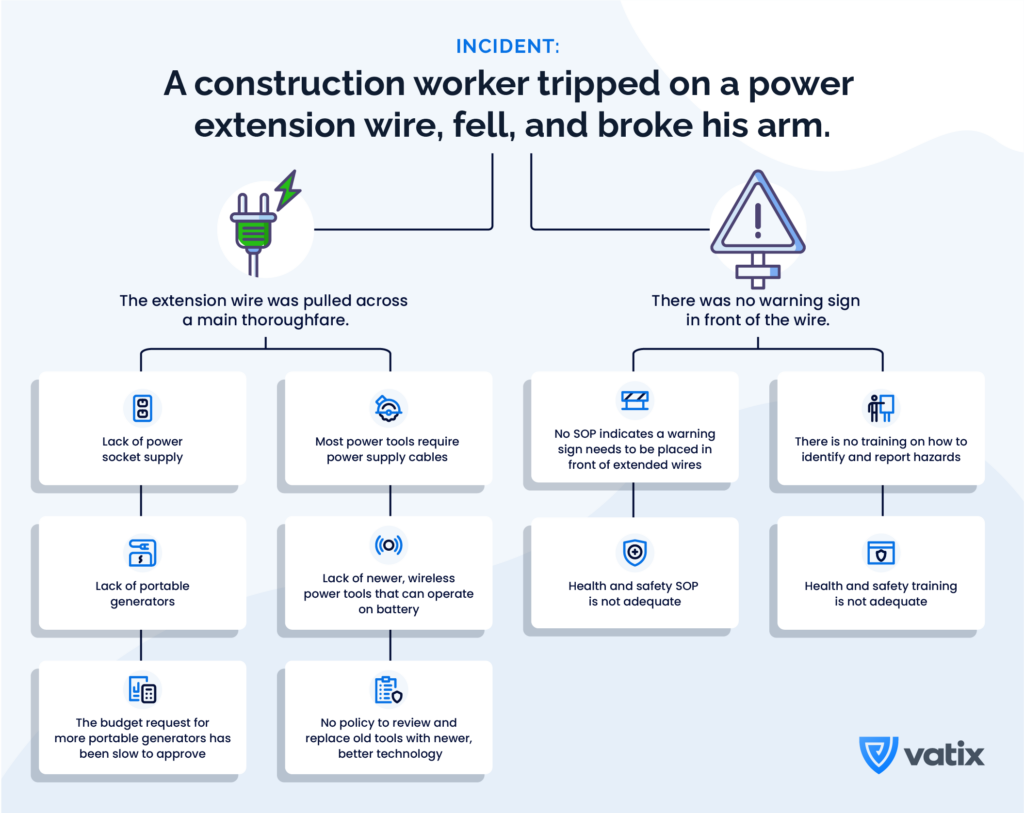
Organisations can explore other possible root causes that need addressing using a causal tree. This RCA methodology is beneficial for identifying root causes across environmental, individual, and organisational categories. Another advantage of using the causal tree framework is that it allows organisations to implement short-term solutions to prevent incidents while they take more time to find answers to more prominent issues. For example, the construction company can implement the short-term solution of placing warning signs in front of extended wires on the ground. Meanwhile, the organisation will look into solving the other root causes identified, such as improving the budget approval process and hazard reporting training.
Common Mistakes to Avoid in Root Cause Analysis
Root Cause Analysis (RCA) can be highly effective in addressing workplace safety issues when done correctly.
However, there are some common mistakes that organisations make when conducting RCA.
Mistake #1: Jumping to conclusions
One of the most common mistakes is jumping to conclusions without thoroughly examining the available information. This often leads to implementing quick fixes that do not address the root cause of the problem.
Tip: Ensure that you take the time to gather all relevant information and systematically work through the RCA process to identify the underlying cause.
Mistake #2: Focusing only on individual errors
Another mistake is solely blaming individuals for incidents without considering the broader organisational context. This can lead to a culture of blame and an unwillingness to report incidents in the future.
Tip: While it is essential to consider individual factors, also examine organisational root causes and environmental factors that may have contributed to the incident. This will help to create a more comprehensive understanding of the issue and lead to more effective solutions.
Mistake #3: Neglecting to involve the right people
One common mistake organisations make is neglecting to involve the right people in the RCA process. A successful RCA requires input from various stakeholders, including employees directly involved in the incident, supervisors, and management. Collaborative analysis helps in collecting a variety of viewpoints and promotes a sense of collective accountability for workplace safety.
Tip: Involving all pertinent stakeholders in the RCA process is crucial, as it aids in collecting a variety of viewpoints and promotes a sense of collective accountability for workplace safety.
Mistake #4: Inadequate documentation
Poor documentation of the RCA process and its outcomes can lead to a lack of accountability and hinder the implementation of corrective actions.
Tip: Document every step of the RCA process, including the incident description, investigation, root cause identification, and proposed corrective actions. This will help ensure that all stakeholders are aware of their responsibilities and can track the progress of the implemented solutions.
Mistake #5: Failing to follow up on corrective actions
Implementing corrective actions is only one part of the RCA process. Organisations sometimes fail to follow up on these actions, which can lead to a recurrence of the incident or issue.
Tip: Establish a system to monitor the progress of corrective actions and evaluate their effectiveness. Regularly review the implemented solutions and make any necessary adjustments to ensure that the root cause is fully addressed and the risk of recurrence is minimised.
How to implement a robust RCA framework
To enhance workplace safety, it is crucial to establish a strong RCA framework within your organisation.
These are the following steps to implement such a framework:
- Train the H&S team on how to use the different types of RCA frameworks.
- Make it easy for employees to report incidents and other events like near misses.
- Update the new employee training, health and safety training, and SOP guides on submitting incident reports and conducting RCA.
- Conduct regular health and safety training sessions.
- Creating an action plan: outline the steps to be taken, the stakeholders involved, and the timeline for implementation
The importance of high-quality incident and hazard reports
The effectiveness of any Root Cause Analysis (RCA) relies heavily on the input data's accuracy and quality. Therefore, it is imperative to have a reliable incident reporting system in place to ensure the provision of high-quality input data.
Here are the characteristics of a high-quality incident report:
- Records the incident's time, date, and location.
- Is honest, clear, and concise.
- Provides accurate information that doesn’t leave out important facts.
- Provide as much context as possible.
- It is written in a first-person, objective observation of what happened, not what they think might have happened.
To write an accurate incident report, employees should be encouraged to start writing the report as soon as possible.
Delaying writing the report can lead to inaccurate reports or reports without enough detail because the memory gets fuzzy. Whenever possible or relevant, employees should also attach photos for additional context.
To help you navigate the complexities of incident reporting, we strongly recommend downloading our free checklist and comprehensive guide .
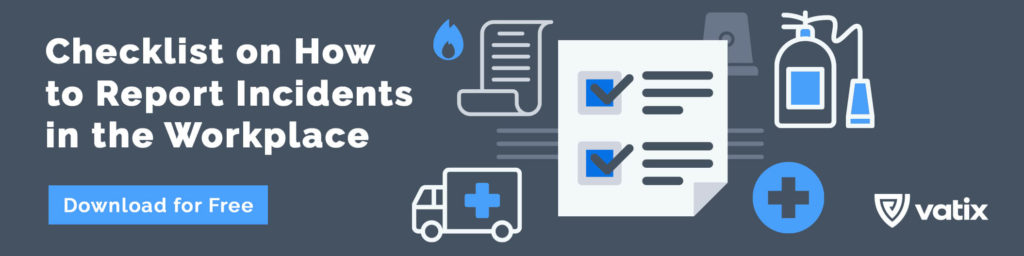
Best practices to improve incident reporting and RCA
One of the best practices to improve the quality of incident reports is digitalising the incident reporting process.
Here’s an example of how Vatix’s incident reporting systems can improve the quality of workplace incident reports and RCA.
- Higher quality incident reports Our mobile platform makes it easy for employees to report an incident from anywhere without the friction of filling out and submitting a paper form. Facilitating on-the-spot reporting for employees minimises the likelihood of postponing or neglecting to report incidents or other events. Faster reporting of incidents also improves the quality of the report. Employees are more likely to record details with better descriptions and upload photos directly from their mobile devices, improving the data needed for an effective RCA.
- Customise incident types to an organisation’s specific needs Our incident reporting software allows organisations to customise the types of incidents employees can report. These templates eliminate the need to print out, distribute, and file multiple forms.
- Easily customise the incident reporting template to capture relevant information. With our incident reporting software, organisations can customise the incident reporting forms to ensure employees submit all required and relevant information.
- Real-time reporting and location tracking for faster response Paper-based incident reporting causes a lot of delays and it can take hours before supervisors or managers can view the incident reports. With real-time mobile incident reporting, employees can submit incidents on-the-spot and the H&S team will be alerted with a location so they can respond to the incident within minutes. In some cases, faster response time with location tagging can be the difference between life and death.
- Easy to get more context at a glance Unlike manual paper-and-pen incident reporting forms, employees can easily add photographs to the incident report directly from their mobile. The incident reporting app also logs the location and provides visual maps for additional context at a glance.
Improve workplace health & safety processes
By combining mobile incident reporting with an effective RCA strategy, organisations can respond to incidents faster and more effectively to create a positive safety culture, leading to increased productivity and decreased risk of accidents and injuries. Talk to our sales here to learn more about how you can customise our mobile incident reporting software to fit your business and improve workplace safety.
Related Articles
Subscribe to our newsletter, subscribe to our newsletter.

- RCA 101 – 5-Why Analysis (Free Training)
- RCA 201 – Basic Failure Analysis
- RCA 301 – PROACT® RCA Certification
- RCA 401 – RCA Train The Trainer
- Other Trainings
- 5 Whys Root Cause Analysis Template
- RCA Template
- Chronic Failure Calculator
Root Cause Analysis with 5 Whys Technique (With Examples)
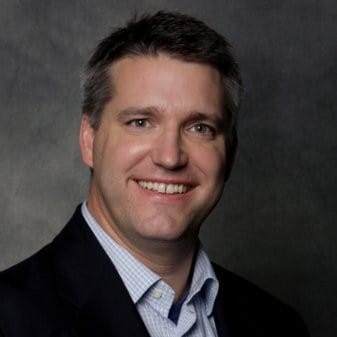
By Sebastian Traeger
Updated: April 23, 2024
Reading Time: 7 minutes
What Is the 5 Whys Technique?
Example of the 5 whys technique, how to conduct a 5 whys analysis in 5 steps, when to use a 5 whys analysis, using 5 whys template, tips for mastering the 5 whys technique, frequently asked questions about 5 whys.
With over two decades in business – spanning strategy consulting, tech startups and executive leadership – I am committed to helping your organization thrive.
At Reliability, we’re on a mission to help enhance strategic decision-making and operational excellence through the power of Root Cause Analysis, and I hope this article will be helpful!
Our goal is to help you better understand 5 whys techniques by offering insights and practical tips based on years of experience. Whether you’re new to doing RCAs or a seasoned pro, we trust this will be useful in your journey towards working hard and working smart.
The 5 Whys Technique is like peeling an onion – it helps you uncover the underlying reasons behind a problem, layer by layer. By repeatedly asking “why” at least five times, this method digs deep to reveal the root cause of an issue. It’s a simple yet powerful problem-solving approach that aims to get to the heart of the matter rather than just addressing surface-level symptoms.
5 Whys Technique: A method that involves iteratively asking “why” five times to unveil the fundamental cause of a problem.
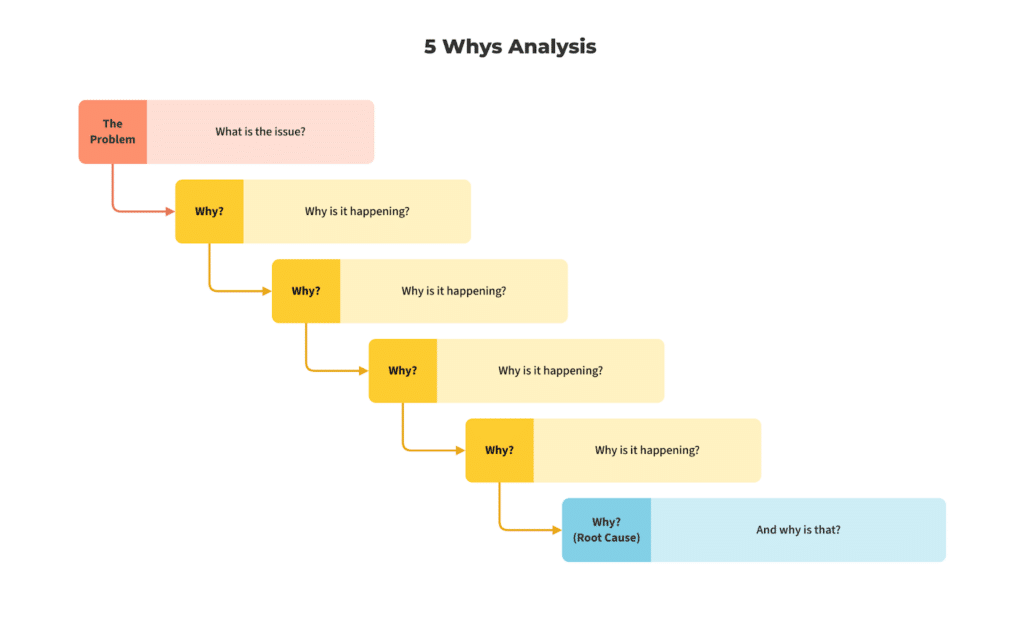
In essence, the 5 Whys Technique is not just about fixing what’s broken on the surface; it’s about understanding and addressing the deeper issues that lead to problems in the first place.
The 5 Whys Technique is like a detective, uncovering the truth behind recurring problems. Let’s take a look at how this method works in two different scenarios.
Case Study: Manufacturing Defects
Imagine a company that keeps encountering the same manufacturing defects despite various attempts to fix them. By using the 5 Whys Technique, they discovered that the defects were not caused by faulty machinery, as previously assumed, but rather by human error due to unclear operating instructions. This realization led to improved training procedures and clear work guidelines, ultimately eliminating the defects.
Application in Service Industry
Now, consider a service industry struggling with frequent customer complaints and service failures. Through the 5 Whys Technique, it was revealed that these issues stemmed from inadequate staffing levels during peak hours. By addressing this root cause, such as hiring additional staff or adjusting schedules, the service quality can significantly improve, leading to higher customer satisfaction.
These examples illustrate how the 5 Whys Technique can be applied across different sectors to identify and address underlying issues effectively.
Step 1: Identify the Problem
Before diving into a 5 Whys analysis, it’s crucial to clearly identify the problem or issue at hand . This step sets the stage for the entire process and ensures that the focus remains on addressing the right concern. Take the time to gather relevant data, observe patterns, and consult with team members or stakeholders to gain a comprehensive understanding of the problem.
Step 2: Ask ‘Why’ Five Times
Once the problem is clearly defined, it’s time to start peeling back the layers. The process involves asking “why” five times, not necessarily limited to five questions but enough to delve deeper into the underlying causes of the problem . Each “why” serves as a gateway to uncovering additional factors contributing to the issue. This iterative approach helps in identifying not just one cause, but multiple interconnected elements that may be at play.
By consistently probing deeper with each “why,” you can reveal hidden complexities and nuances that may have been overlooked initially. This method allows for a more thorough understanding of the situation, paving the way for effective solutions that address root causes rather than surface-level symptoms.
This structured approach encourages critical thinking and enables teams to move beyond quick fixes towards sustainable improvements.
The 5 Whys Technique is a versatile problem-solving approach that can be applied in various scenarios to uncover root causes and drive continuous improvement. Here are two key situations where the 5 Whys Analysis can be particularly beneficial:
Recurring Issues
- The 5 Whys Technique is especially useful when dealing with recurring issues. Whether it’s a manufacturing defect that keeps resurfacing or a persistent customer complaint in the service industry, this method helps identify the underlying reasons behind these repetitive problems. By repeatedly asking “why,” it becomes possible to trace the issue back to its root cause, allowing for targeted solutions that prevent reoccurrence.
Process Improvement
- Organizations constantly strive to enhance their processes and workflows for increased efficiency and quality. When seeking to improve existing procedures, the 5 Whys Technique serves as a valuable tool. By systematically analyzing the factors contributing to inefficiencies or bottlenecks, teams can gain insights into how processes can be optimized at their core. This method enables organizations to make informed decisions about process improvements based on a deep understanding of the underlying issues.
In both cases, the 5 Whys Analysis offers a structured yet flexible approach to delve into complex problems, making it an indispensable tool for driving meaningful change and progress within organizations.
When it comes to conducting a 5 Whys analysis, utilizing a structured template can greatly facilitate the process and ensure a comprehensive investigation into the root cause identification. Using RCA software such as EasyRCA can benefit the team by streamlining your 5-why process. Here’s how organizations can benefit from using a template:

Benefits of Using a Template
- Streamlined Process: A well-designed 5 Whys template provides a clear framework for conducting the analysis, guiding teams through the iterative questioning process. This streamlines the investigation, making it easier to navigate and ensuring that no crucial aspects are overlooked.
- Thorough Investigation: By following a predefined template, teams are prompted to explore various facets of the problem systematically. This ensures that all relevant factors are considered, leading to a more thorough and insightful investigation into the underlying causes.
- Consistent Approach: Templates offer a standardized approach to conducting 5 Whys analyses within an organization. This consistency promotes uniformity in problem-solving methods across different teams or departments, enhancing overall efficiency and effectiveness.
Customizing the Template
Organizations have the flexibility to customize 5 Whys templates according to their specific needs and industry requirements. This adaptability allows for tailoring the template to address unique challenges and incorporate industry-specific considerations. Customization may include:
- Adding Industry-Specific Prompts: Tailoring the template by incorporating prompts or questions relevant to particular industries or types of issues being analyzed.
- Incorporating Visual Aids: Enhancing the template with visual aids such as flow charts or diagrams can help teams better understand and communicate complex causal relationships.
- Iterative Refinement: Regularly reviewing and refining the template based on feedback and evolving organizational needs ensures that it remains aligned with current processes and challenges.
Customizing the template empowers organizations to harness the full potential of the 5 Whys Technique in addressing diverse problems while aligning with their unique operational contexts.
Encouraging Open Communication
In mastering the 5 Whys Technique as a problem-solving method, creating an environment that fosters open communication is paramount. When team members feel comfortable expressing their perspectives and insights, it leads to a more comprehensive exploration of the underlying causes of a problem. Encouraging open communication allows for diverse viewpoints to be considered, providing a holistic understanding of the issue at hand.
By promoting an atmosphere where individuals are empowered to voice their observations and concerns, the 5 Whys analysis can benefit from a rich tapestry of ideas and experiences. This inclusive approach not only enhances the depth of the analysis but also cultivates a sense of ownership and collective responsibility for addressing root causes within the team or organization.
Continuous Improvement Mindset
A key aspect of mastering the 5 Whys Technique is embracing a continuous improvement mindset. Rather than viewing problems as isolated incidents, this approach encourages teams to see them as opportunities for growth and development. By instilling a culture of continuous improvement, organizations can leverage the insights gained from 5 Whys analyzes to drive positive change across various aspects of their operations.
Fostering a mindset focused on continuous improvement entails actively seeking feedback, evaluating processes, and implementing iterative enhancements based on the findings. It involves an ongoing commitment to learning from past experiences and leveraging that knowledge to proactively address potential issues before they escalate. Embracing this mindset ensures that the 5 Whys Technique becomes ingrained in the organizational ethos, leading to sustained progress and resilience in problem-solving efforts.
As we wrap up our exploration of the 5 Whys Technique, let’s address some common questions that may arise regarding this powerful problem-solving method.
What is the primary goal of the 5 Whys Technique?
The primary goal of the 5 Whys Technique is to uncover the root cause of a problem by iteratively asking “why” at least five times. This approach aims to move beyond surface-level symptoms and address the underlying issues that lead to recurring problems.
Is the 5 Whys Technique limited to specific industries or sectors?
No, the 5 Whys Technique is versatile and can be applied across various industries and sectors. Whether it’s manufacturing, healthcare, service, or technology, this method offers a structured yet flexible approach to identifying root causes and driving continuous improvement.
How does the 5 Whys Technique contribute to continuous improvement?
By delving into the fundamental reasons behind problems, the 5 Whys Technique provides organizations with valuable insights for driving continuous improvement. It not only helps in resolving immediate issues but also fosters a culture of ongoing enhancement and development within an organization.
Can the 5 Whys Technique be used for complex problems with multiple contributing factors?
Yes, while initially designed as a simple and straightforward method, the 5 Whys Technique can certainly be applied to complex problems with multiple interconnected factors. By systematically probing deeper into each layer of causality, this technique enables a comprehensive understanding of intricate issues.
I hope you found this guide to 5 whys technique insightful and actionable! Stay tuned for more thought-provoking articles as we continue to share our knowledge. Success is rooted in a thorough understanding and consistent application, and we hope this article was a step in unlocking the full potential of Root Cause Analysis for your organization.
Reliability runs initiatives such as an online learning center focused on the proprietary PROACT® RCA methodology and EasyRCA.com software. For additional resources, visit Reliability Resources .
- Root Cause Analysis /
Recent Posts
5 Root Cause Analysis Examples That Shed Light on Complex Issues
What Is Fault Tree Analysis (FTA)? Definition & Examples
Guide to Failure Mode and Effects Analysis (FMEA)
Root Cause Analysis Software
Our RCA software mobilizes your team to complete standardized RCA’s while giving you the enterprise-wide data you need to increase asset performance and keep your team safe.
Root Cause Analysis Training
[email protected]
Tel: 1 (800) 457-0645
Share article with friends:
Root Cause Analysis: How to Solve Problems Effectively
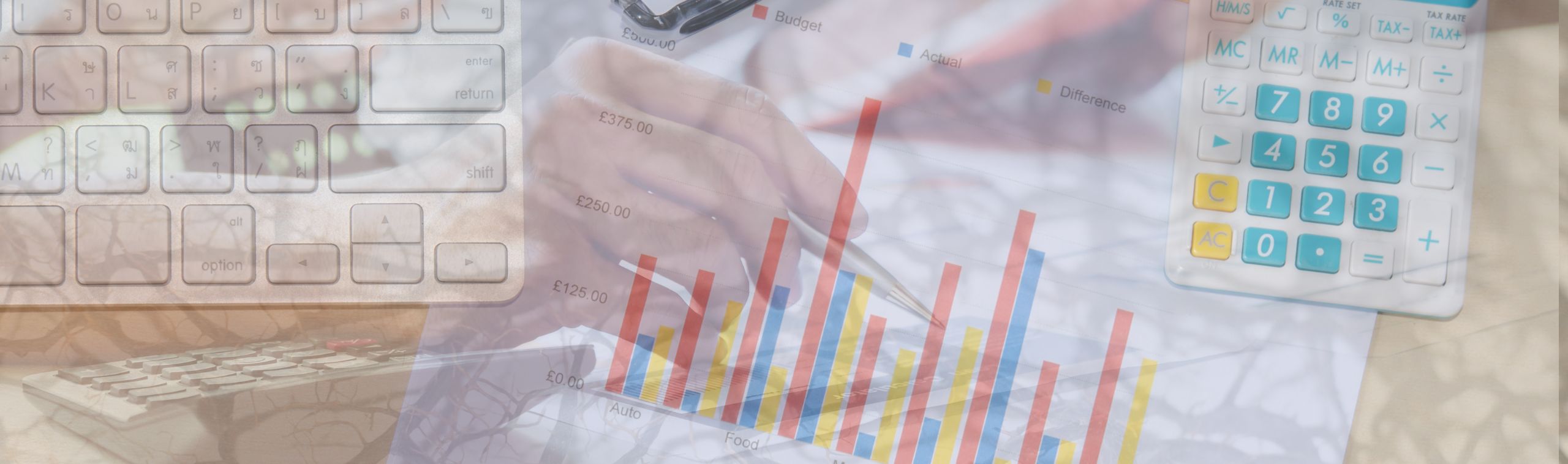
Liz Dyrsmid
- Published: Jan 17, 2023
- Last updated: Jan 18, 2023
Problems develop inside businesses. There are a wide range of possible causes for this. Only by investigating the causes of these problems can they be resolved permanently.
You can get to the bottom of a problem and figure out how to fix it by following a procedure known as root cause analysis (RCA) . RCA is different from other methods because instead of just trying to fix the symptoms of a problem, people who use it look into and try to fix its root causes.
It is best not to rush to find a solution to a problem but rather to take one’s time determining why the problem is occurring in the first place. By doing a root cause analysis (RCA), you will learn more about how problem-solving can be done in an effective way.
Reading this article will help you understand how root cause analysis (RCA) can lead to effective problem-solving.
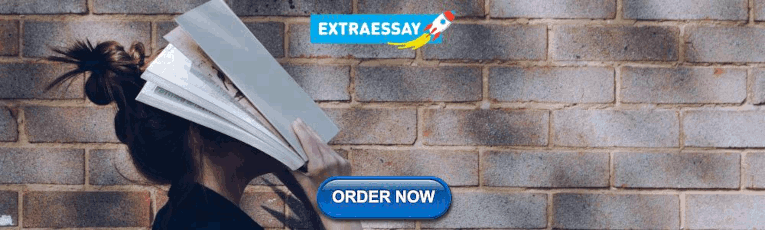
Article Outline
What is root cause analysis.
The phrase “root cause” refers to the main reason for the problem being discussed as well as the first event in the chain of events that led to the problem (or problems).
“Root cause analysis” (RCA) is a term used to describe a wide range of methods, tools, and strategies that are used to figure out where problems come from. When trying to find the “root cause” of a problem, these methods and strategies can be used.
Some root cause analysis methods focus on finding the real causes, while others offer more general solutions to problems or just add to the RCA process.
There are many reasons why a root cause analysis (RCA) might be needed, such as human error, broken physical systems, problems with how an organization works, or any number of other things.
How Do Root Cause Analyses Benefit You?
In order to fix problems and prevent them from happening again, you need to know where they are in your business process. If you use this on a factory line, you can increase output per shift while reducing mistakes at the same time.
For these reasons and more, identifying and addressing root causes is crucial.
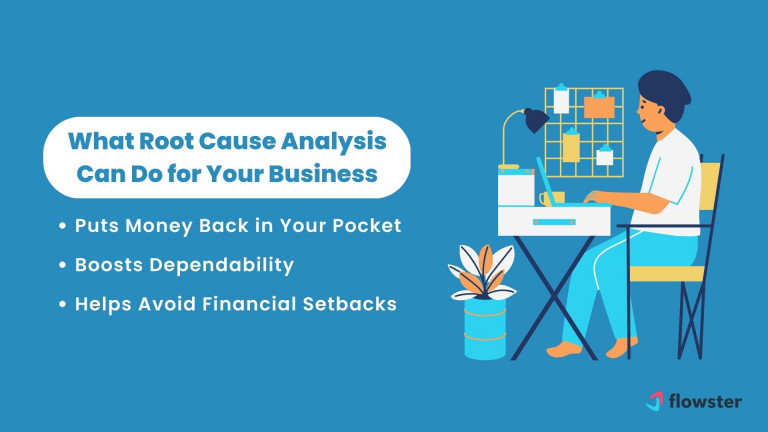
Puts Money Back in Your Pocket
Spend as much time and money as you like on a root cause analysis, and you’ll always come out ahead. This is because your business will always have to deal with the damage and ongoing costs that come from not fixing a problem for good.
Boosts Dependability
To make your business more secure and reliable, conduct a root cause analysis. Quality-focused businesses can benefit from it as well. Reducing the number of errors made during production is one way to win over skeptical customers and increase product reliability.
Helps Avoid Financial Setbacks
Because it provides a framework for developing SOPs , root cause analysis can help businesses gain the public’s trust if they use it to concentrate on prevention. Finding the true cause of a problem will also help you come up with a plan for fixing it.
Common Methods of Root Cause Analysis
The following is by no means an exhaustive list of the methods and approaches that can be used in an RCA. We’ll go over some of the most popular and widely applicable methods below.
The “5 Whys” Method
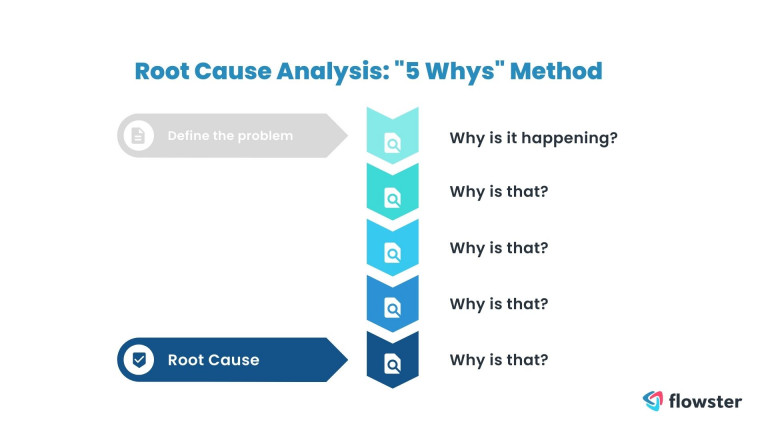
The method known as “5 Whys” is frequently utilized when attempting to figure out what went wrong. If you get an answer to one of your WHY questions, you should ask another WHY question that is more in-depth.
It is commonly believed that by asking five “why” questions, one should be able to get to the bottom of most problems. However, the truth is that you might only need two questions, or you might need fifty.
When you use the 5 Whys to look into a situation, you can leave any ideas you already have at the door.
Event Analysis Method
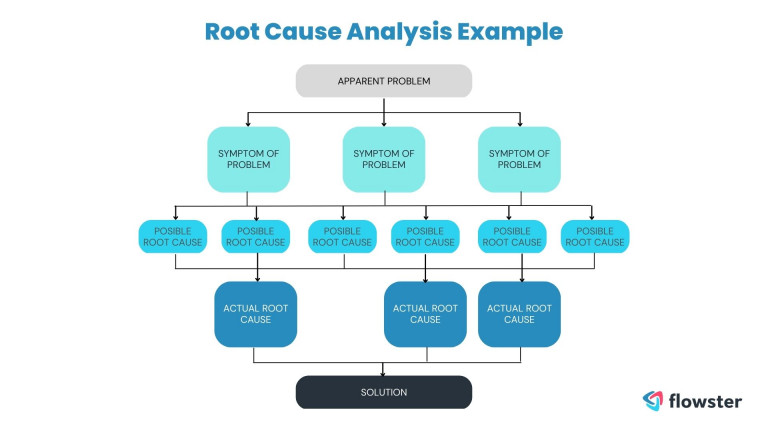
You can also try to determine what caused an event by paying close attention to the things that occurred and how they changed before the event. This is another method for determining what caused an event.
To get started, we would compile a list of every single conceivable cause that led up to an occurrence.
After that, you would go through each individual occurrence and decide whether or not that specific occurrence was a factor that was unrelated to the issue, a factor that was correlated with the issue, a factor that contributed to the issue, or a factor that was likely the root cause.
This is the stage at which the majority of the analysis is performed, and it is also the stage at which other approaches, such as the “5 Whys,” can be utilized.
Last but not least, investigate whether or not the problem can be reproduced and whether or not there is a solution to it.
Fishbone Diagram
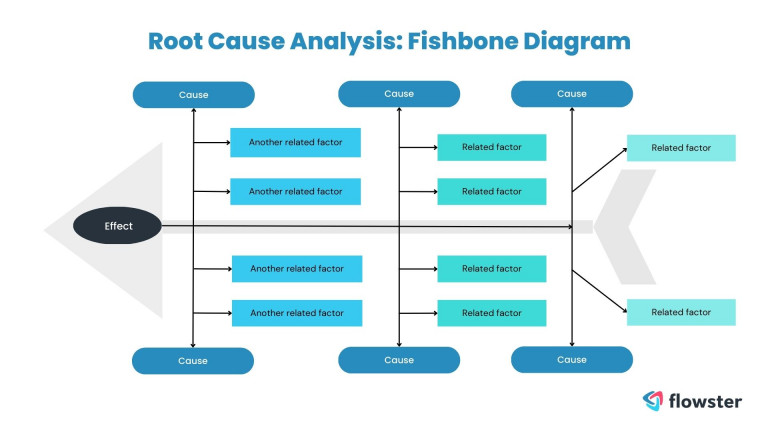
Fishbone diagrams, which are also called Ishikawa diagrams , are another common way to show how causes and effects are connected.
The issue is placed in the middle of the diagram (similar to how the spine of the fish skeleton is positioned), and the various causes are placed around the outside (similar to how the rib bones of the fish skeleton are positioned).
We are getting closer to the root of the issue as we investigate both possible causes and root causes and question each offshoot as we investigate.
By using this method, we can eliminate classes that don’t matter while also showing how different causes are linked and where those causes are likely to come from.
How to Effectively Perform Root Cause Analysis
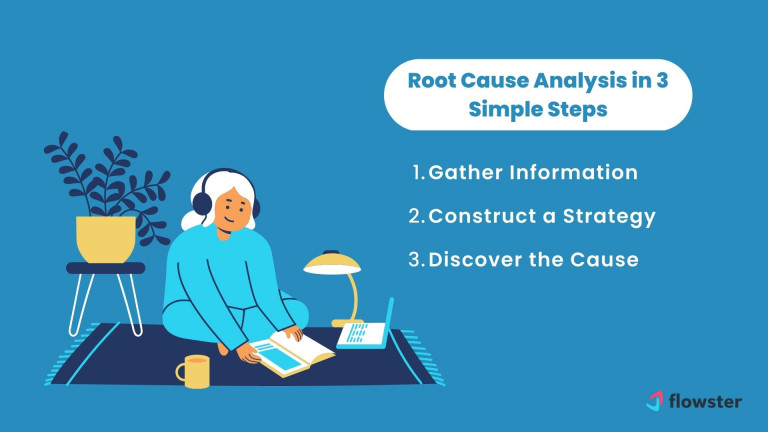
To do a thorough root-cause analysis, you must keep certain guidelines in mind. These guidelines will help you figure out why certain things happen and come up with the best solutions.
- Gather information that shows how the causes you identified led to the effects you saw.
- Construct a comprehensive strategy to support the recommendations you have made.
- Discover what caused this situation and consider how to prevent it from happening again.
It’s important to keep in mind that problems often have more than one underlying cause.
Conclude with the causes you believe to be most at the heart of the problem, and be ready to take on those causes head-on with effective solutions.
The following are some more tips for performing an effective root-cause analysis
Make it a Team Effort
When you and other people work together, you can see things from a different points of view. The process of problem-solving will move along more quickly if you have access to additional perspectives, whether those perspectives come from a partner or from a group of coworkers. This will also help you avoid being overly biased.
Continually Improve Your Process
The process of root cause analysis is very important to understand well. Notate. Investigate the method of analysis. Check to see if a method or technique is right for your company’s needs and culture.
Examine Your Success
Investigate not only what led to your success but also the factors that contributed to it. Even though root cause analysis is typically used to figure out what went wrong, it can also be used to figure out why something turned out successfully. This is an uncommon application of the technique, but it is possible.
Begin Implementing the Solutions
The RCA process doesn’t produce results right away, but figuring out what caused a problem in the first place leads to a long-term solution. You’ll be asked to put your good solution into action after you’ve developed it.
Start creating workflows to help you put solutions into action. Workflows are a set of activities or steps that are followed to complete a specific task or process.
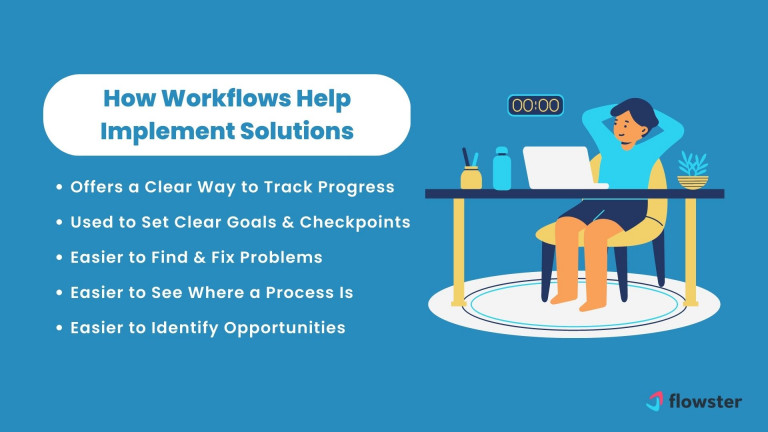
Using workflows to put solutions in place after doing root cause analysis has a number of benefits, such as:
Progress Tracking
Workflows offer a clear and organized way to track the progress of a task or process. This can help you determine whether you are on track and whether there are any delays or obstacles that need to be addressed.
Goal Setting
Workflows can be used to set clear goals and checkpoints for a process or task. This can help to keep the team focused and motivated, as well as provide a way to measure the implementation’s success.
Problem-Solving
Solving Problems: A workflow makes it easier to find and fix problems by breaking down a task or process into specific steps. This can help avoid delays and make problems less of a problem for the whole project.
Workflows can also make it easier for managers, stakeholders, and team members to see where a task or process is in its lifecycle. This lets them make better decisions about any changes or adjustments that need to be made.
Continuous Improvement
Workflows can be used to monitor performance and identify opportunities for improvement over time. This can help make sure that the implementation is always getting better and more efficient, leading to better results and better solutions.
Overall, using workflows to implement solutions lets you keep track of progress, set clear goals, and work more efficiently to solve problems as they come up and get the desired result.
Your effective solutions need to be put into action, so you should get started right away on developing your workflow .
A root cause analysis (RCA) determines why a problem arises in the first place. Instead of just treating the symptoms of a problem, RCA involves looking into and trying to fix its root causes.
It is important to use the tools and methods that are best for your situation when doing a root cause analysis (RCA). Set up a system for ensuring that the work done at each RCA phase is correct.
Every step of the investigation, from identifying the problem to implementing a solution, should be meticulously documented. By completing an RCA, you will gain a better understanding of how to solve problems effectively.
After developing a decent solution, you’ll need to implement it. Start workflows to implement solutions . Workflows let you measure progress, set objectives, handle obstacles, and reach your goals.
We would love to hear your thoughts on root cause analysis. Have you used this method in your own work? What have been your successes and challenges? Please share your comments below, we would love to hear from you!
Ready to Create Your First Workflow?
Visit the Flowster Marketplace to find the newest templates you can use to make your workflows or SOPs.
You can use the templates out of the box or edit them. If you lack time to customize your templates, try our “ Done For You” service. Allow our staff to build custom SOPs for your business.
Request a custom SOP today!
Related Articles
How to Use Workflow Tools to Easily Create Effective Document Workflows
How to Document Workflows for Easy and Efficient Task Management
The Complete Guide to Building Your Workflows – with Free Templates
Leave a Reply Cancel reply
Your email address will not be published. Required fields are marked *
Save my name, email, and website in this browser for the next time I comment.
3827 S Carson St, 505-25 Unit #3040 Carson City, NV 89701, USA
© Copyright – Flowster, LLC
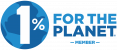
- Integrations
- Virtual Assistant Placement Program
- Training Videos
- Partner Webinars
- Content Partner Program
- Privacy Policy
- Terms of Service
Stay up to date on the latest from Flowster
Privacy Overview
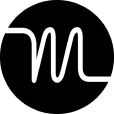
Root Cause Analysis: the Art of Solving Problems in Business
Learn all about root cause analysis, including what it is, the different methodologies, and the exact steps to excel in this problem-solving approach.
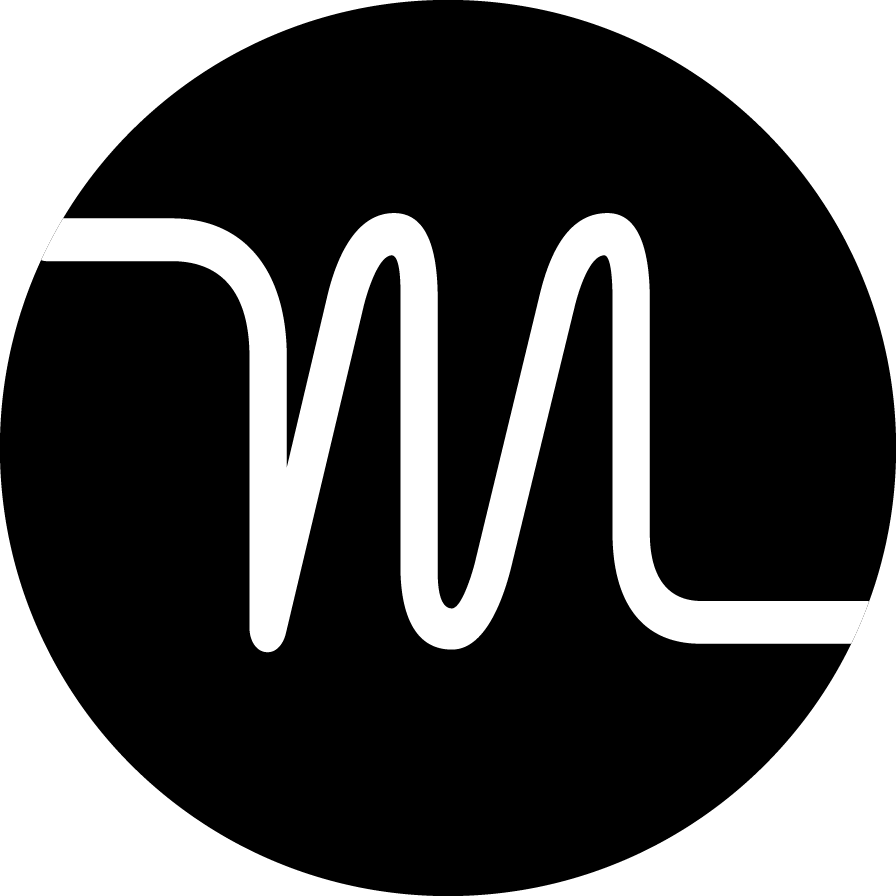
Are you constantly dealing with the same issues in your business? Putting in the effort and resources to solve a problem only to see it reappear a few weeks or months later?
If this sounds familiar, you’re not alone. Many managers grapple with frustrating and costly repeat problems.
Fortunately, a framework exists that can help address this issue. It’s called root cause analysis.
Root cause analysis is a problem-solving method that aims to identify the fundamental cause of a problem so that you can create a solution that fixes it for good.
In this article, we’ll give you an in-depth understanding of root cause analysis, including what it is, its benefits, and its common methodologies. Then, we’ll walk you through a step-by-step root cause analysis guide, clear up some common myths, and offer a few essential tips.
With that knowledge in hand, you’ll be able to solve problems once and for all.
Let’s dive in.
Understanding root cause analysis
Let’s discuss what root cause analysis is and explain how it differs from treating the symptoms of a problem.
What is root cause analysis?
Root cause analysis is the process of identifying the underlying issues behind an organizational problem.
Think of it as a detective’s investigation. It’s not asking, “What happened?” but “ Why did it happen?”
The causes that could be at play include the following:
- Physical causes: These are tangible issues, like a software bug or a machine breaking.
- Human causes: These are tied to people’s actions, such as human error, negligence, or lack of training.
- Organizational causes: These are linked to bigger-picture issues, like operational inefficiencies, policies, or cultural problems.
Looking into root problems is common in many industries, including healthcare, manufacturing, and IT.
Imagine you run a small business, and the business is struggling with late deliveries.
The late deliveries are what’s happening. But the real issue — or root cause — is something different. Here are examples of physical, human, or organizational causes that could be at play:
Physical : Your delivery vehicles are old and unreliable.
Human : Your drivers need better training.
Organizational : Your delivery scheduling system is inefficient.
How do root causes differ from symptoms?
Symptoms are the expression of a problem. They’re not the problem’s origin — rather, they’re the pain points that show you something’s wrong.
Symptoms can include the following:
- A reduction in productivity
- An increase in the frequency of errors
- A customer complaint
Root causes, on the other hand, are the hidden factors that drive these visible issues.
For example, losing customers is a symptom. Figuring out why this issue is happening leads you to the root cause — which, in this case, might be poor customer service or an inferior product.
Unveiling the benefits of root cause analysis
Root cause analysis is more than a problem-solving method. It’s a strategic approach that enables your business to avoid getting stuck in a cycle of recurring problems.
Essentially, you can work through issues, learn from them, and move forward, which leads to better productivity, fewer roadblocks, and a clearer path to success.
Better efficiency and productivity
Identifying the root cause means you tackle the inefficient processes and broken operations that are bringing about symptoms. That leads to time savings and improved performance.
For example: if a manufacturing plant has too many machine breakdowns from a lack of maintenance, then you need to address the root cause (the lack of maintenance). So, you set up a maintenance schedule to streamline production and improve delivery rates.
Fewer recurring problems
Since root cause analysis confronts the problem at its source rather than treating the symptoms, problems are fixed and don’t reoccur. That reduces the time and resources spent on repeat fixes.
Considering that 85% of C-suite executives believe their organizations are poor at diagnosing problems, mastering root cause analysis could be a game-changer for a lot of companies.
Better bottom line
Root cause analysis does require a time investment, but it’s important to remember that fixing your recurring problem can impact your bottom line, too.
Think about an online retail shop experiencing high return rates. Through root cause analysis, they might determine the cause of this problem is an inaccurate product description.
The business could make a big dent in its return rates by editing the product description on its website — ultimately improving its profit margin.
The methodologies of root cause analysis
There are multiple ways to practice root cause analysis. Each methodology has a set of benefits and best scenarios for use. Let’s look at a few of them below.
The 5 whys methodology is just as straightforward as it sounds.
In it, you ask five “why” questions to drill down to the root cause of a problem.
Let’s play out an example:
Say your website's conversion rate has significantly dropped. We might ask the following 5 whys:
- Why has the conversion rate dropped ? Because fewer people are clicking the “purchase” button.
- Why are fewer people clicking the purchase button? Because they’re abandoning their shopping carts.
- Why are they abandoning their shopping carts? Because the checkout process is too complicated.
- Why is the checkout process too complicated? Because it’s not intuitive, and there are too many steps.
- Why are there too many steps, and why isn’t it intuitive? Because we didn’t consider the user experience when we designed the website.
It may take a bit of time to answer each question effectively. But the 5 whys is a great method for getting under the layers of symptoms to find the root cause.
Fishbone diagram
The fishbone diagram, also known as the Ishikawa diagram, is a visual root cause analysis methodology. It helps identify all possible causes of a particular problem. It’s most useful for complex issues in which multiple causal factors might be involved.
Here’s how it works:
- The “head” of the fish skeleton is where the problem is stated.
- The major “bones” of the fish are the cause categories , such as equipment or infrastructure problems.
- The “branches” coming out of each bone list the causes within each category.
The fishbone method encourages team brainstorming and provides a clear visual representation of the potential root causes.
For example, if you’re experiencing high turnover, you could create the following categories for the cause of the problem: “work environment,” “compensation and benefits,” and “training.” Then, list the problems within each one until you start to uncover the root causes.
Cause-and-effect matrix
The cause-and-effect matrix is a more complex method. But, like the others, it’s beneficial in certain circumstances.
This method involves listing all possible causes and then ranking them based on their severity and frequency. The result is a prioritized list of potential root causes to investigate.
Think about a small restaurant receiving customer complaints about long wait times. They could list potential causes of this issue, such as being understaffed, cooking too slowly, or having delayed suppliers. Afterward, they’d rank each cause to determine which is affecting wait times the most.
Implementing root cause analyses: a step-by-step guide
Now, we’ll cover the basic steps to executing an effective analysis.
Step 1: Identify the problem
The first step is to clearly define the problem, being as specific as possible.
Step 2: Gather data
Next, gather as much relevant information about the problem as possible.
This could include the following:
- When the problem started
- How often the problem occurs
- The conditions under which the problem happens
- Who or what the problem affects
The more comprehensive your data is, the better equipped you’ll be to find the root cause of your problem.
Step 3: Identify possible causes
Once you’ve gathered all the necessary data, start brainstorming possible causes of the problem you’re experiencing.
Here, you can apply one of the methodologies discussed earlier, such as the 5 whys or the fishbone diagram.
Encourage your team to suggest any cause that comes to mind. That way, you can generate a wide range of possibilities to work from.
Step 4: Determine the root cause
Now it’s time to analyze and identify the root cause of the problem.
You may need to conduct more in-depth data analyses, interviews, or observations. Don’t rush this step. It’s vital to confirm that the identified cause is indeed the root cause. If it’s not, the problem will likely continue.
Step 5: Develop and implement a solution
The next step is to develop a solution that addresses the root cause you just discovered.
You want your solution to be action-oriented, specific, and time-bound
Step 6: Monitor the results and make adjustments as needed
You can’t simply put a solution in place and then walk away. Track the solution’s effects, and steer your course where necessary.
Remember to document your root cause analysis process and results. This will not only provide a record for future reference but will also help establish a culture of learning and continuous improvement.
Common objections and misunderstandings
Root cause analysis is a potent tool in the problem-solving toolkit, but it’s not without misconceptions and challenges. Understanding these things can help you more effectively navigate your root cause analysis journey.
Let’s debunk some common myths and offer tips for overcoming potential obstacles.
Myth 1: Root cause analysis isn’t worthwhile
While the root cause analysis method does require effort and time, the potential return on this investment is significant. The time you spend identifying the root cause of a problem can end up saving many hours addressing recurring issues.
Also, not all methods are time-consuming and complex. Techniques like the 5 whys, for instance, can be quick and easy to apply.
Pro tip: Start with simple root cause analysis techniques, like the 5 whys, and gradually move to more complex ones later if you wish.
Myth 2: Only large organizations benefit from root cause analysis
That couldn’t be further from the truth. Small businesses stand to benefit significantly from a root cause analysis. This technique can help identify inefficiencies and improve business processes, both of which are vital for lean operations and competitiveness.
Pro tip: Don’t think about the size of your business as much as the complexity of your problem and the resources you have available.
Myth 3: Root cause analysis always reveals one clear cause
Some problems can have multiple root causes, and it’s essential to address all of them to find a comprehensive solution.
Pro tip: If you think your problem has multiple causes, try the fishbone diagram analysis. It’s great for getting a multifaceted view of the issue.
Embracing root cause analysis as a proactive tool
As with many business strategies, there are ways to go deeper with root cause analysis. Here are some points to keep in mind:
It’s not just for problems
While root cause analysis does solve problems, it can also help you understand why things are going well when they do.
This can be valuable for scaling success.
For instance, if you find one of your marketing campaigns to be particularly successful, a root cause analysis could help identify the reason(s) behind that success. You could then replicate those factors in future campaigns.
It can reveal deeper organizational issues
Root cause analysis can bring systemic issues to light.
What might seem like a standalone problem could really be an indicator of underlying organizational challenges, such as communication gaps or inadequate training.
Don’t be afraid to go in-depth with your analysis to find bigger problems at the organizational level. While these issues can be troubling to find, think of them more as an opportunity.
It can foster a culture of continual learning and improvement
Root cause analysis encourages teams to investigate problems.
Rather than patching up issues superficially, you can create a culture in your organization that asks, “ Why is this happening?”
This mindset can go beyond simple problem-solving to have far-reaching benefits.
Level up your problem-solving with Motion
Root cause analysis is an incredibly powerful tool for any organization. It’s not just about troubleshooting — it’s about addressing your business’s challenges at their source.
Motion can eliminate many scheduling and task management issues before they even arise. Our advanced calendar can streamline your project and task management.
Take your problem-solving to the next level using Motion’s AI software. Sign up for our 7-day free trial today!
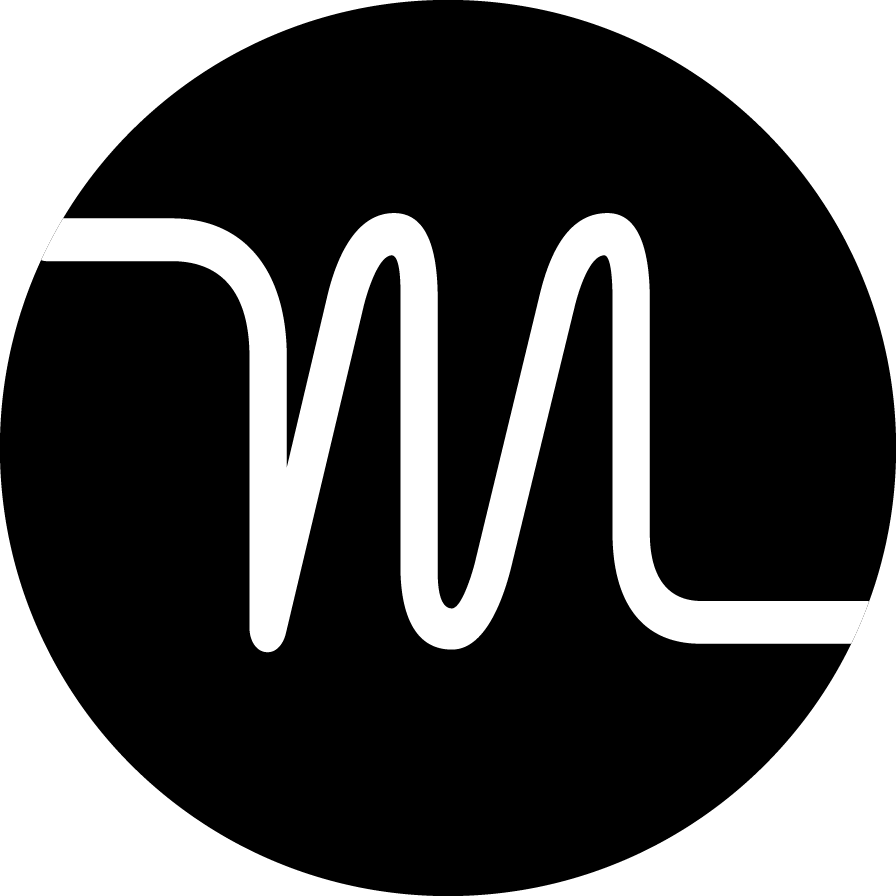
Related articles
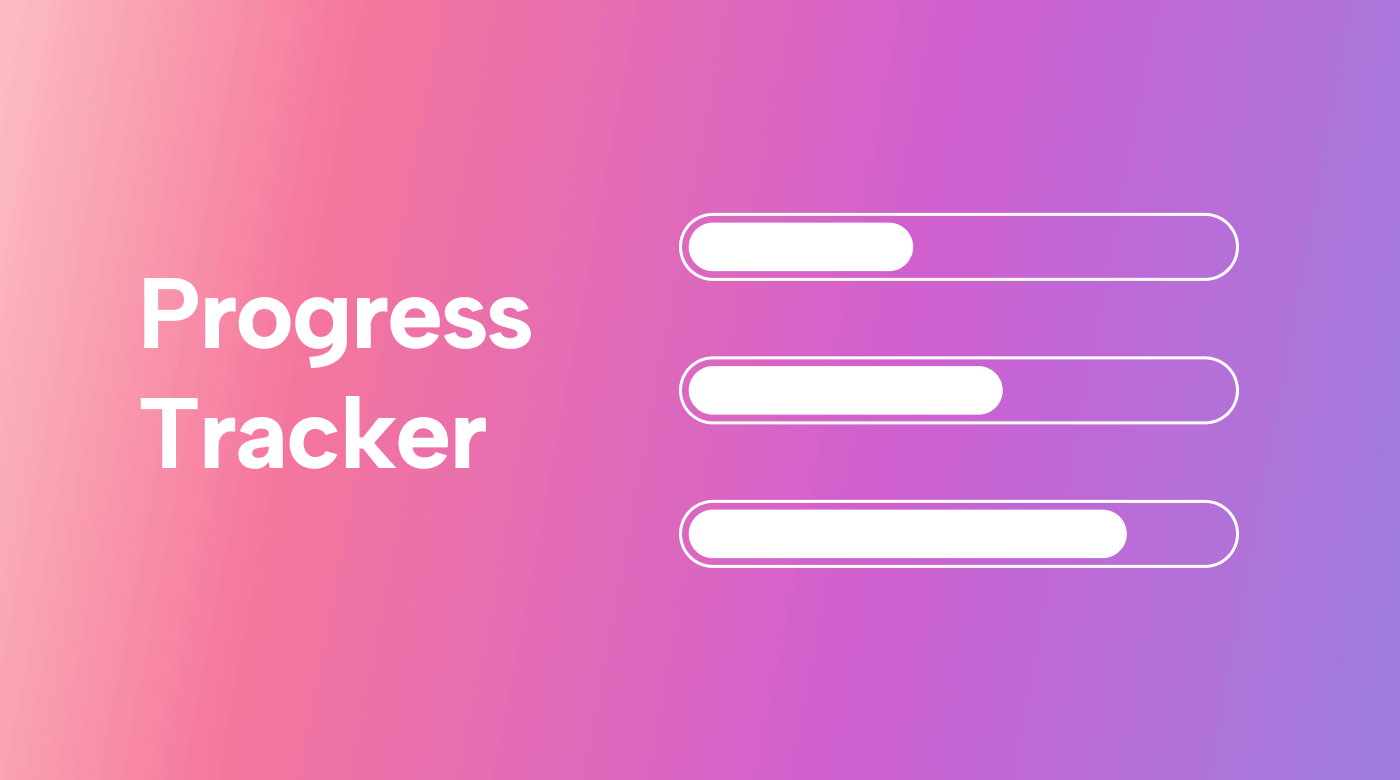
How to Use a Progress Tracker to Deliver Successful Projects
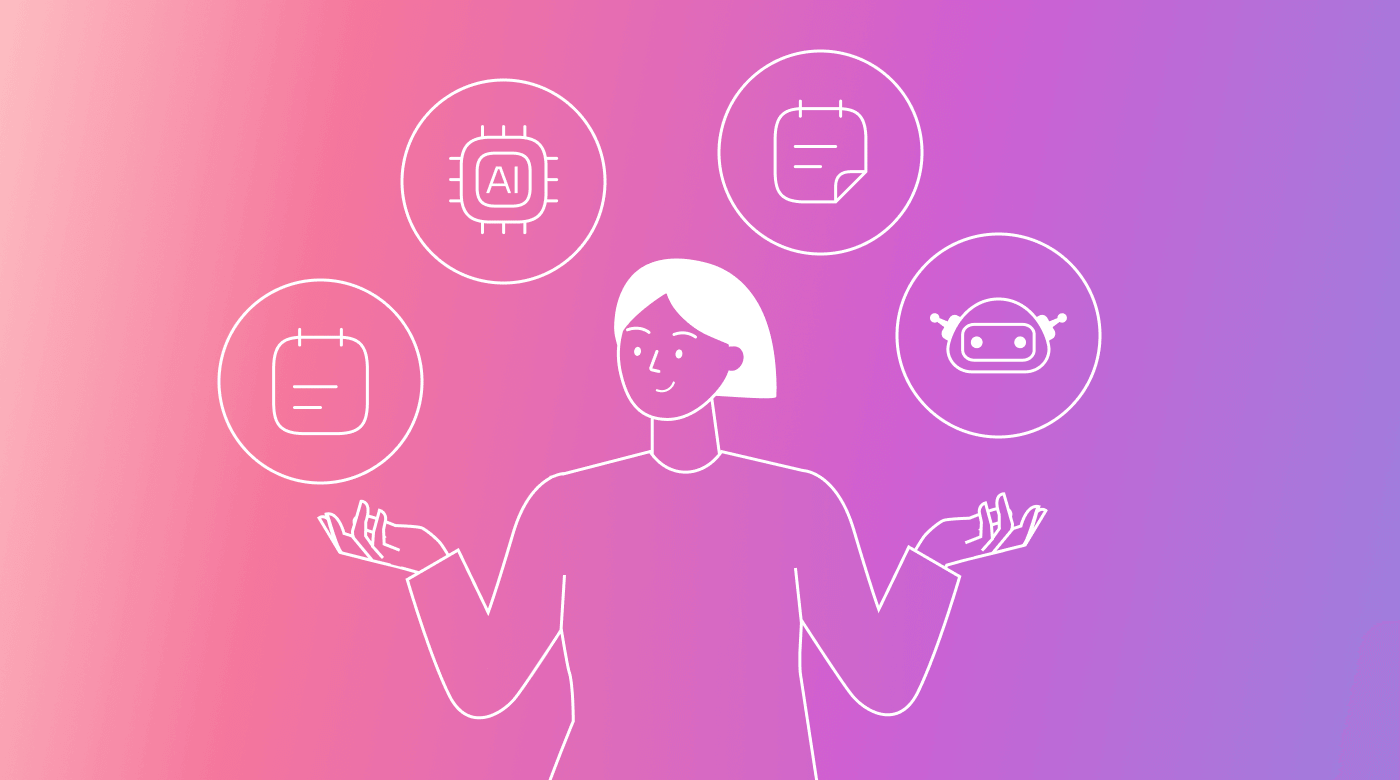
6 Best AI Calendar Assistants for Easy Organization
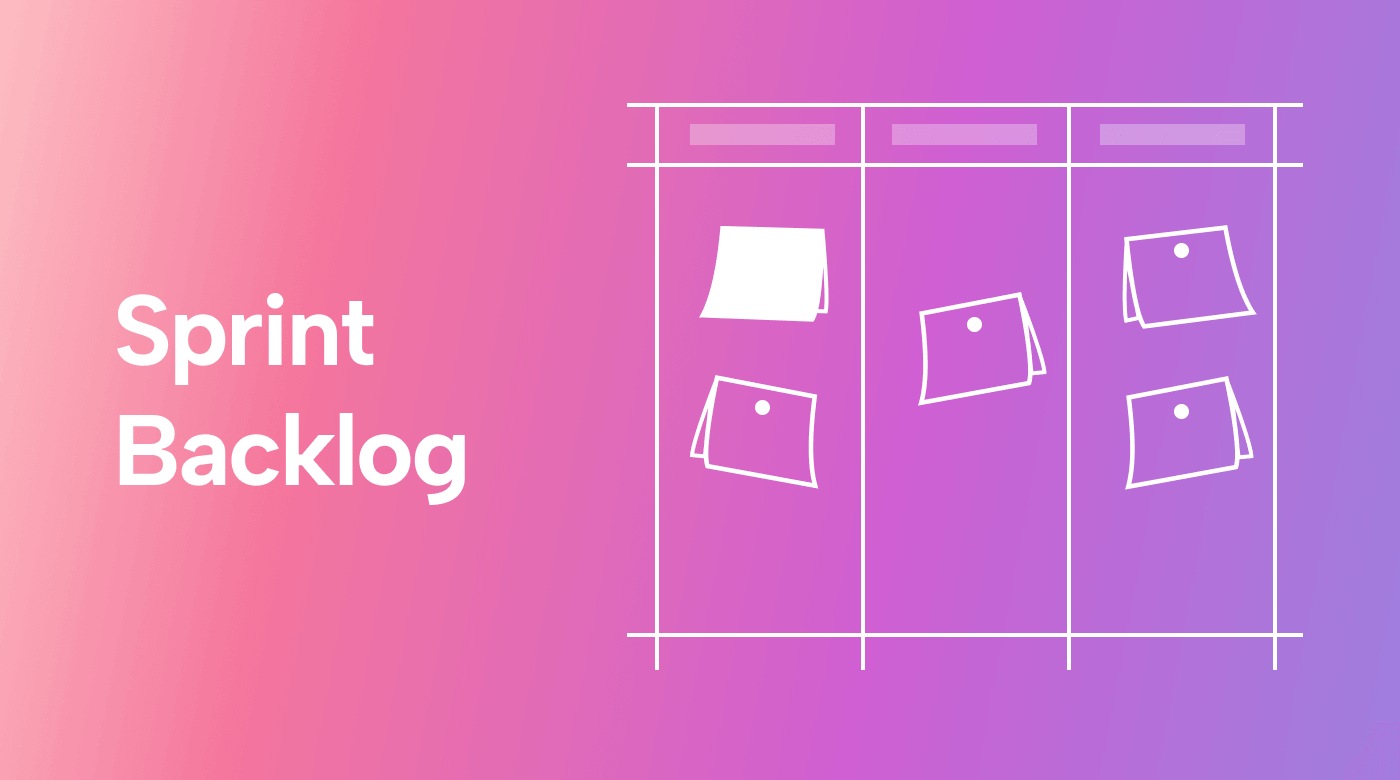
Understanding the Sprint Backlog and How to Use It
Put motion to the test., tech and media companies are talking about motion.
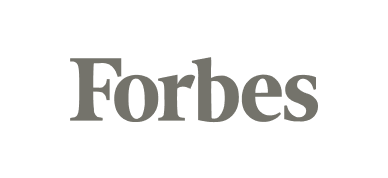
Unlock insights with root cause analysis tools
Solve complex issues and dive deeper into solutions with Miro’s suite of root cause analysis tools. Be better equipped to facilitate conversations to improve strategies in your organization.
Over 60M users love Miro.
Empower teams
With Miro's root cause analysis tools, everyone can bring their insights into a shared workspace, fostering a sense of unity and understanding. Dig deeper, highlight the root cause of problems in real time or async, and find solutions collaboratively.
Visualize to understand
Illustrate and connect the dots with Miro’s tools for root cause analysis. Sketch, draft, and pin your thoughts to understand how different factors relate to each other.
Templates to increase efficiency
Miro's ready-made templates pave the way to problem-solving. Create a fishbone diagram or use the 5 Whys framework simply by picking a template and letting your ideas flow into an organized structure.
Why Miro is the perfect tool for root cause analyses
Simplify issues.
Run a brainstorming session with your team and visualize all possible causes of your problem by breaking them down into more minor issues. Miro helps you to easily co-create an action plan using one of the many root cause analysis tools.
Include everyone
Make sure everyone is heard, allowing you to gain diverse perspectives. Invite the whole crew to join you on your board and work in real time or async, crafting the perfect root cause analysis.
Infinite canvas
Miro's online workspace allows you to map out complex problems and identify the root causes one by one. Enable teams to explore ideas without constraints, fostering creative and critical thinking.
Circulate your board
Share your board link with all relevant stakeholders, or download your root cause analysis as an image or PDF. With just a few clicks, export your work quickly, saving time and effort.
Related templates
5 Whys Template
Analyze and understand the root of a problem or issue with the 5 Whys Template.
Fishbone Diagram Template
Visualize the potential causes of a problem, to solve it collaboratively using a Fishbone Ishikawa Diagram.
DMAIC Analysis Template
Use the DMAIC process (or Six Sigma Map) to solve problems using a structured approach.
FMEA Analysis Template
Identify risks so you can optimize and stabilize business processes.
Quick Retrospective Template
Look back at success and failures in order to improve everyday practices.
Affinity Diagram Template
Organize and cluster ideas and data in order to effectively develop solutions.
Problem-solving made easy
Explore complex issues, visualize problems, and uncover their root causes through effective collaboration. Miro’s range of root cause analysis tools and templates lets you systematically narrow down potential causes, allowing your team to run a complete analysis effectively.
Fishbone Diagram
Bring your team together around one problem and find all possible root causes with Miro’s fishbone diagram maker. Brainstorm possibilities, analyze the current situation, and gain insights, all in one tool.
Diagramming
Miro’s all-in-one diagram maker removes the hassle of switching between diagramming and collaboration tools while helping you check off all the essential steps of your diagramming process.
Process mapping
Map processes, strategies, and everything in between with Miro. Get ideas, develop plans and build concepts everyone understands, creating alignment and bringing agility to teams.
BPMN diagram
Stay on top of your business processes by mapping them out with an online BPMN diagram. Have a shared understanding of your business’ procedures and increase productivity across the whole organization.
How to perform a root cause analysis with Miro
Select a ready-made template
From Fishbone diagrams to 5 Whys, choose a template that fits your project.
Add it to the board
Drag and drop the template directly to your board.
Analyze your problem
Start breaking down your issue to better understand the root causes. Use the template to guide you in this process.
Share your findings
Invite others to your board and keep it as a living document, so people can comment, give feedback and uncover more insights!
Root cause analysis tools FAQs
What are the tools for root cause analysis.
Teams and managers use root cause analysis tools to identify the underlying causes of a problem or issue. There are many different ones that can be used for this purpose, including 5 Whys, Fishbone Diagrams, Fault Tree Analysis, and FMEA. The 5 Whys framework involves asking "why" questions repeatedly to drill down into the root cause of a problem. Fishbone Diagrams are visual tools that help identify all the possible causes of a problem. Fault Tree Analysis is a method of identifying the causes of a specific event or failure. FMEA is a systematic approach to identifying and preventing potential failures in a system or process. Understanding and using these tools improves problem-solving and helps prevent future issues.
Can any team in any industry use root cause analysis tools?
Absolutely. Teams across industries and sectors use root cause analysis tools, including manufacturing, healthcare, IT, logistics, finance, and more. The RCA framework is flexible and adaptable, allowing organizations to identify and address the root causes of problems regardless of the specific field or context.
Are root cause analysis tools suitable for both simple and complex issues?
Yes, root cause analysis tools are adaptable to both simple and complex issues. Many teams use it for straightforward problems, and it enables them to identify and address root causes quickly. RCA tools also bring more clarity and visibility when decoding relationships between multiple factors in complex issues, making it easier for teams to understand and flag underlying causes.
What is root cause analysis?
What's a fishbone diagram?
5 Whys: Examples, explanations, and how to find the causes of problems
FMEA: How to properly set up Failure Modes and Effects Analysis
Get on board in seconds
Join thousands of teams using Miro to do their best work yet.
Root-cause problem solving in the Ops 4.0 era
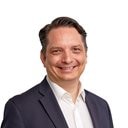
Passionate about the “human factor”: helping people develop broad skills and deep functional expertise. Experienced operations practitioner, faculty member, and author.
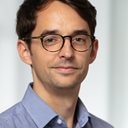
Wouter Michiels, a consultant based in the Brussels Office, has more than 10 years’ experience in petrochemical manufacturing, engineering, and supply chains.
April 15, 2019 To improve, organizations must consistently seek out and solve their problems—an insight that underpins lean management ’s emphasis on root-cause problem solving (RCPS). Indeed, companies that have used RCPS to build a problem-solving culture that lasts are able to avoid continuous firefighting by effectively preventing fires from starting.
But RCPS takes discipline and patience, which some leaders resist: a manager may be reluctant to use this model if she’s convinced that she has already identified an “operational solution.” Nevertheless, persuading her to join her team on a problem-solving journey can help uncover a more effective and sustainable set of solutions—most importantly by including the people who know the problem best: shop-floor employees. Their perspective often shows that the initial idea would not have addressed the problem’s real causes, and would have met with a lot of resistance from the people charged with implementation.
Ops 4.0 technologies are making it easier to overcome that resistance and invigorate root-cause problem solving performance. What follows is a non-exhaustive overview of how different technologies ( italicized ) could be applied in each of the five RCPS elements (exhibit).
1. Identifying and defining the problem
The rise of advanced analytics and business-intelligence applications allows companies can detect many more problems than in the past, and in a more effective way—so long as they have sufficient internal support to interpret the output . Examples include fraud detection in banking and insurance, as well as deviations from normal operating conditions of equipment in manufacturing plants. For the latter, the increased availability of high-frequency, high-precision sensors , together with the rise of the Internet of Things provides companies with larger data sets from which to identify problems.
2. Assessing root cause(s)
Once the problem is defined, root causes are often identified via the five-why methodology. Instead of using the traditional colored sticky notes to facilitate this exercise, companies can now use interactive whiteboards incorporating speech-to-text or handwriting-to-text algorithms, together with high-quality touch commands . Moreover, the whiteboards can link to data warehouses , thereby enabling self-service analytics or even machine-learning algorithms for performing the analyses required in confirming or rejecting potential root causes.
3. Designing solutions
Augmented- and virtual-reality applications can help designers’ creation process become even more productive. Faster iterations between the drawing board and a more real-life representation shorten lead times toward final design. Rapid prototyping and 3D printing can accelerate this process even further by bringing intermediate versions of the solution to life.
4. Testing solutions
Once a solution has been designed, it is crucial to test its efficiency and effectiveness. The increase in computing power enables companies to perform extensive computational simulations . Using digital twins helps organizations create virtual mirrors of their operations, allowing them to test ideas more realistically before implementation.
5. Sustaining, sharing, and continuously improving
The digital communication and collaboration platforms that are now in widespread use can often be linked with interactive tools such as digital whiteboards, minimizing the time teams spend on documentation so they can instead focus on the creative parts of problem solving. Having past records of problem-solving sheets available at only one touch avoids solving the same problem all over again.
The above list shows how the ancient art of root-cause problem solving can take shape in today’s environment. The question for most organizations is how to start, especially with technologies that can sound like science fiction. A learning center designed to replicate an actual, digitally enabled working environment can provide the first step, helping people experience the impact these technologies can achieve in a practical and realistic setting.
Connect with our Operations Practice
Root Cause Analysis – The 5 Whys Technique
This elementary and often effective approach to problem-solving promotes deep thinking through questioning, and can be adapted quickly and applied to most problems. For example, asking “Why?” may be a favorite technique of your three-year-old child in driving you crazy, but it could teach you a valuable problem-solving technique.
“If you don’t ask the right questions, you don’t get the right answers. A question asked in the right way often points to its answer. Asking questions is the ABC of diagnosis. Only the inquiring mind solves problems.” – Edward Hodnett
The “5 Whys” is a simple problem-solving technique that helps you to get to the root of a problem quickly, which was originally developed by Sakichi Toyota. It was used within the Toyota Motor Corporation during the evolution of its manufacturing methodologies. It is a critical component of problem-solving training, delivered as part of the induction into the Toyota Production System.
How to Conduct 5 Whys Analysis?
When you’re looking to solve a problem, start at the result and work backward (toward the root cause), continually asking: “Why?” You’ll need to repeat this over and over until the root cause of the problem becomes apparent.
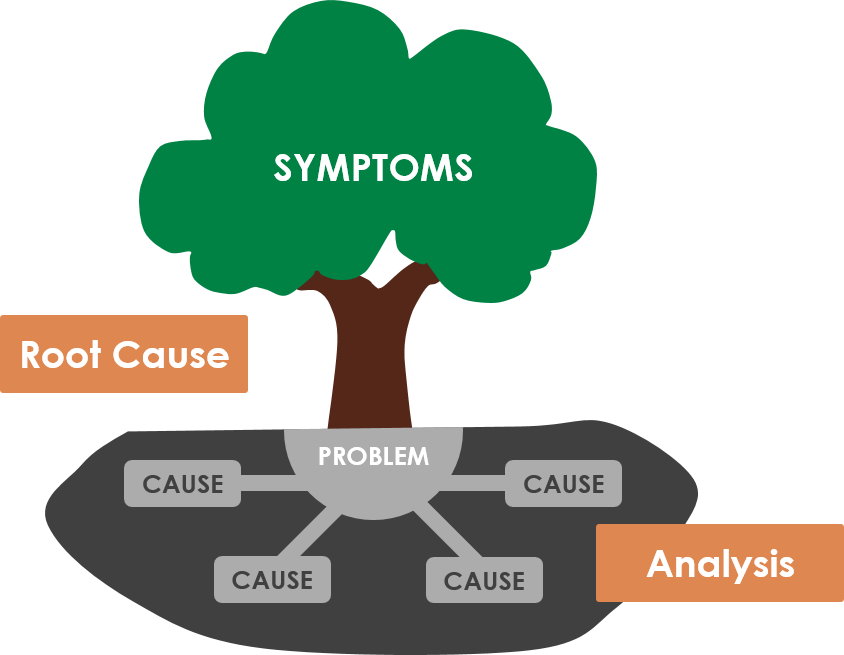
The 5 Whys strategy involves looking at any problem and asking: “Why?” and “What caused this problem?” Very often, the answer to the first “why” will prompt another “why” and the answer to the second “why” will prompt another and so on; hence the name the 5 Whys strategy.
The 5 Whys exercise is vastly improved when applied by a team and there are five basic steps to conducting it:
- Write down the specific problem. Writing the issue helps you formalize the problem and describe it completely. It also helps a team focus on the same problem.
- Ask “Why” the problem happens and write the answer down below the problem.
- If the answer you just provided doesn’t identify the root cause of the problem that you wrote down in Step 1, ask “Why” again and write that answer down.
- Loopback to step 3 until the team is in agreement that the problem’s root cause is identified. Again, this may take fewer or more times than five Whys.
- After settling on the most probable root cause of the problem and obtaining confirmation of the logic behind the analysis, develop appropriate corrective actions to remove the root cause from the system.
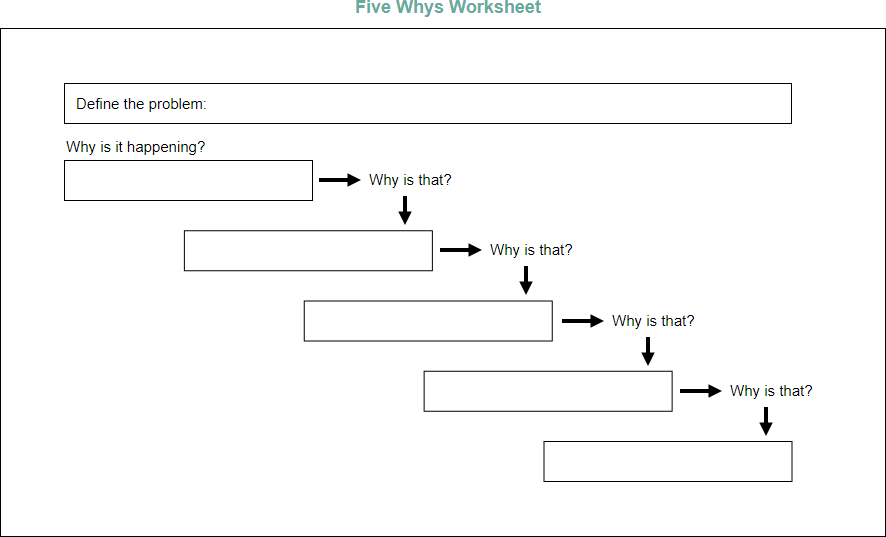
Edit this Diagram
5 Whys Example
The vehicle will not start. (The problem)
- Why? – The battery is dead. (First why)
- Why? – The alternator is not functioning. (Second why)
- Why? – The alternator belt has broken. (Third why)
- Why? – The alternator belt was well beyond its useful service life and not replaced. (Fourth why)
- Why? – The vehicle was not maintained according to the recommended service schedule. (Fifth why, a root cause)
Note: A 5 Whys analysis sometime could be taken further to a sixth, seventh, or higher level, but five iterations of asking why are generally sufficient to get to a root cause.
5-Whys Criticisms
Here are each of the criticisms as listed on the Wikipedia:
- Stopping at symptoms, not the root cause
- Limited by the investigator’s knowledge.
- Not asking the right Why questions.
- Not repeatable – Different people build different 5 Whys.
- The tendency to isolate a single root cause
©2024 by Visual Paradigm. All rights reserved.
- Terms of Service
- Privacy Policy
- Security Overview
By using this site you agree to our use of cookies. Please refer to our privacy policy for more information. Close

7 Powerful Problem-Solving Root Cause Analysis Tools
The first step to solving a problem is to define the problem precisely. It is the heart of problem-solving.
Root cause analysis is the second important element of problem-solving in quality management. The reason is if you don't know what the problem is, you can never solve the exact problem that is hurting the quality.
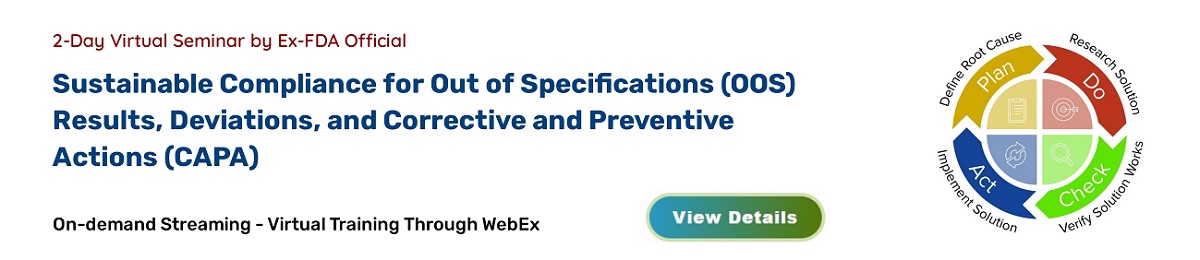
Manufacturers have a variety of problem-solving tools at hand. However, they need to know when to use which tool in a manner that is appropriate for the situation. In this article, we discuss 7 tools including:
- The Ishikawa Fishbone Diagram (IFD)
- Pareto Chart
- Failure Mode and Effects Analysis (FMEA)
- Scatter Diagram
- Affinity Diagram
- Fault Tree Analysis (FTA)
1. The Ishikawa Fishbone Diagram IFD
The model introduced by Ishikawa (also known as the fishbone diagram) is considered one of the most robust methods for conducting root cause analysis. This model uses the assessment of the 6Ms as a methodology for identifying the true or most probable root cause to determine corrective and preventive actions. The 6Ms include:
- Measurement,
- Mother Nature- i.e., Environment
Related Training: Fishbone Diagramming
2. Pareto Chart
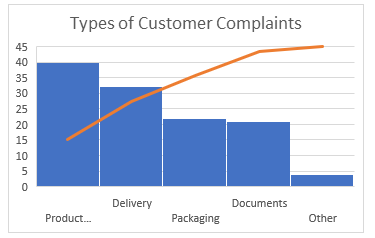
The Pareto Chart is a series of bars whose heights reflect the frequency or impact of problems. On the Chart, bars are arranged in descending order of height from left to right, which means the categories represented by the tall bars on the left are relatively more frequent than those on the right.
Related Training: EFFECTIVE INVESTIGATIONS AND CORRECTIVE ACTIONS (CAPA) Establishing and resolving the root causes of deviations, problems and failures
This model uses the 5 Why by asking why 5 times to find the root cause of the problem. It generally takes five iterations of the questioning process to arrive at the root cause of the problem and that's why this model got its name as 5 Whys. But it is perfectly fine for a facilitator to ask less or more questions depending on the needs.
Related training: Accident/Incident Investigation and Root Cause Analysis
4. Failure Mode and Effects Analysis (FMEA)
FMEA is a technique used to identify process and product problems before they occur. It focuses on how and when a system will fail, not if it will fail. In this model, each failure mode is assessed for:
- Severity (S)
- Occurrence (O)
- Detection (D)
A combination of the three scores produces a risk priority number (RPN). The RPN is then provided a ranking system to prioritize which problem must gain more attention first.
Related Training: Failure Mode Effects Analysis
5. Scatter Diagram
A scatter diagram also known as a scatter plot is a graph in which the values of two variables are plotted along two axes, the pattern of the resulting points revealing any correlation present.
To use scatter plots in root cause analysis, an independent variable or suspected cause is plotted on the x-axis and the dependent variable (the effect) is plotted on the y-axis. If the pattern reflects a clear curve or line, it means they are correlated. If required, more sophisticated correlation analyses can be continued.
Related Training: Excel Charting Basics - Produce Professional-Looking Excel Charts
6. Affinity Diagram
Also known as KJ Diagram, this model is used to represent the structure of big and complex factors that impact a problem or a situation. It divides these factors into small classifications according to their similarity to assist in identifying the major causes of the problem.
7. Fault Tree Analysis (FTA)
The Fault Tree Analysis uses Boolean logic to arrive at the cause of a problem. It begins with a defined problem and works backward to identify what factors contributed to the problem using a graphical representation called the Fault Tree. It takes a top-down approach starting with the problem and evaluating the factors that caused the problem.
Finding the root cause isn't an easy because there is not always one root cause. You may have to repeat your experiment several times to arrive at it to eliminate the encountered problem. Using a scientific approach to solving problem works. So, its important to learn the several problem-solving tools and techniques at your fingertips so you can use the ones appropriate for different situations.
ComplianceOnline Trainings on Root Cause Analysis
P&PC, SPC/6Sigma, Failure Investigation, Root Cause Analysis, PDCA, DMAIC, A3 This webinar will define what are the US FDA's expectation for Production and Process Control / Product Realization, the use of statistical tehniques, 6 sigma, SPC, for establishing, controlling , and verifying the acceptability of process capability and product characteristics, product acceptance or validation and other studies. Non-conformance, OOS, deviations Failure Investigations, and Root Cause Analysis, PDCA, DMAIC, and similar project drivers to improvement, A# and similar dash boards.
Accident/Incident Investigation and Root Cause Analysis If a major workplace injury or illness occurred, what would you do? How would you properly investigate it? What could be done to prevent it from happening again? A properly executed accident/incident investigation drives to the root causes of the workplace accident to prevent a repeat occurrence. A good accident/incident investigation process includes identifying the investigation team, establishing/reviewing written procedures, identifying root causes and tracking of all safety hazards found to completion.
Root Cause Analysis - The Heart of Corrective Action This presentation will explain the importance of root cause analysis and how it fits into an effective corrective and preventive action system. It will cover where else in your quality management system root cause analysis can be used and will give examples of some of the techniques for doing an effective root cause analysis. Attendees will learn how root cause analysis can be used in process control.
Addressing Non-Conformances using Root Cause Analysis (RCA) RCA assumes that systems and events are interrelated. An action in one area triggers an action in another, and another, and so on. By tracing back these actions, you can discover where the issue started and how it grew into the problem you're now facing.
Introduction to Root Cause Investigation for CAPA If you have reoccurring problems showing up in your quality systems, your CAPA system is not effective and you have not performed an in-depth root cause analysis to be able to detect through proper problem solving tools and quality data sources, the true root cause of your problem. Unless you can get to the true root cause of a failure, nonconformity, defect or other undesirable situation, your CAPA system will not be successful.
Root Cause Analysis and CAPA Controls for a Compliant Quality System In this CAPA webinar, learn various regulations governing Corrective and Preventive Actions (CAPA) and how organization should collect information, analyze information, identify, investigate product and quality problems, and take appropriate and effective corrective and/or preventive action to prevent their recurrence.
Root Cause Analysis for CAPA Management (Shutting Down the Alligator Farm) Emphasis will be placed on realizing system interactions and cultural environment that often lies at the root of the problem and prevents true root cause analysis. This webinar will benefit any organization that wants to improve the effectiveness of their CAPA and failure investigation processes.
Root Cause Analysis for Corrective and Preventive Action (CAPA) The Quality Systems Regulation (21 CFR 820) and the Quality Management Standard for Medical Devices (ISO 13485:2003), require medical device companies to establish and maintain procedures for implementing corrective and preventive action (CAPA) as an integral part of the quality system.
Strategies for an Effective Root Cause Analysis and CAPA Program This webinar will provide valuable assistance to all regulated companies, a CAPA program is a requirement across the Medical Device, Diagnostic, Pharmaceutical, and Biologics fields. This session will discuss the importance, requirements, and elements of a root cause-based CAPA program, as well as detailing the most effective ways to determine root cause and describing the uses of CAPA data.
Legal Disclaimer
This piece of content and any of its enclosures, attachments or appendices, references are created to provide solely for information purpose. ComplianceOnline has made all effort to provide accurate information concerning the subject matter covered. This content is created from interpretation, and understanding of relevant and applicable information and it is not all inclusive. It can be best used in conjunction with your professional judgment and discretion.
However, this piece of content and any other ancillary items disseminated in connection with same are not necessarily prepared by a person licensed to practice law in a particular jurisdiction. This piece of content is not a substitute for the advice of an attorney. If you require legal or other expert advice, you should seek the services of a competent attorney or other professional.
ComplianceOnline necessarily is not, cannot and will not be liable for any claims, damages, or regulatory legal proceedings initiated as a consequence of you using whole or any part of the content present in this document. If any action, claim for damages, or regulatory proceedings is commenced against ComplianceOnline as a consequence of your use of this document, then and in that event, you agree to indemnify ComplianceOnline for such claims, and for any attorney's fees expended by ComplianceOnline in connection with defense of same.


How it works
For Business
Join Mind Tools
Article • 11 min read
Getting to the Root of a Problem Quickly
By the Mind Tools Content Team
5 Whys Root-Cause Analysis
Have you ever had a problem that refused to go away? No matter what you did, sooner or later it would return, perhaps in another form.
Stubborn or recurrent problems are often symptoms of deeper issues. "Quick fixes" may seem convenient, but they often solve only the surface issues and waste resources that could otherwise be used to tackle the real cause.
In this article and in the video, below, we look at the 5 Whys technique (sometimes known as 5Y). This is a simple but powerful tool for cutting quickly through the outward symptoms of a problem to reveal its underlying causes – so that you can deal with it once and for all.
Origins of the 5 Whys Technique
Sakichi Toyoda, the Japanese industrialist, inventor, and founder of Toyota Industries, developed the 5 Whys technique in the 1930s. It became popular in the 1970s, and Toyota still uses it to solve problems today.
Toyota has a "go and see" philosophy. This means that its decision making is based on an in-depth understanding of what's actually happening on the shop floor , rather than on what someone in a boardroom thinks might be happening.
The 5 Whys technique is true to this tradition, and it is most effective when the answers come from people who have hands-on experience of the process or problem in question.
The method is remarkably simple: when a problem occurs, you drill down to its root cause by asking "Why?" five times. Then, when a counter-measure becomes apparent, you follow it through to prevent the issue from recurring.
The 5 Whys uses "counter-measures," rather than "solutions." A counter-measure is an action or set of actions that seeks to prevent the problem from arising again, while a solution may just seek to deal with the symptom. As such, counter-measures are more robust, and will more likely prevent the problem from recurring.
When to Use a 5 Whys Analysis
You can use 5 Whys for troubleshooting, quality improvement, and problem solving, but it is most effective when used to resolve simple or moderately difficult problems.
It may not be suitable if you need to tackle a complex or critical problem. This is because 5 Whys can lead you to pursue a single track, or a limited number of tracks, of inquiry when, in fact, there could be multiple causes. In cases like these, a wider-ranging method such as Cause and Effect Analysis or Failure Mode and Effects Analysis may b e more effective.
This simple 5 Whys technique, however, can often direct you quickly to the root cause of a problem. So, whenever a system or process isn't working properly, give it a try before you embark on a more in-depth approach – and certainly before you attempt to develop a solution.
The tool's simplicity gives it great flexibility, too, and 5 Whys combines well with other methods and techniques, such as Root Cause Analysis . It is often associated with Lean Manufacturing , where it is used to identify and eliminate wasteful practices. It is also used in the analysis phase of the Six Sigma quality improvement methodology.
How to Use the 5 Whys
The model follows a very simple seven-step process: [1]
1. Assemble a Team
Gather together people who are familiar with the specifics of the problem, and with the process that you're trying to fix. Include someone to act as a facilitator , who can keep the team focused on identifying effective counter-measures.
2. Define the Problem
If you can, observe the problem in action. Discuss it with your team and write a brief, clear problem statement that you all agree on. For example, "Team A isn't meeting its response time targets" or "Software release B resulted in too many rollback failures."
Then, write your statement on a whiteboard or sticky note, leaving enough space around it to add your answers to the repeated question, "Why?"
3. Ask the First "Why?"
Ask your team why the problem is occurring. (For example, "Why isn't Team A meeting its response time targets?")
Asking "Why?" sounds simple, but answering it requires serious thought. Search for answers that are grounded in fact: they must be accounts of things that have actually happened, not guesses at what might have happened.
This prevents 5 Whys from becoming just a process of deductive reasoning, which can generate a large number of possible causes and, sometimes, create more confusion as you chase down hypothetical problems.
Your team members may come up with one obvious reason why, or several plausible ones. Record their answers as succinct phrases, rather than as single words or lengthy statements, and write them below (or beside) your problem statement. For example, saying "volume of calls is too high" is better than a vague "overloaded."
4. Ask "Why?" Four More Times
For each of the answers that you generated in Step 3, ask four further "whys" in succession. Each time, frame the question in response to the answer you've just recorded.
What Is a 5 Whys Template?
The diagram, below, shows an example of 5 Whys in action, following a single lane of inquiry.
Figure 1: 5 Whys Example (Single Lane)
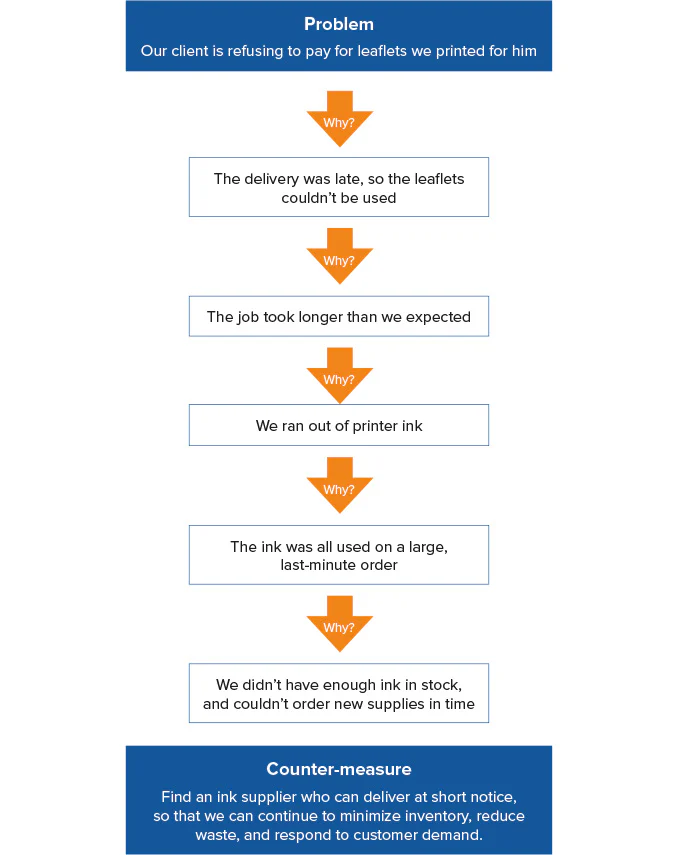
The 5 Whys method also allows you to follow multiple lanes of inquiry. An example of this is shown in Figure 2, below.
In our example, asking "Why was the delivery late?" produces a second answer (Reason 2). Asking "Why?" for that answer reveals a single reason (Reason 1), which you can address with a counter-measure.
Similarly, asking "Why did the job take longer than expected?" has a second answer (Reason 2), and asking "Why?" at this point reveals a single reason (Reason 1). Another "Why?" here identifies two possibilities (Reasons 1 and 2) before a possible counter-measure becomes evident.
There is also a second reason for "Why we ran out of printer ink" (Reason 2), and a single answer for the next "Why?" (Reason 1), which can then be addressed with a counter-measure.
Figure 2: 5 Whys Example (Multiple Lanes)

Step 5. Know When to Stop
You'll know that you've revealed the root cause of the problem when asking "why" produces no more useful responses, and you can go no further. An appropriate counter-measure or process change should then become evident. (As we said earlier, if you're not sure that you've uncovered the real root cause, consider using a more in-depth problem-solving technique like Cause and Effect Analysis , Root-Cause Analysis , or FMEA .)
If you identified more than one reason in Step 3, repeat this process for each of the different branches of your analysis until you reach a root cause for each one.
6. Address the Root Cause(s)
Now that you've identified at least one root cause, you need to discuss and agree on the counter-measures that will prevent the problem from recurring.
7. Monitor Your Measures
Keep a close watch on how effectively your counter-measures eliminate or minimize the initial problem. You may need to amend them, or replace them entirely. If this happens, it's a good idea to repeat the 5 Whys process to ensure that you've identified the correct root cause.
Appreciation
A similar question-based approach known as "appreciation" can help you to uncover factors in a situation that you might otherwise miss.
It was originally developed by the military to assist commanders in gaining a comprehensive understanding of any fact, problem or situation. But you can also apply it in the workplace.
Starting with a fact, you first ask the question, "So what?" – in other words, what are the implications of that fact? Why is this fact important?
You then continue asking that question until you've drawn all possible conclusions from it.
The major difference between this and the 5 Whys technique is that appreciation is often used to get the most information out of a simple fact or statement, while 5 Whys is designed to drill down to the root of a problem.
Tips for Using the 5 Whys Technique
- Try to move quickly from one question to the next. That way, you'll have the full picture before you jump to any conclusions.
- The "5" in 5 Whys is really just a " rule of thumb ." In some cases, you may need to ask "Why?" a few more times before you get to the root of the problem. In other cases, you may reach this point before you ask your fifth "Why?" If you do, make sure that you haven't stopped too soon, and that you're not simply accepting "knee-jerk" responses.
- Know when to stop! The important point is to stop asking "Why?" when you stop producing useful responses.
Frequently Asked Questions About 5 Whys
1. what is the 5 whys technique.
The 5 Whys Technique is a problem-solving method involving repeatedly asking "why?" It's a way of quickly getting to the root cause of a situation.
2. Who Invented 5 Whys?
The 5 Whys technique was invented in the 1930s by Sakichi Toyoda, the Japanese industrialist, inventor, and founder of Toyota Industries.
5 Whys Infographic
See our infographic on the 5 Whys and use it to get to the root of your problems!
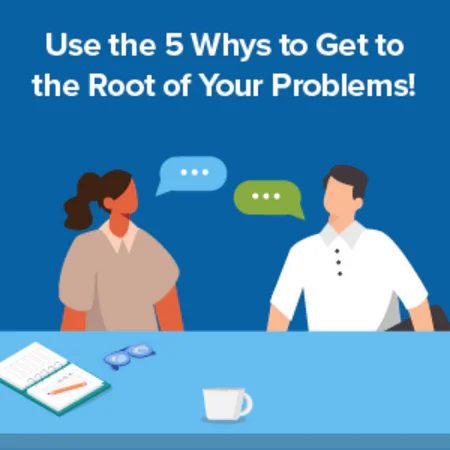
Bear in mind that appreciation can restrict you to one line of thinking. For instance, once you've answered your first "So what?" question, you might follow a single line of inquiry to its conclusion. To avoid this, repeat the appreciation process several times over to make sure that you've covered all bases.
The 5 Whys strategy is a simple, effective tool for uncovering the root of a problem. You can use it in troubleshooting, problem-solving, and quality-improvement initiatives.
Start with a problem and ask why it is occurring. Make sure that your answer is grounded in fact, and then ask the question again. Continue the process until you reach the root cause of the problem, and you can identify a counter-measure that will prevent it from recurring.
Bear in mind that this questioning process is best suited to simple or moderately difficult problems. Complex problems may benefit from a more detailed approach, although using 5 Whys will still give you useful insights.
[1] Pojasek, R. (2000). 'Asking "Why?" Five Times,' Environmental Quality Management , Volume 10, Issue 1, 79–84. Available here . [Accessed July 1, 2022.]
You've accessed 1 of your 2 free resources.
Get unlimited access
Discover more content
Using root cause analysis.
Find the Root of Your Problems
Root Cause Analysis
Tracing a Problem to Its Origins
Add comment
Comments (0)
Be the first to comment!
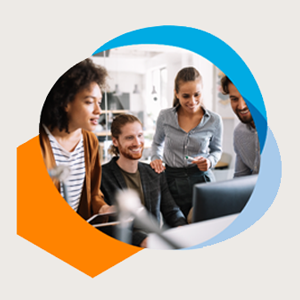
Try Mind Tools for FREE
Get unlimited access to all our career-boosting content and member benefits with our 7-day free trial.
Sign-up to our newsletter
Subscribing to the Mind Tools newsletter will keep you up-to-date with our latest updates and newest resources.
Subscribe now
Business Skills
Personal Development
Leadership and Management
Member Extras
Most Popular
Newest Releases
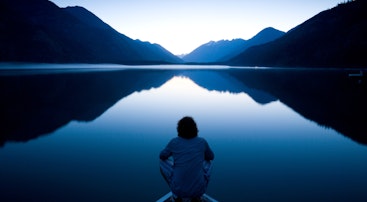
What Is Gibbs' Reflective Cycle?
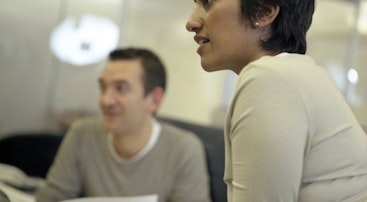
Team Briefings
Mind Tools Store
About Mind Tools Content
Discover something new today
Onboarding with steps.
Helping New Employees to Thrive
NEW! Pain Points Podcast - Perfectionism
Why Am I Such a Perfectionist?
How Emotionally Intelligent Are You?
Boosting Your People Skills
Self-Assessment
What's Your Leadership Style?
Learn About the Strengths and Weaknesses of the Way You Like to Lead
Recommended for you
The cedar™ feedback model.
Feeding Back, Collaboratively
Business Operations and Process Management
Strategy Tools
Customer Service
Business Ethics and Values
Handling Information and Data
Project Management
Knowledge Management
Self-Development and Goal Setting
Time Management
Presentation Skills
Learning Skills
Career Skills
Communication Skills
Negotiation, Persuasion and Influence
Working With Others
Difficult Conversations
Creativity Tools
Self-Management
Work-Life Balance
Stress Management and Wellbeing
Coaching and Mentoring
Change Management
Team Management
Managing Conflict
Delegation and Empowerment
Performance Management
Leadership Skills
Developing Your Team
Talent Management
Problem Solving
Decision Making
Member Podcast
Medical Fishbone Diagram
Explore the Medical Fishbone Diagram to identify the causes of healthcare issues with our free PDF template. Streamline problem-solving in clinical settings.
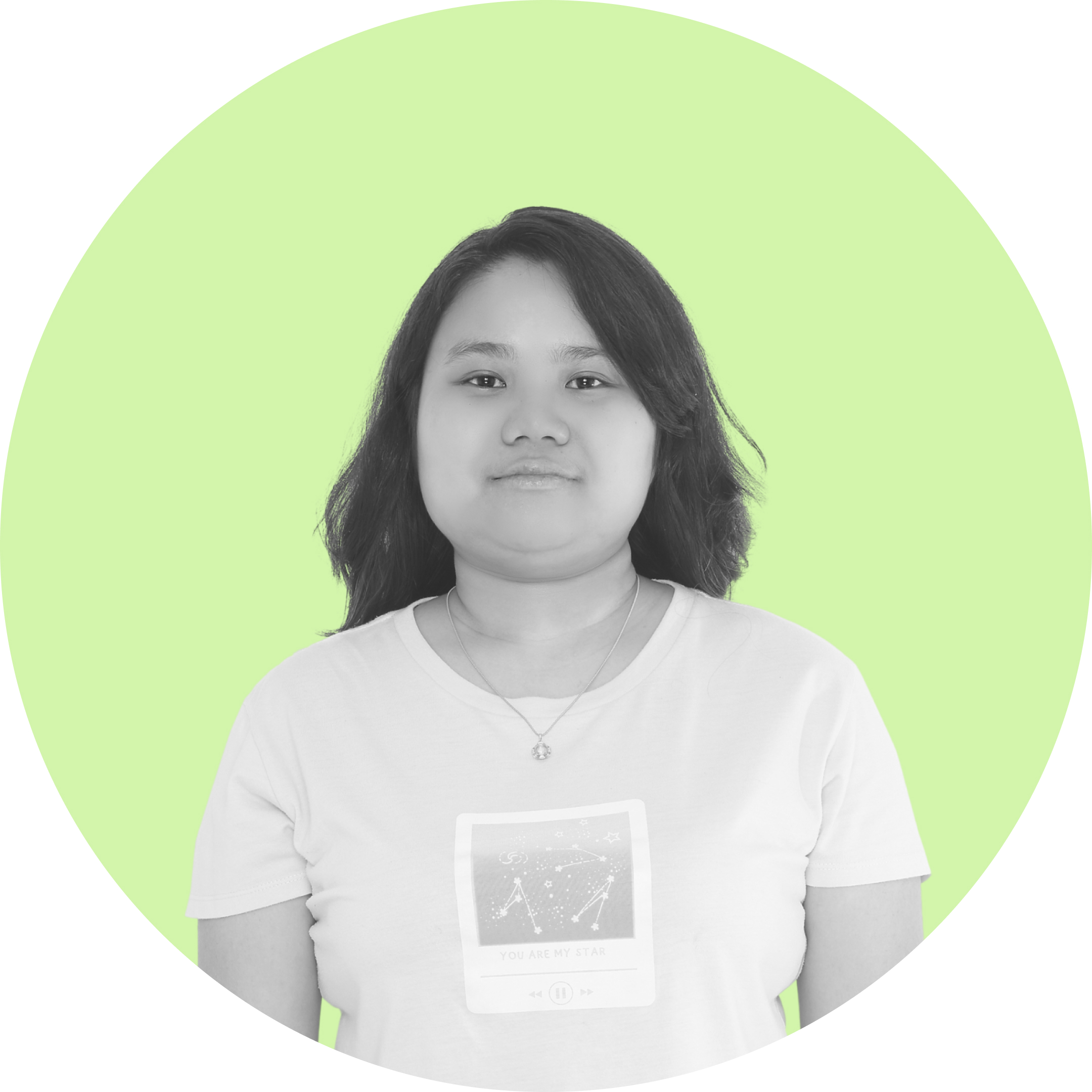
By Russell Tan on Apr 21, 2024.
Fact Checked by Ericka Pingol.
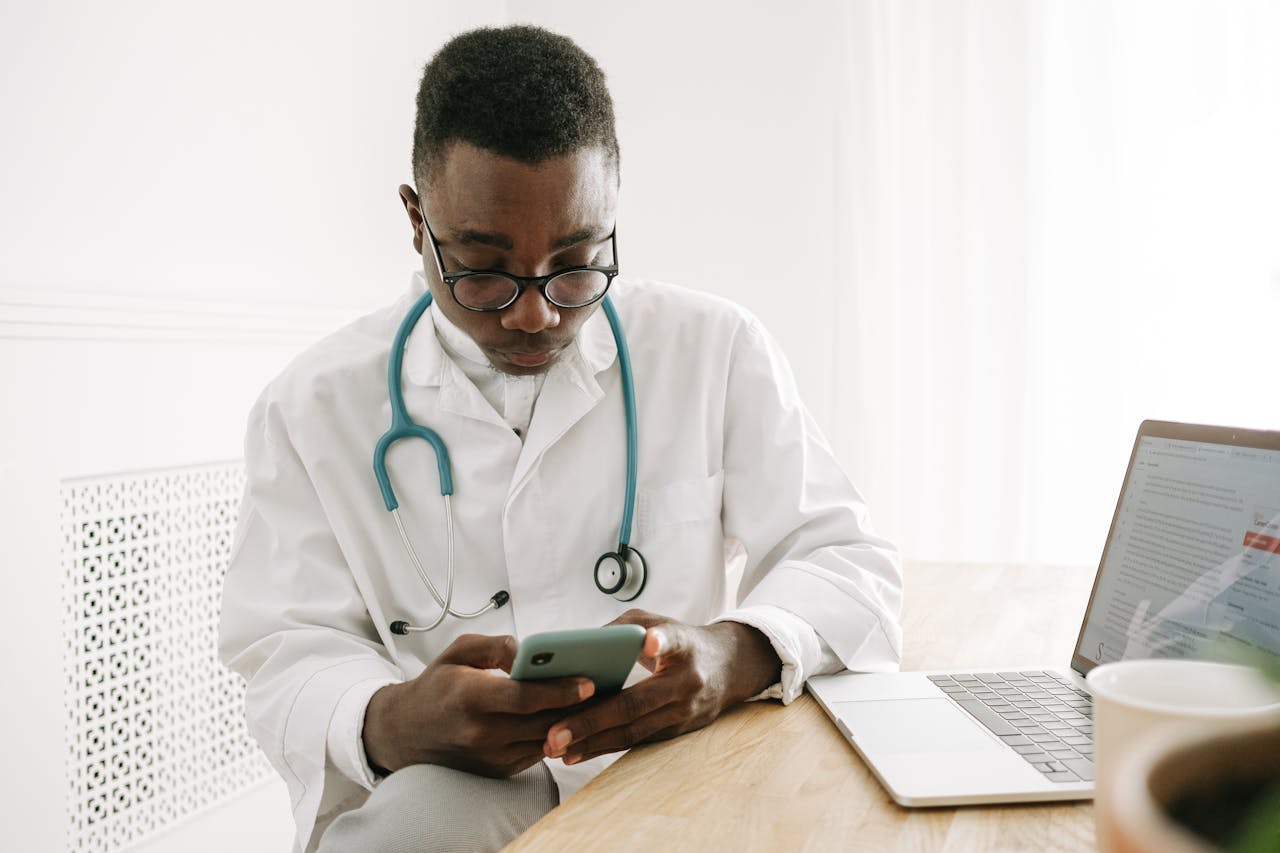
What is a fishbone diagram?
A Fishbone Diagram, also known as an Ishikawa diagram or a cause-and-effect diagram, is a visual tool used to systematically identify, sort, and display possible causes of a specific problem or effect. It helps to identify potential underlying issues by categorizing potential causes into major categories, which can vary depending on the context.
The diagram is called a "fishbone" because its shape resembles the skeleton of a fish, with a central "spine" and several branches representing different categories of root causes or contributing factors leading to the problem.
When is a fishbone diagram used?
Fishbone diagrams are ideal for situations where you have a complex problem and a lot of initial ideas about major cause of what might be causing it. Here are some specific times they come in handy:
- Brainstorming sessions: Fishbone diagrams help organize a team's initial thoughts on potential causes. Everyone can contribute ideas, which are then categorized logically for further discussion.
- Complex problems: For issues with many potential causes, a fishbone diagram helps you delve deeper into the root causes, not just surface-level solutions.
- Quality improvement projects: These diagrams help identify and document all the factors contributing to a problem, allowing for targeted interventions to improve quality.
- Before implementing solutions: Using a fishbone diagram ensures you've considered all possible causes before taking action. This helps you choose the most effective corrective steps.
By organizing and categorizing potential causes, fishbone diagrams promote a thorough analysis of problems. This leads to a deeper, better understanding of the root causes and, ultimately, more effective solutions.
Printable Medical Fishbone Diagram
Download this Medical Fishbone Diagram to visually map out potential causes of medical issues, aiding in root cause analysis and problem-solving for healthcare professionals.
When is the fishbone diagram used in the medical field?
Fishbone diagrams are a valuable tool for healthcare and health care professionals to tackle various challenges. Here are some key areas where they shine:
- Improving patient care: Fishbone diagrams can help identify the root causes of quality issues in patient care. This allows teams to develop targeted interventions for enhanced care delivery.
- Ensuring patient safety: Following a safety incident or near miss, these diagrams help analyze the event and pinpoint contributing factors. This knowledge is then used to develop strategies to prevent similar incidents in the future.
- Diagnosing complex conditions: Fishbone diagrams can organize and analyze potential contributing factors for patients with complex medical conditions, aiding in a more accurate diagnosis.
- Boosting operational efficiency: Fishbone diagrams can help healthcare teams identify and address inefficiencies in everyday operations, such as delays in patient discharge or medication errors.
By promoting a structured approach to problem-solving, fishbone diagrams empower healthcare professionals to improve patient care, enhance safety, and optimize healthcare delivery.
How is the fishbone diagram used in the medical field?
Fishbone diagrams are powerful tools for healthcare professionals to pinpoint the root causes of problems. Here's how they work:
- Define the problem: Start by clearly stating the issue you want to address. Is it a rise in medication errors, high patient readmission rates, or inefficient appointment scheduling? Write this problem statement at the "head" of the fishbone diagram.
- Build the fishbone: Draw a horizontal line as the "spine" of the fish. Branching off this line at an angle, draw main categories that might contribute to the problem.
- Brainstorm causes: For each category, brainstorm specific factors that could be causing the problem. This is where teamwork shines! Include a diverse group of healthcare providers to capture various perspectives.
- Analyze and prioritize: Don't stop at listing everything! Analyze the brainstormed causes to identify the most likely culprits. Consider factors like frequency, severity, and available data.
- Develop solutions: Finally, use the identified root causes to develop action plans. This might involve staff training, implementing new workflows, or acquiring new equipment.
By following these steps, healthcare teams can effectively create and leverage fishbone diagrams to troubleshoot and improve patient care and overall operational efficiency.
What can you expect to see in a Medical Fishbone Diagram?
The fishbone diagram helps identify, explore, and display the root causes, contributing factors, and problems with fish bones. Here’s a detailed look at the essential components of a Medical Fishbone Diagram:
Problem statement
The problem statement is the focal point of the Fishbone Diagram and is usually placed at the head of the fish, with the fishbone diagram's spine leading to it. This statement should clearly and concisely describe the issue being addressed.
In a medical context, this could be a specific patient safety concern, a frequent clinical diagnostic error, or any undesirable outcome in patient care. The problem statement serves as the endpoint to which all diagram branches contribute, effectively summarizing the effect or issue the analysis aims to resolve.
Root causes of the problem
Root causes are the underlying factors that contribute directly to the problem. These are typically identified through brainstorming sessions and are placed along the main branches or "bones" stemming from the diagram's spine. In the context of healthcare improvement, root causes can be categorized into various domains, such as:
- Personnel: Staff-related factors, such as training, skill levels, or staffing ratios.
- Procedures: Clinical and administrative processes or guidelines that are inadequate, outdated, or incorrectly followed.
- Equipment: Issues with the medical or technological equipment used in patient care, including availability, maintenance, and functionality.
- Materials: Concerns about the supplies and medications used, such as their quality, availability, or storage conditions.
- Environment: Physical or organizational work environment issues that affect the quality of care or staff performance.
Identifying root causes requires a deep dive into the systemic issues that lead to the problem, looking beyond the immediate or superficial to define and identify root causes.
Contributing factors
Contributing factors are secondary causes that, while not directly causing the problem, influence its occurrence or severity. These are often found along the smaller branches or "fishbones" that stem from the main categories of root causes. In healthcare and medical education, contributing factors might include:
- Communication: Breakdowns or lapses in communication among healthcare providers or between providers and patients.
- Culture: Organizational culture aspects that might discourage reporting errors, asking for help, or adhering to best practices.
- External factors: Regulatory changes, insurance policies, or other external pressures that affect clinical practice.
- Patient factors: Patient-specific factors include comorbidities, non-adherence to treatment plans, or unique vulnerabilities.
It is essential to identify contributing factors because they often represent areas where small changes can significantly improve outcomes or prevent the problem.
How does our Medical Fishbone Diagram template work?
Our fishbone diagram templates provide a structured method for healthcare professionals to analyze and visualize the root cause of medical issues. It's crafted to facilitate a systematic approach to problem-solving in clinical settings. Here’s how to use our template:
Step 1: Download the template
Begin the process by downloading a copy of our template from our website. The template is free in various formats, catering to different preferences, whether you like working digitally or prefer a physical copy. Ensure you have the appropriate software to open and edit the template to customize it digitally.
Step 2: Customize according to the specific medical issue
Tailor the template to the particular medical issue or problem you're addressing. The template is designed to help you categorize potential causes into main categories such as personnel, procedures, equipment, and environment. Adapt these categories based on the nature of the problem and the specific context of your healthcare setting.
Step 3: Explain how it works to your team
If you're using this template within a team or with colleagues, it is crucial to ensure everyone understands how to interpret and contribute to it. Guide them through each section, emphasizing the importance of identifying the root cause and any contributing factors. This step is essential for fostering a collaborative problem-solving environment.
Step 4: Identify and list potential causes
Use the template for a brainstorming session and list all possible causes of the problem, placing them under the appropriate categories. Encourage team members to contribute their insights and perspectives to ensure a comprehensive analysis. This collective approach enhances the depth and breadth of the root cause analysis.
Step 5: Analyze and prioritize issues
With all potential causes listed, the next step involves analyzing them to identify which are most likely contributing to the problem. This might require additional data collection or consultation with experts. Prioritize the issues based on their impact and the feasibility of addressing them, focusing on interventions identified causes that offer the greatest potential for improvement.
Step 6: Develop and implement action plans
Develop action plans to address the root causes based on the diagram created. This might involve procedures, training, equipment, or environmental changes. Implement these plans in a structured manner, monitoring their impact and adjusting as necessary.
What are the benefits of using the fishbone diagram in medicine?
Fishbone diagrams are powerful tools for healthcare and medical professionals, offering several key benefits:
- Deeper problem-solving: They visually break down complex problems, helping teams grasp the root causes more effectively.
- Enhanced collaboration: By encouraging input from everyone, fishbone diagrams foster teamwork and lead to more comprehensive solutions.
- Targeted solutions: These diagrams help identify the root causes, not just symptoms, leading to more effective and long-lasting improvements.
- Prioritized action: Teams can prioritize issues based on impact and feasibility, optimizing resource allocation and achieving quicker results.
- Improved diagnosis and treatment: Fishbone diagrams can streamline diagnosis by organizing and evaluating potential causes of patient symptoms.
By leveraging these benefits, fishbone diagrams empower healthcare professionals to have creative thinking to tackle challenges, improve patient care, and cultivate a culture of continuous improvement.
Why use Carepatron as your clinical documentation software?
Are overflowing charts and endless forms hindering your ability to connect with patients? Carepatron offers a comprehensive clinical documentation solution to streamline workflow and elevate patient care.
Imagine a secure, user-friendly platform that stores all your patient records, progress notes, and treatment plans in one place. Carepatron empowers you to manage documentation effortlessly while built-in communication tools keep you connected with patients and colleagues for seamless collaboration. Plus, with Carepatron, you can quickly develop and manage individualized care plans, ensuring a holistic approach to patient well-being.
Stop letting paperwork stand in the way of exceptional care. Sign up for a free Carepatron trial today and experience the difference. We'll help you streamline documentation of medical errors, free up valuable time, and empower you to focus on what matters most - your patients.
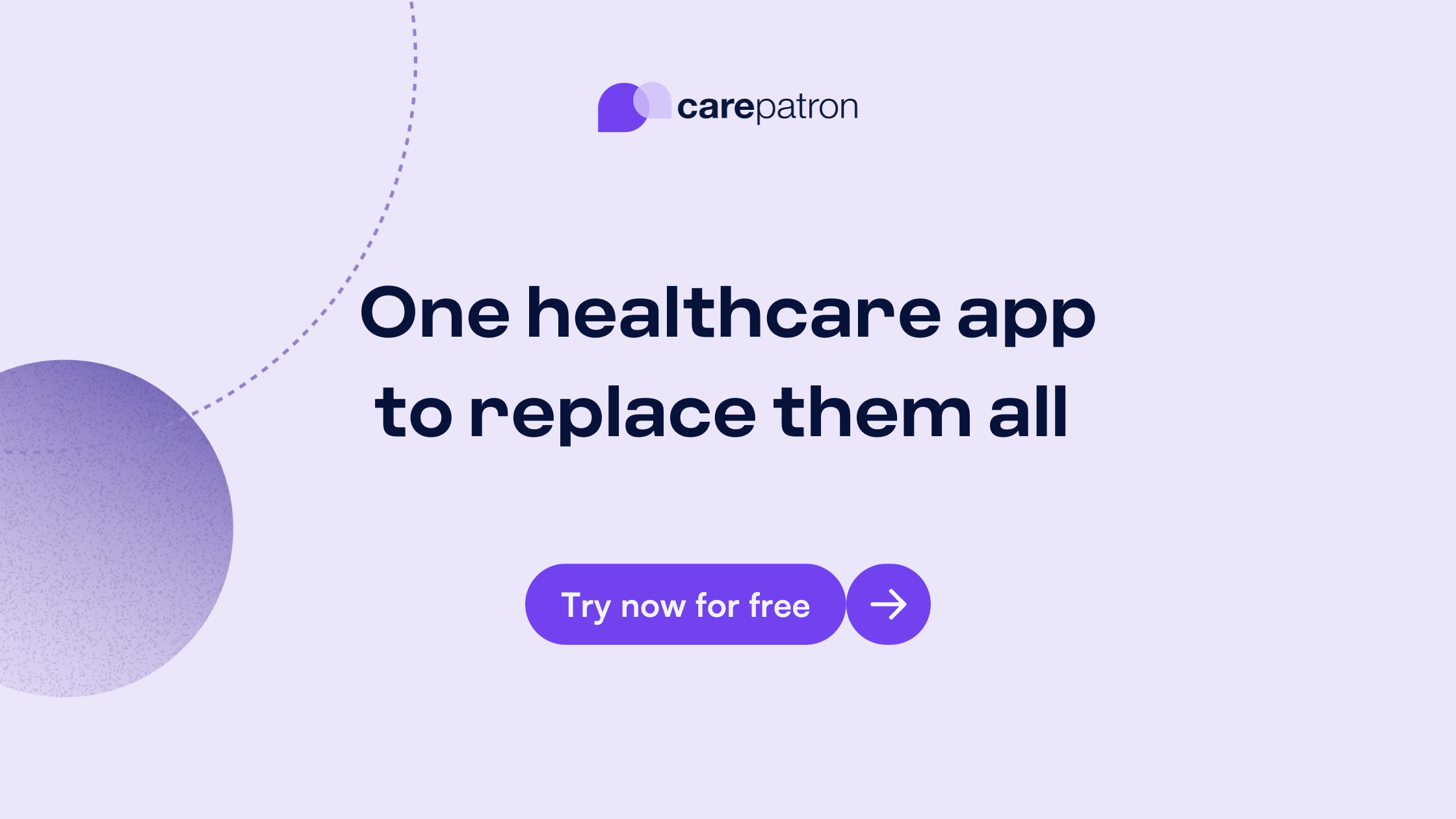
Commonly asked questions
By identifying the underlying causes of healthcare issues, Medical Fishbone Diagrams can help teams implement targeted solutions, ultimately improving patient care, quality management, and safety.
The main limitation of Medical Fishbone Diagrams is that they require accurate identification of causes and contributing factors, which can be challenging without sufficient data or if biases influence the analysis.
Yes! While they are instrumental in healthcare, Fishbone Diagrams can be adapted to analyze and solve problems in various fields such as business, engineering, and health care, research, and education.
Related Templates
Popular templates.
Massage Therapy Invoice Template
Get access to a free Massage Therapy Invoice Template with Carepatron. Streamline your documentation and invoicing process with our PDF.
Ankle Injury Diagnosis Chart
Learn more about ankle injuries and have a step-by-step guide on diagnosing them with our free ankle injury diagnosis chart template.
Health Triangle Worksheets
Explore and improve your well-being across physical, mental, and social health with our comprehensive Health Triangle Worksheets.
Cholecystitis Treatment Guidelines
Explore our Cholecystitis Treatment Guidelines for managing acute conditions. Download the PDF now.
Schizophrenia Treatment Guidelines
Discover the latest Schizophrenia Treatment Guidelines, including antipsychotic medication, psychosocial interventions, and cognitive behavioral therapy.
Breast Cancer Treatment Guidelines
Explore comprehensive Breast Cancer Treatment Guidelines for informed decisions. Learn about the latest protocols and options for adequate care.
Rheumatoid Arthritis Diagnosis Criteria
Learn about the essential Rheumatoid Arthritis Diagnosis Criteria for accurate identification and timely treatment in healthcare.
Harm Reduction Worksheets PDF
Make your harm reduction psychotherapy meaningful and effective with the help of the Harm Reduction Worksheets PDF.
Stigma in Addiction Worksheet
Discover how to challenge and overcome the stigma associated with addiction with our free downloadable Stigma in Addiction Worksheet.
Surrender in Recovery Worksheet
Discover a path to recovery with our Surrender in Recovery Worksheet. Embrace change and healing with guided self-reflection. Download the free template.
BPD DSM-5 Criteria PDF
Simplify mental health practice management with Carepatron. Secure, easy-to-use software for telehealth, documentation, and collaboration.
DSM 5 Criteria for Persistent Depressive Disorder
Explore the symptoms, diagnosis, and treatment of Persistent Depressive Disorder (PDD) with our comprehensive guide and free PDF download.
Printable List of ICD 10 Codes for Mental Health
Download our free PDF for a practical guide on using ICD-10 codes in mental health diagnosis and billing. Streamline your practice today.
Polyvagal Ladder
Explore the Polyvagal Ladder, a visual guide to understanding stress responses, promoting safety, and enhancing social engagement.
Face Sheet (Medical)
Explore the benefits of using a medical face sheet for efficient patient care, including quick patient data access and insurance verification.
Medicare 8-minute Rule Chart
Master the Medicare 8-Minute Rule with our comprehensive chart and guide. Simplify billing for time-based therapy services and maximize reimbursement.
Cataract Evaluation
Streamline your Cataract Evaluation process by using our template for documentation. Download for free today!
Wheelchair Evaluation
Download our Wheelchair Evaluation template to streamlines the documentation process through a evaluation of clients' mobility and seating needs.
Pediatric BMI Chart
Download our Pediatric BMI Chart for a resource that can assist you in assessing and documenting a child's weight status.
Bariatric Psychological Evaluation
Explore our comprehensive guide on Bariatric Psychological Evaluation to understand the importance, process, and benefits for surgery candidates.
Navicular Stress Fracture Test
Explore diagnosis and treatment for navicular stress fractures with our free guide on tests, symptoms, and recovery strategies.
Relationship Workbook
Strengthen your relationship with our workbook, offering exercises for better communication, intimacy, and conflict resolution.
Triphasic BBT Chart
Discover how a Triphasic BBT Chart can help track fertility and early pregnancy signs. Download our free PDF for insights and examples.
Scaphoid Fracture Test
Explore the essential aspects of scaphoid fractures, including symptoms, risk factors, and treatments. Access our free Scaphoid Fracture Test PDF for better patient care.
Health Anxiety CBT Worksheets
Overcome health anxiety with our CBT worksheets designed to help you understand and manage your fears. Download our free example today.
Female Acupuncture Points Chart
Explore our Female Acupuncture Points Chart for a comprehensive guide on key acupuncture points and meridians to enhance women's health treatments.
Musculoskeletal Examination Checklist
Explore a comprehensive guide on musculoskeletal system examination, conditions, treatments, and FAQs with a free checklist PDF download.
House-Tree-Person Test
Discover the House-Tree-Person Test, a simple yet insightful tool used in psychology to understand an individual's emotions and personality through drawings.
Pain Management Coding Cheat Sheet
Streamline your medical billing and coding for pain management with our comprehensive cheat sheet. Download our free PDF today.
Body Neutrality Worksheet
Explore our Body Neutrality Worksheet to help individuals foster self-acceptance and focus on the functionality of their bodies. Download it now!
Cope Ahead Worksheet
Master the art of coping ahead with our comprehensive worksheet. Prepare for challenging situations and enhance emotional resilience with Carepatron.
BPD Favorite Person Test
Discover more about the BPD Favorite Person Test, along with an example and free PDF download from Carepatron. Learn more about this critical aspect of borderline personality disorder.
EMDR Resourcing PDF
Download Carepatron's free PDF with examples of EMDR resourcing techniques. Explore different ways to support your clients with effective resourcing strategies.
Physical Therapy Exercise Flow Sheet PDF
Download Carepatron's free PDF of a Physical Therapy Exercise Flow Sheet example to track and document exercises effectively in your therapy practice.
CBT for Psychosis Worksheets PDF
Click here for PDFs of CBT for psychosis worksheets you can incorporate into your patient's treatment plan to help them manage their symptoms better.
Psychological Flexibility Worksheet
Our free Psychological Flexibility Worksheet will help you enhance psychological flexibility, improve resilience in relationships, and find purpose.
Schizoaffective Disorder Test
Discover if you may have Schizoaffective Disorder with our test. Get insights and guidance for better mental health. Quick, accurate, and confidential.
Autism Test for Adults
Make accurate adult autism assessments with our comprehensive testing guide and template. Try them now!
Massage Therapy Business Plan
Creating a massage therapy business plan? Download Carepatron's free PDF to guide you through the process and help you create a successful massage therapy business plan.
Example of Counseling Session Dialogue PDF
Explore a sample counseling session dialogue PDF for insight into effective communication and therapeutic techniques. Download now!
Food and Symptom Diary PDF
Track your food intake and symptoms on a symptom-free day with our convenient Food and Symptom Diary PDF report. Monitor your health quickly and effectively.
Newborn Exam Template
Streamline newborn examinations with our comprehensive template, ensuring thorough newborn assessment and care. Download now!
Schizotypal Personality Disorder Test (SPDT)
Explore the use of a self-report tool to screen for symptoms of schizotypal personality disorder among clients. Download a free printable test here!
ACT Bullseye Worksheet
Integrate the ACT Bullseye Worksheet to help clients reflect on and align their goals with their values.
Learning Needs Assessment Nursing
Unleash your full potential! Master nursing skills & knowledge with Carepatron's LNA guide. Boost patient care & career growth.
Hypochondria Test
Explore our guide on illness anxiety disorder: signs, impact, and treatments. Download a free Hypochondria Test to start your journey to better health.
Binocular Vision Test
Carepatron's free PDF download provides a binocular vision test example that you can use to assess your vision. Learn more about binocular vision and how to conduct the test effectively.
Radical Forgiveness Worksheet
Unlock the power of Radical Forgiveness with our comprehensive worksheet. Guide your patients to healing and transformation with our template and guide.
Family Roles In Addiction Worksheet
Guide families in building a supportive dynamic to aid clients struggling with substance use through their recovery journey.
Dependent Personality Disorder Treatment Guidelines
Improve treatment planning for dependent personality disorder with our free resource to improve client outcomes.
PASS Assessment
Explore the use of a specialized test to assess postural control among stroke patients to craft a more targeted rehabilitation plan.
CPT Test for ADHD
Learn about the CPT Test for ADHD, a vital tool for assessing attention deficit hyperactivity disorder efficiently and accurately.
Eden's Test
Discover the significance of Eden's Test in diagnosing thoracic outlet syndrome. Learn how this maneuver aids in identifying neurovascular compression.
Esthetician Business Plan
Crafting an Esthetician Business Plan is crucial for success. Download Carepatron's free PDF to guide you in creating your own professional business plan.
Teenage Bipolar Test
The teenage bipolar test is a crucial tool for identifying potential mood disorder symptoms in adolescents. Download Carepatron's free PDF example to learn how to administer and interpret the test.
Putting Thoughts on Trial Worksheet
Guide clients to learn how to support or challenge their thoughts with evidences through this free worksheet.
Test for Muscle Weakness
Learn how to determine muscle weakness with Carepatron's free PDF download and example. This resource provides valuable information on assessing muscle strength and functionality.
ADHD Planner
Help clients organize effectively with this ADHD Planner. Download Carepatron's free PDF example to better manage tasks and time, specially designed for individuals with ADHD.
Healthcare Marketing Plan
Download Carepatron's comprehensive Healthcare Marketing Plan PDF, which helps create a successful strategy that drives patient engagement, trust, and growth for your organization.
Hearing Aid Evaluation
Learn how to conduct a thorough hearing aid evaluation with our free PDF download. This comprehensive guide includes examples and tips for success.
OCD Treatment Guidelines
Navigate through the complexities of OCD with our comprehensive treatment guidelines. Discover evidence-based strategies for effective management.
Behavioral Health Treatment Plan
Explore effective mental health treatment plans with our free PDF template, which is ideal for mental health professionals seeking structured recovery paths.
Speech Sound Development Chart
Explore the stages of speech sound development in children, from early vocalizations to complex language use, and how it influences communication and literacy.
Classical Conditioning Worksheet
Explore classical conditioning with our worksheet, perfect for students, therapists, and self-learners to deepen their understanding of behavior theories.
Action Planning Worksheet
Maximize project success with our Action Planning Worksheet. Track and measure progress effectively. Download free templates for complete project management.
Pharmacy Technician Worksheets
Unlock pharmacy tech skills with our free worksheets for exam prep, skill refreshment, and practical knowledge. Download now.
Cross Addiction Worksheet
Carepatron offers integrated software for therapy practice management, streamlining scheduling, billing, and clinical documentation for healthcare providers.
IADLS Assessment
Download our free IADLS Assessment template to evaluate daily living skills for better care and independence planning. Ideal for professionals and families.
Type 2 Diabetes Treatment Guidelines
Get comprehensive guidelines and examples for treating Type 2 Diabetes in Carepatron's free PDF download.
Pain Management Treatment
Discover effective pain management treatments and examples through Carepatron's free PDF download. Learn about various strategies to alleviate pain and improve your quality of life.
Facts vs Feelings Worksheet
Differentiate between facts and feelings with our Facts vs Feelings Worksheet. Ideal for therapy sessions, promoting emotional regulation and logical thinking.
Gaslighting Worksheet
Use our Gaslighting Worksheet to empower your clients. Help patients recognize and overcome gaslighting, facilitate healing, and improve mental wellness.
Gratitude Jar Worksheet
Enhance well-being in your practice with our Gratitude Jar Worksheet. Empower your clients to cultivate positivity and gratitude in their lives.
Inner Child Healing Exercises
Unlock your healing journey with Inner Child Healing Exercises. Reconnect with your inner child, heal childhood trauma, and find emotional resilience.
Intention Setting Worksheet
Clarify your goals and create meaningful steps forward with our Intention Setting Worksheet. Reflect, set intentions, and achieve your aspirations.
Goodbye Letter to Addiction
Overcome addiction with our Goodbye Letter to Addiction template. Reclaim your personal and professional life for long-term recovery. Download now!
Burnout Recovery Plan
Get your free PDF of a burnout recovery plan from Carepatron to help you overcome burnout and regain work-life balance. Explore practical recovery strategies.
Therapy Invoice Template
Our Therapy Invoice Template streamlines billing processes, enhances professionalism, and effortlessly keeps you organized. Download now!
Speech Therapy Invoice Template
Streamline your speech therapy practice with Carepatron's downloadable invoice template and billing software! Save time, ensure accurate billing, and impress clients.
Muscle Test
Discover everything you need to know about muscle testing, examples, and Carepatron's free PDF download to help you better understand this technique.
Pisiform Fracture Test
Learn how to conduct the Pisiform Fracture Test. Get a free PDF template to record results and streamline your documentation.
90-90 Hamstring Test
Learn how to perform the 90-90 Hamstring Test. Access a free PDF template and example here.
Overhead Squat Assessment
Get access to a free Overhead Squat Assessment template. Learn how to perform this test and interpret the results.
Severity Measure for Social Anxiety Disorder
Explore the Severity Measure for Social Anxiety Disorder to assess the intensity of social anxiety symptoms. Download our template for precise evaluation and treatment planning.
Speech Intelligibility Rating Scale
Download our Speech Intelligibility Rating Scale to assess and improve clarity in speech. Perfect for therapists and educators. Enhance communication now.
Stages of Relapse Worksheet
Download our free Stages of Relapse Worksheet to effectively track and manage signs of emotional, mental, and physical relapse.
Cervical Flexion Rotation Test
Discover the Cervical Flexion Rotation Test for assessing upper cervical spine dysfunction, ideal for diagnosing cervicogenic headaches and neck issues.
Bipolar Treatment Guidelines
Explore expert Bipolar Treatment Guidelines, including diagnosis, symptom management, and personalized care strategies for improved health.
Levels of Hoarding Test
Access a resource that will aid you in evaluating a patient's hoarding disorder. Download our Levels of Hoarding Test today!
Inner Child Worksheets PDF
Try the transformative power of Inner Child Worksheets PDF. Heal past wounds, foster self-discovery, and embrace authenticity with our guide and template.
Mental Health Diagnosis Cheat Sheet
Discover our Mental Health Diagnosis Cheat Sheet for accurate ICD-10 coding, enhancing care and billing in mental health practices.
Antisocial Personality Disorder Treatment Plan
Discover an effective treatment plan for Antisocial Personality Disorder to help individuals manage symptoms and improve quality of life.
Vineland Adaptive Behavior Scale
Learn more about the comprehensive Vineland Adaptive Behavior Scale, which assesses adaptive behaviors in individuals and provides targeted support.
Norton Scale
Learn about the Norton Scale, a tool used in healthcare to assess the risk of pressure ulcers. Understand its significance and application.
Adjustment Disorder PDF
Navigate the complexities of adjustment disorder with our comprehensive PDF guide. Explore symptoms, diagnosis criteria, and treatment options here.
Medical Diagnosis Form
This form helps healthcare professionals gather patient information for accurate diagnosis. Download a free medical diagnosis form template.
Authenticity Test
Discover how authentic you are with our Authenticity Test. Uncover your true self, live more authentically, and improve your life satisfaction. Try it now!
IFS Treatment Plan
Download Carepatron's free PDF example of an Internal Family Systems (IFS) treatment plan. Learn how to create a comprehensive treatment plan using IFS therapy techniques.
Beers Criteria Template
Explore the Beers Criteria Template, guiding principles for safer medication use in older adults—essential knowledge for healthcare professionals.
Psychotic Disorders List
Download our free Psychotic Disorders List as a helpful reference tool based on the diagnostic criteria outlined in the DSM-5.
Join 10,000+ teams using Carepatron to be more productive
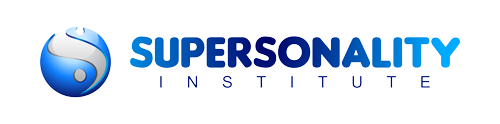
Miniclass online
Problem solving dengan root cause analysis (rca), "menemukan solusi permanen dan mencegah masalah terulang kembali", selasa, 30 april 2024 pkl. 20.00 wib live zoom, menemukan solusi permanen : pentingnya pemecahan masalah dengan metode root cause analysis.
Di era yang serba cepat dan penuh dengan perubahan ini, kemampuan memecahkan masalah menjadi keahlian yang krusial bagi individu maupun organisasi. Namun, seringkali, solusi yang diaplikasikan hanya bersifat tambal sulam, sehingga masalah yang sama terus berulang. Di sinilah letak pentingnya metode Root Cause Analysis (RCA) dalam proses pemecahan masalah.
Memahami Akar Permasalahan
Berbeda dengan metode konvensional yang hanya fokus pada gejala, RCA menyelami lebih dalam untuk menemukan akar permasalahan. Analogikan dengan penyakit: jika hanya mengobati gejalanya (misalnya, sakit kepala), penyakit tersebut dapat kambuh kapan saja. Namun, dengan mengidentifikasi dan mengatasi penyebabnya (misalnya, infeksi), penyakit dapat disembuhkan secara permanen.
Manfaat RCA dalam Pemecahan Masalah:
- Meningkatkan Efektivitas Solusi: RCA membantu menemukan solusi yang tepat sasaran, sehingga masalah teratasi secara permanen dan tidak terulang kembali.
- Menghemat Biaya dan Waktu: Dengan mencegah masalah terulang, RCA dapat menghemat biaya dan waktu yang terbuang untuk menyelesaikan masalah yang sama berulang kali.
- Meningkatkan Kualitas: RCA membantu mengidentifikasi dan menghilangkan sumber inefisiensi dan kesalahan, sehingga meningkatkan kualitas produk, layanan, dan proses.
- Meningkatkan Keselamatan: RCA dapat membantu mengidentifikasi dan mengatasi potensi bahaya, sehingga meningkatkan keselamatan di tempat kerja dan lingkungan sekitar.
- Meningkatkan Budaya Belajar: RCA mendorong budaya belajar dan perbaikan berkelanjutan dengan menganalisis kegagalan dan mencari cara untuk memperbaikinya.
RCA dapat diterapkan di berbagai bidang, seperti:
- Bisnis: Meningkatkan kualitas produk dan layanan, mengurangi biaya, meningkatkan efisiensi, dan meningkatkan kepuasan pelanggan.
- Manufaktur: Mengurangi cacat produk, meningkatkan waktu henti mesin, dan meningkatkan keselamatan kerja.
- Teknologi Informasi: Mengidentifikasi dan mengatasi masalah sistem, meningkatkan uptime, dan meningkatkan keamanan data.
- Kesehatan: Meningkatkan diagnosis dan pengobatan penyakit, meningkatkan kualitas perawatan pasien, dan mengurangi risiko infeksi.
- Pemerintahan: Meningkatkan pelayanan publik, meningkatkan efisiensi birokrasi, dan meningkatkan akuntabilitas.
- JIKA ANDA MENGALAMI BEBERAPA MASALAH INI
- Timbul masalah yang terjadi berulang, meskipun sudah dicoba berbagai solusi
- Mengalami kerugian finansial, waktu, dan sumber daya akibat masalah yang berulang.
- Mendapat keluhan dari pelanggan atau pengguna atas produk atau layanan yang berkualitas rendah.
- Terjadi peningkatan cacat produk atau kesalahan dalam proses kerja.
- Inefisiensi dalam proses kerja yang mengakibatkan pemborosan waktu dan sumber daya
- Adanya peningkatan potensi bahaya dan kecelakaan di tempat kerja
- Mengalami stagnasi dalam pengembangan dan inovasi.
- Mengalami konflik dan ketidaksepakatan antar individu atau tim dalam organisasi.
KAMI HADIRKAN UNTUK ANDA
Miniclass online.
Kelas ini dirancang untuk memperkenalkan Anda pada konsep dan prinsip Root Cause Analysis (RCA), teknik problem solving yang ampuh untuk menemukan akar permasalahan dan mengatasinya secara permanen.
- SIAPA YANG HARUS IKUT KELAS INI
- Pemimpin tim yang ingin meningkatkan kinerja tim mereka.
- Pengusaha yang ingin meningkatkan profitabilitas dan keberhasilan bisnis mereka.
- Profesional / Staf di bidang Teknik, Medis, Pendidikan, dll
- Siapapun yang ingin meningkatkan kemampuan mereka dalam problem solving
- APA YANG DIPELAJARI DI KELAS INI
- Pengenalan Root Cause Analysis
- Langkah-langkah Melakukan RCA
- Teknik-teknik RCA
- Studi Kasus Problem Solving dengan RCA
- TUJUAN PEMBELAJARAN
- Memahami konsep dan prinsip Root Cause Analysis (RCA).
- Mampu mengidentifikasi akar permasalahan dengan berbagai teknik.
- Mampu mengembangkan solusi yang efektif dan permanen.
- Mampu mempraktikkan RCA dalam berbagai studi kasus.
- MEET THE TRAINER
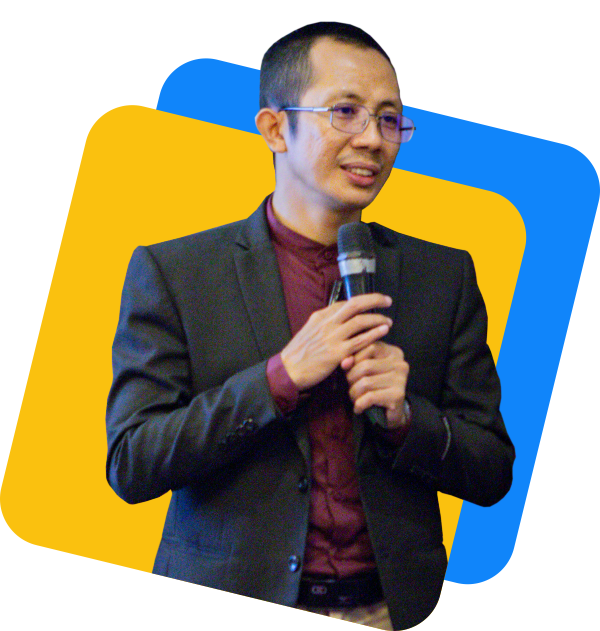
Ryan Martian, CPHRM
Trainer & master hr coach leadership trainer business consultant, praktisi bisnis, konsultan dan praktisi manajemen sdm, sejak 2008 bersama tim supersonality institute telah menjadi konsultan sdm di puluhan perusahaan, membantu ratusan umkm, baik dalam program pendampingan maupun pelatihan, telah melatih ribuan orang mengembangkan bisnis mereka melalui pelatihan dan workshop di berbagai kota dan perusahaan..
More than 15 Years Experience in Human Resources Development (2007 – Now) . Magister Management Graduate Major Study Human Resources Management (2016) . Certified Professional Human Resourcess Management (CPHRM) from Society of Human Resources Management (SHRM). Certified Human Resources with Neuro Linguistic Programming (CHRNLP) . IBH Certified Instructor (IBH CI) , Jakarta, Indonesia. Certified NLP Practitioner (CNLP) , NFNLP Florida USA. Certified Trainer Badan Nasional Sertifikasi Profesi (BNSP) .
- TESTIMONI PESERTA WORKSHOP HRM 4.0 BERSAMA RYAN MARTIAN
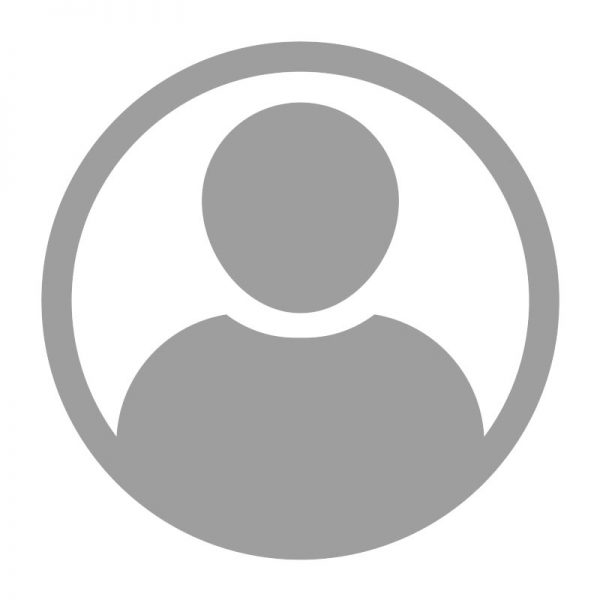
PELAKSANAAN
1 sesi miniclass, 1 sesi live zoom, materi dan rekaman bisa diakses di member area..
- Selasa 30 April 2024
- Pkl. 20.00 WIB
- LIVE via ZOOM
Daftar sekarang !!!
Manfaatkan HARGA SPESIAL EARLY BIRD
miniclass online Problem Solving Dengan Root Cause Analysis (RCA)
30 april 2024 pkl. 20.00 wib - live via zoom.
Rp. 349.000 (Harga Normal)
Rp. 179.000 (Harga Promo)
Rp. 119.000 (Early Bird)*
*Berlaku s/d 26 April 2024
- Kelas ZOOM 1 kali
- Rekaman Kelas
- Modul Soft file
- E-Sertifikat
Daftar via Form
Silahkan isi Form dibawah, dan nanti CS kami akan menghubungi Anda via whatsapp.
Troubleshoot SQL Server Always On Availability Groups with SQL LogScout
By: Edwin Sarmiento | Updated: 2024-04-25 | Comments | Related: > Availability Groups
We experienced several unplanned outages and failovers on our SQL Server Always On Availability Groups. We want to know the root cause to prevent them from happening in the future. How do we identify the root causes of unplanned Availability Group outages and failovers?
The goal of deploying an Always On Availability Group is to provide high availability to SQL Server databases. So, it becomes problematic when an unplanned outage or unexpected failover happens more often than necessary. You need to troubleshoot the issue and find the root cause to prevent it from happening again. The first step in troubleshooting an issue is to collect as many logs as possible for analysis.
The challenge with a complex architecture like Always On Availability Groups is that there are so many moving parts with different components that can each contribute to the issue. Part of that challenge is collecting logs from various sources like SQL Server error logs, AlwaysOn_health Extended Events sessions, Windows Event Logs, and Windows Server failover Cluster logs. On top of that, you need to make sure that you've collected enough logs from each of those sources at the same time within the same time frame for proper analysis.
Fortunately, Microsoft technical support engineers developed a tool for this purpose - SQL LogScout. SQL LogScout is mentioned in this Microsoft documentation as one of the tools for troubleshooting SQL Server on-premises and hybrid scenarios. It is a light, script-based, open-source tool that allows you to collect diagnostic logs from your SQL Server system to help troubleshoot problematic issues faster. It makes the log collection process across many different components a lot easier. While you can use it to analyze logs for a variety of SQL Server issues, this tip will focus on using SQL LogScout to identify the root causes of unplanned Availability Group outages and failovers.
Download and Install SQL LogScout
To get started, download SQL LogScout from its GitHub repository . SQL LogScout is a compilation of PowerShell scripts, T-SQL scripts, and batch files. That being said, you need PowerShell version 4.0 or higher. You also need to configure the script execution policy to RemoteSigned using the Set-ExecutionPolicy cmdlet to run PowerShell scripts as described in this tip . Since it will collect logs from Windows Server Failover Cluster, Windows Event Log, system information, etc., you need local Administrator privileges on the server running the Availability Group primary replica in addition to your existing sysadmin privileges on the SQL Server instance ( VIEW SERVER STATE and ALTER ANY EVENT SESSION are the minimum permissions needed for the data collection on the SQL Server side).
Extract the compressed file to any location on the primary replica of your Availability Group. We will be using C:\SQLLogScout for this tip. Open an Administrative command prompt and navigate to this folder. Note that the account I'm using has local Administrator privileges on the server and sysadmin privileges on the SQL Server instance running the Availability Group primary replica.
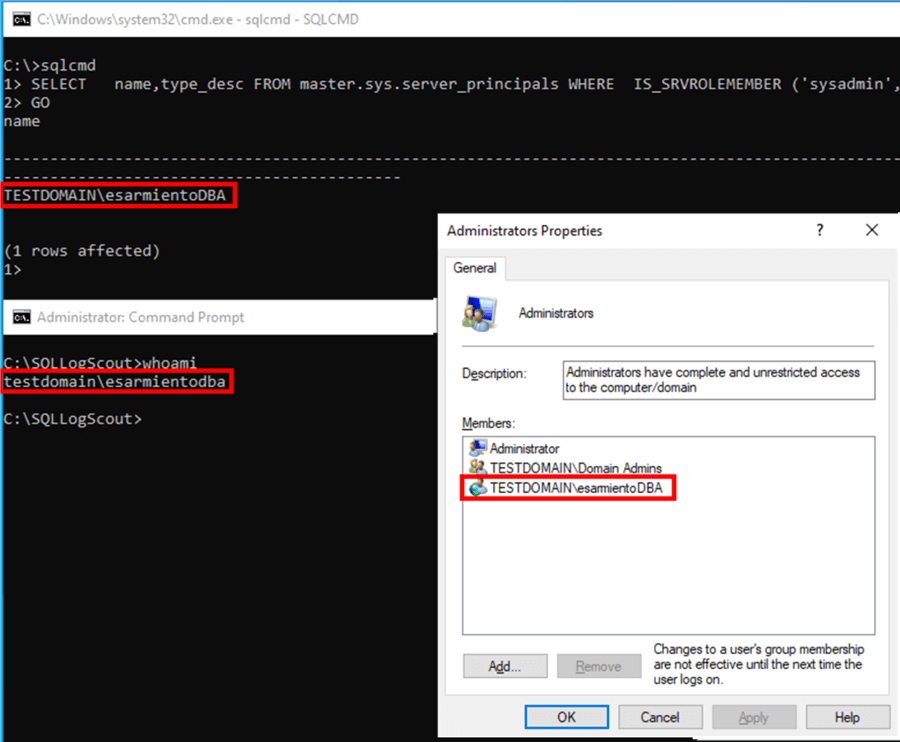
SQL LogScout to Collect Logs for Analyzing Unplanned Availability Group Outages and Failovers
SQL LogScout can be used to collect logs for a variety of SQL Server issues. This tip will only focus on Availability Group outages and failovers. The good thing about using SQL LogScout to analyze and identify root causes of unplanned Availability Group outages and failovers is that you can do this even after the issue has occurred and has been resolved. Just make sure you keep enough logs – SQL Server error logs, AlwaysOn_health Extended Events sessions, Windows Server Failover Clustering logs, Windows Event Logs, etc. - so you have something to work on.
NOTE: In most cases, the focus of all activities during an outage is to bring the databases, Availability Groups, and/or the Windows Server Failover Cluster online as quickly as possible. Root cause analysis becomes less of a priority when everything returns to normal. If you have a very busy system or have not properly configured to keep the logs long enough to analyze, such as recycling the SQL Server error log daily, you may not have any logs to work with. I've worked on dozens of cases where I couldn't do a root cause analysis because we no longer have the logs when the issue happened - either they've already been recycled or overwritten. Sometimes, it's been weeks after the issue occurred before the customer decided to do a root cause analysis. Make it a part of your incident management process to do a root cause analysis as soon as everything is back to regular business operation.
Assuming that an unplanned Availability Group outage or failover has already occurred, run the batch file, SQL_LogScout.cmd, on the primary replica (or the original primary replica if an automatic failover occurred) of the Availability Group.
- When prompted to allow execution of the PowerShell scripts, type A and press Enter . This will run all the PowerShell scripts without additional prompts.
- When prompted to use GUI mode, type N and press Enter . This will keep SQL LogScout running in command-prompt mode.
- When prompted to use a non-default drive and directory, type N and press Enter . This will save all the collected logs inside the C:\SQLLogScout\output directory.
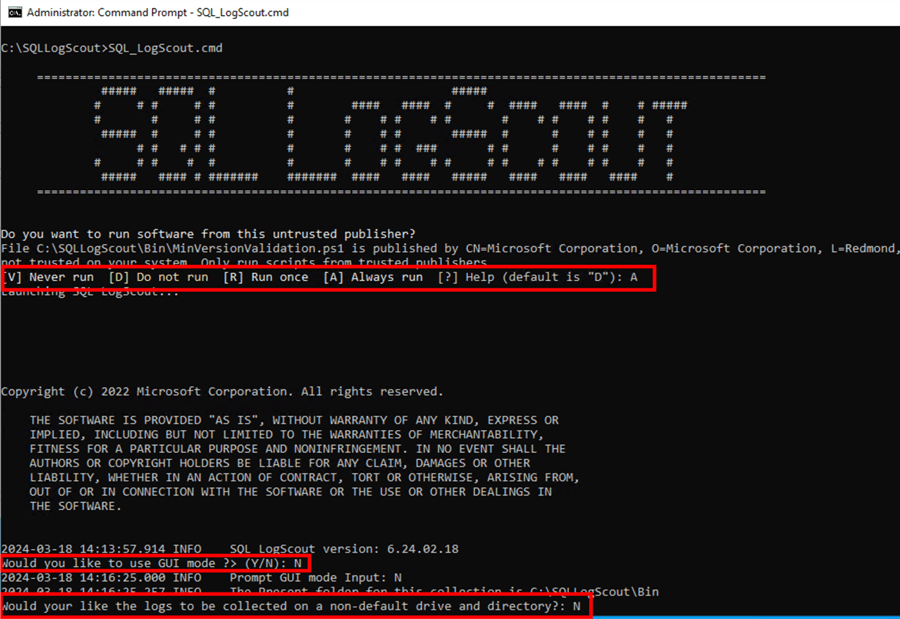
This is where you start to see the power of SQL LogScout. It will collect logs based on different scenarios you provide, which are provided on the SQL LogScout GitHub page . Since this tip aims to collect logs to analyze unplanned Availability Group outages and failovers, limit it to that scenario.
- When prompted for the scenario, type 4+12 and press Enter . The value 4 is for the AlwaysOn scenario. It will collect Availability Group-related logs from SQL Server error logs, AlwaysOn_health Extended Events session, Availability Group diagnostic information from DMVs, Windows Server Failover Cluster logs, etc. The value 12 is for the LightPerf scenario and will collect light performance data for an overall system performance view. This does not include detailed information such as query execution plans and the like. By default, it will also run the Basic scenario (the value 0) to collect static logs.
- When prompted for the ID of the SQL Server instance, type the corresponding number and press Enter . You may have multiple SQL Server instances running on this server. Be sure to provide the ID of the SQL Server instance running the Availability Group you want to analyze. In this example, I'm using ID 0 for the instance TDPRD021 .
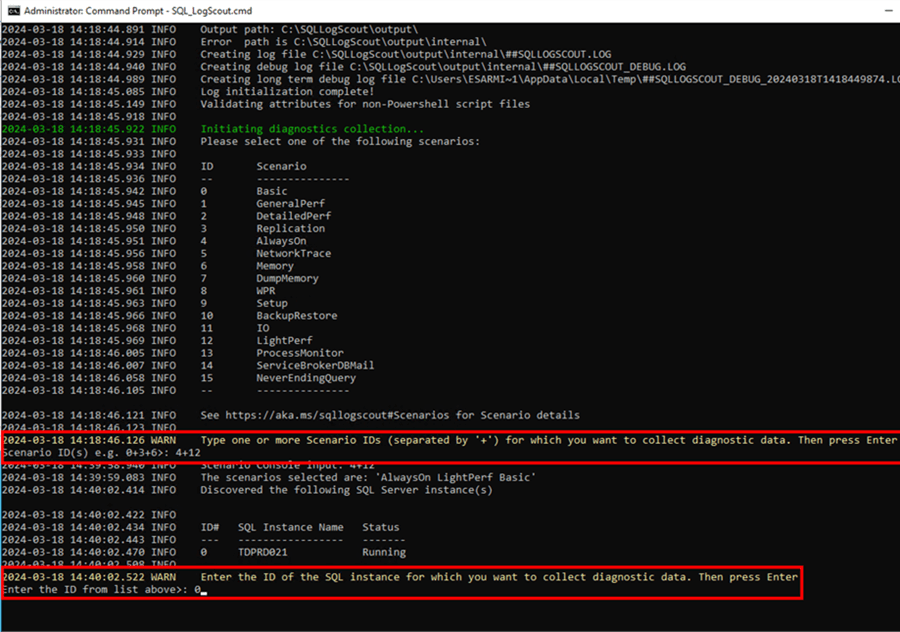
Since the issue has already occurred, you're collecting the logs containing the events for analysis. Type STOP and press Enter when you see the prompt to terminate the diagnostics collection. This stops the log collection and terminates the execution of SQL LogScout.
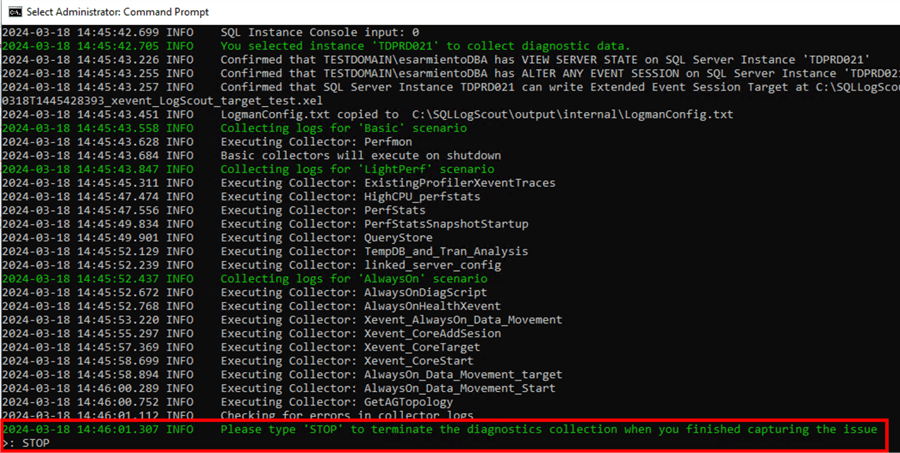
If you want to automate the process of running SQL LogScout or simply want a consistent, standardized command, run the command below containing the parameters you provided.
- AlwaysOn+LightPerf : The AlwaysOn and LightPerf scenarios. Names are used instead of the equivalent numerical values.
- TDPRD021 : The SQL Server instance name; used instead of the equivalent numerical value.
- UsePresentDir : Use the current directory. This is equivalent to responding N to using the non-default drive and directory.
- DeleteDefaultFolder : Used to delete the default \output folder, if present.
- "01-01-2024" : Used to set the start time in the past to ensure the data collection starts without delay.
- "03-18-2024 15:20" : Used to set the stop time in the future with enough time for the data collection to run properly.
- Quiet : Used to accept all the prompts automatically and not require user input.
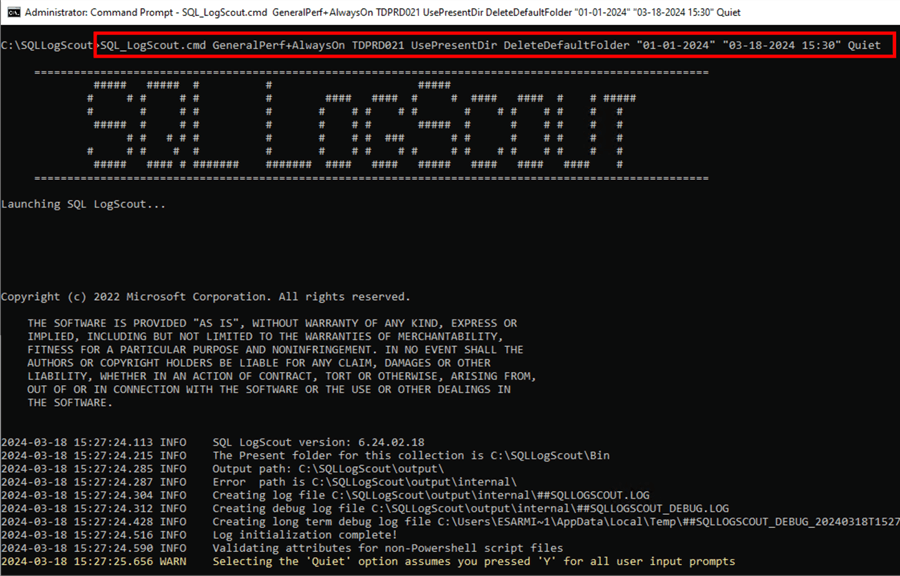
Reviewing Collected Logs
Navigate to the C:\SQLLogScout\output directory to view the collected logs. Notice the logs collected: AlwaysOn_health Extended Events session, system_health Extended Events session, Windows Server Failover Cluster logs, SQL Server error logs, SQLDIAG Extended Events session, Perfmon log, Windows Event Logs, etc.
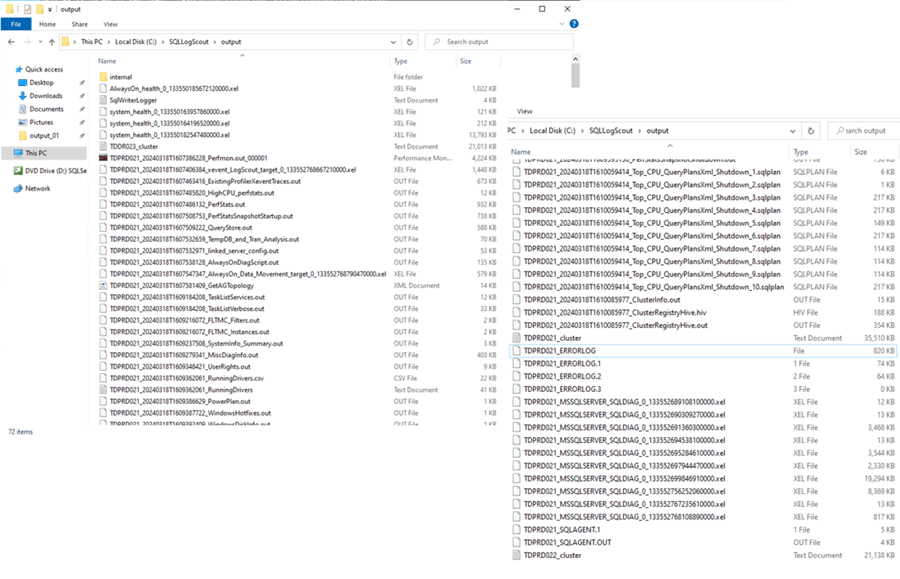
SQL LogScout makes it easier to collect all the logs from different sources and consolidates them in a single repository for easier analysis. You can use these collected logs to analyze the root cause of unplanned Availability Group outages and failovers. Although it can be tedious to go through each log manually, decipher error messages, and investigate potential root causes of the issues, there is not an easier way to do so.
The next tip will cover how to process these logs using another open-source tool from Microsoft, which makes analyzing unplanned Availability Group outages and failovers much easier.
- Read more about SQL LogScout from the GitHub repository .
- Download and install SQL LogScout .
- Start collecting logs using SQL LogScout to identify the root causes of unplanned Availability Groups outages and failovers.
- Read this Microsoft documentation on Troubleshooting and diagnostic tools for SQL Server on-premises and hybrid scenarios .

About the author

Comments For This Article

Related Content
How To Fix SQL Server Always On Availability Group Database Not Synchronized
Fix SQL Server AlwaysOn Error: 35250 Failed to Join the Availability Group
Recover WSFC using Forced Quorum for SQL Server AlwaysOn Availability Group
Fix SQL Server AlwaysOn Availability Group Error: 1408 Joining database on secondary replica resulted in an error
SSISDB and SQL Server 2016 Availability Group Issue with Automatic Seeding
SQL Server Availability Group Error 35246 missing sqlconf.dll
What is SQL Server AlwaysOn?
Related Categories
Availability Groups
Database Mirroring
Disaster Recovery
High Availability
Log Shipping
Replication
Development
Date Functions
System Functions
JOIN Tables
SQL Server Management Studio
Database Administration
Performance
Performance Tuning
Locking and Blocking
Data Analytics \ ETL
Microsoft Fabric
Azure Data Factory
Integration Services
Popular Articles
SQL Date Format Options with SQL CONVERT Function
SQL Date Format examples using SQL FORMAT Function
SQL Server CROSS APPLY and OUTER APPLY
DROP TABLE IF EXISTS Examples for SQL Server
SQL Server Cursor Example
SQL CASE Statement in Where Clause to Filter Based on a Condition or Expression
Rolling up multiple rows into a single row and column for SQL Server data
SQL Convert Date to YYYYMMDD
SQL NOT IN Operator
Resolving could not open a connection to SQL Server errors
Format numbers in SQL Server
SQL Server PIVOT and UNPIVOT Examples
Script to retrieve SQL Server database backup history and no backups
How to install SQL Server 2022 step by step
An Introduction to SQL Triggers
Using MERGE in SQL Server to insert, update and delete at the same time
List SQL Server Login and User Permissions with fn_my_permissions
SQL Server Loop through Table Rows without Cursor
How to monitor backup and restore progress in SQL Server
SQL Server Database Stuck in Restoring State
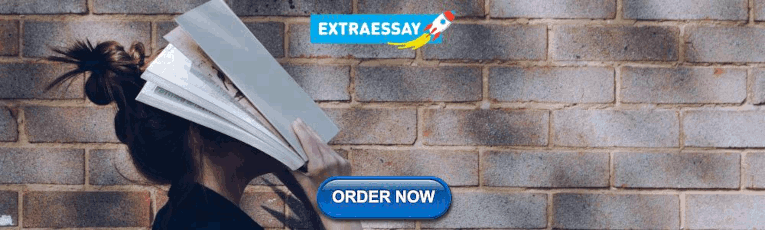
COMMENTS
The problems that affect a company's success don't always result from not understanding how to solve them. In many cases, their root causes aren't easily identified. That's why root cause analysis is vital to organizational leadership.. According to research described in the Harvard Business Review, 85 percent of executives believe their organizations are bad at diagnosing problems ...
The process to conduct a root cause analysis can be broken down into a few easy steps: Define the problem. Identify and map the problem causes. Identify the evidence that supports your causes. Create a root cause analysis report and set up your action plan. 1. Define the problem.
The first goal of root cause analysis is to discover the root cause of a problem or event. The second goal is to fully understand how to fix, compensate, or learn from any underlying issues within the root cause. The third goal is to apply what we learn from this analysis to systematically prevent future issues or to repeat successes.
Let's dive into seven widely utilized RCA techniques and explore how they can empower your team's problem-solving efforts. 1. The Ishikawa Fishbone Diagram (IFD) Named after Japanese quality control statistician Kaoru Ishikawa, the Fishbone Diagram is a visual tool designed for group discussions.
Root cause analysis is a problem-solving approach that uses the analogy of roots and blooms to model cause-and-effect relationships. Rather than focusing on what's above the surface, root cause analysis troubleshoots solutions to problems by analyzing what is causing them. Note. Similarly to exploratory research, it's important to remember ...
Root cause analysis (RCA) is the quality management process by which an organization searches for the root of a problem, issue or incident after it occurs. Issues and mishaps are inevitable in any organization, even in the best of circumstances. While it could be tempting to simply address symptoms of the problem as they materialize, addressing ...
Guide. Guide: Root Cause Analysis. Root Cause Analysis (RCA) is a key tool in continuous improvement, acting as a systematic approach to identify and tackle the underlying issues behind problems. RCA aims not only to provide a temporary fix but to offer long-lasting solutions by addressing the root causes. RCA, such as the Fishbone Diagram, the ...
Definition. Root Cause Analysis (RCA) is a systematic approach to identify the underlying cause of a problem. By focusing on the root cause, you can effectively address the issue and prevent recurrence. Generally, RCA is used to investigate incidents, eliminate defects, and enhance systems or processes.
Fishbone Diagram (Click on the template to edit it online) . Here's how to use the cause and effect analysis to solve business problems.You can also refer to our guide on fishbone diagrams to learn how to use the tool in more detail.. Pareto Chart . Pareto chart is a combination of a bar chart and a line graph. While the length of the bars represent the frequency or cost of faults, they are ...
Root Cause Analysis (RCA) is not just a structured method of problem-solving; it's a vital component of organisational leadership. The goal of RCA is to fully understand what caused an issue, allowing for effective corrective actions. One of the first steps in a successful RCA is identifying performance or opportunity gaps within an organisation.
The 5 Whys Technique is a versatile problem-solving approach that can be applied in various scenarios to uncover root causes and drive continuous improvement. Here are two key situations where the 5 Whys Analysis can be particularly beneficial: Recurring Issues. The 5 Whys Technique is especially useful when dealing with recurring issues.
Root Cause Analysis (RCA) is defined as a systematic process for identifying the underlying causes or factors that contribute to a problem, incident, or undesirable outcome. Learn more about root cause analysis types, examples, and methods. ... Root Cause Analysis helps organizations improve problem-solving capabilities, reduce risks, and drive ...
1.Fishbone Diagrams. The Fishbone Diagram is a popular Root Cause Analysis Tool - and yes, it looks like a fish! Phrase the problem as a "why" question and place it at the head of the diagram. Now track possible causes using the Fishbone Diagram categories most relevant to your industry type.
Root Cause Analysis is a useful process for understanding and solving a problem. Figure out what negative events are occurring. Then, look at the complex systems around those problems, and identify key points of failure. Finally, determine solutions to address those key points, or root causes.
Root cause analysis (RCA) is defined as a collective term that describes a wide range of approaches, tools, and techniques used to uncover causes of problems. Some RCA approaches are geared more toward identifying true root causes than others, some are more general problem-solving techniques, and others simply offer support for the core ...
A root cause analysis (RCA) determines why a problem arises in the first place. Instead of just treating the symptoms of a problem, RCA involves looking into and trying to fix its root causes. It is important to use the tools and methods that are best for your situation when doing a root cause analysis (RCA).
It's called root cause analysis. Root cause analysis is a problem-solving method that aims to identify the fundamental cause of a problem so that you can create a solution that fixes it for good. In this article, we'll give you an in-depth understanding of root cause analysis, including what it is, its benefits, and its common methodologies.
Root Cause Analysis is a popular process for finding the underlying cause of a problem. This technique is useful because, when you deal with the root cause, you also fix many other issues associated with it. There are five steps in Root Cause Analysis. You first need to define the problem. What is happening and what are the symptoms of it?
Root cause analysis. In science and engineering, root cause analysis ( RCA) is a method of problem solving used for identifying the root causes of faults or problems. [1] It is widely used in IT operations, manufacturing, telecommunications, industrial process control, accident analysis (e.g., in aviation, [2] rail transport, or nuclear plants ...
Teams and managers use root cause analysis tools to identify the underlying causes of a problem or issue. There are many different ones that can be used for this purpose, including 5 Whys, Fishbone Diagrams, Fault Tree Analysis, and FMEA. The 5 Whys framework involves asking "why" questions repeatedly to drill down into the root cause of a problem.
Root-cause problem solving in the Ops 4.0 era. Root-cause problem solving remains a crucial part of the continuous-improvement process. Today's technologies make it even easier—and more powerful. Passionate about the "human factor": helping people develop broad skills and deep functional expertise. Experienced operations practitioner ...
The 5 Whys exercise is vastly improved when applied by a team and there are five basic steps to conducting it: Write down the specific problem. Writing the issue helps you formalize the problem and describe it completely. It also helps a team focus on the same problem. Ask "Why" the problem happens and write the answer down below the problem.
The first step to solving a problem is to define the problem precisely. It is the heart of problem-solving. Root cause analysis is the second important element of problem-solving in quality management. The reason is if you don't know what the problem is, you can never solve the exact problem that is hurting the quality.
The 5 Whys strategy is a simple, effective tool for uncovering the root of a problem. You can use it in troubleshooting, problem-solving, and quality-improvement initiatives. Start with a problem and ask why it is occurring. Make sure that your answer is grounded in fact, and then ask the question again.
By regularly using Cause and Effect Diagrams as part of problem-solving and root cause analysis initiatives, organizations can drive ongoing improvements in quality, efficiency, and effectiveness. ... Cause and Effect Diagrams serve as valuable tools for problem-solving, analysis, and decision-making processes within organizations, helping ...
Use the template for a brainstorming session and list all possible causes of the problem, placing them under the appropriate categories. Encourage team members to contribute their insights and perspectives to ensure a comprehensive analysis. This collective approach enhances the depth and breadth of the root cause analysis.
Problem Solving Dengan Root Cause Analysis (RCA) Kelas ini dirancang untuk memperkenalkan Anda pada konsep dan prinsip Root Cause Analysis (RCA), teknik problem solving yang ampuh untuk menemukan akar permasalahan dan mengatasinya secara permanen.
Problem. We experienced several unplanned outages and failovers on our SQL Server Always On Availability Groups. We want to know the root cause to prevent them from happening in the future. ... Root cause analysis becomes less of a priority when everything returns to normal. If you have a very busy system or have not properly configured to keep ...