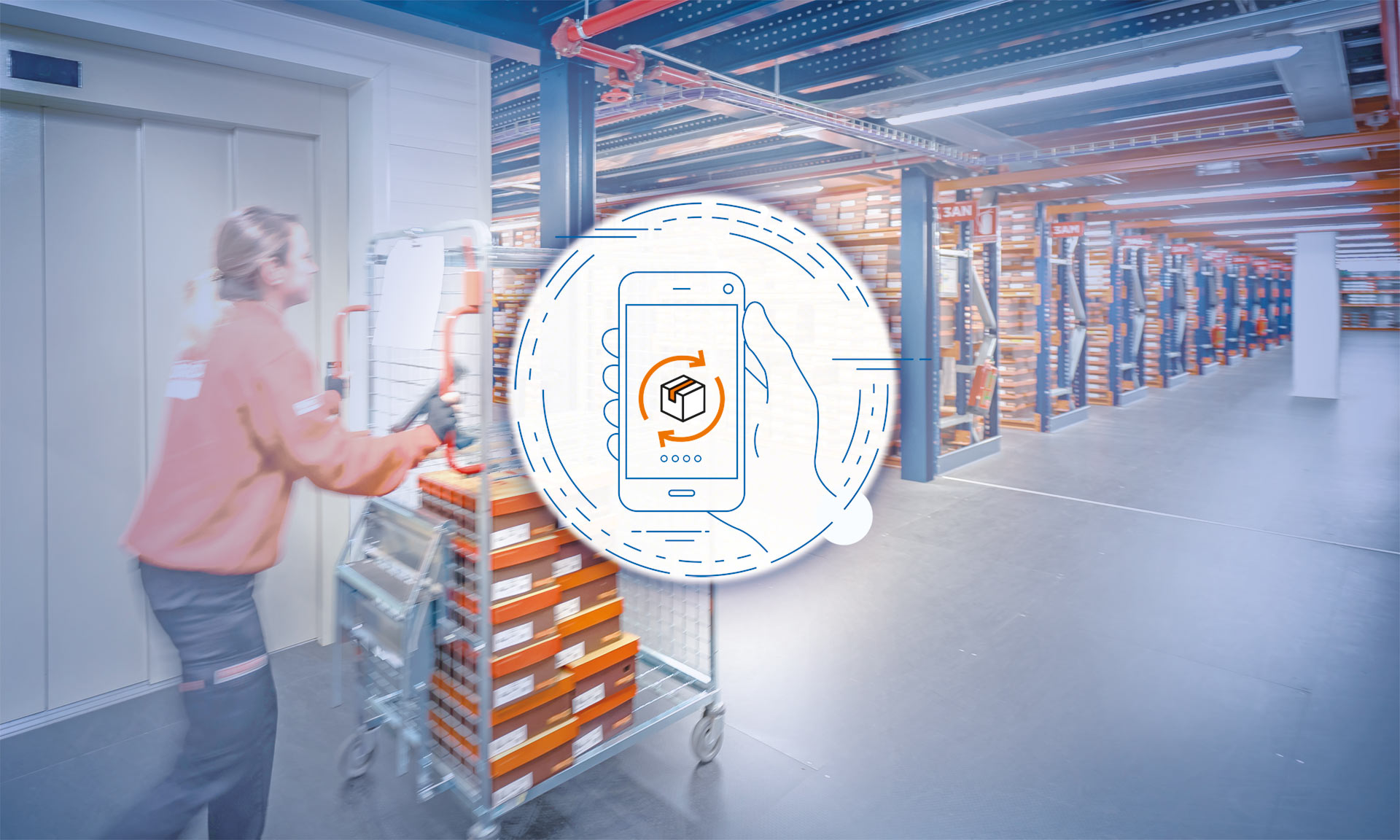
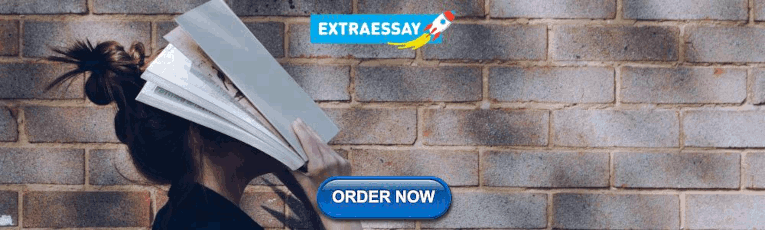
5 reverse logistics examples for successful returns management
In this post, we’ll take a look at some examples of reverse logistics in companies that have managed to turn returns management into a way to stand out from the competition and even into a business model of their own.
When a product rejected by a customer arrives at the warehouse, knowing how to repair or recondition it can prevent major losses in addition to reducing the business’s environmental footprint. At any rate, truly successful management lies in minimizing returns, and here, warehouses play a key role when it comes to adopting appropriate measures.
Reverse logistics strategies
Reverse logistics is the process involving the return of a product to the seller or manufacturer in order to recover its value or dispose of it properly. Reverse logistics is the antithesis of the standard supply chain; that is, processes are carried out in an order opposite to that of product marketing.
Businesses are receiving more and more returns these days. According to a study by consulting firm Deloitte , by 2022, retailers are expected to receive 13 billion returns worth $573 billion every year. That accounts for four times the total ecommerce sales in 2018). As a result, businesses with a high volume of returns usually adopt different strategies to minimize losses. For example, they recondition products to resell them, recycle certain materials, and reuse components, ( cannibalization ). And, when there is no alternative, they destroy or discard the product while minimizing the environmental impact.
In any case, the best reverse logistics is the absence of reverse logistics — when the customer is happy with a product and, thus, doesn’t return it. To this end, it’s vital to establish mechanisms in the warehouse to avoid errors and, thus, improve customer satisfaction .
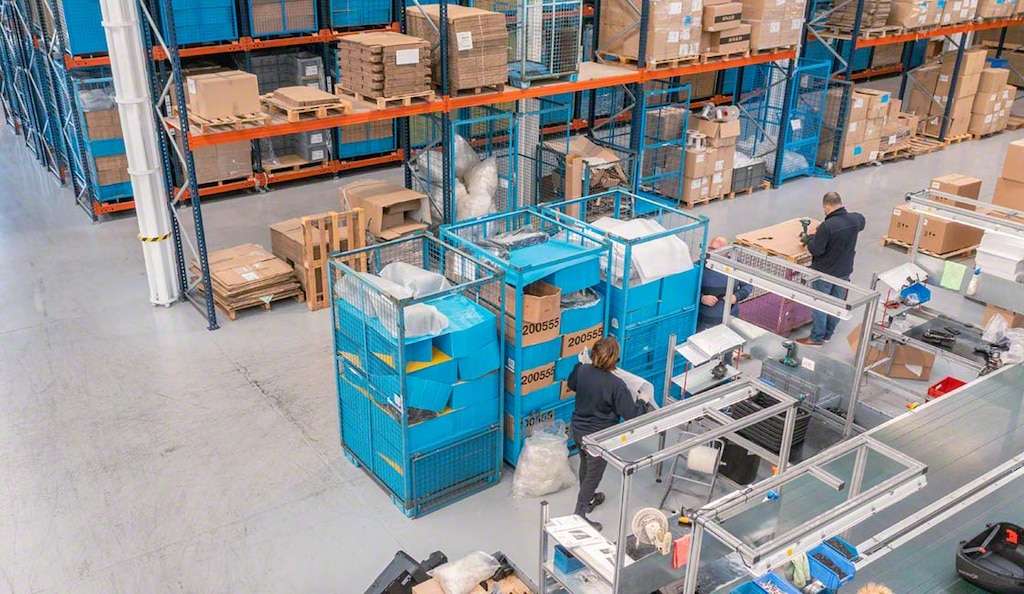
Reverse logistics examples from our customers
In the reverse logistics examples below, we’ll take a look at several strategies of businesses that have implemented solutions from the Mecalux Group to effectively manage returns.
1) Refurbishment (Rent the Runway)
Refurbishment consists of reselling a product that a customer has brought back . The merchandise must not have been significantly damaged by the previous customer and must undergo a reconditioning process.
Refurbishment is a common practice in the day-to-day of Rent the Runway , as it forms part of the business model of this New York-based fashion rental company that offers pieces from 550 designers on its website. At its warehouse in New Jersey, equipped with multi-tier shelving from Interlake Mecalux to store hanging garments, Rent the Runway houses over 65,000 dresses and 25,000 earrings, bracelets, and necklaces.
Warehouse operations comprise receiving the items returned by customers, cleaning them, and storing them until they are rented to another customer in the future. To manage these operations efficiently, the company’s facility needs to be optimally organized. When Rent the Runway receives the garments, it temporarily places them on racks to remove any potential stains, sterilize the jewelry, and sew torn clothing. The garments are ready to be reused, that is, to be rented again by other customers.
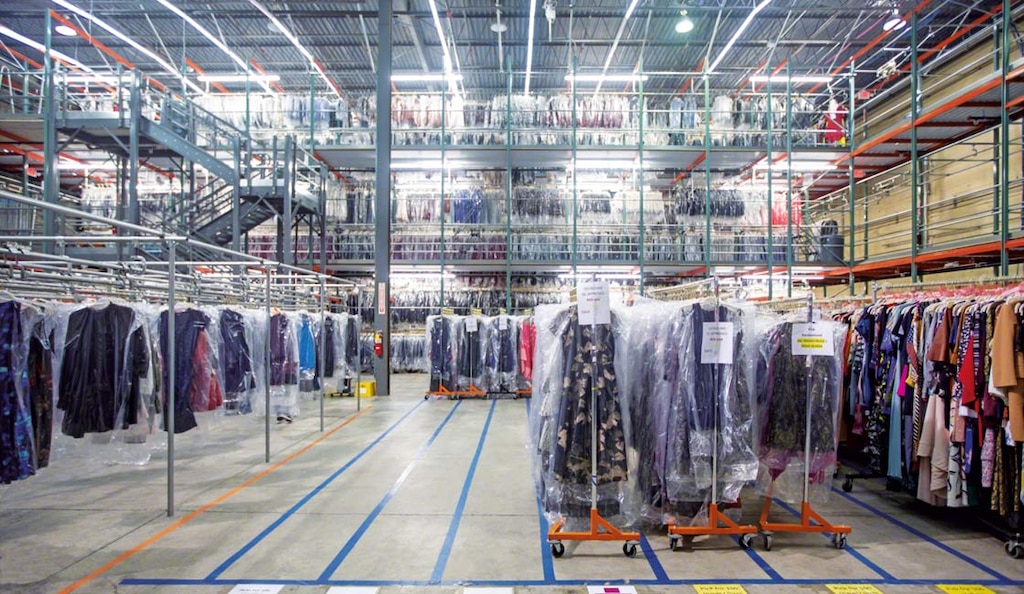
2) Outlet store (Motocard)
Outlet sales are another way to manage reverse logistics. The main aim of this type of retail is to obtain a financial return on products that can’t be sold via the usual sales channels. It constitutes marketing, at a discounted price, items that have been sent back to the warehouse because they are out of season or have minor defects .
Outlets are a common option in fashion companies. An example of this is Motocard , a chain specializing in equipment and accessories for motorcyclists. The company offers its customers the option to purchase some of its refurbished items in its online outlet at a lower cost.
Its facility in Solsona, Spain, was equipped by the Mecalux Group with storage systems and the Easy WMS, the warehouse management system . The building has an area with picking shelves , where all returned products are stored temporarily. There, operators check the returns with the help of the WMS, which gives them detailed instructions on storing and reconditioning the products.
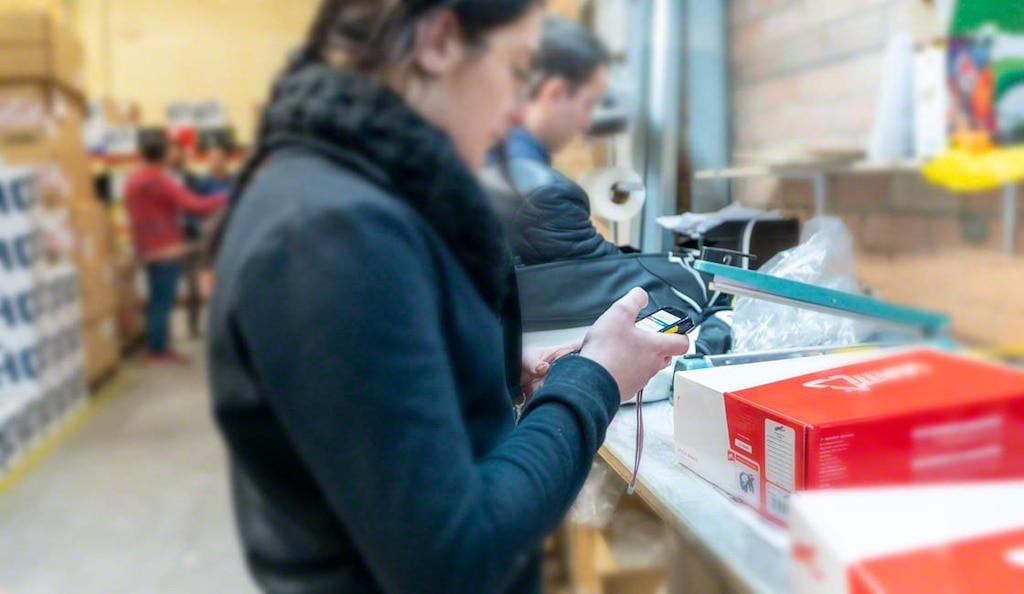
3) Product repair (Cosgra)
The repair of damaged products is an operation composed of taking an item that has stopped working or doesn’t work properly and putting it back into operation. Generally, the repair involves replacing a part or component that has reached the end of its useful life.
The warehouse of Cosgra , a parts distributor for automotive and electronics companies, houses products sold in over 20 countries in Europe, Africa, and Latin America. Additionally, it carried out repairs in a space set up for that purpose.
To organize returns and repairs, the company uses the WMS from the Mecalux Group, which sends instructions to operators on what to do at every turn. This can include storing the product on the pallet racks or repairing it to prolong its useful life.
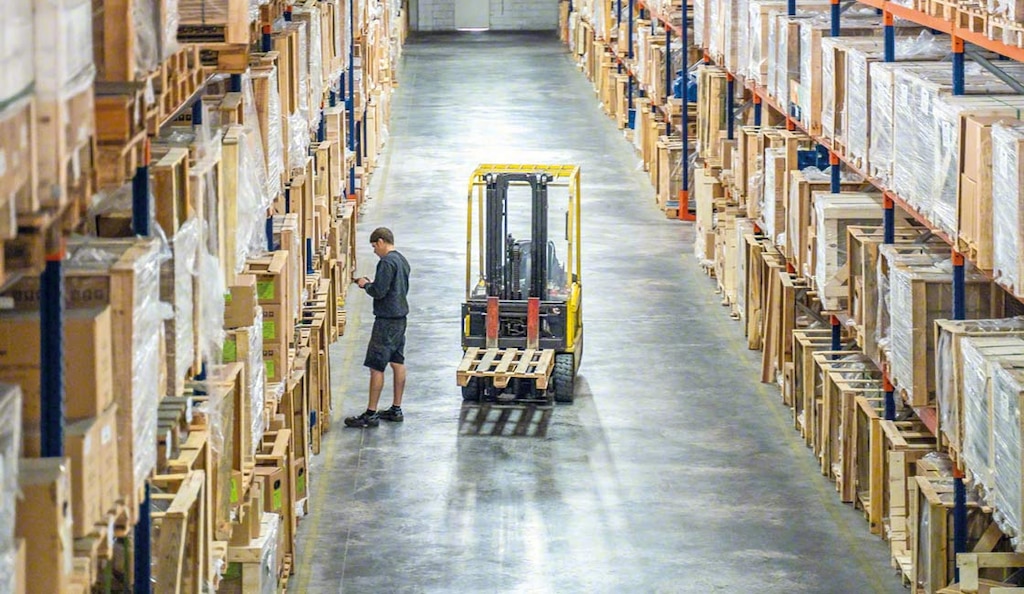
4) Cannibalization or recovery of parts (Surplus Motos)
In reverse logistics, cannibalization refers to the recovery of a product part or component that has reached the end of its service life . This process involves the disassembly of a used item and the inspection of the parts that can be reused in other processes, such as repair and remanufacturing. This is an extremely rigorous process in which the recovered parts must meet certain quality standards in order to be reused.
Surplus Motos , a retailer of spare parts for used motorcycles, bases its business on cannibalization. At its logistics center, the company decontaminates, disassembles, and cleans its motorbike components. The parts are then photographed, stored and put on sale at a price 30%-70% cheaper compared to new parts.
To efficiently organize all the goods, the company has outfitted its distribution center in Gaillac, France, with a miniload system for boxes from the Mecalux Group. This automated storage and retrieval system (AS/RS) holds 300,000 parts, a sufficient volume to reach its objective: to recycle up to 10,000 motorcycles a year.
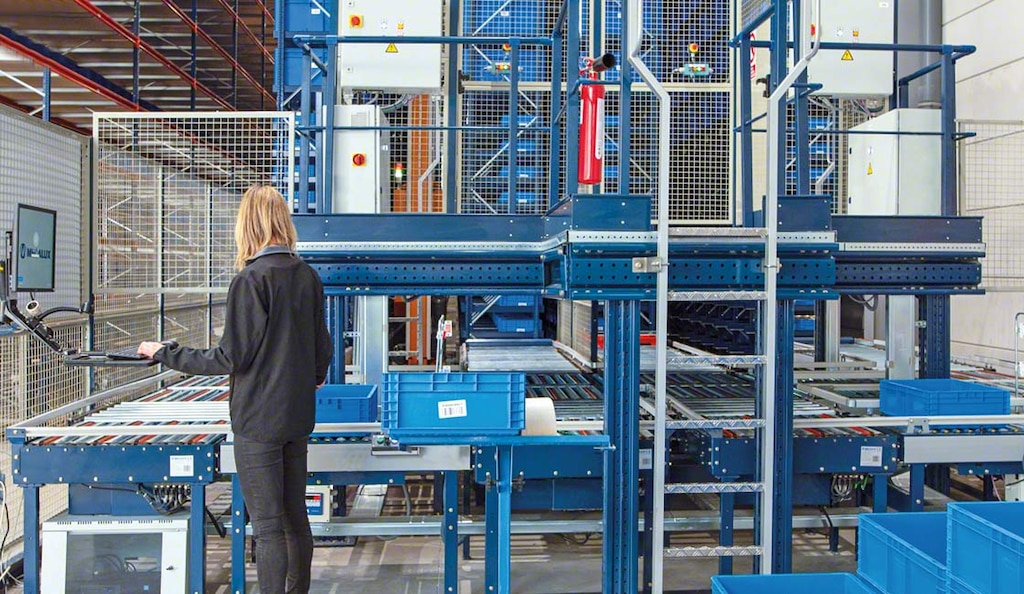
5) Returns rate reduction (Espace des Marques)
Reverse logistics management is a real headache for many companies, as it requires time and resources. Therefore, it’s essential to minimize returns.
A prime example of how to do this is that of French online fashion store Espace des Marques . The retailer has considerably lowered its number of returns with the Mecalux Group’s Easy WMS, which sends operators specific instructions on how to prepare each order, thus, avoiding mistakes.
With this solution, the company has completely eliminated errors in order picking. Consequently, its customers are happier and don’t return as many purchases. Of course, there is still a percentage of returns not necessarily due to mistakes in the warehouse (e.g., changes in sizes, colors, and models).
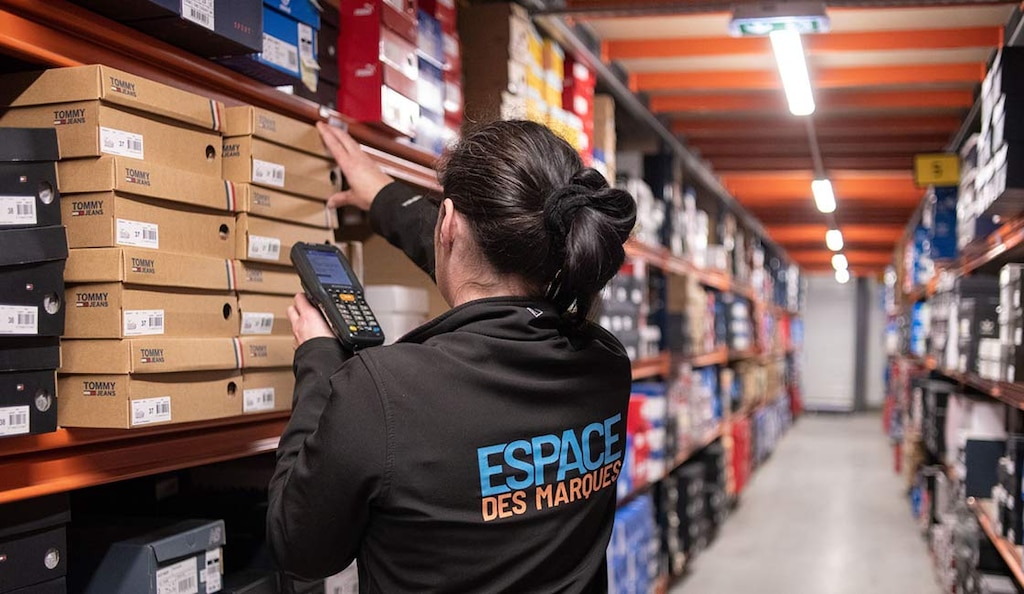
Reverse logistics: strategies for every need
The various examples of reverse logistics we’ve seen in this post demonstrate that reverse logistics is a competitive opportunity for many businesses. They can benefit from giving merchandise a second chance, recovering its value. And, if there’s no alternative, they can dispose of it properly.
To implement reverse logistics effectively , the warehouse must be designed well. For example, it could be equipped with an area for refurbishing items and with storage and management systems that facilitate proper organization of the goods. At Interlake Mecalux, we have extensive expertise in devising the most appropriate storage solution for each need. Get in touch so we can give you helpful advice on how to design your warehouse.
Recent entries
Edge AI: benefits of local artificial intelligence
Predictive maintenance: techniques and advantages
Material handling and the logistics operations involved
Computer vision: the senses reach automation
The power of best-of-suite software in the supply chain
- Warehouse Automation
- Logistics Software
- Warehouse Organization & Design
- Order Fulfillment
- Warehouse Safety & Staff Management
- Industrial Storage Systems
A Guide to Reverse Logistics: How It Works, Types and Strategies

Reverse logistics is the reverse of the standard supply chain flow, where goods move from manufacturer to end consumer. Reverse logistics includes activities like returns management, refurbishment, recycling, and disposal. It's an important part of supply chain management, often involving the return of products due to damage, seasonal inventory, restock, salvage, recalls, or excess inventory.
What Is Reverse Logistics?
Reverse logistics is a type of supply chain management that moves goods from customers back to the sellers or manufacturers. Once a customer receives a product, processes such as returns or recycling require reverse logistics.
Reverse logistics start at the end consumer, moving backward through the supply chain to the distributor or from the distributor to the manufacturer. Reverse logistics can also include processes where the end consumer is responsible for the final disposal of the product, including recycling, refurbishing or resale.
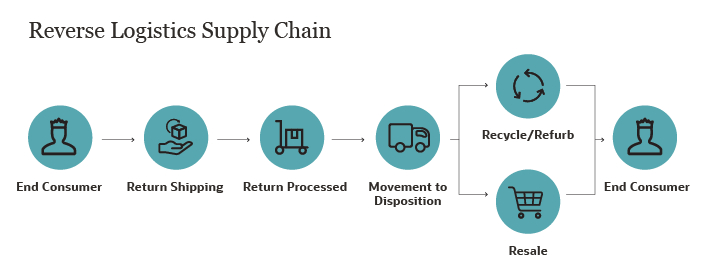
When Is Reverse Logistics Used?
Organizations use reverse logistics when goods move from their destination back through the supply chain to the seller and potentially back to the suppliers. The goal is to regain value from the product or dispose of it. Worldwide, returns are worth almost a trillion dollars annually (opens in a new tab) and have become increasingly common with the growth of ecommerce.
The objectives of reverse logistics are to recoup value and ensure repeat customers. Less than 10% of in-store purchases are returned, compared to at least 30% (opens in a new tab) of items ordered online. Savvy companies use reverse logistics to build customer loyalty and repeat business and to minimize losses related to returns.
Reverse Logistics vs. Traditional Logistics
Traditional product flow starts with suppliers and moves on to a factory or distributor. From there, the goods go to retailers and customers. Reverse logistics management starts at the consumer and, moving in the opposite direction, returns products to any point along the supply chain .
Well-designed supply chains are responsive to changes and can handle some reverse logistics requirements. This reverse process can return products one step back in the chain or to the original supplier. They can even send returned products back to regular sales or discount channels (like liquidators).
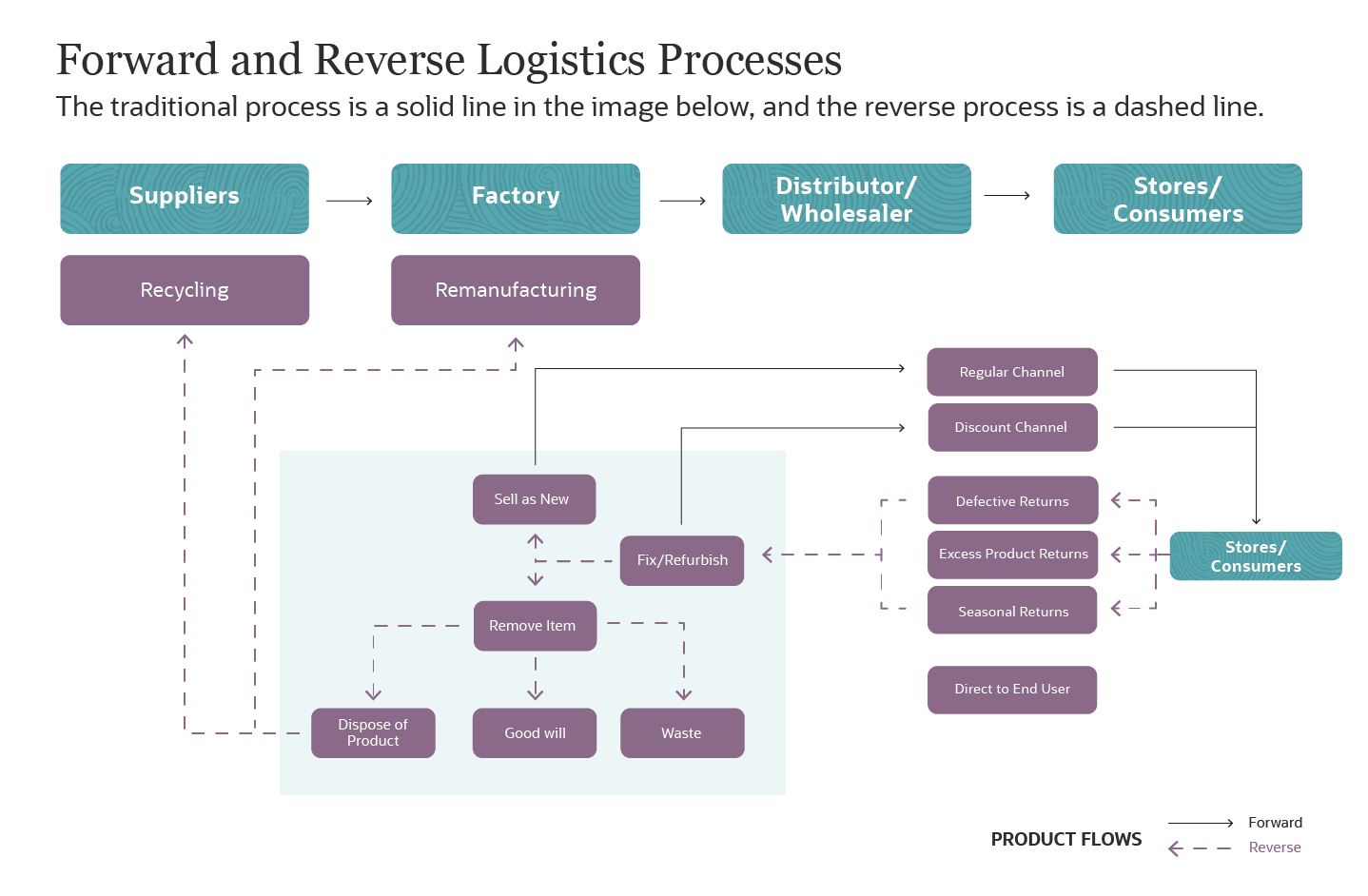
How Reverse Logistics Works
Reverse logistics moves goods from the traditional endpoint of the supply chain at least one step backward. This process can involve various plans and controls. Some companies prefer to outsource this work.
Reverse Logistics Process
The reverse logistics process involves managing returns and buying surplus goods and materials. The process is also responsible for dealing with any leases or refurbishments. Reverse logistics vary across different industries, and there are different economic incentives for improving reverse logistics management.
For example, in the beverage industry, the reverse logistics process uses empty tap containers. Beverage production companies want to recapture the value of their containers by reusing them. This requires planning transportation , managing shipping loads and cleaning the containers.
In the construction industry, reverse logistics moves and recycles salvaged materials to new sites. As the construction industry adopts more sustainable practices to reduce waste, there is an opportunity for cost savings by using reverse logistics.
In the food industry, reverse logistics is responsible for returning packaging materials and pallets. Companies also must deal with rejected food shipments. Rejections can create logistical challenges due to delays that lead to food spoilage and concerns over tampering. The Reverse Logistics Association (opens in a new tab) is developing secure, quick, reliable, login (SQRL) codes on packaging to provide detailed product information and address these logistical challenges.
5 Steps to Good Reverse Logistics
- Process the Return The return process starts when the consumer signals they want to return a product. This step should include return authorization and identify the product’s condition. This process also involves scheduling return shipments, approving refunds and replacing faulty goods.
- Deal with Returns Once a returned product arrives at your location or centralized processing center, inspect it and determine its return category. (Note: If you have optimized reverse logistics, you should know where the product should go before it arrives.) Sort products into the disposition options: fix, resell as new, resell as a return, recycle, scrap or refurbish.
- Keep Returns Moving Reduce your daily waste by sending repairable items to the repair department.
- Repair After reviewing the returned item/equipment and determining whether it can be repaired, move it to the repair area. If not possible, sell any sellable parts.
- Recycle Any parts or products that you cannot fix, reuse or resell should be sent to the area for recycling.
Video: What Is Reverse Logistics?
Types of Reverse Logistics
The different types of reverse logistics are also known as reverse logistics components. They focus on returns management and return policies and procedures (RPP) and account for remanufacturing, packaging, unsold goods and delivery issues. Other types of reverse logistics account for leases, repairs and product retirement.
Reverse Logistics Components:
- Returns management: This process deals with product returns from customers or avoiding returns in the first place. These activities should be fast, controllable, visible and straightforward. Customers judge a company on its return flow and re-return policies. A re-return is the return of an item a second time. Often, these returns trigger the extended return policies, such as offering store credit. For example, a customer buys a returned product on clearance, takes it home and discovers it broken. The store policy would not normally accept the return, but it does allow for a store credit for the faulty product. A re-return can also occur when a vendor rejects the return and gives it back to the purchaser without a refund. This scenario could happen with custom-made items.
- Return policy and procedure (RPP): The policies about returns that a company shares with customers is its RPP. These policies should be visible and consistent. Employees should also adhere to them.
- Remanufacturing or refurbishment: Another type of reverse logistics management includes remanufacturing, refurbishing and reconditioning. These activities repair, rebuild and rework products. Companies recover interchangeable, reusable parts or materials from other products, also known as the cannibalization of parts. Reconditioning involves taking apart, cleaning and reassembling products.
- Packaging management: This type of reverse logistics focuses on reuse of packing materials to reduce waste and the disposal.
- Unsold goods: Reverse logistics for unsold goods handles returns from retailers to manufacturers or distributors. These types of returns can be due to poor sales, inventory obsolescence or a delivery refusal.
- End-of-life (EOL): When a product is EOL, it is no longer useful or does not work. The product may no longer meet a customer's needs or be replaced by a newer, better version. Manufacturers often recycle or dispose of products that are end-of-life. These goods can create environmental challenges for manufacturers and countries.
- Delivery failure: With failed deliveries, drivers return products to sorting centers. From there, the sorting centers return the products to their point of origin. While rare, some sorting centers may have the staff available to identify why a delivery failed, correct the problem and resend.
- Rentals and leasing: When a piece of equipment comes to the end of its lease or rental contract, the company that owns the product can remarket, recycle or redeploy it.
- Repairs and maintenance: In some product agreements, customers and companies maintain equipment or repair it if issues arise. In some cases, the company sells damaged returned products to another consumer after repair.
What Are the Five Rs of Reverse Logistics?
The five Rs of reverse logistics are returns, reselling, repairs, repackaging and recycling. Companies apply metrics to each of these options to track improvement and success. Your business may want to take a closer look at the Five Rs to streamline its reverse logistics processes and reduce losses there.
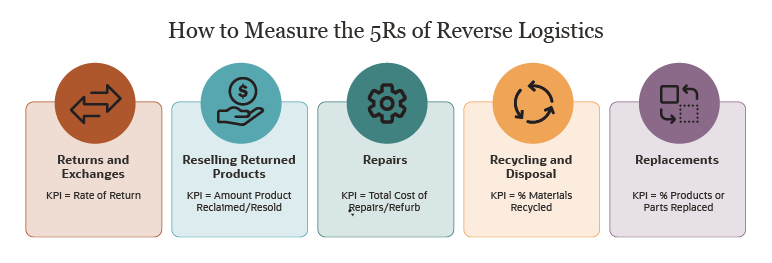
Reverse Logistics Examples
Globally, companies are changing the ways they address waste, and the supply chain is a big piece of that initiative. These reverse logistics examples focus on returns, exchanges and recycling.
People are more likely to buy products from a company if they think returns are easy and they are even more likely to become repeat customers if they’ve had a good return experience. For example, Home Depot offers reverse logistics help for online purchases via its website. In 2020, the company’s online sales represented almost 15% of total sales (opens in a new tab) . When a customer returns goods, they have a choice: send products back by printing a shipping label, or drop them off in-store. These items are then sent to Home Depot reverse logistics centers that handle damaged and misdirected products.
Retailer Levi Strauss uses reverse logistics to improve sustainability in textiles. The business repurposes jeans or recovers and reprocesses the fibers into raw materials to make new jeans. By partnering with other companies for repurposing, Levi Strauss can produce reconstructed jeans at a higher price point.
Kohl’s, a major retailer with more than 1,000 brick-and-mortar stores, is another example of the reverse supply chain in action. Kohl’s partners with Amazon to accept, screen and send back Amazon returns in a single shipment. Customers who prefer returning products in-person benefit from this relationship and Kohl’s gets customers in its door who may not normally visit its stores. Kohl’s also carries some Amazon products and can simply return them if they do not sell.
Some big brands are also turning to reverse logistics to address waste. Proctor & Gamble, PepsiCo, and Unilever are shifting to reusable packaging (opens in a new tab) that consumers can return. The companies will clean and use the containers again. Transportation and logistics are evolving for these companies and will pick-up the packaging when they drop off products.
Some companies, such as GE Healthcare and Cisco, specialize in refurbishing, repairing and remanufacturing defective or out-of-date goods for consumers. Cisco remanufactures goods such as phones, routers and switches. GE Healthcare remanufactures imaging devices and ultrasound machines.
Microsoft has a large global initiative to deal with end-of-life for devices, batteries and packaging. Microsoft’s product packaging is 100% recyclable, and it has a program for refurbishing and reusing personal computers.
Some organizations resell overstocked goods to the secondary market, like factory outlets, off-price and discount stores, and online auction sites. Retailers such as TJX Companies (TJ Maxx, Marshalls and HomeGoods) buy these overstock items and sell them at a discounted price to consumers.
Importance of Reverse Logistics to Your Business
Reverse logistics is important because it maintains an efficient flow of goods. The process reduces costs, creates value, decreases risk and completes the product life cycle.
Gartner Research says that about 70% of businesses plan to invest in the " circular economy (opens in a new tab) ." This circular economy follows traditional logistics and then continues around through what Gartner calls a closed-loop supply chain.
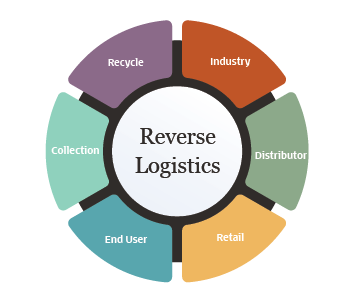
With this practice, companies are participating in a system focused on a sustainable economy. Companies find new uses for disposed products with recovery, repair and recycling. Materials once typically viewed as waste have value again.
The circular economy also ensures compliance as many countries institute a policy requiring "producers" to develop more sustainable practices (opens in a new tab) . The guidelines outline subsidies for waste prevention, research and development and recycling. Other policies restrict landfills, mandate collection and recycling programs, and penalize certain waste practices.
How Does Reverse Logistics Create Value?
Reverse logistics creates value by turning waste into sales and builds customer trust. Businesses resell, reuse and recycle returned products. In addition, effective reverse logistics keeps down any storage and distribution costs.
Gartner Research finds that less than half of returned goods are resold at their full price. There is value in finding the best disposition option for returned items. For example, retail businesses like B-Stock resell returned goods. B-Stock sold 70 million returned or excess goods in 2019. The company buys the returns for a percentage of their original cost and then resells them at a discount to the consumer.
Using reverse logistics to boost the efficiency of the traditional supply chain benefits everyone. Some businesses separate their forward and reverse logistics, and others combine them. The relative success of combining them depends on the company’s experience, the value of its products and return volume. Either way, they use practices to maximize their profitability ratios with their supply chain activities. Read these expert tips on how to maximize profits in business.
Benefits of Optimized Reverse Logistics
Optimized reverse logistics produce financial benefits while positively impacting the environment and business culture. Refining the processes for what happens to products after delivery helps retain customers and save money.
The product data collected when engaging with customers after delivery is an advantage of well-executed reverse logistics. Data provides insight into an organization’s supply chain and an opportunity to improve products and/or the customer experience.
Optimized reverse logistics also leads to better supply chain visibility , which leads to benefits like:
- Cost reduction
- Greater customer satisfaction
- Better customer retention
- Faster and better service
- Loss reduction
- Improved brand sentiment
- Waste reduction and greater sustainability
Challenges of Reverse Logistics
A challenge of reverse logistics is that the flow must be bi-directional. Managers need to set up the right infrastructure for it to be effective. That often requires software that can automate and track every step of reverse logistics. Additionally, once that infrastructure is in place, management needs to continually monitor and evaluate the organization’s reverse logistics processes to ensure efficiency.
Companies must track inbound and outbound logistics to get the full picture. Inbound logistics manages the receipt of raw materials or goods from the supplier to the manufacturer. Outbound logistics is the processes that deliver the finished goods to the end user. Both inbound and outbound logistics are measured from the manufacturer’s perspective, while reverse logistics can be part of any point in the supply chain.
7 Strategies to Optimize Reverse Logistics
To optimize reverse logistics, companies need cohesive strategies that account for speed, efficiency and cost. When taking action, consider policies, partners, data, capacity, logistics and transportation.
The seven strategic ways to optimize reverse logistics are:
- Evaluate Relevant Policies and Agreements Review and revise the procedures related to your company's returns and repairs. These policies should be clear and consider the root causes of returns and repairs. The way a company deals with returns and repairs can be competitive differentiators.
- Collaborate with Suppliers Close collaboration with suppliers can help ensure a smooth, integrated experience for customers, not a disjointed one they will struggle to navigate.
- Use Data to Optimize Processes By collecting data on product returns, you can understand why customers may be returning products. Then, you can make adjustments in sales, product design and forward logistics processes accordingly.
- Track products forward and backwards Linking raw materials to the finished good and the customer order allows you to trace ingredients in the event that you need to process recalls—instead of issuing them for entire lines, you can find the issue and selectively issue recalls.
- Centralize Return Centers With a centralized return center, you can better sort products and identify the best next step for each of them. With a center, businesses can more efficiently determine how best to reclaim product value. If your company lacks the resources to have a separate returns center, consider dedicating a portion of your warehouse or factory to returns.
- Examine Logistics and Transportation Regularly review the processes for forward and reverse logistics and transportation. Determine if it is feasible to integrate some of these processes and transit. For example, if your delivery drivers can pick up empty pallets as they drop off full pallets, you save trips, time and money.
- Automate Use cloud-based logistics software to help streamline operations. For example, a software system can track asset recovery, manage refurbishment and provide business intelligence analytics.
How Do Reverse Logistics Impact Supply Chain Management?
Reverse logistics provide another critical opportunity for supply chain optimization. Supply chain management accounts for the reverse and forward flow of goods, and a surge of returns can drive up supply chain costs, harming profitability.
What Is Reverse Logistics vs. Reverse Supply Chain?
The reverse supply chain is the backward movement of goods (such as defective products) from vendors back up the supply chain. It is the opposite of the typical supply chain, where items go from manufacturer to retailer to consumer.
Reverse logistics refers to everything related to returns and what happens to those products after the consumer takes them back. That includes planning and implementing strategies to reduce costs and losses related to returns and to build a better returns experience.
Monitoring Reverse Logistics in Your Supply Chain
Companies monitor reverse logistics in the supply chain to find better ways to process and dispose of products. There is a considerable volume of information available in the ways goods move back and forth through the supply chain. This detail can help companies meet their delivery goals.
Some organizations have the simple goal of on-time delivery; others reach for what they call the "perfect order.” For every order, the goal is to get a perfect score in place, time, condition, package, quantity, documentation, customer and invoice. The only way to achieve a perfect order is to monitor the data, develop metric targets and improve processes based on your results. Reverse logistics can play a central role in delivering the perfect order.
5 Key Reverse Logistics Supply Chain Metrics to Monitor and Confirm
There are five key reverse logistics-focused supply chain metrics that will help increase asset recovery. Supply chain analytics can help management make data-driven decisions at all steps of the supply chain.
Key supply chain metrics include:
- Volume: The volume of products returned and subsequently resold, reused and recycled is a top metric used to track reverse logistics. Companies should use these measurements to identify missed opportunities or problems and determine where process improvements can make a difference.
- Percent of Costs: Compare the costs attributed to resales, refurbishing, reuse and recycling to the total supply chain cost. Determine the difference in the price of these activities versus the cost of returns. Be sure to calculate the percent of expenses recovered by item.
- Condition of Returned Products: Some products come back in perfect resale condition, and companies can turn them around for resale at full value. Other goods may need some work before a company can resell them. In that scenario, companies should consider other sales channels for those products. For example, companies may sell refurbished electronics through another sales channel. Determine the cost of materials and workmanship to determine the full value. Review the percent of items sent to each sales channel and whether the company is recouping enough money.
- Financial Value: Each part of the supply chain has economic value. Understanding what financial stake your company has in each step can lead to better processes and efficiencies.
- Errors: Every step in the supply chain also has the potential for errors, such as unaccepted deliveries or defective materials. Review the cost of mistakes and how frequently they occur to identify opportunities for improvement.
Supply chain analytics should exist throughout the entire value chain, from sourcing materials through distribution and delivery . Useful metrics lead to growth in revenue, better margins and controlled capital. Supply chains are increasingly going digital (opens in a new tab) , so collecting the data is easier. Read the supply chain analytics guide to learn how to make the most of this practice.
The Future of Reverse Logistics
The future of reverse logistics is all about minimizing disruptions from returns. Especially in ecommerce, and increasingly in the retail industry, the volume of returns is increasing. Companies can use reverse logistics to integrate all parts of the returns process.
One way to integrate returns is to connect the product’s data to how staff needs to handle it. Documenting what happens to a returned product—whether the item will go to resale, repairs, or be recused for raw goods—the supply chain can support this integration. The future of reverse logistics involves integrated supply chain management software that helps make these determinations and can also provide valuable reports.
Manage Reverse Logistics with Warehouse Management Software
Managing your reverse logistics is essential for the bottom line and reputation of your business. Consumers need to feel like they are buying products from companies with integrity, and improving your reverse logistics opens up opportunities for a number of sustainable business practices.
That’s why it is crucial to have a warehouse management system (WMS) that can manage inbound and outbound logistics and deliver analytics in real time. Businesses need insights across transportation and logistics providers, through warehouse and fulfillment and ultimately need to integrate all that information with financial data in an enterprise resource planning (ERP) system . ERP platforms like NetSuite, paired with a warehouse management system , allow companies to easily track returns, monitor the movement of goods, issue credits through the accounting system and update everything in the customer record.
Similarly, inventory management is key to efficient returns processes. A high rate of returns can lead to inventory buildup, and an effective inventory management system will alert you when inventory levels are growing too quickly—faster than your rate of sales.
Many companies are taking a closer look at their reverse logistics as they realize returns are a major source of expenses and there are opportunities to recover more money on those goods. Additionally, rising return rates make it imperative for these businesses to figure out a more cost-effective way to handle products sent back to them. Evaluating your reverse logistics processes to identify inefficiencies and address those shortcoming can boost your bottom line by not only lowering costs, but increasing customer loyalty and elevating brand reputation.
Award Winning Cloud Inventory
Reverse Logistics FAQ
You may have additional questions about reverse logistics. Below, we answer some of the most popular ones.
What is integrated logistics?
Integrated logistics is the full process that covers delivery through end-user issues and then deals with product disposition. Integrated logistics stresses material and resource sustainability.
How much does it cost to implement a reverse logistics plan?
Implementing a reverse logistics plan costs about 7-10% of the cost of goods in a company. However, it’s worth noting that reverse logistics planning should bring down the costs associated with returns.
How does reverse logistics work in the pharmaceutical industry?
In the pharmaceutical industry, reverse logistics helps keep medicines safe (out of landfills and water supplies). The sector handles product returns and disposal through third-party companies and distributors.
Can you explain the role of reverse logistics in the service industry?
In the service industry, reverse logistics helps address repairs more quickly. Best practices include refunds, warranty work and credit. Working out these policies keeps customers happy.
How does reverse logistics differ for the manufacturing and service industries?
The service and manufacturing industries differ from others. Their products and services are not standard, so the returns are not standard. The reverse logistics process starts after the company fixes the service or manufacturing part.
Manufacturing companies sell fixed parts as refurbished items. These parts have a lower value and may go through a different supply chain. In the service industry, companies can provide warranty work, credit, or work refunds.
How can ecommerce organizations handle reverse logistics to ensure it’s a low-cost transaction?
To make returns a low-cost transaction, ecommerce companies should combine returns with deliveries. They should also consider turning to third-party partners. Ecommerce businesses should identify the root causes of problems and develop strategies to decrease these issues.
What is a reverse logistics expert?
A reverse logistics expert is a professional who can help your company be more efficient by suggesting and implementing process improvements in your reverse supply chain. Good reverse logistics experts consider your customers, business priorities and sales goals.
How are forward logistics and reverse logistics different?
The difference between reverse and forward logistics is the direction the product is moving along the supply chain. Products that come from the manufacturer and move toward the customer are going forward. Products coming back from customers to retailers or manufacturers are heading in reverse.
What is reverse distribution?
Reverse distribution is the role of removing goods that are unsold, damaged, expired or recalled from retailers. Like with returns, these goods go in the reverse direction through the supply chain.
What is design for logistics (DFL)?
The concept of DFL states that products and their packaging design can lower the expenses related to logistics. For example, soda cans became flat on top, making them easier and cheaper to transport and store.
What is design for reverse logistics (DFRL)?
DFRL refers to designing products and packaging that makes it cheaper and easier to move in a reverse flow in the supply chain. For example, manufacturers package products in reusable canisters that they refill for retailers.
How does reverse logistics reduce business risk?
Reverse logistics reduce business risk by ensuring companies adhere to policies for waste and disposal. Some governments fine companies that do not meet guidelines. Reverse logistics also help companies recoup value in unsold and returned goods.
How do you lower the cost of reverse logistics?
Cut the costs in reverse logistics by first decreasing returns. Experts recommend enabling customer product reviews to help set expectations and reduce returns. Then, look for ways to combine reverse and forward logistics to drive cost savings.
How does reverse logistics contribute to a lean supply chain?
A solid reverse logistics plan reduces waste. Lean principles can also make the supply chain more efficient. Instead of separating shipping and returns, a lean supply chain combines them.
Inventory Management
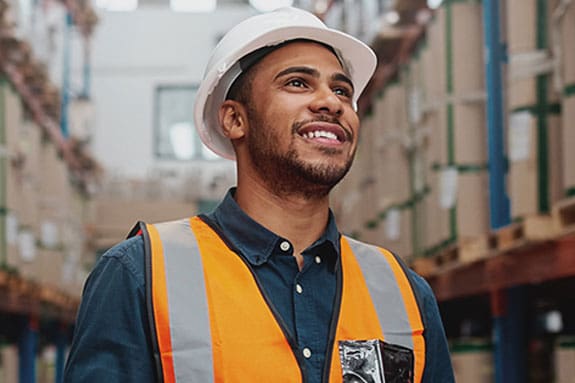
Guide to Inbound and Outbound Logistics: Processes, Differences and How to Optimize
Strong inbound and outbound logistics are crucial to the success of a business. These processes affect production, profits and customer service. There are many challenges in getting logistics right, and the costs of…

Trending Articles
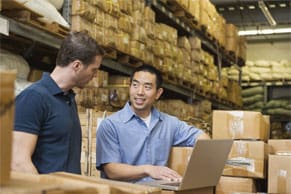
Learn How NetSuite Can Streamline Your Business
NetSuite has packaged the experience gained from tens of thousands of worldwide deployments over two decades into a set of leading practices that pave a clear path to success and are proven to deliver rapid business value. With NetSuite, you go live in a predictable timeframe — smart, stepped implementations begin with sales and span the entire customer lifecycle, so there’s continuity from sales to services to support.
Before you go...
Discover the products that 37,000+ customers depend on to fuel their growth.
Before you go. Talk with our team or check out these resources.
Want to set up a chat later? Let us do the lifting.
NetSuite ERP
Explore what NetSuite ERP can do for you.
Business Guide
Complete Guide to Cloud ERP Implementation

Exploring Amazon’s Reverse Logistics Strategies

Table of Contents:
- The Importance of Reverse Logistics in E-commerce
- Understanding Amazon’s Supply Chain Management
- The Role of Reverse Logistics in Amazon’s Sustainability Efforts
- How Amazon Manages Returns and Excess Inventory
- Analyzing Amazon’s Reverse Logistics Process for Customer Satisfaction
- Impact of Reverse Logistics on Amazon’s Bottom Line
- Best Practices for Reverse Logistics in Online Retail
- The Future of Reverse Logistics in E-commerce Industry
- Challenges Faced by Amazon in Managing its Reverse Logistics Operations
- Comparison of Amazon’s Reverse Logistics Strategies with Competitors
- How Technology is Transforming the Reverse Logistics Landscape for Amazon and Retailers Alike
- Efficient Strategies for Reducing Costs and Enhancing Efficiency in Reverse Logistics for E-commerce Industry
- Customer Insights: What Do They Expect from a Good Return Experience on Amazon?
- Case Study: Successful Implementation of a Comprehensive Reverse Logistics Strategy by Amazon
Join hundreds of smart shippers. Guaranteed to save.
In the highly competitive world of e-commerce, efficient reverse logistics strategies have become increasingly important for businesses looking to stay ahead. As the world’s largest online retailer, Amazon has implemented innovative and effective methods to manage its reverse logistics operations. In this article, we will explore various facets of Amazon’s reverse logistics strategies and their impact on the company’s overall success.
Reverse logistics refers to the process of managing and disposing of goods that are returned to the seller by customers. In the e-commerce industry, returns are a common occurrence and managing them effectively has become vital for retailers to ensure customer satisfaction and maintain profit margins. Given the vast scale of Amazon’s operations, the company’s reverse logistics strategies have a significant impact on its bottom line.
One of the key challenges in managing reverse logistics in e-commerce is the high cost associated with it. Retailers have to bear the cost of shipping the returned goods, inspecting them, and either restocking or disposing of them. To mitigate these costs, some retailers have started offering incentives to customers for keeping the returned items, rather than shipping them back. This approach not only reduces the cost of reverse logistics but also encourages customers to make more purchases.
Another important aspect of reverse logistics in e-commerce is the environmental impact of returned goods. Many returned items end up in landfills, contributing to the growing problem of electronic waste. To address this issue, some retailers have started partnering with organizations that specialize in recycling and repurposing returned goods. By doing so, they not only reduce their environmental footprint but also create a positive brand image among customers who are increasingly conscious of sustainability.
Understanding Amazon’s Supply Chain Management
One of the key factors behind Amazon’s success is its highly efficient supply chain management. The company’s supply chain encompasses multiple complex processes, including procurement, warehousing, inventory management, and transportation. By optimizing these processes, Amazon is able to offer fast and reliable delivery to customers at a lower cost than its competitors.
Amazon’s supply chain management also includes the use of advanced technologies such as robotics, artificial intelligence, and machine learning. These technologies are used to automate various processes, such as picking and packing in warehouses, and to analyze data to improve inventory management and forecasting. Additionally, Amazon has implemented a system called “Frustration-Free Packaging” which reduces waste and makes it easier for customers to open and use their products.
The Role of Reverse Logistics in Amazon’s Sustainability Efforts
As a major player in the retail industry, Amazon has a responsibility to minimize its impact on the environment. The company has made significant strides in this area by implementing sustainability initiatives across various aspects of its operations, including reverse logistics. By refurbishing and reselling returned products, Amazon is able to reduce the amount of waste generated and promote a circular economy.
In addition to refurbishing and reselling returned products, Amazon also utilizes reverse logistics to optimize transportation and reduce emissions. By consolidating shipments and using more efficient routes, the company is able to minimize the carbon footprint of its logistics operations. This not only benefits the environment, but also helps to reduce costs and improve delivery times for customers.
Furthermore, Amazon has implemented a program called “Frustration-Free Packaging” which aims to reduce the amount of excess packaging materials used in shipping. This program not only reduces waste, but also makes it easier for customers to open and use their products. By incorporating sustainable practices into its reverse logistics operations, Amazon is setting an example for other companies in the industry to follow and demonstrating its commitment to environmental responsibility.
Amazon has a well-established process in place to manage returns and excess inventory. When a customer initiates a return, the product is first evaluated to determine whether it can be resold as new or needs to be refurbished or disposed of. If the product is in good condition, it is either restocked or sold as part of Amazon’s “Amazon Warehouse” program, which offers discounted products to customers. Amazon also uses predictive analytics to forecast the level of returns and adjust its inventory levels accordingly.
In addition to these processes, Amazon also partners with third-party liquidators to sell excess inventory that cannot be resold through their own channels. These liquidators purchase the inventory in bulk and then sell it to other retailers or wholesalers. This allows Amazon to recoup some of the cost of the excess inventory and prevent it from taking up valuable warehouse space.
Analyzing Amazon’s Reverse Logistics Process for Customer Satisfaction
Customer satisfaction is a top priority for Amazon, and the company’s reverse logistics process is designed to ensure a smooth and hassle-free experience for customers. Amazon’s customer service representatives are trained to handle returns and address any complaints or issues that customers may have. Additionally, the company offers a range of return options to cater to different customer preferences, including drop-off locations, pick-up services, and mail returns.
Another key aspect of Amazon’s reverse logistics process is their use of technology. The company has developed sophisticated software that tracks returned items and analyzes the reasons for returns. This data is then used to improve product quality and reduce the number of returns in the future. Amazon also uses automation technology to streamline the returns process, reducing the time it takes for customers to receive refunds or replacements.
Furthermore, Amazon’s commitment to sustainability is reflected in their reverse logistics process. The company has implemented a program called “Frustration-Free Packaging” which aims to reduce waste and improve the customer experience. This program involves using recyclable materials and designing packaging that is easy to open and dispose of. By reducing the amount of packaging waste generated by returns, Amazon is able to minimize their environmental impact while also improving customer satisfaction.
Impact of Reverse Logistics on Amazon’s Bottom Line
Effective reverse logistics strategies have a significant impact on Amazon’s bottom line. By refurbishing and reselling returned products, the company is able to recover a portion of the cost and reduce the financial impact of returns. Additionally, proper management of excess inventory reduces the amount of money tied up in unsold products, allowing Amazon to invest in other areas of its business.
Another way that reverse logistics benefits Amazon is by improving customer satisfaction. By offering hassle-free returns and exchanges, customers are more likely to continue shopping with Amazon and recommend the company to others. This leads to increased sales and revenue for the company.
Furthermore, Amazon’s commitment to sustainability is also supported by its reverse logistics strategies. By refurbishing and reselling returned products, the company is reducing waste and extending the life cycle of products. This not only benefits the environment but also aligns with the values of many of Amazon’s customers, leading to increased loyalty and brand reputation.
Amazon’s success in reverse logistics can serve as a model for other businesses in the e-commerce industry. Some best practices include implementing a robust returns management system, using data analytics to forecast returns and inventory levels, and offering a range of return options to cater to different customer preferences. By adopting these strategies, businesses can reduce the financial impact of returns and enhance customer satisfaction.
Another important aspect of reverse logistics is the proper disposal or recycling of returned products. Businesses should have a clear policy in place for handling returned items that cannot be resold. This not only helps to reduce waste and environmental impact but also ensures compliance with regulations and laws related to product disposal.
In addition, businesses can also leverage reverse logistics as an opportunity to gather valuable feedback from customers. By analyzing the reasons for returns and customer feedback, businesses can identify areas for improvement in their products, services, and overall customer experience. This can lead to increased customer loyalty and retention, as well as improved brand reputation.
The e-commerce industry is constantly evolving, and reverse logistics is no exception. With the rise of new technologies such as blockchain, AI, and the Internet of Things (IoT), the reverse logistics landscape is set to transform rapidly in the coming years. Amazon is at the forefront of these innovations, and its continued investment in reverse logistics will likely set the standard for the industry as a whole.
As with any complex system, managing reverse logistics comes with its own set of challenges. Some of the main challenges faced by Amazon in this area include managing the logistics of returns from third-party sellers, reducing the cost of refurbishment, and effectively managing excess inventory. However, the company’s adoption of innovative technologies and emphasis on sustainability will likely help it overcome these challenges.
Comparison of Amazon’s Reverse Logistics Strategies with Competitors
Amazon’s reverse logistics strategies have set it apart from its competitors. By offering a seamless returns experience and using predictive analytics to manage inventory levels, Amazon is able to reduce the financial impact of returns and minimize waste. Additionally, the company’s focus on sustainability sets it apart from competitors who prioritize profit over environmental impact.
The use of technology in reverse logistics has transformed the industry in recent years. Amazon has been quick to adopt these technologies, including robotics, automation, and data analytics. By integrating these technologies into its reverse logistics operations, the company has been able to reduce costs, enhance efficiency, and improve customer satisfaction.
Reducing costs and enhancing efficiency are key objectives of any reverse logistics strategy. Amazon has achieved this by using data analytics to forecast returns and inventory levels, optimizing its refurbishment process, and streamlining its logistics operations. By adopting similar strategies, businesses can reduce the financial impact of returns and enhance customer satisfaction.
Customer expectations are important when it comes to managing returns effectively. Amazon’s customers expect a simple and hassle-free returns experience, with flexible return options and clear communication from the company. By prioritizing customer satisfaction in its reverse logistics strategies, Amazon has set a high bar for the industry as a whole.
Amazon’s success in reverse logistics can be seen through its implementation of a comprehensive strategy that encompasses multiple facets of the process. By using innovative technologies, promoting sustainability, and prioritizing customer satisfaction, Amazon has effectively managed its returns and excess inventory. This success has set the standard for the e-commerce industry as a whole.
Overall, Amazon’s reverse logistics strategies have played a crucial role in the company’s success in the e-commerce industry. By using innovative technologies, prioritizing sustainability, and emphasizing customer satisfaction, Amazon has effectively managed returns and excess inventory, reduced costs, and maintained its position as a leader in the industry. As the industry evolves, Amazon will continue to drive innovation and set the standard for reverse logistics strategies in e-commerce.

268 N Santa Cruz Ave, Los Gatos, CA 95030 [email protected] 800.303.6644
© Copyright 2023, ShipScience.com. All Rights Reserved. Terms of Use | Privacy All other trademarks and copyrights are the property of their respective owners.
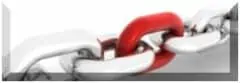
Supply Chain Game Changer™
Daily Insights, Trends and Solutions for Professionals, Experts, Students and Society
A Case Study in Reverse Logistics Optimization!
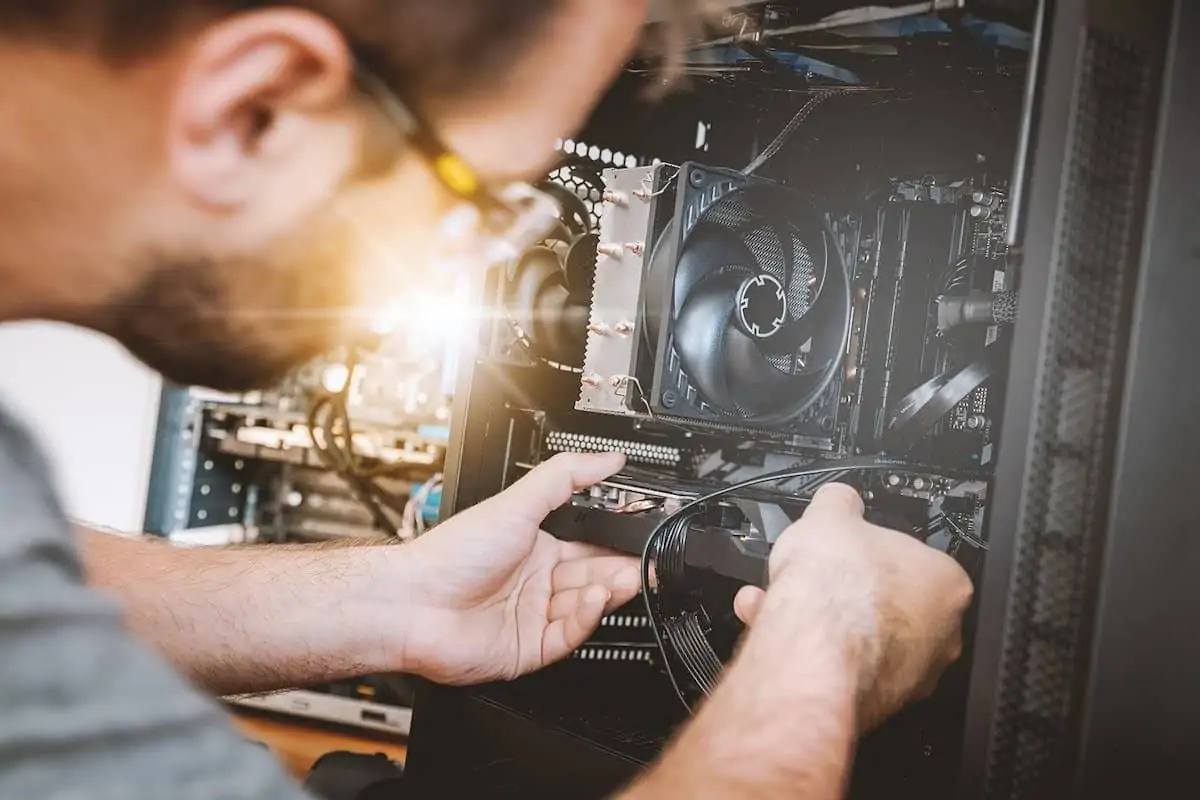
Reverse Logistics and the Power of Your 3PL!
The application of advanced forecasting and planning methodologies improve inventory management in a critical, high-volume repair and reverse logistics optimization business, dramatically reducing costs and fulfillment cycles while improving customer satisfaction.
When one of the world’s leading manufacturers of personal computers set new goals for its European operations, ModusLink was there to help.
The OEM turned over management of one of the most critical, high-volume segments of its reverse logistics program —the processor business—saving the manufacturer millions of dollars each year; reducing excess inventory; increasing same-day, on-time ship rates; and improving customer satisfaction.
Before we start, let’s shortly discuss what a case study is. Teachers, writers from an essays writing service , and some students may know it, but there should be an explanation for the whole audience. A case study refers to a real example of some situation – a particular problem, usually.
It should offer not only a description of the problem but also how it can be (or was) solved. Read on to find out the issues we have faced and how we’ve dealt with them.
The Challenges
- Difficulties forecasting demand in a high-volume repair environment caused inventory costs to skyrocket
- Inadequate planning and execution resulted in excess and obsolete inventory and poor utilization of warehouse space
- Variability of hardware and component sourcing affected production efficiency, causing fulfillment delays and lower customer satisfaction

The difficulties of forecasting demand in a service repair environment caused a major PC manufacturer to keep large amounts of spare parts on hand, resulting in skyrocketing inventory costs and poor utilization of warehouse and factory space.
The Solution
- Implemented a world-class forecasting model to improve inventory management and asset utilization while reducing costs
- Utilized advanced sourcing and materials planning to speed fulfillment cycles and improve service levels for increased customer satisfaction
- Configured a highly structured and efficient reverse logistics program to supplement demand inventory and reduce sourcing costs
ModusLink immediately tackled the forecasting and demand challenges by implementing its proven demand planning methodology. This solution uses sophisticated rules and procedures to create a feasible demand-driven execution plan that reduces inventory risk by minimizing the amount of time, product and cash a company has tied up in inventory.
The plan considers variability of demand while allowing for rapid changes characteristic of the service repair environment. The new model yielded a dramatic improvement in forecast accuracy, which quickly rose from 35 percent to 99 percent accuracy. Additionally, the client’s inventory levels were reduced by 52 percent or $2.3 million in just the first year.
Once a forecasting model was set up, ModusLink needed to round out the solution with more efficient and cost effective sourcing for the hardware elements. ModusLink’s primary source for processors was the returns management program, which required it to conduct rigorous testing to identify units that could be put back into forward logistics inventory— providing the OEM with significant cost savings, given the exorbitant price tag for processors.
When supply levels are low, ModusLink taps the open market to purchase processors, leveraging its local market expertise worldwide to obtain the right product, at the right price, at the right time.
ModusLink also handles shipments of spare modems, heat sinks, quick- restore CDs (which ModusLink presses in-house) and product documentation. ModusLink continuously monitors the supply levels of all these elements at the PC manufacturer’s central European hub and replenishes stock on a daily basis to ensure that consistent inventory levels are always on hand to meet the forecasted demand.
Reverse Logistics Optimization Results
- Immediately improved demand forecast accuracy from 35 percent to 99 percent
- Reduced spare parts inventory levels by 52 percent or $2.3 million in the rst year
- Reduced cycle time by 70 percent from 3.35 to 1.10 days
- Improved on-time, same day ship rates from 84 percent to 99 percent
- Reduced obsolescence by 75 percent
- Improved efficiencies in supply chain related processes by approximately 15 percent
ModusLink was able to reduce product excess and obsolescence by 75 percent, resulting in significant cost savings and improved asset utilization for the manufacturer. In addition, overall efficiency for supply chain related processes was improved by approximately 15 percent.
With a new demand-planning and sourcing infrastructure in place, ModusLink focused on improving customer service levels within the client’s after market repair-service business by driving process efficiency and distribution improvements. Within one year, ModusLink reduced cycle time by 70 percent, accelerating fulfillment from 3.35 to 1.10 days.
Reverse logistics optimization article and permission to publish here provided by ModusLink . Originally published on Supply Chain Game Changer on December 20, 2017.
Share this:.
- Click to share on LinkedIn (Opens in new window)
- Click to share on Twitter (Opens in new window)
- Click to share on Facebook (Opens in new window)
Leave a Reply
Your email address will not be published. Required fields are marked *
Notify me of new posts by email.
This site uses Akismet to reduce spam. Learn how your comment data is processed .
Academia.edu no longer supports Internet Explorer.
To browse Academia.edu and the wider internet faster and more securely, please take a few seconds to upgrade your browser .
Enter the email address you signed up with and we'll email you a reset link.
- We're Hiring!
- Help Center
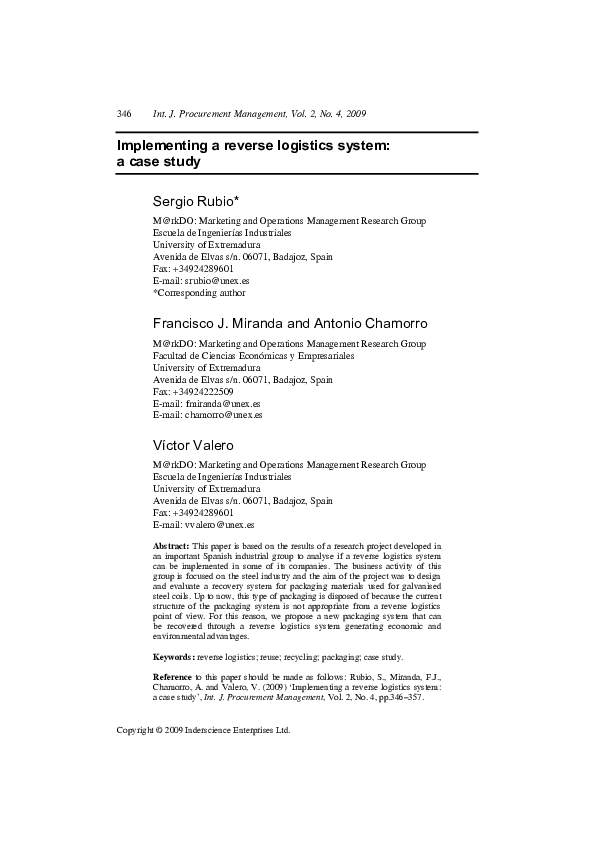
Implementing a reverse logistics system: a case study

2009, International Journal of Procurement Management
Related Papers
Andrej Lisec
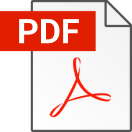
Acta logistica
Helena Vidova
The aim of the article is to present streamlining reverse logistics challenging the trends of increased amount costs of packaging and a need to meet sustainable development goals. Analysis of the packaging process has identified increased costs for the purchase of packaging, increased volume of imported and produced packaging material, increased volume of packaging waste and thus high recycling fees (related to producer responsibility). A proposed solution for streamlining reverse logistics processes have been introduced, including workflow of the packaging process, a new packaging registration system and measures for standardisation of the packaging process. The solution's main benefits are economical and ecological: first, cost reduction for purchasing new packaging materials and cost reduction for recycling fees, the second elimination of negative influence on the environment by respecting the waste management hierarchy and principles of the circular economy. Other benefits e...
Logistics Engineering Handbook
James Stock
José Antonio V A L L E S Romero
Summary This paper describes the state of the art of Reverse Logistics (RL), highlighting the importance for the development of communities where there is no other possibility; highlights the importance of quantitative methods applied to assess the current situation on the implementation of the RL, and finally point transport applications. The concept of recovered product management, which aims to "recover both economic and ecological value as possible, thereby reducing the final amounts of waste", In order to develop a policy for administration of recovered products (spare parts, tires, complete vehicles) resulting from their activities, allowing its use in areas where economic conditions do not exist to solve it through direct logistics. Are classified and analyzed, the options apply effectively the cycle of RL. To efficiently develop recovery activities of life products, it requires the implementation of logistics systems able to put in the hands of companies and governments to organize from the collection of disused products, so implement the best option either reuse, recycling or remanufacturing total or partial freight service. We define a classification of systems RL in response to this function who develops and presents the most relevant characteristics of each, carriers can support organizations in this classification to determine the most appropriate to their needs, depending the characteristics of local society, the type of product transported, the production process in the area, the market is addressed or of the possibilities of economic recovery, taking into account than only in the United States, RL represents about 4% of the total costs of a company and 0.5% of gross national product.
International Journal of Physical Distribution & Logistics Management
Claudia Turkson
IRJET Journal
Procedia Manufacturing
Maria João Félix
Snehal Khaire , Rajesh Singh
In recent years, reverse logistics (RL) has become a field of importance for all organizations due to growing environmental concerns, legislation, corporate social responsibility and sustainable competitiveness. RL refers to the sequence of activities required to collect the used product from the customers for the purpose of either reuse or repair or re-manufacture or recycle or dispose of it. Perusal of the literature shows that research in the field of RL is in evolving phase and issues pertaining to adoption and implementation, forecasting product returns, outsourcing, RL networks from secondary market perspective, and disposition decisions have not been reviewed extensively. This study attempts to fill the existing gap through literature review on these issues, and outline the future directions for research based on research gap analysis. Total 242 published articles were selected, categorized, analyzed, and gaps in literature were identified to suggest for future research opportunities. The review may be useful for academicians, researchers and practitioners for better understanding of RL and guidance for future research.
Reviews In Environmental Science And Bio/technology
Patrick Beullens
Festus Olorunniwo
RELATED TOPICS
- We're Hiring!
- Help Center
- Find new research papers in:
- Health Sciences
- Earth Sciences
- Cognitive Science
- Mathematics
- Computer Science
- Academia ©2024
Reverse Logistics: Explained, Implemented, & Optimized

Scott Riddle
February 14, 2024
[show_reviewed_by_link]
Darren DeMatas
The ecommerce landscape is rapidly evolving, driven by changing consumer demands and market dynamics. Within this fast-paced environment, the efficiency of supply chains becomes a critical factor for success. An often overlooked yet vital component of these supply chains is reverse logistics. This aspect significantly affects a business’s operational flexibility, cost-effectiveness, environmental sustainability, and customer satisfaction .
What is Reverse Logistics?
Reverse logistics is a critical yet often understated aspect of supply chain management, dealing with the return journey of products from the customer to the seller or manufacturer. This process involves reversing the traditional supply chain flow, where goods move from their final destination back to their point of origin for various reasons such as return , repair , recycling , or disposal .
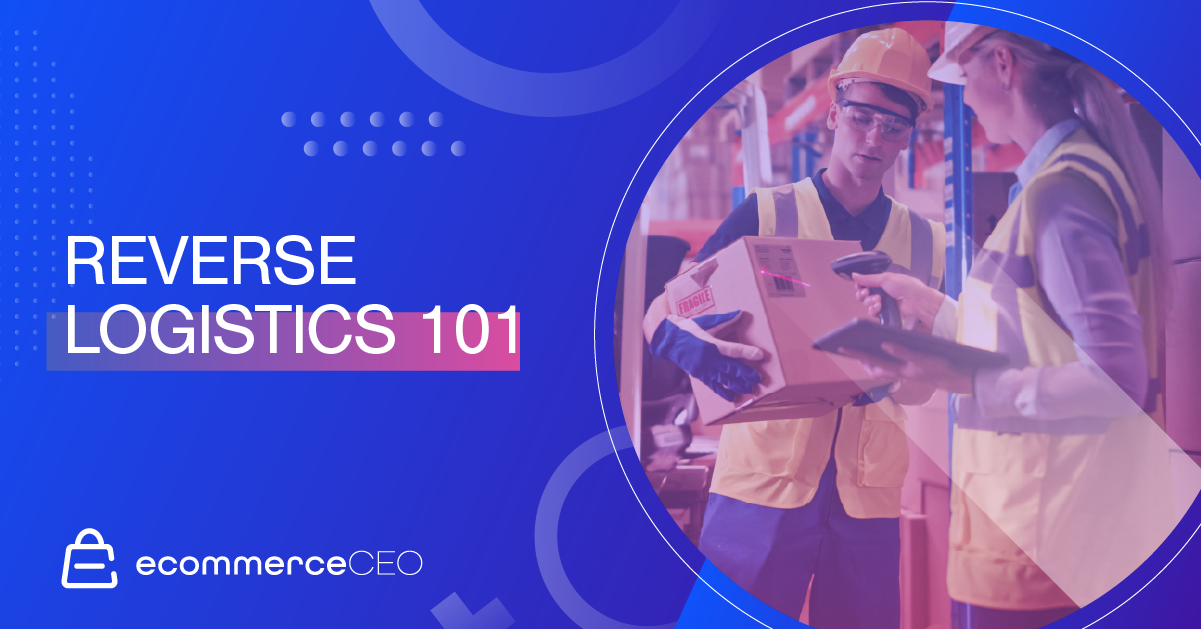
The complexity of reverse logistics arises from its multifaceted nature. It’s not merely about ferrying returned goods from point A to B. Encompassing a wide array of activities, it’s a spectrum that extends to inspecting the items, restocking them, processing refunds, dealing with waste management, and much more. This rich tapestry of operations forms the backbone of what we call the reverse supply chain.
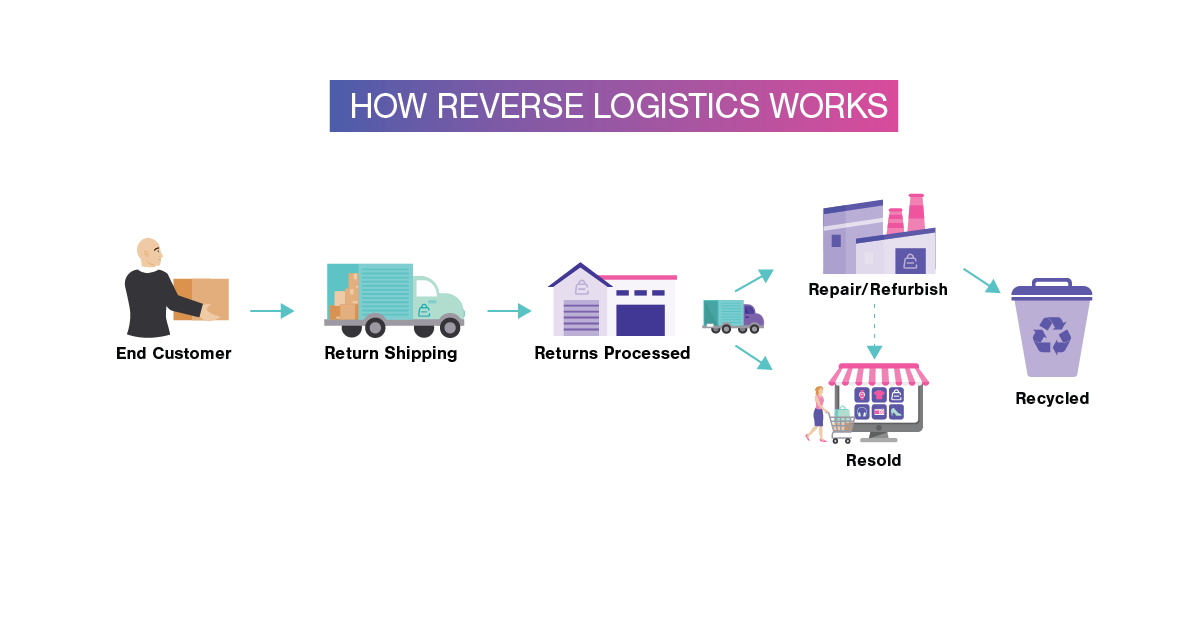
From the moment a customer decides to return a product, the reverse supply chain kicks into action. Rather than a linear path, it’s a web of interconnected processes designed to handle returns efficiently . The goal is to optimize recovery value or ensure proper disposal. Reverse logistics encompasses a wide range of activities:
Return Management:
This includes handling customer returns due to dissatisfaction, defects, or delivery errors. Effective return management requires a seamless process that ensures customer convenience while maintaining cost efficiency for the company. In order to optimize reverse logistics, companies must prioritize efficient repackaging strategies that allow for the swift handling, sorting, sorting, and refurbishment of returned products.
As part of reverse logistics, the returns management process is essential for retailers and manufacturers. It is centered around the concept of asset recovery, seeking to regain the maximum value from returned, overstocked, or unused products to increase revenue. Precise execution of this process can significantly improve your bottom line, turning potential losses into profits.
As a retailer, you may need to send products back to different manufacturers for repair or even get your money back.
Repair and Refurbishment:
Products that are returned due to defects or damage often undergo repair or refurbishment . This process involves assessing the item’s condition, performing necessary repairs, and restoring it to a sellable state, if possible.
Reverse logistics looks to reintroduce these revamped products back into the market through redistribution. After repairing, refurbishing , remanufacturing, or reconditioning, your products are ready for a market comeback. It’s now up to you to reappraise their value, propose a competitive price, and navigate them back to the sales window quickly and efficiently. This process of distributing products back into the marketplace is crucial in making the most out of your returned goods.
Recycling and Waste Management:
A significant aspect of reverse logistics is addressing products that are unsellable. Here, the principle of reusing comes into play, where recyclable materials are optimally harvested and subsequently reused, contributing to the economy. This process leverages trucks for transportation across cities and ensures that landfills are responsibly managed by minimizing waste disposal, thereby promoting environmental sustainability.
Inventory Management:
Managing the returned products as inventory is another crucial aspect. This involves tracking items, assessing their condition, and determining the most appropriate subsequent action, whether it’s resale, recycling, or disposal.
In the realm of ecommerce, the role and importance of reverse logistics in the supply chain are magnified. The online shopping model inherently leads to a higher volume of returns compared to traditional retail. Reasons include customers’ inability to physically inspect products before purchase, product appearance or function variations from online descriptions, and the ease of return policies offered by ecommerce platforms.
The Importance of Focusing on Reverse Logistics
Emphasizing reverse logistics is crucial for businesses in the digital marketplace, as it impacts several key areas of operations, each contributing significantly to overall success.
Whether a retailer or manufacturer navigating customer returns or a company managing end-of-life products, understanding and strategically implementing reverse logistics can unlock many benefits.
Enhancing Operational Efficiency
Effective reverse logistics goes beyond mere cost savings; it’s about enhancing overall operational efficiency . By refining the process of handling returns, businesses can streamline workflows , reduce bottlenecks , and optimize resource allocation . This efficiency not only cuts down on unnecessary expenditures but also speeds up the return-to-market of refurbished goods , maximizing asset utilization .
Driving Sustainable Practices
The focus on reverse logistics is increasingly intertwined with sustainability goals. Effective management of this aspect ensures the responsible handling of product lifecycles, from returns to final disposal. By implementing sustainable practices in reverse logistics, companies not only contribute to environmental conservation but also align with the growing consumer preference for eco-friendly businesses. This approach includes minimizing waste through innovative recycling programs and finding new ways to repurpose returned goods .
Bolstering Customer Relations
In the realm of ecommerce, the ease and flexibility of the return process are often as important as the initial purchase experience. A customer-centric approach in reverse logistics—characterized by clear communication, convenient return policies, and responsive service—can significantly enhance customer satisfaction. This focus helps in building a positive reputation, long-term relationships with customers, encouraging repeat business, and positive word-of-mouth.
Providing Strategic Business Insights
Reverse logistics is a rich source of data that can offer valuable business insights . Analyzing trends in returns and customer feedback can highlight areas for product improvement , reveal insights about customer preferences , and inform strategic decisions . This information is vital for adapting product offerings, refining marketing strategies, and enhancing overall business operations.
Readiness for Market Shifts and Regulatory Compliance
A robust reverse logistics strategy positions businesses to better adapt to market shifts and regulatory changes. As consumer habits evolve and regulations around sustainability and waste management become more stringent, a well-structured reverse logistics process ensures businesses remain agile and compliant.
Long-term Financial Health
While initially focused on immediate cost reductions, the long-term financial health of a business greatly benefits from an effective reverse logistics strategy. Companies can improve their financial resilience and profitability by reducing losses associated with returns, extending the life of products through refurbishment, and capitalizing on recycling opportunities.
Prioritizing reverse logistics is not just about managing returns but encompasses a broader strategy that touches upon operational efficiency, environmental responsibility, customer satisfaction, business intelligence, regulatory readiness, and financial stability . It’s an integral part of modern business practices, especially in the ecommerce sector, where its impact is even more pronounced.
The Impact of Ecommerce on Reverse Logistics
The growth of ecommerce has substantially altered consumer purchasing behaviors, leading to an increase in product returns. This shift has necessitated a reevaluation of reverse logistics strategies, elevating this function from a logistical afterthought to a key element of customer service. Today, businesses face the challenge of efficiently managing high volumes of returns while controlling logistics costs and maintaining positive customer experiences. In response, many ecommerce companies have adopted more flexible return policies and invested in advanced technologies to automate and streamline return processes.
Examples of Reverse Logistics
The classic example of reverse logistics is when a car manufacturer recalls a line of cars due to safety concerns. The process of retrieving these vehicles and returning them to the manufacturer is an excellent example of reverse logistics at work in the industry. Your business must be equipped to handle a product recall.
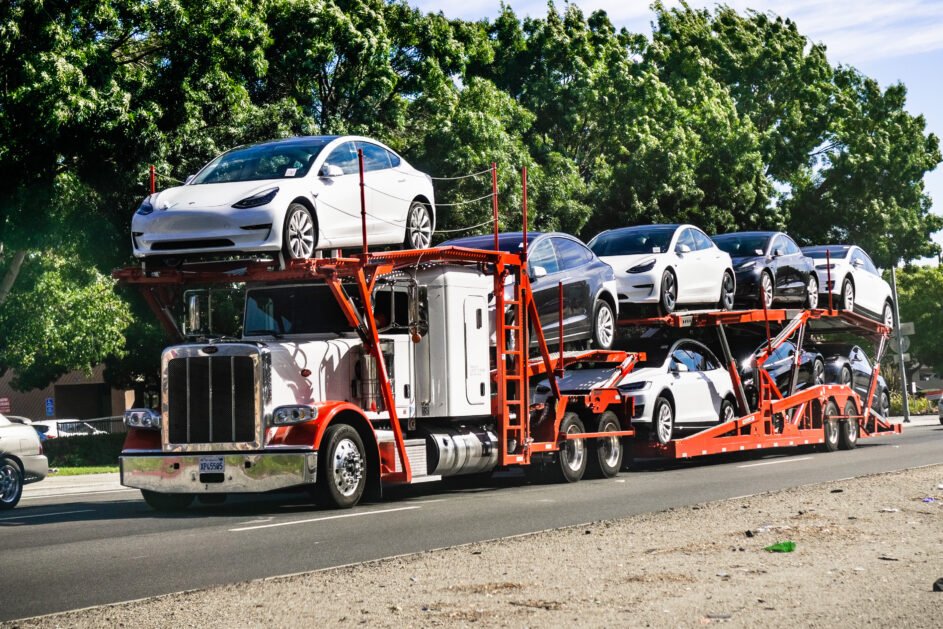
Imagine you’re the owner of a clothing company. A customer wants to return a dress that didn’t fit. This is a typical example of reverse logistics – your company needs to arrange the transportation of the dress back from the customer, inspect and restock the item, or discard it accordingly. This process not only involves logistics but also customer services and quality control .
Another representative example is seen in the electronics industry. Consider you’ve purchased a new smartphone, and after a few weeks, it starts malfunctioning. Under the warranty’s terms, you return the device to the manufacturer. Here, reverse logistics come into play – this involves handling the return shipment , tracking the returned product, evaluating its condition, providing a replacement or refund to the customer, and possibly refurbishing or recycling the defective device.
A less well-known but equally valuable example involves recycling initiatives. Suppose you are part of a city council that sets up a recycling program where the residents can return used batteries for safe disposal. These batteries’ collection, transportation, and disposal represent an instance of reverse logistics. Such initiatives help promote environmental sustainability while addressing hazardous materials appropriately.
Technology’s Crucial Role in Enhancing Reverse Logistics
Let’s dive right into how technology plays a pivotal role in enhancing reverse logistics. As you may know, reverse logistics can be a complex and challenging process. It involves handling returned products, processing refunds, dealing with customer complaints, and reallocating resources. But here’s the good news. Thanks to technology, companies can now streamline these procedures and pave the way for efficiency and customer satisfaction.
Technology now takes center stage in managing reverse logistics, from shipping software to automated return systems. Let’s take a closer look at these pivotal technological advancements.
Return Management Systems
Return management systems , often called RMA (Return Merchandise Authorization) systems, play a key role in systematically processing returns. Tracking, handling, and analyzing returns has never been easier with this technology. More importantly, RMA systems can give emotionally charged situations – like returns – a sorted, hassle-free approach, thereby enhancing customer satisfaction.
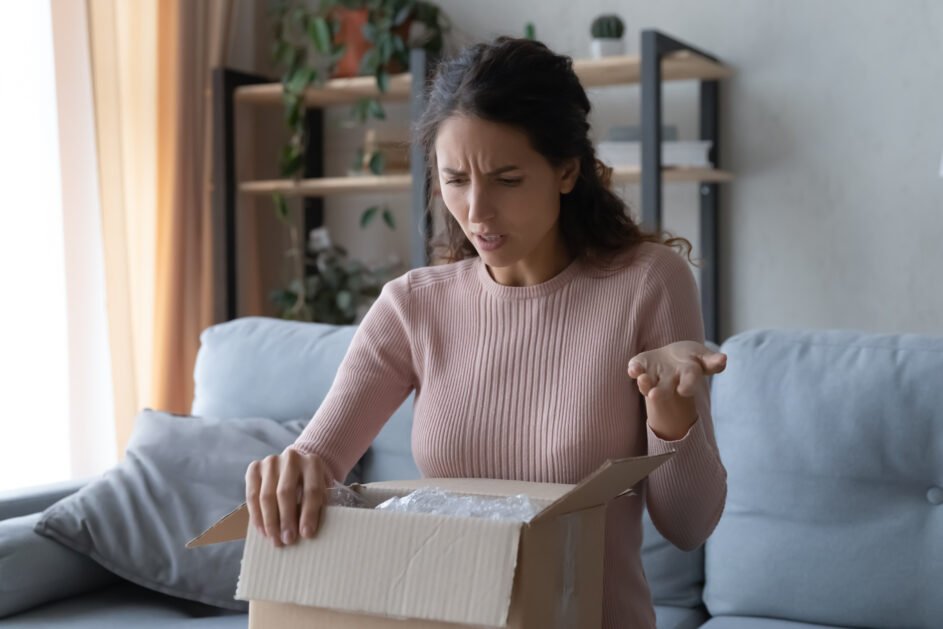
Warehouse Management Systems (WMS)
Remember the times when returns would come in, creating chaos in warehouses? Well, those days are long gone. Using Warehouse Management Systems (WMS), companies can now handle returns with ease, allocating resources, managing stocks, and processing returns efficiently.
Real-time Tracking
Real-time tracking empowers not just the sellers but the customers as well. Customers can have full visibility of their returns process right from filing a return to processing a refund, adding an extra layer of transparency to the whole process. On the business front, this enables businesses to make well-informed, strategic decisions based on real-time data.
To sum it up, technology has indeed revolutionized reverse logistics. It’s all about efficiency and effectiveness, ensuring a smooth, hassle-free return process for both the customer and the company to maximize revenue. Navigating the complex maze of return logistics just got a lot easier, thanks to the wonders of technology.
AI and Automation
As you delve deeper into the technological aspects of reverse logistics, you can’t overlook the revolutionary roles of Artificial Intelligence (AI) and automation. These are not just buzzwords but key driving forces in the effective operation of reverse logistics. AI and automation help businesses streamline their returns process, maximize efficiency, and minimize human error.
This is achievable by automating return authorization and processing, improving warehouse management and transportation, and reducing unnecessary costs. Conversely, AI uses machine learning techniques to effectively analyze return patterns, customer behaviors, and product life cycles, helping companies make informed decisions on reselling, refurbishing, recycling, or discarding returned products. Moreover, predictive analytics enabled by AI can provide valuable insight suggesting specific actions to prevent potential product returns and improve customer satisfaction.
With clear advantages of incorporating AI and automation into reverse logistics, businesses are equipped with robust tools making them more responsive and agile in the complex and competitive marketplace. So remember, embracing AI and automation is not just an option, it’s a strategic move to stay ahead in the game. For more in-depth insights into AI and automation in reverse logistics, you can refer to this research article, “AI and Automation in Reverse Logistics” .
Strategies for Reverse Logistics Optimization
Optimizing your reverse logistics can make a monumental difference in your business operations, improving customer service, reducing costs, and increasing overall efficiency. But to unlock these benefits, you’ll need to implement some strategic steps. Here are some best practices you could consider:
- Clear return policy: Good communication is the essence of smooth reverse logistics. Make your return policies as clear and straightforward as possible. Provide detailed procedures on how customers can return their purchases to minimize confusion and improve the return process.
- Efficient return process: Time is of the essence in reverse logistics. The more efficient your return processes are, the quicker items can be restocked or disposed of, reducing inventory costs. Consider using technology like automation and real-time tracking to increase efficiency.
- Product Life-cycle Management: Understanding the lifecycle of your products can significantly impact your reverse logistics. By being aware of each product’s lifecycle, you can anticipate returns and prepare appropriately to manage the returned inventory.
- Examine and act on customer behavior: Use data analytics to understand why customers are returning items. This information can help reduce return rates in the future by addressing common issues, such as product quality or misleading product descriptions. This can have a huge impact on long-term customer retention.
- Partner with expert third-party logistics (3PL) providers : Collaborating with experienced 3PL providers can help optimize your reverse logistics. These companies have the expertise and resources to handle large-scale and complex reverse logistics operations.
Beyond these strategies, it’s critical always to improve, test, and iterate your reverse logistics over time. Remember, a successful reverse logistics strategy isn’t a set-it-and-forget-it process; it’s a continually evolving system that should adapt based on ongoing developments and the changing needs of your business and customers.
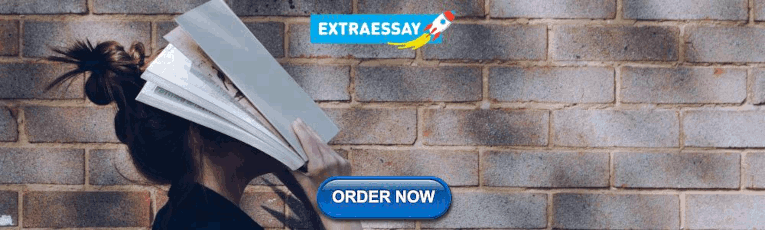
Choosing a Reverse Logistics Partner: Key Considerations
When navigating the complexities of reverse logistics, choosing the right partner is a crucial decision. Several key factors must be considered:
Technology and Innovation
A competent reverse logistics partner should utilize cutting-edge technology to enhance the return process. This includes the adoption of real-time tracking systems , the use of AI for predictive analytics , and the integration of automation technologies to improve efficiency. This tech-driven approach reduces errors and provides actionable insights through data analysis , which is essential for informed decision-making and strategic planning.
Sustainability Practices
The environmental impact of reverse logistics is increasingly a concern for businesses and consumers alike. It’s vital to partner with organizations that are committed to environmental sustainability. This includes employing sustainable packaging solutions , optimizing logistics routes to reduce carbon emissions , and engaging in product recycling and reuse initiatives .
Customer Experience Focus
The way a partner handles customer experience is another crucial factor. This includes having clear and straightforward return policies, a user-friendly return process, and a responsive customer support system . Providing an effortless and transparent return experience can significantly boost customer satisfaction and loyalty, reinforcing a positive brand image.
Reinventing Your Supply Chain with Reverse Logistics
In the dynamic world of eCommerce, the efficiency of reverse logistics is just as crucial as the direct shipping process. Understanding this, ShipNetwork includes reverse logistics in its array of logistics solutions, aiming to streamline the return process for eCommerce businesses.
This holistic approach plays a pivotal role in enhancing customer satisfaction and optimizing operational efficiency. Effectively managing returns is key to fostering customer loyalty and growth, and ShipNetwork’s inclusion of reverse logistics in its services underlines its commitment to offering comprehensive support for eCommerce businesses.
Reverse logistics is an indispensable component of the ecommerce ecosystem, playing a crucial role in maintaining operational efficiency, reducing costs, and enhancing customer satisfaction. In an era marked by rapidly changing consumer expectations and intense market competition, the effective management of reverse logistics is not just an operational need but a strategic imperative .
By focusing on this critical aspect and partnering with the right logistics providers , companies can ensure enhanced efficiency, sustainability, and customer loyalty, solidifying their position in the dynamic world of ecommerce.
Featured on
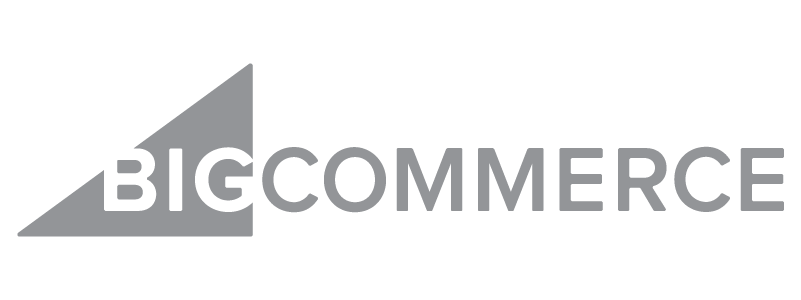
Join 30K+ entrepreneurs already learning ecommerce.
Ecommerce ceo.
Partner With Us
Editorial Policy
Review Guidelines
Terms Of Use
Affiliate Disclosure
Privacy Policy
Guides & Resources
Ecommerce Learning Center
How To Start An Ecommerce Business
How To Make Money Online
What To Sell Online
How To Sell On Amazon
Online Business Ideas
Best Ecommerce Tools
Ecommerce Platforms
Fulfillment Services
Shipping Software
Inventory Management
Print On Demand
Dropshipping Companies
Amazon Research
Online Course Platforms
POS Systems
3PL Companies
BigCommerce
Shopify vs BigCommerce
2800 N 6th Street #5156 St. Augustine, FL 32084 United States
(904) 458-7077
Copyright © 2024 - Mission Demand LLC . All rights reserved.
Exclusive Member of Mediavine Finance
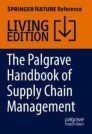
The Palgrave Handbook of Supply Chain Management pp 1–28 Cite as
Reverse Logistics Within the Supply Chain
- Marilyn Helms 2 &
- Aref Hervani 2
- Living reference work entry
- Latest version View entry history
- First Online: 14 November 2023
28 Accesses
While much emphasis is on the procurement of raw materials, manufacturing of products, storage, and delivery to the end user in the forward supply chain, the backward or reverse logistics process of the supply chain is of growing strategic and environmental importance. Examples of reverse logistics are included in this chapter along with examples of reusing products and remanufacturing wastes, recycling, reclamation, refurbishing, restocking, and even repurposing and upcycling products. All processes reduce landfill waste and can decrease manufacturing needs, conserving scarce resources, and reduce emissions and organizations’ carbon footprints. Partners in the reverse logistic process include collection and consolidation centers and recover facilities. Managing reverse logistics are critical functions of modern supply chain management. With an increasing interest in the environmental impact of organizational activities, this chapter presents the need to integrate reverse logistics supply chain activities into organizations and the circular economy for social sustainability.
- Reverse logistics
- Green supply chain
- Social sustainability
- Environmental impact
- Reclamation
- Scarce resources
- Carbon footprint
- Circular economy
- Green logistics
- Supply chain
This is a preview of subscription content, log in via an institution .
Agarwal, V., Govindan, K., Darbari, J. D., & Jha, P. C. (2016a). An optimization model for sustainable solutions towards implementation of reverse logistics under collaborative framework. International Journal of System Assurance Engineering and Management, 7 , 480–487.
Google Scholar
Agarwal, S., Singh, R. K., & Murtaza, Q. (2016b). A literature review and perspectives in reverse logistics. Resources, Conservation and Recycling, 97 , 76–92.
Agarwal, S., Singh, R. K., & Murtaza, Q. (2016c). Triple bottom line performance evaluation of reverse logistics. Competitiveness Review .
Al Majzoub, M., & Davidavičienė, V. (2019, May). Comparative analysis of reverse e-logistics’ solution in Asia and Europe. In International scientific conference on contemporary issues in business, management and education, proceedings . https://doi.org/10.3846/cibmee
Chapter Google Scholar
Al-Shihmani, W. I. M., Ali Agha, M. S., & Masood, T. (2022, July). Reverse supply chains in Industry 4.0. In 29th International European Operations Management Association Annual Conference . Reverse supply chains in Industry 4.0 – Strathprints.
Bekrar, A., Ait El Cadi, A., Todosijevic, R., & Sarkis, J. (2021). Digitalizing the closing-of-the-loop for supply chains: A transportation and blockchain perspective. Sustainability, 13 , 2895. https://doi.org/ . https://doi.org/10.3390/su13052895
Article Google Scholar
Bottani, E., Montanari, R., & Rinaldi, M. (2019). Simulation and performance improvement of a reverse logistics system for waste electrical and electronic equipment: a case study in Italy. International Journal of Simulation and Process Modelling, 14 (3), 308–323.
Centobelli, P., Cerchione, R., & Esposito, E. (2020a). Evaluating environmental sustainability strategies in freight transport and logistics industry. Business Strategy and the Environment, 29 (3), 1563–1574.
Centobelli, P., Cerchione, R., & Esposito, E. (2020b). Pursuing supply chain sustainable development goals through the adoption of green practices and enabling technologies: A cross-country analysis of LSPs. Technological Forecasting and Social Change, 153 , 119920.
Chen, D., Ignatius, J., Sun, D., Zhan, S., Zhou, C., Marra, M., & Demirbag, M. (2019). Reverse logistics pricing strategy for a green supply chain: A view of customers’ environmental awareness. International Journal of Production Economics, 217 , 197–210.
Chen, Z. S., Zhang, X., Govindan, K., Wang, X. J., & Chin, K. S. (2021). Third-party reverse logistics provider selection: A computational semantic analysis-based multi-perspective multi-attribute decision-making approach. Expert Systems with Applications, 166 , 114051.
Chileshe, N., Rameezdeen, R., Hosseini, M. R., Martek, I., Li, H. X., & Panjehbashi-Aghdam, P. (2018). Factors driving the implementation of reverse logistics: A quantified model for the construction industry. Waste Management, 79 , 48–57.
Choi, Y., & Mai, D. Q. (2018). The sustainable role of the e-trust in the B2C e-commerce of Vietnam. Sustainability, 10 (1), 291. https://doi.org/10.3390/su10010291
Davidavičienė, V., & Al Majzoub, M. (2021). Performance of reverse logistics in electronic commerce: A case study from Lebanon and Syria. Transport, 36 (3), 260–282. https://doi.org/10.3846/transport.2021.14956
De Clercq, D., Thongpapanl, N., & Voronov, M. (2018). Sustainability in the face of institutional adversity: market turbulence, network embeddedness, and innovative orientation. Journal of Business Ethics, 148 (2), 437–455.
do Prado, G. F., Piekarski, C. M., da Luz, L. M., de Souza, J. T., Salvador, R., & de Francisco, A. C. (2020). Sustainable development and economic performance: Gaps and trends for future research. Sustainable Development, 28 (1), 368–384.
Eketu, C. A. (2018). Perspectives on human nature and implications for research in the behavioural sciences. International Journal of Emerging Trends in Social Sciences, 4 (1), 42–46.
Ellsworth-Krebs, K., Rampen, C., Rogers, E., Dudley, L., & Wishart, L. (2022). Circular economy infrastructure: Why we need track and trace for reusable packaging. Sustainable Production and Consumption, 29 , 249–258., ISSN 2352–5509. https://doi.org/10.1016/j.spc.2021.10.007
Eren, E., & Tuzkaya, U. R. (2019). Occupational health and safety-oriented medical waste management: A case study of Istanbul. Waste Management & Research, 37 (9), 876–884.
Euchi, J., Bouzidi, D., & Bouzid, Z. (2019). Structural analysis of acute success factors of performance of reverse logistics relative to customer satisfaction. International Journal of Combinatorial Optimization Problems and Informatics, 10 (2), 39.
Fan, H., Liu, H., Liu, P., & Ren, X. (2020). Optimization of the simultaneous distribution and collection path of irregular vehicles with fuzzy collection demand [J/OL]. Control Theory and Application , vol. 1–14, 2020.
Farooq, O., Farooq, M., & Reynaud, E. (2019). Does employees’ participation in decision making increase the level of corporate social and environmental sustainability? An investigation in South Asia. Sustainability, 11 (2), 511.
González-Sánchez, R., Settembre-Blundo, D., Ferrari, A. M., & García-Muiña, F. E. (2020). Main dimensions in the building of the circular supply chain: A literature review. Sustainability, 12 (6), 2459.
Guo, Y., Yu, J., Allaoui, H., & Choudhary, A. (2022). Lateral collaboration with cost-sharing in sustainable supply chain optimization: A combinatorial framework. Transportation, 157 , 102593.
Hammes, G., De Souza, E. D., Rodriguez, C. M. T., Millan, R. H. R., & Herazo, J. C. M. (2020). Evaluation of the reverse logistics performance in civil construction. Journal of Cleaner Production, 248 , 119212.
Han, H., & Trimi, S. (2018). A fuzzy TOPSIS method for performance evaluation of reverse logistics in social commerce platforms. Expert Systems with Applications, 103 , 133–145.
Hansen, Z. N. L., Larsen, S. B., Nielsen, A. P., Groth, A., Gregersen, N. G., & Ghosh, A. (2018). Combining or separating forward and reverse logistics . The International Journal of Logistics Management (Vol. 29, p. 216).
He, L. (2021). Design of the reverse logistics network of new energy vehicle waste power batteries. In E3S web of conferences (Vol. 275, p. 02019). EDP Sciences.
He, Z. G., Li, Q., & Fang, J. (2016). The solutions and recommendations for logistics problems in the collection of medical waste in China. Procedia Environmental Sciences, 31 , 447–456.
Hervani, A., & Helms, M. (2006). Chapter 7: Reverse logistics for recycling: Challenges facing the carpet industry. In J. Sarkis (Ed.), Greening the supply chain (pp. 117–135). Springer-Verlag London Limited Publishing.
Jiang, J., Zhang, D., Li, S., & Liu, Y. (2019). Multimodal green logistics network design of urban agglomeration with stochastic demand. Journal of Advanced Transportation, 2019 , 4165942.
Joshi, S. (2022). A review on sustainable supply chain network design: Dimensions, paradigms, concepts, framework and future directions . Sustainable Operations and Computers (Vol. 3, p. 136).
Ka, J. M. R., Ab, N. R., & Lb, K. (2019). A review on supply chain performance measurement systems. Procedia Manuf, 30 , 40–47.
Kargar, S., Pourmehdi, M., & Paydar, M. M. (2020). Reverse logistics network design for medical waste management in the epidemic outbreak of the novel coronavirus (COVID-19). Science of the Total Environment, 746 , 141183.
Kashveenjit, K. (2021). Business intelligence on supply chain responsiveness and agile performance: empirical evidence from Malaysian logistics industry. International Journal of Supply Chain Management, 6 (2), 31–63.
Khan, S. A. R., Yu, Z., Belhadi, A., & Mardani, A. (2020). Investigating the effects of renewable energy on international trade and environmental quality. Journal of Environmental Management, 272 , 111089, ISSN 0301-4797. https://doi.org/10.1016/j.jenvman.2020.111089
Kilic, H. S., Cebeci, U., & Ayhan, M. B. (2015). Reverse logistics system design for the waste of electrical and electronic equipment (WEEE) in Turkey. Resources, Conservation and Recycling, 95 , 120–132.
Kopnina, H. (2018). Circular economy and Cradle to Cradle in educational practice. Journal of Integrative Environmental Sciences, 15 (1), 119–134.
Krikke, H. (2020). Value creation in a circular economy: an interdisciplinary approach. In Decent work and economic growth (pp. 1–15). Springer Nature.
Kubasakova, I., & Kubanova, J. (2021). The comparison of implementation items of reverse logistics in terms of chosen companies in Europe and Slovakia. Transportation Research Procedia, 53 , 167–173.
Lambrechts, W. (2021). Ethical and sustainable sourcing: Toward strategic and holistic sustainable supply chain management. In W. L. Filho, A. M. Azul, L. Brandli, A. L. Salvia, & T. Wall (Eds.), Encyclopedia of the UN sustainable development goals. Decent work and economic growth (Encyclopedia of the UN sustainable development goals) (pp. 402–414). Springer Nature Switzerland AG. https://doi.org/10.1007/978-3-319-71058-7_11-1
Li, Z., Wang, W. M., Liu, G., Liu, L., He, J., & Huang, G. Q. (2018). Toward open manufacturing: A cross-enterprises knowledge and services exchange framework based on blockchain and edge computing. Industrial Management & Data Systems., 118 , 303.
Li, G., Du, S., Huang, D., Zhao, C., & Deng, Y. (2019). Dynamics modeling-based optimization of process parameters in face milling of workpieces with discontinuous surfaces. Journal of Manufacturing Science and Engineering, 141 (10), 84–99.
Liu, A., Ji, X., Lu, H., & Liu, H. (2019). The selection of 3PRLs on self-service mobile recycling machine: Interval-valued Pythagorean hesitant fuzzy best-worst multi-criteria group decision-making. Journal of Cleaner Production, 230 , 734–750.
Lu, Y. (2019). The blockchain: State-of-the-art and research challenges. Journal of Industrial Information Integration, 15 , 80–90.
Mahindroo, A., Samalia, H. V., & Verma, P. (2018). Moderated influence of return frequency and resource commitment on information systems and reverse logistics strategic performance. International Journal of Productivity and Performance Management, 67 , 550.
Majzoub, M. A., Davidavičienė, V., & Meidute-Kavaliauskiene, I. (2020). Measuring the impact of factors affecting reverse e-logistics’ performance in the electronic industry in Lebanon and Syria. Independent Journal of Management & Production, 11 (6), 1969–1990.
Makarova, I., Shubenkova, K., Buyvol, P., Shepelev, V., & Gritsenko, A. (2021). The role of reverse logistics in the transition to a circular economy: Case study of automotive spare parts logistics. FME Transactions, 49 (1), 173–185.
Martínez-Martínez, A., Cegarra-Navarro, J. G., Garcia-Perez, A., & Wensley, A. (2019). Knowledge agents as drivers of environmental sustainability and business performance in the hospitality sector. Tourism Management, 70 , 381–389.
Meherishi, L., Narayana, S. A., & Ranjani, K. S. (2019). Sustainable packaging for supply chain management in the circular economy: A review. Journal of Cleaner Production, 237 , 117582.
Mehmood, T., Asim, M., & Manzoor, M. (2021). The relationship between green supply chain and logistics practices performance. Electronic Research Journal of Behavioral Sciences, 4 . ISSN: 2652-7782. http://erjbehaviouralsciences.com/
Melan, M. (2021). Reverse logistics from recycling of used paper boxes from online shopping in china: A literature review. Turkish Journal of Computer and Mathematics Education (TURCOMAT), 12 (3), 1543–1549.
Morgan, T. R., Tokman, M., Richey, R. G., & Defee, C. (2018). Resource commitment and sustainability: a reverse logistics performance process model . International Journal of Physical Distribution & Logistics Management (Vol. 48, p. 164).
Nisar, T. M., & Prabhakar, G. (2017). What factors determine e-satisfaction and consumer spending in e-commerce retailing? Journal of Retailing and Consumer Services, 39 , 135–144.
Pakhomova, N. V., Richter, K. K., & Vetrova, M. A. (2017). Transition to circular economy and closedloop supply chains as driver of sustainable development. St Petersburg University Journal of Economic Studies, 33 , 244–268.
Panigrahi, S. K., Kar, F. W., Fen, T. A., Hoe, L. K., & Wong, M. (2018). A strategic initiative for successful reverse logistics management in retail industry. Global Business Review, 19 (3_suppl)., S151–S175.
Paula, I. C., Campos, E. A. R., Pagani, R. N., Guarnieri, P., & Kaviani, M. A. (2019). Are collaboration and trust sources for innovation in the reverse logistics? Insights from a systematic literature review. Supply Chain Manag: An International Journal, 25 , 176–222. https://doi.org/10.1108/SCM-03-2018-0129
Pham, T. S. H., & Ahammad, M. F. (2017). Antecedents and consequences of online customer satisfaction: A holistic process perspective. Technological Forecasting and Social Change, 124 , 332–342.
Pieroni, M. P., McAloone, T. C., & Pigosso, D. C. (2021). Circular economy business model innovation: Sectorial patterns within manufacturing companies. Journal of Cleaner Production, 286 , 124921.
Pilkington, M. (2016). Blockchain technology: principles and applications. In Research handbook on digital transformations . Edward Elgar Publishing.
Pundhir, S. K. S., Gupta, A. K., & Kumar, S. (2020). Determining decision variables for manufacturer and retailer in the co-operative and non-cooperative environment: A game theory approach. International Journal of Supply and Operations Management, 7 (2), 129–138.
Rakhmangulov, A., Sladkowski, A., Osintsev, N., & Muravev, D. (2018). ZelenaLogistika: SustavMetodaiInstrumenata–2. Dio. Naše More, 65 , 49–55.
Ribeiro, D. P., De Oliveira, U. R., da Silva César, A., & Aprigliano Fernandes, V. (2021). Evaluation of medicine reverse logistics practices in hospitals. Sustainability, 13 (6), 3496.
Richnák, P., & Gubová, K. (2021). Green and reverse logistics in conditions of sustainable development in enterprises in Slovakia. Sustainability, 13 (2), 581. https://doi.org/10.3390/su13020581
Rubio, S., Chamorro, A., & Miranda, F. (2008). Characteristics of the research on reverse logistics (1995–2005). International Journal of Production Research, 46 (4), 1099–1120.
Santana, J. C. C., Guerhardt, F., Franzini, C. E., Ho, L. L., Júnior, S. E. R. R., Cânovas, G., et al. (2021). Refurbishing and recycling of cell phones as a sustainable process of reverse logistics: A case study in Brazil. Journal of Cleaner Production, 283 , 124585.
Sarkis, J., Helms, M. M., & Hervani, A.A. (2010) Reverse logistics and social sustainability. Corporate Social Responsibility and Environmental Management, 17 , 337–354.
Schöggl, J. P., Stumpf, L., & Baumgartner, R. J. (2020). The narrative of sustainability and circular economy-A longitudinal review of two decades of research. Resources, Conservation and Recycling, 163 , 105073.
Seroka-Stolka, O., & Ociepa-Kubicka, A. (2019). Green logistics and circular economy. Transportation Research Procedia, 39 , 471–479.
Shadkam, E. (2021). Cuckoo optimization algorithm in reverse logistics: A network design for COVID-19 waste management. International Journal of Computer-Aided Technologies, 2 , 1–9.
Sharma, N. K., Kumar, V., Verma, P., & Luthra, S. (2021). Sustainable reverse logistics practices and performance evaluation with fuzzy TOPSIS: A study on Indian retailers. Cleaner Logistics and Supply Chain, 1 , 100007.
Sirisawat, P., & Kiatcharoenpol, T. (2018). Fuzzy AHP-TOPSIS approaches to prioritizing solutions for reverse logistics barriers. Computers & Industrial Engineering, 117 , 303–318.
Sonego, M., Echeveste, M. E. S., & Debarba, H. G. (2022). Repair of electronic products: consumer practices and institutional initiatives. Sustainable Production and Consumption, 30 , 556.
Sousa-Zomer, T. T., Magalhães, L., Zancul, E., Campos, L. M., & Cauchick-Miguel, P. A. (2018). Cleaner production as an antecedent for circular economy paradigm shift at the micro-level: Evidence from a home appliance manufacturer. Journal of Cleaner Production, 185 , 740–748.
Tan, Y., & Guo, C. (2019). Research on two-way logistics operation with uncertain recycling quality in government multi-policy environment. Sustainability, 11 (3), 882.
Tosarkani, B. M., & Amin, S. H. (2018). A multi-objective model to configure an electronic reverse logistics network and third-party selection. Journal of Cleaner Production, 198 , 662–682.
Trivellas, P., Malindretos, G., & Reklitis, P. (2020). Implications of green logistics management on sustainable business and supply chain performance: Evidence from a survey in the Greek agri-food sector. Sustainability, 12 (24), 10515.
Vargas, M., Alfaro, M., Karstegl, N., Fuertes, G., Gracia, M. D., Mar-Ortiz, J., et al. (2021). Reverse logistics for solid waste from the construction industry. Advances in Civil Engineering, 2021 , 1.
Wang, D. F., Dong, Q. L., Peng, Z. M., Khan, S. A. R., & Tarasov, A. (2018). The green logistics impact on international trade: Evidence from developed and developing countries. Sustainability, 10 (7), 2235.
Wang, Z., Li, H., & Zhang, X. (2019). Construction waste recycling robot for nails and screws: Computer vision technology and neural network approach. Automation in Construction, 97 , 220–228.
Wang, B., Luo, W., Zhang, A., Tian, Z., & Li, Z. (2020). Blockchain-enabled circular supply chain management: A system architecture for fast fashion. Computers in Industry, 123 , 103324.
Weingarten, F., & Longoni, A. (2015). A nuanced view on supply chain integration: A coordinative and collaborative approach to operational and sustainability performance improvement. Supply Chain Management, 20 (2), 139.
Wijekoon, P., Koliyabandara, P. A., Cooray, A. T., Lam, S. S., Athapattu, B. C., & Vithanage, M. (2022). Progress and prospects in mitigation of landfill leachate pollution: Risk, pollution potential, treatment, and challenges. Journal of Hazardous Materials, 421 , 126627.
Xu, W., Chen, P.-K., & Ye, Y. (2020). Effective improvement in supply chain integration through a revised taxonomy. IEEE Engineering Management Review, 48 , 127–144.
Xue, D., Teunter, R. H., Zhu, S. X., & Zhou, W. (2021). Entering the high-end market by collecting and remanufacturing a competitor’s high-end cores. Omega, 99 , 102168.
Yu, H., & Solvang, W. D. (2016). A stochastic programming approach with improved multi-criteria scenario-based solution method for sustainable reverse logistics design of waste electrical and electronic equipment (WEEE). Sustainability, 8 (12), 1331.
Yu, H., Sun, X., Solvang, W. D., et al. (2020). Reverse logistics network design for effective management of medical waste in epidemic outbreaks: Insights from the coronavirus disease 2019 (COVID-19) outbreak in Wuhan (China). International Journal of Environmental Research and Public Health, 17 , 1770.
Yue, T., Sun, L., & Zhou, Y. (2020) Multi-model vehicle path optimization method considering the risk of dangerous goods transportation. Systems Engineering, 38 (1), 93–102.
Zarbakhshnia, N., Soleimani, H., Goh, M., & Razavi, S. S. (2019). A novel multi-objective model for green forward and reverse logistics network design. Journal of Cleaner Production, 208 , 1304–1316.
Zhang, K., He, F., Zhang, Z., Lin, X., & Li, M. (2020). Multi-vehicle routing problems with soft time windows: A multi-agent reinforcement learning approach. Transportation Research Part C: Emerging Technologies, 121 , 102861.
Zhang, X., Zou, B., Feng, Z., Wang, Y., & Yan, W. (2022). A review on remanufacturing reverse logistics network design and model optimization. PRO, 10 (1), 84.
Download references
Author information
Authors and affiliations.
Dalton State College C. Lamar and Ann Wright School of Business, Dalton, GA, USA
Marilyn Helms & Aref Hervani
You can also search for this author in PubMed Google Scholar
Corresponding author
Correspondence to Marilyn Helms .
Editor information
Editors and affiliations.
Business School, Worcester Polytechnic Institute, Worcester, MA, USA
Joseph Sarkis
Rights and permissions
Reprints and permissions
Copyright information
© 2024 The Author(s), under exclusive licence to Springer Nature Switzerland AG
About this entry
Cite this entry.
Helms, M., Hervani, A. (2024). Reverse Logistics Within the Supply Chain . In: Sarkis, J. (eds) The Palgrave Handbook of Supply Chain Management. Palgrave Macmillan, Cham. https://doi.org/10.1007/978-3-030-89822-9_44-2
Download citation
DOI : https://doi.org/10.1007/978-3-030-89822-9_44-2
Received : 22 August 2022
Accepted : 26 April 2023
Published : 14 November 2023
Publisher Name : Palgrave Macmillan, Cham
Print ISBN : 978-3-030-89822-9
Online ISBN : 978-3-030-89822-9
eBook Packages : Springer Reference Business and Management Reference Module Humanities and Social Sciences Reference Module Business, Economics and Social Sciences
- Publish with us
Policies and ethics
Chapter history
DOI: https://doi.org/10.1007/978-3-030-89822-9_44-2
DOI: https://doi.org/10.1007/978-3-030-89822-9_44-1
- Find a journal
- Track your research
To read this content please select one of the options below:
Please note you do not have access to teaching notes, reverse logistics in the electronic industry of china: a case study.
Supply Chain Management
ISSN : 1359-8546
Article publication date: 25 September 2009
The purpose of this paper is to report on research undertaken to investigate whether current reverse logistics theories and models can be totally applied in developing countries like China using the electronic industry as a case study.
Design/methodology/approach
A case study approach was adopted with information collected from company web sites, direct observation, and in‐depth interviews with four major consumer electronic product manufacturers in China. Findings were analyzed and compared across all the cases studied to determine the common external and internal drivers for reverse logistics implementation as well as the obstacles faced by the whole electronic industry. A comparison with the literature was made to identify the gaps between current theories and models and actual practices in China.
The findings suggest that while reverse logistics drivers vary from company to company, barriers to reverse logistics are common and are mainly external. The major difficulty in implementing reverse logistics in the electronic industry of China is the lack of enforceable laws, regulations or directives to motivate manufacturers. Furthermore, economic support and preferential tax policies are absent to help manufacturers offset the high investment costs of reverse logistics. Low public awareness of environmental protection and underdevelopment of recycling technologies are also some of the obstacles to widespread reverse logistics implementation. The findings also reveal the presence of linkages between the various external factors that are not fully explored in current reverse logistics models.
Research limitations/implications
The study corroborates the application of transaction cost economics and resource‐based view theory to account for the different approaches to reverse logistics adopted by firms in developing countries. It also reveals a need for further research on the linkages between external factors affecting reverse logistics implementation. The four case studies of large corporations are drawn from a Chinese setting in which implementation of reverse logistics is still in an early stage. The complex nature of China's transitional economy and political considerations may influence the perspectives and practices of small manufacturers in the management of environmental issues thus limiting the generalizability of the findings.
Practical implications
The study reveals the problems encountered in the implementation of reverse logistics in China and proposes measures to expedite the development.
Originality/value
This paper presents a systematic analysis of the external and the internal factors affecting reverse logistics implementation in developing countries like China. It reveals the need to investigate the linkages between the various external factors that are less explored in current reverse logistic theories and models. The study also identifies the major drivers and obstacles faced by the industry, a clear understanding of which might facilitate the formulation of appropriate nation‐wide reverse logistics policy and strategy through the support of the government and the investment of the manufacturers.
- Distribution management
- Electronics industry
- Outsourcing
- Case studies
- Developing countries
Hung Lau, K. and Wang, Y. (2009), "Reverse logistics in the electronic industry of China: a case study", Supply Chain Management , Vol. 14 No. 6, pp. 447-465. https://doi.org/10.1108/13598540910995228
Emerald Group Publishing Limited
Copyright © 2009, Emerald Group Publishing Limited
Related articles
We’re listening — tell us what you think, something didn’t work….
Report bugs here
All feedback is valuable
Please share your general feedback
Join us on our journey
Platform update page.
Visit emeraldpublishing.com/platformupdate to discover the latest news and updates
Questions & More Information
Answers to the most commonly asked questions here
IT Asset Management
Reverse logistics, tech services, case studies.
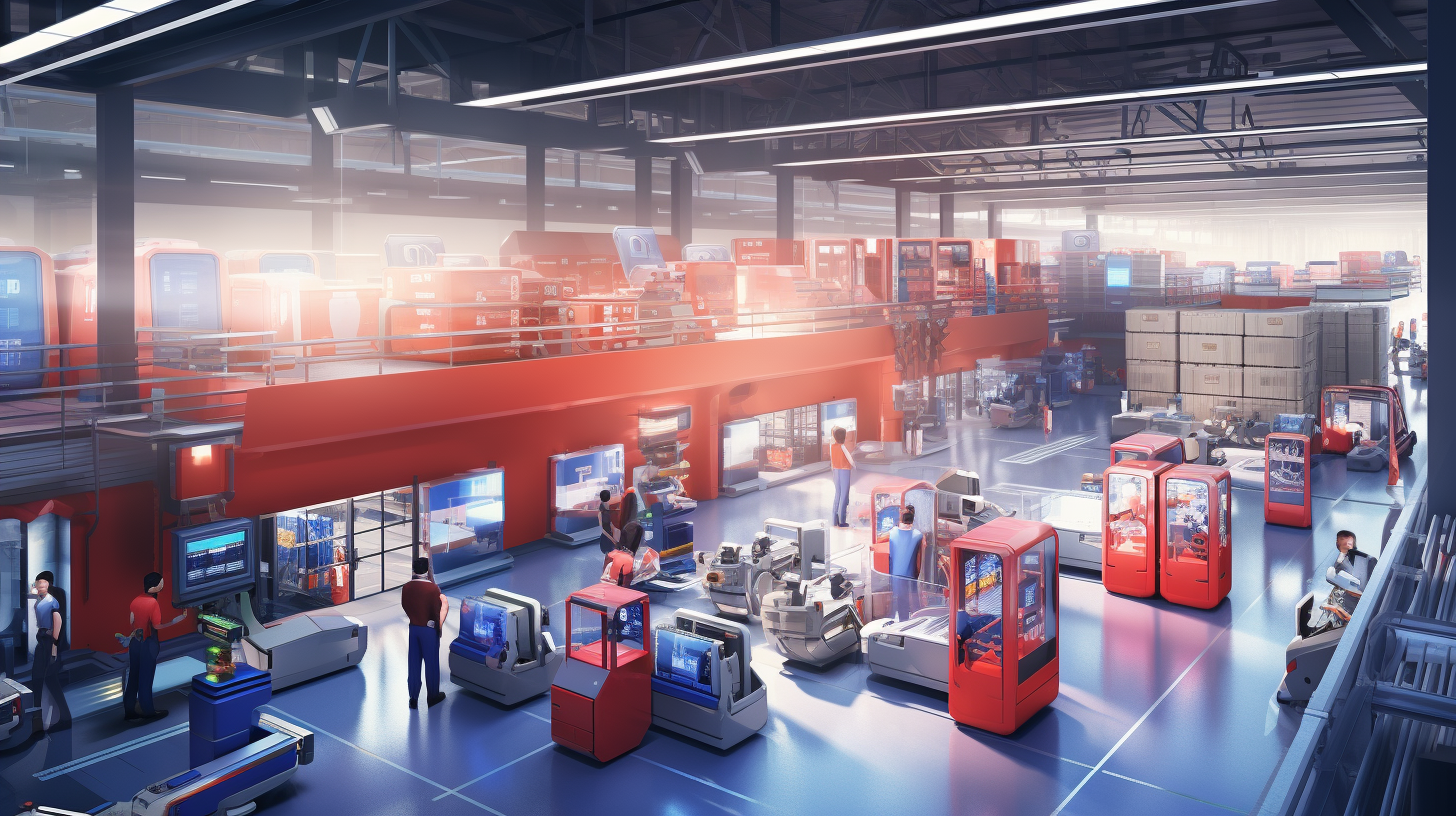
9 Best Practices In Reverse Logistics
Ditch the waste: discover the ideal it solution for your needs.
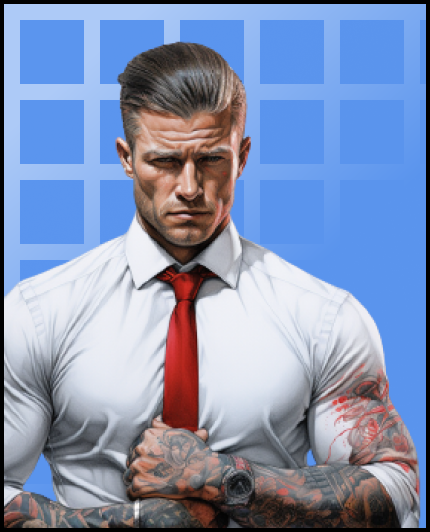
Welcome to our comprehensive guide on the "9 Best Practices in Reverse Logistics." In the fast-paced world of IT asset management, organizations face many challenges in efficiently handling product returns, optimizing inventory, and ensuring compliance with regulations. Whether you're a CIO, IT director, or asset manager, navigating these complexities effectively is crucial.
At UCS Logistics, we understand IT asset management's unique needs and challenges. This article delves into nine best practices to transform your IT asset management processes. From returns management to data analytics, supplier collaboration to recycling and disposal, these practices are the key to streamlining your operations, reducing costs, and enhancing sustainability.
Join us as we explore these practices in detail and discover how UCS Logistics can be your trusted partner on the journey to better IT asset management.
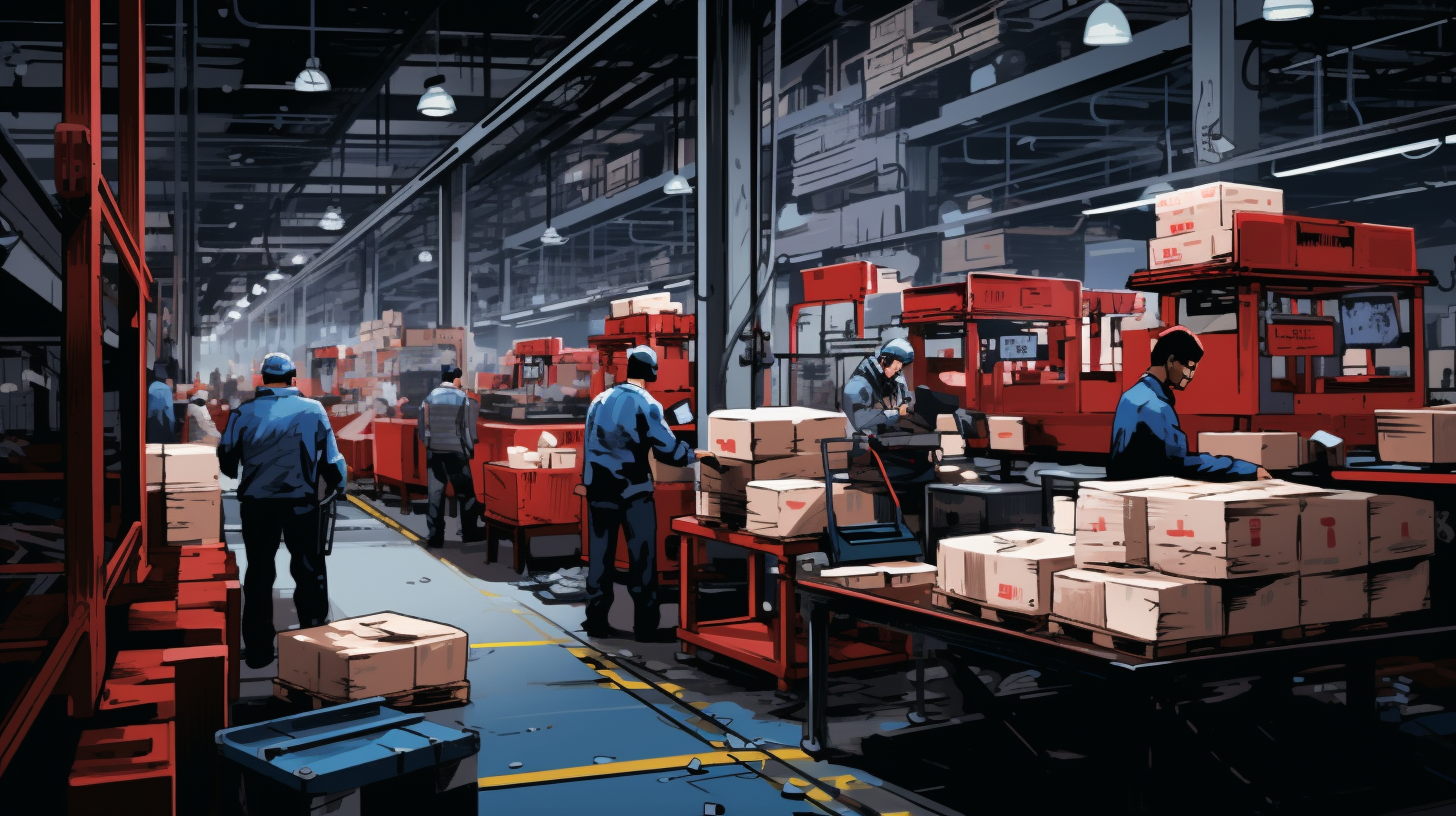
What Is Reverse Logistics?
Reverse logistics is a crucial aspect of supply chain management that deals with moving products and materials from their final destination back to the manufacturer or another designated location. It involves returning, remanufacturing, refurbishing, recycling, and disposing of products and materials.
Understanding the Importance of Reverse Logistics
Reverse logistics is pivotal in optimizing resource utilization and sustainability in various industries. It encompasses a range of activities aimed at reducing waste, recovering value from returned or used products, and minimizing the environmental impact of disposal.
Effective Returns Management
Effective returns management is a critical component of reverse logistics that focuses on efficiently handling product returns to minimize costs and maximize customer satisfaction. It involves several key processes and considerations:
Return Authorization
When a customer wishes to return a product, the first step is to initiate the return authorization process. This involves gathering information about the return, including the reason for the return, product details, and purchase history.
Inspection and Evaluation
Upon receiving the returned product, inspecting and evaluating its condition is essential. This step helps determine whether the product is eligible for resale, refurbishment, or needs to be disposed of.
For products that are in good condition and suitable for resale, the next step is restocking. This involves returning the product to inventory for future sale to customers.
Refurbishment and Repair
In cases where returned products require refurbishment or repair, it is essential to have processes in place to address these needs promptly. Refurbished products can often be resold at a lower cost, benefiting both the company and customers.
Customer Communication
Clear and effective communication with customers throughout the returns process is crucial. Providing customers with updates on the status of their returns and refunds helps build trust and enhances the overall customer experience.
Inventory Management
Managing returned products in inventory efficiently is essential to avoid overstocking or understocking spare parts or refurbished items. An organized approach to inventory management ensures that returned items are readily available when needed.
Data Analytics
Data analytics tools can provide valuable insights into return trends, reasons for returns, and areas for process improvement. Companies can make informed decisions to optimize their returns management processes by analyzing data.
Please visit our website for more information on how UCS Logistics can assist with effective returns management and comprehensive IT asset management solutions.
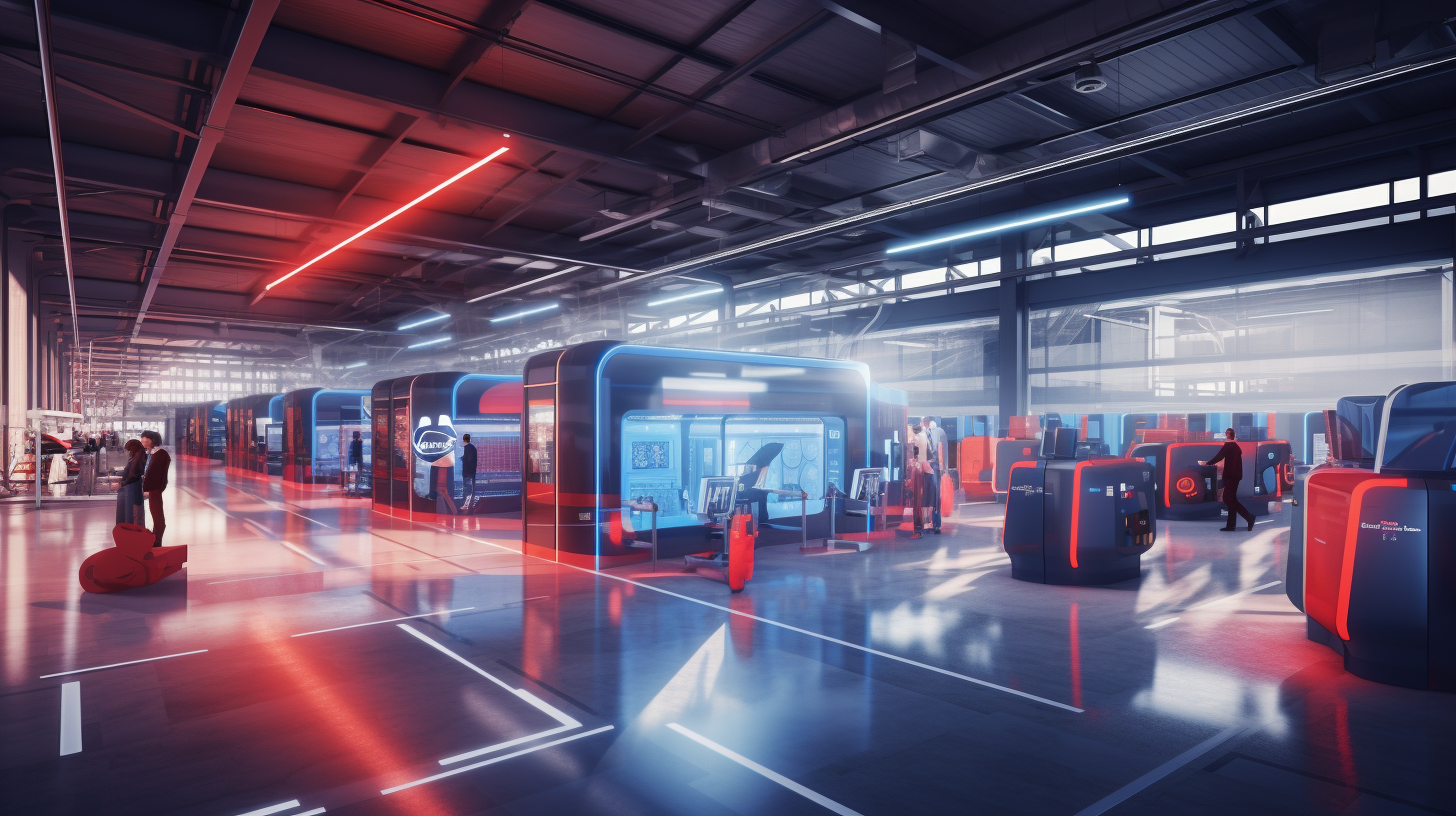
Product Evaluation and Sorting
In reverse logistics, product evaluation and sorting are essential processes that follow the initial return of products. These processes help determine the fate of returned items and play a crucial role in optimizing resource utilization and sustainability:
Evaluation of Product Condition
Upon receiving a returned product, the first step is to evaluate its condition thoroughly. This evaluation includes assessing whether the product is in a state suitable for resale, refurbishment, or recycling. Products may vary widely in condition, from like-new to heavily damaged.
Sorting for Resale
Products in good condition and can be returned to the inventory for resale are sorted accordingly. These items can be made available to customers again, reducing waste and maximizing revenue.
Refurbishment and repair processes are initiated for products that require attention due to damage or wear and tear. Skilled technicians work to bring these items back to a sellable or usable state, extending their lifecycle and reducing the need for new replacements.
Products that cannot be refurbished or resold due to extensive damage or obsolescence are sorted for recycling. Recycling ensures that materials are recovered and reused, contributing to sustainability efforts and reducing environmental impact.
In cases where products are beyond repair and recycling, responsible disposal is critical. This involves adhering to environmental regulations and disposing of items in an eco-friendly manner to minimize environmental harm.
Managing returned products in inventory efficiently is essential to ensure that they are readily available for resale or refurbishment. Effective inventory management prevents overstocking and understocking of spare parts or refurbished items.
Data analytics tools play a vital role in product evaluation and sorting. By analyzing data on returned products, companies can identify trends, patterns, and opportunities for process improvement. Data-driven decisions can lead to more efficient sorting and resource allocation.
Inventory management is crucial to reverse logistics and overall supply chain management. It involves handling returned products efficiently and ensuring they are accounted for in the inventory. Here are key aspects of inventory management in the context of reverse logistics:
Organized Tracking
Efficient inventory management starts with organized tracking of returned products. Each returned item should be documented accurately, including details about its condition, reason for return, and expected disposition.
Avoiding Overstocking
Proper inventory management helps companies avoid overstocking returned products. This prevents the unnecessary storage of excess items that may become obsolete and incur storage costs.
Preventing Understocking
Conversely, effective inventory management ensures enough refurbished or repaired items in stock to meet demand promptly. This ensures the timely delivery of customer orders.
Prioritizing Resale
Returned products that are suitable for resale should be prioritized within the inventory. This allows companies to recapture value from these items by making them available for purchase by customers.
Timely Handling
Inventory management also involves ensuring that returned items are handled promptly. Delays in processing returns can lead to increased storage costs and customer dissatisfaction.
Data analytics tools play a vital role in inventory management. By analyzing data related to returned products, companies can make informed decisions about stock levels, trends, and areas for improvement.
Integration with Other Systems
Inventory management in reverse logistics should be seamlessly integrated with other systems, including order management and fulfillment, to ensure smooth operations.
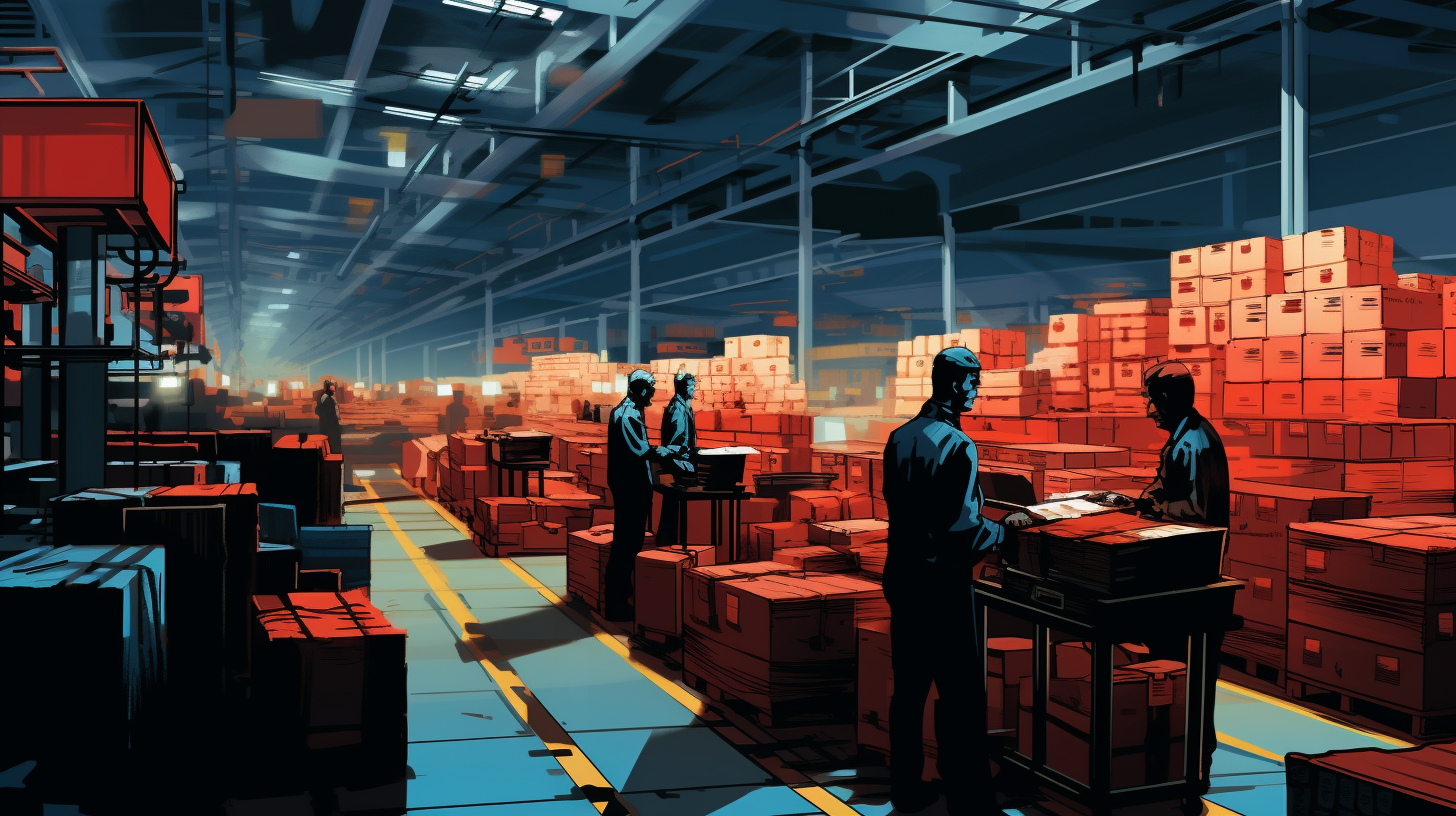
Data analytics is crucial to effective reverse logistics and IT asset management. It involves the analysis of data related to returned products and various aspects of the supply chain. Here's a breakdown of the importance of data analytics in this context:
Insights into Return Trends
Data analytics allows companies to gain insights into return trends. By analyzing patterns, such as the types of products commonly returned or the reasons for returns, businesses can make informed decisions to address recurring issues.
Process Improvement
Analyzing data from reverse logistics processes helps identify areas for improvement. Based on data-driven insights, companies can streamline operations, reduce bottlenecks, and enhance efficiency.
Inventory Optimization
Data analytics aids in optimizing inventory levels. By studying inventory data, companies can adjust stock levels to meet demand effectively while minimizing carrying costs.
Customer Behavior Analysis
Understanding customer behavior is vital. Data analytics can reveal customer returns and preferences patterns, enabling companies to tailor their product offerings and services.
Forecasting
Data analytics can be used for demand forecasting. Predictive analytics helps businesses anticipate future returns and plan accordingly, reducing the risk of overstocking or understocking.
Data analytics should be integrated with other systems, such as inventory management and order fulfillment, to ensure a seamless flow of information and decision-making.
Supplier Collaboration
Supplier collaboration is key in optimizing reverse logistics and IT asset management. It involves working closely with suppliers to improve various aspects of the supply chain. Here are the primary reasons why supplier collaboration is crucial:
Streamlining Returns
Collaboration with suppliers is essential for streamlining the returns process. Suppliers need to be involved in return authorization, providing return labels, and coordinating the return of products.
Defective Products
When products are returned due to defects, working with suppliers to identify root causes and implement corrective actions is vital. This helps reduce the recurrence of defective products in the future.
Excess Inventory
Collaboration with suppliers can help address issues related to excess inventory. Suppliers may agree to take back excess products or provide flexible return policies to manage overstocked items.
Timely Replacement
Supplier collaboration ensures that replacement products are delivered promptly, minimizing customer downtime when replacements are needed for returned items.
Cost Reduction
Collaborating with suppliers can lead to cost reductions in the reverse logistics process. Shared responsibilities and efficient communication can reduce operational costs.
Quality Control
Collaboration with suppliers includes quality control measures. Suppliers and manufacturers can work together to improve product quality and reduce the number of returns.
Sustainability
Suppliers can play a role in environmentally responsible disposal and recycling of products. Collaborative efforts can ensure that end-of-life products are handled in an eco-friendly manner.
Continuous Improvement
Supplier collaboration should be an ongoing process. Regular meetings and feedback mechanisms enable continuous reverse logistics and supply chain management improvement.
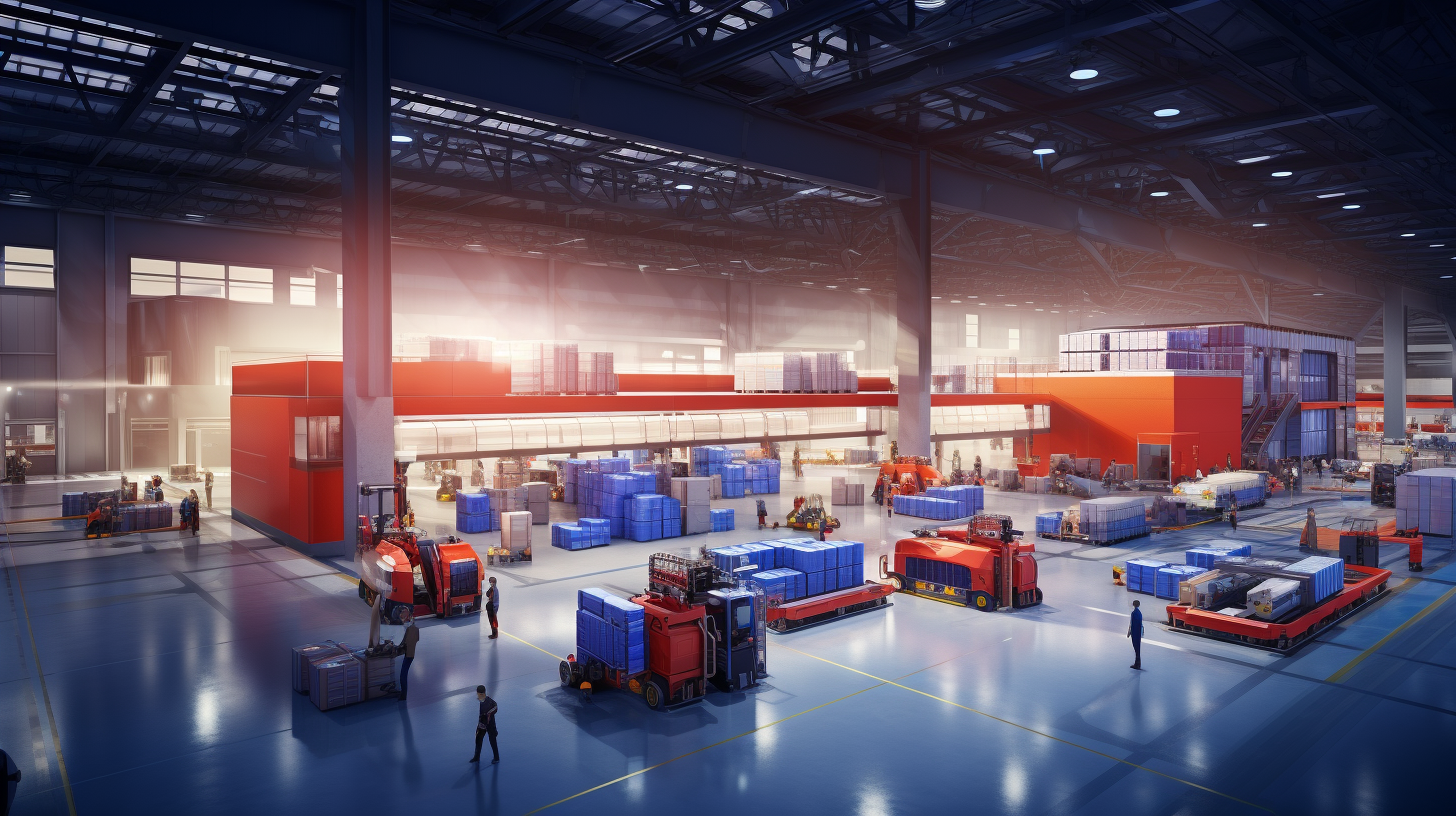
Refurbishment and repair are essential processes within reverse logistics that focus on returning returned or damaged products to a usable or sellable state. Here's a closer look at the significance of refurbishment and repair in the context of IT asset management:
Extending Product Lifecycle
Refurbishment and repair processes extend the lifecycle of IT assets. Rather than discarding slightly damaged or outdated products, these processes enable companies to salvage and reuse them.
Cost Savings
Repairing and refurbishing IT assets is often more cost-effective than purchasing new ones. It helps companies save on procurement costs while maintaining operational efficiency.
Sustainable Practices
Refurbishment and repair contribute to sustainability efforts by reducing electronic waste. By reusing and repairing IT equipment, companies reduce their environmental footprint.
During refurbishment, strict quality control measures are implemented to ensure that the repaired or refurbished products meet or exceed industry standards.
Timely Deployment
Efficient repair and refurbishment processes ensure that IT assets are quickly deployed into the organization's infrastructure, minimizing downtime.
Customization
Refurbishment can include customizations based on the organization's specific needs. This allows companies to tailor IT assets to their requirements without the cost of new purchases.
Refurbishment processes should adhere to regulatory and industry-specific compliance standards to ensure that repaired equipment meets legal requirements.
Warranty Support
Repaired and refurbished products may come with warranties or guarantees, providing peace of mind to organizations that choose these cost-effective options.
Recycling and Disposal
Recycling and disposal are critical components of reverse logistics and IT asset management, focusing on the environmentally responsible handling of end-of-life products. Here's why recycling and disposal matter:
Environmental Responsibility
Recycling and disposing of IT assets in an eco-friendly manner demonstrate a commitment to environmental responsibility. It reduces the impact of electronic waste on the planet.
Regulatory Compliance
Companies must adhere to regulatory requirements when it comes to electronic waste disposal. Compliance ensures that the disposal process follows legal guidelines.
Data Security
Proper disposal includes data sanitization and secure data destruction. Ensuring that sensitive data is not accessible on disposed assets is essential for protecting sensitive information.
Resource Recovery
Recycling allows for recovering valuable resources from IT assets, such as metals and rare materials. This reduces the need for mining and conserves natural resources.
Landfill Reduction
Responsible disposal practices help reduce the amount of electronic waste in landfills, which can have harmful environmental consequences.
Certified Recycling Facilities
Choosing certified recycling facilities ensures that industry standards and environmental best practices carry out disposal.
Circular Economy
Recycling contributes to a circular economy, where products and materials are reused and recycled, minimizing waste and promoting sustainability.
Public Image
A commitment to responsible recycling and disposal positively impacts a company's public image and sustainability efforts.
For more information on how UCS Logistics handles recycling and disposal responsibly as part of comprehensive IT asset management solutions, please visit our website .
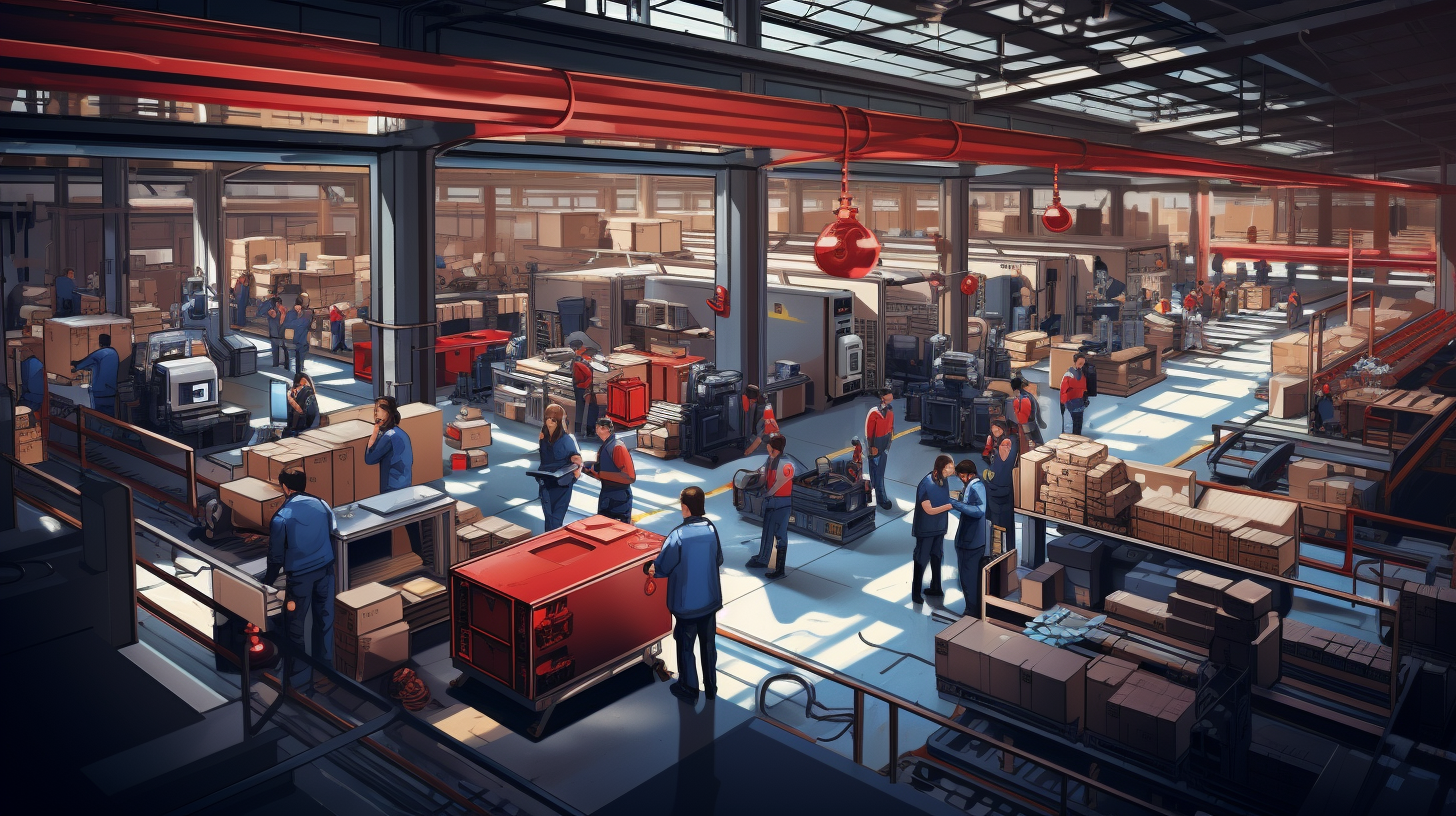
Transportation Efficiency
Transportation efficiency is a crucial aspect of reverse logistics and IT asset management, focusing on optimizing the movement of products and materials within the supply chain. Here's why transportation efficiency is essential:
Efficient transportation practices help reduce shipping costs associated with returning, refurbishing, and distributing IT assets. This translates into cost savings for organizations.
Timely Product Delivery
Efficient transportation ensures that returned or refurbished IT assets are delivered to their destinations promptly. This minimizes delays and downtime for organizations.
Minimized Carbon Footprint
Streamlining transportation routes and methods can minimize the carbon footprint associated with logistics operations. This aligns with sustainability goals.
Route Optimization
Route optimization technologies help identify the most efficient routes for transporting IT assets, reducing fuel consumption and transportation time.
Inventory Flow
Efficient transportation is linked to inventory management. Ensuring products are transported to the right locations at the right time helps maintain an optimized inventory flow.
Collaboration with Carriers
Collaboration with transportation carriers and logistics partners is essential for achieving transportation efficiency. Partnerships can lead to cost-effective solutions.
Compliance with Regulations
Efficient transportation practices should comply with regulations and standards, ensuring safe and secure shipments.
Customer Satisfaction
Timely and efficient transportation contributes to customer satisfaction by ensuring that products are available when needed, reducing disruptions.
Effective customer communication is critical to reverse logistics and IT asset management, focusing on building trust and ensuring a positive customer experience. Here's why customer communication matters:
Transparency
Transparent communication regarding return processes, expected timelines, and policies fosters trust between organizations and customers.
Updates on Returns
Providing customers with regular updates on the status of their returns helps manage expectations and reduces uncertainty.
Return Policies
Clear and concise communication of return policies helps customers understand their rights and responsibilities when returning products.
Feedback Mechanisms
Establishing feedback mechanisms allows customers to provide input on their return experience, enabling organizations to improve.
Resolution of Issues
Effective communication channels enable quick resolution of any issues or concerns that customers may have during the return process.
Building Loyalty
Positive communication experiences contribute to customer loyalty, vital for long-term business success.
Educating Customers
Informing customers about the importance of responsible disposal and recycling of IT assets promotes sustainability and environmental responsibility.
Accessibility
Ensuring customer communication channels are accessible and user-friendly enhances the overall customer experience.
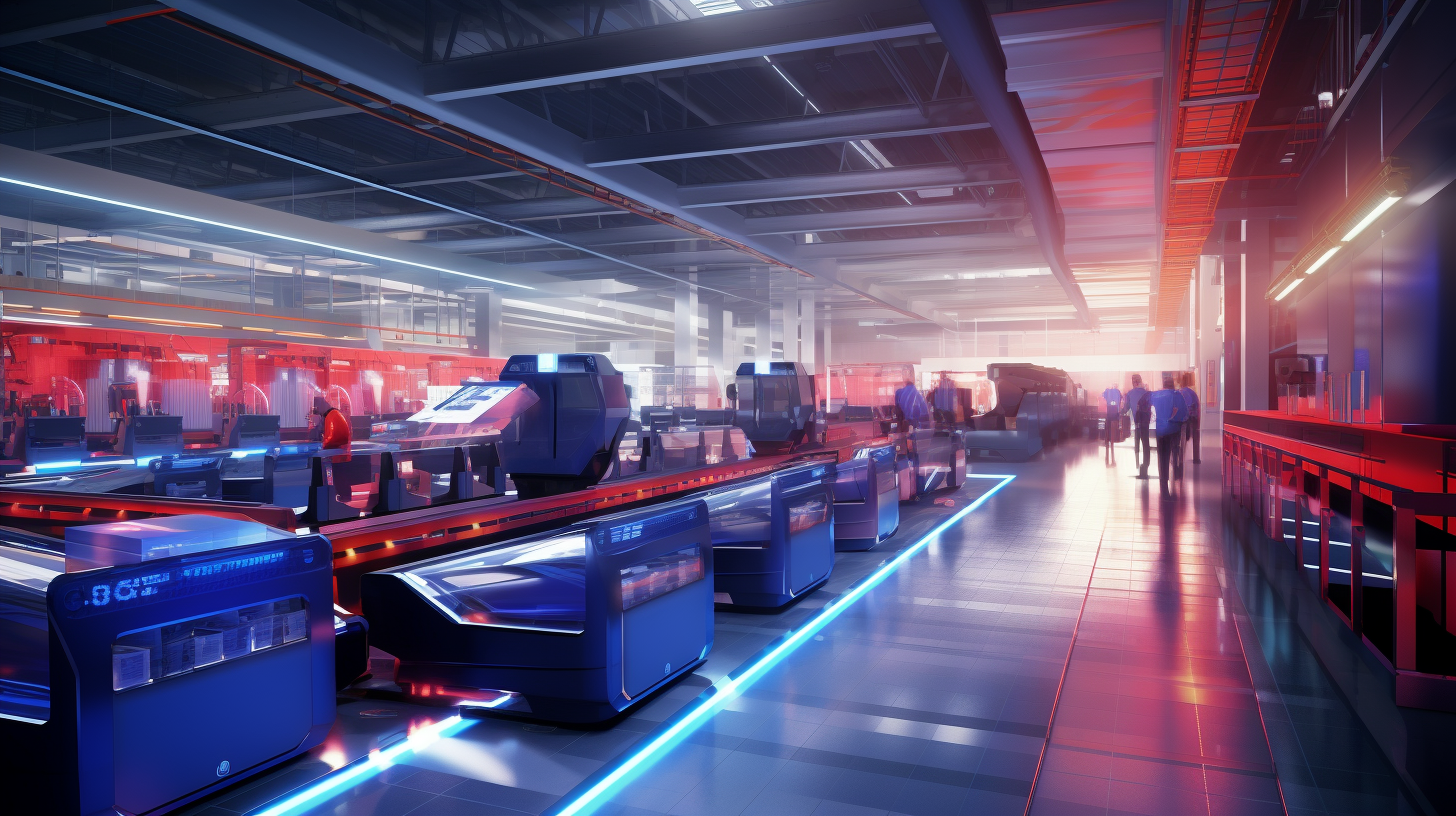
In conclusion, IT asset management is rapidly evolving, and organizations must adapt to stay competitive. The nine best practices in reverse logistics discussed in this article provide a roadmap for success. Whether seeking to optimize returns, improve inventory management, or enhance customer communication, UCS Logistics is here to help.
Our commitment to transparency, sustainability, and customer satisfaction sets us apart. By choosing UCS Logistics, you can access a wealth of expertise and resources to transform your IT asset management processes. Together, we can unlock the full potential of your IT assets, reduce costs, and drive efficiency within your organization.
To embark on a seamless IT asset management journey, visit our website for more information. Contact us today, and let's take your IT asset management to the next level.
Key Takeaways from the Article
Definition and Importance of Reverse Logistics
Reverse logistics is a critical part of supply chain management, involving the return of products to the manufacturer or a designated location for various purposes like refurbishment or recycling.
Key to reverse logistics, it includes processes like return authorization, inspection, evaluation, restocking, refurbishment, repair, and customer communication to minimize costs and maximize customer satisfaction.
This involves assessing returned products' condition, sorting for resale, refurbishment, recycling, disposal, and efficient inventory management, backed by data analytics for process improvement.
Crucial for handling returned products efficiently, it covers organized tracking, avoiding overstocking, preventing understocking, prioritizing resale, timely handling, and integrating with other systems for smooth operations.
Data Analytics in Reverse Logistics
Offers insights into return trends, process improvement, inventory optimization, customer behavior analysis, demand forecasting, and integrates with other systems for informed decision-making.
Essential for optimizing reverse logistics, it involves streamlining returns, managing defective products, addressing excess inventory, ensuring timely replacements, reducing costs, and improving quality and sustainability through continuous improvement.
Focuses on returning damaged products to a usable state, extending product lifecycle, saving costs, promoting sustainability, maintaining quality control, ensuring timely deployment, customization, compliance, and warranty support.
Vital for handling end-of-life products responsibly, ensuring environmental responsibility, regulatory compliance, data security, resource recovery, landfill reduction, using certified facilities, and contributing to a circular economy.
Aims to optimize product movement within the supply chain, reducing costs, ensuring timely delivery, minimizing carbon footprint, optimizing routes, managing inventory flow, collaborating with carriers, and complying with regulations.
Effective Customer Communication
Critical for building trust and ensuring a positive experience, it involves transparency, regular updates, clear return policies, feedback mechanisms, issue resolution, building loyalty, educating customers, and ensuring accessibility.
Reminder of the Post’s Main Point: The article from UCS Logistics provides a comprehensive guide on best practices in reverse logistics to enhance efficiency, sustainability, and customer satisfaction in IT asset management.
Frequently Asked Questions about Reverse Logistics
What is Reverse Logistics in Supply Chain Management?
Why is Effective Returns Management Important in Reverse Logistics?
How does data analytics contribute to reverse logistics, what role does supplier collaboration play in reverse logistics, why is transportation efficiency essential in reverse logistics, related searches.
Google Search
Best Practices in IT Asset Management
Effective Strategies for Customer Satisfaction in Logistics
Role of Data Analytics in Supply Chain Optimization
Sustainable Practices in Electronic Waste Management
Organize your lifecycle inventory
Ucs logistics: your partner in it asset lifecycle management, securing your assets: ucs's security protocols, expert hardware installation with ucs logistics, standard operating procedure for asset management, the role of ai in revolutionizing it logistics, "partnering with ucs logistics was the best decision we made. their professionalism and commitment to excellence set them apart. highly recommended.

Numbers Matter

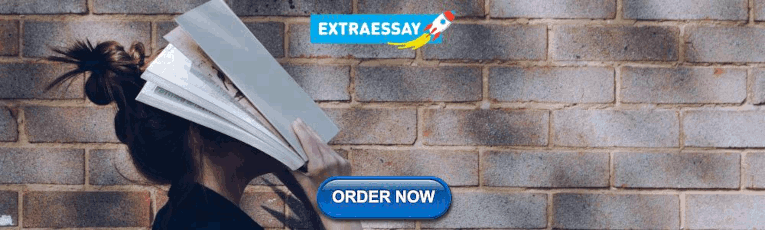
IMAGES
VIDEO
COMMENTS
According to a study by consulting firm Deloitte, by 2022, retailers are expected to receive 13 billion returns worth $573 billion every year. That accounts for four times the total ecommerce sales in 2018). ... In any case, the best reverse logistics is the absence of reverse logistics — when the customer is happy with a product and, thus ...
Case study: How Amazon handles reverse logistics. Amazon is an excellent example of a company that has implemented a successful reverse logistics program. The company's official statement on returns policy states that customers get free returns within 30 days of receiving the product.
Abstract. Reverse logistics deals with the processes associated with the flows of products, components and materials from users/owners to re-users. This paper provides a review and content analysis of more than sixty case studies on reverse logistics. The case studies deal with issues such as the structure of the networks, the relationships ...
We then provide case study examples for each activity in the framework, each demonstrating how an organization is successfully managing this task. ... Case: Reverse logistics strategic management at Cisco. One organization that has had success managing a strategic reverse logistics program is the multinational technology organization Cisco ...
Key words: Reverse logistics; Case studies; Content analysis. 1 Introduction Reverse logistics, dealing with the physical flows of products, components and materials flowing from users/owners to re-users, is a growing field both in practice and in the academic world. In order to get insight in how reverse logistics are dealt
some case studies o n reverse logistics have b een described in the literature, dealing with different industries, rec overy options and dr ivers, see e .g. (Kopicki et al., 19 93; Kostecki,
3. CONCLUSIONS The system reconfiguration for a reverse logistics system in this paper is done by using Lean Six-sigma methodologies, with a linear programming model utilized to optimize the system performance. The Lean Six-sigma methodology, DMAIC, is used in addressing each step in this case study.
Reverse Logistics in the Transition Towards Circular A Case Study of Customer Returns at IKEA . Master's thesis in Supply Chain Management Master's Programme . Karin Malmgren Karl Mötsch Larsson . REPORT NO. E 2020:016 . Reverse Logistics in the Transition Towards Circular Economy .
Reverse Logistics. Case Studies January 15, 2021. The Challenge. A nation-wide battery company serving the technology data center market needed a full-service partner who could bring them an end-to-end solution. The client needed to 1) ship new batteries to be installed directly to MyPorter's reverse logistics distribution center 2) deliver ...
Abstract. Reverse logistics deals with the processes associated with the flows of products, components and materials from users/owners to re-users. This paper provides a review and content ...
This paper sets out to analyze a case study of ABC, one of the leading manufacturers of automobiles in India to assess its current status of reverse logistics operations. A situation-actor-process (SAP)-learning-action-performance (LAP) model has been applied to analyze the case study. Literature review indicates that issues like regulations, top management commitment, competition in market ...
Case studies 4.1 Reverse Logistics Network Structures A main activity in reverse logistics is the collection of the products to be recovered and the redistribution of the processed goods. Although this problem resembles the standard forward distribution problem, there are also some differences. There are usually many points from which goods
Reverse Logistics Examples. Globally, companies are changing the ways they address waste, and the supply chain is a big piece of that initiative. These reverse logistics examples focus on returns, exchanges and recycling. People are more likely to buy products from a company if they think returns are easy and they are even more likely to become ...
Overall, Amazon's reverse logistics strategies have played a crucial role in the company's success in the e-commerce industry. By using innovative technologies, prioritizing sustainability, and emphasizing customer satisfaction, Amazon has effectively managed returns and excess inventory, reduced costs, and maintained its position as a ...
Reverse Logistics Optimization Results. Immediately improved demand forecast accuracy from 35 percent to 99 percent. Reduced spare parts inventory levels by 52 percent or $2.3 million in the rst year. Reduced cycle time by 70 percent from 3.35 to 1.10 days. Improved on-time, same day ship rates from 84 percent to 99 percent.
The development of a reverse logistics system requires a detailed analysis of technical, economical and environmental issues with the aim to evaluate the system's viability. This paper shows, through a case study, the main results of a project for the implementation of a reverse logistics system in a steel company and provides general ...
This paper is aimed at introducing the concept of reverse logistics (RL) and its implications for supply chain management (SCM). RL is a research area focused on the management of the recovery of products once they are no longer desired (end-of-use products, EoU) or can no longer be used (end-of-life products) by the consumers, in order to obtain an economic value from the recovered products.
Reverse logistics is a critical yet often understated aspect of supply chain management, dealing with the return journey of products from the customer to the seller or manufacturer. This process involves reversing the traditional supply chain flow, where goods move from their final destination back to their point of origin for various reasons ...
This paper presents a systematic literature review of the various aspects of reverse logistics (RL) and closed-loop supply chains (CLSC) in implementing and achieving circular economy (CE) motives. CE is identified as a method of embracing imperishability into the economic structure, helping shift from a linear to a condition leading to ...
For example, reverse logistics operations may reduce flows of waste disposal and divert waste from landfills, reducing contaminated run-offs, which lower individual and community risk of exposure to toxins. ... Refurbishing and recycling of cell phones as a sustainable process of reverse logistics: A case study in Brazil. Journal of Cleaner ...
A case study approach was adopted with information collected from company web sites, direct observation, and in‐depth interviews with four major consumer electronic product manufacturers in China. Findings were analyzed and compared across all the cases studied to determine the common external and internal drivers for reverse logistics ...
For example, Sunny discussed various blockchain-based traceability solutions, and many companies have ... Chia-Yi Chieh, Ming-Hung Shih, and Ting-Wei Wu. 2021. "Preventing Return Fraud in Reverse Logistics—A Case Study of ESPRES Solution by Ethereum" Journal of Theoretical and Applied Electronic Commerce Research 16, no. 6: 2170-2191 ...
Discover the 9 best practices in reverse logistics to enhance efficiency, reduce costs, and improve customer satisfaction in your supply chain. +1 (609) 528-2410. [email protected]. ... Case Studies. Industries. UCSL SERVICES. 9 Best Practices In Reverse Logistics . Created by: Erik von Hollen. Created. November 20, 2023. Home /